Designing Effective Modular Belt Conveyor Systems
Modular belt conveyor systems are versatile and efficient solutions for material handling in various industries. They are composed of interlocking plastic modules, providing flexibility and ease of maintenance. These systems are cost-effective due to their durability and modular design, allowing for easy repairs and modifications. Suitable for a wide range of applications, from food processing to manufacturing, modular belt conveyors enhance productivity and operational efficiency. Key components like FlexLink conveyor parts and MCE conveyors ensure seamless integration and high performance, making them a popular choice for industrial conveyor systems.
Modular Belt Conveyor Systems Cost
When considering the implementation of modular belt conveyor systems in an industrial setting, understanding the cost implications is crucial. The cost of modular belt conveyor systems can vary significantly based on a range of factors. This section will delve into the elements that influence the cost, compare initial investments with long-term savings, and provide case studies that demonstrate the cost efficiency of modular belt conveyor systems.
Overview of Factors Influencing the Cost of Modular Belt Conveyor Systems
- Material and Build Quality: The choice of materials used in the construction of modular belt conveyor systems plays a significant role in the overall cost. High-quality materials, such as stainless steel or durable plastics, tend to be more expensive but offer better longevity and reliability.
- System Complexity and Customization: The complexity of the modular conveyor belt system, including the need for customization, can impact the price. Customized modular conveyor belt systems designed to meet specific industry needs may require additional engineering and design work, which can increase costs.
- Size and Capacity: The size and load capacity of the modular belt conveyor systems also affect the overall cost. Larger systems designed to handle heavy loads will generally be more expensive than smaller systems.
- Technology and Features: Advanced features such as automated controls, sensors, and integration with other industrial systems can add to the cost of modular belt conveyors. These features, while increasing the initial investment, can enhance the efficiency and functionality of the system.
- Installation and Maintenance: The costs associated with the installation and maintenance of modular conveyor belts must be considered. Professional installation ensures the system is set up correctly, and regular maintenance is essential for long-term performance.
Initial Investment vs. Long-Term Savings
Investing in modular belt conveyor systems involves significant initial outlay, but the long-term savings can justify the expenditure. Here are some factors to consider:
- Reduced Downtime: Modular belt conveyor systems are designed for easy maintenance and quick repairs. The modular design allows for the replacement of individual sections, reducing downtime and maintenance costs.
- Energy Efficiency: Modern modular conveyor belt systems are built to be energy-efficient, which can result in lower operational costs over time. The energy savings can accumulate, leading to substantial cost reductions.
- Scalability and Flexibility: The modular design offers flexibility, allowing businesses to scale their operations without significant additional costs. As production needs change, modular conveyor systems can be easily reconfigured or expanded.
- Durability and Longevity: High-quality modular belt conveyors are durable and have a long operational life. The initial investment is offset by the reduced need for frequent replacements and repairs.
Case Studies Highlighting Cost Efficiency
Case Study 1: Food Processing Industry – Green Valley Foods
Green Valley Foods, a mid-sized food processing company, invested in modular conveyor belt systems to improve its production line efficiency. The initial cost of the system was substantial, but Green Valley Foods experienced a 20% increase in productivity and a 15% reduction in energy costs within the first year. The modular design of the conveyor belts allowed the company to quickly adapt to new products, further enhancing cost efficiency and operational flexibility.
Case Study 2: Automotive Manufacturing – SpeedTech Auto Parts
SpeedTech Auto Parts, an automotive parts manufacturer, implemented a modular belt conveyor system to streamline its assembly line operations. The initial investment was high due to the need for customization to fit the specific requirements of the automotive assembly process. However, the system’s flexibility and ease of maintenance led to a 30% reduction in downtime and a significant decrease in operational costs over five years. This investment proved to be highly beneficial for SpeedTech Auto Parts, ensuring smooth and efficient production.
Case Study 3: Pharmaceutical Industry – HealthGuard Pharmaceuticals
HealthGuard Pharmaceuticals required a clean and efficient conveyor solution for its packaging line to meet stringent hygiene standards. The modular belt conveyor systems installed provided the necessary hygiene and operational efficiency. Although the initial cost was significant, it was balanced by the long-term savings in maintenance and improved production rates. HealthGuard Pharmaceuticals saw a return on investment within three years, thanks to the enhanced productivity and reduced maintenance costs provided by the modular conveyor systems.
