Innovative Rubber Conveyor Belt Technologies in 2024
A rubber conveyor belt is a crucial component in many industrial applications, providing an efficient means of transporting materials across various stages of production and logistics. The rubber conveyor belt is valued for its durability, flexibility, and resistance to harsh conditions, making it suitable for heavy-duty tasks. Typically made from natural or synthetic rubber, these belts are reinforced with layers of fabric or metal to enhance their strength and longevity. Industries such as mining, agriculture, manufacturing, and transportation rely heavily on rubber conveyor belts to ensure seamless operations. Selecting the right rubber conveyor belt involves considering factors like load capacity, environmental conditions, and specific application needs to ensure optimal performance and efficiency.
Selecting the Right Rubber Conveyor Belt
Choosing the appropriate rubber conveyor belt is crucial for the efficiency, safety, and longevity of your operations. A rubber conveyor belt is a versatile and durable solution for various material handling applications, but selecting the right one requires careful consideration of several factors. This section will provide tips for choosing the appropriate rubber conveyor belt for different applications, highlight key features to look for in a high-quality belt, and emphasize the importance of working with reputable manufacturers and suppliers.
Tips for Choosing the Appropriate Rubber Conveyor Belt for Various Applications
Selecting the right rubber conveyor belt involves understanding the specific requirements of your application and the environment in which the belt will operate. Here are some essential tips to help you make an informed decision:
Assess the Material to be Transported
The type and characteristics of the material being transported play a significant role in determining the suitable rubber conveyor belt. Consider factors such as the weight, size, abrasiveness, and temperature of the material. For example, if you are handling heavy and abrasive materials like ore or coal, you will need a belt with high abrasion resistance and durability.
Determine the Operating Conditions
The environment in which the rubber conveyor belt will operate is another critical factor. Consider the temperature range, exposure to chemicals, moisture levels, and potential for impact or puncture. For high-temperature applications, choose a heat-resistant conveyor belt material. If the belt will be exposed to chemicals, opt for a chemical-resistant variant.
Evaluate the Load and Speed Requirements
The load capacity and speed at which the belt will operate are essential considerations. Ensure that the rubber conveyor belt can handle the maximum load without excessive stretching or wear. The belt’s speed should also match the system’s requirements to maintain efficient and smooth operation.
Consider the Belt’s Flexibility and Tension
Flexibility and tension are vital for ensuring that the rubber conveyor belt can navigate through curves and bends in the conveyor system without compromising performance. Select a belt with appropriate flexibility to suit the layout of your conveyor system. Proper tension is necessary to prevent slippage and ensure efficient material transport.
Key Features to Look for in a High-Quality Rubber Conveyor Belt
When selecting a rubber conveyor belt, it’s essential to consider certain features that indicate high quality and reliable performance. Here are some key features to look for:
Durability and Abrasion Resistance
A high-quality rubber conveyor belt should exhibit excellent durability and resistance to abrasion. This ensures that the belt can withstand the rigors of continuous operation and the abrasive nature of certain materials. Look for belts reinforced with multiple layers of fabric or steel to enhance their strength and longevity.
Heat and Chemical Resistance
For applications involving high temperatures or exposure to chemicals, choose a rubber conveyor belt with heat and chemical resistance. These belts are specially formulated to maintain their integrity and performance under challenging conditions. Heat-resistant belts can operate at elevated temperatures without deforming or losing strength, while chemical-resistant belts can withstand corrosive substances.
Anti-Static and Fire-Resistant Properties
Safety is paramount in industrial operations, so it’s essential to select rubber conveyor belts with anti-static and fire-resistant properties when needed. Anti-static belts help prevent the buildup of static electricity, reducing the risk of sparks and fires. Fire-resistant belts are designed to resist ignition and prevent the spread of flames, ensuring safer operation in environments where fire hazards are present.
Flexibility and Adaptability
A high-quality rubber conveyor belt should offer flexibility and adaptability to suit various conveyor system designs. This includes the ability to navigate curves, bends, and inclines without compromising performance. Flexible belts ensure smooth operation and reduce the risk of mechanical failures and downtime.
Easy Maintenance and Repair
Maintenance and repair are crucial for the longevity and efficiency of a rubber conveyor belt. Choose belts that are easy to maintain and repair, with modular designs that allow for quick replacement of damaged sections. This minimizes downtime and ensures that the conveyor system remains operational with minimal disruptions.
