Ceramic Conveyor Rollers: Revolutionizing Material Handling
Ceramic Conveyor Rollers represent a significant leap in conveyor technology. Traditionally, conveyor rollers were primarily made from metals or rubber, which, while effective, had limitations in terms of wear resistance, friction management, and longevity. The introduction of advanced ceramic materials has revolutionized this domain, with these rollers providing superior durability, less maintenance, and enhanced performance over traditional ones.
The significance of Ceramic Conveyor Rollers in modern industries cannot be overstated. These rollers are not just components of a conveyor system; they are pivotal in enhancing the overall efficiency and productivity of operations. Their high wear resistance makes them ideal for environments where abrasive materials are handled, significantly reducing the downtime caused by roller replacements. The smooth, hard surface of ceramic rollers minimizes friction, which is crucial for maintaining the integrity and longevity of conveyor belts.
Moreover, Ceramic Conveyor Rollers are uniquely suited for challenging industrial environments. Their resistance to corrosion and temperature extremes makes them a preferred choice in industries like mining, cement production, and steel manufacturing, where harsh conditions are the norm. Additionally, the non-stick properties of ceramic surfaces ensure that materials like sticky ores or chemicals do not adhere to the rollers, maintaining a clean and efficient transport line.
GRAM Conveyor : The Best Choose of Ceramic Conveyor Rollers
GRAM Conveyor-The industry leader and standard for a complete product line of corona treater coverings.
BENEFITS:
GRAM specialty rollers are available in ten specific solutions tailored for use in elastomer, epoxy, and ceramic treater applications. Each roller undergoes 100% corona treater testing before shipment to ensure the highest quality and longevity. Additionally, these rollers come with the strongest warranty in the market, guaranteeing superior performance.
BEST USED FOR:
Corona Treater applications
What Is The Ceramic Conveyor Rollers
Unraveling the Mystique of Ceramic Conveyor Rollers
Intriguing and innovative, Ceramic Conveyor Rollers represent a remarkable advancement in the realm of material handling. These rollers seamlessly blend durability, efficiency, and top-notch performance. Made from tough, wear-resistant ceramic materials, they outperform traditional metal or rubber rollers, especially in harsh, abrasive, or corrosive industrial settings.
Ceramic Conveyor Rollers stand out due to their high resistance to wear and tear, capacity to endure high temperatures, and low friction, thanks to their alumina (Al₂O₃) ceramic composition. The inherent hardness of ceramics contributes significantly to the extended lifespan of these rollers, ultimately reducing the frequency of replacements needed.
Ceramic Conveyor Roller’s Composition and Manufacturing Process
The core composition of Ceramic Conveyor Rollers invariably revolves around the use of high-purity ceramic materials, with alumina being a prime example. These materials are renowned for their exceptional hardness, a quality that places them just a notch below the illustrious diamond in terms of toughness. The manufacturing journey of these rollers commences with the meticulous molding of the ceramic substance into the desired size and shape, followed by subjecting it to a high-temperature firing process. This intense thermal treatment serves as the crucible in which the roller’s strength and durability are significantly elevated to meet the rigorous demands of industrial applications.
During the manufacturing process, meticulous attention is paid to refining the rollers’ surface finish. This step involves careful smoothing and polishing, resulting in a surface that exhibits minimal friction with the conveyor belt. This attention to detail not only extends the lifespan of both the roller and the conveyor belt but also ensures seamless, efficient operation, enhancing the overall performance of the conveyor system.
Key Properties of Ceramic Conveyor Rollers
- High Wear Resistance: Ceramic materials are inherently resistant to abrasion, making these rollers ideal for environments where material wear is a significant concern. This resistance ensures that the rollers maintain their integrity and functionality over long periods, even under constant use.
- Low Friction Coefficient: Ceramic has a lower friction coefficient compared to metals and plastics. This property reduces the energy required to move belts or loads, which can lead to significant energy savings and reduced operational costs.
- Corrosion Resistance: Unlike metal rollers, ceramic is impervious to most corrosive substances, making these rollers suitable for use in chemical processing environments or applications where exposure to corrosive agents is common.
- Temperature Tolerance: Ceramic materials can withstand extremely high temperatures without losing strength or shape. This makes ceramic rollers suitable for applications in high-temperature environments where other materials might degrade.
These properties make ceramic conveyor rollers an excellent choice for industries looking to optimize their conveyor systems for performance, durability, and cost-efficiency. They are particularly valuable in harsh environments where the conveyor system needs to resist mechanical and chemical stresses.
