How Head Pulleys Drive Conveyor Belt Systems
Head pulleys are critical components in conveyor systems, located at the discharge end where they drive the belt and propel materials forward. These pulleys are essential for providing the necessary traction to move the conveyor belt efficiently. Head pulleys are often lagged with rubber or ceramic to increase friction and reduce slippage, ensuring smooth operation. They play a vital role in maintaining belt tension and alignment, which are crucial for the overall performance and longevity of the conveyor system. Proper maintenance of head pulleys is important to prevent operational issues and to maximize the efficiency of material handling processes in various industries, such as mining, manufacturing, and food processing.
Enhancing Conveyor Systems with Head Pulleys
Snub Pulley
Explanation of the Snub Pulley’s Function in Increasing Belt Wrap
Snub pulleys are essential components in conveyor systems, especially in setups involving head pulleys. A snub pulley is typically located near the head pulley and serves a specific purpose: to increase the belt wrap around the head pulley. This increased wrap enhances the contact area between the conveyor belt and the head pulley, which is crucial for improving traction and preventing slippage.
How Snub Pulleys Increase Belt Wrap:
- Positioning: Snub pulleys are strategically placed close to the head pulley on the return side of the belt. Their primary function is to redirect the belt and increase the angle of wrap around the head pulley.
- Wrap Angle: The additional angle created by the snub pulley increases the belt’s surface contact with the head pulley. For example, if the head pulley has a wrap angle of 180 degrees, incorporating a snub pulley can increase this angle to 210 degrees or more, depending on the specific configuration.
- Enhanced Contact: The increased contact area ensures that more of the belt’s surface is engaged with the head pulley, which significantly enhances the traction force between the belt and the pulley.
Advantages of Using Snub Pulleys for Better Traction and Drive Efficiency
Integrating snub pulleys into a conveyor system that uses head pulley for conveyor offers several advantages, primarily related to improved traction and drive efficiency.
Better Traction
The primary advantage of using snub pulleys is the significant improvement in traction. Better traction ensures that the conveyor belt maintains its grip on the head pulley, which is essential for efficient and reliable operation.
- Reduced Slippage: By increasing the wrap angle, snub pulleys reduce the risk of belt slippage on the head pulley. This ensures a consistent speed and reduces the wear on both the belt and the pulley.
- Enhanced Load Handling: Improved traction allows the conveyor system to handle heavier loads more efficiently without the risk of the belt slipping or losing grip, which is crucial for high-capacity operations.
Improved Drive Efficiency
Another key advantage of snub pulleys is their ability to enhance drive efficiency. With better traction, the power from the drive motor is more effectively transferred to the conveyor belt, improving overall system efficiency.
- Energy Efficiency: Improved traction means less energy is wasted due to slippage, leading to more efficient power usage and potentially lower energy costs.
- Consistent Operation: Enhanced drive efficiency ensures that the conveyor belt operates smoothly and consistently, reducing the risk of operational disruptions and downtime.
Common Uses of Snub Pulleys in Various Conveyor Setups
Snub pulleys are versatile components used in a variety of conveyor setups across different industries. Their ability to improve traction and drive efficiency makes them valuable in several applications.
Mining and Aggregate Industry
In the mining and aggregate industry, conveyor systems are used to transport heavy materials such as ores, rocks, and minerals. Snub pulleys are critical in these setups to ensure the conveyor belts maintain proper traction and handle the heavy loads effectively.
- Heavy Load Transport: Snub pulleys help increase the belt’s grip on the head pulley, which is essential for transporting heavy materials without slippage.
- Harsh Conditions: These pulleys are designed to withstand the harsh conditions typical in mining operations, including extreme temperatures and abrasive materials.
Manufacturing and Assembly Lines
In manufacturing and assembly lines, conveyor systems are used to move products through various stages of production. Snub pulleys enhance the efficiency and reliability of these systems.
- Product Handling: By ensuring consistent belt movement, snub pulleys help maintain the smooth flow of products along the assembly line.
