6 Essential Rules for Conveyor Belt Tracking Theory
In the realm of industrial operations, the efficiency and longevity of conveyor belt systems hinge significantly on the precision of conveyor belt tracking. This critical aspect ensures that belts run smoothly and consistently along their intended paths, minimizing wear and tear and preventing potential downtimes. However, the journey to achieving flawless alignment is often marred by common issues such as misalignment and tracking problems, which can lead to belt damage, product mishandling, and reduced operational efficiency. Understanding and applying the principles of conveyor belt tracking theory is paramount in addressing these challenges. It provides a structured approach to diagnosing and rectifying tracking issues, ensuring that conveyor belts meet the rigorous demands of industrial applications while maintaining optimal performance and safety standards.
The Basics of Conveyor Belt Tracking and the Conveyor Belt Tracking Theory
Conveyor Belt Tracking
Conveyor belt tracking is the process of ensuring that the conveyor belt runs true and straight on the pulleys and rollers. At the heart of this process lies the conveyor belt tracking theory, which provides the foundational principles necessary for understanding and correcting the path of the conveyor belt. This theory is not just a set of guidelines but a comprehensive approach that considers the various factors influencing the belt’s behavior, from the initial installation and alignment of the conveyor components to the ongoing maintenance practices that keep the system in check.
Conveyor Belt Tracking Theory
The conveyor belt tracking theory delves into the dynamics of belt movement, examining how factors such as tension, alignment, and load distribution affect the belt’s trajectory. By understanding these principles, operators and maintenance personnel can make informed adjustments to pulleys, rollers, and other critical components, ensuring the belt remains centered and runs smoothly.The significance of conveyor belt tracking cannot be overstated. Proper tracking prevents the belt from drifting off course, which can lead to a host of operational issues, including premature wear of the belt and conveyor structure, product spillage, and even potential safety hazards.
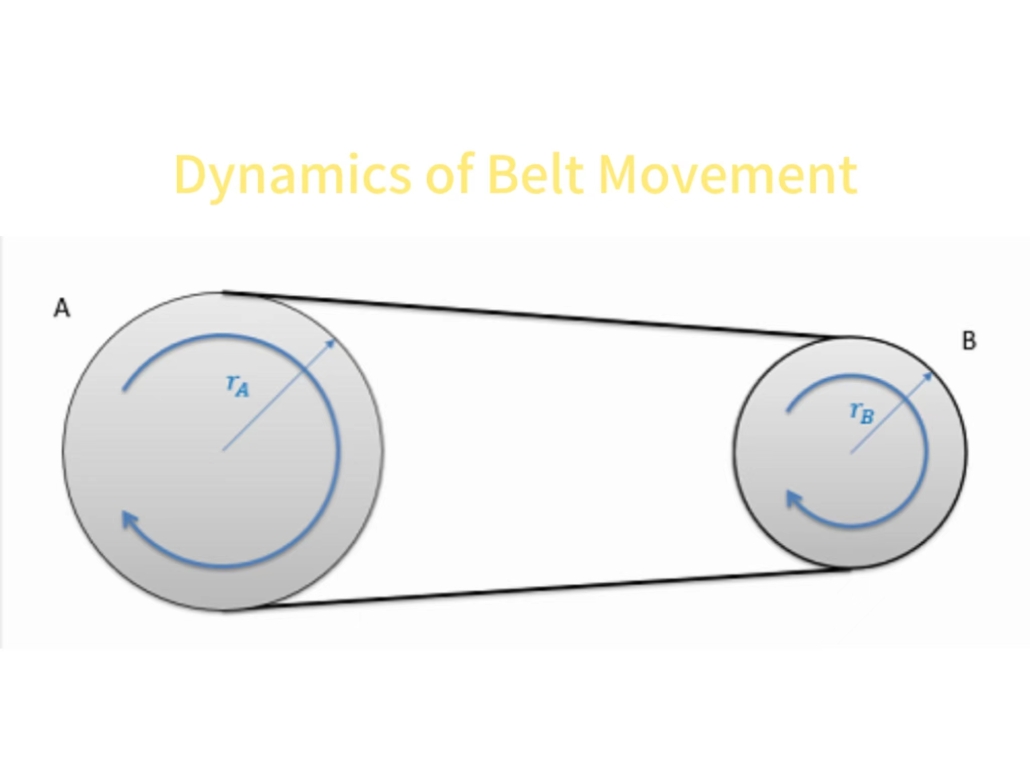
Moreover, the conveyor belt tracking theory emphasizes the importance of a holistic approach to conveyor belt maintenance. It suggests that effective tracking is not merely about reactive adjustments in response to misalignment but involves a proactive stance on installation precision, regular inspections, and the timely correction of even the slightest deviations from the ideal path. This proactive approach not only extends the lifespan of the conveyor belt but also enhances the efficiency and reliability of the entire conveyor system, making it an indispensable practice in the realm of industrial operations.
The Primary Goal of Conveyor Belt Tracking Theory
A fundamental principle of Conveyor Belt Tracking Theory is to ensure that the conveyor belt runs centrally on the pulleys and idlers. This central alignment is critical for the efficient operation of the conveyor system, as it prevents the belt from drifting sideways, which can cause uneven wear, potential damage to the belt, and material spillage.