Importance of Working with Reputable Manufacturers and Suppliers
Collaborating with reputable manufacturers and suppliers is essential for obtaining high-quality rubber conveyor belts that meet your specific needs. Here are some reasons why it’s important to choose trusted partners:
Assurance of Quality and Reliability
Reputable manufacturers and suppliers have a proven track record of delivering high-quality products. They adhere to stringent quality control standards and use premium materials to ensure that their rubber conveyor belts offer reliable performance and durability. By working with trusted partners, you can be confident that the belts you receive will meet your expectations and withstand the demands of your applications.
Access to Technical Expertise and Support
Established manufacturers and suppliers provide valuable technical expertise and support throughout the selection and installation process. They can offer guidance on choosing the right rubber conveyor belt for your specific requirements and provide insights into optimizing your conveyor system for maximum efficiency. Access to expert support ensures that you make informed decisions and receive solutions tailored to your needs.
Availability of Customized Solutions
Every industrial application has unique requirements, and reputable manufacturers can offer customized rubber conveyor belt solutions to meet those needs. They can design and produce belts with specific features, dimensions, and properties to match your operational conditions. Customization ensures that you get a conveyor belt that fits seamlessly into your system and delivers optimal performance.
Comprehensive Warranty and After-Sales Service
Working with reputable manufacturers and suppliers provides the benefit of comprehensive warranty coverage and after-sales service. This ensures that any issues or defects are promptly addressed, and you receive the necessary support to maintain and repair your rubber conveyor belts. Reliable after-sales service enhances the longevity and performance of your conveyor system, reducing the risk of costly downtime.
Exploring the Versatile Applications of Rubber Conveyor Belts
A rubber conveyor belt is an essential component in various industries, known for its durability, flexibility, and reliability. These belts are designed to transport materials efficiently and safely, making them indispensable in numerous sectors. This article explores the diverse applications of rubber conveyor belts, highlighting their significance in industrial, agricultural, and other key sectors.
Applications of Rubber Conveyor Belts
Industrial Uses: Manufacturing, Mining, and Logistics
Rubber conveyor belts are widely used in the industrial sector due to their ability to handle heavy loads, resist wear and tear, and operate under extreme conditions. Here are some key industrial applications:
Manufacturing: In manufacturing facilities, rubber conveyor belts are used to streamline production processes by transporting raw materials, components, and finished products between different stages of production. These belts help in reducing manual handling, thereby increasing efficiency and minimizing the risk of workplace injuries. For instance, in the automotive industry, rubber conveyor belts are used to move car parts through assembly lines, ensuring a smooth and continuous workflow.
Mining: The mining industry relies heavily on rubber conveyor belts to transport extracted materials such as coal, ore, and aggregates over long distances. These belts are designed to withstand harsh conditions, including abrasion, impact, and exposure to chemicals. Rubber conveyor belts in mining operations help in improving productivity by allowing continuous material flow, reducing the need for manual transport, and ensuring the safety of workers. They are also used in underground mining operations where the belts must navigate tight spaces and steep inclines.
Logistics: In logistics and warehousing, rubber conveyor belts play a crucial role in the efficient movement of goods. These belts are used in sorting facilities, distribution centers, and warehouses to transport packages, pallets, and other items. The use of rubber conveyor belts in logistics helps in speeding up the sorting and distribution process, reducing handling time, and increasing overall operational efficiency. For example, in an e-commerce fulfillment center, rubber conveyor belts help in quickly moving packages from storage areas to shipping docks, ensuring timely delivery to customers.
Agricultural Uses: Handling Crops, Grains, and Machinery
The agricultural sector benefits greatly from the use of rubber conveyor belts, which aid in the efficient handling of crops, grains, and machinery. Here are some key applications in agriculture:
Handling Crops: Rubber conveyor belts are used in various stages of crop handling, from harvesting to processing. During harvesting, these belts are used in combine harvesters and other agricultural machinery to transport crops such as wheat, corn, and soybeans from the fields to storage areas. This helps in reducing manual labor and increasing the speed of harvest operations. In processing plants, rubber conveyor belts transport crops through cleaning, sorting, and packaging processes, ensuring a seamless workflow and reducing the risk of damage to delicate products.