- Precision Operations: Improved traction ensures precise control of the conveyor belt speed, which is crucial for synchronized operations in manufacturing processes.
Food Processing Industry
In the food processing industry, conveyor systems must operate efficiently to handle perishable goods. Snub pulleys play a vital role in ensuring reliable and hygienic transport.
- Hygienic Transport: The enhanced grip provided by snub pulleys ensures that the conveyor belts operate smoothly, minimizing the risk of contamination due to belt slippage or disruptions.
- Efficient Processing: Improved drive efficiency helps maintain the speed and reliability of conveyor systems, which is essential for meeting production targets and maintaining food quality.
Logistics and Warehousing
In logistics and warehousing, efficient material handling is crucial for operations. Conveyor systems equipped with snub pulleys enhance the speed and reliability of these processes.
- Material Handling: Snub pulleys help maintain consistent belt movement, ensuring that packages and goods are transported efficiently within the facility.
- Operational Efficiency: By reducing the risk of belt slippage and enhancing drive efficiency, snub pulleys contribute to smoother and more reliable material handling operations.
The Critical Role of Head Pulleys in Conveyor Systems
Head pulleys are integral components of conveyor systems, providing the necessary traction to drive the conveyor belt and ensuring efficient and reliable material transport. In this detailed exploration, we introduce wing pulleys and their purpose, discuss the benefits of using wing pulleys for cleaning and maintaining conveyor belts, and highlight typical applications of wing pulleys in harsh environments.
Wing Pulley
Introduction to Wing Pulleys and Their Purpose
Wing pulleys, also known as self-cleaning pulleys, are designed with a unique construction that differentiates them from traditional pulleys. Unlike standard pulleys, which have a smooth cylindrical surface, wing pulleys feature a series of fins or wings extending radially from the central axis. These wings form a spiral pattern around the pulley, creating gaps through which debris and material can escape.
Purpose:
- Self-Cleaning: The primary purpose of wing pulleys is to provide a self-cleaning mechanism that helps remove material buildup and debris from the conveyor belt. As the belt moves over the wing pulley, the wings deflect loose material, preventing it from adhering to the belt surface.
- Preventing Belt Damage: By continuously clearing debris and buildup, wing pulleys help prevent damage to the conveyor belt. This reduces wear and tear on the belt, extending its lifespan and maintaining its performance.
- Enhanced Traction: The unique design of wing pulleys ensures consistent contact with the conveyor belt, providing enhanced traction and reducing the risk of belt slippage.
Benefits of Using Wing Pulleys for Cleaning and Maintaining Conveyor Belts
Wing pulleys offer several advantages for conveyor systems, particularly in terms of cleaning and maintenance. Here are some key benefits:
Improved Belt Cleanliness:
- Debris Removal: The self-cleaning action of wing pulleys effectively removes debris, fines, and material buildup from the conveyor belt. This helps maintain a clean belt surface, reducing the risk of contamination and ensuring smooth material transport.
- Reduced Carryback: By preventing material buildup, wing pulleys minimize carryback—the material that sticks to the return side of the conveyor belt and falls off along the return path. This reduces the need for frequent cleaning and maintenance of the conveyor system and surrounding areas.
Extended Belt Life:
- Reduced Wear and Tear: The continuous cleaning action of wing pulleys reduces the abrasive effects of debris on the conveyor belt. This helps prevent premature wear and tear, extending the lifespan of the belt and reducing replacement costs.
- Consistent Performance: By maintaining a clean and debris-free belt surface, wing pulleys ensure consistent traction and alignment. This contributes to the reliable and efficient operation of the conveyor system.
Enhanced Safety:
- Minimized Belt Slippage: The enhanced traction provided by wing pulleys reduces the risk of belt slippage, which can lead to operational disruptions and safety hazards. This ensures safer and more reliable conveyor operation.
- Prevention of Blockages: By continuously clearing debris and material buildup, wing pulleys help prevent blockages and jams in the conveyor system. This reduces the risk of equipment damage and operational downtime.