Modular Belt Conveyor Systems: What You Need to Know
A modular conveyor system is a versatile and efficient solution designed to meet the varying needs of different industries. This section will provide a definition of modular conveyor systems, highlight their key features, discuss the advantages they offer across various sectors, and give examples of industries that benefit from their use.
Definition and Key Features of Modular Conveyor Systems
Modular conveyor systems consist of individual sections or modules that can be easily assembled, disassembled, and reconfigured. These systems are designed to offer flexibility, efficiency, and ease of maintenance. The key features include:
- Modularity: The primary characteristic of a modular conveyor belt system is its modularity. Each section can be customized or replaced independently, allowing for quick adjustments and scalability.
- Durability: Modular conveyor belts are made from high-quality materials that provide durability and resistance to wear and tear. This ensures a long operational life and consistent performance.
- Versatility: Modular conveyor systems can be adapted to handle a wide range of products, from small items to large, heavy loads. This versatility makes them suitable for various industries.
- Ease of Maintenance: The design of modular belt conveyors allows for easy access to components, making maintenance and repairs straightforward. This reduces downtime and maintenance costs.
- Efficiency: These systems are designed for optimal performance, with features such as smooth belt surfaces, low friction, and efficient power usage, enhancing overall productivity.
Advantages of Modular Conveyor Systems in Various Industries
- Flexibility in Design and Application: Conveyor belt modular systems can be tailored to specific applications, whether in manufacturing, food processing, or packaging. This flexibility allows businesses to optimize their operations and meet specific requirements.
- Cost-Effectiveness: While the initial investment in modular belt conveyors can be high, the long-term cost savings are significant. Reduced maintenance, energy efficiency, and minimal downtime contribute to overall cost-effectiveness.
- Scalability: As business needs change, modular conveyor systems can be easily expanded or reconfigured. This scalability makes them an ideal solution for growing businesses or those with fluctuating production demands.
- Hygiene and Cleanliness: In industries such as food processing and pharmaceuticals, hygiene is paramount. Modular conveyor belts can be designed to meet stringent cleanliness standards, with materials that are easy to clean and resistant to contamination.
- Enhanced Productivity: The efficient design of modular conveyor systems, combined with their durability and ease of maintenance, results in increased productivity. Businesses can achieve higher throughput and improved workflow with minimal interruptions.
Examples of Industries Utilizing Modular Conveyor Systems
- Food and Beverage Industry: Conveyor modular belt systems are widely used in the food and beverage industry for applications such as packaging, processing, and distribution. Their ability to maintain hygiene standards and handle a variety of products makes them ideal for this sector.
- Automotive Manufacturing: In the automotive industry, modular conveyor systems are used to transport parts and assemblies along production lines. Their flexibility and durability support the high demands of automotive manufacturing.
- Pharmaceuticals: The pharmaceutical industry benefits from modular conveyor belts that ensure clean and efficient handling of products. These systems are used in packaging, sorting, and distribution, meeting the industry’s strict hygiene requirements.
- Logistics and Warehousing: Modular conveyor systems play a crucial role in logistics and warehousing by facilitating the efficient movement of goods. Their scalability and adaptability make them suitable for various warehousing operations.
- Electronics Manufacturing: In electronics manufacturing, modular conveyor systems are used for assembling and testing components. The precision and flexibility of these systems support the intricate processes involved in electronics production.
Modular Belt Conveyor Systems: Modular Conveyor Design
Key Aspects of Modular Conveyor Design
The design of modular conveyor systems is a critical factor that determines their performance, efficiency, and adaptability. This section will explore the principles of designing modular conveyor systems, covering key aspects such as system layout, material selection, and integration with other equipment.
Principles of Designing Modular Conveyor Systems
- System Layout and Configuration: The layout of a modular conveyor system should be designed to optimize the flow of materials and products. Considerations include the arrangement of conveyor modules, the placement of drive units, and the integration with other machinery.
- Material Selection: The choice of materials for modular conveyor belts and components is crucial. Materials should be selected based on the specific application requirements, such as durability, resistance to wear and tear, and ease of maintenance.
- Customization and Flexibility: A well-designed modular conveyor system should offer customization options to meet the unique needs of different industries. This includes the ability to add or remove modules, adjust conveyor speeds, and incorporate specialized features.