Central to Conveyor Belt Tracking Theory is the understanding that the belt’s position on the pulleys and idlers is influenced by several factors, including the belt’s tension, the alignment of the system’s structure, and the loading conditions. To achieve and maintain this central position, Conveyor Belt Tracking Theory provides a framework for adjustments and regular maintenance checks. These include ensuring all components are properly aligned, the belt is appropriately tensioned, and the load is evenly distributed across the belt’s width.
Implementing the strategies outlined in Conveyor Belt Tracking Theory not only enhances the lifespan and functionality of the conveyor belt but also improves the safety and productivity of the entire system. By focusing on keeping the belt centered on the pulleys and idlers, facilities can minimize downtime and reduce the need for costly repairs, thus ensuring a smoother and more reliable material handling process.
Understanding the Roles of Idlers and Pulleys in Conveyor Belt Tracking Theory
Within the framework of Conveyor Belt Tracking Theory, understanding the roles and functions of key components such as idlers and pulleys is crucial for maintaining the alignment of conveyor belts. These components are fundamental to the effective tracking and operation of conveyor systems, helping to ensure that the belts run smoothly and efficiently.
Idlers: Idlers play a pivotal role in Conveyor Belt Tracking Theory by supporting the conveyor belt and providing a smooth surface for the belt to run on. They are strategically placed along the conveyor frame to support the weight of the belt and the materials being transported. In the context of Conveyor Belt Tracking Theory, idlers also help in adjusting the tracking of the belt. There are different types of idlers used in conveyor systems, including impact idlers, which absorb shock at loading points, and troughing idlers, which help to keep the belt centered while carrying loads. Each idler type is designed to fulfill a specific function in maintaining belt alignment and preventing slippage or misalignment.
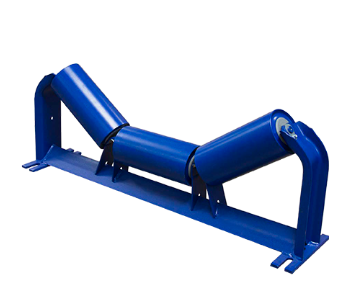
Pulleys: Pulleys are another essential component addressed in Conveyor Belt Tracking Theory. They function as the primary contact points for the motion of the belt and are critical for directing and driving the belt. Conveyor systems typically feature two types of pulleys: drive pulleys, which power the belt’s movement, and tail pulleys, which guide the belt as it loops back. In Conveyor Belt Tracking Theory, the alignment and maintenance of these pulleys are paramount. Properly aligned pulleys ensure that the belt runs centrally and does not drift side to side. Misaligned or worn pulleys can lead to uneven belt wear, increased strain on the conveyor, and eventual operational failure.
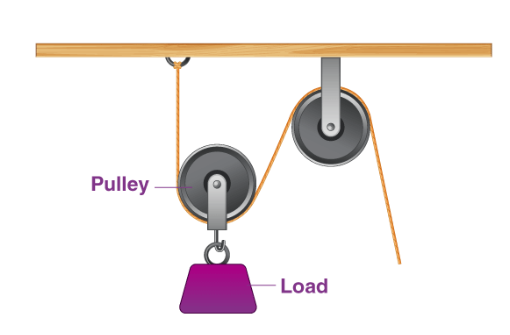
Integration of Idlers and Pulleys: Conveyor Belt Tracking Theory emphasizes the need for both idlers and pulleys to work in harmony for optimal belt tracking. By ensuring that both components are properly aligned and functioning correctly, the conveyor belt is more likely to remain centered and stable under various operating conditions. Regular inspections and maintenance according to Conveyor Belt Tracking Theory can prevent small issues from becoming major problems, thereby enhancing the efficiency and lifespan of conveyor systems.
Key Factors Affecting Belt Tracking in Conveyor Belt Tracking Theory
Understanding the various factors that influence the tracking of a conveyor belt is crucial in Conveyor Belt Tracking Theory. Proper tracking is essential for the efficiency and longevity of conveyor systems, and several key factors must be considered to maintain optimal belt alignment:
Influence of Installation and Operational Conditions
In Conveyor Belt Tracking Theory, the conditions under which a conveyor belt is installed and operated play a significant role in its tracking performance. Misalignment of the conveyor structure during installation can lead to persistent tracking issues. Moreover, operational conditions such as the speed of the conveyor, the alignment of the load point, the use of high speed conveyor rollers, and environmental factors like temperature and humidity can all impact how well the belt tracks. Ensuring that the conveyor is installed accurately and adjusted to suit specific operational conditions is a critical aspect of Conveyor Belt Tracking Theory.
Impact of Material Properties and Belt Design on Tracking
Another vital component of Conveyor Belt Tracking Theory is the consideration of the material properties of the belt itself and its design. The weight, flexibility, and texture of the belt can affect how it behaves on the conveyor. Heavy-duty belts might resist alignment changes better than lighter belts, while belts with a rough surface might interact differently with idlers and pulleys compared to those with a smoother surface. Additionally, the design of the belt, including aspects such as the belt’s width, thickness, and the type of seams used, can also influence its tracking properties. Understanding these factors is essential in applying Conveyor Belt Tracking Theory to anticipate potential issues and make necessary adjustments.
Conveyor Belt Alignment Procedures and the Conveyor Belt Tracking Theory
The alignment of a conveyor belt is a critical procedure that directly impacts the operational efficiency and longevity of conveyor systems. Grounded in the conveyor belt tracking theory, these alignment procedures are designed to ensure that the belt operates within its intended path, minimizing wear and reducing the risk of downtime. This section provides a detailed step-by-step guide on the conveyor belt alignment process, complemented by references to authoritative PDF resources that offer in-depth instructions and insights.
