Conveyor Belt Wear: Identifying Causes and Solutions
Conveyor belt wear is a critical issue that can significantly impact industrial operations. This wear, which occurs over time due to the continuous movement and load on the belts, can lead to decreased efficiency, increased downtime, and higher operational costs. Understanding the concept of conveyor belt wear is essential for industries that rely heavily on these systems for their daily operations. It involves recognizing the signs of wear, such as thinning, tearing, or misalignment, and understanding its implications. Properly addressing conveyor belt wear is crucial for maintaining the longevity and functionality of the conveyor system, ensuring smooth and uninterrupted industrial processes. This introduction sets the stage for a deeper exploration of the causes, effects, and mitigation strategies for conveyor belt wear.
Conveyor Belt Wear: Causes and Implications
Understanding the causes of conveyor belt wear is crucial for maintaining the efficiency and longevity of conveyor systems. This section delves into the various factors that contribute to conveyor belt wear, highlighting the importance of proper maintenance, usage, and environmental considerations.
Common Causes of Conveyor Belt Wear
Conveyor belt wear can be attributed to a range of factors, each affecting the belt’s integrity and operational efficiency. These include:
- Lack of Maintenance: Regular maintenance is key to prolonging the life of a conveyor belt. Neglecting routine checks and repairs can lead to significant wear and tear. This includes failing to clean the belt, not lubricating moving parts, and ignoring minor damages that can escalate.
- Improper Use: Using a conveyor belt in a manner that it’s not designed for can accelerate wear. This includes exceeding the recommended speed, load capacity, or using it for materials it’s not suited for.
- Environmental Factors: Exposure to harsh environmental conditions such as extreme temperatures, moisture, and corrosive substances can degrade the belt material over time, leading to increased wear.
Specific Factors Contributing to Wear and Tear
- Overloading: Consistently loading the conveyor belt beyond its capacity can strain the belt, leading to stretching, tearing, or breaking. Overloading not only wears the belt but also puts excessive pressure on the entire conveyor system.
- Underloading: Contrary to common belief, underloading can also contribute to conveyor belt wear. Running a conveyor system without adequate load can cause uneven belt wear and potential misalignment.
- Mechanical Issues: Problems with conveyor components like misaligned rollers, defective bearings, or improper belt tension can cause uneven wear patterns on the belt. Mechanical issues can lead to additional stress on certain parts of the belt, accelerating the wear process.
- Abrasive Materials: The type of material being transported plays a significant role in the wear rate. Materials that are abrasive can erode the surface of the belt, especially if the belt is not specifically designed for such conditions.
- Slippage: Conveyor belt slippage occurs when the belt loses grip on the pulleys, often due to improper tensioning. This not only leads to inefficient operation but also results in significant wear due to friction.
Conveyor belt wear is a multifaceted issue influenced by maintenance practices, usage patterns, environmental conditions, and mechanical factors. Understanding these causes is essential for taking preventive measures and ensuring the optimal performance and longevity of conveyor belts. Regular inspections, proper usage, and timely repairs are key strategies to mitigate conveyor belt wear and maintain the efficiency of conveyor systems.
Conveyor Belt Wear: Understanding Its Impact
In this section, we delve into the critical issue of conveyor belt wear and tear, a common challenge faced in various industries utilizing conveyor systems. Understanding the wear and tear of conveyor belts is essential for maintaining their efficiency and prolonging their lifespan. We will examine how regular operation can lead to wear and tear over time and analyze specific wear patterns and their implications for conveyor belt health.
The Dynamics of Conveyor Belt Wear and Tear
Conveyor belts are subjected to continuous use, often under harsh conditions. This constant operation can inevitably lead to various forms of wear and tear. Factors contributing to this wear include:
- Material Abrasiveness: The type of materials being transported can significantly affect the rate of wear. Materials with abrasive characteristics, like sand or gravel, can erode the surface of the belt more quickly.
- Load Weight: Heavier loads exert more pressure and friction on the belt, accelerating wear.
