Conveyor Roller Replacement and Specialty Solutions
In industrial environments, maintaining the integrity of conveyor systems is crucial for operational efficiency and workplace safety. Regular conveyor roller replacement is essential to avoid the costly disruptions caused by equipment failures. Over time, rollers can undergo wear and tear from constant use, which not only impedes the smooth operation of conveyors but also poses significant safety risks. Prompt replacement of these worn-out rollers ensures the system operates at peak efficiency, prevents potential accidents, and reduces downtime. This practice not only sustains the longevity of the conveyor system but also supports consistent, quality production and the safety of the workforce. Recognizing the signs of roller wear early and understanding the correct replacement procedures are vital steps in maintaining the effectiveness and safety of conveyor operations.
Recognizing the Need for Conveyor Roller Replacement
Identifying when to perform a conveyor roller replacement is critical for maintaining the efficiency and safety of conveyor systems. There are several indicators that facility managers and maintenance teams should monitor to determine the appropriate time for replacing conveyor rollers. Neglecting these signs can lead to more severe issues, impacting productivity and increasing operational costs.
Signs and Symptoms of Worn Rollers
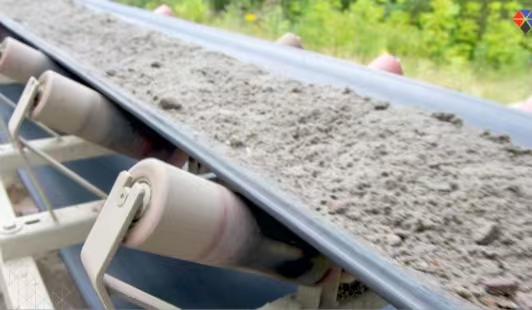
The first step in recognizing the need for conveyor roller replacement is to understand the signs of wear and tear:
- Unusual Noises: Grinding, squeaking, or rattling sounds from the conveyor rollers are often the first indication of wear. These sounds suggest that the rollers are not rotating smoothly, potentially due to debris accumulation, lack of lubrication, or physical damage to the bearings.
- Irregular Operation: Rollers that stick or stop randomly can cause irregularities on the conveyor belt. Such issues may result in product mishandling or accidents, signaling the need for immediate inspection and likely replacement.
- Visible Wear on Rollers: Physical signs include cracks, chips, or significant surface wear on the rollers. Visible wear compromises the roller’s integrity and its ability to provide a smooth surface for the conveyor belt.
- Decreased Conveyor Performance: If the conveyor starts operating slower, or with less precision in product handling, it might indicate that the rollers are failing and cannot support the belt or products effectively.
Impact of Delayed Roller Replacements
Failing to promptly address the need for conveyor roller replacement can have detrimental effects on the conveyor system:
- System Downtimes: Worn rollers can lead to conveyor belt malfunctions, such as misalignment or belt slippage, which in turn causes unplanned system shutdowns to perform emergency repairs.
- Higher Maintenance Costs: The longer damaged rollers are left in place, the more likely they are to cause damage to other components of the conveyor, such as the conveyor belt itself. Early replacement of rollers can mitigate extensive repairs and reduce overall maintenance costs.
- Increased Wear on Other Conveyor Components: Imbalanced or rough roller surfaces increase friction and strain on the conveyor belt and adjacent rollers. Over time, this additional wear can degrade other parts of the system, compounding repair needs and costs.
- Safety Risks: Damaged or inefficient rollers pose safety risks to operators, particularly if the conveyor handles heavy or hazardous materials. Proper and timely replacements are essential to maintain a safe working environment.
Understanding these signs and the potential impacts of delayed conveyor roller replacement helps maintain operational efficiency and safety standards. Regular inspections and maintenance schedules should be in place to assess the condition of conveyor rollers and to perform replacements as needed to avoid the above complications.
Types of Available Conveyor Roller Replacement
Standard Duty Conveyor Rollers

Standard duty conveyor rollers, commonly used in various material handling applications, are ideal for light to medium load capacities. Here are some typical applications and specifications for material handling roller conveyors:
- 4″ Conveyor Roller: A common size used in conveyor systems for general material handling tasks such as sorting, packaging, and assembly.
- 1 Inch Diameter Conveyor Roller: Smaller diameter conveyor rollers suitable for applications requiring precision or where space is limited, such as conveyor curves or tight conveyor layouts.