Benefits of Ceramic Conveyor Rollers
Ceramic Conveyor Rollers have revolutionized the material handling sector with their exceptional properties and performance enhancements.
- Increased Friction and Grip: One of the primary advantages of Ceramic Conveyor Rollers is their ability to provide increased friction between the roller and the conveyor belt. This enhanced grip ensures that materials are moved smoothly and consistently along the conveyor, reducing slippage and improving overall handling efficiency. This feature is particularly beneficial in industries where precise material movement is crucial.
- High Wear Resistance: Ceramic materials are known for their incredible wear resistance, which is a critical factor in the longevity of conveyor rollers. Unlike traditional materials that can wear down quickly in harsh conditions, ceramic rollers maintain their integrity over extended periods, even under constant use. This resistance to wear and tear translates to fewer replacements, reduced downtime, and lower long-term operational costs.
- Self-Cleaning Properties and Suitability in Various Environments: Ceramic Conveyor Rollers, with self-cleaning properties and smooth, non-porous surfaces, resist dust, debris, and stickiness, maintaining cleanliness and efficiency in challenging environments like mining, agriculture, and food processing.
- Extended Lifespan: Ceramic Conveyor Rollers offer unparalleled longevity and durability. Their robust construction and resistance to high temperatures, corrosion, and abrasion mean they can withstand challenging industrial environments without significant wear. This durability not only ensures a longer lifespan but also means that the rollers can maintain their performance level over time, providing consistent and reliable operation.The robust properties of ceramic ensure that these rollers last much longer than their traditional counterparts. The extended lifespan not only reduces the frequency of replacement but also minimizes downtime caused by maintenance. The investment in ceramic rollers thus pays off in the long run, with reduced maintenance requirements and lower replacement costs.
- Reduced Maintenance Costs: The durability and low wear characteristics of ceramic mean that these rollers require less frequent maintenance, saving on labor costs and spare parts.
- Enhanced Efficiency: The smooth surface and low friction of ceramic rollers allow for smoother and more efficient belt operation, which can improve the throughput of the conveying system.
- Self-Cleaning Properties and Suitability in Various Environments: With lower energy consumption and reduced need for replacements, ceramic conveyor rollers are a more sustainable option, aligning with environmental conservation goals of many modern businesses.Ceramic Conveyor Rollers, with self-cleaning properties and smooth, non-porous surfaces, resist dust, debris, and stickiness, maintaining cleanliness and efficiency in challenging environments like mining, agriculture, and food processing.
What is the Types and Features of Ceramic Rollers?
Ceramic Conveyor Rollers come in various types, each designed to meet specific industrial requirements and applications. The diversity in these rollers is primarily based on their ceramic composition, surface treatment, and design features. Understanding these variations is crucial for selecting the right roller for specific conveyor system needs.These rollers are primarily differentiated by the type of ceramic used and the specific applications they are designed for. Below is a detailed explanation of the types and features of ceramic rollers:
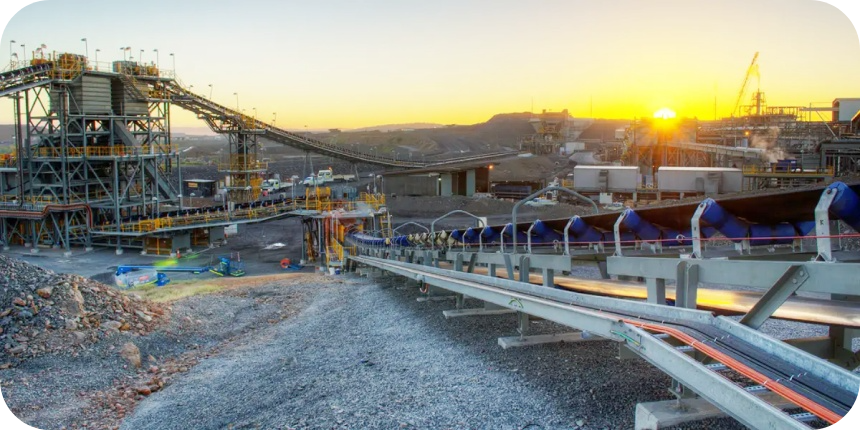
1. Alumina (Aluminum Oxide) Ceramic Rollers
Alumina-based Ceramic Conveyor Rollers, made primarily from aluminum oxide (Al₂O₃), are common due to their high density and extreme hardness, offering excellent wear resistance, especially in abrasive environments.