- Speed of Operation: Higher operational speeds can increase the friction between the belt and rollers or skirting, leading to faster deterioration.
- Environmental Factors: Exposure to extreme temperatures, moisture, chemicals, and UV light can weaken the belt material over time.
- Mechanical Issues: Misalignment, improper tensioning, and issues with rollers or pulleys can cause uneven wear.
Analyzing Conveyor Belt Wear Patterns
The pattern of wear on a conveyor belt can provide valuable insights into the health and functioning of the conveyor system. Common wear patterns include:
- Edge Wear: This occurs when the belt is misaligned and rubs against the conveyor structure. It can lead to fraying or tearing of the belt edges.
- Top Cover Wear: Caused by abrasive materials, this type of wear affects the upper layer of the belt, reducing its thickness and potentially exposing the carcass.
- Pulley Cover Wear: This happens when the belt interacts with the drive pulley. Excessive wear in this area can indicate issues with pulley alignment or hardness.
- Bottom Cover Wear: Often a result of friction against rollers or sliders, wear on the bottom cover can compromise the belt’s structural integrity.
- Cleat or Sidewall Wear: For belts with raised features, wear on these elements can reduce their effectiveness in material handling.
Understanding these wear patterns is crucial for diagnosing issues within the conveyor system and implementing timely maintenance or adjustments. Regular inspections and monitoring of conveyor belt wear patterns are vital for early detection of potential problems, allowing for corrective actions before significant damage or costly downtime occurs. By addressing wear and tear proactively, the lifespan of conveyor belts can be significantly extended, ensuring continuous and efficient operation of the conveyor system.
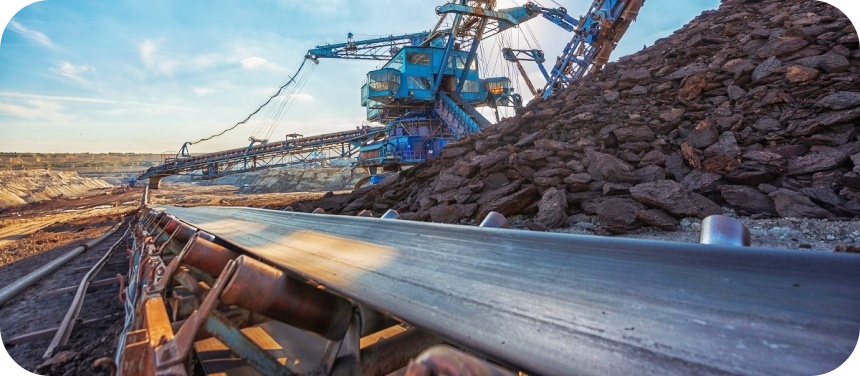
Enhancing Durability with Wear-Resistant Conveyor Belt Wear Solutions
Wear-resistant conveyor belts represent a significant advancement in combating conveyor belt wear. These belts are engineered using robust materials like high-grade rubber, reinforced with synthetic fibers or metals, designed to withstand harsh operational conditions. The incorporation of these durable materials extends the life of the conveyor belt, ensuring it can handle abrasive materials, heavy loads, and continuous operation without significant degradation.
The benefits of using wear-resistant conveyor belts in industrial applications are manifold:
- Extended Lifespan: The primary advantage of wear-resistant belts is their enhanced durability. These belts are less prone to cracking, fraying, and breaking, which means they need to be replaced less frequently than standard belts. This longevity is particularly beneficial in industries like mining, where belts are exposed to harsh materials.
- Reduced Maintenance Costs: With increased resistance to wear and tear, these belts require less maintenance. This reduction in upkeep not only saves money over time but also minimizes downtime for repairs, keeping production lines moving.
- Improved Efficiency: Wear-resistant belts maintain their integrity over longer periods, which means they are less likely to suffer from issues that could cause slowdowns or stoppages in production. Consistent performance is key to maintaining high levels of operational efficiency.
- Enhanced Safety: When conveyor belts fail, they can pose significant safety risks to workers. Wear-resistant belts reduce the likelihood of sudden failures, thereby enhancing the overall safety of the workplace.
