Key Functions of Bend Pulley Conveyor in Industrial Use
In industrial settings, the efficiency and reliability of conveyor systems are paramount for smooth operations. Conveyor system components, such as the bend pulley conveyor, play a critical role in ensuring optimal performance and minimal downtime. The bend pulley conveyor is essential in guiding and redirecting the conveyor belt, which helps in maintaining the system’s overall functionality. This article will focus on the bend pulley conveyor and its crucial role within the system, alongside other important components like snub pulleys and take-up pulleys. Understanding these components’ functions and interactions is key to optimizing conveyor system performance and enhancing industrial efficiency.
Bend Pulley Conveyor Essentials
Definition and Core Application
A bend pulley is a critical component within a conveyor system, primarily used to change the direction of the conveyor belt. Its fundamental role involves altering the belt’s path to navigate various angles and routes essential for efficient material handling. The bend pulley is typically positioned at points in the conveyor system where the belt needs to be redirected, ensuring smooth transitions and maintaining continuous flow. By redirecting the belt, the bend pulley helps in optimizing the conveyor layout, allowing for more complex and space-efficient designs.
The bend pulley consists of a cylindrical drum, usually made of high-strength materials such as steel, designed to withstand the rigors of constant belt movement and load stress. It is mounted on bearings that enable it to rotate freely, ensuring minimal friction and wear on the belt. The surface of the bend pulley can be smooth or coated with materials like rubber to enhance grip and reduce slippage, depending on the specific requirements of the conveyor system.
Bend Pulley Function
The primary function of a bend pulley in a conveyor system is to change the direction of the conveyor belt, facilitating smooth and efficient material transport. By redirecting the belt at various angles, bend pulleys enable the conveyor system to navigate around obstacles, fit within constrained spaces, and achieve the desired routing for optimal material flow.
Bend pulleys are strategically placed in conveyor systems to accomplish different directional changes. Common applications include 180° loops, where the belt needs to reverse its direction entirely, and 90° turns, where the belt must navigate a right-angle turn. These directional changes are crucial for maximizing the use of available space and ensuring that the conveyor system can accommodate complex layouts required in industrial settings.
For instance, in a 180° loop, the bend pulley allows the belt to double back on itself, creating a compact and efficient loop that can save valuable floor space. This configuration is often used in applications where the conveyor needs to return to its starting point without requiring additional straight sections, thereby optimizing the overall system layout.
In the case of 90° turns, the bend pulley facilitates right-angle direction changes, enabling the conveyor belt to navigate around corners and obstacles seamlessly. This is particularly useful in environments with limited space or where the conveyor system needs to follow a specific path to connect different processing or handling areas.
Bend pulleys are also employed in combination with other types of pulleys, such as snub pulleys and take-up pulleys, to enhance the overall performance and efficiency of the conveyor system. Snub pulleys, for example, are used to increase the wrap angle of the belt around the drive pulley, providing additional grip and reducing the risk of slippage. This synergistic use of different pulleys ensures that the conveyor system operates smoothly, with minimal disruptions and maintenance requirements.
Bend Pulley Conveyor Parts
Purpose and Design
A snub pulley is an essential component in conveyor systems, designed to improve the belt’s efficiency by increasing its contact with the drive pulley. Unlike a bend pulley, which primarily serves to change the direction of the belt within the system, a snub pulley’s main purpose is to enhance the grip and control of the conveyor belt. This is achieved by increasing the wrap angle, the portion of the belt that comes into contact with the drive pulley, thereby improving traction and reducing the likelihood of slippage.
Snub pulleys are generally smaller in diameter compared to bend pulleys and are positioned close to the drive pulley. The strategic placement allows the snub pulley to redirect the belt slightly, increasing the wrap angle around the drive pulley without altering the overall direction of the conveyor belt. This increased wrap angle ensures that the belt maintains a better grip on the drive pulley, which is crucial for efficient power transmission and minimizing wear and tear on the belt and pulley surfaces.
The design of a snub pulley includes a robust cylindrical body, typically made of durable materials like steel or heavy-duty polymers, to withstand the mechanical stresses and environmental conditions of industrial settings. The surface of the snub pulley may also be coated with rubber or other friction-enhancing materials to further improve the grip between the belt and pulley, reducing the risk of slippage and ensuring smooth operation.
Function in Belt Conveyors
In the context of belt conveyors, the function of a snub pulley is vital for optimizing the system’s performance and efficiency. One of the primary roles of a snub pulley is to adjust and increase the wrap angle around the drive pulley, which directly impacts the belt’s ability to transmit force from the drive motor to the belt itself. By increasing the wrap angle, a snub pulley ensures that the belt has a greater surface area in contact with the drive pulley, enhancing friction and improving the transmission of power.
