Reliable Pulley Conveyors for Diverse Industrial Needs
Conveyor systems are essential in various industries, including manufacturing, mining, and logistics, for efficient material handling. These systems streamline operations, reduce labor costs, and enhance productivity by automating the movement of goods. Within these systems, the pulley conveyor plays a pivotal role. Pulley conveyors are integral components that drive and guide the conveyor belt, ensuring smooth and continuous movement of materials. They consist of various types of pulleys, such as drive pulleys and idler pulleys, each serving a specific function. Understanding the significance and functionality of pulley conveyors is crucial for optimizing conveyor system performance and achieving operational efficiency in diverse industrial applications.
What are Pulley Conveyor Parts
Definition and Function
Pulley conveyors are a vital component of conveyor systems, playing an essential role in the movement and direction of materials. In a conveyor system, pulley conveyors function as the driving force, controlling the conveyor belt’s motion and ensuring the smooth and efficient transport of goods. Conveyor pulleys are responsible for driving the belt and require at least two to function, categorized as drive or head, and return or tail pulleys. The primary function of pulley conveyors is to provide the necessary tension and support to the conveyor belt, enabling it to move materials over various distances and through different processes within an industrial setting.
Key Components of Pulley Conveyors
Pulley conveyors consist of several key components, each serving a specific purpose within the conveyor system. Understanding these components and their roles is crucial for optimizing the performance and efficiency of the conveyor system. The main types of pulleys used in pulley conveyors include drive pulleys, tail pulleys, and idler pulleys.
Pulley Type | Location | Function | Surface Treatment |
---|---|---|---|
Drive Pulley | Discharge end | Drives the conveyor belt forward | Rubber coating for grip |
Tail Pulley | Receiving end | Maintains tension and alignment of the conveyor belt | Surface covering for grip |
Idler Pulley | Between drive and tail pulleys | Supports the conveyor belt along its return path | Various types (flat, troughing, impact) |
How Pulley Conveyors Function Within a Conveyor System
Pulley conveyors function by utilizing the mechanical advantage of rotating pulleys to move the conveyor belt and the materials it carries. The drive pulley, connected to a motor, provides the initial force required to move the belt. As the drive pulley rotates, it pulls the belt along with it, creating a continuous loop of movement. The tail pulley ensures the belt remains taut and properly aligned, while the idler pulleys provide additional support and prevent sagging.
The interaction between these components is critical for the efficient operation of the conveyor system. Proper tension and alignment are essential to prevent belt slippage, reduce wear and tear on the components, and ensure smooth and consistent material flow. Regular maintenance and inspection of the pulleys are necessary to identify and address any issues that may arise, such as misalignment, wear, or damage.
Importance of Understanding Pulley Conveyor Parts
A thorough understanding of pulley conveyor parts is essential for optimizing the performance and efficiency of conveyor systems. By knowing the roles and functions of each pulley type, operators can ensure that the conveyor system operates smoothly and efficiently. This knowledge also helps in identifying and troubleshooting potential issues, allowing for timely maintenance and repairs to prevent costly downtime and disruptions.
Pulley conveyors are a critical component of conveyor systems, providing the necessary force and support to move materials efficiently. Understanding the various pulley types and their functions is key to maintaining a well-functioning conveyor system and achieving optimal operational efficiency.
Types of Pulleys Used in Pulley Conveyors
Drive Pulley Conveyor Belt (Head Pulley)
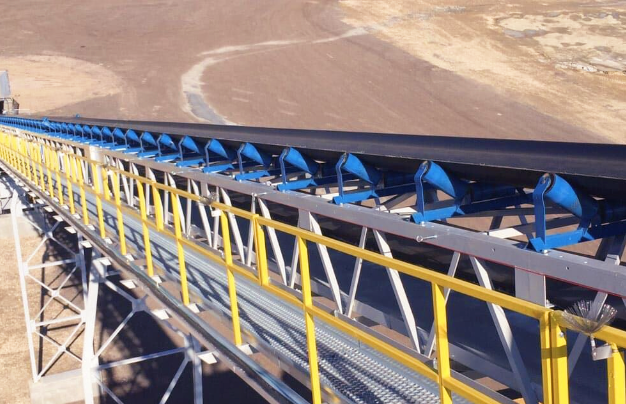
The drive pulley, also known as the head pulley, is a crucial component in the pulley conveyor system. It is located at the discharge end of the conveyor and is responsible for driving the conveyor belt forward. The drive pulley is connected to a motor that provides the necessary torque to rotate the pulley, thus moving the belt. This pulley plays a pivotal role in the overall functioning of the conveyor system as it generates the force needed to transport materials along the conveyor belt.
