Self-Aligning Idlers: Enhancing Conveyor System Efficiency
Conveyor systems are crucial in industries, moving materials between endpoints via a continuous conveyor belt. However, prolonged operation can lead to a common problem: belt misalignment.
The Widespread Issue: Conveyor Belt Deviation
Belt misalignment refers to the gradual deviation of a conveyor belt from its intended path or centerline during operation. This misalignment can be attributed to multiple factors, including uneven material distribution on the belt, imbalanced tension within the conveyor system, external impacts, or vibrations. The consequences of belt misalignment can be far-reaching and detrimental, encompassing: – Material buildup or spillage. – Premature wear and damage to the conveyor belt. – Equipment downtime and maintenance requirements. – Decreased production efficiency. This is where self-aligning idlers emerge as a valuable solution.
Overview of Self-Aligning Idlers
Self-Aligning Idlers are ingeniously designed mechanical components that serve the purpose of automatically correcting belt misalignment issues within conveyor systems. These idlers are usually positioned in the roller assemblies of the conveyor system to maintain belt centering and prevent deviation from the intended track. Here is an overview of the key characteristics and functions of self-aligning idlers:
- Automatic Correction: Self-Aligning Idlers possess the capability to detect any deviation of the conveyor belt from its desired path. They achieve this by constantly monitoring the belt’s position and making real-time adjustments to correct any misalignment, ensuring the belt stays on track.
- Reduction in Wear and Tear: By reducing friction between the conveyor belt and idlers, self-aligning idlers extend the conveyor belt’s lifespan, reducing maintenance costs.
- Enhanced Production Efficiency: The reduction in blockages and damage caused by misalignment leads to increased production efficiency and decreased downtime within the conveyor system.
- Safety in Operations: Keeping the conveyor belt on the correct path contributes to a safer operating environment by reducing the likelihood of accidents and incidents associated with belt misalignment.
The Crucial Role of Self-Aligning Idlers in Belt Alignment
Self-aligning idlers are indispensable and irreplaceable components within conveyor systems, ensuring the crucial maintenance of belt alignment. Their proactive approach not only enhances operational efficiency but also establishes them as a cost-effective solution for preventing conveyor belt damage. This cost-effectiveness, combined with their ability to preserve conveyor belt integrity, offers a long-term advantage to industries reliant on conveyor systems for material handling.
Preserving Belt Alignment
The fundamental function of self-aligning idlers is to actively monitor and rectify any deviations in the alignment of the conveyor belt. They accomplish this through continuous, real-time adjustments, ensuring that the belt maintains its central position and avoids straying from its intended trajectory. This proactive approach holds immense significance for several compelling reasons:
- Mitigating Material Spillage: Self-aligning idlers act as sentinels against material spillage that often occurs when a conveyor belt veers off its intended path. The reduction in spillage not only prevents material wastage but also enhances workplace safety by minimizing slip hazards and the need for extensive clean-up.
- Prolonged Belt Lifespan: Proper alignment, facilitated by self-aligning idlers, significantly diminishes the wear and tear experienced by the conveyor belt. Consequently, the belt’s operational lifespan is extended, yielding substantial cost savings by minimizing the frequency of belt replacement and maintenance.
- Heightened Operational Efficiency: Conveyor systems equipped with self-aligning idlers exhibit higher operational efficiency. The occurrence of belt blockages is minimized, resulting in reduced downtime and heightened productivity. This efficiency enhancement has a direct and positive impact on operational costs and profitability.
- Safety at the Forefront: Preserving belt alignment is paramount for personnel safety. A misaligned conveyor belt poses risks such as jamming, equipment damage, and accidents. Self-aligning idlers actively contribute to creating a safer working environment by ensuring proper belt alignment.
Safeguarding Against Conveyor Belt Damage
Self-aligning return idlers belt conveyor emerge as a robust shield for conveyor belts. Their continuous alignment action substantially reduces friction and stress that would otherwise lead to premature wear and damage. This safeguarding against belt damage translates into several cost-saving implications:
- Diminished Maintenance Expenditures: A conveyor system featuring properly aligned belts requires less maintenance. Fewer repairs and infrequent replacement of damaged belts result in substantial cost reductions over time.
- Extended Component Lifespan: Beyond extending the conveyor belt’s life, self-aligning idlers also contribute to prolonging the lifespan of other conveyor system components, including pulleys and rollers. This translates to diminished replacement costs for these critical components.
