Eriez Magnetic Head Pulley: Efficient Metal Separation
A magnetic head pulley is an integral part of a belt conveyor system, designed to remove ferrous contaminants from material flows automatically. By integrating a magnetic head pulley into a belt conveyor, industries can enhance their operational efficiency and ensure the purity of their products. The magnetic head pulley attracts and holds metal contaminants as the belt moves, effectively separating them from the non-magnetic material. This system offers significant benefits, including reducing equipment damage, minimizing downtime, and improving product quality. Common applications of magnetic head pulley belt conveyors include recycling facilities, mining operations, and food processing plants, where maintaining contaminant-free material is critical.
The Magnetic Head Pulley: Cross Belt Magnetic Separator
The magnetic head pulley is a critical component in industrial conveyor systems, designed to separate ferrous materials from non-ferrous ones. A related and equally important device is the cross belt magnetic separator. This section will provide a comprehensive explanation of cross belt magnetic separators, how they differ from magnetic head pulleys, and their benefits and applications in various industries.
Cross Belt Magnetic Separator
Cross belt magnetic separators are designed to remove ferrous contaminants from conveyed materials, providing an efficient and effective solution for maintaining product purity and protecting downstream equipment. They are widely used in recycling, mining, and other industries where the removal of ferrous materials is essential.
Explanation of Cross Belt Magnetic Separators and Their Design
A cross belt magnetic separator consists of a powerful magnet positioned above a conveyor belt. The magnet is mounted on a frame that spans the width of the conveyor belt, and a motorized belt runs across the magnet, perpendicular to the main conveyor belt. As materials pass under the cross belt magnetic separator, ferrous contaminants are attracted to the magnet and lifted from the main conveyor belt. The motorized belt then carries the captured ferrous materials to a designated discharge point, separating them from the non-ferrous materials.
Key Components of a Cross Belt Magnetic Separator:
- Magnet: The central component, typically made of either permanent magnets or electromagnets, generates a strong magnetic field to attract ferrous materials.
- Cross Belt: A motorized belt that runs across the magnet, perpendicular to the main conveyor belt, transporting captured ferrous materials to a discharge point.
- Frame: A sturdy structure that supports the magnet and cross belt, ensuring stability and proper alignment with the main conveyor belt.
- Control System: Manages the operation of the cross belt, including the speed and timing of the motorized belt.
How Cross Belt Magnetic Separators Differ from Magnetic Head Pulleys
Aspect | Cross Belt Magnetic Separators | Magnetic Head Pulleys |
---|---|---|
Design | Consists of a magnet mounted across the conveyor belt. | Magnet is integrated into the head pulley of the conveyor belt. |
Installation Location | Positioned above the conveyor belt, usually at the discharge end. | Installed at the head of the conveyor belt, replacing the standard pulley. |
Function | Removes ferrous contaminants from the material flow as it passes beneath. | Separates ferrous materials from the non-ferrous materials at the discharge point. |
Operation | Continuous cleaning with a self-cleaning belt to carry the ferrous material away. | Magnetic field pulls ferrous materials onto the belt, which are then discharged separately. |
Maintenance | Requires periodic maintenance to ensure the magnet and belt system are functioning properly. | Lower maintenance, mainly ensuring the pulley surface is clean and the magnet remains effective. |
Efficiency | High efficiency in removing ferrous contaminants from bulk materials. | Efficient for continuous separation but might be less effective for very small or deeply embedded ferrous particles. |
Cost | Generally higher due to the additional components and complexity. | Typically lower cost as it integrates into existing conveyor systems. |
Versatility | Can be used in various points of the conveyor system, not just the end. | Limited to being used at the head of the conveyor belt. |
Material Handling | Suitable for high-volume and bulk material processing. | Effective for a variety of materials but best for those with higher ferrous content. |
Industries | Commonly used in recycling, mining, and heavy industrial applications. | Used in industries such as recycling, mining, and food processing where ferrous contamination is an issue. |
Space Requirements | Requires additional space above the conveyor for installation. | Does not require additional space, fits within the existing conveyor layout. |
Power Consumption | May require additional power for the self-cleaning belt mechanism. | Generally lower power consumption as it relies on the conveyor's existing drive system. |
Benefits and Applications of Cross Belt Magnetic Separators in Various Industries
Cross belt magnetic separators offer numerous benefits, making them valuable assets in various industries. Their ability to efficiently remove ferrous contaminants improves product quality, protects equipment, and enhances overall operational efficiency.