The increased wrap angle provided by a snub pulley is particularly important in high-tension conveyor systems where the belt is required to move heavy loads or operate over long distances. In such scenarios, the additional grip facilitated by the snub pulley helps in maintaining consistent belt movement, preventing slippage that can lead to inefficiencies, increased wear, and potential system downtime. The snub pulley essentially helps to balance the tension distribution across the belt, ensuring that the drive pulley can effectively pull the belt and the transported materials without excessive strain or slippage.
Moreover, the role of the snub pulley is crucial in maintaining the alignment and tracking of the conveyor belt. By strategically redirecting the belt and increasing the wrap angle, the snub pulley helps to keep the belt centered on the pulleys, reducing the risk of misalignment and ensuring that the belt runs smoothly along the intended path. This contributes to the overall longevity of the conveyor system, as proper alignment minimizes wear on the belt edges and pulleys, reducing the need for frequent maintenance and replacements.
In combination with other pulleys, such as the bend pulley conveyor, snub pulleys play a significant role in enhancing the overall efficiency and reliability of conveyor systems. While the bend pulley conveyor is primarily responsible for changing the direction of the belt, snub pulleys work alongside to ensure optimal grip and tension management, creating a synergistic effect that improves the system’s performance. The interplay between these pulleys allows for more complex and efficient conveyor designs, capable of handling diverse industrial applications with minimal downtime and maintenance requirements.
Snub pulleys are indispensable components in conveyor systems, designed to improve the grip and control of the conveyor belt by increasing the wrap angle around the drive pulley. Their function in enhancing traction, reducing slippage, and maintaining belt alignment is crucial for the efficient operation of belt conveyors, particularly in high-tension and heavy-duty applications. Understanding the distinct roles and designs of snub pulleys and bend pulley conveyors is essential for optimizing conveyor system performance and ensuring long-term reliability in industrial settings.
The Role of Take-up Pulleys in Bend Pulley Conveyor Systems
Take-up pulleys are crucial components in conveyor systems, including those utilizing bend pulley conveyor setups. Their primary function is to maintain the proper tension on the conveyor belt, which is vital for ensuring smooth operation, reducing wear, and preventing slippage. Proper belt tension is essential for the conveyor system’s efficiency and longevity, making take-up pulleys an indispensable part of the overall design.
Importance of Take-up Pulleys
A take-up pulley is designed to adjust the tension of the conveyor belt automatically or manually, compensating for changes in belt length due to stretching, load variations, and environmental conditions. By maintaining optimal tension, take-up pulleys help prevent issues such as belt sagging, misalignment, and slippage, ensuring the conveyor system operates smoothly and efficiently. Here are five examples of how take-up pulleys are essential in maintaining proper belt tension:
- Compensating for Belt Stretch: Over time, conveyor belts can stretch due to the constant load and movement. Take-up pulleys adjust the tension to accommodate this stretching, preventing the belt from becoming too loose and causing operational issues.
- Load Variation Adjustment: Conveyor systems often handle varying loads, which can affect belt tension. Take-up pulleys automatically adjust to these load changes, ensuring consistent tension and preventing slippage or belt damage.
- Thermal Expansion and Contraction: Changes in temperature can cause conveyor belts to expand or contract. Take-up pulleys compensate for these changes, maintaining proper tension and avoiding belt damage caused by excessive tension or sagging.
- Starting and Stopping Impact: The process of starting and stopping the conveyor system can cause sudden changes in belt tension. Take-up pulleys help absorb these shocks, preventing damage to the belt and other components.
- Belt Alignment Maintenance: Proper tension is crucial for keeping the conveyor belt aligned on the pulleys. Take-up pulleys ensure the belt remains centered, reducing the risk of misalignment and associated wear and tear.
Adjustable Positioning of Take-up Pulleys
The adjustable positioning of take-up pulleys significantly influences the functionality and efficiency of conveyor systems, including those with bend pulley conveyor configurations. Take-up pulleys can be manually adjusted or designed to self-adjust based on the system’s requirements. Here are some key aspects of adjustable positioning and its impact on conveyor systems:
- Manual Adjustment: In some conveyor systems, take-up pulleys are manually adjusted using threaded rods or screws. This allows operators to fine-tune the belt tension according to specific needs. Manual adjustment is often used in systems where precise control is required or where automatic adjustment is not feasible.