- Properties: Alumina ceramic rollers are known for their excellent hardness and strength, high thermal conductivity, and resistance to wear and chemical attack.
- Features: These rollers are ideal for high-temperature environments, such as in steel and glass manufacturing, because of their ability to withstand temperatures up to 1650°C without deformation or loss of mechanical properties.
2. Zirconia (Zirconium Oxide) Ceramic Rollers
For even higher durability and toughness, some ceramic rollers incorporate zirconia. These are particularly useful in applications where impact resistance is as crucial as wear resistance.
- Properties: Zirconia ceramics possess outstanding fracture toughness and thermal insulation properties. They are also highly resistant to crack propagation.
- Features: Zirconia rollers are particularly beneficial in applications requiring high durability and resistance to thermal shock. This makes them suitable for rapid temperature changes and demanding environments.
3. Silicon Carbide Ceramic Rollers
- Properties: Silicon carbide ceramics are noted for their exceptional hardness, thermal conductivity, and low thermal expansion.
- Features: These rollers are used in applications that require high wear resistance and thermal shock resistance, such as in the processing of metals and ceramics.
4. Silicon Nitride Ceramic Rollers
Known for their lightweight and high strength, silicon nitride rollers are ideal for applications where weight reduction is essential without compromising durability.
- Properties: Silicon nitride features excellent thermal stability, high fracture resistance, and good shock resistance.
- Features: Their durability and ability to perform under high stress and at high speeds make them a preferred choice for high-performance applications in the aerospace, automotive, and electronics industries.
5.Ceramic Coating: Many ceramic rollers feature a specialized ceramic coating that enhances their wear resistance and reduces friction. This coating is typically applied through advanced techniques like plasma spraying, ensuring a uniform and durable layer.
6.Diamond-Polished Surfaces: Some ceramic rollers undergo a diamond polishing process, resulting in exceptionally smooth surfaces. This feature is crucial for minimizing wear on the conveyor belt and ensuring smooth operation.
Common Features Across All Types
- Wear Resistance: Ceramic rollers offer superior wear resistance, reducing downtime and maintenance needs in industrial settings.
- Corrosion Resistance: These rollers are impervious to most acids and alkalis, making them suitable for chemical processing environments.
- Low Friction: The smooth surface of ceramic reduces friction between the roller and other components, enhancing efficiency and reducing energy costs.
- Thermal Stability: Ceramic materials can handle extreme temperatures, making them ideal for applications involving heat treatment processes.
Comparison with Traditional Conveyor Rollers
Feature | Ceramic Conveyor Rollers | Metal Rollers | Rubber Rollers |
---|---|---|---|
Wear Resistance | Superior wear resistance, lasting much longer even in abrasive environments. | Prone to wear, especially when handling abrasive materials. | Good resistance but can degrade under harsh conditions. |
Corrosion Resistance | Highly resistant to corrosion, suitable for various industrial applications. | Can corrode over time, especially in moist or chemically active environments | Generally resistant to corrosion but can |
Customization Options
Ceramic Conveyor Rollers are highly customizable to meet diverse industrial needs. Manufacturers offer various customization options, including: Size and Diameter Customization: Depending on the conveyor system and the materials being transported, rollers can be customized in different sizes and diameters. Groove Patterns: Custom groove patterns can be etched onto the roller surface to suit specific material handling requirements. These patterns can aid in material grip and alignment. Surface Treatments: Apart from diamond polishing, other surface treatments like matte finishing or specific coatings can be applied based on the operational environment and material characteristics. Bearing and Shaft Options: Customization extends to the roller’s bearings and shafts, ensuring compatibility with different conveyor systems and operational speeds.
The Versatile Applications of Ceramic Conveyor Rollers
Ceramic conveyor rollers are increasingly popular in various industrial sectors due to their superior properties over traditional materials like steel or rubber. Here’s a detailed overview of their applications across different industries:
- Mining and Mineral Processing: Ceramic rollers are used in the harsh environments of mining operations, where they handle abrasive materials such as ores and minerals. Their resistance to wear and tear ensures long-lasting performance under tough conditions, reducing the frequency of conveyor roller replacements and maintenance.