- Initial Inspection: Before any adjustments are made, a thorough inspection of the conveyor belt and its components is essential. This includes checking for signs of wear on the belt, misaligned rollers, and improper belt tension. These initial observations can provide valuable clues about the underlying causes of misalignment.
- Adjusting Tension: Proper belt tension is crucial for effective tracking. The conveyor belt tracking theory emphasizes that too much tension can lead to excessive wear, while too little can cause the belt to wander off course. Adjusting the tension should be done gradually and evenly on both sides of the conveyor.
- Aligning Rollers and Pulleys: Rollers and pulleys must be perpendicular to the belt’s direction of travel. Using a standard level, ensure that these components are correctly aligned. Misaligned rollers and pulleys are common culprits of tracking issues.
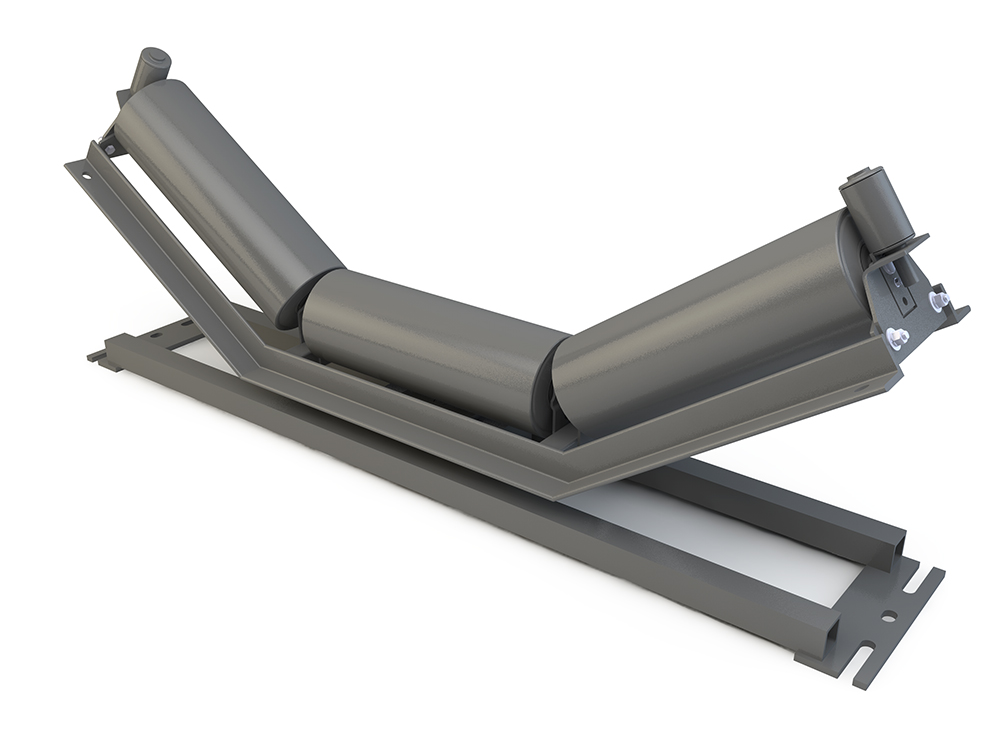
- Checking for Material Build-up: Material build-up on conveyor roller material, pulleys, and the underside of the belt can cause the belt to misalign. Regular cleaning of these components is essential to maintain proper alignment.
- Square the Frame: The conveyor frame itself must be square and parallel to the belt. Use a carpenter’s square or a similar tool to check the frame’s alignment and make necessary adjustments.
- Test Run: After adjustments are made, perform a test run to observe the belt’s behavior. It’s important to monitor the belt over several revolutions, as some issues may only become apparent after the belt has been running for a period.
- Regular Maintenance and Checks: Consistent with the conveyor belt tracking theory, regular maintenance and checks are vital to sustaining proper alignment. Scheduled inspections can identify potential issues before they lead to significant problems, ensuring the conveyor system remains efficient and reliable.
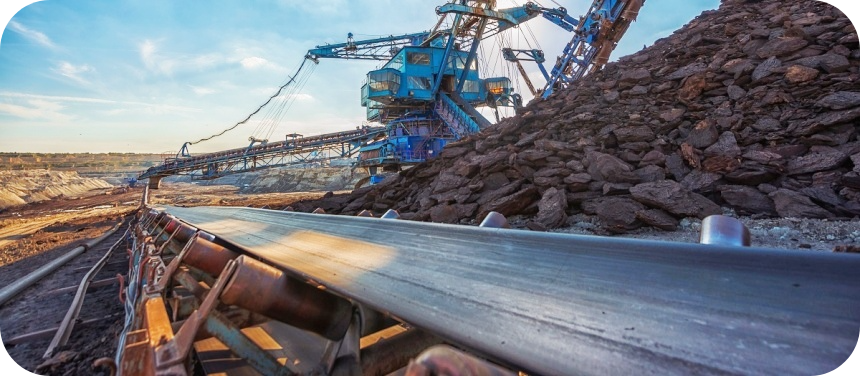
By adhering to these conveyor belt alignment procedures, informed by the conveyor belt tracking theory, facilities can enhance the performance and lifespan of their conveyor systems. For those seeking more detailed guidance, numerous PDF resources are available that delve deeper into each step of the alignment process, offering valuable tips and best practices for achieving optimal conveyor belt tracking.
