Fabric Conveyor Belts
Among the various types of conveyor belts available, fabric conveyor belts have carved a niche for themselves, particularly in handling heavy-duty and abrasive materials. Known for their durability and resilience, these belts are designed to withstand the rigors of transporting rough and rugged materials like ores, rocks, and other abrasive substances. Fabric belt conveyors are a testament to engineering innovation, offering an effective solution for industries that demand robust material handling capabilities.
The uniqueness of fabric conveyor belts lies in their construction. Made from layers of specially treated synthetic fabrics, these belts offer a perfect blend of flexibility and strength. The use of materials like polyester and polyamide in the warp and weft of the belt respectively, contributes to their high tensile strength and exceptional troughing characteristics. This design not only ensures the belt’s longevity but also its capability to handle the stress of heavy loads and abrasive materials without significant wear and tear.
What is a Fabric Conveyor Belt?
Fabric belt conveyors are essential equipment in modern industry, using strong, flexible belts made of bonded or stitched synthetic fiber layers to efficiently transport goods.
Basic structure and specifications
The core of a fabric belt conveyor design lies in its layered construction. These layers typically include a top cover, a carcass made of fabric layers, and a bottom cover. The carcass is the main strength and load-bearing portion of the conveyor belt and is made of multiple layers of fabric, such as polyester and nylon, which enhance the strength and durability of the conveyor belt. Fabric conveyor belt specifications typically outline the dimensions of the conveyor belt, its material composition, tensile strength, and other key parameters that determine its suitability for a variety of applications.
Types of Fibers Used
The fiber selection for fabric conveyor belts is critical to their performance. Polyester and polyamide are the most commonly used fibers in these conveyor belts. Polyester has high strength, low stretch, and excellent water and mildew resistance, making it an ideal choice for fabric warp yarns (the longitudinal yarns in the fabric). Polyamides are known for their high impact and abrasion resistance and are typically used for weft yarns (the transverse yarns). The combination of these fibers in fabric conveyor belts ensures a balance of strength, flexibility, and durability for a wide range of industrial applications.
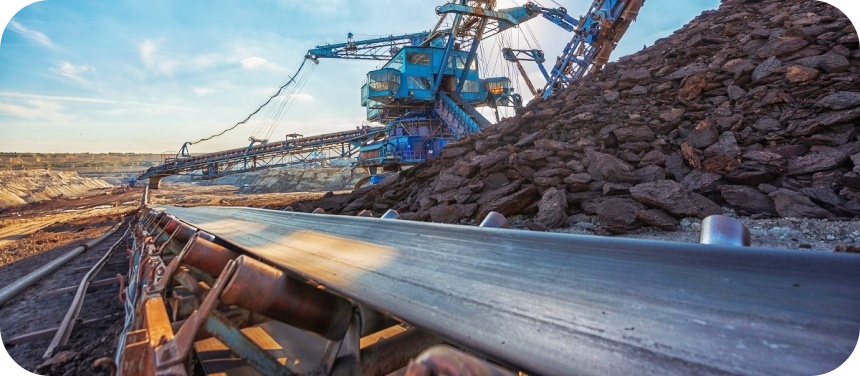
Advantages of Fabric Conveyor Belts
Cost-Effectiveness
One of the primary advantages of fabric belt conveyor is their cost-effectiveness, especially for shorter distances and lower capacities. When the transportation needs do not involve extremely long distances or excessively heavy loads, fabric conveyor belts provide an efficient and economical solution. The initial cost, installation, maintenance, and repair expenses are generally lower for fabric belts compared to heavier-duty options like steel cord conveyor belts. This cost-effectiveness makes fabric conveyor belts a practical choice for many businesses looking to optimize their operations while controlling expenses.
High Tensile Strength-to-Weight Ratio and Flexibility
Fabric conveyor belts feature a high tensile strength-to-weight ratio, crucial for their flexibility and performance, offering strong yet lightweight efficiency in conveyor systems. The flexibility of fabric conveyor belts allows for easier handling, installation, and adaptation to different conveyor configurations and pathways. This flexibility also contributes to the belt’s ability to form troughs easily, enhancing its capacity to carry materials securely.
Superior Troughing Properties and Resistance to Impact and Chemicals
The troughing properties of fabric conveyor belts are superior due to their flexible yet strong structure. This ability to form a trough shape effectively contains and transports a variety of materials, minimizing spillage and increasing the efficiency of material transfer. Additionally, the structure and materials used in fabric conveyor belts provide significant resistance to impact and chemicals.