Grains: In grain handling and storage facilities, rubber conveyor belts are essential for moving grains efficiently and safely. These belts are used to transport grains from silos to processing plants, mills, and packaging facilities. The use of rubber conveyor belts helps in preventing grain spillage, reducing handling losses, and maintaining the quality of the grains. Additionally, rubber conveyor belts are used in grain elevators, where they move large quantities of grains vertically, saving time and labor.
Machinery: Rubber conveyor belts are also used in various types of agricultural machinery, such as balers, combine harvesters, and grain augers. These belts ensure the smooth operation of machinery by transporting materials and reducing the need for manual handling. For example, in a baler, rubber conveyor belts are used to move cut hay or straw through the machine, forming compact bales for easy transport and storage. This not only increases efficiency but also helps in maintaining the quality of the harvested material.
Other Sectors: Food Processing, Construction, and Automotive Industries
Beyond industrial and agricultural uses, rubber conveyor belts are also crucial in several other sectors. Here are some notable applications:
Food Processing: In the food processing industry, rubber conveyor belts are used to transport a wide range of food products, from raw ingredients to packaged goods. These belts are designed to meet strict hygiene and safety standards, ensuring that food products are transported in a clean and sanitary manner. Rubber conveyor belts are used in various stages of food processing, including washing, sorting, cutting, cooking, and packaging. For example, in a meat processing plant, rubber conveyor belts transport carcasses through different stages of processing, ensuring efficient and hygienic handling. Additionally, these belts are used in bakeries to move dough and baked goods through ovens and cooling lines.
Construction: The construction industry utilizes rubber conveyor belts for the transport of construction materials such as sand, gravel, cement, and bricks. These belts are essential for moving materials efficiently on construction sites, reducing the need for manual labor and speeding up construction projects. Rubber conveyor belts are used in various construction equipment, such as concrete mixers, brick-making machines, and portable conveyors. For instance, in concrete mixers, rubber conveyor belts are used to transport sand and gravel to the mixing chamber, ensuring a consistent supply of materials and improving the efficiency of the mixing process.
Automotive Industries: In the automotive industry, rubber conveyor belts are used extensively in manufacturing and assembly processes. These belts transport car parts, engines, and other components through different stages of production, ensuring a smooth and continuous workflow. Rubber conveyor belts help in reducing manual handling, increasing production speed, and improving the overall efficiency of the assembly line. Additionally, these belts are used in the final inspection and testing stages, where they transport finished vehicles through quality control checks. For example, rubber conveyor belts are used to move cars through paint booths, ensuring even and consistent application of paint and reducing the risk of defects.
How about Manufacturing Process of Rubber Conveyor Belts
The manufacturing process of a rubber conveyor belt is a complex and precise procedure that involves several stages to ensure the final product is durable, reliable, and capable of meeting the demands of various industrial applications. As a key component in material handling systems, the quality and performance of a rubber conveyor belt depend on the meticulous execution of each manufacturing step. This section will provide a detailed explanation of the vulcanization process, the materials used in the production of rubber conveyor belts, and the quality control measures implemented to ensure their durability and performance.
The Vulcanization Process
Vulcanization is a critical step in the manufacturing of rubber conveyor belts, where raw rubber is transformed into a more durable and elastic material through a chemical process. This process involves the addition of sulfur or other curatives to the raw rubber, followed by the application of heat and pressure.
Steps in the Vulcanization Process
- Mixing: The process begins with the mixing of raw rubber with various chemicals, including sulfur, accelerators, and antioxidants. This mixture, known as a rubber compound, is thoroughly blended to ensure even distribution of the curatives.
- Calendering: The mixed rubber compound is then passed through a series of rollers in a process called calendering. This step involves pressing the rubber into thin sheets of uniform thickness. These sheets will form the layers of the conveyor belt.
- Layering: Multiple layers of rubber sheets are combined, often with reinforcement materials such as fabric or steel cords sandwiched between them. This reinforcement provides additional strength and stability to the rubber conveyor belt.
- Molding and Shaping: The layered sheets are then placed into molds that define the final shape and size of the conveyor belt. The molds are designed to ensure precise dimensions and consistent quality.
- Curing: The most critical phase of vulcanization is curing, where the molded rubber is subjected to heat and pressure in a vulcanizing press. The temperature and pressure cause the sulfur to form cross-links between the rubber molecules, transforming the compound into a more robust and elastic material. This step enhances the tensile strength, elasticity, and durability of the rubber conveyor belt.