- Integration with Other Equipment: Modular conveyor systems should be designed to seamlessly integrate with other equipment in the production line. This includes synchronization with automated systems, sensors, and control units to ensure smooth operation.
- Ergonomics and Safety: The design should prioritize ergonomics and safety, ensuring that the system is easy to operate and maintain. Safety features such as guards, emergency stop mechanisms, and user-friendly controls are essential.
- Energy Efficiency: Incorporating energy-efficient components and design principles can reduce the operational costs of modular conveyor systems. This includes the use of low-friction materials, efficient motors, and optimized power usage.
- Maintenance and Accessibility: Design considerations should include easy access to components for maintenance and repairs. Modular designs that allow for quick replacement of parts can minimize downtime and improve overall efficiency.
- Scalability: The design should allow for future expansion and scalability. Modular conveyor systems should be able to adapt to changing production demands without requiring significant modifications.
By focusing on these design principles, businesses can ensure that their modular conveyor systems meet their operational needs and provide long-term value.
Modular Belt Conveyor Systems: Industrial Conveyor Systems
Role of Modular Belt Conveyors in Industrial Conveyor Systems
Industrial conveyor systems are fundamental to various manufacturing and processing industries, providing efficient material handling solutions that enhance productivity and streamline operations. Among the diverse types of conveyor systems available, modular belt conveyor systems stand out due to their versatility, durability, and ease of maintenance. This section will delve into the integration of modular belt conveyor systems in industrial setups, the benefits they offer in such environments, and real-world applications across different industrial sectors.
Integration of Modular Belt Conveyors in Industrial Setups
Modular belt conveyor systems are designed to be highly adaptable, making them suitable for integration into a wide range of industrial setups. These systems consist of interlocking plastic modules that form a continuous belt, which can be easily configured and reconfigured to meet specific operational requirements. The integration process involves several key steps:
- Custom Design and Configuration: The modular nature of these conveyors allows for custom design and configuration to fit the specific layout and workflow of an industrial facility. This flexibility ensures that the conveyor system can be tailored to handle various types of products, from small components to large assemblies.
- Compatibility with Existing Equipment: Modular belt conveyor systems are compatible with a variety of existing equipment and machinery. This compatibility facilitates seamless integration into current production lines without the need for extensive modifications, minimizing downtime and disruption.
- Ease of Installation: The modular design simplifies the installation process, allowing for quick assembly and commissioning. This ease of installation is particularly beneficial in industries where rapid deployment is crucial to maintaining continuous operations.
- Scalability and Expansion: One of the significant advantages of modular belt conveyor systems is their scalability. As industrial needs evolve, these systems can be easily expanded or reconfigured to accommodate changes in production volumes, product types, or process flows. This scalability ensures that the conveyor system remains relevant and efficient over time.
Benefits of Using Modular Belt Conveyors in Industrial Environments
The use of modular belt conveyor systems in industrial environments offers numerous benefits, making them a preferred choice for many businesses. Some of the key advantages include:
- Durability and Longevity: Modular belt conveyors are built to withstand the rigors of industrial environments. The plastic modules are resistant to wear, corrosion, and impact, ensuring a long service life even under harsh operating conditions.
- Low Maintenance: These conveyor systems require minimal maintenance compared to traditional belt conveyors. The modular design allows for easy replacement of damaged or worn modules without the need to replace the entire belt, reducing maintenance costs and downtime.
- Hygiene and Cleanliness: In industries such as food processing and pharmaceuticals, hygiene is paramount. Modular belt conveyors are designed with smooth surfaces and minimal crevices, making them easy to clean and sanitize. This design feature helps maintain high standards of hygiene and prevents contamination.
- Enhanced Safety: Safety is a critical concern in industrial environments. Modular belt conveyor systems are designed with safety features such as smooth edges and non-slip surfaces to reduce the risk of accidents and injuries. Additionally, the ease of maintenance and repair minimizes the need for extended manual intervention, further enhancing workplace safety.
- Operational Efficiency: The flexibility and adaptability of modular belt conveyors contribute to improved operational efficiency. These systems can be easily adjusted to handle different product sizes and shapes, optimizing the flow of materials and reducing bottlenecks in the production process.
- Energy Efficiency: Modular belt conveyor systems are designed to operate efficiently, consuming less energy compared to conventional conveyor systems. This energy efficiency translates to lower operational costs and a reduced environmental footprint.
