Integration of Snub Pulley Design in Belt Conveyor Systems
A snub pulley design is essential in conveyor systems to improve belt tension and alignment. Positioned near the drive pulley, the snub pulley increases the angle of contact between the belt and drive pulley, enhancing traction and reducing slippage. Proper snub pulley design ensures efficient operation, reduces wear on the belt, and maintains optimal conveyor performance. Design considerations include pulley diameter, belt tension, and alignment, all of which are detailed in snub pulley design calculations and standards. Accessing snub pulley design PDF resources can provide further insights into the technical specifications and implementation.
Snub Pulley Design PDF
Importance of Snub Pulley Design PDFs
Understanding the design and implementation of snub pulleys in conveyor systems is crucial for engineers and technicians. Snub pulley design PDFs provide a comprehensive guide to the principles and practices involved in designing these critical components. These documents often include detailed diagrams, design standards, and calculation methods that are essential for ensuring the proper functioning and longevity of conveyor systems.
Accessing Snub Pulley Design PDFs
Many industry websites, engineering forums, and academic repositories offer snub pulley design PDFs. These resources are often available for free or through institutional subscriptions. Websites like ResearchGate, academic journals, and industry-specific publications frequently have detailed guides and papers on the subject. Additionally, many conveyor pulley manufacturers provide technical documents and design guides on their websites.
Utilizing Snub Pulley Design PDFs
To effectively use snub pulley design PDFs, one should start by familiarizing themselves with the basic concepts and terminologies related to conveyor pulley design. These documents typically cover various aspects, including the types of materials used, the mechanical properties required, and the environmental conditions to consider. By thoroughly understanding these factors, one can better interpret the technical drawings and specifications provided in the PDFs.
Benefits of Snub Pulley Design PDFs
- Comprehensive Information: Snub pulley design PDFs offer detailed information, making it easier for engineers to design efficient and reliable pulleys.
- Standardization: These documents often adhere to industry standards, ensuring that the designs meet regulatory requirements and best practices.
- Ease of Access: Having access to a well-organized PDF allows for quick reference and easy sharing among team members.
- Cost-Effective: Utilizing freely available or institutionally accessible PDFs can save significant costs compared to purchasing expensive design manuals.
Key Components Covered in Snub Pulley Design PDFs
- Design Conveyor Pulley: Understanding the overall design principles that apply to conveyor pulleys, including material selection and structural integrity.
- Conveyor Pulley Design Calculations: Detailed methodologies for calculating dimensions and load capacities to ensure optimal performance.
- Conveyor Pulley Design Standards: Industry standards that must be adhered to during the design process to ensure safety and efficiency.
- Conveyor Drive Pulley Design: Specific considerations for designing the drive pulleys that power the conveyor system.
- Conveyor Pulley Shaft Design: Detailed analysis of the shaft’s role, including stress distribution and material requirements.
- Conveyor Pulley Dimensions: Standardized dimensions and tolerances that are critical for interoperability and performance.
- Conveyor Pulley Drawing: Technical drawings that provide precise visual representations of pulley designs.
Snub Pulley Design Calculations PDF
Importance of Snub Pulley Design Calculations
Snub pulley design calculations are crucial for the safe and efficient operation of conveyor systems. These calculations help determine the appropriate size, strength, and configuration of the pulley, ensuring it can handle the intended load and operating conditions.
Accessing Snub Pulley Design Calculations PDFs
Similar to general design PDFs, snub pulley design calculations PDFs can be found on various industry and academic websites. These documents are often included in broader design guides or available as standalone resources. Manufacturers and engineering firms frequently provide calculation sheets and detailed guides on their websites.
Utilizing Snub Pulley Design Calculations PDFs
To make the most of these PDFs, it is important to have a basic understanding of mechanical engineering principles, particularly those related to force, stress, and material properties. These documents typically include step-by-step procedures for calculating key parameters, such as:
- Pulley Diameter: Determining the optimal diameter to balance load capacity and operational speed.