- Automatic Adjustment: Many modern conveyor systems use automatic take-up pulleys that adjust tension dynamically. These systems use counterweights, hydraulic cylinders, or spring-loaded mechanisms to maintain consistent tension without manual intervention. Automatic adjustment is ideal for systems with frequent load changes or in environments where manual adjustment is impractical.
- Horizontal and Vertical Positioning: Take-up pulleys can be positioned horizontally or vertically, depending on the conveyor system’s design and space constraints. Horizontal take-up pulleys are often used in systems with limited vertical space, while vertical take-up pulleys are suitable for applications where floor space is a concern.
- Impact on Belt Tracking: Properly adjusted take-up pulleys help maintain belt tracking, ensuring the belt runs smoothly on the pulleys and reducing the risk of misalignment. This is especially important in bend pulley conveyor systems, where directional changes can impact belt alignment.
- Ease of Maintenance: Adjustable take-up pulleys make maintenance easier by allowing for quick tension adjustments. This reduces downtime and ensures the conveyor system operates efficiently with minimal interruptions.
Integration with Bend Pulley Conveyor Systems
In conveyor bend pulley systems, the integration of take-up pulleys is crucial for maintaining optimal belt tension and ensuring smooth directional changes. The combination of bend pulleys and take-up pulleys creates a synergistic effect, enhancing the overall performance and reliability of the conveyor system. Proper tension management ensures that the belt maintains consistent contact with the bend pulleys, reducing wear and improving the system’s efficiency.
Take-up pulleys also play a vital role in extending the lifespan of the conveyor belt and other components. By maintaining proper tension, they minimize the stress on the belt and pulleys, reducing the likelihood of premature wear and failure. This not only improves the system’s reliability but also reduces maintenance costs and downtime.
Take-up pulleys are essential components in conveyor systems, including those utilizing bend pulley conveyor setups. Their role in maintaining proper belt tension, compensating for various operational factors, and enhancing overall system functionality is critical for efficient and reliable conveyor operation. Understanding the importance of take-up pulleys and their adjustable positioning is key to optimizing conveyor system performance and ensuring long-term operational success.
Why Pulley Quality Matters in Bend Pulley Conveyor Systems
In the context of industrial operations, the quality of conveyor parts, including the bend pulley conveyor, is paramount to ensure minimal downtime and improved longevity. High-quality pulleys are crucial for maintaining the efficiency, reliability, and safety of conveyor systems, which are integral to numerous industries such as mining, manufacturing, and logistics.
Importance of High-Quality Conveyor Parts
High-quality conveyor parts are essential for several reasons. Firstly, they ensure the system operates smoothly, reducing the likelihood of unexpected breakdowns that can lead to costly downtime. Downtime not only halts production but also incurs additional costs related to repairs, labor, and lost productivity. By investing in high-quality parts, companies can mitigate these risks and maintain continuous operations.
Secondly, high-quality parts enhance the longevity of the conveyor system. Components like bend pulley conveyors and snub pulleys are subjected to significant stress and wear due to constant motion and load-bearing activities. Using durable and robust materials in these components ensures they can withstand harsh conditions and prolonged use without deteriorating quickly. This longevity translates to fewer replacements and lower maintenance costs over time.
Furthermore, high-quality parts contribute to the overall safety of the conveyor system. Inferior components are more likely to fail, posing risks to workers and potentially leading to accidents. Reliable, high-quality pulleys reduce these risks, creating a safer working environment and ensuring compliance with safety regulations.
Custom Designs and Materials in Manufacturing Bend and Snub Pulleys
The manufacturing of bend pulleys and snub pulleys involves careful consideration of design and material selection to meet specific operational requirements. Custom designs and the use of high-grade materials are essential to ensure these pulleys perform optimally under various conditions.
Custom Designs
Custom-designed pulleys are tailored to meet the specific needs of the conveyor system they are a part of. This customization includes factors such as size, shape, and surface texture. For instance, the diameter of a bend pulley is determined based on the belt width and the required angle of direction change. A larger diameter might be used to reduce belt stress and increase the lifespan of the pulley and belt.
The surface texture of pulleys is another critical design element. For bend pulley conveyors, a smooth or rubber-coated surface might be used to enhance grip and reduce slippage, especially in systems that handle heavy loads or operate in environments with varying conditions such as moisture or dust.
Custom designs also address specific challenges such as space constraints, load distribution, and environmental factors. By tailoring pulleys to these unique requirements, manufacturers can optimize the performance and reliability of the conveyor system.
Materials Used
The choice of materials in manufacturing bend and snub pulleys significantly impacts their durability and performance. High-quality materials such as stainless steel, cast iron, and specialized polymers are commonly used in pulley construction.