Conveyor Belt Tracking Adjustments and Troubleshooting in Light of Conveyor Belt Tracking Theory
Mastering the adjustments and troubleshooting of conveyor belt tracking is essential for maintaining the operational efficiency of conveyor systems. The conveyor belt tracking theory provides a solid foundation for understanding the dynamics of conveyor belt behavior, guiding the adjustment process to ensure the belt runs straight and true. This section delves into the practical application of this theory, offering detailed instructions for adjustments and troubleshooting common tracking issues.
Adjusting the Conveyor Belt to Run Straight
- Inspect and Adjust Rollers and Pulleys: Ensure all rollers and pulleys are parallel to each other and perpendicular to the belt’s direction. Misaligned rollers are often the primary cause of tracking issues.
- Check Belt Tension: Incorrect tension is a common issue. Adjust the tension evenly on both sides to prevent the belt from pulling to one side.
- Utilize Tracking Rollers and Guides: Install and adjust tracking rollers and guides, which are designed to gently steer the belt back to its correct path without causing damage or excessive wear.
- Realign the Conveyor Frame: A misaligned frame can cause the belt to track incorrectly. Use a carpenter’s square or laser alignment tools to ensure the frame is square and true.
- Lubricate Moving Parts: Proper lubrication of rollers and pulleys can reduce friction and prevent the belt from drifting off track.
- Adjust the Loading Chute: Material should be loaded centrally onto the belt. An off-center load can cause the belt to drift.
- Correct Splice Techniques: Ensure that the belt splice is straight and square. A poorly executed splice can cause the belt to track off to one side.
- Monitor Wear Patterns: Regularly inspect the belt for wear patterns that might indicate tracking issues, and make adjustments as necessary.
- Implement Crowned Pulleys: In some cases, using crowned pulleys can help maintain belt alignment. The conveyor belt tracking theory suggests that the belt will naturally move towards the highest point of the pulley.
- Continuous Monitoring and Adjustment: Conveyor belt tracking is not a set-and-forget task. Continuous monitoring and periodic adjustments are crucial for maintaining proper alignment.
Troubleshooting Common Conveyor Belt Tracking Problems
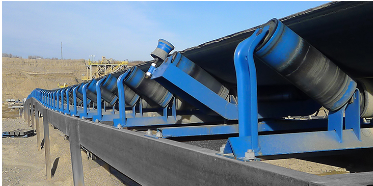
- Belt Tracks to One Side at Specific Points: Check for debris, material build-up, or damage at those points. Clean and repair as necessary.
- Belt Drifts in One Direction Across the Entire System: This often indicates an issue with tension or roller alignment. Recheck and adjust the tension and ensure all rollers are properly aligned.
- Sudden Belt Misalignment: This could be due to a damaged roller or a sudden change in load. Inspect the system for damaged components and ensure the load is evenly distributed.
- Edge Wear on the Belt: This is often a sign of misaligned rollers or guides. Adjust or replace worn components as necessary.
- Belt Slippage: This can be caused by inadequate tension or worn pulley surfaces. Adjust the tension and inspect pulleys for wear.
- Frequent Re-tracking Required: If the belt requires frequent adjustments, this could indicate a more systemic issue, such as a fundamentally misaligned conveyor frame or improper belt installation.
By applying the principles of conveyor belt tracking theory to the adjustment and troubleshooting processes, operators can ensure their conveyor belts run smoothly and efficiently, minimizing downtime and maximizing productivity. Regular maintenance, combined with a thorough understanding of conveyor belt dynamics, is key to preventing and resolving tracking issues.
Visual Guides and Diagrams in Conveyor Belt Tracking Theory
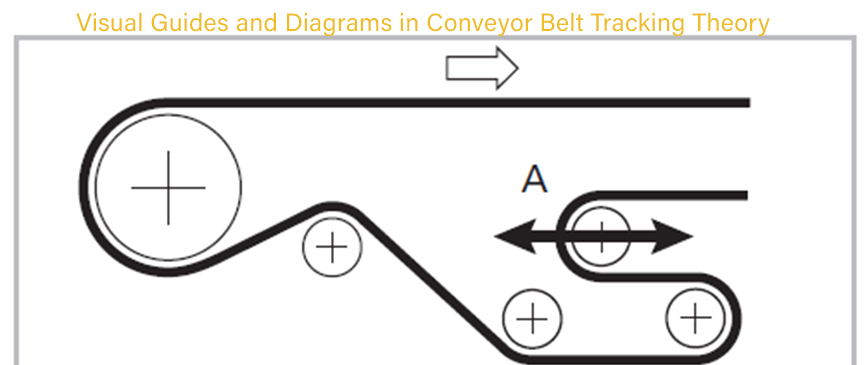
The intricate nature of conveyor belt tracking theory can sometimes be challenging to grasp through text alone. This is where visual guides and diagrams become invaluable tools, offering a clear and concise representation of the alignment and tracking processes. By incorporating detailed conveyor belt tracking diagrams, we can demystify the complexities involved, making the theory more accessible and understandable.