Benefits
- Efficient Separation: Cross belt magnetic separators provide continuous and effective separation of ferrous materials from non-ferrous ones, ensuring high levels of product purity.
- Protection of Downstream Equipment: By removing ferrous contaminants, cross belt magnetic separators protect downstream equipment from damage and wear, reducing maintenance costs and downtime.
- Versatility: These separators can be used in various applications, from recycling and mining to food processing and pharmaceuticals, making them highly versatile.
- Increased Productivity: By automating the separation process, cross belt magnetic separators enhance productivity and operational efficiency, allowing for higher processing speeds and volumes.
- Improved Safety: Reducing the presence of ferrous materials in conveyed products minimizes the risk of equipment malfunctions and accidents, improving workplace safety.
Applications
- Recycling Industry: Cross belt magnetic separators are widely used in recycling facilities to remove ferrous metals from mixed waste streams, such as municipal solid waste, construction debris, and electronic scrap. This separation process is crucial for recovering valuable metals and ensuring the quality of recycled materials.
- Mining Industry: In mining operations, cross belt magnetic separators are used to remove tramp iron and other ferrous contaminants from conveyed ores and minerals. This separation process protects crushers, grinders, and other processing equipment from damage and ensures the purity of the extracted materials.
- Food Processing Industry: Cross belt magnetic separators play a vital role in the food processing industry by removing metal contaminants from food products. This ensures product safety and compliance with food safety standards, preventing contamination and potential health hazards.
- Pharmaceutical Industry: In the pharmaceutical industry, cross belt magnetic separators are used to remove ferrous contaminants from raw materials and finished products. This ensures the purity and quality of pharmaceutical products, meeting stringent regulatory requirements.
- Aggregate and Construction Industry: Cross belt magnetic separators are used in the aggregate and construction industry to remove ferrous materials from crushed stone, sand, and gravel. This separation process ensures the quality of construction materials and protects processing equipment from damage.
- Wood and Pulp Industry: In the wood and pulp industry, cross belt magnetic separators are used to remove nails, staples, and other ferrous contaminants from wood chips and pulp. This ensures the quality of the final product and protects equipment from damage.
- Glass and Ceramic Industry: Cross belt magnetic separators are used to remove ferrous contaminants from raw materials used in the production of glass and ceramics. This ensures the quality and purity of the final products, preventing defects and improving manufacturing efficiency.
The Versatility of Magnetic Head Pulley Systems in Industrial Applications
A magnetic head pulley is an essential component in many industrial conveyor systems, providing efficient separation of ferrous contaminants from materials. This article will explore the functionality of overhead magnets, compare them with magnetic head pulleys, and discuss their typical use cases in industrial settings.
Overhead Magnet
Description of Overhead Magnets and Their Functionality
Overhead magnets are powerful magnetic devices installed above conveyor belts to remove ferrous materials from the product stream. They play a crucial role in ensuring the purity of the materials and protecting downstream equipment from damage caused by metal contaminants. Here’s a detailed look at their functionality:
- Construction: Overhead magnets are typically constructed with a robust housing to withstand harsh industrial environments. They contain powerful magnets, such as ceramic or rare earth magnets, depending on the application’s needs.
- Installation: These magnets are mounted above conveyor belts or vibratory feeders. They can be suspended either on a crossbelt configuration or inline with the conveyor.