- Shaft Diameter: Calculating the required shaft diameter to withstand the applied forces and prevent bending or failure.
- Bearing Selection: Choosing the appropriate bearings to support the pulley and ensure smooth operation.
- Load Capacity: Assessing the maximum load the pulley can handle without compromising safety or performance.
- Material Selection: Identifying the best materials for the pulley and shaft based on the operating environment and load requirements.
Benefits of Snub Pulley Design Calculations PDFs
- Precision: Accurate calculations are essential for designing pulleys that meet specific operational requirements.
- Safety: Proper calculations help prevent failures and accidents by ensuring that pulleys are designed to handle their intended loads.
- Efficiency: Well-designed pulleys contribute to the overall efficiency of the conveyor system, reducing energy consumption and maintenance costs.
- Documentation: Having detailed calculation records is important for future reference, troubleshooting, and compliance with industry standards.
Key Components Covered in Snub Pulley Design Calculations PDFs
- Design Conveyor Pulley: Detailed steps for designing a conveyor pulley, including load analysis and material selection.
- Conveyor Pulley Design Calculations: Specific formulas and methodologies for calculating critical dimensions and load capacities.
- Conveyor Pulley Design Standards: Guidelines and standards that must be followed during the design process.
- Conveyor Drive Pulley Design: Considerations for designing pulleys that drive the conveyor system.
- Conveyor Pulley Shaft Design: Calculations related to the shaft, including diameter, material, and stress analysis.
- Conveyor Pulley Dimensions: Standard dimensions and tolerances for conveyor pulleys.
- Conveyor Pulley Drawing: Technical drawings that illustrate the design and dimensions of the pulley.
Snub Pulley Design Calculations
Snub pulley design calculations are essential for ensuring that the pulley can perform its intended function without failure. These calculations involve determining the correct dimensions, materials, and configurations to handle the specific loads and conditions of the conveyor system.
Key Calculations in Snub Pulley Design
- Pulley Diameter: The diameter of the snub pulley is a critical factor that influences the tension and wrap angle of the conveyor belt. A larger diameter can reduce the bending stress on the belt, while a smaller diameter might be necessary for space constraints.
- Shaft Diameter: The shaft must be designed to withstand the forces applied by the belt tension and the weight of the pulley itself. Calculating the correct shaft diameter involves considering the material properties and the expected load.
- Bearing Selection: Bearings support the pulley and allow it to rotate smoothly. The selection of bearings depends on the load, speed, and environmental conditions.
- Load Capacity: The maximum load that the snub pulley can handle without failing is determined by analyzing the forces acting on the pulley and ensuring that the materials and dimensions are adequate.
- Material Selection: The materials used for the pulley and shaft must be chosen based on their mechanical properties, corrosion resistance, and compatibility with the operating environment.
Steps in Snub Pulley Design Calculations
- Determine the Load Requirements: Assess the total load that the pulley will need to support, including the weight of the belt and the materials being conveyed.
- Calculate the Pulley Diameter: Use the load requirements and space constraints to determine the optimal pulley diameter.
- Select the Shaft Diameter: Calculate the shaft diameter based on the load and material properties, ensuring that it can withstand the applied forces.
- Choose the Bearings: Select appropriate bearings that can support the load and operate smoothly under the expected conditions.
- Material Selection: Choose materials that can withstand the operating environment and provide the necessary strength and durability.
Benefits of Accurate Snub Pulley Design Calculations
- Enhanced Performance: Proper calculations ensure that the pulley operates efficiently and effectively, reducing downtime and maintenance costs.
- Safety: Accurate design calculations prevent failures and accidents, ensuring the safety of personnel and equipment.
- Cost Savings: Optimized pulley designs can reduce material costs and improve the overall efficiency of the conveyor system.
- Compliance: Adhering to industry standards and guidelines in the design calculations ensures compliance with regulatory requirements and best practices.
Key Components Covered in Snub Pulley Design Calculations
- Design Conveyor Pulley: Comprehensive guidelines for designing conveyor pulleys, including material selection and structural analysis.