- Steel Manufacturing: In steel mills, conveyors equipped with ceramic rollers are crucial for moving hot steel slabs, sheets, or rods. The high temperature resistance of ceramic prevents deformation and failure, ensuring smooth and continuous operation.
- Glass Manufacturing: The non-reactive nature of ceramic makes these rollers ideal for transporting glass sheets and other components within glass manufacturing facilities. They prevent contamination and damage to the glass, which is essential for maintaining product quality.
- Food Processing: Ceramic’s resistance to corrosion and its easy-to-clean surface make it suitable for food processing applications. These rollers can handle wet and acidic food products without rusting or corroding, ensuring compliance with strict hygiene standards.
- Pharmaceutical Production: In pharmaceutical manufacturing, maintaining a contamination-free environment is critical. Ceramic rollers do not shed particles as some other materials might, making them ideal for environments where product purity is paramount.
- Printing and Paper Industries: These industries benefit from ceramic rollers as they facilitate the smooth and precise transportation of paper and printing materials. Their smooth surface ensures that the delicate materials are not damaged during the process.
- Chemical Processing: The chemical-resistant properties of ceramic are advantageous in settings where rollers may be exposed to corrosive substances. This makes them suitable for conveyors that transport chemicals or are involved in chemical treatment processes.
- Automotive Manufacturing: Ceramic rollers are used in the automotive industry for the transport of automotive parts through paint shops and other treatment areas where exposure to harsh chemicals and temperatures may occur.
- Electronics and Semiconductor Manufacturing: The anti-static properties of ceramic help in safely transporting sensitive electronic components and semiconductors. This reduces the risk of static damage, which is crucial in these industries.
- Recycling Facilities: The durability and resistance to abrasive materials make ceramic rollers ideal for recycling operations, where they can handle a variety of materials without suffering surface wear.
- Cement Production: The cement industry involves the handling of gritty and abrasive materials. Ceramic Rollers excel in these environments by minimizing wear and tear, thus maintaining consistent production levels without frequent maintenance interruptions. The plant replaced its traditional rollers with ceramic ones and observed a 30% decrease in conveyor-related downtime. The smooth operation of Ceramic Rollers also contributed to a more consistent product quality.
- Thermal Power Plants: Conveying coal and other fuels in thermal power plants requires rollers that can handle high loads and resist fire hazards. Ceramic Rollers, with their fire-resistant properties, offer a safe and efficient solution for these demanding conditions. In a thermal power plant, the introduction of Ceramic Conveyor Rollers resulted in a safer and more reliable fuel handling system. The rollers’ fire-resistant properties minimized the risk of fire hazards, a critical consideration in such environments.
These applications highlight the versatility of ceramic conveyor rollers and their ability to improve operational efficiencies, reduce maintenance costs, and extend the lifespan of conveyor systems in a diverse range of industrial settings.
How to Select Right Ceramic Conveyor Rollers?
When it comes to integrating Ceramic Conveyor Rollers into an industrial setting, selecting the right type is crucial for achieving optimal performance and efficiency. Here are some essential tips and factors to consider when choosing the appropriate ceramic conveyor roller for specific industrial needs:
- Material Compatibility:
- Ensure that the ceramic material is suitable for the type of products or substances it will transport. Consider the roller’s resistance to chemicals, temperatures, and abrasive materials based on the operational environment.
- Temperature Tolerance:
- Evaluate the temperature range that the conveyor will be exposed to. Ceramic rollers are excellent for high-temperature applications, but it’s important to choose a ceramic type that can handle the specific maximum and minimum temperatures of your environment.
- Load Capacity:
- Consider the weight of the materials the conveyor needs to support. Different ceramic compositions have varying strength levels. Ensure that the rollers you choose can withstand the load without cracking or breaking.
- Dimensional Requirements:
- Measure the necessary roller dimensions, including length, diameter, and thickness, which need to fit precisely in your conveyor system. Incorrect sizing can lead to operational inefficiencies and equipment damage.
- Friction Coefficient:
- The surface texture and material properties of ceramic rollers affect their friction coefficient. Choose rollers with an appropriate friction level to ensure smooth operation and to avoid slipping or sticking of materials being transported.
- Corrosion Resistance:
- If the rollers will be exposed to corrosive substances or humid environments, it’s crucial to select ceramics with high corrosion resistance to prolong the life of the rollers and maintain their functionality.
- Maintenance and Cleaning:
- Consider how easy it is to clean and maintain the rollers. Rollers with smoother surfaces tend to accumulate less debris and are easier to clean, which is particularly important in industries requiring high hygiene standards, like food processing or pharmaceuticals.