Cost Savings:
- Reduced Maintenance Costs: The self-cleaning action of wing pulleys reduces the frequency and intensity of maintenance required for the conveyor system. This leads to lower maintenance costs and increased operational efficiency.
- Lower Replacement Costs: By extending the lifespan of the conveyor belt and reducing wear and tear, wing pulleys help lower the overall cost of conveyor system maintenance and operation.
Typical Applications of Wing Pulleys in Harsh Environments
Wing pulleys are particularly well-suited for use in harsh environments where material buildup and debris can pose significant challenges. Here are some typical applications:
Mining Industry:
- Ore and Aggregate Handling: In the mining industry, conveyors are used to transport ore, aggregates, and other bulk materials. Wing pulleys help maintain clean belt surfaces, preventing material buildup and reducing the risk of conveyor belt damage in these abrasive and harsh conditions.
- Underground Mining: Wing pulleys are also used in underground mining operations, where space constraints and harsh environmental conditions make effective material handling and maintenance critical.
Aggregate and Quarry Operations:
- Sand and Gravel Processing: In aggregate and quarry operations, conveyors transport sand, gravel, and crushed stone. Wing pulleys help prevent material buildup on the belt, ensuring efficient material transport and reducing maintenance requirements.
- Crushing and Screening Plants: Wing pulleys are used in crushing and screening plants to maintain clean belt surfaces, reducing the risk of equipment blockages and ensuring consistent material flow.
Recycling Industry:
- Material Recovery Facilities: In recycling facilities, conveyors handle various materials, including metals, plastics, and paper. Wing pulleys help maintain clean belt surfaces, preventing material buildup and reducing the risk of contamination.
- Scrap Metal Processing: Wing pulleys are used in scrap metal processing to prevent material buildup and ensure efficient transport of ferrous and non-ferrous metals.
Construction and Demolition:
- Debris Handling: In construction and demolition operations, conveyors transport debris, rubble, and other materials. Wing pulleys help maintain clean belt surfaces, reducing the risk of blockages and ensuring efficient material handling.
- Recycling Plants: Wing pulleys are used in recycling plants that process construction and demolition waste, helping to maintain clean belt surfaces and ensuring efficient material separation and recovery.
Food Processing Industry:
- Bulk Material Handling: In the food processing industry, conveyors transport bulk materials such as grains, sugar, and flour. Wing pulleys help maintain clean belt surfaces, reducing the risk of contamination and ensuring efficient material transport.
- Packaging Lines: Wing pulleys are used in packaging lines to maintain clean belt surfaces, ensuring the safe and efficient transport of packaged food products.
How about Head Pulleys in Conveyor Systems
Tail Pulley Function
Specific Roles of the Tail Pulley in a Conveyor System
In a conveyor system, head pulleys and tail pulleys are fundamental components that work together to ensure smooth and efficient material handling. While head pulley conveyor drive the conveyor belt, tail pulleys play several critical roles that contribute to the system’s overall functionality and performance.
Guiding the Conveyor Belt:
The tail pulley is located at the opposite end of the conveyor system from the head pulley. Its primary role is to guide the conveyor belt back into the loop, ensuring that it stays aligned and moves smoothly. This guidance is essential for preventing the belt from drifting off track, which could lead to operational disruptions and increased wear on the belt and other components.
Providing Support:
The tail pulley supports the return side of the conveyor belt, helping to maintain its stability as it travels back to the starting point. This support is crucial for minimizing sagging and bouncing of the belt, which can cause damage and reduce the efficiency of the conveyor system.
Assisting with Belt Tension:
Proper belt tension is essential for the efficient operation of a conveyor system, and the tail pulley plays a significant role in maintaining this tension. The tail pulley works in conjunction with the head pulley to keep the belt tight, ensuring that it has the necessary grip to move materials effectively.
How the Tail Pulley Maintains Proper Belt Tension
Maintaining the correct belt tension is vital for preventing slippage and ensuring that the conveyor belt can carry loads efficiently without excessive wear or damage. The tail pulley contributes to this by adjusting and maintaining the belt’s tension.
