Benefits of Installing a Pulley Magnet in Conveyors
A pulley magnet is an essential component in conveyor systems, designed to remove ferrous contaminants from the material flow. By integrating a pulley magnet into the conveyor belt system, industries can achieve continuous and automatic separation of metal impurities. The pulley magnet attracts and holds ferrous particles as the material passes over it, ensuring only clean material continues through the production line. This not only improves product purity but also protects downstream equipment from potential damage caused by metal debris. Common applications of a pulley magnet include recycling plants, mining operations, and food processing facilities, where maintaining high standards of material purity and equipment safety is critical.
The Pulley Magnet: Magnetic Separators
Overview of Different Types of Magnetic Separators, Including Pulleys and Cross Belt Magnets
Magnetic separators are critical components in various industrial processes, designed to remove ferrous contaminants from materials to ensure product purity and protect machinery. Among the different types of magnetic separators, pulley magnets and cross belt magnets are widely used due to their efficiency and versatility.
Pulley Magnets
Pulley magnets, also known as magnetic head pulleys, are installed at the discharge end of conveyor belts. They function as both a pulley and a magnetic separator, attracting and removing ferrous metals from the material flow as it moves off the end of the conveyor. The ferrous materials are held to the belt until they move out of the magnetic field, where they are discharged into a separate collection area.
Key Features of Pulley Magnets:
- Simple integration with existing conveyor systems.
- Continuous separation of ferrous materials.
- Low maintenance requirements.
- Efficient removal of tramp metal to protect downstream equipment.
Cross Belt Magnets
Cross belt magnets are suspended above conveyor belts and use a powerful magnet to lift and remove ferrous materials from the conveyed product. The magnet is mounted on a frame that spans the conveyor belt, and a motorized belt runs perpendicular to the main conveyor, carrying the captured ferrous materials to a discharge point.
Key Features of Cross Belt Magnets:
- High-intensity magnetic fields for effective separation.
- Continuous operation with automatic discharge of ferrous materials.
- Adjustable height and angle for optimal performance.
- Versatility to handle various types of conveyed materials.
Importance of Magnetic Separators in Ensuring Material Purity and Protecting Equipment
Magnetic separators play a crucial role in maintaining the quality and safety of industrial processes by ensuring material purity and protecting equipment from damage.
Ensuring Material Purity
One of the primary functions of magnetic separators is to remove ferrous contaminants from materials, ensuring that the end product is free from metal impurities. This is particularly important in industries such as food processing, pharmaceuticals, and chemicals, where product purity is critical for safety and quality.
By removing ferrous metals, magnetic separators help maintain high standards of product integrity, preventing contamination that could lead to product recalls, regulatory non-compliance, and damage to brand reputation.
Protecting Equipment
Ferrous contaminants in material streams can cause significant damage to processing equipment, leading to costly repairs, maintenance, and downtime. Magnetic separators, including pulley magnets and cross belt magnets, remove these metal contaminants before they reach sensitive machinery.
By protecting equipment from metal damage, magnetic separators extend the lifespan of machinery, reduce maintenance costs, and enhance overall operational efficiency. This protection is vital in industries such as mining, recycling, and manufacturing, where equipment uptime is crucial for productivity and profitability.
Applications and Benefits of Using Magnetic Separators in Various Industries
Magnetic separators, particularly magnetic pulley conveyor and cross belt magnets, are used in a wide range of industries due to their effectiveness and versatility. Here are some of the key applications and benefits of using magnetic separators.
Recycling Industry
In the recycling industry, magnetic separators are essential for separating ferrous metals from mixed waste streams. This separation process ensures that valuable metals are recovered and non-metallic materials are free from metal contamination.
Benefits in Recycling:
- Efficient recovery of ferrous metals for recycling.
- Protection of shredders and crushers from metal damage.
- Improved quality of recycled materials.
- Increased profitability through the recovery of valuable metals.
Mining Industry
The mining industry relies heavily on magnetic separators to remove tramp iron and other ferrous contaminants from extracted ores. This separation process protects crushers, grinders, and other processing equipment, ensuring efficient and safe operations.
Benefits in Mining:
- Protection of processing equipment from metal damage.
- Enhanced safety and operational efficiency.
- Improved quality of mined materials.
- Reduced maintenance and repair costs.
Food Processing Industry
In the food processing industry, maintaining product purity is paramount. Magnetic separators are used to remove ferrous contaminants from raw materials and finished products, ensuring that food products are safe for consumption.
Benefits in Food Processing:
- Ensuring product purity and safety.
- Compliance with food safety regulations.
