High Temperature Conveyor Rollers: Material And Applications
In many industrial sectors, conveyor systems are pivotal for the seamless movement of goods, playing a critical role in maintaining operational efficiency. These systems are especially crucial in environments where heat-intensive processes are routine, necessitating the use of robust equipment capable of withstanding extreme conditions. This is where high temperature conveyor rollers become essential. Designed to endure the rigors of high heat, high temperature conveyor rollers are tailored to meet the specific demands of industries such as metalworking, glass manufacturing, and food processing. Their durability not only ensures the continuous flow of production but also minimizes downtime caused by equipment failure, highlighting their significance in maintaining high industrial standards and safety.
What are High Temperature Conveyor Rollers
High temperature conveyor rollers are specialized components designed to operate efficiently within environments exposed to extreme heat. Typically constructed from materials that can withstand high temperatures without degrading, such as stainless steel, high-grade plastics, or coated with thermally resistant substances like Teflon, these rollers are crucial for industries where heat is a constant during processing. Industries such as ceramics production, steel manufacturing, and baking rely on these rollers to ensure their conveyor systems can handle the thermal stress without failure.
The significance of using high temperature conveyor rollers cannot be overstated. In high-temperature environments, regular conveyor rollers may warp, melt, or even emit hazardous fumes, leading to potential production halts and safety issues. High temperature conveyor rollers are designed to resist such conditions, ensuring that production lines continue to operate smoothly and safely. This capability not only extends the life of the conveyor system but also protects the integrity of the products being manufactured. By employing these specialized rollers, companies can avoid frequent replacements and maintenance costs, while also boosting their operational efficiency in challenging conditions.
How High Temperature Conveyor Rollers Work
High temperature conveyor rollers are designed to operate under extreme heat conditions while maintaining their structural integrity and functionality. These rollers consist of a cylindrical body that may be composed of various materials suited for high temperatures, supported by bearings that allow them to rotate smoothly under loads.
The mechanism of high temperature conveyor rollers relies heavily on the materials used in their construction. Materials must be selected based on their thermal tolerance, strength, and wear resistance. Here’s how materials like Teflon play a crucial role in enhancing the performance of these rollers:
- Thermal Resistance: Teflon, known for its outstanding heat resistance, can withstand temperatures up to 260°C (500°F). This makes it ideal for applications involving prolonged exposure to high heat, ensuring that the rollers do not degrade or lose functionality over time.
- Low Friction Coefficient: Teflon has a very low coefficient of friction. This property is essential in high temperature environments as it reduces the energy required for the rollers to move, thus minimizing wear and extending the lifespan of both the rollers and the conveyor belt.
- Chemical Resistance: In environments where chemicals are present along with high temperatures, Teflon’s chemical inertness ensures that the rollers do not corrode or react with the substances they come into contact with. This is crucial for maintaining the quality and safety of the conveyor system in chemical processing plants.
- Non-stick Surface: Teflon’s non-stick properties prevent materials from adhering to the surface of the rollers. This is particularly beneficial in industries like food processing and packaging, where residue on the rollers can cause contamination or operational issues.
These features combined make Teflon and similar materials invaluable for enhancing the efficiency and reliability of high temperature conveyor rollers. By mitigating the physical stresses and reducing the thermal impact on the rollers, these materials ensure that the conveyor systems can operate smoothly, without frequent maintenance or replacement, thereby supporting continuous industrial processes even in challenging conditions.

Material of High Temperature Conveyor Rollers
High temperature conveyor rollers are typically constructed from materials that can withstand extreme heat and maintain their structural integrity and functionality.High temperature conveyor rollers materials ensure that the conveyor rollers can operate efficiently in high-temperature environments, such as in heat-intensive industrial processes. The common materials used for high temperature conveyor rollers include:
- Stainless Steel: Known for its heat resistance and strength, stainless steel is a popular choice for high temperature environments.
- Ceramic: Ceramic rollers can withstand very high temperatures and are resistant to thermal shock, making them ideal for extreme heat applications.
- Heat-Resistant Alloys: Alloys such as Inconel, Hastelloy, and other nickel-based alloys are used for their excellent heat resistance and durability.
- Cast Iron: Cast iron rollers can handle high temperatures and are often used in industrial applications where heat resistance is critical.
- Silicon Carbide: This material is known for its high thermal conductivity and thermal shock resistance, making it suitable for high-temperature applications.
- Graphite: Graphite rollers can withstand high temperatures and provide good lubrication properties, reducing friction in conveyor systems.
These materials ensure that the conveyor rollers can operate efficiently in high-temperature environments, such as in furnaces, kilns, and other heat-intensive industrial processes.