- Light Duty Applications: Standard duty rollers are best suited for applications with relatively light loads, such as retail distribution, packaging, and small-scale manufacturing.
- Materials: Standard duty conveyor rollers are often made from materials like galvanized steel, aluminum, or PVC, providing a balance of strength, durability, and affordability.
- Versatility: These rollers can be used in gravity conveyor systems or powered conveyor systems, providing flexibility in conveyor design and layout.
- Ease of Replacement: Standard duty conveyor rollers are readily available and easy to replace, minimizing downtime and maintenance costs in conveyor systems.
- Smooth Operation: They offer smooth and reliable operation, ensuring efficient material handling and product flow on the conveyor line.
- Cost-Effective Solution: Standard duty conveyor rollers offer a cost-effective solution for light to medium duty applications, providing reliable performance at a competitive price point.
Heavy Duty Conveyor Rollers
Heavy duty conveyor rollers are designed to withstand high loads and intensive operations, making them suitable for demanding industrial applications. Here are some features of heavy duty rollers:
- Industrial Conveyor Rollers: Designed for use in heavy-duty industrial environments such as manufacturing plants, warehouses, and distribution centers.
- Enhanced Durability: Heavy duty steel rollers are constructed from robust materials such as steel or stainless steel, providing superior strength and durability to withstand heavy loads and harsh operating conditions.
- High Load Capacity: These rollers are engineered to support heavy loads without deformation or failure, ensuring reliable performance in high-capacity conveyor systems.
- Large Diameter Options: Heavy duty conveyor rollers are available in larger diameter options to distribute load weight more effectively and reduce stress on bearings and axles.
- Sealed Bearings: Many heavy duty rollers feature sealed bearings to protect against contamination and extend the lifespan of the roller, reducing maintenance requirements and downtime.
- Precision Machining: Heavy duty rollers are precision machined to tight tolerances, ensuring smooth and consistent operation even under heavy load conditions.
- Impact Resistance: They are designed to withstand impact and shock loads, reducing the risk of damage to the conveyor system and ensuring continuous operation in demanding environments.
- Customization Options: Heavy duty rollers can be customized to meet specific application requirements, including special coatings, shaft configurations, and mounting options.
- Long Service Life: With their durable construction and high-quality components, heavy duty conveyor rollers offer a long service life and reliable performance, minimizing the need for frequent replacements and maintenance.
Choosing the Right Conveyor Roller Replacement
When selecting the appropriate conveyor roller replacement for your system, several factors need to be considered to ensure optimal performance and compatibility.
By Material and Design
Different materials and designs offer unique advantages and suitability for specific industrial environments. Consider the following options:
- Stainless Steel Rollers: Ideal for corrosive or sanitary environments, stainless steel rollers offer excellent resistance to rust, corrosion, and contamination, making them suitable for food processing, pharmaceutical, and chemical industries.
- Polyurethane Coated Rollers: Featuring a durable polyurethane coating, these rollers provide enhanced grip and abrasion resistance, making them suitable for applications where slippage or wear is a concern, such as inclined conveyors or handling delicate materials.
- Rollers with Brackets: Rollers with integrated brackets simplify installation and replacement processes, reducing downtime and labor costs. These rollers are commonly used in conveyor systems where quick and easy maintenance is essential, such as distribution centers and warehouses.
- Aluminum Rollers: Lightweight and corrosion-resistant, aluminum rollers are suitable for applications requiring high-speed operation or where weight reduction is a priority, such as airport baggage handling systems or automotive manufacturing.
- Galvanized Steel Rollers: Galvanized steel rollers offer a balance of strength, durability, and cost-effectiveness, making them suitable for a wide range of general-purpose material handling applications in industrial settings.
- Nylon Rollers: Nylon rollers are known for their low friction properties and resistance to chemicals and abrasion, making them suitable for applications where smooth and quiet operation is essential, such as conveyor systems in retail and distribution facilities.
By Size and Load Capacity
Choosing the right size and load capacity for conveyor roller replacements is crucial to ensure compatibility and optimal performance. Consider the following factors:
- Matching Roller Sizes: Select rollers with dimensions (e.g., diameter and length) that match the specifications of your existing conveyor system to ensure proper fit and functionality. Incorrectly sized rollers can cause misalignment, increased wear, and conveyor malfunctions.
- Load Specifications: Determine the maximum load capacity required for your application and select rollers with appropriate load ratings to support the anticipated weight of transported items. Overloaded rollers can lead to premature failure and system downtime.