- Conveyor Pulley Design Calculations: Detailed steps and methodologies for calculating critical dimensions and load capacities.
- Conveyor Pulley Design Standards: Industry standards and guidelines that must be followed during the design process.
- Conveyor Drive Pulley Design: Specific considerations for designing pulleys that drive the conveyor system.
- Conveyor Pulley Shaft Design: Detailed analysis and calculations related to the shaft, including diameter, material, and stress distribution.
- Conveyor Pulley Dimensions: Standardized dimensions and tolerances for conveyor pulleys to ensure compatibility and performance.
- Conveyor Pulley Drawing: Technical drawings that provide precise visual representations of the pulley design, including dimensions and specifications.
By following these guidelines and utilizing available resources, engineers and technicians can design snub pulleys that are efficient, reliable, and compliant with industry standards. The information provided in snub pulley design PDFs and calculation guides is invaluable for achieving optimal performance and safety in conveyor systems.
Snub Pulley Design: Snub Pulley Function
The snub pulley is a critical component in belt conveyor systems, designed to enhance the efficiency and performance of the conveyor by increasing the angle of wrap of the belt around the drive pulley. This increased wrap angle provides greater traction and reduces slippage, ensuring smooth and reliable operation.
Role in Belt Conveyor Systems
In belt conveyor systems, the snub pulley serves several essential functions:
- Increased Belt Wrap: By redirecting the belt’s path, the snub pulley increases the angle of contact between the belt and the drive pulley. This additional wrap helps to distribute the load more evenly and provides better grip, reducing the likelihood of belt slippage, especially under heavy loads or during acceleration and deceleration phases.
- Tension Management: Snub pulleys help manage belt tension by creating a more consistent tension profile across the belt’s length. This uniform tension is crucial for preventing excessive wear and tear on both the belt and the pulleys, extending their operational lifespan and reducing maintenance costs.
- Improved Tracking: Proper belt alignment is vital for efficient conveyor operation. Snub pulleys assist in maintaining the belt’s tracking by keeping it aligned with the other components, preventing it from drifting off-center and causing potential operational disruptions or damage to the conveyor system.
- Energy Efficiency: By improving traction and reducing slippage, snub pulleys contribute to the overall energy efficiency of the conveyor system. Less energy is wasted in overcoming slippage, leading to lower operational costs and reduced environmental impact.
Practical Examples of Snub Pulley Applications
Snub pulleys are commonly used in various industrial applications where reliable and efficient belt conveyor operation is crucial. Some practical examples include:
- Mining Operations: In mining, snub pulleys are used in conveyor systems to transport raw materials from extraction points to processing facilities. The harsh conditions and heavy loads in mining make snub pulleys essential for maintaining belt traction and alignment, ensuring continuous and efficient material handling.
- Manufacturing Plants: In manufacturing, conveyor systems are used to move products through different stages of production. Snub pulleys help maintain the necessary belt tension and alignment, preventing disruptions in the production process and ensuring timely delivery of finished goods.
- Agricultural Processing: In agricultural processing, conveyor systems transport crops and other products through cleaning, sorting, and packaging stages. Snub pulleys ensure that the belts operate smoothly, reducing downtime and enhancing the overall efficiency of the processing line.
- Port Facilities: At ports, conveyor systems are used to load and unload bulk materials from ships. Snub pulleys help manage the heavy loads and ensure that the belts operate reliably, facilitating the efficient transfer of materials between ships and storage facilities.
Snub Pulley Design: Snub Pulley Belt Conveyor
The integration of snub pulleys into belt conveyor systems plays a pivotal role in enhancing their performance and reliability. This section delves into how snub pulleys are incorporated into conveyor setups and their impact on belt tension and alignment.
Integration into Conveyor Setups
Snub pulleys are strategically placed within the conveyor system to maximize their effectiveness. Typically, they are installed near the drive pulley or tail pulley to increase the wrap angle of the belt around these primary pulleys. The placement of snub pulleys is determined based on several factors, including the conveyor’s length, the load it carries, and the operational conditions.