Adjustable Tensioning Mechanisms:
Many tail pulleys are equipped with adjustable tensioning mechanisms that allow operators to fine-tune the belt tension as needed. This adjustability is crucial for accommodating different load conditions and ensuring optimal performance. By tightening or loosening the belt, the tail pulley helps maintain the appropriate tension to prevent slippage and ensure smooth operation.
Compensating for Belt Stretch:
Conveyor belts can stretch over time due to constant use and the weight of the materials being transported. The tail pulley compensates for this stretch by allowing for adjustments that keep the belt tight. Regular monitoring and adjustment of the belt tension are essential for maintaining the efficiency and longevity of the conveyor system.
Preventing Belt Slippage:
By maintaining the correct tension, the tail pulley ensures that the conveyor belt remains in firm contact with the head pulley. This firm contact is essential for preventing slippage, which can cause operational inefficiencies and potential damage to the belt and other components. Proper tension helps maintain the belt’s grip on the head pulley, ensuring consistent movement and efficient material handling.
Impact of the Tail Pulley on the Overall Performance of the Conveyor System
The tail pulley significantly impacts the overall performance and efficiency of a conveyor system. By ensuring proper belt tension, alignment, and support, the tail pulley contributes to the smooth operation and longevity of the system.
Enhancing Operational Efficiency:
The tail pulley’s role in maintaining proper belt tension and alignment is crucial for enhancing the conveyor system’s operational efficiency. By preventing slippage and ensuring smooth belt movement, the tail pulley helps optimize the system’s performance, allowing for efficient material handling and reducing the risk of downtime.
Reducing Maintenance Costs:
Proper tension and alignment reduce wear and tear on the conveyor belt and other components, leading to lower maintenance requirements and costs. The tail pulley’s ability to maintain these critical factors helps extend the lifespan of the belt and other parts, reducing the frequency and cost of repairs and replacements.
Improving Safety:
A well-maintained tail pulley ensures that the conveyor belt operates smoothly and reliably, reducing the risk of accidents and injuries. Proper tension and alignment minimize the chances of belt slippage and misalignment, which can cause sudden stops, material spills, and potential hazards for workers. Ensuring that the tail pulley is functioning correctly is essential for maintaining a safe working environment.
Supporting Consistent Material Flow:
The tail pulley’s role in guiding and supporting the conveyor belt helps maintain a consistent flow of materials. This consistency is vital for meeting production targets and ensuring that materials are transported efficiently and reliably. Any disruptions in the belt’s movement can lead to delays and reduced productivity, making the tail pulley’s function crucial for overall operational success.
Integration of Snub Pulleys with Head and Tail Pulleys
In addition to head and tail pulleys, snub pulleys play a critical role in optimizing the performance of conveyor systems. Snub pulleys are strategically positioned near the head pulley to increase the belt wrap around it, enhancing traction and drive efficiency.
Increasing Belt Wrap:
Snub pulleys are placed close to the head pulley to increase the angle of wrap around the head pulley. This increased wrap enhances the contact area between the belt and the pulley, improving traction and preventing slippage. By ensuring that more of the belt is in contact with the head pulley, snub pulleys help maintain consistent movement and efficient material handling.
Advantages of Using Snub Pulleys:
- Better Traction: Increased belt wrap provides better traction, reducing the risk of slippage and improving the conveyor system’s overall efficiency.
- Drive Efficiency: Enhanced traction ensures that the head pulley can drive the belt more effectively, leading to improved drive efficiency and reduced energy consumption.
- Reduced Wear: By preventing slippage and maintaining proper tension, snub pulleys help reduce wear and tear on the belt and other components, extending their lifespan and reducing maintenance costs.
Common Uses of Snub Pulleys:
Snub pulleys are commonly used in various conveyor setups to improve performance and efficiency. They are particularly beneficial in applications where heavy loads, high speeds, or long conveyor lengths are involved. By enhancing traction and drive efficiency, snub pulleys help ensure that the conveyor system operates smoothly and reliably, regardless of the specific application.