- Maximized Return on Investment (ROI): The initial investment made in self-aligning idlers proves to be a wise and profitable decision over time. It leads to decreased operational disruptions, lower maintenance expenses, and an extended equipment lifespan, ultimately maximizing the ROI for conveyor systems.
How is Self-Aligning Idlers Working?
Certainly, let’s delve into a more detailed explanation of how Self-Aligning Idlers work, with a focus on their general working principle and how they correct belt deviation through friction and automatic adjustment.
General Self Aligning Carrying Idler Working Principle
Self-Aligning Idlers are designed with a sophisticated mechanism that allows them to actively monitor and correct any deviations in the alignment of conveyor belts. They operate on the principle of proactive friction and automatic adjustment, ensuring that the conveyor belt remains centered and maintains its intended trajectory.
Correcting Belt Deviation through Friction
Self-Aligning Idlers are equipped with specially designed rollers that come into contact with the conveyor belt’s edges. These rollers create controlled friction when the belt starts to deviate from its central path. The frictional forces are essential for two primary reasons:
- Sensing Misalignment: As the conveyor belt begins to move off-center due to factors such as material distribution or tension imbalances, the self-aligning carrying idler rollers detect this deviation through the increased friction on one side. This friction acts as a sensory mechanism that alerts the idlers to the misalignment.
- Initiating Adjustment: Once the misalignment is detected, the self-aligning idlers initiate automatic adjustments. The increased friction on one side prompts the idlers to exert pressure, gently nudging the belt back towards its intended path. This friction-driven correction mechanism ensures that the conveyor belt maintains proper alignment.
Self Aligning Carrying Idler Automatic Adjustment
The automatic adjustment process of self-aligning idlers is a remarkable feature of their design. It involves the following steps:
- Monitoring: Self aligning return idler continuously monitor the position of the conveyor belt as it moves. They assess whether the belt is deviating to the left or right from its central path.
- Detection: When a deviation is detected, the self-aligning carrying idlers on the side with increased friction come into play. They recognize the need for correction based on this frictional difference.
- Application of Force: The idlers apply a controlled force to the side of the belt experiencing increased friction. This force is strategically adjusted to realign the belt without causing damage or excessive wear.
- Realignment: The applied force gently guides the conveyor belt back to its correct trajectory. The idlers maintain a delicate balance, ensuring that the belt remains centered without excessive tension or strain. By consistently implementing this friction-based and automatic adjustment process, self-aligning idlers play an instrumental role in maintaining belt alignment throughout the conveyor system’s operation.
Types and Designs of Self-Aligning Idlers
Overview of Different Types
Self-Aligning Idlers come in various types, each designed to serve specific functions within conveyor systems. Two prominent types are:
- Self-Aligning Return Idler The Self-Aligning Return Idler is primarily responsible for aligning the return side of the conveyor belt. It is positioned on the underside of the conveyor system, near the tail pulley. This type of idler is crucial for ensuring that the belt returns smoothly and maintains proper alignment after completing its circuit.
- Self-Aligning Carrying Idler In contrast, the Self-Aligning Carrying Idler aligns the load-carrying side of the conveyor belt. Positioned along this side, it helps maintain belt alignment while transporting materials from one point to another. This idler type is particularly vital for preventing misalignment issues during the material transportation process.
Specific Designs and Functionalities
Self-Aligning Return Idler Design: Self-Aligning Return Idlers typically feature a unique design with offset rollers. These offset rollers, often set at an angle to the direction of belt travel, come into contact with the return side of the conveyor belt. This design allows them to sense any misalignment and initiate corrective action. Functionality: When a deviation in belt alignment is detected, the offset rollers apply pressure to the return side of the belt experiencing increased friction. This pressure gently nudges the belt back towards its central path, effectively realigning it. Self-Aligning Return Idlers are designed to operate with minimal friction, ensuring that they correct misalignment without causing excessive wear on the belt. Self-Aligning Carrying Idler Design: Self-Aligning Carrying Idlers are characterized by their distinctive design, which includes a series of idler rollers with a central pivot point. These idlers are strategically positioned along the carrying side of the conveyor belt. They are designed to pivot and move independently in response to belt misalignment. Functionality: When the conveyor belt deviates from its intended path on the carrying side, the Self-Aligning Carrying Idlers pivot in the direction of the misalignment. This movement exerts corrective force, guiding the belt back to its central position. These idlers are engineered to operate smoothly and respond swiftly to deviations, minimizing the risk of belt damage.