- Near Drive Pulley: Placing a snub pulley near the drive pulley increases the belt’s wrap angle around the drive pulley, enhancing traction and reducing slippage. This configuration is especially useful in high-torque applications where maintaining a strong grip on the belt is critical.
- Near Tail Pulley: Installing a snub pulley near the tail pulley helps to improve belt tension at the conveyor’s start. This setup is beneficial in applications where the conveyor experiences variable loads, ensuring consistent tension throughout the belt’s length.
- Multiple Snub Pulleys: In some conveyor systems, multiple snub pulleys are used to achieve the desired tension and alignment. This approach allows for fine-tuning of the belt’s path and tension profile, providing greater control over the conveyor’s performance.
Impact on Belt Tension and Alignment
The inclusion of snub pulleys in belt conveyor systems significantly influences belt tension and alignment, both of which are crucial for optimal performance.
- Belt Tension: Snub pulleys help maintain consistent belt tension by adjusting the belt’s path and increasing the wrap angle around the drive and tail pulleys. Proper tension is essential for preventing belt sagging, reducing wear and tear, and ensuring smooth operation. Consistent tension also minimizes the risk of belt slippage, which can lead to operational disruptions and increased maintenance needs.
- Belt Alignment: Snub pulleys play a key role in keeping the belt aligned with the conveyor’s components. Misaligned belts can cause uneven wear, damage to the conveyor structure, and material spillage. By redirecting the belt’s path and maintaining the correct alignment, snub pulleys help to prevent these issues, ensuring that the belt runs smoothly and efficiently.
- Load Distribution: Snub pulleys aid in distributing the load more evenly across the belt’s surface. This even distribution reduces localized stress points and minimizes the risk of belt damage. It also helps to maintain a stable and reliable conveyor operation, especially in applications where the belt is subjected to varying loads and harsh conditions.
Snub Pulley Design: Take-Up Pulley
The take-up pulley is another crucial component in conveyor systems, responsible for maintaining proper belt tension and alignment. This section explores the role of the take-up pulley and its interaction with snub pulleys.
Role in Maintaining Belt Tension and Alignment
The primary function of the take-up pulley is to ensure that the conveyor belt remains at the correct tension. Proper belt tension is vital for preventing sagging, slippage, and misalignment, all of which can negatively impact the conveyor’s performance and efficiency.
- Automatic Adjustment: Many take-up pulleys are designed to automatically adjust the belt tension as needed. This self-adjusting mechanism helps to compensate for changes in belt length due to stretching, temperature variations, or load fluctuations. Automatic take-up pulleys are particularly useful in long conveyor systems or those operating under varying conditions.
- Manual Adjustment: Some conveyor systems use manually adjustable take-up pulleys, allowing operators to fine-tune the belt tension as required. While manual adjustment requires more oversight, it provides greater control over the tension settings and can be useful in applications where precise tension control is necessary.
- Constant Tension: Maintaining constant belt tension is essential for minimizing wear and tear on the belt and the pulleys. The take-up pulley ensures that the belt tension remains within the optimal range, preventing excessive stress on the conveyor components and reducing the risk of belt failure.
Interaction with Snub Pulleys
The take-up pulley and snub pulleys work together to maintain proper belt tension and alignment. Their interaction is crucial for ensuring the conveyor system operates smoothly and efficiently.
- Complementary Roles: While the take-up pulley primarily focuses on adjusting and maintaining belt tension, snub pulleys help to increase the wrap angle and improve traction. Together, they ensure that the belt operates under the correct tension and maintains proper alignment with the drive and tail pulleys.
- Enhanced Tension Control: By combining the functions of take-up pulleys and snub pulleys, conveyor systems achieve more precise and stable tension control. This enhanced control is particularly important in applications where the conveyor is subjected to varying loads or harsh conditions, ensuring consistent and reliable operation.