- Cooling and Finishing: After curing, the belt is allowed to cool and is then removed from the mold. The edges are trimmed, and any excess material is removed to ensure a smooth and uniform surface. The belt is then subjected to various finishing processes, such as embossing or adding a protective coating, depending on its intended application.
Materials Used in the Production of Rubber Conveyor Belts
The selection of materials is crucial in the production of high-quality rubber conveyor belts. The materials used must provide the necessary properties to withstand the operational demands of the belt’s application.
Raw Rubber
The primary material used in the production of rubber conveyor belts is raw rubber, either natural or synthetic. Natural rubber is derived from the latex of rubber trees, while synthetic rubber is produced from petrochemicals. Each type of rubber has its advantages, with natural rubber offering excellent elasticity and abrasion resistance, and synthetic rubber providing enhanced durability and resistance to chemicals and heat.
Reinforcement Materials
To improve the strength and stability of rubber belting conveyor belt, reinforcement materials are incorporated into the rubber layers. Common reinforcement materials include:
- Fabric: Polyester, nylon, and cotton fabrics are often used to reinforce rubber conveyor belts. These materials provide flexibility and resistance to tearing and stretching.
- Steel Cords: For applications requiring high tensile strength, such as mining and heavy industrial use, steel cords are embedded within the rubber layers. Steel cords offer superior strength and durability, allowing the belts to handle heavy loads and harsh conditions.
Additives and Curatives
Various chemicals and additives are used in the rubber compound to enhance the properties of the final product. These include:
- Sulfur: Used as a primary vulcanizing agent to create cross-links in the rubber molecules.
- Accelerators: Chemicals that speed up the vulcanization process, reducing the time and energy required for curing.
- Antioxidants: Compounds added to prevent the degradation of rubber caused by exposure to oxygen, heat, and light.
- Fillers: Materials such as carbon black and silica are added to improve the mechanical properties and durability of the rubber conveyor belt.
Quality Control Measures to Ensure Durability and Performance
Ensuring the durability and performance of rubber conveyor belts requires stringent quality control measures throughout the manufacturing process. These measures are designed to detect and eliminate defects, ensuring that each belt meets the required standards and specifications.
Material Inspection
Quality control begins with the inspection of raw materials. All incoming materials, including raw rubber, reinforcement fabrics, and chemicals, are tested for purity and quality. This ensures that only high-quality materials are used in the production process.
In-Process Monitoring
During the manufacturing process, various in-process checks are conducted to monitor the quality of the rubber compound and the calendered sheets. This includes checking the thickness, uniformity, and composition of the rubber layers. Any deviations from the specified standards are immediately corrected to prevent defects in the final product.
Vulcanization Control
The vulcanization process is closely monitored to ensure that the temperature, pressure, and curing time are precisely controlled. This is critical for achieving the desired properties of the rubber conveyor belt. Advanced sensors and control systems are used to maintain optimal conditions during vulcanization.
Final Inspection and Testing
Once the rubber conveyor belts are produced, they undergo rigorous final inspection and testing. This includes visual inspections to detect surface defects, as well as mechanical tests to assess tensile strength, elongation, and abrasion resistance. The belts are also tested for flexibility, impact resistance, and heat tolerance to ensure they meet the specific requirements of their intended application.
Continuous Improvement
Quality control is an ongoing process that involves continuous improvement initiatives. Feedback from customers and field performance data are used to identify areas for improvement in the manufacturing process. This helps manufacturers refine their techniques and develop new products that offer even better performance and reliability.
The Versatility of Rubber Conveyor Belts: Types and Comparisons
A rubber conveyor belt is a critical component in various industries, known for its durability, flexibility, and adaptability. These belts are designed to efficiently transport materials and goods, making them indispensable in many sectors. In this article, we will explore the different types of mining conveyor belts available, compare rubber conveyor belting with other materials like metal and plastic, and discuss the factors to consider when choosing the right type of conveyor belt for specific needs.
Types of Conveyor Belts
Overview of Different Types of Conveyor Belts Available
Conveyor belts come in various types, each designed to meet specific operational requirements and environmental conditions. Some of the most common types include:
Rubber Conveyor Belts: These are the most widely used type of conveyor belts, known for their flexibility, durability, and resistance to wear and tear. They are suitable for a wide range of applications, including industrial, agricultural, and mining operations. Rubber conveyor belts can handle heavy loads, resist abrasion, and operate in harsh environments.