Structure and Material Composition
Self-Aligning Idlers are typically constructed using durable materials to withstand the rigors of conveyor system operation. Common materials include high-quality steel for the idler frame, while the rollers are often made of robust materials such as rubber or polyurethane to provide an optimal balance of friction and wear resistance.
Advantages and Applications of Self-Aligning Idlers
The Benefits of Self-aligning Idlers
- Enhanced Belt AlignmentSelf-Aligning Idlers excel in maintaining precise belt alignment within conveyor systems. Their ability to actively correct misalignment issues ensures that conveyor belts remain centered, reducing the risk of costly problems such as material spillage and belt damage. This enhanced alignment directly contributes to increased operational efficiency.
- Cost SavingsOne of the primary advantages of self-aligning idlers lies in their cost-effectiveness. By preventing misalignment-related issues, these idlers reduce maintenance expenses, extend the lifespan of conveyor components, and minimize downtime. This translates into significant cost savings for industries that rely on conveyor systems for material handling.
- Improved Safety
Proper belt alignment, facilitated by self-aligning idlers, enhances workplace safety. Reduced material spillage and minimized risk of accidents due to belt misalignment create a safer environment for personnel working in proximity to conveyor systems. - Longevity of Conveyor ComponentsSelf-Aligning Idlers play a pivotal role in preserving the integrity of conveyor belts and other components. Their ability to minimize friction and wear ensures the longevity of belts, pulleys, and rollers, reducing the frequency of component replacements and associated costs.
- High EfficiencyEfficient operation is a hallmark of conveyor systems equipped with self-aligning idlers. The reduction in material spillage and blockages, coupled with minimized downtime, leads to heightened production efficiency. Industries can achieve higher throughput and meet production targets with ease.
Self-aligning Idlers Applicate in Various Industries
- Mining IndustryIn the mining industry, where conveyor systems are essential for transporting ores, minerals, and bulk materials, self-aligning idlers are indispensable. They prevent misalignment-induced material spillage, reducing cleanup efforts and enhancing safety in mining operations.
- Steel MillsSteel mills rely on conveyor systems to transport heavy and hot materials within their facilities. Self-aligning idlers play a crucial role in maintaining belt alignment under challenging conditions, contributing to uninterrupted production and minimizing equipment wear.
- Cement PlantsCement plants use conveyor systems for the bulk handling of materials like cement clinker and raw materials. Self-aligning idlers ensure that conveyor belts remain aligned during the transportation of these materials, preventing spillage and minimizing maintenance needs.
- Bulk Material HandlingIndustries involved in bulk material handling equipment, such as ports and terminals, benefit significantly from self-aligning idlers. They enhance the efficiency of loading and unloading processes by preventing belt misalignment, which can lead to material spillage and delays.
- Recycling FacilitiesRecycling facilities rely on conveyor systems to sort and transport recyclable materials. Self-aligning idlers contribute to the efficient operation of these systems by preventing material jams and optimizing the flow of recyclables.
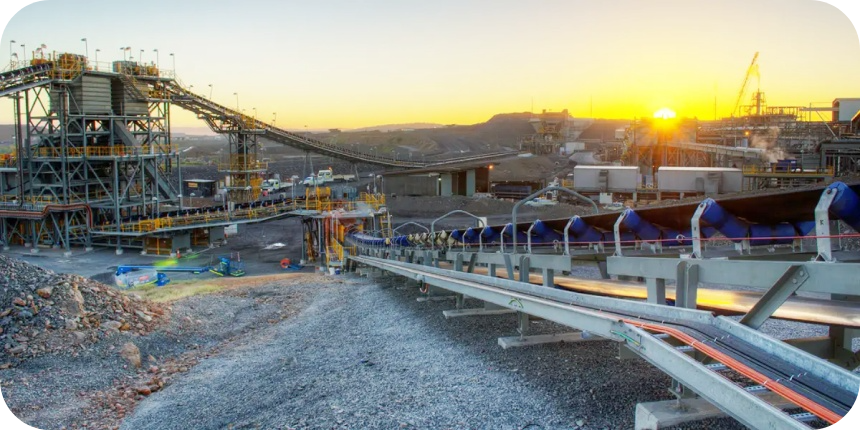
How to Choose the Right Self-Aligning Idler
Selecting the appropriate type of Self-Aligning Idler is crucial to ensure the efficient and reliable operation of your conveyor system. Here’s a comprehensive guide to help you make the right choice.