- Measuring Rollers: When replacing rollers, accurately measure the dimensions of the existing rollers, including diameter, length, and axle size, to ensure compatibility with replacement units. Use calipers or measuring tools to obtain precise measurements and avoid errors.
- Consider Environmental Factors: Take into account environmental conditions such as temperature, humidity, and exposure to chemicals or abrasive materials when selecting conveyor roller replacements. Choose rollers with materials and coatings that offer suitable resistance to environmental factors to ensure long-term durability and performance.
- Consult Manufacturer Guidelines: Refer to the manufacturer’s guidelines and specifications for your conveyor system to identify recommended roller sizes and load capacities. Following manufacturer recommendations ensures compatibility and compliance with system requirements.
- Evaluate Roller Configurations: Consider the configuration of your conveyor system, including roller spacing, orientation, and mounting requirements, when selecting replacement rollers. Choose rollers with compatible configurations to ensure seamless integration and proper operation within the conveyor system.
By considering these factors, businesses can choose the right conveyor roller replacements that meet their specific requirements and ensure reliable performance in their material handling operations.
Step-by-Step Guide to Conveyor Roller Replacement
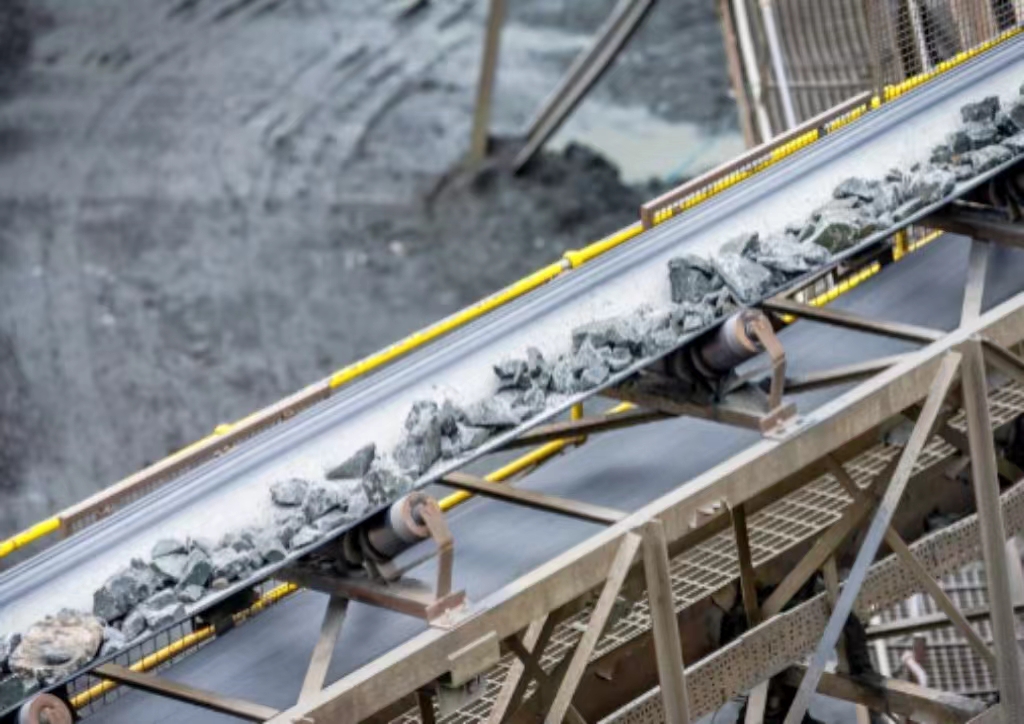
When it comes to conveyor roller replacement, following a systematic approach ensures a smooth and efficient process. Here’s a comprehensive guide:
Preparation and Safety
Before beginning the replacement process, gather the necessary tools and equipment, including wrenches, socket sets, and safety gear such as gloves and safety glasses. Ensure the conveyor system is shut down and locked out according to established safety procedures to prevent accidental startup.
Removal of Old Rollers
- Locate Roller Mounting Points: Identify the mounting points of the old rollers along the conveyor frame.
- Release Tension: If applicable, release any tension mechanisms or adjusters to relieve tension on the conveyor belt or chain.
- Remove Roller Retention Mechanisms: Loosen and remove any retaining bolts, clips, or brackets securing the old rollers to the conveyor frame.