- Protection of processing equipment from metal damage.
- Prevention of product recalls and brand damage.
Pharmaceutical Industry
The pharmaceutical industry requires the highest standards of product purity. Magnetic separators are used to remove ferrous contaminants from raw materials, ensuring that pharmaceutical products meet stringent quality and safety standards.
Benefits in Pharmaceuticals:
- Ensuring the purity and safety of pharmaceutical products.
- Compliance with regulatory standards.
- Protection of processing equipment from metal contamination.
- Prevention of costly product recalls.
Chemical Industry
In the chemical industry, magnetic separators are used to remove ferrous contaminants from raw materials and finished products, ensuring product quality and protecting equipment from metal damage.
Benefits in Chemicals:
- Ensuring the purity of chemical products.
- Protection of sensitive processing equipment.
- Compliance with industry standards.
- Reduced maintenance and repair costs.
Aggregate and Construction Industry
Magnetic separators are used in the aggregate and construction industry to remove ferrous metals from crushed stone, sand, and gravel. This separation process ensures the quality of construction materials and protects processing equipment.
Benefits in Construction:
- Ensuring the quality of construction materials.
- Protection of crushers and other processing equipment.
- Improved operational efficiency.
- Reduced maintenance and repair costs.
The Essential Role of Pulley Magnet Systems in Industrial Material Separation
A pulley magnet is a crucial component in the field of material separation, playing a vital role in ensuring the purity and quality of processed materials in various industrial applications. This article explores the functionality of cross belt magnets, the differences between cross belt magnets and magnetic pulleys, and the advantages of using cross belt magnets in industrial settings.
Cross Belt Magnet
Explanation of Cross Belt Magnets and Their Use in Material Separation
Cross belt magnets are powerful magnetic devices designed to remove ferrous materials from a product stream as they travel on a conveyor belt. These magnets are typically suspended over the conveyor belt and run perpendicular to the flow of the material. Their primary function is to attract and remove ferrous contaminants, ensuring that only clean, non-magnetic materials continue through the processing line.
Functionality of Cross Belt Magnets:
- Magnetic Field: Cross belt magnets generate a strong magnetic field that penetrates through the material on the conveyor belt. This field attracts ferrous particles, pulling them out of the product stream.
- Separation Process: As the conveyor belt moves, the ferrous contaminants are lifted and held against the magnet. The cross belt magnet is equipped with a self-cleaning mechanism that continuously removes the captured ferrous materials, depositing them into a separate collection area.
- Continuous Operation: The self-cleaning feature of cross belt magnets allows for continuous operation without the need for manual intervention. This ensures a steady and efficient separation process, crucial for high-volume industrial applications.
Differences Between Cross Belt Magnets and Magnetic Pulleys
While both cross belt magnets and magnetic pulleys serve the purpose of separating ferrous materials from a product stream, they have distinct operational differences and applications.
Installation and Placement:
- Cross Belt Magnets: These magnets are suspended above the conveyor belt, running perpendicular to the material flow. They do not come into direct contact with the materials but use a magnetic field to attract and lift ferrous contaminants from above.
- Magnetic Pulleys: A magnetic pulley replaces the standard head pulley at the end of the conveyor belt. It interacts directly with the material, attracting and removing ferrous particles as the belt turns around the pulley.
Separation Efficiency:
- Cross Belt Magnets: These magnets are particularly effective at removing ferrous materials from the top layers of the product stream. They are ideal for applications where contaminants are likely to be found on the surface.
- Magnetic Pulleys: Magnetic pulleys are efficient at removing ferrous materials embedded within the product stream. As materials pass over the pulley, the magnetic field pulls out ferrous particles, ensuring thorough separation.
Flexibility and Control:
- Cross Belt Magnets: These magnets can be either permanent or electromagnetic. Electromagnetic cross belt magnets offer adjustable magnetic strength, providing greater control and flexibility for different applications.
- Magnetic Pulleys: Typically, magnetic pulleys are permanent magnets, offering consistent magnetic strength without the need for external power. They provide reliable, continuous separation but with less control over magnetic field adjustments.
Maintenance Requirements:
- Cross Belt Magnets: The self-cleaning mechanism in cross belt magnets reduces the need for manual cleaning, making them easier to maintain. Regular inspections are necessary to ensure the mechanism functions correctly.
- Magnetic Pulleys: These pulleys require less maintenance compared to cross belt magnets. The primary maintenance involves ensuring the conveyor belt and pulley are in good working condition and free from excessive wear.