- Operation: As materials pass beneath the overhead magnet, ferrous contaminants are attracted to the magnetic field and separated from the product stream. The captured ferrous materials are then removed from the magnet either manually or automatically, ensuring continuous operation.
- Types: There are different types of overhead magnets, including permanent magnets and electromagnetic separators. Permanent magnets are always on and require no external power source, while electromagnets can be turned on and off as needed, providing more control over the separation process.
Comparison Between Overhead Magnets and Magnetic Head Pulleys
While both overhead magnets and magnetic head pulleys serve the purpose of separating ferrous materials from a product stream, they have distinct differences in their application and functionality:
Installation and Placement:
- Overhead Magnets: As the name suggests, these magnets are installed above the conveyor belt. They do not contact the material directly but instead use a magnetic field to attract and remove ferrous contaminants from above.
- Magnetic Head Pulley: These are installed at the end of the conveyor belt and serve as the driving pulley for the belt. The magnetic head pulley directly interacts with the material, attracting and removing ferrous metals as the belt turns around the pulley.
Separation Efficiency:
- Overhead Magnets: These magnets are highly effective in removing ferrous contaminants from the top layer of materials on the conveyor belt. They are particularly useful in applications where ferrous metals are likely to be found on the surface of the product stream.
- Magnetic Head Pulley: Magnetic head pulleys are efficient at removing ferrous contaminants that are embedded within the product stream. As the material comes into direct contact with the pulley, the magnetic field pulls out ferrous metals, ensuring thorough separation.
Flexibility and Control:
- Overhead Magnets: Electromagnetic overhead magnets offer greater flexibility as they can be turned on and off as needed. This control allows operators to adjust the magnetic field’s strength based on the specific requirements of the application.
- Magnetic Head Pulley: Magnetic head pulleys, typically permanent magnets, provide consistent magnetic strength and continuous operation without the need for external power.
Maintenance:
- Overhead Magnets: These require regular maintenance to ensure that the magnetic surface is clear of accumulated ferrous materials. Automatic cleaning systems can be installed to reduce manual intervention.
- Magnetic Head Pulley: These pulleys generally require less maintenance compared to overhead magnets. The main maintenance task involves ensuring that the conveyor belt and pulley are in good working condition and free of excessive wear.
Typical Use Cases for Overhead Magnets in Industrial Settings
Overhead magnets are versatile and find use in various industrial settings due to their effectiveness in removing ferrous contaminants. Here are some typical applications:
Recycling Industry:
- In recycling facilities, overhead magnets are used to separate ferrous metals from mixed waste streams. This process is crucial for recovering valuable metals and ensuring the purity of recycled materials. Overhead magnets help in sorting scrap metals, electronic waste, and other recyclable materials, improving the efficiency and quality of recycling operations.
Mining and Aggregate:
- Overhead magnets are commonly used in mining operations to remove tramp metal from ores and other materials. This helps in protecting crushers, grinders, and other processing equipment from damage caused by metal contaminants. In aggregate processing, overhead magnets ensure the quality of the final product by removing ferrous impurities.
Food Processing:
- In the food industry, maintaining product purity is paramount. Overhead magnets are used to remove metal contaminants from food products during processing and packaging. This ensures the safety and quality of food products, protecting consumers from potential hazards and complying with industry regulations.
Bulk Material Handling:
- Overhead magnets are essential in handling bulk materials such as coal, grains, and wood chips. They help in removing ferrous metals from these materials, preventing damage to conveyors, crushers, and other handling equipment. This improves the efficiency and longevity of bulk material handling systems.
Wood and Pulp Industry:
- In the wood processing and pulp industry, overhead magnets are used to remove nails, screws, and other metal contaminants from wood chips and logs. This prevents damage to saws, chippers, and other processing equipment, ensuring smooth and efficient operations.
Integration of Magnetic Head Pulleys in Conveyor Systems
While overhead magnets are installed above the conveyor belt, magnetic head pulleys are integrated directly into the conveyor system. This integration provides a seamless and efficient method for continuous separation of ferrous materials.