- Improved Alignment: The take-up pulley and snub pulleys also work together to maintain the belt’s alignment. Proper alignment is crucial for preventing uneven wear, reducing the risk of belt damage, and ensuring efficient material handling. The combined effect of these pulleys helps to keep the belt running smoothly and efficiently, minimizing operational disruptions and maintenance needs.
Snub Pulley Design: Design Conveyor Pulley
Designing a conveyor pulley involves several critical considerations to ensure its effective performance and longevity. This section will explore the key aspects of conveyor pulley design, including material selection, structural integrity, and operational efficiency.
Material Selection
The choice of materials for conveyor pulleys is crucial for their durability and performance. Pulley materials must withstand the operational conditions, including load capacity, environmental factors, and maintenance requirements.
- Steel: Steel is a common material for conveyor pulleys due to its strength, durability, and resistance to wear and tear. It is suitable for heavy-duty applications where the pulleys are subjected to significant loads and harsh conditions.
- Stainless Steel: Stainless steel pulleys are used in applications where corrosion resistance is essential, such as in food processing, chemical, and pharmaceutical industries. Stainless steel offers excellent resistance to rust and corrosion, ensuring long-term reliability and hygiene.
- Aluminum: Aluminum pulleys are lightweight and resistant to corrosion, making them ideal for applications where weight reduction is important. However, aluminum is less durable than steel and is typically used in lighter-duty applications.
- Composite Materials: Advanced composite materials are also used in conveyor pulley design, offering a balance of strength, weight, and corrosion resistance. These materials are suitable for specialized applications where traditional materials may not perform optimally.
Structural Integrity
Ensuring the structural integrity of conveyor pulleys is essential for their safe and efficient operation. This involves designing pulleys that can withstand the operational loads and stresses without failure.
- Hub and Shaft Connection: The connection between the hub and the shaft is a critical design aspect. It must be strong enough to transmit the required torque without slipping or causing excessive wear. Common connection methods include keyed shafts, splined shafts, and interference fits.
- Shell Design: The shell or outer surface of the pulley must be designed to withstand the forces exerted by the belt and the load. This includes considering factors such as shell thickness, reinforcement ribs, and the use of wear-resistant coatings.
- Balance and Alignment: Proper balance and alignment of the pulley are essential for minimizing vibrations and ensuring smooth operation. This involves precision manufacturing and assembly processes to ensure that the pulley is balanced and aligned correctly with the conveyor system.
Operational Efficiency
Designing conveyor pulleys for operational efficiency involves optimizing their performance to reduce energy consumption, maintenance requirements, and operational costs.
- Energy Efficiency: Energy-efficient pulley designs help to reduce the power consumption of the conveyor system. This can be achieved through features such as low-friction bearings, optimized shell design, and lightweight materials.
- Maintenance Considerations: Designing pulleys for ease of maintenance helps to minimize downtime and reduce maintenance costs. This includes features such as easily replaceable wear parts, accessible lubrication points, and modular design for quick replacement.
- Load Capacity: The pulley design must consider the load capacity requirements of the conveyor system. This involves selecting materials and structural features that can handle the expected loads without failure or excessive wear.
Snub Pulley Design Calculations
Designing a conveyor pulley involves complex calculations to ensure that the pulley can withstand the operational loads and stresses. This section will explore the key calculations involved in conveyor pulley design, including load analysis, torque calculations, and stress analysis.
Load Analysis
Load analysis is a critical step in conveyor pulley design, involving the calculation of the forces acting on the pulley due to the belt tension and the load being conveyed.
- Belt Tension: The belt tension is the primary force acting on the pulley, and it must be calculated accurately to ensure proper pulley design. This includes both the static tension (when the conveyor is at rest) and the dynamic tension (when the conveyor is operating).
- Load Distribution: The load distribution across the pulley must be considered to ensure that the pulley can handle the varying loads along its length. This involves calculating the maximum and minimum loads and designing the pulley to withstand these loads without failure.
Torque Calculations
Torque calculations are essential for determining the power requirements of the conveyor pulley and ensuring that it can transmit the required torque without slipping or excessive wear.