Advantages of Using Cross Belt Magnets in Industrial Applications
Cross belt magnets offer several advantages that make them highly valuable in various industrial applications. Here are some key benefits:
Enhanced Material Purity:
- Efficient Separation: Cross belt magnets efficiently remove ferrous contaminants from the material stream, ensuring high purity levels in the final product. This is crucial for industries where product quality is paramount, such as food processing and pharmaceuticals.
- Continuous Operation: The continuous, self-cleaning operation of cross belt magnets ensures consistent separation performance, reducing the risk of contamination in subsequent processing stages.
Protection of Equipment:
- Reduced Wear and Tear: By removing ferrous contaminants, cross belt magnets help protect downstream equipment from damage and excessive wear. This extends the lifespan of machinery and reduces maintenance costs.
- Preventing Downtime: Protecting equipment from damage caused by ferrous materials minimizes unexpected breakdowns and operational downtime, ensuring smoother and more reliable production processes.
Increased Operational Efficiency:
- Automated Process: The automated, self-cleaning operation of cross belt magnets improves the efficiency of material handling processes. This reduces the need for manual intervention and allows for higher throughput.
- Labor Cost Savings: Automated separation reduces labor costs associated with manual sorting and inspection, increasing overall productivity.
Versatility and Adaptability:
- Wide Range of Applications: Cross belt magnets are versatile and can be used in various industries, including recycling, mining, food processing, and bulk material handling. Their adaptability makes them suitable for different types of conveyor systems and material handling requirements.
- Customizable Solutions: Cross belt magnets can be customized to meet specific operational needs. This includes adjusting the magnetic strength, size, and design to suit different applications and material characteristics.
Environmental Benefits:
- Recycling and Waste Reduction: In recycling operations, cross belt magnets play a critical role in separating ferrous metals from waste streams, facilitating the recycling process and reducing landfill waste.
- Resource Conservation: By effectively separating and recovering ferrous materials, cross belt magnets contribute to the conservation of valuable resources and support sustainable manufacturing practices.
What is The Pulley Magnet: Magnetic Head Pulley
Magnetic Head Pulley
Description of the Function and Benefits of Magnetic Head Pulleys
Magnetic head pulleys, often referred to as permanent magnetic pulleys, are crucial components in conveyor systems, designed to separate ferrous materials from non-ferrous ones efficiently. These pulleys are integrated into the conveyor system’s drive pulley and use powerful magnets to attract and hold ferrous contaminants, ensuring that only clean, non-metallic materials continue along the conveyor.
Function of Magnetic Head Pulleys
The primary function of a magnetic head pulley is to remove ferrous contaminants from the material flow on the conveyor belt. As the conveyor belt carries the material toward the pulley, the magnetic field of the pulley attracts any ferrous particles. These particles are then held against the belt until they move out of the magnetic field, where they are discharged into a separate collection area. This continuous process ensures that the conveyor system effectively separates metal contaminants from the material flow, enhancing the purity of the end product.
Benefits of Magnetic Head Pulleys
Magnetic head pulleys offer numerous benefits that make them indispensable in various industrial applications:
- Continuous and Automatic Separation: Magnetic head pulleys provide continuous, automatic separation of ferrous materials, reducing the need for manual intervention and increasing efficiency.
- Improved Product Purity: By removing ferrous contaminants, magnetic head pulleys ensure that the end products are pure and free from metal impurities, which is essential for maintaining high quality in industries such as food processing, pharmaceuticals, and chemicals.
- Equipment Protection: Ferrous contaminants can cause significant damage to processing equipment, leading to costly repairs and downtime. Magnetic head pulleys protect equipment by removing these contaminants before they can cause harm.
- Low Maintenance: Magnetic head pulleys are designed for durability and require minimal maintenance, making them a cost-effective solution for long-term use.
- Versatility: These pulleys can be used in various conveyor systems, making them adaptable to different industrial environments and material handling needs.
Applications of Magnetic Head Pulleys in Conveyor Systems
Magnetic head pulleys are used in a wide range of industries, each benefiting from the ability to remove ferrous contaminants and protect equipment. Some of the most common applications include:
Recycling Industry
In the recycling industry, magnetic head pulleys are essential for separating ferrous metals from mixed waste streams. This separation process is crucial for recovering valuable metals and ensuring that non-metallic materials are free from metal contamination. By integrating magnetic head pulleys into their conveyor systems, recycling facilities can improve the efficiency and effectiveness of their operations.
Key Applications in Recycling:
- Separating ferrous metals from municipal solid waste.
- Recovering metals from construction and demolition debris.
- Sorting electronic scrap to extract valuable metals.