Real-World Applications in Different Industrial Sectors
Modular belt conveyor systems are employed across various industrial sectors, each benefiting from the unique advantages these systems offer. Here are some real-world applications:
- Food and Beverage Industry: In the food and beverage industry, modular belt conveyors are used to transport products through various stages of production, including processing, packaging, and distribution. Their ease of cleaning and sanitation makes them ideal for maintaining food safety standards.
- Automotive Industry: The automotive industry utilizes modular belt conveyor systems for the assembly of components and vehicles. These conveyors can handle a wide range of parts, from small nuts and bolts to large car bodies, ensuring efficient and organized assembly lines.
- Pharmaceutical Industry: In pharmaceutical manufacturing, modular belt conveyors are used to move products through different stages of production, from raw materials to finished goods. The ability to maintain high hygiene standards and adapt to different product sizes is crucial in this industry.
- Electronics Manufacturing: The electronics industry benefits from modular belt conveyor systems for the assembly and testing of electronic components and devices. The flexibility to configure the conveyors for different production processes and product types enhances efficiency and productivity.
- Packaging Industry: Modular belt conveyors are widely used in the packaging industry to transport products through various packaging stages. Their ability to handle diverse product sizes and shapes ensures smooth and efficient packaging operations.
- Logistics and Distribution: In logistics and distribution centers, modular belt conveyors facilitate the movement of goods from receiving to shipping. Their scalability and adaptability make them ideal for handling varying volumes of products and optimizing the flow of materials.
Modular Belt Conveyor Systems: FlexLink Conveyor Parts
Importance of FlexLink Conveyor Parts in Modular Belt Conveyor Systems
FlexLink conveyor parts are integral components of modular belt conveyor systems, enhancing their functionality, reliability, and efficiency. This section will provide an overview of FlexLink conveyor parts, their compatibility with modular belt conveyors, how they enhance the functionality of these systems, and considerations for maintenance and replacement.
Overview of FlexLink Conveyor Parts and Their Compatibility
FlexLink, a leading provider of conveyor components and systems, offers a wide range of parts that are compatible with modular belt conveyor systems. These parts include:
- Chains and Belts: FlexLink provides a variety of chains and belts designed for different applications, including plastic modular belts that integrate seamlessly with modular belt conveyor systems.
- Guide Rails and Brackets: FlexLink guide rails and brackets help in maintaining proper belt alignment and guiding products along the conveyor path. These components are essential for ensuring smooth and efficient material handling.
- Drive and Idler Units: FlexLink drive and idler units are designed to provide reliable power transmission and support for the conveyor belt. These units are compatible with modular belt conveyors, ensuring consistent and efficient operation.
- Support Structures: FlexLink offers robust support structures that provide stability and durability to modular belt conveyor systems. These structures can be customized to fit specific conveyor layouts and operational requirements.
- Transfer and Diverting Modules: FlexLink transfer and diverting modules facilitate the smooth transfer of products between different conveyor sections and the sorting or diverting of products to different paths. These modules enhance the flexibility and efficiency of modular belt conveyor systems.
How FlexLink Parts Enhance the Functionality of Modular Belt Conveyors
FlexLink conveyor parts play a crucial role in enhancing the functionality of modular belt conveyor systems in several ways:
- Improved Performance: FlexLink chains and belts are designed to provide optimal performance in various applications. Their compatibility with modular belt conveyors ensures smooth and reliable operation, reducing the risk of downtime and improving overall productivity.
- Enhanced Flexibility: The wide range of FlexLink guide rails, brackets, and support structures allows for the customization of modular belt conveyor systems to meet specific operational needs. This flexibility is essential for accommodating different product types and handling requirements.
- Efficient Power Transmission: FlexLink drive and idler units are engineered for efficient power transmission, ensuring that modular belt conveyors operate smoothly and with minimal energy consumption. This efficiency contributes to lower operational costs and improved system reliability.
- Seamless Integration: FlexLink transfer and diverting modules integrate seamlessly with modular belt conveyor systems, facilitating the smooth transfer and sorting of products. This integration enhances the efficiency of material handling processes and optimizes workflow.
- Durability and Reliability: FlexLink conveyor parts are built to withstand the rigors of industrial environments, offering durability and reliability. This robust construction ensures that modular belt conveyor systems can operate continuously with minimal maintenance requirements.