The fabric belt conveyor specification often includes details on the belt’s ability to withstand different types of environmental stressors, such as exposure to harsh chemicals or abrasive materials. This resistance is crucial in industries where conveyor belts are exposed to challenging conditions.
Comparison with Steel Cord Conveyor Belts
Feature | Fabric Conveyor Belts | Steel Cord Conveyor Belts |
---|---|---|
Suitable Applications | Better suited for shorter distances and less intensive load-bearing | Ideal for long-distance, high-load conveying tasks |
Construction | Multiple layers of fabric materials | Incorporate steel cables running lengthwise |
Tensile Strength | Moderate tensile strength | Very high tensile strength |
Elongation | Higher elongation than steel cord belts | Low elongation due to steel cables |
Flexibility | Higher flexibility, can easily adapt to different conveyor paths | Less flexible compared to fabric belts |
Repair and Splicing | Easier to splice and repair | More challenging and time-consuming to splice and repair |
Load-Bearing Capacity | Suitable for less intensive load-bearing applications | Designed to handle extremely heavy loads |
Practicality for Industries | More practical for industries that don’t require heavy-duty conveying | Preferred in industries with heavy-duty, long-distance needs |
Key Features of Fabric Conveyor Belts
Cover Grades
Fabric conveyor belts are available in different resistance types to suit the challenging conditions they might encounter. These include:
Wear-resistant: Essential for belts handling abrasive materials. These belts can withstand constant wear and tear, prolonging their lifespan. Heat-resistant: Designed for transporting materials at high temperatures, such as in foundries or steel mills. These belts can resist degradation at elevated temperatures. Flame-resistant: Crucial for applications in environments where there’s a risk of fire or explosion. These belts are treated to be self-extinguishing.
The specification of resistance types in the fabric conveyor belt specification allows users to select a belt that best fits their operational environment, ensuring safety and longevity of the belt.
Reinforcement Properties
Reinforcement is a key feature of fabric belt conveyors, involving the use of fabrics like polyester, nylon, or a blend of both to provide strength and stability. The reinforcement properties include:
Low Elongation: This ensures that the belt stretches minimally under load, maintaining consistent length and tension in operation.
Good Adhesion to Rubber: The fabric layers effectively bond with the rubber or synthetic cover, providing integral strength and preventing layers from separating under stress.
The reinforcement properties ensure that the belt can withstand the mechanical stresses of load-bearing and motion, while maintaining its structural integrity over time.
Products of Fabric Conveyor Belt
steel cord rubber conveyor belts Textile Conveyor Belts
It is perfect for elevated tensile, long distance and large rows. Fabric conveyor belts are also called textile conveyor belts.
How to Choose the Right Belt for Your Application?
Choosing the right fabric conveyor belt is vital for operational efficiency, safety, and cost-effectiveness, requiring knowledge of specifications, manufacturers’ roles, and available fabric types.
Assessing Operational Requirements
Load and Material Type: Consider the nature of the materials being transported (e.g., abrasive, corrosive, heavy). This will influence the choice of belt material and design. Conveying Distance and Speed: Shorter conveying systems may be well-served by standard fabric conveyor belts, while longer or faster systems may require specialized belts. Environmental Condition: Factors like temperature, exposure to chemicals, and moisture can affect belt performance.
Matching Belt Properties to Industry Needs
Mining Industry: Belts used in mining need to be robust, abrasion-resistant, and capable of handling heavy loads. Fabric conveyor belts with reinforced materials and specialized cover grades are often suitable.
Construction Industry: Belts in construction may require flexibility and resistance to wear and tear from rough materials.
Food Industry: Belts here need to comply with hygiene standards, necessitating easy-to-clean and possibly anti-microbial materials.
Each industry has unique demands that must be matched with the right conveyor belt fabric types to ensure optimal performance and safety.
Understanding Fabric Conveyor Belt Specification
Strength and Durability: Specifications will detail the belt’s tensile strength, resistance to tearing, and expected lifespan. Dimensional Specifications: Belt width, thickness, and length must align with your system’s requirements. Special Features: Some belts have specific features like rip resistance, low noise, or energy efficiency that might be crucial for your application.