What is The Critical Role of Head Pulleys in Conveyor Systems
Head pulleys are integral components in conveyor systems, providing the necessary traction to drive the conveyor belt and ensuring efficient and reliable material transport. This article delves into the detailed description of head and tail pulleys in conveyor systems, their functions and features, and examples of how they improve material handling and processing.
Conveyor Head and Tail Pulley
Detailed Description of the Head and Tail Pulleys in a Conveyor System
Head Pulley:
The head pulley is located at the discharge end of the conveyor system. It is a primary driver of the conveyor belt, powered by an external drive mechanism such as an electric motor. The head pulley’s surface interacts directly with the conveyor belt, creating the necessary friction to move the belt and its load. The head pulley’s design typically includes a larger diameter to provide sufficient torque and grip, and it may be coated with a rubber or ceramic material to enhance its traction capabilities.
Tail Pulley:
The tail pulley is situated at the opposite end of the conveyor system, at the loading point. Unlike the head pulley, the tail pulley is not powered but serves a crucial role in maintaining belt tension and alignment. The tail pulley guides the conveyor belt back to the head pulley, ensuring that it travels smoothly and stays properly aligned. This pulley is also designed to minimize friction and wear on the belt, often featuring a smooth or lagged surface to facilitate its function.
Functions and Features of Head and Tail Pulleys
Functions of Head Pulleys:
- Driving the Belt: The primary function of the head pulley is to drive the conveyor belt. The friction between the belt and the head pulley provides the necessary traction to move the belt and the materials on it.
- Direction Change: The head pulley changes the direction of the conveyor belt, ensuring that the belt returns along the lower path of the conveyor system after discharging the materials.
- Tension Maintenance: The head pulley helps maintain the correct tension of the conveyor belt, which is essential for preventing slippage and ensuring smooth operation.
- Belt Tracking: By ensuring proper alignment, the head pulley helps in tracking the conveyor belt, reducing wear and tear and preventing operational disruptions.
Features of Head Pulleys:
- Durable Construction: Head pulleys are constructed from high-strength materials to withstand the operational stresses and provide long service life.
- Enhanced Traction Surface: Many head pulley on conveyor feature a rubber or ceramic coating to improve traction between the pulley and the belt.
- Lagging Options: Lagging, such as grooved or diamond patterns, is often applied to enhance grip and reduce belt slippage.
Functions of Tail Pulleys:
- Tension Provider: The tail pulley provides the necessary tension to the conveyor belt, ensuring it remains taut and properly aligned.
- Belt Tracking: The tail pulley helps guide the belt back to the head pulley, ensuring it stays aligned and reducing the risk of belt misalignment.
- Smooth Return: The tail pulley ensures a smooth return path for the conveyor belt, minimizing wear and tear.
Features of Tail Pulleys:
- Smooth Surface: Tail pulleys often have a smooth surface to reduce friction and wear on the conveyor belt.
- Adjustable Positioning: Many tail pulleys are mounted on adjustable frames to allow fine-tuning of belt tension and alignment.
- Robust Design: Like head pulley in conveyor, tail pulleys are built from durable materials to endure the demands of continuous operation.
Examples of How They Improve Material Handling and Processing
Mining Industry:
- Efficient Ore Transport: In the mining industry, head and tail pulleys are essential for the continuous transport of extracted ores. The head pulley drives the belt, while the tail pulley maintains the necessary tension, ensuring efficient movement of heavy loads over long distances. This setup reduces the need for manual labor and increases the overall efficiency of ore processing operations.
Manufacturing Industry:
- Streamlined Production Lines: In manufacturing facilities, head and tail pulleys are critical for the smooth operation of conveyor belts that transport parts and products along assembly lines. The head pulley ensures the belt moves consistently, while the tail pulley keeps it aligned and taut. This combination reduces operational downtime and enhances the efficiency of the production process.
Food Processing Industry:
- Hygienic Transport: In the food processing industry, head and tail pulleys are used in conveyor systems that transport food products through various stages of processing, such as sorting, washing, cooking, and packaging. The consistent movement provided by the head pulley, along with the proper tension maintained by the tail pulley, ensures that food products are transported hygienically and efficiently, maintaining product quality and safety.