- Torque Requirements: The torque requirements of the pulley depend on the load being conveyed, the belt speed, and the drive motor’s power. Accurate torque calculations are essential for selecting the appropriate drive components and ensuring efficient conveyor operation.
- Drive Pulley Torque: The drive pulley torque is calculated based on the belt tension and the radius of the pulley. This calculation helps to determine the required drive motor power and the appropriate pulley design to handle the torque.
Stress Analysis
Stress analysis involves calculating the stresses acting on the pulley components to ensure that they can withstand the operational loads without failure.
- Shell Stress: The shell stress is calculated based on the belt tension and the load distribution. This includes considering both the axial and radial stresses acting on the shell and designing the shell to withstand these stresses without deformation or failure.
- Hub and Shaft Stress: The hub and shaft stress is calculated based on the torque requirements and the connection method between the hub and the shaft. This includes considering the bending and torsional stresses acting on the hub and shaft and designing them to withstand these stresses without failure.
- Bearing Stress: The bearing stress is calculated based on the load distribution and the rotational speed of the pulley. This includes considering both the radial and axial loads acting on the bearings and selecting bearings that can handle these loads without excessive wear or failure.
Snub Pulley Design Standards
Design standards are essential for ensuring the safety and reliability of conveyor pulleys. This section will explore the key design standards for conveyor pulleys, including industry standards, material standards, and manufacturing standards.
Industry Standards
Industry standards provide guidelines for the design, manufacturing, and testing of conveyor pulleys to ensure their safety and reliability.
- CEMA: The Conveyor Equipment Manufacturers Association (CEMA) provides standards for the design and manufacturing of conveyor pulleys. CEMA standards cover various aspects of pulley design, including material selection, load capacity, and safety requirements.
- ISO: The International Organization for Standardization (ISO) provides global standards for conveyor pulley design. ISO standards cover various aspects of pulley design, including material selection, load capacity, and safety requirements.
- ASME: The American Society of Mechanical Engineers (ASME) provides standards for the design and manufacturing of conveyor pulleys. ASME standards cover various aspects of pulley design, including material selection, load capacity, and safety requirements.
Material Standards
Material standards provide guidelines for the selection of materials used in conveyor pulley design to ensure their durability and performance.
- ASTM: The American Society for Testing and Materials (ASTM) provides standards for the selection of materials used in conveyor pulley design. ASTM standards cover various aspects of material selection, including material properties, testing methods, and safety requirements.
- DIN: The Deutsches Institut für Normung (DIN) provides standards for the selection of materials used in conveyor pulley design. DIN standards cover various aspects of material selection, including material properties, testing methods, and safety requirements.
- BS: The British Standards Institution (BS) provides standards for the selection of materials used in conveyor pulley design. BS standards cover various aspects of material selection, including material properties, testing methods, and safety requirements.
Manufacturing Standards
Manufacturing standards provide guidelines for the manufacturing processes used in conveyor pulley design to ensure their quality and consistency.
- ISO 9001: The ISO 9001 standard provides guidelines for quality management systems used in the manufacturing of conveyor pulleys. ISO 9001 covers various aspects of manufacturing processes, including quality control, testing methods, and safety requirements.
- Lean Manufacturing: Lean manufacturing principles provide guidelines for optimizing the manufacturing processes used in conveyor pulley design. Lean manufacturing covers various aspects of manufacturing processes, including waste reduction, efficiency improvement, and quality control.
- Six Sigma: Six Sigma principles provide guidelines for improving the quality and consistency of manufacturing processes used in conveyor pulley design. Six Sigma covers various aspects of manufacturing processes, including process optimization, defect reduction, and quality control.
Conveyor Drive Pulley Design
The design of the conveyor drive pulley is crucial for the efficient and reliable operation of the conveyor system. This section will explore the key aspects of conveyor drive pulley design, including power requirements, material selection, and structural integrity.
Power Requirements
The power requirements of the conveyor drive pulley are critical for ensuring that the pulley can transmit the required torque and drive the conveyor belt efficiently.