Consulting with Conveyor Belt Fabric Manufacturers
Expert Advice: Gram can provide valuable insights into the most suitable belt types for different applications. They often have data and case studies to guide your choice. Custom Solutions: We offer custom-designed belts tailored to specific operational needs.
Sustainability Considerations
Reducing Waste: Choosing a durable, high-quality belt can minimize replacement frequency, thus reducing waste. Energy Efficiency: Some fabric conveyor belts are designed to reduce energy consumption, which not only cuts costs but also supports sustainability targets. Recyclability: Consider belts made from recyclable materials to further enhance environmental responsibility.
CONTACT US
Let us help you find a better solution!
FAQs about Fabric Conveyor Belt
What fabric are belts made of?
Belts used in heavy industries such as mining are often made of durable, high-strength materials designed to withstand harsh conditions. These belts can be constructed from synthetic fabrics like polyester, nylon, and Kevlar. Polyester is favored for its strength and resistance to stretching, making it ideal for handling heavy loads. Nylon offers excellent flexibility and high tensile strength, while Kevlar is renowned for its exceptional durability and resistance to abrasion. These fabrics are typically woven or laminated to form a robust belt structure capable of enduring the rigorous demands of industrial applications. Additionally, these belts may be reinforced with steel cords or other materials to further enhance their load-bearing capabilities and longevity.
Which Fibre is used to make conveyor belt?
Conveyor belts in heavy industries are commonly made from a blend of synthetic fibers that provide both strength and durability. Polyester and nylon are the primary fibers used in the manufacturing of these belts. Polyester fibers offer excellent resistance to stretching and wear, making them suitable for the continuous movement of heavy materials. Nylon fibers add flexibility and high tensile strength, which helps in accommodating the varying loads and stresses encountered in industrial operations. In some cases, aramid fibers such as Kevlar may be used to enhance the belt’s resistance to impact and abrasion, providing a longer service life in demanding environments like mining and quarrying.
What is belt material called?
The material used to construct belts, especially in heavy industries, is commonly referred to as conveyor belt material or belt carcass. This term encompasses a variety of materials designed to provide the necessary strength, flexibility, and durability for different industrial applications. Conveyor belt material typically includes a combination of synthetic fabrics such as polyester, nylon, and aramid fibers, often reinforced with steel cords or other materials. These components are layered and bonded together to form a robust belt capable of withstanding the rigorous demands of transporting heavy loads, abrasive materials, and operating in harsh environmental conditions.
What are the materials commonly used for belts?
Belts used in heavy industrial applications like mining are typically made from a range of robust materials designed to endure extreme conditions. Common materials include synthetic fabrics such as polyester, nylon, and aramid fibers like Kevlar. Polyester is valued for its excellent tensile strength and resistance to stretching, while nylon offers flexibility and high tensile strength. Kevlar is used for its superior abrasion resistance and durability. Additionally, these belts often incorporate steel cords or wires for added strength and stability, ensuring they can handle the significant stresses of transporting heavy and abrasive materials. The combination of these materials results in belts that are both durable and capable of long-term performance in demanding industrial environments.
What are fabric belts?
Fabric belts, especially in the context of heavy industries like mining, refer to conveyor belts made from various layers of synthetic fabrics. These belts are designed to transport materials such as ores, coal, and aggregates across significant distances. The fabric layers, typically made from materials like polyester, nylon, or aramid fibers, provide the necessary strength, flexibility, and durability to handle the heavy loads and harsh conditions of mining operations. These belts are engineered to resist wear and tear, impact, and abrasion, ensuring efficient and reliable material handling. The fabric belts are often reinforced with additional materials like steel cords to enhance their load-bearing capacity and lifespan.
Why is polyester required to make a conveyor belt?
Polyester is essential in making conveyor belts for heavy industries due to its exceptional strength, durability, and resistance to stretching. In mining operations, conveyor belts are subjected to extreme stresses from heavy loads and continuous operation. Polyester fibers provide the necessary tensile strength to withstand these demands without deforming. Additionally, polyester is resistant to moisture, chemicals, and abrasions, making it ideal for the harsh environments found in mining. Its stability under varying temperatures ensures that the conveyor belts maintain their integrity and performance, contributing to efficient and reliable material transportation over long periods, which is critical in large-scale mining operations.
What type of fabric is used in conveyor belts?