- Versatility in Harsh Conditions: These belts are designed to perform in extreme environments, whether that involves exposure to high temperatures, corrosive chemicals, or abrasive materials. This versatility makes them suitable for a wide range of industrial applications, from metalworking to agricultural processing.
Wear-resistant conveyor belts offer a robust solution to the problem of conveyor belt wear. By investing in these advanced belts, industries can enjoy a range of benefits, from cost savings to improved safety, making them a wise choice for any operation where conveyor belts are a critical component.
Conveyor Belt Wear Strips and Maintenance for Prolonged Durability
In the context of conveyor belt wear, an essential aspect to consider is the use of conveyor belt wear strips and the implementation of regular maintenance practices. Conveyor belt wear strips are designed to protect the belts from excessive wear and tear, especially in high-contact areas. These strips are typically made from durable materials like UHMW polyethylene or reinforced rubber, which provide a protective layer between the belt and any surfaces or edges that might cause abrasion.
The role of these wear strips is crucial in extending the lifespan of conveyor belts. By absorbing the impact and friction that would otherwise be directly exerted on the belt, these strips prevent premature wear and safeguard the belt’s structural integrity. This is particularly important in applications where the conveyor belt is subject to constant or heavy loads, sharp materials, or rough handling.
To further minimize conveyor belt wear and extend its life, here are some essential maintenance tips:
- Regular Inspections: Conduct frequent visual inspections of the conveyor belt to identify any signs of wear, such as cracks, fraying, or misalignment. Early detection of these issues can prevent more severe damage.
- Proper Cleaning: Keep the conveyor belt clean from debris and materials that could cause wear or get lodged in the machinery. Use appropriate cleaning tools and methods that do not damage the belt.
- Lubrication and Alignment: Ensure that all moving parts of the conveyor system, including rollers and pulleys, are well-lubricated and properly aligned. Misalignment can cause uneven wear on the belt.
- Tension Adjustment: Regularly check and adjust the tension of the conveyor belt. Over-tensioning can lead to excessive wear, while under-tensioning can cause slippage and misalignment.
- Use of Wear Strips: Install and regularly inspect wear strips to ensure they are in good condition. Replace them as needed to maintain their protective function.
- Training of Personnel: Ensure that all personnel operating the conveyor system are trained in proper usage and maintenance procedures to avoid practices that could lead to increased wear.
By incorporating conveyor belt wear strips and adhering to these maintenance practices, businesses can significantly reduce the rate of wear and tear on their conveyor belts, ensuring longer operational life and greater efficiency in their conveyor systems.
Have questions about our conveyor belts? Reach out today!
Cost-Effective Solutions for Managing Conveyor Belt Wear
The issue of conveyor belt wear is not only a matter of operational efficiency but also of cost. Understanding and managing the cost implications of conveyor belt wear is crucial for businesses looking to maintain profitability while ensuring the smooth running of their conveyor systems.
Analyzing the Cost of Conveyor Belt Wear:
- Conveyor belt wear leads to increased maintenance and replacement costs. Frequent wear can cause unexpected downtime, leading to lost productivity and increased labor costs for repairs.
- The cost of replacing a worn-out belt includes not just the price of the new belt but also the time and labor involved in the installation process.
- Inefficient conveyor belts due to wear can lead to higher energy consumption, thus increasing operational costs.
Strategies for Cost-Effective Maintenance:
- Implement a regular maintenance schedule to identify and address issues before they lead to significant wear. Routine inspections can help spot early signs of wear and tear.
- Invest in quality conveyor belt wear strips and other protective components. While this may have an upfront cost, it can significantly reduce the rate of wear and extend the belt’s lifespan.
- Train staff on proper conveyor belt usage and maintenance practices. Misuse or neglect can accelerate wear and increase costs.
Cost-Effective Replacement Strategies:
- When replacement is necessary, consider the total cost of ownership rather than just the purchase price. More durable, higher-quality belts may have a higher initial cost but can offer savings in the long run due to less frequent replacements.