- Stainless Steel: Known for its strength and corrosion resistance, stainless steel is ideal for environments where exposure to moisture, chemicals, or extreme temperatures is common. Stainless steel pulleys provide excellent durability and longevity, making them suitable for heavy-duty applications.
- Cast Iron: Cast iron is another durable material that offers high strength and wear resistance. It is often used in applications where the pulley must withstand significant mechanical stress and impact.
- Specialized Polymers: In some cases, high-performance polymers are used for pulleys, especially where weight reduction and corrosion resistance are critical. These materials provide a balance of strength, flexibility, and resistance to environmental factors.
Manufacturing Processes
Advanced manufacturing processes also play a role in the quality of pulleys. Precision machining, heat treatment, and surface finishing techniques are employed to enhance the mechanical properties and longevity of the pulleys. Heat treatment, for example, improves the hardness and strength of the metal, making it more resistant to wear and deformation.
Surface finishing processes such as galvanization or coating with anti-corrosive materials further protect the pulleys from environmental damage, extending their service life and maintaining their performance under challenging conditions.
The quality of pulleys, including bend pulley conveyors and snub pulleys, is critical to the efficient and safe operation of conveyor systems. High-quality parts reduce downtime, enhance longevity, and improve safety, providing significant benefits to industrial operations. Custom designs and the use of superior materials ensure these pulleys meet specific operational needs and withstand the rigors of industrial use. By prioritizing quality in conveyor components, companies can achieve more reliable, cost-effective, and safe material handling solutions.
Additional Considerations for Bend Pulley Conveyor Systems
When designing and maintaining a bend pulley conveyor system, several additional considerations can enhance performance, ensure safety, and optimize efficiency. These considerations include the use of pulley accessories such as guards and lagging, as well as guidelines for selecting the right pulley for specific conveyor system needs.
Pulley Accessories for Enhanced Performance
Pulley Guards
Pulley guards are essential accessories designed to improve safety and protect both the conveyor system and its operators. These guards cover the exposed parts of the pulley, preventing accidental contact with moving components. This not only reduces the risk of injury but also protects the pulley and belt from debris and contaminants that can cause wear and damage.
- Safety Enhancement: By preventing direct contact with moving pulleys, guards minimize the risk of workplace accidents, ensuring a safer environment for workers.
- Protection from Debris: Guards help keep the pulley and belt free from dust, dirt, and other contaminants that can lead to premature wear and reduce the efficiency of the conveyor system.
- Compliance with Regulations: Using pulley guards helps meet safety regulations and standards, ensuring the conveyor system operates within legal and safety guidelines.
Lagging
Lagging refers to the application of a coating or covering on the surface of the pulley to enhance its performance. This coating is typically made from materials such as rubber or ceramic, providing additional grip and reducing slippage between the pulley and the belt.
- Increased Traction: Rubber lagging increases the friction between the pulley and the belt, reducing slippage and improving the efficiency of power transmission.
- Wear Resistance: Ceramic lagging offers excellent resistance to abrasion and wear, extending the lifespan of the pulley and reducing maintenance costs.
- Reduced Belt Tension: By improving grip, lagging allows for lower belt tension, reducing stress on the belt and other conveyor components, which enhances the overall system longevity.
Selecting the Right Pulley for Specific Needs
Choosing the right pulley for a bend pulley conveyor system involves considering several factors to ensure optimal performance and longevity. Here are five key examples:
- Material Compatibility
Selecting a pulley made from materials compatible with the operating environment and the type of material being transported is crucial. For example, stainless steel pulleys are ideal for environments with high moisture or corrosive substances, while cast iron pulleys are suited for high-stress applications.
- Load Capacity
The pulley must be capable of handling the maximum load expected in the conveyor system. Overloading a pulley can lead to premature failure and potential system downtime. Ensuring the pulley’s load capacity matches or exceeds the operational requirements is vital for reliable performance.
- Size and Diameter
The size and diameter of the pulley should be chosen based on the belt width and the required wrap angle. Larger pulleys reduce belt stress and extend the belt’s lifespan, while smaller pulleys might be necessary for systems with space constraints. It’s essential to balance these factors to achieve the best performance.
- Surface Texture
The surface texture of the pulley affects its grip and interaction with the conveyor belt. Smooth surfaces are suitable for light-duty applications with minimal slippage risk, while textured or lagged surfaces provide better grip for heavy-duty applications. Selecting the appropriate surface texture ensures efficient power transmission and reduces wear.