Mining Industry
The mining industry relies heavily on magnetic head pulleys to remove tramp iron and other ferrous contaminants from extracted ores. This separation process protects crushers, grinders, and other processing equipment from damage, ensuring efficient and safe operations.
Key Applications in Mining:
- Removing metal contaminants from conveyor belts carrying mined ores.
- Protecting crushers and grinders from ferrous materials.
- Ensuring the purity of extracted minerals.
Food Processing Industry
In the food processing industry, maintaining product purity is paramount. Magnetic head pulleys are used to remove ferrous contaminants from raw materials and finished products, ensuring that food products are safe for consumption and meet strict quality standards.
Key Applications in Food Processing:
- Removing metal fragments from bulk food ingredients.
- Ensuring the purity of finished food products.
- Protecting processing equipment from metal damage.
Pharmaceutical Industry
The pharmaceutical industry requires the highest standards of product purity and safety. Magnetic head pulleys are used to remove ferrous contaminants from raw materials, ensuring that pharmaceutical products are free from metal impurities and meet stringent regulatory requirements.
Key Applications in Pharmaceuticals:
- Removing metal contaminants from pharmaceutical ingredients.
- Ensuring the purity and safety of pharmaceutical products.
- Protecting processing equipment from metal contamination.
Chemical Industry
In the chemical industry, magnetic head pulleys are used to remove ferrous contaminants from raw materials and finished products. This ensures product quality and protects sensitive processing equipment from metal damage.
Key Applications in Chemicals:
- Ensuring the purity of chemical products.
- Removing metal contaminants from raw materials.
- Protecting processing equipment from metal damage.
Aggregate and Construction Industry
Magnetic head pulleys are used in the aggregate and construction industry to remove ferrous metals from crushed stone, sand, and gravel. This separation process ensures the quality of construction materials and protects processing equipment from metal damage.
Key Applications in Construction:
- Ensuring the quality of construction materials.
- Removing metal contaminants from aggregates.
- Protecting crushers and other processing equipment.
How Magnetic Head Pulleys Improve Material Purity and Equipment Safety
Magnetic head pulleys play a crucial role in improving material purity and equipment safety in various industries. By effectively removing ferrous contaminants, these pulleys ensure that the final products are free from metal impurities, which is essential for maintaining high quality and safety standards.
Improving Material Purity
The ability of magnetic head pulleys to continuously and automatically remove ferrous materials from the conveyor belt stream ensures that the end products are pure and free from metal contaminants. This is particularly important in industries such as food processing, pharmaceuticals, and chemicals, where product purity is critical for safety and compliance with regulatory standards.
By ensuring that only non-ferrous materials continue along the conveyor, magnetic head pulleys help maintain high standards of product integrity, preventing contamination that could lead to product recalls, regulatory non-compliance, and damage to brand reputation.
Enhancing Equipment Safety
Ferrous contaminants in material streams can cause significant damage to processing equipment, leading to costly repairs, maintenance, and downtime. Magnetic head pulleys remove these metal contaminants before they reach sensitive machinery, protecting the equipment and ensuring smooth and efficient operation.
By reducing the risk of metal damage, magnetic head pulleys extend the lifespan of machinery, reduce maintenance costs, and enhance overall operational efficiency. This protection is vital in industries such as mining, recycling, and manufacturing, where equipment uptime is crucial for productivity and profitability.
Additional Safety Measures
In addition to improving material purity and protecting equipment, magnetic head pulleys also contribute to overall workplace safety. By removing ferrous contaminants, these pulleys reduce the risk of metal shards and debris causing injuries to workers. This is particularly important in industries where workers are in close proximity to conveyor systems and processing equipment.
Ensuring a clean and safe working environment helps prevent accidents and injuries, contributing to a safer and more productive workplace.
The Role of Pulley Magnet Systems in Enhancing Compressor Efficiency
A pulley magnet is a critical component in many industrial systems, including compressors. By integrating magnetic technology into compressor operations, industries can achieve significant improvements in efficiency and performance. This article explores the role of magnetic pulleys in enhancing compressor efficiency, provides examples of their use in various compressor applications, and highlights the benefits of using magnetic pulleys in these systems.
Magnetic Pulley Compressor
Role of Magnetic Pulleys in Enhancing Compressor Efficiency
Magnetic pulleys play a pivotal role in enhancing the efficiency of compressor systems. Compressors are vital in numerous industrial applications, including air conditioning, refrigeration, and pneumatic tools. The integration of a pulley magnet into these systems can significantly improve their performance and energy efficiency.