Metal Conveyor Belts: Made from stainless steel, aluminum, or other metals, these belts are used in applications that require high strength and resistance to heat, corrosion, and chemicals. Metal conveyor belts are commonly used in food processing, manufacturing, and pharmaceutical industries where hygiene and durability are critical.
Plastic Conveyor Belts: These belts are lightweight, corrosion-resistant, and easy to clean, making them ideal for applications in the food and beverage, pharmaceutical, and packaging industries. Plastic conveyor belts are also used in environments where the belt needs to be flexible and operate at high speeds.
Fabric Conveyor Belts: Composed of woven fabrics such as polyester, nylon, or cotton, these belts are used in applications that require lightweight and flexible material handling. Fabric conveyor belts are commonly used in logistics, warehousing, and light manufacturing operations.
Modular Conveyor Belts: These belts consist of interlocking plastic modules that can be easily replaced or reconfigured. They are highly versatile and used in industries such as automotive, packaging, and material handling where customization and maintenance efficiency are essential.
Comparison of Rubber Belts with Other Materials
Aspect | Rubber Conveyor Belts | Metal Conveyor Belts | Aspect | Rubber Conveyor Belts | Metal Conveyor Belts | Aspect | Rubber Conveyor Belts | Metal Conveyor Belts |
Durability | High flexibility, absorbs impacts well. | Superior durability, withstands high temperatures and corrosion. | Durability | High flexibility, absorbs impacts well. | Superior durability, withstands high temperatures and corrosion. | Durability | High flexibility, absorbs impacts well. | Superior durability, withstands high temperatures and corrosion. |
Flexibility | Highly flexible, suitable for heavy loads and rough handling. | Less flexible, ideal for specific industrial applications. | Flexibility | Highly flexible, suitable for heavy loads and rough handling. | Less flexible, ideal for specific industrial applications. | Flexibility | Highly flexible, suitable for heavy loads and rough handling. | Less flexible, ideal for specific industrial applications. |
Maintenance | Requires less maintenance. | Prone to rust, requires regular lubrication. | Maintenance | Requires less maintenance. | Prone to rust, requires regular lubrication. | Maintenance | Requires less maintenance. | Prone to rust, requires regular lubrication. |
Cost | More cost-effective (initial and long-term). | Higher cost due to durability and specialized applications. | Cost | More cost-effective (initial and long-term). | Higher cost due to durability and specialized applications. | Cost | More cost-effective (initial and long-term). | Higher cost due to durability and specialized applications. |
Application Suitability | Versatile, used in a wide range of industries. | Preferred in environments needing hygiene, high temperature, and chemical resistance. | Application Suitability | Versatile, used in a wide range of industries. | Preferred in environments needing hygiene, high temperature, and chemical resistance. | Application Suitability | Versatile, used in a wide range of industries. | Preferred in environments needing hygiene, high temperature, and chemical resistance. |
Factors to Consider When Choosing the Type of Conveyor Belt
When selecting the appropriate conveyor belt for a specific application, several factors must be considered:
Load Capacity: Determine the weight and size of the materials to be transported. Rubber conveyor belts are ideal for heavy loads, while plastic and fabric belts are suitable for lighter materials.
Environmental Conditions: Consider the operating environment, including temperature, humidity, and exposure to chemicals or abrasive materials. Rubber belts offer excellent resistance to harsh conditions, while plastic belts are preferred for environments requiring high hygiene standards.
Flexibility and Durability: Assess the need for flexibility in the conveyor system. Rubber belts provide good flexibility and impact resistance, making them suitable for various industrial applications. Metal belts, though less flexible, offer superior durability for specific uses.
Maintenance Requirements: Evaluate the maintenance needs and costs associated with different types of conveyor belts. Rubber belts generally require less maintenance compared to metal belts, which can be more expensive to upkeep.
Application Specificity: Consider the specific requirements of the application, such as speed, hygiene, and ease of cleaning. Plastic belts are ideal for high-speed and hygienic environments, while rubber belts are better suited for heavy-duty applications.