- Environmental Conditions
Considering the operating environment is critical when selecting a pulley. For instance, in dusty or abrasive environments, pulleys with protective coatings or lagging can reduce wear and extend their lifespan. In high-temperature environments, pulleys made from heat-resistant materials ensure continuous operation without degradation.
The efficiency and reliability of a bend pulley conveyor system can be significantly enhanced by considering additional accessories and selecting the right pulleys for specific needs. Pulley guards and lagging are vital accessories that improve safety, increase traction, and protect the system from wear. When selecting pulleys, it is important to consider material compatibility, load capacity, size and diameter, surface texture, and environmental conditions. By addressing these factors, companies can optimize their conveyor systems for better performance, reduced downtime, and extended component life. Understanding and implementing these additional considerations ensures that conveyor bend pulley systems operate smoothly and efficiently in diverse industrial applications.
FAQs About Bend Pulley Conveyor
A bend pulley on a conveyor is a crucial component designed to change the direction of the conveyor belt. Positioned at various points within the conveyor system, bend pulleys help guide the belt through complex layouts and around obstacles, ensuring smooth and continuous operation. The primary function of a bend pulley is to redirect the belt, allowing the conveyor to navigate sharp turns and optimize the use of available space. Made from high-strength materials like steel or heavy-duty polymers, bend pulleys are built to withstand significant stress and wear, contributing to the overall durability and efficiency of the conveyor system. By maintaining proper belt alignment and tension, bend pulleys play an essential role in preventing slippage, minimizing wear, and ensuring the conveyor system operates efficiently.
The primary difference between a snub pulley and a bend pulley lies in their design and purpose within a conveyor system. A bend pulley is primarily used to change the direction of the conveyor belt, allowing it to navigate complex layouts and fit within constrained spaces. In contrast, a snub pulley is designed to increase the wrap angle of the conveyor belt around the drive pulley, enhancing grip and reducing the risk of slippage. While both types of pulleys contribute to the overall efficiency of the conveyor system, their specific functions are distinct. Bend pulleys are used to redirect the belt path, whereas snub pulleys are positioned close to the drive pulley to improve traction and power transmission. The surface of snub pulleys is often coated with rubber or other friction-enhancing materials to maximize grip, while bend pulleys may have a smooth or similarly coated surface depending on the application requirements.
The minimum bend radius of a conveyor belt is the smallest radius at which the belt can be bent without causing damage or compromising its structural integrity. This radius depends on several factors, including the belt’s construction, material, and thickness. Generally, the minimum bend radius is specified by the belt manufacturer and can vary widely depending on the type of belt used. For instance, fabric-reinforced belts typically have a larger minimum bend radius compared to steel-cord belts due to their flexibility and material properties. Adhering to the recommended minimum bend radius is crucial to prevent issues such as belt cracking, delamination, or excessive wear, which can lead to premature failure and costly downtime. Understanding and respecting the minimum bend radius ensures that the conveyor belt maintains its performance and longevity, even when navigating sharp turns and complex layouts within the conveyor system.
The purpose of a snub pulley in a conveyor system is to increase the wrap angle of the conveyor belt around the drive pulley, thereby enhancing the belt’s grip and reducing slippage. Positioned close to the drive pulley, the snub pulley redirects the belt slightly to increase the contact area between the belt and the drive pulley. This increased wrap angle improves traction and ensures efficient power transmission from the drive motor to the belt. By enhancing grip, the snub pulley helps maintain consistent belt movement, especially in high-tension systems where the belt is required to move heavy loads or operate over long distances. Additionally, the snub pulley plays a role in maintaining belt alignment and tracking, ensuring the belt runs smoothly and remains centered on the pulleys. This function is vital for reducing wear, preventing misalignment, and ensuring the overall efficiency and reliability of the conveyor system.
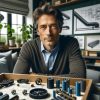
Jordan Smith, a seasoned professional with over 20 years of experience in the conveyor system industry. Jordan’s expertise lies in providing comprehensive solutions for conveyor rollers, belts, and accessories, catering to a wide range of industrial needs. From initial design and configuration to installation and meticulous troubleshooting, Jordan is adept at handling all aspects of conveyor system management. Whether you’re looking to upgrade your production line with efficient conveyor belts, require custom conveyor rollers for specific operations, or need expert advice on selecting the right conveyor accessories for your facility, Jordan is your reliable consultant. For any inquiries or assistance with conveyor system optimization, Jordan is available to share his wealth of knowledge and experience. Feel free to reach out at any time for professional guidance on all matters related to conveyor rollers, belts, and accessories.