- Support Conveyor Belt: Support the conveyor belt or chain to prevent sagging or movement during roller removal.
- Remove Old Rollers: Carefully lift and slide the old rollers out of conveyor roller mounting brackets or bearings. Use caution when handling heavy rollers to prevent injury or damage to the conveyor frame.
- Inspect Conveyor Frame: While the rollers are removed, inspect the conveyor frame for signs of wear, damage, or misalignment. Address any issues as needed before proceeding with installation.
Installation of New Rollers
- Prepare New Rollers: Ensure the new rollers are clean and free of any debris or contaminants. Verify that they are the correct size and type for the conveyor system. Made from precision bearings and quality steel, these durable replacement conveyor rollers can easily replace or upgrade existing rollers on compatible conveyors or stands.
- Align New Rollers: Align the new rollers with the mounting points on the conveyor frame, ensuring they are positioned correctly for smooth operation.
- Secure Rollers: Insert the new rollers into their respective mounting brackets or bearings. Secure them in place using retaining bolts, clips, or brackets, tightening them to the manufacturer’s specifications.
- Adjust Tension: If necessary, adjust any tension mechanisms or adjusters to ensure proper tension on the conveyor belt or chain.
- Test Operation: Once all new rollers are installed, carefully test the operation of the conveyor system. Verify that the rollers rotate freely and that the conveyor belt or chain tracks properly along the rollers.
- Final Checks: Conduct a final inspection of the conveyor system to ensure all components are securely fastened and aligned. Make any necessary adjustments to achieve proper alignment and tension.
By following these step-by-step instructions, businesses can successfully replace conveyor rollers, ensuring smooth and efficient operation of their conveyor systems while maintaining a safe working environment.
Where to Buy Conveyor Roller Replacements
When it comes to sourcing conveyor roller replacements, there are several options available, both locally and online. Here’s a guide to finding the right suppliers and considering cost factors:
Finding Suppliers
- Local Suppliers: Start by searching for local suppliers or distributors specializing in conveyor components and replacements. Look for industrial supply stores or bulk material handling equipment suppliers in your area.
- Online Suppliers: Explore online marketplaces and e-commerce platforms for a wide selection of conveyor roller replacements. Websites dedicated to industrial equipment and parts often offer a comprehensive range of options.
- Manufacturer Websites: Many conveyor roller manufacturers have official websites where you can browse their product catalogs and place orders directly. This allows you to access the latest product offerings and specifications.
- Industrial Trade Shows: Attend industrial trade shows and exhibitions where conveyor equipment suppliers showcase their products. This provides an opportunity to meet with representatives, compare options, and negotiate deals.
- Word of Mouth: Seek recommendations from colleagues, industry peers, or maintenance professionals who have experience with conveyor systems. They may be able to provide valuable insights and referrals to reliable suppliers.
- Online Directories: Utilize online business directories to search for suppliers of conveyor roller replacements. These directories often provide contact information, reviews, and ratings to help you make informed decisions.
- Supplier Reviews: Before making a purchase, research suppliers and read customer reviews to gauge their reputation for product quality, reliability, and customer service.
- Specialized Manufacturers: Consider specialized conveyor roller manufacturers that focus exclusively on conveyor components. They may offer a broader selection and more specialized expertise in conveyor roller replacements.
- Check for OEM Parts: If your conveyor system is from a specific manufacturer, check if they offer OEM replacement parts. Using original manufacturer parts ensures compatibility and quality assurance.
Cost Considerations
- Price Comparison: Compare prices from multiple suppliers to ensure you’re getting the best value for your investment. Consider factors such as product quality, warranty, and shipping costs.
- Bulk Purchase Discounts: Inquire about bulk purchase discounts if you’re planning to buy multiple conveyor roller replacements. Many suppliers offer discounted rates for large orders, saving you money in the long run.
- Total Cost of Ownership: Consider the total cost of ownership, including installation, maintenance, and potential downtime costs associated with using lower-quality replacement parts.
- Budget Allocation: Allocate a budget for conveyor roller replacements and factor in potential unforeseen expenses. It’s essential to prioritize quality and reliability to avoid frequent replacements and costly repairs down the line.
- Long-Term Savings: Investing in high-quality conveyor roller replacements may initially cost more but can result in long-term savings through improved performance, reduced maintenance, and extended service life.