Types of High Temperature Conveyor Rollers
Selecting the right type of high temperature conveyor rollers is crucial for ensuring operational efficiency and longevity in environments exposed to extreme heat. Each material and design offers specific benefits and is suitable for different high-temperature applications. Here we delve into four common types of conveyor rollers used in such conditions:
- Steel Mesh Rollers: These rollers are particularly useful in industries where air circulation around the conveyed items is necessary. The open structure of steel mesh allows for excellent heat dissipation, making them ideal for use in baking and drying processes where high temperatures are a norm. Their robust structure also withstands thermal expansion well.
- Fiberglass Rollers: Fiberglass is renowned for its heat resistance and minimal thermal expansion. High temperature conveyor rollers made from fiberglass are suitable for applications involving chemicals and high heat, such as in the manufacture of composites and in certain chemical processing plants. They provide excellent resistance to warping and deformation under heat.
- Modular Plastic Rollers: Made from high-performance plastics that can withstand elevated temperatures, modular plastic rollers are versatile and can be used in a variety of applications, including food processing and packaging. These rollers offer the advantage of corrosion resistance and are lighter in weight, which can reduce overall system strain.
- Steel Chain Rollers: For extremely high temperatures and loads, steel chain rollers are the go-to option. They are particularly prevalent in heavy industries such as forging and steel processing. The strength and durability of steel ensure that these rollers can handle both the high temperatures and the heavy loads typical of these environments.
- Ceramic Conveyor Rollers:Ceramic materials such as silicon carbide or alumina.Excellent thermal resistance, non-metallic, and resistant to wear.Used in glass manufacturing, ceramics production, and high-temperature furnaces.
- Composite Conveyor Rollers:A combination of metal cores with high-temperature resistant composite coatings.A combination of metal cores with high-temperature resistant composite coatings.Used in applications where weight reduction and thermal resistance are critical.
- Stainless Steel Conveyor Rollers:Stainless steel grades like 304, 316, or specialized high-temperature stainless steel.Corrosion-resistant, durable, and capable of handling high temperatures.Used in food processing, pharmaceuticals, and chemical industries where both high temperatures and hygiene are essential.
- Heat-Treated Conveyor Rollers:Various metals that have undergone heat treatment to enhance thermal resistance.Enhanced strength and thermal stability.Used in heavy-duty industrial applications, such as mining and material handling.
- Silicone-Coated Conveyor Rollers:Metal cores with a high-temperature silicone coating.Excellent heat resistance, non-stick surface, and good grip.Excellent heat resistance, non-stick surface, and good grip.
- Polymer Conveyor Rollers:High-temperature resistant polymers like PEEK (Polyether ether ketone).Lightweight, corrosion-resistant, and capable of withstanding high temperatures.Used in applications where chemical resistance and thermal stability are required.
Each of these types of high temperature conveyor rollers offers specific advantages that make them suitable for particular applications within heat-intensive industries. When selecting the appropriate roller type, it is important to consider not only the temperature range but also the physical and chemical conditions of the environment to ensure optimal performance and durability of the conveyor system.

Common Applications of High Temperature Conveyor Rollers
High temperature conveyor rollers are indispensable in several key industries that face intense heat during their processing stages. These specialized rollers are designed to withstand conditions that could severely impair typical conveyor systems.
- Food Processing and Baking: In the food industry, particularly in baking and cooking processes, temperatures can soar to extremely high levels to ensure thorough cooking and safety. High temperature conveyor rollers enable the conveyance of food items through ovens and cooling tunnels without compromising the equipment’s integrity or the food’s quality.
- Heat Sealing and Packaging: Packaging materials such as plastics and foils often require heat sealing at high temperatures to ensure airtight and secure packaging. High temperature conveyor rollers facilitate the movement of these materials through sealing equipment, ensuring continuous operation without the risk of melting or distorting the conveyor components.
- Solar Panel Manufacturing: The production of solar panels involves processes such as lamination and curing, which require exposure to high temperatures. High temperature conveyor rollers are essential to move panels through these processes, maintaining the integrity of the conveyor system and the panels themselves.
- Glass Manufacturing: The glass industry involves extremely high temperatures for melting and molding glass. Conveyor systems equipped with high temperature conveyor rollers transport glass safely through furnaces and cooling zones without equipment degradation.
- Metallurgical Industry:Used in steel mills, aluminum plants, and foundries.Used in steel mills, aluminum plants, and foundries.
- Ceramics Industry:Used in kilns and drying ovens.To move ceramic items through high-temperature zones for firing and drying.
- Textile Industry:Used in heat-setting machines and drying equipment.To move textiles through processes involving high temperatures for setting and drying.