- Explore refurbished or quality used belts as a cost-effective alternative to new belts, especially for less critical or lower-load applications.
- Work with suppliers to find the most cost-effective solutions tailored to your specific needs. Some suppliers may offer discounts or better terms for regular customers or bulk purchases.
Effectively managing conveyor belt wear involves a balance between proactive maintenance and strategic replacement. By understanding the cost implications and employing cost-effective strategies, businesses can ensure their conveyor systems remain functional and efficient without incurring unnecessary expenses.
Conveyor Belt Wear: Examples and Definitions in Industry
In this section, we delve into real-world examples and essential definitions to deepen the understanding of conveyor belt wear across various industries.
Real-World Examples of Conveyor Belt Wear:
- Mining Industry: In mining operations, conveyor belts often transport abrasive materials like ores and rocks. Over time, these materials can cause significant wear, leading to tears and reductions in belt thickness, which may result in belt failure.
- Food Processing: Conveyor belts in food processing are subject to wear from constant contact with food items, cleaning chemicals, and water. This wear can manifest as surface nicks and cuts, compromising hygiene standards.
- Packaging and Distribution: High-speed conveyor systems used in packaging can experience wear due to frequent start-stop motions and varying weights of packages, leading to belt misalignment and surface wear.
- Airports: Baggage handling systems use conveyor belts that can wear down due to the heavy and irregular load of luggage, leading to surface abrasions and weakened belt joints.
Key Terms and Definitions Related to Conveyor Belt Wear:
- Abrasion Resistance: The ability of a conveyor belt material to resist surface wear caused by the rubbing or friction of materials being transported.
- Belt Tension: The degree of tightness or stretch of the conveyor belt. Improper belt tension can accelerate wear.
- Misalignment: Refers to the conveyor belt not running in its intended path, often leading to edge wear and increased friction.
- Tear Resistance: The ability of a conveyor belt to resist tearing due to sharp objects or heavy loads.
- Fatigue: The weakening of a conveyor belt material over time due to repeated stress or flexing, leading to cracks and wear.
- Elongation: The extent to which a conveyor belt stretches under load. Excessive elongation can indicate wear and the need for tension adjustments or replacement.
Understanding these examples and definitions is crucial for identifying and addressing conveyor belt wear in various industrial settings. It helps in selecting the right type of conveyor belt for specific applications and in implementing effective maintenance strategies to mitigate wear and prolong belt life.
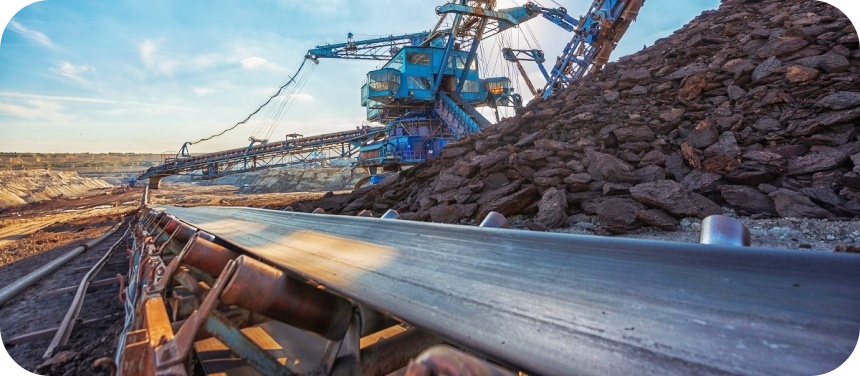
Selecting the Right Size and Type to Minimize Conveyor Belt Wear
The choice of the right conveyor belt size and type is pivotal in minimizing conveyor belt wear and ensuring optimal performance. This section provides guidance on making informed decisions tailored to specific industrial needs and operational conditions.
Determining the Appropriate Conveyor Belt Size:
- Measure Accurately: Accurate measurements of the conveyor system are crucial. The belt width should be compatible with the width of the conveyor, and the length should be sufficient to accommodate the system’s path and configurations.