Enhanced Material Purity:
- By incorporating a magnetic head pulley at the end of the conveyor belt, industries can ensure that ferrous contaminants are effectively removed from the product stream before the materials move to the next processing stage. This enhances the purity and quality of the final product.
Protection of Equipment:
- Magnetic head pulleys help protect downstream equipment from damage caused by ferrous contaminants. By removing these metals early in the process, industries can reduce maintenance costs and avoid costly repairs to crushers, grinders, and other machinery.
Operational Efficiency:
- The continuous operation of magnetic head pulleys ensures that material handling processes remain efficient and uninterrupted. This reliability is crucial in high-volume industrial settings where downtime can be costly.
Versatility:
- Magnetic head pulleys are versatile and can be used in various applications, from small-scale operations to large industrial facilities. They are suitable for a wide range of materials, including aggregates, grains, recyclables, and more.
The Essential Role of Magnetic Head Pulley Systems in Material Purification
A magnetic head pulley is a critical component in the realm of magnetic separators, playing an indispensable role in ensuring the purity and quality of materials processed in various industrial applications. This article provides an overview of magnetic separators, their importance, the function and types of these devices, including magnetic head pulleys, and the advantages they offer for material purification.
Magnetic Separator
Overview of Magnetic Separators and Their Importance
Magnetic separators are devices designed to remove ferrous materials from a mixture using magnetic force. They are essential in many industries, including mining, recycling, food processing, and bulk material handling, to ensure that the end products are free from contaminants that could affect their quality and safety.
The importance of magnetic separators cannot be overstated. They help in protecting machinery from damage caused by tramp metal, reducing downtime and maintenance costs. Additionally, they play a crucial role in ensuring product quality, which is vital for meeting industry standards and maintaining consumer safety.
Function and Types of Magnetic Separators, Including Magnetic Head Pulleys
Magnetic separators work by generating a magnetic field that attracts and removes ferrous particles from the material stream. These separators come in various types, each designed for specific applications and operational requirements. Here are some common types of magnetic separators:
Overhead Magnets:
- Function: Overhead magnets are installed above conveyor belts to attract and remove ferrous contaminants from the material stream. They can be either permanent magnets or electromagnets.
- Applications: Overhead magnets are commonly used in recycling plants, food processing facilities, and aggregate operations to ensure the purity of the materials being processed.
Drum Magnets:
- Function: Drum magnets consist of a rotating drum with a magnetic core inside. As materials pass over the drum, ferrous particles are attracted to the drum’s surface and separated from the non-magnetic material.
- Applications: Drum magnets are widely used in scrap yards, mining operations, and industrial processing plants for the continuous separation of ferrous materials.
Magnetic Head Pulley:
- Function: A magnetic head pulley conveyor replaces the standard head pulley at the end of a conveyor belt. As materials reach the end of the conveyor, the magnetic field of the pulley attracts and holds ferrous particles, which are then removed from the belt as it rotates.
- Applications: Magnetic head pulleys are used in various industries, including mining, recycling, and bulk material handling, to ensure the removal of ferrous contaminants from the material stream.
Suspended Magnets:
- Function: Suspended magnets are mounted above conveyor belts and use a magnetic field to attract ferrous materials. They can be either permanent or electromagnetic.
- Applications: These magnets are typically used in heavy-duty industrial applications where large volumes of material need to be processed and cleaned.
Advantages of Using Magnetic Separators for Material Purification
The use of magnetic separators, including the magnetic conveyor head pulleys, offers numerous advantages for material purification, making them an essential tool in many industrial processes. Here are some key benefits:
Enhanced Product Quality:
- Consistency: Magnetic separators ensure that products are free from ferrous contaminants, which can affect the quality and consistency of the final product. This is particularly important in industries such as food processing and pharmaceuticals, where product purity is paramount.
- Compliance: By removing contaminants, magnetic separators help industries comply with stringent quality and safety standards, ensuring that products meet regulatory requirements and customer expectations.