- Aerospace Industry:Used in composite material curing ovens.To handle aerospace components during high-temperature curing processes.
These examples underscore the versatility and necessity of high temperature conveyor rollers in maintaining operational efficiency and safety in environments exposed to extreme heat. The specialized materials and designs of these rollers ensure that they can meet the demands of various high-temperature processes, making them a critical component in the infrastructure of these heat-intensive industries.
Request a quote for reliable conveyor rollers here!
How to Choose the Best High Temperature Conveyor Rollers
Choosing the best high temperature conveyor rollers involves careful consideration of several critical factors to ensure they meet the specific needs of your industrial applications. Here are some key aspects to consider:
- Material Compatibility: The material of the roller must be suitable for the temperatures and conditions of the environment in which they will be used. For instance, steel might be preferred for its strength in heavy industries, whereas fiberglass might be chosen for its resistance to chemical corrosion.
- Load Capacity: It is vital to choose rollers that can support the weight and type of goods they will carry without deforming. Different materials and designs have varying load capacities.
- Thermal Resistance: The rollers must withstand the maximum temperatures they will encounter without degradation. This includes not only the material’s melting point but also its ability to resist warping and structural weakening at high temperatures.
- Maintenance Requirements: Consider how easy it is to maintain and replace the rollers. Some materials may require more frequent inspections and replacements due to wear and tear at high temperatures.
When comparing different manufacturers of high temperature conveyor rollers, it’s helpful to use a standardized table format to assess their offerings. The table should include categories like material types, maximum temperature tolerance, load capacity, price, and customer reviews. This data provides a clear comparison to help make an informed decision based on your specific requirements.
Measuring Tips for High Temperature Conveyor Rollers:
To ensure a perfect fit for your conveyor system, follow these measuring tips:
- Diameter Measurement: Measure the outer diameter of the roller. This is critical for ensuring the roller fits within the system without causing any alignment issues.
- Length Measurement: Measure the length of the roller from end to end. Ensure this matches the width of the conveyor belt or frame to maintain proper alignment and distribution of load.
- Shaft Diameter: Measure the diameter of the shaft where the roller will be mounted. This must be accurate to ensure the roller is secured in place and rotates smoothly without excess play.
- Spacing Consideration: Consider the spacing between rollers. This affects the conveyor’s ability to handle different types of goods. For heavier items, closer spacing might be necessary to prevent sagging between rollers.
By thoroughly assessing these factors and carefully measuring, you can ensure that the high temperature conveyor rollers you select will perform optimally in your specific industrial environment, thereby enhancing efficiency and reducing downtime.

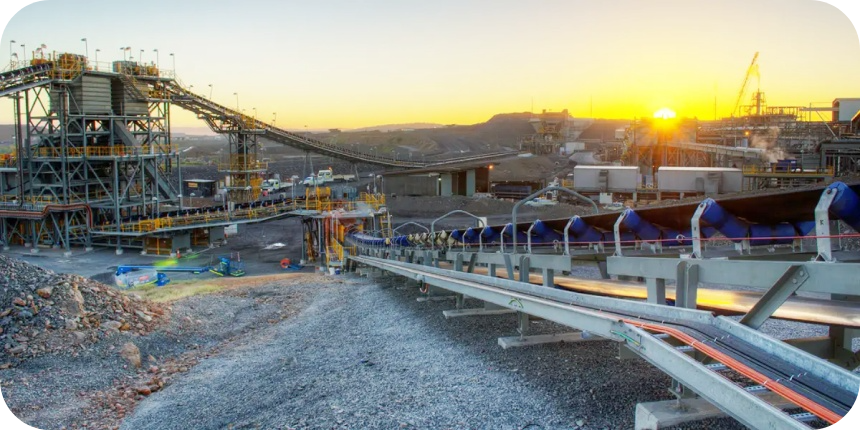
Selecting the Right Manufacturer for High Temperature Conveyor Rollers
Choosing the right manufacturer for high temperature conveyor rollers is crucial for ensuring that the equipment will perform adequately under extreme conditions and have a long service life. Here’s some guidance on selecting manufacturers that specialize in high temperature conveyor rollers and key traits that set apart the best in the industry:
- Material Expertise: Top manufacturers of high temperature conveyor rollers will have extensive knowledge about the properties and performance of various materials under different temperature conditions. They should be able to provide detailed information on why certain materials are chosen for their rollers, such as Teflon for its heat resistance and low friction, or stainless steel for its strength and durability.
- Customization Capabilities: The best manufacturers offer customization options to meet specific industrial needs. Whether it’s varying roller sizes, materials, or bearing types, they should be able to tailor their products to your exact specifications, which is crucial for ensuring efficiency and reliability in your specific operational environment.