- Motor Selection: The selection of the drive motor is based on the power requirements of the conveyor system. This includes calculating the required torque and speed to drive the conveyor belt and selecting a motor that can provide the necessary power.
- Drive Components: The drive components, including the gearbox and coupling, must be selected to transmit the required torque from the motor to the drive pulley. This includes considering factors such as load capacity, efficiency, and maintenance requirements.
Material Selection
The material selection for the conveyor drive pulley is critical for its durability and performance.
- Steel: Steel is a common material for conveyor drive pulleys due to its strength, durability, and resistance to wear and tear. It is suitable for heavy-duty applications where the pulleys are subjected to significant loads and harsh conditions.
- Stainless Steel: Stainless steel drive pulleys are used in applications where corrosion resistance is essential. Stainless steel offers excellent resistance to rust and corrosion, ensuring long-term reliability and hygiene.
- Composite Materials: Advanced composite materials are also used in conveyor drive pulley design, offering a balance of strength, weight, and corrosion resistance. These materials are suitable for specialized applications where traditional materials may not perform optimally.
Structural Integrity
Ensuring the structural integrity of the conveyor drive pulley is essential for its safe and efficient operation.
- Shell Design: The shell or outer surface of the drive pulley must be designed to withstand the forces exerted by the belt and the load. This includes considering factors such as shell thickness, reinforcement ribs, and the use of wear-resistant coatings.
- Hub and Shaft Connection: The connection between the hub and the shaft is a critical design aspect. It must be strong enough to transmit the required torque without slipping or causing excessive wear. Common connection methods include keyed shafts, splined shafts, and interference fits.
- Balance and Alignment: Proper balance and alignment of the drive pulley are essential for minimizing vibrations and ensuring smooth operation. This involves precision manufacturing and assembly processes to ensure that the pulley is balanced and aligned correctly with the conveyor system.
Snub Pulley Design: Conveyor Pulley Shaft Design
The design of the conveyor pulley shaft is crucial for ensuring that it can withstand the operational loads and stresses without failure. This section will explore the key aspects of conveyor roller shaft design, including material selection, stress analysis, and manufacturing processes.
Material Selection
The material selection for the conveyor pulley shaft is critical for its durability and performance.
- Steel: Steel is a common material for conveyor pulley shafts due to its strength, durability, and resistance to wear and tear. It is suitable for heavy-duty applications where the shafts are subjected to significant loads and harsh conditions.
- Stainless Steel: Stainless steel shafts are used in applications where corrosion resistance is essential. Stainless steel offers excellent resistance to rust and corrosion, ensuring long-term reliability and hygiene.
- Alloy Steel: Alloy steel shafts are used in applications where enhanced strength and toughness are required. Alloy steel offers improved mechanical properties, making it suitable for high-stress applications.
Stress Analysis
Stress analysis involves calculating the stresses acting on the pulley shaft to ensure that it can withstand
the operational loads without failure.
- Bending Stress: The bending stress is calculated based on the load distribution along the shaft’s length. This includes considering the maximum and minimum loads and designing the shaft to withstand these loads without deformation or failure.
- Torsional Stress: The torsional stress is calculated based on the torque requirements of the conveyor system. This includes considering the torsional forces acting on the shaft and designing the shaft to withstand these forces without failure.
- Shear Stress: The shear stress is calculated based on the load distribution and the connection method between the shaft and the hub. This includes considering the shear forces acting on the shaft and designing the shaft to withstand these forces without failure.
Manufacturing Processes
The manufacturing processes used in conveyor pulley shaft design are critical for ensuring the quality and consistency of the shafts.
- Precision Machining: Precision machining processes are used to manufacture the shafts to the required specifications. This includes using advanced machining techniques to ensure the shafts are produced with high accuracy and consistency.
- Heat Treatment: Heat treatment processes are used to enhance the mechanical properties of the shafts. This includes processes such as quenching and tempering to improve the shafts’ strength, toughness, and wear resistance.