Recycling Industry:
- Effective Material Separation: In recycling facilities, head and tail pulleys are used in conveyor systems that handle the sorting and separation of recyclable materials. The head pulley drives the belt, ensuring continuous movement, while the tail pulley maintains alignment and tension. This setup enhances the efficiency of material separation processes, improving the overall effectiveness of recycling operations.
Logistics and Warehousing:
- Optimized Package Handling: In logistics and warehousing operations, head and tail pulleys are essential for the efficient movement of packages along conveyor systems. The head pulley drives the belt, ensuring smooth and continuous transport, while the tail pulley maintains the necessary tension and alignment. This improves the speed and accuracy of order fulfillment processes, enhancing overall productivity.
Agriculture Industry:
- Reliable Crop Handling: In the agriculture industry, head and tail pulleys are used in conveyor systems that transport harvested crops from fields to storage or processing facilities. The head pulley drives the belt, ensuring consistent movement of crops, while the tail pulley maintains the required tension and alignment. This setup reduces the need for manual handling, minimizing post-harvest losses and enhancing operational efficiency.
The Integral Role of Head Pulleys and Tail Pulleys in Conveyor Systems
Head Pulley and Tail Pulley
Explanation of the Interaction Between Head Pulleys and Tail Pulleys
In conveyor systems, head pulleys and tail pulleys serve as critical components that work together to ensure the efficient and reliable movement of materials. Each pulley has distinct roles, but their interaction is essential for the overall functionality of the conveyor system.
Head Pulley:
The head pulley is typically located at the discharge end of the conveyor belt. Its primary function is to drive the conveyor belt, providing the necessary force to move the belt and the materials it carries. The head pulley is usually connected to a motor that supplies the power needed for the belt’s movement. As the driving force, the head pulley must maintain a strong grip on the belt to prevent slippage and ensure continuous motion.
Tail Pulley:
The tail pulley, located at the opposite end of the conveyor system, serves as the anchor point for the belt. It redirects the belt back toward the head pulley, completing the loop. The tail pulley is crucial for maintaining proper belt tension and alignment, ensuring that the belt moves smoothly and efficiently.
How Head and Tail Pulleys Work Together to Maintain Conveyor Efficiency
The interaction between conveyor head pulley and tail pulleys is fundamental to the smooth operation of conveyor systems. Their combined functions help maintain optimal belt tension, alignment, and traction, which are essential for efficient material handling.
Maintaining Belt Tension:
Proper belt tension is critical for preventing slippage and ensuring that the belt can carry loads effectively. The head pulley provides the driving force, while the tail pulley adjusts to maintain the appropriate tension. Many tail pulleys are equipped with tensioning devices that allow operators to fine-tune the belt tension, ensuring that it remains within the optimal range for efficient operation.
Ensuring Belt Alignment:
Belt alignment is crucial for preventing operational disruptions and minimizing wear and tear on the belt and other components. The head pulley helps guide the belt as it moves, while the tail pulley ensures that the belt remains aligned as it returns to the start of the conveyor loop. Together, they keep the belt centered and on track, reducing the risk of misalignment issues that can cause damage and inefficiency.
Enhancing Traction and Drive Efficiency:
Traction between the belt and the pulleys is essential for effective material movement. The head pulley must maintain a strong grip on the belt to drive it forward, while the tail pulley helps support and guide the belt. By working together, they ensure that the belt maintains continuous contact with the pulleys, enhancing traction and drive efficiency. This collaboration minimizes slippage and ensures consistent material flow.
Benefits of Using Both Pulleys for Optimal Belt Tension and Alignment
The combined use of head pulleys and tail pulleys offers several significant benefits for conveyor systems, particularly in terms of maintaining optimal belt tension and alignment.
Improved Operational Efficiency:
The interaction between head and tail pulleys ensures that the conveyor belt operates smoothly and efficiently. Proper tension and alignment reduce the risk of slippage and misalignment, which can cause operational disruptions and reduce efficiency. By maintaining these critical factors, the pulleys help optimize the performance of the conveyor system, allowing for efficient material handling and reduced downtime.