Maintenance and Replacement of FlexLink Conveyor Parts
Proper maintenance and timely replacement of FlexLink conveyor parts are essential for ensuring the long-term performance and reliability of modular belt conveyor systems. Key considerations for maintenance and replacement include:
- Regular Inspection: Conducting regular inspections of FlexLink conveyor parts is crucial for identifying signs of wear and tear, misalignment, or damage. Early detection of issues allows for timely maintenance and prevents unexpected breakdowns.
- Lubrication and Cleaning: Proper lubrication and cleaning of FlexLink chains, belts, and other moving parts are essential for maintaining smooth operation and reducing friction. This routine maintenance helps to extend the lifespan of the conveyor components and ensures optimal performance.
- Timely Replacement: FlexLink conveyor parts that show signs of significant wear or damage should be replaced promptly to avoid compromising the overall system’s performance. Keeping spare parts on hand can minimize downtime during replacement.
- Training and Expertise: Ensuring that maintenance personnel are trained and knowledgeable about FlexLink conveyor parts and their maintenance requirements is essential. Proper training helps to ensure that maintenance procedures are carried out correctly and efficiently.
- Documentation and Records: Maintaining detailed records of maintenance activities, inspections, and replacements helps to track the condition of FlexLink conveyor parts and schedule timely maintenance. This documentation also provides valuable insights for future maintenance planning.
Modular Belt Conveyor Systems: MCE Conveyors
MCE (Modular Conveyor Express) conveyors are renowned for their high-quality construction and versatility in modular belt conveyor systems. This section will introduce MCE conveyors, their key features, how they integrate into modular belt conveyor systems, and the benefits and applications of using MCE conveyors.
MCE conveyors are designed to provide efficient and reliable material handling solutions for various industries. Some key features of MCE conveyors include:
- Modular Design: MCE conveyors are built using a modular design that allows for easy customization and reconfiguration. This modularity makes them ideal for diverse applications and changing operational needs.
- Durable Construction: MCE conveyors are constructed with high-quality materials, ensuring durability and long service life. This robust construction allows them to withstand the demands of industrial environments.
- Versatility: MCE conveyors are versatile and can handle a wide range of products, from small components to larger items. Their adaptability makes them suitable for various industries, including manufacturing, packaging, and distribution.
- Ease of Maintenance: The modular design of MCE conveyors simplifies maintenance and repairs. Individual modules can be easily replaced or reconfigured without the need for extensive downtime, ensuring continuous operation.
- High Performance: MCE conveyors are engineered for high performance, providing smooth and efficient material handling. Their design minimizes friction and ensures consistent operation, enhancing productivity.
Integration of MCE Conveyors in Modular Belt Conveyor Systems
Integrating MCE conveyors into modular belt conveyor systems involves several key steps to ensure seamless operation and compatibility. These steps include:
- System Design and Layout: The integration process begins with designing the conveyor system layout, taking into account the specific operational requirements and workflow. MCE conveyors can be configured to fit various layouts, ensuring optimal space utilization and efficient material flow.
- Compatibility with Existing Systems: MCE conveyors are designed to be compatible with existing conveyor systems, allowing for seamless integration. This compatibility minimizes the need for extensive modifications and ensures smooth operation.
- Customization and Configuration: The modular design of MCE conveyors allows for customization and configuration to meet specific needs. This flexibility ensures that the conveyor system can handle different product types and sizes, enhancing overall efficiency.
- Installation and Commissioning: The installation process for MCE conveyors is straightforward, thanks to their modular design. Once installed, the conveyors are commissioned and tested to ensure proper operation and alignment with the overall system.
- Ongoing Support and Maintenance: After integration, ongoing support and maintenance are essential to ensure the long-term performance of MCE conveyors. Regular inspections, lubrication, and timely replacement of worn parts help to maintain optimal operation.
Benefits and Applications of MCE Conveyors
MCE conveyors offer numerous benefits and are used in a wide range of applications across different industries. Some of the key benefits and applications include:
- Enhanced Flexibility: The modular design of MCE conveyors provides enhanced flexibility, allowing for easy customization and reconfiguration. This flexibility is essential for industries that require adaptable material handling solutions.
- Improved Efficiency: MCE conveyors are designed for high performance, ensuring smooth and efficient material handling. This improved efficiency contributes to higher productivity and reduced operational costs.