The Role of Diagrams in Explaining Conveyor Belt Tracking Theory
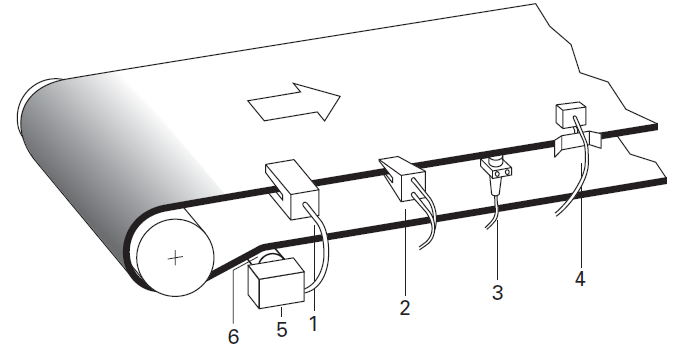
- Illustrating Components: Diagrams can effectively showcase each component involved in the conveyor system, such as rollers, pulleys, and the conveyor belt itself. By highlighting these components, diagrams provide a foundational understanding of how they interact and contribute to belt tracking.
- Demonstrating Alignment Procedures: Visual guides can step-by-step illustrate the alignment process, from initial inspection to the final adjustments. These visuals can show the correct positioning of rollers and pulleys relative to the belt, emphasizing the importance of parallel and perpendicular alignments as dictated by conveyor belt tracking theory.
- Depicting Tracking Adjustments: Adjusting a conveyor belt to run straight involves several nuanced steps, including how to cut conveyor belt straight, which can be effectively communicated through diagrams. These visuals can show how to adjust tension, align the frame, and position tracking rollers, providing a clear reference for maintenance personnel.
- Troubleshooting Guidance: When it comes to troubleshooting common tracking issues, diagrams can visually represent symptoms and solutions, such as how to identify and correct a belt that tracks to one side. This visual representation can simplify the diagnostic process, making it easier to identify and rectify problems.
- Reinforcing Best Practices: Diagrams can also reinforce best practices in conveyor belt maintenance and alignment, illustrating the dos and don’ts in a visually engaging manner. This can include showing the correct way to load materials onto the belt or how to properly lubricate moving parts.
- Enhancing Training Materials: For training purposes, diagrams serve as excellent tools to help new operators and maintenance staff visualize the concepts of conveyor belt tracking theory. They can accelerate the learning process by providing clear, visual references that complement written instructions.
By integrating visual guides and diagrams that align with conveyor belt tracking theory, we can enhance comprehension and application of these critical concepts. These visuals not only aid in the understanding of complex tracking adjustments but also serve as invaluable references during troubleshooting and maintenance activities, ensuring the longevity and efficiency of conveyor belt systems.
Advanced Conveyor Belt Tracking Techniques and the Conveyor Belt Tracking Theory
Building upon the foundational principles of conveyor belt tracking theory, this section delves into advanced techniques and tools designed to enhance the precision and efficiency of conveyor belt tracking and alignment. These sophisticated methods not only address common tracking challenges but also leverage technology to ensure optimal performance of conveyor systems.
Advanced Tracking Techniques and Tools
- Self-Aligning Rollers: These are designed to automatically adjust the belt’s position based on its movement, ensuring continuous alignment without manual intervention.
- Belt Tracking Guides: Installed along the edges of the conveyor frame, these guides provide a physical barrier to gently steer the cut edge conveyor belt back to its correct path, minimizing the risk of misalignment.
- Pneumatic Tensioning Systems: These systems automatically adjust the belt’s tension in real-time, maintaining consistent tension levels and preventing tracking issues related to tension fluctuations.
- Laser Alignment Tools: Utilizing laser technology, these tools offer a high-precision method for aligning rollers and pulleys, ensuring they are perfectly perpendicular to the belt’s direction.
- Infrared Inspection: This technique involves using infrared cameras to detect uneven temperature distributions along the belt, which can indicate misalignment or other issues affecting tracking.
- Digital Monitoring Systems: Advanced sensors and IoT devices can monitor the belt’s position and movement, providing real-time data for predictive maintenance and adjustments.
- 3D Modeling and Simulation: By creating a virtual model of the conveyor system, engineers can simulate various conditions and adjustments, optimizing the tracking strategy before implementing physical changes.
- Automated Adjustment Mechanisms: These systems can automatically adjust rollers and pulleys based on sensor data, ensuring continuous and precise alignment without manual intervention.
The Role of Technology in Improving Conveyor Belt Tracking
- Enhanced Precision: Advanced tools and techniques offer a higher level of precision in alignment and tracking adjustments, reducing the margin of error and improving overall system efficiency.
- Real-Time Adjustments: With the integration of digital monitoring systems, adjustments can be made in real-time, responding to even minor deviations from the ideal path.
- Predictive Maintenance: Technology enables the prediction of potential tracking issues before they occur, allowing for preventative measures to be taken, reducing downtime and maintenance costs.
- Data-Driven Decisions: The wealth of data provided by advanced sensors and monitoring systems allows for more informed decisions regarding conveyor belt maintenance and adjustments.
- Reduced Manual Intervention: Automated systems reduce the need for manual adjustments, minimizing human error and ensuring consistent tracking performance.
- Increased System Longevity: By maintaining optimal alignment and tracking, advanced techniques can extend the lifespan of the conveyor belt and its components.
- Operational Efficiency: Improved tracking and alignment lead to smoother operation, reduced wear on components, and enhanced product handling, contributing to overall operational efficiency.