Identify Conveyor System Requirements
Begin by thoroughly understanding the specific requirements of your conveyor system. Consider factors such as:
- Belt WidthDetermine the width of your conveyor belt. Self-Aligning Idlers come in various sizes, and selecting the right size that matches the belt width is essential for proper alignment.
- Load CapacityEvaluate the maximum load capacity your conveyor system will handle. Different Self-Aligning Idlers are designed to support varying loads. Choose idlers that can comfortably accommodate the heaviest loads expected in your application.
- Conveyor SpeedTake into account the speed at which your conveyor system operates. Some Self-Aligning Idlers are better suited for high-speed systems, while others are designed for slower speeds. Select idlers that can handle the specific speed requirements of your conveyor.
- Material TypeConsider the type of material being transported on the conveyor. Certain materials may be abrasive or corrosive, necessitating the use of idlers with appropriate materials and coatings to withstand these conditions.
- Environmental ConditionsEvaluate the environmental conditions in which the conveyor system operates. Factors such as temperature extremes, moisture levels, and exposure to chemicals can impact the choice of Self-Aligning Idlers. Ensure that the idlers selected are suitable for the prevailing environmental conditions.
Choose the Type of Self-Aligning Idler
There are two primary types of Self-Aligning Idlers: Self-Aligning Return Idlers and Self-Aligning Carrying Idlers. Choose the type that aligns with the specific needs of your conveyor system. Self-Aligning Return Idlers: Ideal for aligning the return side of the conveyor belt. They are positioned near the tail pulley belt conveyor and ensure that the belt returns smoothly. Self-Aligning Carrying Idlers: Suitable for aligning the load-carrying side of the conveyor belt. They are strategically positioned along the carrying side and contribute to maintaining belt alignment during material transport.
Consider Additional Features
Depending on your application, you may need Self-Aligning Idlers with specific features or options. These can include: ealed Bearings: If your conveyor operates in dusty or wet environments, sealed bearings can protect against contamination and prolong bearing life. Adjustable Frames: Some Self-Aligning Idlers offer adjustability, allowing for fine-tuning of alignment settings as needed. Impact Beds: In applications where heavy impact loads are expected, consider Self-Aligning Idlers with built-in impact beds to reduce damage to the belt and idlers.
Installation and Maintenance of Self-Aligning Idlers
Proper installation of Self-Aligning Idlers is crucial for their effective performance. Here are some essential tips:
- Positioning: Ensure that Self-Aligning Return Idlers are placed near the tail pulley on the return side of the conveyor, while Self-Aligning Carrying Idlers should be strategically positioned along the carrying side. Correct placement is key to their functionality.
- Alignment: During installation, carefully align the idlers with the conveyor frame to guarantee that they are parallel to the belt. Misalignment during installation can hinder their ability to correct misalignment during operation.
- Secure Mounting: Use appropriate mounting hardware to securely fasten the idlers to the conveyor frame. Loose or improperly mounted idlers can lead to misalignment issues.
- Tension Adjustment: Ensure that the idlers are properly tensioned. The tension should be adjusted according to the manufacturer’s recommendations to avoid over-tensioning or under-tensioning, which can affect their performance.
- Regular Inspection: Conduct a visual inspection after installation to verify that the idlers are aligned correctly, and there are no obstructions or interferences that may hinder their movement.
In conclusion, proper installation, regular maintenance, and selecting the right supplier are key aspects of ensuring the optimal performance and longevity of Self-Aligning Idlers in a conveyor system. Gram provides excellent customer support can assist with installation guidance, maintenance recommendations, and addressing any issues that may arise. We also offer the warranty offered on the idlers.
Click here to add your own text
CONTACT US
Let us help you find a better solution!
FQAs about Self-aligning Idlers
What is the difference between idler and tensioner?
In heavy industries like mining, idlers and tensioners play crucial roles in the operation of conveyor systems. Idlers are components that support the conveyor belt and its load, ensuring smooth and efficient material transport. They are typically mounted on a frame and positioned at intervals along the conveyor’s length to maintain the belt’s shape and alignment. Tensioners, on the other hand, are devices used to maintain the proper tension on the conveyor belt. Proper tension is critical to prevent slippage, reduce wear, and ensure efficient power transmission. While idlers mainly support the belt and load, tensioners adjust the belt’s tension dynamically or statically to compensate for stretching and operational conditions.