- Negotiation: Don’t hesitate to negotiate with suppliers, especially for large orders or repeat purchases. You may be able to negotiate better pricing or additional perks such as extended warranties or expedited shipping.
By considering these factors, you can make informed decisions when purchasing conveyor roller replacements, ensuring optimal performance and longevity of your conveyor system while staying within budget constraints.
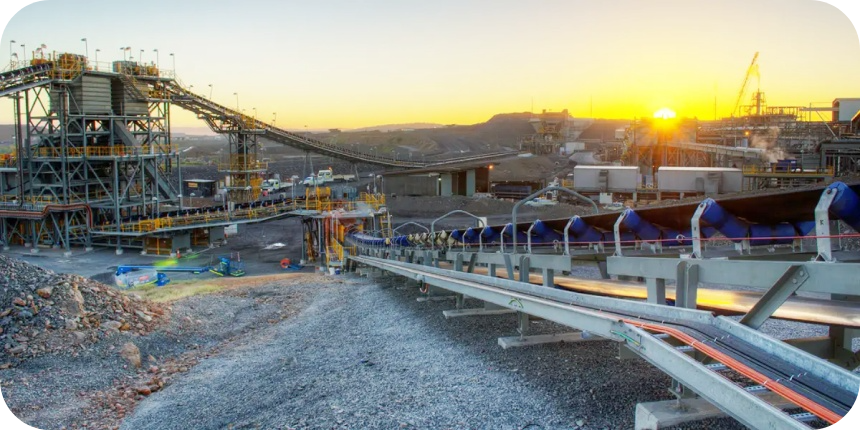
Maintenance Tips to Extend Roller Lifespan
Proper maintenance of conveyor rollers is essential to prevent frequent conveyor roller replacements and to ensure efficient operation of your conveyor system. Here are detailed steps and practices you can adopt to extend the life of your conveyor rollers.
Regular Inspection and Cleaning
To avoid premature conveyor roller replacement, it is crucial to implement a schedule for regular inspections and adhere to effective cleaning procedures:
- Scheduled Inspections: Establish a routine inspection schedule that allows for the examination of rollers for signs of wear, misalignment, or damage. Ideally, inspections should be conducted monthly or based on the operational hours of the conveyor system. Use a checklist to ensure every part is inspected thoroughly.
- Cleaning Techniques: Keeping conveyor rollers clean is vital for their longevity. Remove debris, dust, and any material buildup on rollers using brushes or compressed air. For rollers handling sticky materials, consider using mild detergents and water, but ensure the rollers are dried completely to avoid rusting.
Lubrication and Adjustments
Proper lubrication and timely adjustments are key to reducing the need for conveyor roller replacement:
- Lubrication Practices: Use manufacturer-recommended lubricants for roller bearings. Apply lubricant regularly, depending on the environmental conditions and operational frequency. Over-lubrication can attract dust and under-lubrication can cause premature wear, so follow the guidelines closely.
- Adjusting Tension: Maintain the correct tension on the conveyor belt to prevent excessive wear on rollers and bearings. Check and adjust the tension during routine maintenance checks according to the manufacturer’s specifications.
Tips for Spotting Issues During Routine Maintenance
To further reduce the likelihood of unexpected conveyor roller replacement, here are six tips to help you identify potential issues early:
- Listen for Noises: Unusual noises such as grinding or squeaking are often the first signs of trouble. These sounds can indicate issues like bearing failure or misalignment.
- Check for Movement: Rollers should rotate smoothly without wobbling. Any irregular movement can be a sign of worn out bearings or shaft misalignment.
- Inspect for Visible Wear: Look for visible signs of wear on the roller surface and edges. Excessive wear could lead to material shedding and might necessitate roller replacement.
- Monitor Load Distribution: Uneven distribution of materials can cause certain rollers to wear out faster than others. Ensure that the system is evenly loaded to prevent localized stress.
- Evaluate Roller Alignment: Misaligned rollers can cause the conveyor belt to track incorrectly and lead to increased friction and wear. Realign any rollers that are not parallel to the conveyor frame.
- Observe Material Build-Up: Material build-up on rollers can lead to conveyor belt mistracking and increased strain on bearings and joints. Clean rollers immediately if you notice excessive build-up during inspections.
By following these maintenance tips and regularly checking for the early signs of issues, you can significantly reduce the frequency of conveyor roller replacement and maintain the efficiency of your conveyor system.