Energy Efficiency:
- Reduced Friction: Magnetic pulleys reduce friction between moving parts within the compressor. This reduction in friction leads to lower energy consumption, as less force is required to drive the system.
- Improved Power Transmission: Magnetic pulleys provide more efficient power transmission, reducing the load on the compressor motor and enhancing overall system efficiency.
Operational Stability:
- Consistent Performance: The use of magnetic pulleys ensures consistent performance by maintaining optimal tension and alignment of the compressor belts. This stability reduces wear and tear on the system, extending its operational life.
- Reduced Maintenance: Magnetic pulleys help in maintaining the correct alignment and tension of the belts, reducing the need for frequent adjustments and maintenance.
Examples of How Magnetic Pulleys Are Used in Various Compressor Applications
Magnetic pulleys are utilized in a variety of compressor applications across different industries, contributing to improved efficiency and reliability.
Air Conditioning Systems:
- Automotive Air Conditioning: In automotive air conditioning systems, magnetic pulleys are used to drive the compressor. The reduced friction and improved power transmission provided by the pulley magnet lead to better fuel efficiency and smoother operation.
- Commercial and Residential Air Conditioning: Magnetic pulleys are also used in large-scale air conditioning systems for commercial buildings and residential complexes. They help in reducing energy consumption and enhancing the efficiency of the cooling process.
Refrigeration Systems:
- Industrial Refrigeration: In industrial refrigeration systems, magnetic pulleys are employed to drive large compressors that maintain low temperatures in cold storage facilities. The increased efficiency and reliability provided by the magnetic pulley conveyor ensure consistent cooling and energy savings.
- Supermarket Refrigeration: Magnetic pulleys are also used in refrigeration systems in supermarkets, where they help in maintaining optimal temperatures for perishable goods while reducing operational costs.
Pneumatic Tools and Systems:
- Manufacturing: In manufacturing facilities, compressors are used to power pneumatic tools and machinery. Magnetic pulleys enhance the efficiency of these compressors, leading to improved performance of pneumatic equipment and reduced energy costs.
- Construction: In the construction industry, portable compressors are used to power tools such as jackhammers and nail guns. The integration of magnetic pulleys in these compressors ensures reliable operation and energy efficiency, making them more effective for on-site applications.
HVAC Systems:
- Heating, Ventilation, and Air Conditioning: HVAC systems in large buildings rely on compressors to regulate air temperature and quality. Magnetic pulleys improve the efficiency of these compressors, leading to better climate control and energy savings.
Benefits of Using Magnetic Pulleys in Compressor Systems
The integration of magnetic pulleys into compressor systems offers several significant benefits that enhance the overall performance and efficiency of these systems.
Energy Savings:
- Lower Energy Consumption: Magnetic pulleys reduce the energy required to drive compressors by minimizing friction and improving power transmission. This leads to substantial energy savings, which is particularly beneficial in large-scale industrial applications.
- Cost Efficiency: Reduced energy consumption translates into lower operational costs, making magnetic pulleys a cost-effective solution for improving compressor efficiency.
Improved Reliability:
- Enhanced Durability: By reducing wear and tear on compressor components, magnetic pulleys enhance the durability and reliability of the system. This results in fewer breakdowns and less downtime, ensuring continuous operation.
- Consistent Performance: Magnetic pulleys maintain consistent belt tension and alignment, leading to stable and reliable compressor performance.
Extended Equipment Life:
- Reduced Wear: The reduced friction provided by magnetic pulleys minimizes wear on belts and other moving parts. This extends the life of the compressor components, reducing the need for frequent replacements.
- Lower Maintenance Costs: The decreased wear and tear result in lower maintenance requirements and costs. This is particularly advantageous in industries where equipment reliability is critical.
Environmental Benefits:
- Reduced Carbon Footprint: The energy savings achieved through the use of magnetic pulleys contribute to a lower carbon footprint. This supports environmental sustainability initiatives and helps industries comply with energy efficiency regulations.
- Sustainable Operation: By enhancing the efficiency of compressors, magnetic pulleys promote sustainable industrial operations. This aligns with the growing emphasis on green technologies and energy conservation.
Versatility and Adaptability:
- Wide Range of Applications: Magnetic pulleys are versatile and can be used in various compressor applications across different industries. Their adaptability makes them suitable for both small-scale and large-scale operations.
- Customizable Solutions: Magnetic pulleys can be customized to meet specific operational needs, including adjusting the magnetic strength and size to suit different compressor systems.