Cost: Finally, consider the cost implications, including initial investment and long-term maintenance expenses. Rubber conveyor belts are often more cost-effective, but the choice should be based on the overall cost-benefit analysis specific to the application.
The Types of Rubber Conveyor Belt Characteristics
Rubber conveyor belts are integral components in various industries, known for their versatility, durability, and adaptability. As a fundamental part of material handling systems, rubber conveyor belts ensure the efficient and safe transportation of materials. This section will provide a comprehensive description of rubber belts, explore their properties, highlight the advantages of using rubber belts, and discuss their common applications across different industries.
Description and Properties of Rubber Belts
Rubber conveyor belts are made from natural or synthetic rubber, often reinforced with layers of fabric or metal to enhance their strength and durability. The primary purpose of these belts is to transport materials efficiently and safely from one point to another within industrial settings.
Composition of Rubber Belts
The composition of rubber conveyor belts typically includes:
- Top Cover: The outer layer that comes into direct contact with the materials being transported. It is designed to withstand abrasion, impact, and various environmental conditions.
- Carcass: The core of the belt, which provides structural support and strength. It is usually made from layers of fabric (such as polyester, nylon, or cotton) or metal cords (steel) that are embedded within the rubber.
- Bottom Cover: The underside layer of the belt, which helps to protect the carcass and improve the belt’s grip on the conveyor rollers.
Properties of Rubber Belts
Rubber conveyor belts possess several key properties that make them suitable for a wide range of applications:
- Durability: Rubber belts are highly durable and resistant to wear and tear, making them ideal for heavy-duty applications. They can withstand continuous operation and the abrasive nature of certain materials.
- Flexibility: The flexibility of rubber belts allows them to navigate through complex conveyor systems with curves, bends, and inclines without losing their structural integrity.
- Heat Resistance: Certain types of rubber conveyor belts are formulated to resist high temperatures, making them suitable for applications involving hot materials.
- Chemical Resistance: Rubber belts can be designed to resist chemicals and corrosive substances, ensuring longevity in environments where such exposure is common.
- Anti-Static and Fire-Resistant Properties: For applications where static electricity and fire hazards are concerns, rubber belts can be manufactured with anti-static and fire-resistant properties to enhance safety.
Advantages of Using Rubber Belts
Rubber conveyor belts offer numerous advantages that make them a preferred choice in various industrial applications. These advantages include:
Durability and Longevity
One of the primary benefits of using rubber conveyor belts is their exceptional durability. The robust nature of rubber, especially when reinforced with fabric or metal, ensures that these belts can endure the rigors of continuous operation and harsh environmental conditions. This durability translates to a longer lifespan, reducing the need for frequent replacements and minimizing downtime.
Flexibility and Versatility
Rubber conveyor belts are highly flexible and versatile, capable of handling a wide range of materials and operating conditions. Their ability to bend and flex without breaking makes them suitable for conveyor systems with curves and inclines. This versatility allows rubber belts to be used in diverse applications, from light-duty tasks to heavy-duty industrial operations.
Heat and Chemical Resistance
For applications involving high temperatures or exposure to chemicals, rubber conveyor belts offer excellent resistance. Heat-resistant rubber belts can operate at elevated temperatures without deforming or losing strength, making them ideal for industries such as metallurgy and foundries. Similarly, chemical-resistant belts can withstand corrosive substances, ensuring reliability and longevity in chemical processing plants.
Enhanced Safety Features
Rubber conveyor belts can be manufactured with anti-static and fire-resistant properties to enhance safety in environments where these hazards are present. Anti-static belts prevent the buildup of static electricity, reducing the risk of sparks and potential fires. Fire-resistant belts are designed to resist ignition and prevent the spread of flames, ensuring safer operation in industries like grain handling and mining.
Cost-Effectiveness
The durability and longevity of rubber for conveyor belt contribute to their cost-effectiveness. By reducing the need for frequent replacements and minimizing maintenance costs, these belts offer a favorable return on investment. Additionally, their versatility and adaptability mean that one type of rubber belt can be used for multiple applications, further enhancing their cost-effectiveness.
Common Applications of Rubber Belts in Different Industries
Rubber conveyor belts are used in a wide range of industries due to their versatility and adaptability. Some of the most common applications include:
Mining Industry
In the mining industry, rubber conveyor belts are essential for transporting extracted materials such as coal, ore, and aggregates. These belts must be extremely durable to withstand the abrasive nature of these materials and the harsh environmental conditions. Rubber conveyor belts are favored in mining due to their ability to handle heavy loads and resist wear from sharp and rough materials.