Extended Belt and Component Life:
Proper tension and alignment are essential for minimizing wear and tear on the conveyor belt and other components. By preventing slippage and ensuring that the belt moves smoothly, head and tail pulleys help extend the lifespan of the belt and reduce the frequency of repairs and replacements. This durability leads to lower maintenance costs and improved operational reliability.
Enhanced Safety:
A well-maintained conveyor system is safer for workers and reduces the risk of accidents and injuries. Proper belt tension and alignment minimize the chances of belt slippage and misalignment, which can cause sudden stops, material spills, and potential hazards for workers. Ensuring that the head and tail pulleys are functioning correctly is essential for maintaining a safe working environment.
Consistent Material Flow:
The head and tail pulleys’ role in maintaining belt tension and alignment helps ensure consistent material flow. This consistency is vital for meeting production targets and ensuring that materials are transported efficiently and reliably. Any disruptions in the belt’s movement can lead to delays and reduced productivity, making the pulleys’ function crucial for overall operational success.
Reduced Maintenance Requirements:
The effective interaction between head and tail pulleys reduces the need for frequent maintenance and adjustments. Proper tension and alignment minimize wear on the belt and other components, leading to fewer breakdowns and lower maintenance requirements. This reduction in maintenance needs translates to cost savings and increased uptime for the conveyor system.
The Essential Role of Head Pulleys in Conveyor Systems
Head pulleys are a critical component in conveyor systems, essential for driving the conveyor belt and ensuring efficient and reliable material transport. This article provides an in-depth overview of the head pulley’s role in conveyor systems, the importance of head pulleys in driving the conveyor belt, and their applications across various industries.
Head Pulley Conveyor
Overview of the Head Pulley’s Role in Conveyor Systems
The head pulley is located at the discharge end of the conveyor system and is a primary driver of the conveyor belt. This pulley is integral to the movement and control of the conveyor system, playing several key roles:
- Driving the Belt: The head pulley is connected to a motor that provides the necessary power to rotate the pulley and move the conveyor belt. The friction between the belt and the surface of the head pulley generates the traction needed to drive the belt forward.
- Changing Direction: As the belt wraps around the head pulley, it changes direction and begins its return journey along the conveyor system. This direction change is crucial for maintaining a continuous loop of belt movement.
- Maintaining Tension: The head pulley helps to maintain the appropriate tension in the conveyor belt. Proper tension is vital for preventing belt slippage, ensuring smooth operation, and reducing wear and tear on the belt and other components.
- Ensuring Alignment: By keeping the belt aligned, the head pulley helps to reduce misalignment issues that can lead to increased maintenance costs and operational inefficiencies. Proper alignment ensures that the belt runs smoothly and reduces the risk of damage.
Importance of Head Pulleys in Driving the Conveyor Belt
Head pulleys are crucial for several reasons:
- Providing Traction: The head pulley generates the friction needed to drive the conveyor belt. This traction is essential for moving materials efficiently and reliably along the conveyor system. Without sufficient traction, the belt may slip, leading to operational disruptions and potential damage.
- Supporting High Loads: In many industrial applications, conveyor systems are required to move heavy loads. The head pulley must be designed to handle these loads without compromising performance. This includes ensuring that the pulley is made from durable materials and is adequately supported by the conveyor structure.
- Enabling Speed Control: The speed at which the conveyor belt moves can be controlled by adjusting the rotational speed of the head pulley. This is important for synchronizing the conveyor system with other machinery and processes within the production line, allowing for optimized material handling and processing.
- Enhancing Efficiency: By providing consistent and reliable movement of the conveyor belt, head pulleys help to enhance the overall efficiency of the conveyor system. This includes reducing downtime, minimizing maintenance requirements, and improving the productivity of the entire operation.