- Load Considerations: The size of the belt must align with the load it will carry. Overloading a belt not designed for heavy loads can accelerate wear and lead to premature failure.
Selecting the Suitable Conveyor Belt Type:
- Material Type: The material of the conveyor belt should be chosen based on the type of goods it will transport. For abrasive materials, a belt with high abrasion resistance is necessary, whereas for delicate items, a softer surface may be required.
- Environmental Factors: Consider the operational environment. Belts used in outdoor or harsh environments should have weather-resistant properties, while those used in food processing may need to comply with hygiene standards.
Operational Speed and Frequency:
- Conveyor belts operating at high speeds or with frequent start-stop cycles may require specific materials and designs to withstand the additional stress and reduce wear.
Custom Features for Specific Needs:
- Some applications may benefit from custom features like reinforced edges, special coatings, or particular textures to enhance grip and reduce wear under specific conditions.
Consultation with Experts:
- Engaging with conveyor belt manufacturers or specialists can provide valuable insights. Their expertise can guide you in selecting a belt that not only fits your system but also offers the best resistance to wear for your specific application.
Choosing the right conveyor belt size and type is a critical step in reducing conveyor belt wear. It involves considering various factors such as load capacity, material type, environmental conditions, and operational demands. By carefully selecting a conveyor belt that aligns with these considerations, businesses can significantly extend the lifespan of their conveyor systems and enhance overall efficiency.
FAQs about Conveyor Belt Wear
Conveyor belt dressing is a product used to enhance the performance of conveyor belts in industrial applications. It is designed to improve grip and reduce slippage on the belt, thereby increasing efficiency. Belt dressing typically waterproofs and preserves the belt material, preventing deterioration and glazing. It can be applied to various types of belts, including flat, round, and v-style belts, and is suitable for both indoor and outdoor use.
The lifespan of a conveyor belt depends on several factors, including the type of material it’s made from, the conditions it operates in, and how well it’s maintained. Generally, a well-maintained conveyor belt can last anywhere from three to ten years. However, belts in harsher environments or under constant heavy use may have a shorter lifespan. Regular maintenance and proper usage are key to maximizing a conveyor belt’s longevity.
Common defects in conveyor belts include:
Wear and Tear: Regular use can lead to surface wear, reducing efficiency and increasing the risk of breakdown.
Misalignment: Improper alignment can cause uneven wear and potential operational issues.
Material Buildup: Accumulation of materials on the belt can affect its movement and efficiency.
Belt Slippage: Occurs when the belt loses grip, often due to improper tension or alignment.
Tears and Rips: Caused by sharp objects or heavy loads, tears and rips can significantly impair a belt’s functionality.
Conveyor belt rips can be caused by several factors:
Impact from Sharp Objects: Heavy or sharp materials dropping on the belt can cause rips or tears.
Overloading: Exceeding the belt’s load capacity can strain the belt, leading to rips.
Trapped Material: Objects getting trapped in the conveyor system can create tears as the belt moves.
Poor Maintenance: Lack of regular maintenance can lead to weakened areas in the belt, making it more susceptible to ripping.
Age and Wear: Older belts that have worn thin are more likely to rip under stress.
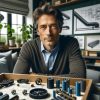
Jordan Smith, a seasoned professional with over 20 years of experience in the conveyor system industry. Jordan’s expertise lies in providing comprehensive solutions for conveyor rollers, belts, and accessories, catering to a wide range of industrial needs. From initial design and configuration to installation and meticulous troubleshooting, Jordan is adept at handling all aspects of conveyor system management. Whether you’re looking to upgrade your production line with efficient conveyor belts, require custom conveyor rollers for specific operations, or need expert advice on selecting the right conveyor accessories for your facility, Jordan is your reliable consultant. For any inquiries or assistance with conveyor system optimization, Jordan is available to share his wealth of knowledge and experience. Feel free to reach out at any time for professional guidance on all matters related to conveyor rollers, belts, and accessories.