- Durability and Reliability: MCE conveyors are built to last, with durable construction and high-quality materials. Their reliability ensures continuous operation, minimizing downtime and maintenance costs.
- Wide Range of Applications: MCE conveyors are used in various industries, including manufacturing, packaging, distribution, and food processing. Their versatility allows them to handle different product types and sizes, making them suitable for diverse applications.
- Ease of Maintenance: The modular design of MCE conveyors simplifies maintenance and repairs, allowing for quick replacement of individual modules. This ease of maintenance helps to reduce downtime and ensure continuous operation.
Real-World Applications of MCE Conveyors
- Manufacturing: In manufacturing, MCE conveyors are used to transport components and assemblies through different stages of production. Their flexibility and durability make them ideal for handling various products and ensuring efficient production lines.
- Packaging: In the packaging industry, MCE conveyors facilitate the movement of products through various packaging stages. Their adaptability allows for the handling of different package sizes and shapes, optimizing packaging operations.
- Distribution Centers: MCE conveyors are widely used in distribution centers to move products from receiving to shipping. Their scalability and efficiency make them suitable for handling varying volumes of products and ensuring timely order fulfillment.
- Food Processing: In the food processing industry, MCE conveyors are used to transport food products through various processing stages. Their ease of cleaning and sanitation ensures compliance with food safety standards and prevents contamination.
- Pharmaceuticals: In pharmaceutical manufacturing, MCE conveyors move products through different production stages, from raw materials to finished goods. Their ability to maintain high hygiene standards and handle different product sizes is crucial in this industry.
By exploring the role of modular belt conveyors in industrial conveyor systems, the importance of FlexLink conveyor parts, and the benefits of MCE conveyors, this detailed blog post provides comprehensive insights into the advantages and applications of modular belt conveyor systems in various industrial sectors.
FAQs about Modular Belt Conveyor Systems
What is a modular conveyor belt?
What is a module conveyor?
What are the 2 categories of conveyor system?
Powered Conveyor Systems: These conveyors are driven by motors and are used to move products along a path automatically. They include belt conveyors, roller conveyors, chain conveyors, and screw conveyors. Powered conveyors are ideal for applications where products need to be moved at a controlled speed, over long distances, or through complex paths. They are commonly used in manufacturing, packaging, and distribution centers.
Gravity Conveyor Systems: These conveyors use the force of gravity to move products. They include gravity roller conveyors and gravity skatewheel conveyors. Gravity conveyors are typically used for simple, flat paths where products can move on their own without the need for powered assistance. They are cost-effective and require minimal maintenance, making them suitable for loading and unloading areas, and assembly lines.
What are types of belt conveyor?
Flat Belt Conveyors: These are the most common type, featuring a flat belt that runs on a flat surface or rollers. They are used for moving products over long distances and are ideal for items with a flat bottom.
Cleated Belt Conveyors: These conveyors have cleats attached to the belt, which help to move products up inclines or prevent them from sliding. They are used in applications where products need to be moved vertically or at steep angles.
Modular Belt Conveyors: Comprising interlocking plastic modules, these conveyors are highly flexible and can handle a wide range of products. They are often used in food processing and packaging due to their easy-to-clean design.
Curved Belt Conveyors: Designed to navigate turns and changes in direction, curved belt conveyors allow for a smooth transition of products around corners.
Incline/Decline Belt Conveyors: These conveyors are used to move products between different heights. They are equipped with belts that can handle the incline or decline without products slipping.
Sanitary Belt Conveyors: Designed for use in hygienic environments, such as food processing and pharmaceuticals, these conveyors are made with materials and designs that allow for easy cleaning and sanitization.
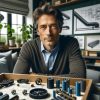
Jordan Smith, a seasoned professional with over 20 years of experience in the conveyor system industry. Jordan’s expertise lies in providing comprehensive solutions for conveyor rollers, belts, and accessories, catering to a wide range of industrial needs. From initial design and configuration to installation and meticulous troubleshooting, Jordan is adept at handling all aspects of conveyor system management. Whether you’re looking to upgrade your production line with efficient conveyor belts, require custom conveyor rollers for specific operations, or need expert advice on selecting the right conveyor accessories for your facility, Jordan is your reliable consultant. For any inquiries or assistance with conveyor system optimization, Jordan is available to share his wealth of knowledge and experience. Feel free to reach out at any time for professional guidance on all matters related to conveyor rollers, belts, and accessories.