Agriculture Industry
In agriculture, rubber conveyor belts are used for handling grains, seeds, and other agricultural products. These belts facilitate the efficient movement of goods through various stages of processing, from harvesting to packaging. The flexibility and durability of rubber belts ensure smooth operation and reduce the risk of product damage during transport.
Manufacturing Industry
The manufacturing industry relies heavily on conveyor belts for assembly lines and material handling. Rubber conveyor belts are used to transport products through different stages of production, ensuring efficiency and consistency. Their resistance to wear and ability to handle a variety of materials make them indispensable in manufacturing processes.
Food Processing Industry
In the food processing industry, belt rubber conveyors are used to transport raw materials and finished products through various stages of production. These belts must meet stringent hygiene and safety standards, often requiring easy cleaning and resistance to contamination. Food-grade rubber belts are designed to ensure the safe handling of food products, minimizing the risk of contamination and spoilage.
Construction Industry
Rubber conveyor belts are also widely used in the construction industry for transporting construction materials such as sand, gravel, and cement. These belts need to be robust and durable to handle the heavy loads and harsh conditions typically found on construction sites. Their flexibility and resistance to abrasion make them ideal for use in construction applications.
Logistics and Warehousing
In logistics and warehousing, rubber conveyor belts are used for sorting, handling, and transporting packages and goods. These belts ensure efficient movement and organization of items within warehouses and distribution centers. Their versatility allows them to handle a variety of products, from small packages to large boxes, making them an essential component in modern logistics operations.
The Significance of a Rubber Conveyor Belt in Various Industries
A rubber conveyor belt is a fundamental component in numerous industries, playing a crucial role in the efficient movement of materials and products. These belts are designed to transport goods smoothly and reliably, making them indispensable in many sectors. This article delves into the definition and importance of conveyor belts, the history and evolution of conveyor belt technology, and the critical aspects of selecting the right conveyor belt for specific applications.
Conveyor Belt Overview
Definition of Conveyor Belts and Their Significance in Various Industries
Conveyor belts are continuous loops of material that are used to move products and materials from one location to another. They are an integral part of material handling systems, enabling the efficient and automated transport of goods. Conveyor belts come in various materials, including rubber, metal, and plastic, each suited for different applications and environments.
Rubber conveyor belts, in particular, are renowned for their durability, flexibility, and resistance to wear and tear. These belts are used extensively in industries such as manufacturing, mining, agriculture, food processing, and logistics. In manufacturing, rubber conveyor belts help streamline production processes by transporting raw materials, components, and finished products between different stages. In mining, they facilitate the continuous movement of extracted materials, such as coal and ore, over long distances. In agriculture, rubber conveyor belts assist in handling crops and grains, reducing manual labor and increasing efficiency.
The significance of conveyor belts lies in their ability to enhance productivity, reduce labor costs, and minimize the risk of workplace injuries. By automating material transport, conveyor belts contribute to smoother operations and higher efficiency across various industries.
Brief History and Evolution of Conveyor Belt Technology
The history of conveyor belts dates back to the late 18th century, with simple systems used in agriculture and mining. Early conveyor belts were made from basic materials like leather and canvas. These early belts were used to transport bulk materials such as grain and coal, significantly improving efficiency and reducing the need for manual labor.
The advent of the Industrial Revolution in the 19th century brought about significant advancements in conveyor belt technology. The introduction of rubber as a primary material for conveyor belts marked a major milestone. Rubber offered superior durability, flexibility, and resistance to wear and tear compared to earlier materials. The development of vulcanization processes further enhanced the strength and longevity of rubber conveyor belts, making them suitable for heavy-duty applications.
In the 20th century, the introduction of synthetic materials such as nylon and polyester revolutionized the conveyor belt industry. These materials provided greater strength, flexibility, and resistance to environmental factors, further expanding the applications of conveyor belts. Innovations in belt design, such as the development of modular belts and heat-resistant belts, have continued to enhance the performance and versatility of conveyor belts.
Today, conveyor belts are used in a wide range of industries, from food processing and packaging to mining and logistics. Advances in technology have led to the creation of specialized conveyor belts tailored for specific applications, ensuring optimal performance and efficiency.