Applications of Head Pulleys in Various Industries
Head pulleys are used in a wide range of industries, each with specific applications that benefit from the efficient and reliable operation of conveyor systems. Here are some examples:
Mining Industry:
- Ore and Aggregate Transport: In the mining industry, head pulleys are used in conveyor systems that transport extracted ores, aggregates, and other bulk materials from mining sites to processing plants. These pulleys ensure continuous movement of heavy loads over long distances, facilitating efficient processing and reducing the need for manual labor.
- Underground Mining: Head pulleys are also used in underground mining operations, where space constraints and harsh environmental conditions make effective material handling critical.
Manufacturing Industry:
- Assembly Lines: In manufacturing facilities, head pulleys drive conveyor belts that transport parts and products along assembly lines. These pulleys ensure the smooth and efficient movement of materials, enabling seamless integration of different production stages and increasing overall productivity.
- Material Handling: Head pulleys are used in material handling systems to move raw materials, components, and finished products between different areas of a manufacturing plant. This reduces the need for manual handling and enhances operational efficiency.
Food Processing Industry:
- Product Transportation: In the food processing industry, head pulleys drive conveyor belts that transport food products through various stages of processing, including sorting, washing, cooking, and packaging. The efficient movement of products ensures high productivity levels and maintains product quality and safety.
- Packaging Lines: Head pulleys are used in conveyor systems that handle the packaging of food products. They ensure that packaged goods are transported smoothly to packing and shipping areas, reducing the risk of damage and ensuring timely delivery.
Recycling Industry:
- Waste Sorting: In recycling facilities, head pulleys drive conveyor belts that transport recyclable materials through sorting systems. These pulleys facilitate the efficient separation of different types of waste, including metals, plastics, and paper, improving the effectiveness of recycling operations.
- Metal Recovery: Head pulleys are used in magnetic separation systems to recover ferrous metals from mixed waste streams. They drive the conveyor belts that transport materials through magnetic separators, ensuring the efficient removal of metal contaminants.
Logistics and Warehousing:
- Package Handling: In logistics and warehousing operations, head pulleys drive conveyor systems that handle the sorting, distribution, and transportation of packages. These pulleys ensure the efficient movement of goods through sorting facilities and distribution centers, enhancing the speed and accuracy of order fulfillment.
- Automated Systems: Head pulleys are used in automated conveyor systems that handle the storage and retrieval of goods in warehouses. They drive the belts that transport items to and from storage locations, improving inventory management and operational efficiency.
Agriculture Industry:
- Crop Handling: In the agriculture industry, head pulleys drive conveyor systems that transport harvested crops from fields to storage or processing facilities. These pulleys ensure the efficient movement of crops, reducing the need for manual labor and minimizing post-harvest losses.
- Grain Elevators: Head pulleys are used in grain elevators to move grains vertically, facilitating the storage and handling of large quantities of grain. They provide the necessary traction to lift grains to different levels, ensuring efficient grain management and processing.
FAQS about Head Pulleys
What is a pulley on a conveyor?
Head Pulley: Drives the conveyor belt and is located at the discharge end.
Tail Pulley: Guides the belt back towards the head pulley and maintains tension.
Snub Pulley: Increases the belt wrap angle around the drive pulley for better traction.
Take-Up Pulley: Adjusts its position to maintain proper belt tension.
Bend Pulley: Changes the direction of the belt.
What is head pulley lagging?
What is the head of a conveyor?
What is a head pulley?
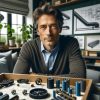
Jordan Smith, a seasoned professional with over 20 years of experience in the conveyor system industry. Jordan’s expertise lies in providing comprehensive solutions for conveyor rollers, belts, and accessories, catering to a wide range of industrial needs. From initial design and configuration to installation and meticulous troubleshooting, Jordan is adept at handling all aspects of conveyor system management. Whether you’re looking to upgrade your production line with efficient conveyor belts, require custom conveyor rollers for specific operations, or need expert advice on selecting the right conveyor accessories for your facility, Jordan is your reliable consultant. For any inquiries or assistance with conveyor system optimization, Jordan is available to share his wealth of knowledge and experience. Feel free to reach out at any time for professional guidance on all matters related to conveyor rollers, belts, and accessories.