Protection of Equipment:
- Reduced Wear and Tear: Ferrous particles can cause significant wear and tear on processing equipment, leading to increased maintenance costs and downtime. Magnetic separators protect machinery by removing these contaminants before they can cause damage.
- Extended Equipment Life: By reducing the amount of ferrous material that passes through machinery, magnetic separators help extend the life of equipment, resulting in lower capital expenditure over time.
Increased Efficiency:
- Continuous Operation: Magnetic separators, such asmagnetic head pulley price, allow for continuous operation without the need for manual intervention. This improves the efficiency of material handling processes and reduces labor costs.
- Improved Throughput: By ensuring that only clean, ferrous-free materials are processed, magnetic separators help improve the overall throughput and efficiency of industrial operations.
Cost Savings:
- Reduced Downtime: The protection of equipment from ferrous contaminants leads to fewer breakdowns and reduced downtime, which translates to significant cost savings for businesses.
- Lower Maintenance Costs: Magnetic separators help minimize the wear and tear on machinery, reducing the frequency and cost of maintenance and repairs.
Versatility and Adaptability:
- Wide Range of Applications: Magnetic separators are versatile and can be used in various industries, including mining, recycling, food processing, and bulk material handling. Their adaptability makes them suitable for a wide range of operational requirements.
- Customizable Solutions: Many magnetic separators can be customized to meet the specific needs of different applications, ensuring optimal performance and efficiency.
Innovations in Magnetic Head Pulley: Magnetic Sweeper for Vehicle
Introduction to Magnetic Sweepers and Their Uses in Vehicles
Magnetic sweepers are innovative tools designed to remove ferrous debris from various surfaces. These devices are equipped with powerful magnets that attract and capture metallic objects such as nails, screws, and metal shavings, which can pose hazards to vehicles and personnel. Magnetic sweepers are commonly used in a variety of settings, including construction sites, airports, and industrial facilities, where maintaining a clean and safe environment is crucial.
Magnetic sweepers come in various forms, including handheld models, push-type sweepers, and vehicle-mounted sweepers. Vehicle-mounted magnetic sweepers are particularly effective for covering large areas quickly and efficiently. These sweepers are attached to the front or rear of a vehicle, such as a forklift, truck, or utility vehicle, and as the vehicle moves, the sweeper collects ferrous debris from the ground. This process not only ensures a cleaner environment but also reduces the risk of tire punctures and other damage to vehicles and equipment.
How Magnetic Head Pulleys Can Be Adapted for Use in Magnetic Sweepers
Magnetic head pulleys, typically used in conveyor systems to separate ferrous materials from non-ferrous ones, can be adapted for use in magnetic sweepers. The robust design and strong magnetic field of magnetic head pulleys make them ideal for capturing and holding ferrous debris in various applications.
Adaptation Process
- Magnetic Strength and Configuration: Magnetic head pulleys are designed to generate a strong magnetic field, which can be customized to suit the specific needs of magnetic sweepers. By adjusting the configuration and strength of the magnets, the sweepers can effectively capture ferrous debris of varying sizes and weights.
- Mounting Mechanism: To adapt a magnetic head pulley for use in a magnetic sweeper, a suitable mounting mechanism must be designed. This typically involves attaching the magnetic head pulley to a frame that can be securely mounted to a vehicle. The frame should be adjustable to allow for different mounting positions and heights, ensuring optimal performance in various environments.
- Sweeper Housing: The magnetic head pulley should be enclosed in a durable housing that protects it from environmental factors such as dust, dirt, and moisture. The housing should also include a mechanism for easy debris removal, such as a release handle or sliding tray, allowing for quick and efficient cleaning.
- Integration with Vehicle Controls: For vehicle-mounted magnetic sweepers, it is essential to integrate the magnetic head pulley with the vehicle’s control system. This can include features such as an on/off switch for the magnetic field and indicators to alert the operator when the sweeper needs to be emptied.