- Safety Enhancements: Properly aligned and tracked conveyor systems are safer to operate, reducing the risk of accidents related to belt misalignment or slippage.
Incorporating these advanced conveyor belt tracking techniques, grounded in conveyor belt tracking theory, can significantly enhance the performance and reliability of conveyor systems. By leveraging technology and innovative tools, facilities can achieve superior tracking accuracy, operational efficiency, and system longevity.
Use of Self-Aligning Rollers and Idlers in Conveyor Belt Tracking Theory
In the realm of Conveyor Belt Tracking Theory, the use of self-aligning rollers and idlers stands out as a proactive approach to maintaining proper belt alignment. These specialized components are designed to automatically adjust the position of the belt as needed, which helps to correct any deviations that occur during operation. According to Conveyor Belt Tracking Theory, self-aligning rollers and idlers pivot and tilt in response to the belt’s movements. This adjustment is typically triggered by the belt moving too far to one side or the other, which prompts the idlers to gently guide the belt back to its central path.
The effectiveness of these devices in Conveyor Belt Tracking Theory is largely dependent on their correct placement and calibration. They are usually installed at critical points along the conveyor path where misalignments are most likely to occur, such as near the head and tail pulleys. Ensuring that these self-aligning rollers and idlers are properly maintained and responsive is crucial for their role in Conveyor Belt Tracking Theory, as they must be able to react dynamically to changes in the belt’s path without causing additional stress or wear on the belt.
Techniques for Managing Challenging Tracking Scenarios in Conveyor Belt Tracking Theory
Conveyor Belt Tracking Theory also provides guidance on techniques for managing challenging tracking scenarios that might not be sufficiently addressed by standard adjustments. Such scenarios include severe misalignment, frequent slippage, and excessive edge wear. Techniques recommended by Conveyor Belt Tracking Theory often involve a combination of enhanced monitoring, refined adjustments, and sometimes the integration of additional components.
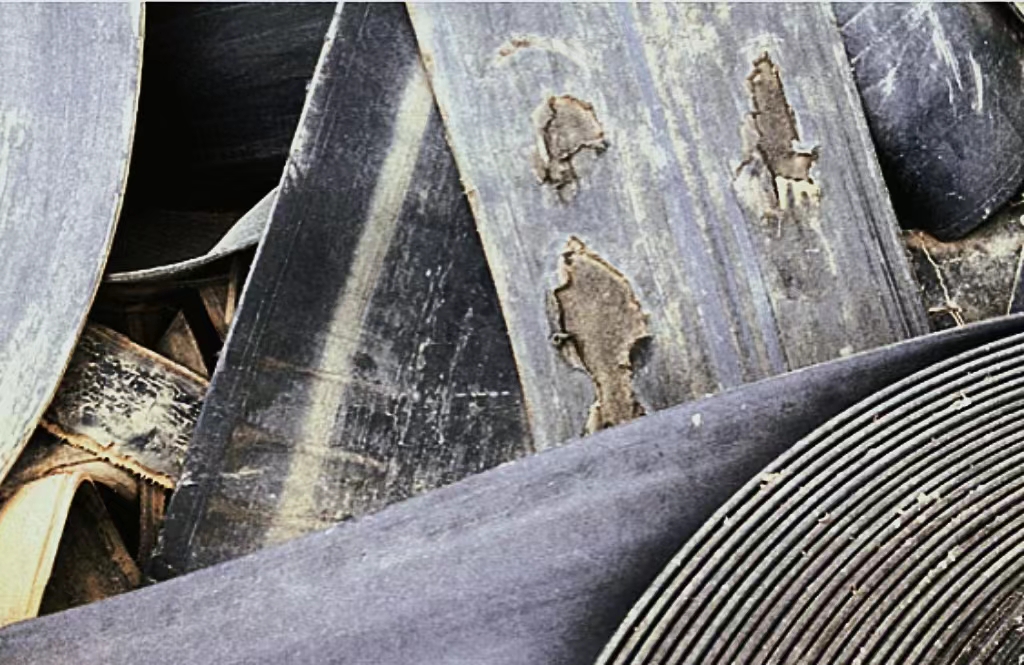
For instance, Conveyor Belt Tracking Theory suggests that in cases of severe misalignment, it may be necessary to reassess the entire conveyor layout, including checking if the conveyor frame is twisted or if the foundation has shifted. Techniques might also include the use of tracking sensors that provide real-time feedback on the belt’s position, allowing for quicker interventions.
In particularly challenging environments, Conveyor Belt Tracking Theory might recommend the installation of more robust tracking controls, such as active trackers that use powered mechanisms to adjust the belt’s position dynamically. These systems are often more responsive and can handle situations where passive components like crowned rollers or standard idlers fail to correct the tracking issue effectively.
By applying these advanced techniques within the framework of Conveyor Belt Tracking Theory, operators can address and mitigate complex and persistent tracking problems, ensuring the conveyor system operates smoothly and continues to meet the demands of high-volume or high-stress applications.
Upgrade to our conveyor belts for unmatched durability and performance!
Case Studies and Real-World Applications of Conveyor Belt Tracking Theory
The practical application of conveyor belt tracking theory is best illustrated through real-world examples and case studies. These instances not only showcase the challenges faced in various industries but also highlight the innovative solutions and techniques employed to resolve conveyor belt tracking issues. This section delves into a selection of such cases, demonstrating the versatility and effectiveness of conveyor belt tracking theory in ensuring operational efficiency and system reliability.