Importance of Selecting the Right Conveyor Belt for Specific Applications
Selecting the right conveyor belt is crucial for ensuring the efficiency and reliability of material handling systems. Several factors must be considered when choosing a conveyor belt for a specific application:
Material Compatibility: The material of the conveyor belt must be compatible with the type of goods or materials being transported. For example, rubber conveyor belts are ideal for heavy-duty applications and environments where abrasion resistance is essential. In contrast, plastic belts may be better suited for applications requiring high hygiene standards, such as food processing.
Operational Conditions: The operating environment plays a significant role in the selection of a conveyor belt. Factors such as temperature, humidity, and exposure to chemicals or abrasive materials must be taken into account. Rubber conveyor belts offer excellent resistance to harsh conditions, making them suitable for industrial and mining applications.
Load Capacity: The weight and size of the materials being transported influence the choice of conveyor belt. Rubber conveyor belts are designed to handle heavy loads, providing the necessary strength and durability for industrial applications. Lighter materials may require different types of belts, such as fabric or plastic belts, which offer greater flexibility and speed.
Maintenance Requirements: The maintenance needs and costs associated with different types of conveyor belts vary. Rubber conveyor belts typically require less maintenance compared to metal belts, which can be prone to rust and require regular lubrication. Considering the long-term maintenance costs is essential for choosing the most cost-effective solution.
Customization Options: Customization is another important factor to consider. Leading conveyor belt manufacturers offer belts tailored to the specific needs of different industries. Customization ensures that the conveyor belt meets the exact requirements of the application, enhancing efficiency and performance.
Cost Considerations: The initial investment and long-term operational costs must be weighed when selecting a conveyor belt. While rubber conveyor belts may have a higher upfront cost compared to some other materials, their durability and lower maintenance requirements often result in cost savings over time.
FAQS about Rubber Conveyor Belt
How to make a rubber conveyor belt?
Material Selection: High-quality rubber, often mixed with additives for enhanced properties, is chosen based on the belt’s intended use.
Compounding: The rubber is compounded with various chemicals to achieve the desired strength, flexibility, and resistance to wear and environmental factors.
Calendaring: The compounded rubber is processed through rollers (calendars) to produce thin sheets of uniform thickness. These sheets form the belt’s base layers.
Reinforcement: Layers of fabric or steel cords are embedded between the rubber sheets to provide additional strength and stability.
Vulcanization: The assembled layers are subjected to heat and pressure in a process called vulcanization, which bonds them together, enhancing the belt’s durability and elasticity.
Cutting and Finishing: The vulcanized belt is cut to the required width and length, and any additional features, such as cleats or sidewalls, are added.
Quality Control: The finished belt undergoes rigorous testing to ensure it meets the required specifications and standards.
What are rubber belts used for?
What are the three types of conveyor belts?
Flat Belt Conveyors: These are the most common type of conveyor belts, used to transport general materials across short and long distances. They consist of a continuous flat rubber or fabric belt running over pulleys.
Cleated Belt Conveyors: These belts have raised sections, or cleats, to help carry loose materials up steep inclines without slipping. Cleated belts are widely used in agricultural applications and for transporting materials like grains, sand, and gravel.
Modular Belt Conveyors: Made from interlocking plastic segments, modular belts are versatile and can be easily customized. They are ideal for applications requiring frequent cleaning, such as food processing and packaging.
Each type of conveyor belt is designed to meet specific requirements, ensuring efficiency and reliability in various industrial processes.
What is a rubber conveyor belt?
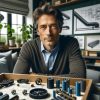
Jordan Smith, a seasoned professional with over 20 years of experience in the conveyor system industry. Jordan’s expertise lies in providing comprehensive solutions for conveyor rollers, belts, and accessories, catering to a wide range of industrial needs. From initial design and configuration to installation and meticulous troubleshooting, Jordan is adept at handling all aspects of conveyor system management. Whether you’re looking to upgrade your production line with efficient conveyor belts, require custom conveyor rollers for specific operations, or need expert advice on selecting the right conveyor accessories for your facility, Jordan is your reliable consultant. For any inquiries or assistance with conveyor system optimization, Jordan is available to share his wealth of knowledge and experience. Feel free to reach out at any time for professional guidance on all matters related to conveyor rollers, belts, and accessories.