Applications in Construction, Airports, and Industrial Facilities
Magnetic sweepers equipped with magnetic head pulley conveyor for sale offer significant benefits in various industries. Their ability to efficiently remove ferrous debris enhances safety, reduces maintenance costs, and improves overall operational efficiency.
Construction Sites
Construction sites are often littered with metal debris, such as nails, screws, and metal shavings, which can pose hazards to both workers and equipment. Magnetic sweepers are invaluable in these settings, as they quickly and effectively remove ferrous debris, ensuring a safer working environment. By preventing tire punctures and other damage to construction vehicles, magnetic sweepers also help reduce maintenance costs and downtime.
Key Benefits:
- Improved Safety: Removing metal debris reduces the risk of injuries to workers and damage to vehicles.
- Cost Savings: Preventing tire punctures and equipment damage reduces maintenance and repair costs.
- Efficiency: Magnetic sweepers cover large areas quickly, minimizing the time and labor required for debris removal.
Airports
Airports are another critical application area for magnetic sweepers. Runways, taxiways, and aprons must be kept free of ferrous debris to ensure the safety of aircraft and ground personnel. Metal objects on these surfaces can cause significant damage to aircraft tires and engines, leading to costly repairs and potential safety hazards.
Magnetic sweepers mounted on airport maintenance vehicles can efficiently clear large areas of ferrous debris, helping to maintain a safe and operational airport environment. Regular use of magnetic sweepers on airport surfaces reduces the risk of foreign object damage (FOD) to aircraft, ensuring smoother and safer operations.
Key Benefits:
- Enhanced Safety: Regular debris removal minimizes the risk of FOD, protecting aircraft and personnel.
- Operational Efficiency: Keeping runways and taxiways clear of debris ensures uninterrupted airport operations.
- Cost Reduction: Preventing damage to aircraft reduces maintenance and repair expenses.
Industrial Facilities
In industrial facilities, ferrous debris can accumulate in production areas, loading docks, and storage yards. This debris poses risks to both personnel and machinery, potentially leading to injuries and equipment damage. Magnetic sweepers are highly effective in these environments, providing a reliable solution for maintaining clean and safe work areas.
Industrial facilities often have large, open spaces that can be efficiently covered by vehicle-mounted magnetic sweepers. These sweepers help maintain a debris-free environment, reducing the risk of accidents and ensuring smooth operation of machinery and vehicles.
Key Benefits:
- Safety: Removing metal debris from work areas reduces the risk of injuries and equipment damage.
- Productivity: Clean work areas contribute to more efficient and uninterrupted operations.
- Maintenance: Regular use of magnetic sweepers reduces the need for manual cleaning and decreases maintenance costs.
Enhancing Compressor Efficiency with Magnetic Head Pulley Technology
Magnetic Pulley Compressor
Description of the Role of Magnetic Pulleys in Compressors
A magnetic head pulley is an essential component in various industrial applications, including compressors. In compressors, magnetic pulleys serve as crucial elements that contribute to the system’s overall functionality and efficiency. These pulleys utilize magnetic fields to interact with metallic components, facilitating smoother operation and improved performance.
Function in Compressors
In compressors, magnetic pulleys are integrated to help drive the compressor’s components. They work by creating a magnetic field that can attract and hold ferrous materials. This magnetic interaction allows for precise control of the moving parts within the compressor, reducing mechanical wear and tear and enhancing the longevity of the equipment.
The magnetic head pulley helps in synchronizing the movement of the compressor’s parts, ensuring that the compression process is efficient and consistent. This synchronization is vital for maintaining the compressor’s performance, especially in high-demand industrial environments where reliability and efficiency are paramount.
How Magnetic Pulleys Enhance the Efficiency of Compressors
The integration of magnetic head pulleys in compressors offers several advantages that enhance the efficiency and performance of these systems. Here’s how they contribute to improved efficiency:
Reduced Friction and Wear
Magnetic pulleys reduce the physical contact between moving parts within the compressor. By relying on magnetic forces to drive and control components, these pulleys minimize friction, which is a primary cause of wear and tear in mechanical systems. Reduced friction leads to less maintenance, lower operational costs, and a longer lifespan for the compressor.