Real-World Examples of Conveyor Belt Tracking Issues and Resolutions
Mining Industry: At Goldstone Mining Co., frequent belt misalignments were common due to heavy loads and harsh conditions. The implementation of self-aligning idlers, as suggested by conveyor belt tracking theory, significantly reduced downtime and maintenance costs.
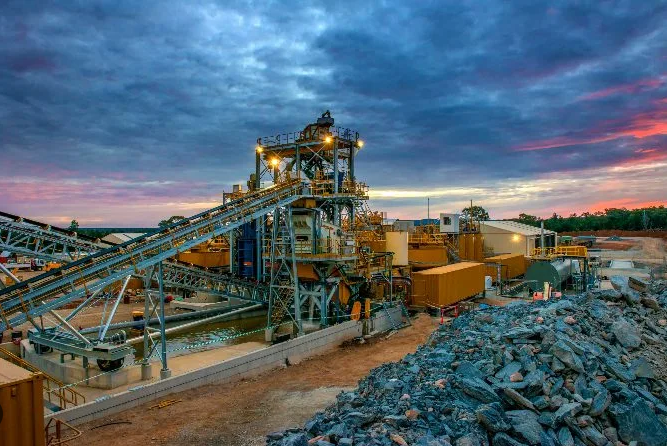
Food Processing Plant: Hygiene issues due to product spillage were a major problem at DeliFresh Foods. Installing belt tracking guides helped maintain alignment, improving cleanliness and reducing waste.
Logistics and Distribution Center: Pack & Ship Logistics Center experienced package damage due to conveyor belts drifting off track. They used laser alignment tools to achieve precise pulley and roller alignment, enhancing package handling and reducing damage rates.
Manufacturing Facility: SpeedTech Manufacturing, dealing with high-speed production lines, encountered belt slippage and tracking problems. They introduced pneumatic tensioning systems that ensured consistent belt tension, resolving the tracking issues effectively.
Recycling Plant: GreenCycle Recycling faced frequent belt misalignments caused by debris and material build-up. Implementing regular cleaning protocols and installing scrapers, as recommended by conveyor belt tracking theory, helped maintain proper alignment.
Airport Baggage Handling System: Skyline International Airport experienced misalignment in its baggage handling system, leading to delays and lost luggage. They implemented advanced digital monitoring systems to provide real-time tracking adjustments, improving system reliability.
Automotive Assembly Line: AutoBuild Corp. faced precision issues due to conveyor belt misalignment in their automotive assembly line. They used 3D modeling and simulation to optimize the conveyor layout and tracking adjustments, enhancing assembly precision.
Pharmaceutical Packaging Line: Precision Pharma needed to ensure exact alignment for delicate packaging operations. Automated adjustment mechanisms were installed, allowing for continuous and precise alignment adjustments.
Agricultural Processing Facility: AgriPro Industries experienced tracking issues due to seasonal temperature fluctuations. They used infrared inspection to identify and rectify temperature-related misalignments, stabilizing belt tracking.
Textile Manufacturing Plant: Fabric Innovations, facing varying fabric weights, had tracking challenges. The implementation of self-adjusting tracking rollers, guided by conveyor belt tracking theory, ensured consistent belt alignment across different production lines.
These enhanced descriptions provide a clearer view of how each company utilized specific solutions based on conveyor belt tracking theory to resolve their unique conveyor belt issues.
Case Studies Highlighting the Implementation of Conveyor Belt Tracking Theory
Case Study 1: Mining Sector Impact
- Company: Vista Mining Solutions
- Summary: A comprehensive study at Vista Mining Solutions demonstrated how the integration of conveyor belt tracking theory led to a 50% reduction in downtime and a significant increase in production efficiency. This improvement was attributed to the successful application of self-aligning idlers and enhanced monitoring systems.
Case Study 2: Food Industry Efficiency
- Company: PureFood Productions
- Summary: A case study at PureFood Productions highlighted the role of belt tracking guides in maintaining hygiene standards. The implementation resulted in a 30% reduction in product waste and improved regulatory compliance, crucial for their operations.
Case Study 3: Logistics and Handling
- Company: SwiftLog Distribution Services
- Summary: SwiftLog Distribution Services showcased the impact of laser alignment tools on package handling efficiency. This technology led to a notable decrease in package damage and an increase in throughput, optimizing their distribution processes.
Case Study 4: Automotive Manufacturing Precision
- Company: AutoTech Assembly
- Summary: An AutoTech Assembly case study illustrated the benefits of 3D modeling and simulation in conveyor system design. The advanced techniques led to a 20% improvement in assembly line precision, enhancing the overall manufacturing quality.
Case Study 5: Recycling Industry Maintenance
- Company: EcoRecycle Facilities
- Summary: At EcoRecycle Facilities, a case study focused on the effectiveness of regular cleaning and maintenance protocols, inspired by conveyor belt tracking theory, in maintaining conveyor belt alignment. This proactive approach resulted in a 40% reduction in maintenance costs and improved system reliability.
These real-world examples and case studies underscore the critical role of conveyor belt tracking theory in addressing and resolving alignment and tracking challenges across various industries. By applying the principles and techniques outlined in conveyor belt tracking theory, organizations can achieve significant improvements in operational efficiency, system reliability, and overall productivity.