- Quality Certifications: Reputable manufacturers will hold relevant quality certifications such as ISO 9001, which demonstrates a commitment to maintaining high standards in their production processes. These certifications are a hallmark of quality and reliability, indicating that their products have been rigorously tested and meet international standards.
- Proven Track Record: The top manufacturers will have a proven track record of reliability and customer satisfaction. Look for companies with robust client testimonials, case studies, and a history of supplying to well-known industries that operate under high temperatures. This experience not only shows their ability to deliver products that perform as expected but also their understanding of diverse industrial needs.
- After-Sales Support: Exceptional manufacturers of high temperature conveyor rollers will offer excellent after-sales support. This includes maintenance services, quick delivery of replacement parts, and access to technical assistance when needed. Such support is vital for minimizing downtime and ensuring continuous operation in high-temperature environments.
Selecting a manufacturer with these qualifications ensures that you receive high temperature conveyor rollers that are not only of high quality but also suited perfectly for your industrial applications. Their expertise and support can make a significant difference in the longevity and efficiency of your conveyor systems.
Find top-quality conveyor rollers. Inquire for more information!
Purchasing High Temperature Conveyor Rollers
When it comes to acquiring high temperature conveyor rollers, buyers face the decision of choosing between new and used options. Each choice has its advantages and considerations, especially in terms of cost, availability, and performance requirements. Here’s some advice on buying used vs. new high temperature conveyor rollers, along with guidance on where to find them.
Buying New vs. Used High Temperature Conveyor Rollers:
- Cost Considerations: New high temperature conveyor rollers, while more expensive, come with manufacturer warranties and the assurance of pristine condition, which can be crucial for demanding applications. Used rollers, on the other hand, can offer significant cost savings, but they may lack warranty protection and require more thorough inspection to ensure they meet operational standards.
- Availability and Lead Times: New rollers may have longer lead times if they are not in stock or require customization. Used rollers can be more readily available, which is beneficial if you need to replace a failed roller quickly to minimize downtime.
- Longevity and Durability: New high temperature conveyor rollers are likely to last longer since they start with no wear. Used rollers, while cost-effective, may have reduced life expectancy and might soon require replacement, adding to long-term costs.
- Specific Requirements: If your application requires rollers with exact specifications or the latest technology (such as advanced heat-resistant materials), purchasing new is often the only option. Used rollers might not meet the current technological or operational standards needed for specialized tasks.
Where to Find High Temperature Conveyor Rollers for Sale:
- Manufacturer Direct: Buying directly from manufacturers is one of the best ways to ensure you are getting rollers that meet the specific needs of your operations. Manufacturers can provide detailed product specifications, customization options, and after-sales support.
- Industrial Supply Companies: Many industrial suppliers stock a variety of conveyor rollers, including those designed for high temperatures. They often have both new and used options available, offering a balance between cost and reliability.
- Online Marketplaces: Websites like eBay, Alibaba, and industry-specific resale platforms can be good sources for finding both new and used high temperature conveyor rollers. These platforms often provide buyer protections and reviews, which can help in making a more informed purchase decision.
- Trade Shows and Industrial Expos: These events provide opportunities to meet directly with manufacturers and suppliers, compare different products firsthand, and negotiate deals. They are especially useful for finding the latest technologies in conveyor roller design.
Choosing the right source and understanding the trade-offs between new and used high temperature conveyor rollers will help ensure that you make a purchase that balances cost, performance, and operational requirements effectively.
Maintenance and Care for High Temperature Conveyor Rollers
Maintaining high temperature conveyor rollers is essential to ensure their longevity and performance efficiency. Proper care and regular inspections are vital to keeping these systems running smoothly and preventing costly downtime. Here are practical tips and the importance of routine inspections in maintaining high temperature conveyor rollers:
Tips on Maintaining High Temperature Conveyor Rollers:
- Regular Lubrication: High temperature conveyor rollers should be regularly lubricated with high-temperature resistant grease to reduce friction and wear. This not only extends the life of the rollers but also ensures they operate smoothly without excessive noise or vibration.
- Cleaning Protocols: It’s crucial to implement regular cleaning schedules to remove any debris, residues, or contaminants that could adhere to the rollers. This is especially important in industries like food processing or chemical manufacturing, where build-up can cause corrosion or contamination.
- Thermal Inspections: Use thermal imaging tools to monitor the temperature distribution of the rollers during operation. This can help identify any overheating issues before they lead to failure, allowing for timely adjustments or replacements.