- Installation and Compatibility:
- Ensure that the ceramic rollers are compatible with existing conveyor systems in terms of mounting configurations and operational mechanics. This includes checking the compatibility of roller bearings and fittings.
- Supplier Reputation and Product Quality:
- Choose a reputable supplier known for high-quality products. Quality assurance certifications or standards, such as ISO certifications, can indicate reliable and high-performance rollers.
- Cost Considerations:
- While ceramic rollers might be more expensive upfront than other materials, consider the long-term savings due to reduced maintenance and replacement costs. Evaluate the total cost of ownership over time, not just the initial purchase price.
By carefully considering these factors, you can select the right ceramic conveyor rollers that meet the specific demands of your industrial applications, leading to improved efficiency, reduced downtime, and overall better performance of your conveyor systems.
CONTACT US
Let us help you find a better solution!
FAQs about Ceramic Conveyor Rollers
1. What is the use of a ceramic roller?
In conveyor systems, ceramic rollers are used for their wear-resistant properties. They are ideal for environments where durability and reduced maintenance are crucial. Ceramic rollers resist wear from abrasive materials and minimize belt slippage, making them suitable for heavy-duty applications.
2. What is a ceramic roll?
A ceramic roll refers to a roller made from ceramic materials. In industrial applications, these rolls are valued for their hardness, wear resistance, and ability to withstand high temperatures. They are often used in processes involving high heat or abrasive materials.
3. Are there different types of rollers?
Yes, there are different types of rollers used in various industries. In conveyor systems, common types include drive, idler, return, and impact rollers. In construction for compaction, types include smooth wheel rollers, vibratory rollers, pneumatic-tired rollers, and sheepsfoot rollers.
4. What material is best for rollers?
The best material for rollers depends on their application. For conveyor systems, steel and heavy-duty plastics are common for their durability and load-bearing capacity. For hair styling, ceramic and titanium are preferred for their heat distribution properties. In construction, metal and rubber-coated rollers are used for soil and asphalt compaction.
5. How heavy is a conveyor roller?
The weight of a conveyor roller varies depending on its size and material. Small plastic rollers might weigh a few pounds, while large, heavy-duty steel rollers can weigh several hundred pounds.
6. What is the purpose of the rollers in a conveyor?
The purpose of rollers in a conveyor is to support and move the conveyor belt or the materials being transported. They help in reducing friction, ensuring smooth movement of the belt, and evenly distributing the load.
7. What roller is best for compaction?
The best roller for compaction depends on the material being compacted. For granular soils, vibratory rollers are effective. For cohesive soils like clay, padfoot or sheepsfoot rollers are better. For asphalt paving, smooth drum vibratory rollers are typically used.
8. What are the different types of industrial rollers?
Industrial rollers include conveyor rollers, compaction rollers, printing rollers, and textile rollers. Each type is designed for specific industrial applications, with variations in size, material, and design to suit different needs.
9. What is an alternative to rollers?
An alternative to rollers in conveyor systems could be flat belts or skate wheel conveyors. In hair styling, alternatives to rollers include curling irons or hot brushes. For soil compaction, plate compactors or rammers can be used instead of rollers.
10. How many roller passes for compaction?
The number of roller passes for compaction depends on the material type, thickness of the layer, and the type of roller used. Generally, it takes multiple passes, often between 4 to 8, to achieve optimal compaction. The exact number should be determined based on field tests and project specifications.
11. How would you select the type of rollers to be used?
Selecting the type of rollers for a project depends on several factors, including the material to be compacted (soil type, asphalt), the depth of the layer, the size of the area, and the desired compaction level. Soil type is particularly crucial, as different soils respond differently to compaction methods.
12. What are the two types of track rollers?
The two types of track rollers are flanged and unflanged track rollers. Flanged track rollers have a flange on one or both sides for guiding along a track, while unflanged track rollers are used where lateral guidance is not required.
13. What are the different types of rollers used in the field for compaction?
In the field for compaction, different types of rollers include smooth wheel rollers, vibratory rollers, pneumatic-tired rollers, and sheepsfoot rollers. Each type is suited for specific soil types and compaction requirements.
14. How many types of conveyor belt joints are there?
There are several types of conveyor belt joints, including mechanical fastening, vulcanization, and gluing. Mechanical fastening involves using metal fasteners, vul