Selecting the Best Pulley Magnet: Insights into Magnetic Pulley Manufacturers
Overview of Leading Manufacturers of Magnetic Pulleys
Magnetic pulleys, also known as magnetic conveyor pulleys, are essential components in various industries, providing effective separation of ferrous materials from non-ferrous ones. The quality and performance of these magnetic pulleys depend significantly on the expertise and reliability of the manufacturers. Here is an overview of some leading manufacturers known for their high-quality magnetic pulleys:
Eriez Manufacturing Co.
Eriez is a global leader in the design and manufacture of magnetic separation equipment, including magnetic pulleys. Known for their innovation and quality, Eriez magnetic pulleys are widely used in recycling, mining, and aggregate industries. Their products are designed to offer high efficiency and durability, ensuring long-term performance in demanding environments.
Key Features:
- High-intensity magnets for effective separation.
- Robust construction for durability.
- Customizable designs to fit specific needs.
Bunting Magnetics Co.
Bunting Magnetics Co. is another prominent manufacturer of magnetic pulleys, offering a wide range of products tailored to various industrial applications. Bunting’s magnetic pulleys are known for their strength and reliability, making them suitable for heavy-duty applications. The company emphasizes innovation and customer satisfaction, providing solutions that meet the highest industry standards.
Key Features:
- Strong magnetic fields for efficient separation.
- Durable materials for long-lasting use.
- Versatile designs for multiple applications.
Dings Magnetic Group
Dings Magnetic Group has been a trusted name in magnetic separation technology for over a century. Their magnetic pulleys are engineered to provide maximum separation efficiency and durability. Dings offers a variety of magnetic pulleys designed to meet the needs of different industries, from recycling to mining.
Key Features:
- High-performance magnets.
- Sturdy construction for tough environments.
- Customizable options for specific applications.
Industrial Magnetics, Inc. (IMI)
Industrial Magnetics, Inc. (IMI) specializes in magnetic solutions for industrial applications. Their magnetic pulleys are designed to provide reliable and efficient separation of ferrous materials, helping to improve product purity and protect processing equipment. IMI’s commitment to quality and innovation ensures that their products meet the highest standards.
Key Features:
- Efficient magnetic separation.
- Durable and reliable design.
- Custom solutions for unique requirements.
Importance of Choosing a Reliable Manufacturer for Quality and Durability
Choosing a reliable manufacturer for magnetic pulleys is crucial for ensuring the quality and durability of the equipment. The following points highlight the importance of selecting a reputable manufacturer:
Ensuring Product Quality
A reliable manufacturer uses high-quality materials and advanced manufacturing processes to produce magnetic pulleys. This ensures that the products are robust, efficient, and capable of withstanding harsh industrial environments. High-quality magnetic pulleys provide consistent performance, reducing the risk of equipment failure and operational disruptions.
Enhancing Operational Efficiency
Magnetic pulleys from reputable manufacturers are designed to operate efficiently, providing effective separation of ferrous materials. This enhances the overall efficiency of the material handling process, improving product purity and protecting downstream equipment. Efficient magnetic pulleys help reduce maintenance costs and downtime, contributing to smoother operations.
Providing Custom Solutions
Leading manufacturers offer customizable magnetic pulleys to meet the specific needs of different applications. By choosing a reliable manufacturer, businesses can access tailored solutions that address their unique requirements, ensuring optimal performance and functionality.
Offering Technical Support and Service
Reputable manufacturers provide comprehensive technical support and service to their customers. This includes assistance with installation, maintenance, and troubleshooting, ensuring that the magnetic pulleys operate at peak efficiency. Access to expert support helps businesses maximize the lifespan and performance of their equipment.
Key Factors to Consider When Selecting a Magnetic Pulley Manufacturer
Selecting the right magnetic pulley manufacturer involves considering several key factors to ensure that the chosen products meet the desired standards of quality and performance. Here are some important factors to consider:
Experience and Reputation
When selecting a magnetic pulley manufacturer, it is essential to consider the company’s experience and reputation in the industry. Manufacturers with a long history of producing high-quality magnetic pulleys are more likely to provide reliable and efficient products. Checking customer reviews and testimonials can provide insights into the manufacturer’s reputation and the performance of their products.
Product Range and Customization
A good manufacturer should offer a wide range of magnetic pulleys to suit different applications. The ability to customize magnetic pulleys is also important, as it allows businesses to obtain solutions tailored to their specific needs. Consider manufacturers that provide customizable options and are willing to work closely with customers to develop the best solutions.