Case Studies and Examples: Conveyor Roller Replacement
E-Commerce Fulfillment Centers: Amazon’s Conveyor Roller Replacement
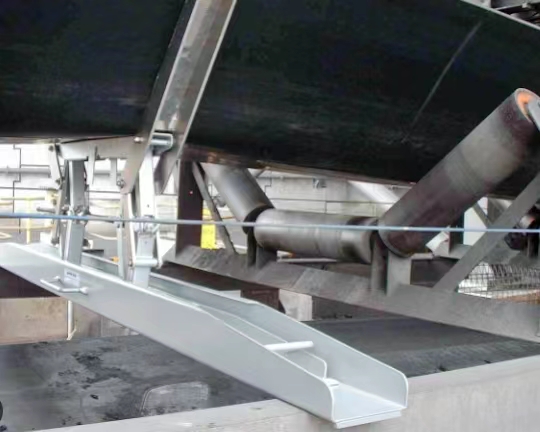
Amazon, a leader in the e-commerce industry, operates numerous fulfillment centers worldwide, processing millions of orders daily. With such high demand, the efficiency and reliability of their conveyor systems are paramount. One notable example of a successful conveyor roller replacement at Amazon involved upgrading their conveyor systems to handle increased order volumes during peak seasons.
Scenario: Amazon’s fulfillment center in Phoenix, Arizona, experienced significant wear and tear on their conveyor rollers due to the constant high volume of packages. The challenge was to replace the damaged rollers without disrupting the fulfillment process.
Solution: Amazon partnered with a reputable conveyor roller manufacturer to source high-quality, heavy-duty replacement rollers. The replacement process was meticulously planned to occur during off-peak hours to minimize impact on operations. Technicians used precise measurements to ensure the new rollers fit perfectly, and the process included thorough testing to verify proper installation.
Lessons Learned: The key takeaway from Amazon’s experience is the importance of high-quality replacement parts and meticulous planning. By scheduling replacements during off-peak hours and using durable rollers, Amazon was able to enhance the efficiency and longevity of their conveyor systems.
Airport Baggage Handling: Heathrow Airport’s Conveyor Roller Replacement
Heathrow Airport, one of the busiest airports in the world, relies on a sophisticated baggage handling system to ensure passengers’ luggage reaches the correct destination efficiently. The airport faced a critical need to replace aging conveyor rollers that were impacting the speed and reliability of the baggage handling process.
Scenario: The existing conveyor rollers at Heathrow’s Terminal 5 were experiencing frequent breakdowns, leading to delays and increased maintenance costs. The goal was to replace these rollers with minimal disruption to airport operations.
Solution: Heathrow Airport contracted a specialized company with expertise in airport conveyor systems. The new rollers were custom-designed to withstand the high demands of airport baggage handling. The replacement process was executed in phases, with each phase carefully planned to coincide with periods of lower passenger traffic. Advanced tracking and testing methods were used to ensure the new rollers met stringent performance standards.
Lessons Learned: Heathrow Airport’s case highlights the importance of using custom-designed replacement rollers tailored to specific operational demands. Phased implementation and rigorous testing ensured that the new system was both efficient and reliable, significantly reducing downtime and maintenance costs.
Food Processing Industry: Nestlé’s Conveyor Roller Replacement
Nestlé, a global leader in the food processing industry, operates numerous plants where hygiene and efficiency are paramount. One of their facilities faced challenges with conveyor rollers that were not meeting the strict hygiene standards required for food processing.
Scenario: At Nestlé’s production plant in California, the conveyor rollers were corroding and contaminating the food products. The challenge was to replace these rollers with materials that could withstand the harsh cleaning processes while maintaining food safety standards.
Solution: Nestlé collaborated with a supplier specializing in food-grade conveyor components. They selected rollers made from stainless steel with a smooth, corrosion-resistant finish. The replacement was carried out in a controlled environment to avoid any contamination during the process. Post-replacement, the new rollers were subjected to stringent hygiene and performance tests.
Lessons Learned: The success of Nestlé’s conveyor roller replacement underscores the necessity of selecting materials that meet industry-specific standards. Stainless steel rollers provided the durability and hygiene required for food processing, demonstrating the importance of material selection in replacement projects.
Mining Operations: Rio Tinto’s Conveyor Roller Replacement
Rio Tinto, a major player in the mining industry, operates in some of the harshest environments. Their conveyor systems must transport heavy loads of raw materials over long distances, often in extreme conditions.