What is the difference between carrying idler and impact idler?
Carrying idlers and impact idlers serve distinct functions in conveyor systems used in heavy industries like mining. Carrying idlers are designed to support the conveyor belt and the materials being transported along the length of the conveyor. They are typically spaced at regular intervals to maintain the belt’s alignment and shape under normal operating conditions. Impact idlers, however, are specifically designed to absorb and reduce the impact of heavy, falling materials. They are usually placed at loading points where the belt is subjected to high impact forces. Impact idlers are equipped with shock-absorbing materials such as rubber rings or pads to protect the belt from damage and extend its lifespan.
What is the purpose of the idler wheel?
In heavy industrial applications like mining, the idler wheel serves a critical role in supporting and guiding conveyor belts. Its primary purpose is to reduce friction and wear on the conveyor belt as it moves, ensuring smooth and efficient material transport. The idler wheel helps maintain the belt’s alignment and shape, preventing it from sagging or misaligning under the weight of the transported materials. This is particularly important in mining operations, where conveyor belts are often subjected to heavy loads and harsh conditions. By providing consistent support and reducing wear, idler wheels help extend the operational life of the conveyor system and improve overall efficiency.
What is the difference between idle and idler?
In the context of heavy industries like mining, “idle” and “idler” have distinct meanings. “Idle” refers to a state of inactivity or not in use, such as machinery that is not operating or an employee who is not currently working. In contrast, an “idler” refers to a component within a conveyor system. An idler is a rotating device that supports and guides the conveyor belt, ensuring its proper alignment and movement. Idlers are critical for reducing friction and wear on the belt, contributing to the efficient transport of materials in mining operations. Thus, while “idle” describes a state of inactivity, “idler” is a functional part of a conveyor system.
Do idler pulleys rotate?
Yes, idler pulleys do rotate. In the context of heavy industries like mining, idler pulleys are essential components in conveyor systems and other machinery that use belts. An idler pulley is mounted on a fixed axis and is designed to guide or tension the conveyor belt. As the conveyor belt moves, the idler pulley rotates freely, reducing friction and wear on the belt. This rotation helps to maintain proper belt alignment and tension, ensuring efficient and reliable operation of the conveyor system. Idler pulleys play a crucial role in extending the life of the belt and reducing maintenance costs in demanding industrial environments.
What are the disadvantages of self aligning bearings?
Self-aligning bearings, while useful in accommodating shaft misalignment in heavy industries like mining, have several disadvantages. Firstly, they generally have lower load-carrying capacity compared to other types of bearings due to their design. This can be a drawback in mining applications where heavy loads are common. Secondly, self-aligning bearings can be more expensive than standard bearings due to their complex construction. Thirdly, they have higher frictional losses, which can lead to increased operating temperatures and reduced efficiency. Additionally, they may require more frequent maintenance and lubrication to ensure optimal performance. Lastly, self-aligning bearings might not handle severe misalignment as effectively as other specialized bearings, leading to potential premature failure in harsh mining conditions.
How do l know if l need an alignment or my bearings are bad?
In heavy industries like mining, determining whether you need an alignment or if your bearings are bad involves observing several signs. If your machinery exhibits unusual vibrations, excessive noise, or uneven wear on the bearings or associated components, it might indicate misalignment. Misaligned equipment often shows signs of rapid or uneven belt wear, loose bolts, or visible misalignment of parts. On the other hand, bad bearings typically manifest through grinding or squealing noises, increased operating temperatures, and visible damage such as cracks or pitting on the bearing surfaces. Regular maintenance checks, including vibration analysis and visual inspections, can help identify the root cause. If unsure, professional diagnostics using specialized equipment can accurately determine whether alignment or bearing replacement is necessary.
What bearings are best for misalignment?
For heavy industrial applications such as mining, spherical roller bearings and self-aligning ball bearings are the best choices for handling misalignment. Spherical roller bearings are designed to accommodate heavy loads and can tolerate moderate misalignment between the shaft and the housing. Their robust construction makes them ideal for harsh environments where shocks and vibrations are common. Self-aligning ball bearings, on the other hand, have a double-row design with an inner ring and ball assembly that can adjust to misalignment, providing smooth operation even when the shaft is not perfectly aligned. These bearings are particularly useful in applications where frequent shaft deflections occur or where the mounting errors cannot be completely avoided.