Quality Assurance and Standards
Quality assurance is crucial for ensuring that magnetic pulleys meet the required standards of performance and durability. Look for manufacturers that adhere to strict quality control processes and industry standards. Certifications and compliance with international standards can also indicate a manufacturer’s commitment to quality.
Technical Support and After-Sales Service
Technical support and after-sales service are important considerations when selecting a magnetic pulley manufacturer. Reliable manufacturers offer comprehensive support, including installation guidance, maintenance tips, and troubleshooting assistance. This support ensures that the magnetic pulleys operate efficiently and helps address any issues that may arise.
Innovation and Technology
Manufacturers that invest in innovation and technology are more likely to produce advanced and efficient magnetic pulleys. Consider manufacturers that use the latest technologies and continuously improve their products to meet evolving industry needs. Innovative solutions can provide better performance, increased efficiency, and longer product life.
Cost and Value
While cost is an important factor, it should not be the sole consideration when selecting a magnetic pulley manufacturer. It is essential to evaluate the overall value provided by the manufacturer, including the quality of the products, customization options, technical support, and after-sales service. Investing in high-quality magnetic pulleys from a reputable manufacturer can result in long-term cost savings and improved operational efficiency.
The Essential Role of Pulley Magnet Systems in Belt Conveyors
A pulley magnet is an integral component in belt conveyor systems, providing efficient and continuous metal separation. This article explores how magnetic pulleys are integrated into belt conveyors, the benefits of using magnetic pulleys for continuous metal separation, and their common applications in industries such as recycling, mining, and food processing.
Magnetic Pulley Belt Conveyor
Explanation of the Integration of Magnetic Pulleys in Belt Conveyors
Magnetic pulleys are seamlessly integrated into belt conveyor systems to enhance their functionality and efficiency. A magnetic pulley replaces the standard head pulley at the discharge end of the conveyor belt. This integration allows the pulley to perform dual functions: driving the conveyor belt and separating ferrous materials from the non-ferrous materials being transported.
Integration Process:
- Replacement: The existing head pulley is replaced with a magnetic pulley. This involves selecting a magnetic pulley of the appropriate size and magnetic strength for the specific conveyor system and the type of materials being processed.
- Alignment: Proper alignment of the magnetic pulley is crucial to ensure efficient operation. The pulley must be installed correctly to maintain the tension and tracking of the conveyor belt.
- Power Source: Magnetic pulleys are typically permanent magnets, which do not require an external power source. However, electromagnetic pulleys, which allow for adjustable magnetic strength, may be used depending on the application.
- Safety Measures: Safety measures, such as guards and warning signs, are implemented to protect operators and maintenance personnel from exposure to the magnetic field.
Once installed, the magnetic pulley continuously removes ferrous contaminants from the material stream. As the conveyor belt moves over the magnetic pulley, ferrous materials are attracted to the pulley’s surface and are carried out of the product stream. Non-ferrous materials continue to travel in their original path, ensuring a clean and contaminant-free output.
Benefits of Using Magnetic Pulleys for Continuous Metal Separation
The integration of magnetic pulleys into belt conveyor systems offers numerous advantages that enhance the overall efficiency, safety, and cost-effectiveness of industrial operations. Here are some key benefits:
Enhanced Material Purity:
- Effective Contaminant Removal: Magnetic pulleys efficiently remove ferrous contaminants from materials, ensuring high purity levels in the final product. This is crucial in industries where product integrity is vital, such as food processing and pharmaceuticals.
- Continuous Operation: The continuous operation of magnetic pulleys provides consistent and reliable removal of ferrous materials, reducing the risk of contamination in subsequent processing stages.
Protection of Equipment:
- Reduced Wear and Tear: By removing ferrous contaminants, magnetic pulleys help protect downstream equipment from damage and excessive wear. This extends the lifespan of machinery and reduces maintenance costs.
- Preventing Downtime: Protecting equipment from damage caused by ferrous materials minimizes unexpected breakdowns and operational downtime, ensuring smoother and more reliable production processes.
Increased Operational Efficiency:
- Automated Process: Magnetic pulleys operate continuously without the need for manual intervention, which improves the efficiency of material handling processes.
- Labor Cost Savings: Automated separation reduces labor costs associated with manual sorting and inspection, increasing overall productivity.
Versatility and Adaptability:
- Wide Range of Applications: Magnetic pulleys are versatile and can be used in various industries, including recycling, mining, food processing, and bulk material handling. Their adaptability makes them suitable for different types of conveyor systems and material handling requirements.
- Customizable Solutions: Magnetic pulleys can be customized to meet specific operational needs. This includes adjusting the magnetic strength, size, and design to suit different applications and material characteristics.