Scenario: At one of Rio Tinto’s mining sites in Australia, the conveyor rollers were frequently breaking down due to the abrasive nature of the transported materials and the harsh environmental conditions. The objective was to replace these rollers with more robust alternatives.
Solution: Rio Tinto opted for heavy-duty conveyor rollers designed with reinforced materials and advanced sealing systems to protect against dust and moisture. The replacement project was planned to minimize downtime, with old rollers replaced incrementally during scheduled maintenance windows. Advanced monitoring systems were also installed to track roller performance and preemptively address potential issues.
Lessons Learned: Rio Tinto’s experience illustrates the critical role of robust materials and advanced technology in conveyor roller replacement. The use of reinforced rollers and proactive monitoring significantly improved the reliability and lifespan of the conveyor system.
Need conveyor rollers? Reach out for expert assistance.
Recycling Facilities: Waste Management Inc.’s Conveyor Roller Replacement
Waste Management Inc., a leading provider of comprehensive waste management services, operates large recycling facilities that require efficient sorting and transport systems.
Scenario: The conveyor rollers in one of Waste Management’s recycling plants were failing frequently due to the diverse and abrasive nature of the materials being processed. The aim was to replace these rollers to improve system efficiency and reduce maintenance costs.
Solution: Waste Management sourced high-durability rollers with specialized coatings to resist wear and tear. The replacement process involved detailed planning to ensure minimal disruption to the recycling operations. The new rollers were tested for compatibility with the existing system and adjusted as necessary.
Lessons Learned: The successful roller replacement at Waste Management’s facility highlights the importance of using durable, coated rollers for handling diverse materials. Proper planning and testing ensured that the new rollers enhanced system efficiency and longevity.
These real-world examples of conveyor roller replacement across different industries demonstrate the critical factors for success: high-quality replacement parts, meticulous planning, and industry-specific solutions. By learning from these cases, businesses can implement effective roller replacement strategies to ensure the reliability and efficiency of their conveyor systems.
FAQs about Conveyor Roller Replacement
Rollers on a conveyor, often referred to as conveyor rollers, play a crucial role in any conveyor system. They are cylindrical devices that rotate around a central axis and move objects along a flat or inclined path. Conveyor rollers are primarily used to transport bulk materials, packages, or objects from one place to another with minimal effort. These rollers are made from various materials, including steel, plastic, rubber, and more, depending on their application requirements. Conveyor rollers can come in many sizes, shapes, and designs to accommodate different types of loads and operating conditions. They are essential to numerous industries, such as manufacturing, distribution, food and beverage, pharmaceutical, and more.
A roller conveyor is a type of conveyor system where materials are carried on a series of rollers which are set at fixed or variable distances apart. The rollers work to aid the transfer of goods, providing a stable surface that enables items to be moved with minimal friction and effort. Roller conveyors are commonly used in warehouses, material handling facilities, manufacturing plants, and other industrial applications. There are different types of roller conveyors, including gravity roller conveyors, driven roller conveyors, accumulation roller conveyors, and more, each designed for specific applications. They are durable, easy to install, and can be customized based on the individual needs of a business.
Designing a conveyor roller involves considerations of several important parameters to ensure optimal performance. These include the roller’s diameter, length, load capacity, and speed, among other things. While each may require a specific calculation, a general formula used to determine the speed of a conveyor roller is: Speed = Distance/Time. It’s important to note that calculating the full specifications of a conveyor roller requires more in-depth knowledge of mechanical engineering principles and can also depend highly on the specific needs and the operating conditions of the system. For intricate calculation or designing a bespoke system, professionals should be consulted.
Maintaining conveyor rollers is essential to ensure their optimal performance and longevity. Regular inspections should be conducted to evaluate the condition of the rollers and the conveyor system as a whole. Check for signs of wear, damage, or incorrect alignment. It’s important to replace worn or broken rollers immediately to prevent whole system breakdown. Keeping the rollers clean is also vital, making sure they are free from debris that could cause jams or friction. Lubrication may be another essential maintenance step for certain types of rollers – always follow the manufacturer’s recommendation for this. Finally, ensuring that the conveyor is being used within its specified load capacity will help maintain the integrity and lifespan of the rollers and system overall.