Which bearing generally used is to avoid chances of misalignment?
In heavy industries like mining, self-aligning ball bearings are commonly used to avoid misalignment issues. These bearings have two rows of balls and a common spherical raceway in the outer ring, which allows the inner ring and ball assembly to rotate freely and accommodate shaft misalignment. This design helps in maintaining smooth operation and reduces the risk of bearing failure due to alignment errors. Additionally, spherical roller bearings are also widely used for their ability to handle heavy loads and compensate for angular misalignment. Both types of bearings are preferred in mining applications where machinery is subjected to significant misalignment and load variations, ensuring reliability and longevity.
What happens when a bearing is misaligned?
When a bearing is misaligned in heavy industrial applications such as mining, it can lead to several detrimental effects. Misalignment causes uneven load distribution across the bearing, leading to increased stress and premature wear on the bearing components. This can result in higher operating temperatures, increased friction, and reduced efficiency. Over time, misaligned bearings can suffer from surface damage like spalling, pitting, and cracking, ultimately leading to bearing failure. Additionally, misalignment can cause excessive vibration and noise, potentially damaging adjacent machinery components and increasing maintenance costs. To prevent these issues, it is crucial to regularly check and correct any misalignment in bearing installations.
Which bearing Cannot tolerate misalignment?
High-precision bearings, such as angular contact ball bearings and cylindrical roller bearings, generally cannot tolerate misalignment. These bearings are designed for applications requiring precise alignment and high load-carrying capacity. In heavy industries like mining, where equipment is subjected to harsh conditions and varying loads, these bearings can quickly fail if misalignment occurs. The tight tolerances and specific load distribution of high-precision bearings mean even minor misalignments can cause excessive stress, leading to rapid wear, overheating, and ultimately, bearing failure. Therefore, they are typically used in applications where alignment can be strictly controlled and maintained.
What is meant by self aligning torque?
Self-aligning torque refers to the torque that helps a wheel or a bearing return to its original, aligned position after being subjected to a misalignment force. In heavy industries like mining, this concept is crucial for ensuring stability and proper functioning of rotating machinery. Self-aligning torque is generated by the interaction between the rolling elements and the raceways in a self-aligning bearing, which allows the bearing to accommodate misalignment and return to its optimal position. This torque helps in reducing wear and tear on the bearing components, maintaining efficient operation, and extending the lifespan of the machinery, which is critical in demanding mining environments.
Which type of coupling is not allowed any misalignment when installed?
In heavy industries such as mining, rigid couplings are types of couplings that do not allow any misalignment when installed. Rigid couplings are designed to precisely connect two shafts, ensuring that there is no relative movement between them. This type of coupling requires perfect alignment during installation because it cannot accommodate any angular, parallel, or axial misalignment. Failure to properly align rigid couplings can lead to excessive stress on the shafts and bearings, resulting in premature wear and potential failure of the connected equipment. Given the demanding conditions in mining operations, achieving and maintaining precise alignment with rigid couplings can be challenging, but it is essential for the reliability and longevity of the machinery.
What are the differences between aligning torque and self aligning torque?
Aligning torque and self-aligning torque are concepts used to describe different types of corrective forces in mechanical systems. Aligning torque refers to the force required to bring misaligned components, such as shafts or bearings, back into proper alignment. This torque is typically applied manually or through mechanical adjustment. In contrast, self-aligning torque is an inherent property of certain mechanical components, such as self-aligning bearings, that allows them to automatically correct misalignment. In heavy industries like mining, self-aligning torque is critical because it helps maintain the stability and performance of machinery under harsh conditions, reducing the need for frequent manual adjustments and ensuring continuous, efficient operation.
What are self aligning hinges?
Self-aligning hinges are specialized hinges designed to automatically adjust and correct minor misalignments between connected components. In heavy industries like mining, self-aligning hinges are particularly useful for ensuring the proper alignment of doors, hatches, and other access panels that are frequently used and subjected to harsh conditions. These hinges typically feature a flexible or pivoting mechanism that allows them to accommodate slight misalignments, ensuring smooth operation and reducing wear and tear on the connected parts. The use of self-aligning hinges in mining equipment can enhance operational efficiency, minimize maintenance requirements, and extend the lifespan of critical access components.