Environmental Benefits:
- Recycling and Waste Reduction: In recycling operations, magnetic pulleys play a critical role in separating ferrous metals from waste streams, facilitating the recycling process and reducing landfill waste.
- Resource Conservation: By effectively separating and recovering ferrous materials, magnetic pulleys contribute to the conservation of valuable resources and support sustainable manufacturing practices.
Common Applications in Industries Such as Recycling, Mining, and Food Processing
Magnetic pulleys are used in a wide range of industries, each with specific applications that benefit from the efficient separation of ferrous materials. Here are some common applications:
Recycling Industry:
- Scrap Metal Recovery: In recycling facilities, magnetic pulleys are used to recover ferrous metals from mixed waste streams. This process ensures that valuable metals are separated and recycled, improving the efficiency and profitability of recycling operations.
- E-Waste Processing: Magnetic pulleys help in the separation of ferrous components from electronic waste (e-waste), ensuring that metals are properly recovered and non-ferrous materials are processed further for recycling.
Mining Industry:
- Ore Processing: In mining operations, magnetic pulleys are used to remove tramp metal from ores and other raw materials. This protects crushers, grinders, and other processing equipment from damage caused by metal contaminants.
- Aggregate Handling: Magnetic pulleys are used in the handling of aggregates, such as sand, gravel, and crushed stone, to ensure that ferrous materials are removed before further processing or use in construction.
Food Processing Industry:
- Product Purity: In food processing plants, magnetic pulleys are crucial for ensuring the purity of food products. They remove ferrous contaminants from raw ingredients and finished products, protecting consumers and ensuring compliance with food safety standards.
- Packaging Lines: Magnetic pulleys are integrated into packaging lines to ensure that food products are free from metal contaminants before they are packaged and shipped to consumers.
Bulk Material Handling:
- Material Sorting: In bulk material handling operations, magnetic pulleys help in sorting and separating ferrous materials from non-ferrous materials. This is essential for industries that handle large volumes of materials, such as agriculture, construction, and logistics.
- Conveyor Belt Protection: By removing ferrous contaminants, magnetic pulleys protect conveyor belts from damage and reduce the frequency of maintenance and repairs.
Waste Management:
- Landfill Diversion: Magnetic pulleys are used in waste management facilities to divert ferrous materials from landfill waste streams, facilitating recycling and reducing the environmental impact of waste disposal.
- Resource Recovery: In waste-to-energy plants, magnetic pulleys help recover ferrous metals from waste streams before the remaining materials are processed for energy production, improving resource recovery and efficiency.
Automotive Industry:
- Shredding Operations: In automotive recycling facilities, magnetic pulleys are used in shredding operations to separate ferrous metals from shredded car bodies and other components. This ensures that metals are properly recovered and non-metallic materials are further processed.
- Parts Manufacturing: Magnetic pulleys are used in the manufacturing of automotive parts to remove metal contaminants from raw materials, ensuring the quality and integrity of the finished products.
FAQS about Pulley Magnet
What is a pulley on a conveyor?
Head Pulley: Located at the discharge end of the conveyor, it drives the belt and is typically connected to a motor.
Tail Pulley: Positioned at the opposite end of the conveyor, it guides the belt back towards the head pulley.
Snub Pulley: Increases the belt wrap angle around the drive pulley for better traction.
Take-Up Pulley: Maintains proper belt tension by adjusting its position.
Magnetic Pulley: Removes ferrous metal contaminants from the material flow.
Pulleys play a crucial role in ensuring the smooth and efficient operation of conveyor systems, supporting the belt and maintaining tension to transport materials effectively. Proper selection and maintenance of pulleys are vital for the longevity and reliability of the conveyor system.
What is a magnetic drum pulley?
Does a pulley use a magnet?
What is a magnetic pulley?
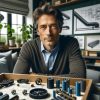
Jordan Smith, a seasoned professional with over 20 years of experience in the conveyor system industry. Jordan’s expertise lies in providing comprehensive solutions for conveyor rollers, belts, and accessories, catering to a wide range of industrial needs. From initial design and configuration to installation and meticulous troubleshooting, Jordan is adept at handling all aspects of conveyor system management. Whether you’re looking to upgrade your production line with efficient conveyor belts, require custom conveyor rollers for specific operations, or need expert advice on selecting the right conveyor accessories for your facility, Jordan is your reliable consultant. For any inquiries or assistance with conveyor system optimization, Jordan is available to share his wealth of knowledge and experience. Feel free to reach out at any time for professional guidance on all matters related to conveyor rollers, belts, and accessories.