- Quality Control: Quality control processes are used to ensure that the shafts meet the required standards and specifications. This includes using advanced testing methods to verify the shafts’ mechanical properties and dimensional accuracy.
Snub Pulley Design: Conveyor Pulley Design
Designing conveyor pulleys involves several critical considerations to ensure their effective performance and longevity. This section will explore the key aspects of conveyor pulley design, including material selection, structural integrity, and operational efficiency.
Material Selection
The choice of materials for conveyor pulleys is crucial for their durability and performance. Pulley materials must withstand the operational conditions, including load capacity, environmental factors, and maintenance requirements.
- Steel: Steel is a common material for conveyor pulleys due to its strength, durability, and resistance to wear and tear. It is suitable for heavy-duty applications where the pulleys are subjected to significant loads and harsh conditions.
- Stainless Steel: Stainless steel pulleys are used in applications where corrosion resistance is essential, such as in food processing, chemical, and pharmaceutical industries. Stainless steel offers excellent resistance to rust and corrosion, ensuring long-term reliability and hygiene.
- Aluminum: Aluminum pulleys are lightweight and resistant to corrosion, making them ideal for applications where weight reduction is important. However, aluminum is less durable than steel and is typically used in lighter-duty applications.
- Composite Materials: Advanced composite materials are also used in conveyor pulley design, offering a balance of strength, weight, and corrosion resistance. These materials are suitable for specialized applications where traditional materials may not perform optimally.
Structural Integrity
Ensuring the structural integrity of conveyor pulleys is essential for their safe and efficient operation. This involves designing pulleys that can withstand the operational loads and stresses without failure.
- Hub and Shaft Connection: The connection between the hub and the shaft is a critical design aspect. It must be strong enough to transmit the required torque without slipping or causing excessive wear. Common connection methods include keyed shafts, splined shafts, and interference fits.
- Shell Design: The shell or outer surface of the pulley must be designed to withstand the forces exerted by the belt and the load. This includes considering factors such as shell thickness, reinforcement ribs, and the use of wear-resistant coatings.
- Balance and Alignment: Proper balance and alignment of the pulley are essential for minimizing vibrations and ensuring smooth operation. This involves precision manufacturing and assembly processes to ensure that the pulley is balanced and aligned correctly with the conveyor system.
Operational Efficiency
In the context of snub pulley design, designing conveyor pulleys for operational efficiency involves optimizing their performance to reduce energy consumption, maintenance requirements, and operational costs.
- Energy Efficiency: Energy-efficient pulley designs help to reduce the power consumption of the conveyor system. This can be achieved through features such as low-friction bearings, optimized shell design, and lightweight materials.
- Maintenance Considerations: Designing pulleys for ease of maintenance helps to minimize downtime and reduce maintenance costs. This includes features such as easily replaceable wear parts, accessible lubrication points, and modular design for quick replacement.
- Load Capacity: The pulley design must consider the load capacity requirements of the conveyor system. This involves selecting materials and structural features that can handle the expected loads without failure or excessive wear.
FAQs about Snub Pulley Design
What is a snub pulley?
What is the wrap angle of a snub pulley?
How to design a conveyor pulley?
What is the function of snub roller?
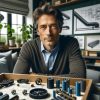
Jordan Smith, a seasoned professional with over 20 years of experience in the conveyor system industry. Jordan’s expertise lies in providing comprehensive solutions for conveyor rollers, belts, and accessories, catering to a wide range of industrial needs. From initial design and configuration to installation and meticulous troubleshooting, Jordan is adept at handling all aspects of conveyor system management. Whether you’re looking to upgrade your production line with efficient conveyor belts, require custom conveyor rollers for specific operations, or need expert advice on selecting the right conveyor accessories for your facility, Jordan is your reliable consultant. For any inquiries or assistance with conveyor system optimization, Jordan is available to share his wealth of knowledge and experience. Feel free to reach out at any time for professional guidance on all matters related to conveyor rollers, belts, and accessories.