Improved Energy Efficiency
Compressors with magnetic head pulleys are generally more energy-efficient. The magnetic interaction requires less energy compared to traditional mechanical methods of driving components. This efficiency translates into lower energy consumption and operational costs, making magnetic pulley compressors more environmentally friendly and cost-effective in the long run.
Enhanced Precision and Control
The use of magnetic pulleys allows for precise control over the movement of the compressor’s parts. This precision ensures that the compression process is smooth and consistent, leading to better performance and reliability. Improved control also means that the compressor can operate at optimal levels, reducing the likelihood of breakdowns and increasing overall productivity.
Vibration Reduction
Magnetic head pulleys contribute to the reduction of vibrations within the compressor. Vibrations can cause significant wear and tear on mechanical components, leading to frequent maintenance and potential system failures. By minimizing vibrations, magnetic pulleys help maintain the integrity of the compressor, ensuring smoother operation and extended service life.
Examples of Industries that Use Magnetic Pulley Compressors
Magnetic pulley compressors are utilized across various industries due to their enhanced efficiency, reliability, and performance. Here are some examples of industries that benefit from this technology:
Manufacturing
In the manufacturing sector, compressors are essential for powering pneumatic tools, machinery, and production lines. Magnetic pulley compressors offer the reliability and efficiency needed to maintain continuous operation in manufacturing plants. They help reduce downtime and improve the overall productivity of the manufacturing process.
Automotive Industry
The automotive industry relies heavily on compressors for various applications, including painting, assembly, and maintenance. Magnetic pulley compressors are ideal for this industry due to their ability to deliver consistent and efficient performance. The reduced maintenance requirements and energy efficiency of these compressors make them a cost-effective choice for automotive manufacturers.
Food and Beverage Industry
In the food and beverage industry, compressors are used for refrigeration, packaging, and processing applications. Magnetic pulley compressors are particularly beneficial in this sector because they provide precise control and reliability, ensuring that food products are processed and stored under optimal conditions. The energy efficiency of these compressors also aligns with the industry’s focus on sustainability and cost savings.
Chemical and Pharmaceutical Industry
The chemical and pharmaceutical industries require compressors for various processes, including mixing, pumping, and chemical reactions. Magnetic pulley compressors offer the precision and control needed for these critical applications. Their ability to reduce wear and tear also means fewer interruptions and a more stable production environment, which is crucial for maintaining product quality and safety.
Mining and Heavy Industry
In mining and heavy industry, compressors are used for drilling, excavation, and material handling. The harsh operating conditions in these sectors demand robust and reliable equipment. Magnetic pulley compressors meet these requirements by providing efficient and durable performance. Their reduced maintenance needs and ability to operate under challenging conditions make them an excellent choice for these industries.
FAQS about Magnetic Head Pulley
What is a head magnet?
What is a magnetic drum pulley?
What is a head pulley?
How does a magnetic head pulley work?
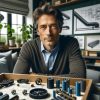
Jordan Smith, a seasoned professional with over 20 years of experience in the conveyor system industry. Jordan’s expertise lies in providing comprehensive solutions for conveyor rollers, belts, and accessories, catering to a wide range of industrial needs. From initial design and configuration to installation and meticulous troubleshooting, Jordan is adept at handling all aspects of conveyor system management. Whether you’re looking to upgrade your production line with efficient conveyor belts, require custom conveyor rollers for specific operations, or need expert advice on selecting the right conveyor accessories for your facility, Jordan is your reliable consultant. For any inquiries or assistance with conveyor system optimization, Jordan is available to share his wealth of knowledge and experience. Feel free to reach out at any time for professional guidance on all matters related to conveyor rollers, belts, and accessories.