Conveyor belts used in heavy industries like mining are primarily made from high-strength synthetic fabrics. The most common types of fabric include polyester, nylon, and aramid fibers. Polyester is chosen for its excellent tensile strength and minimal stretch, providing a stable and durable belt structure. Nylon offers superior flexibility and impact resistance, making it suitable for handling varying loads and harsh conditions. Aramid fibers, such as Kevlar, are used for their exceptional abrasion resistance and high tensile strength, ensuring the belt can endure rigorous usage and extend its service life. These fabrics are often combined and reinforced with steel cords to enhance the belt’s overall strength and durability.
What are the three types of belts?
In heavy industrial applications like mining, there are three primary types of belts used for material handling: flat belts, V-belts, and conveyor belts. Flat belts are simple and used for light to moderate loads, offering flexibility and ease of installation. V-belts are characterized by their trapezoidal cross-section and are used in situations requiring significant power transmission, such as in conveyor systems and heavy machinery. Conveyor belts are specifically designed for transporting materials over long distances and can handle a wide range of heavy and abrasive materials. These belts are typically made from robust materials like polyester, nylon, and steel-reinforced fabrics to ensure durability and long-term performance in harsh mining environments.
What is a PVC conveyor belt used for?
PVC conveyor belts are commonly used in heavy industries, including mining, due to their durability, flexibility, and resistance to chemicals and moisture. These belts are well-suited for transporting a wide range of materials, from raw ores and coal to finished products like aggregates and minerals. PVC (Polyvinyl Chloride) belts offer excellent resistance to wear and abrasion, making them ideal for environments where the conveyor system is exposed to harsh conditions and abrasive materials. Additionally, their smooth surface and ability to maintain a consistent grip on conveyed materials enhance operational efficiency. PVC belts are also preferred for their ease of maintenance and ability to withstand the rough and demanding conditions typical in mining operations.
What material is used for low friction conveyor belts?
Low friction conveyor belts are often made from materials like polyethylene (PE), polypropylene (PP), or thermoplastic polyurethane (TPU). These materials provide a smooth surface that reduces resistance between the belt and the conveyed materials, minimizing energy consumption and wear. In heavy industries like mining, where continuous and efficient material handling is critical, low friction belts ensure smoother operations and lower maintenance costs. Polyethylene and polypropylene are valued for their lightweight and low friction properties, while TPU offers excellent wear resistance and flexibility. These materials are particularly useful in applications where reducing friction is essential to prevent material buildup and ensure consistent conveyor performance.
How to select a conveyor belt?
Selecting a conveyor belt for heavy industries like mining involves considering several critical factors to ensure optimal performance and durability. First, evaluate the type and weight of the materials to be conveyed, as this determines the belt’s strength and load-bearing capacity. Next, consider the operating environment, including temperature, moisture, and exposure to chemicals, which influence the choice of belt material. The belt’s width, length, and speed should match the system’s requirements to ensure efficient material handling. Additionally, consider the belt’s resistance to abrasion, impact, and wear, especially in mining where belts face harsh conditions. Reinforcement options like steel cords or textile layers can enhance durability. Finally, maintenance and ease of installation should be considered to minimize downtime and operational costs.
What is conveyor belt dressing?
Conveyor belt dressing refers to the application of various substances to the surface of a conveyor belt to enhance its performance and extend its lifespan. In heavy industries like mining, belt dressing is used to improve the belt’s grip, reduce slippage, and minimize wear caused by friction and abrasion. It can also help in maintaining the belt’s flexibility and preventing cracking in harsh conditions. Belt dressings are typically made from compounds that provide a protective coating, such as silicone, graphite, or specialized lubricants. These treatments help in reducing the buildup of material on the belt, ensuring smoother operation, and reducing maintenance needs, ultimately improving the efficiency and reliability of the conveyor system.
What type of belt conveyor is used to convey powdery materials?
For conveying powdery materials in heavy industries like mining, a screw conveyor belt is often used. Screw conveyors are specifically designed to handle fine, granular, and powdery substances, providing efficient and controlled movement of materials such as cement, fly ash, or fine minerals. These conveyors consist of a helical screw blade, known as a flighting, that rotates inside a tube or trough, pushing the material along the conveyor’s length. The enclosed design of screw conveyors minimizes dust and prevents spillage, making them ideal for transporting powdery materials that can be difficult to handle with traditional belt conveyors. Additionally, their robust construction ensures reliable operation in demanding industrial environments.