What are the advantages of self aligning bearings?
Self-aligning bearings offer several advantages in heavy industries like mining. Firstly, they can accommodate misalignment between the shaft and housing, reducing the risk of premature bearing failure due to misalignment. This flexibility is particularly beneficial in mining operations, where equipment is often subjected to harsh conditions and variable loads. Secondly, self-aligning bearings can absorb shocks and vibrations, enhancing the durability and reliability of the machinery. They also reduce maintenance requirements, as their design minimizes the need for frequent realignment. Additionally, self-aligning bearings help maintain efficient operation by reducing friction and wear, contributing to longer service life and lower operational costs.
How do self aligning bearings work?
Self-aligning bearings work by utilizing a design that allows the bearing to adjust to misalignment between the shaft and the housing. They typically feature two rows of balls and a common spherical raceway in the outer ring. This spherical raceway allows the inner ring and balls to tilt relative to the outer ring, accommodating angular misalignment. In heavy industries like mining, where machinery is subjected to dynamic and harsh conditions, self-aligning bearings ensure continuous and efficient operation by maintaining alignment automatically. This reduces stress on the bearing components, minimizes friction and wear, and extends the bearing’s lifespan, ultimately contributing to the reliability and efficiency of mining equipment.
Which type of coupling requires the most critical alignment?
Gear couplings require the most critical alignment among the various types of couplings used in heavy industries like mining. Gear couplings consist of two hubs with external gears and a sleeve with internal gears, which mesh together to transmit torque. Proper alignment is crucial for gear couplings because even minor misalignment can lead to increased wear, excessive vibration, and potential failure of the coupling and connected machinery. In mining applications, where equipment is subjected to significant loads and harsh conditions, maintaining precise alignment of gear couplings is essential to ensure reliable and efficient operation, as well as to minimize maintenance and downtime.
Why is it important to align coupling halves?
Aligning coupling halves is crucial in heavy industries like mining to ensure the efficient and reliable operation of connected machinery. Proper alignment minimizes the stress and wear on the coupling, shafts, and bearings, reducing the risk of premature failure. Misaligned couplings can lead to excessive vibrations, noise, and increased power consumption, negatively impacting the performance and lifespan of the equipment. In mining, where machinery operates under heavy loads and harsh conditions, maintaining precise alignment of coupling halves is essential to prevent downtime, reduce maintenance costs, and ensure the safety and productivity of the operations. Proper alignment also improves the overall efficiency and energy consumption of the machinery.
Can alignment fix itself?
In heavy industries such as mining, alignment issues generally do not fix themselves and require manual or mechanical intervention to correct. Misalignment in machinery can be caused by various factors, including wear and tear, heavy loads, and environmental conditions. Once misalignment occurs, it typically worsens over time if not addressed, leading to increased stress on components, higher friction, and potential failure. While certain components, like self-aligning bearings, can compensate for minor misalignments to maintain operational efficiency, the overall system alignment needs to be regularly checked and adjusted by maintenance personnel to ensure optimal performance and prevent costly downtime.
Why does alignment go out?
Alignment issues in heavy mining equipment can occur due to several reasons. Constant exposure to heavy loads and vibrations is a primary cause, as these forces can gradually shift components out of alignment. Environmental factors, such as extreme temperatures, moisture, and dust, can also contribute to alignment problems by causing material expansion, contraction, and corrosion. Wear and tear over time is another significant factor, as the continuous operation of machinery can lead to the degradation of parts, resulting in misalignment. Additionally, improper installation or maintenance practices can initially cause or exacerbate alignment issues, highlighting the importance of regular inspections and professional servicing in maintaining proper alignment.
What is a self aligning coupler?
A self-aligning coupler is a mechanical device used to connect two shafts in heavy industrial applications, such as mining, while allowing for minor misalignments. This type of coupler can automatically adjust to slight angular, parallel, or axial misalignments, ensuring efficient power transmission and reducing stress on connected components. Self-aligning couplers are particularly useful in mining operations where machinery is subjected to heavy loads, vibrations, and harsh environmental conditions. By accommodating misalignment, these couplers help prevent wear and tear on shafts and bearings, enhance the longevity of the equipment, and reduce maintenance needs, ultimately improving the reliability and efficiency of mining machinery.