The lifespan of a conveyor roller varies depending on several factors, including the material quality, operating conditions, maintenance practices, and the specific application. Typically, high-quality conveyor rollers made from precision bearings and quality steel can last anywhere from several years to over a decade under normal operating conditions.
Factors that can influence the lifespan include:
Load and Frequency of Use: Rollers subjected to heavy loads and constant use will wear out faster than those under lighter loads and intermittent use. It’s crucial to choose rollers designed to handle the expected load and usage frequency.
Environmental Conditions: Rollers operating in harsh environments, such as those exposed to extreme temperatures, moisture, chemicals, or abrasive materials, may have a reduced lifespan. Using rollers with appropriate protective coatings or materials can mitigate these effects.
Maintenance Practices: Regular maintenance, including cleaning, lubrication, and inspections, can significantly extend the lifespan of conveyor rollers. Identifying and addressing issues such as misalignment, wear, and damage early can prevent premature failure.
Installation Quality: Proper installation ensures that rollers function optimally. Misaligned or improperly secured rollers can lead to uneven wear and early failure.
Investing in high-quality rollers and adhering to a strict maintenance schedule can maximize their lifespan, providing reliable performance for many years.
Conveyor rollers are measured based on several key dimensions, which are critical for ensuring compatibility with the conveyor system. The primary measurements include:
Roller Length: This is the measurement from one end of the roller to the other, excluding the shaft or axle ends. It is important to measure this accurately to ensure the roller fits within the conveyor frame without causing misalignment or operational issues.
Diameter: The diameter of the roller is measured across its outer surface. This measurement is crucial because it affects the roller’s capacity to support loads and the overall stability of the conveyor system.
Axle Diameter: The diameter of the roller’s axle or shaft needs to be measured to ensure compatibility with the conveyor’s bearing or mounting brackets.
Axle Length and Type: Axle length is the measurement from end to end, including any protrusions beyond the roller body. The type of axle (spring-retained, fixed, etc.) also needs to be specified.
Material and Coating: While not a dimensional measurement, specifying the roller material (e.g., steel, rubber-coated) and any special coatings (e.g., corrosion-resistant) is important for ensuring the roller meets the operational requirements.
Accurate measurement of these dimensions is essential for ordering replacement rollers and ensuring seamless integration into the existing conveyor system.
Conveyor rollers are typically attached to the conveyor frame or structure using several methods, depending on the design of the conveyor system and the type of rollers. Here are common methods for attaching conveyor rollers:
Spring-Retained Axles: Many rollers feature spring-retained axles that allow for easy installation and removal. To attach these rollers, the spring-loaded ends of the axle are compressed, allowing the roller to be positioned between the conveyor frame brackets. When the pressure is released, the spring expands, securing the roller in place.
Set Screws and Locking Collars: Some rollers are attached using set screws or locking collars that secure the axle to the conveyor frame. This method provides a more permanent installation and is often used in applications where rollers need to be firmly fixed in place.
Bearing Mounts: In some conveyor systems, rollers are installed into bearing mounts or housings that are fixed to the conveyor frame. The bearings provide smooth rotation and are secured using bolts or other fasteners.
Retaining Clips or Pins: For certain roller designs, retaining clips or pins are used to hold the rollers in place. These clips or pins are inserted through the frame and the axle ends, preventing the rollers from moving laterally.
Bolt-On Axles: In heavy-duty applications, rollers may have bolt-on axles that are directly attached to the conveyor frame using bolts. This method provides a robust and secure attachment, suitable for high-load scenarios.
The choice of attachment method depends on the specific requirements of the conveyor system, including load capacity, ease of maintenance, and operational conditions. Proper attachment ensures that rollers remain securely in place, providing reliable and efficient performance.
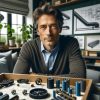
Jordan Smith, a seasoned professional with over 20 years of experience in the conveyor system industry. Jordan’s expertise lies in providing comprehensive solutions for conveyor rollers, belts, and accessories, catering to a wide range of industrial needs. From initial design and configuration to installation and meticulous troubleshooting, Jordan is adept at handling all aspects of conveyor system management. Whether you’re looking to upgrade your production line with efficient conveyor belts, require custom conveyor rollers for specific operations, or need expert advice on selecting the right conveyor accessories for your facility, Jordan is your reliable consultant. For any inquiries or assistance with conveyor system optimization, Jordan is available to share his wealth of knowledge and experience. Feel free to reach out at any time for professional guidance on all matters related to conveyor rollers, belts, and accessories.