FAQs about Conveyor Belt Tracking Theory
Conveyor belt tracking is governed by a set of fundamental rules designed to ensure the belt operates smoothly and efficiently. The first rule is to ensure that all components of the conveyor system, including rollers, pulleys, and the belt itself, are properly aligned and level. Misalignment is a primary cause of tracking issues, leading to uneven wear, potential damage to the belt, and operational inefficiencies.
The second rule emphasizes the importance of maintaining proper belt tension. Incorrect tension can cause the belt to slip, wander off track, or even result in premature wear and tear. The tension should be adjusted so that the belt is tight enough to prevent slippage but not so tight that it causes excessive wear or strain on the system.
The third rule involves regular inspections and maintenance. Conveyor systems should be regularly checked for signs of wear, misalignment, or other issues that could affect tracking. Prompt attention to any identified issues can prevent minor problems from escalating into major disruptions.
Lastly, the use of appropriate tracking technologies and devices, such as tracking rollers or guides, can assist in maintaining the belt’s path. These tools can provide additional support in keeping the belt aligned, especially in challenging operational conditions.
Conveyor tracking works by ensuring the belt remains in its intended path as it moves around the conveyor system. This is achieved through a combination of mechanical adjustments, precise component alignment, and the use of tracking devices. The key to effective tracking lies in the proper alignment of all conveyor components, including rollers, pulleys, and the belt itself.
Tracking rollers and guides play a significant role in this process. These devices are strategically placed along the conveyor frame to gently steer the belt back to its correct path if it begins to drift. This steering action is usually subtle to avoid damaging the belt or causing undue stress on the system.
In addition to mechanical adjustments, conveyor tracking can also involve monitoring systems that use sensors to detect the belt’s position and movement. These systems can provide real-time feedback, allowing for automatic adjustments to be made to keep the belt aligned. This advanced approach to tracking is particularly useful in complex or high-speed conveyor systems where manual adjustments may not be feasible.
The conveyor belt theory is a conceptual framework used to understand and analyze the movement and dynamics of conveyor belts in various applications. In principle, to track a conveyor belt, it moves toward the end it contacts first and is adjusted by cylindrical-conical pulleys.
At its core, the conveyor belt theory examines the relationships between belt tension, speed, load distribution, and alignment. It provides insights into how these factors interact to influence the belt’s behavior and efficiency. The theory also covers the impact of external forces, such as friction and gravitational pull, on the belt’s operation.
In a broader sense, the conveyor belt theory can also refer to meteorological models that describe large-scale atmospheric motions in terms of conveyor belts. This analogy is used to explain complex weather patterns, such as the movement of air masses and the development of weather fronts.
The belt tracking method refers to the techniques and procedures used to ensure a conveyor belt remains aligned and follows its intended path along the conveyor system. This method involves a combination of mechanical adjustments, regular inspections, and the use of tracking devices to maintain the belt’s position.
Mechanical adjustments are a critical aspect of the belt tracking method. This includes aligning rollers and pulleys to be perpendicular to the belt’s direction and ensuring the conveyor frame is level and square. Adjusting the tension of the belt is also crucial, as improper tension can lead to tracking issues.
Regular inspections are another key component of the belt tracking method. These inspections help identify potential issues, such as wear, misalignment, or damage, that could affect the belt’s tracking. Addressing these issues promptly can prevent minor problems from escalating and disrupting the conveyor’s operation.
Tracking devices, such as tracking rollers and guides, are also used as part of the belt tracking method. These devices provide additional support in maintaining the belt’s alignment, especially in challenging operational conditions or when the belt is under heavy loads.
The theory of conveyor systems revolves around the efficient and effective movement of materials from one point to another within a specified area, such as a manufacturing plant, warehouse, or distribution center. Conveyor systems are designed to handle a wide variety of materials, including packages, parts, raw materials, and finished products, facilitating seamless operations across numerous industries.
At its core, the theory emphasizes the optimization of material handling processes to minimize labor, reduce costs, and increase speed and efficiency. The system utilizes mechanical elements like belts, rollers, or chains that are driven by motors and guided by rollers and wheels to transport items. These elements are configured in various ways depending on the application’s requirements, including the type of materials, the distance to be covered, and the environmental conditions.
Conveyor systems are also integral to reducing human error and enhancing safety in workplaces. They can be tailored with sensors and automated controls to adjust speeds, detect load weights, and identify potential issues, thereby preventing accidents and ensuring continuous operation. In essence, the theory underpinning conveyor systems is about leveraging automation and mechanical engineering to improve productivity and operational efficiency in material handling tasks.
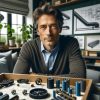
Jordan Smith, a seasoned professional with over 20 years of experience in the conveyor system industry. Jordan’s expertise lies in providing comprehensive solutions for conveyor rollers, belts, and accessories, catering to a wide range of industrial needs. From initial design and configuration to installation and meticulous troubleshooting, Jordan is adept at handling all aspects of conveyor system management. Whether you’re looking to upgrade your production line with efficient conveyor belts, require custom conveyor rollers for specific operations, or need expert advice on selecting the right conveyor accessories for your facility, Jordan is your reliable consultant. For any inquiries or assistance with conveyor system optimization, Jordan is available to share his wealth of knowledge and experience. Feel free to reach out at any time for professional guidance on all matters related to conveyor rollers, belts, and accessories.