- Bearing Checks: Since bearings are critical to the operation of conveyor rollers, regularly check them for signs of wear or damage. Replace bearings that show signs of excessive heat damage or corrosion to prevent roller failure.
Importance of Regular Inspections:
- Alignment Checks: Regularly inspect the alignment of the high temperature conveyor rollers to ensure they are uniformly positioned. Misalignment can cause uneven wear and tear, leading to premature breakdowns and reduced efficiency.
- Surface Integrity: Inspect the surface of the rollers for signs of wear, cracks, or warping. In high-temperature conditions, the integrity of the roller surface is crucial to maintain the quality and safety of the conveyed materials.
- Load Testing: Periodically test the rollers under load conditions to ensure they can handle the specified weight without deformation or failure. This is particularly important after installation or maintenance.
- System Calibration: Ensure that the conveyor system’s settings are calibrated correctly for the load and speed. Improper calibration can put unnecessary stress on the rollers, leading to faster degradation.
Adhering to these maintenance tips and performing regular inspections will help maintain the integrity and performance of high temperature conveyor rollers. These practices are essential not only for the durability of the rollers but also for the overall safety and efficiency of the conveyor system in high-temperature environments.
FAQs About High Temperature Conveyor Rollers
Conveyor rollers come in a variety of types, each designed for different industrial applications based on load requirements, environmental conditions, and operational speeds. The most common types include:
Gravity Rollers: These are simple and operate without external power, relying on gravity or manual force to move goods along.
Driven Rollers: Connected to an external power source, these rollers are used in automated conveyor systems for consistent and controlled motion.
Impact Rollers: Installed at points where items are loaded onto the conveyor, these help absorb the shock and reduce damage to both the conveyor belt and the goods.
Tapered Rollers: These are used in curved sections of conveyors to maintain the alignment and positioning of the goods.
Grooved Rollers: Often used with round belts, grooved rollers are suitable for lightweight packages and can provide directional guidance to the conveyed items.
Each type is crafted from materials that may include steel, plastic, or rubber, depending on the intended use and specific needs like temperature resistance or noise reduction.
The temperature range of conveyor belts varies widely based on the material used in their construction. Standard PVC belts, for example, can typically handle temperatures from -20°C to +80°C. Rubber belts are generally suitable for temperatures between -25°C and +100°C. For environments that demand higher or lower temperature ranges, specialized materials are used:
Teflon-coated belts are suitable for temperatures up to 250°C.
Silicone belts can handle intermittent exposures up to 180°C.
Metal belts, often made from stainless steel, can withstand temperatures up to 500°C and beyond, making them ideal for extremely high-temperature applications such as foundries or steel mills.
Choosing the correct type of belt material is crucial to avoid degradation, preserve operational integrity, and ensure safety.
The HS code (Harmonized System code) for conveyor rollers is typically 8431.39. This code is used internationally to classify and define types of equipment parts and accessories, including those for conveyors. The specific subcategory codes might vary based on the country and the exact type of roller, such as whether it’s motorized or purely mechanical. Knowing the correct HS code is important for businesses as it is used for customs declarations and international trade.
Rollers in conveyor systems serve several fundamental purposes:
Facilitating Movement: They allow the conveyor belt or items to move smoothly over long distances with minimal effort.
Reducing Friction: By providing a rolling surface, rollers significantly reduce the friction that would typically occur with a stationary surface, leading to decreased wear and tear on both the conveyor belt and the motor.
Supporting the Load: Rollers help distribute the weight of the materials being transported evenly across the surface of the conveyor, which enhances stability and prevents sagging or undue stress on the conveyor structure.
Enhancing Efficiency: Well-placed and well-maintained rollers can increase the efficiency of a conveyor system, ensuring that goods are moved swiftly and reliably from one point to another with minimal downtime and maintenance requirements.
Effective use of rollers is key to optimizing the performance and longevity of conveyor systems in various industrial settings.
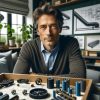
Jordan Smith, a seasoned professional with over 20 years of experience in the conveyor system industry. Jordan’s expertise lies in providing comprehensive solutions for conveyor rollers, belts, and accessories, catering to a wide range of industrial needs. From initial design and configuration to installation and meticulous troubleshooting, Jordan is adept at handling all aspects of conveyor system management. Whether you’re looking to upgrade your production line with efficient conveyor belts, require custom conveyor rollers for specific operations, or need expert advice on selecting the right conveyor accessories for your facility, Jordan is your reliable consultant. For any inquiries or assistance with conveyor system optimization, Jordan is available to share his wealth of knowledge and experience. Feel free to reach out at any time for professional guidance on all matters related to conveyor rollers, belts, and accessories.