The material and surface treatment of the drive pulley are essential to its performance. The surface of the drive pulley is often coated with a material such as rubber, known as lagging, to enhance grip and reduce wear. Lagging increases the friction between the pulley and the conveyor belt, preventing slippage and ensuring efficient operation. Additionally, lagging helps to extend the lifespan of both the pulley and the belt by reducing abrasion and wear.
Conveyor Head and Tail Pulley
The head pulley and tail pulley serve distinct functions within a pulley conveyor system. The head pulley, as previously mentioned, drives the conveyor belt forward. The tail pulley, on the other hand, is located at the receiving end of the conveyor system. Its primary function is to provide a return path for the conveyor belt and to help maintain the proper tension and alignment.
Differences and Functions:
- Head Pulley: Located at the discharge end, drives the conveyor belt, connected to a motor.
- Tail Pulley: Located at the receiving end, returns the conveyor belt, maintains tension and alignment.
Importance in Tension Regulation and Direction Change:
Both head and tail pulleys are essential for tension regulation and direction change in the conveyor belt system. Proper tension is critical to prevent belt slippage, reduce wear and tear, and ensure smooth operation. The tail pulley is often adjustable, allowing operators to make precise tension adjustments to maintain optimal belt performance.
Examples:
- Steel Head Pulley with Rubber Lagging: Used in heavy-duty applications for enhanced grip.
- Aluminum Tail Pulley: Lightweight and corrosion-resistant, ideal for food processing.
- Wing Tail Pulley: Designed for self-cleaning, reducing material build-up.
- Ceramic Lagged Head Pulley: Provides superior grip and wear resistance.
- Stainless Steel Tail Pulley: Suitable for environments requiring high hygiene standards.
Conveyor Drum Pulley
Drum pulleys are another vital type of pulley used in pulley conveyor systems. These pulleys are typically cylindrical and can be used as drive, tail, or idler pulleys depending on the application. Drum pulleys are designed to provide stable and efficient belt support, and they come in various sizes and configurations to suit different needs.
Common Features and Applications:
Drum pulleys are characterized by their cylindrical shape and robust construction. They are commonly used in applications that require heavy-duty performance and can withstand high loads and harsh operating conditions. Drum pulleys are also available in different variations, such as wing pulleys, which are designed for self-cleaning and reducing material build-up.
Importance in Heavy-Duty Applications:
Drum pulleys are essential in heavy-duty applications where durability and reliability are crucial. The robust construction of drum pulleys allows them to handle high loads and provide consistent performance over long periods. Variations like wing pulleys are particularly beneficial in environments where material build-up can be an issue, as they help to keep the conveyor belt clean and reduce maintenance requirements.
Examples:
- Heavy-Duty Steel Drum Pulley: Used in mining and aggregate applications for high load capacity.
- Rubber Coated Drum Pulley: Enhances grip and reduces wear, suitable for industrial applications.
- Wing Drum Pulley: Self-cleaning design for environments with material build-up.
- Stainless Steel Drum Pulley: Corrosion-resistant, ideal for food and pharmaceutical industries.
- Custom Engineered Drum Pulley: Designed for specific applications, offering tailored performance.
Pulley Type | Location | Function | Surface Treatment | Examples |
---|---|---|---|---|
Drive Pulley (Head) | Discharge end | Drives the conveyor belt forward | Rubber lagging for grip | Steel Head Pulley with Rubber Lagging |
Tail Pulley | Receiving end | Returns the conveyor belt, maintains tension and alignment | Adjustable for tension control | Aluminum Tail Pulley, Wing Tail Pulley |
Drum Pulley | Various positions | Provides stable belt support, handles heavy-duty applications | Various, including self-cleaning wings | Heavy-Duty Steel Drum Pulley, Wing Drum Pulley |
Understanding the different types of pulleys used in pulley conveyors is essential for selecting the right components for specific applications. Drive pulleys, tail pulleys, and drum pulleys each have unique roles and features that contribute to the efficient operation of conveyor systems. By choosing the appropriate pulley types and configurations, operators can ensure optimal performance, reduce maintenance requirements, and extend the lifespan of their conveyor systems.
Discussing Pulley Conveyor Sizes and Specifications
Standard Sizes and Customizations
When it comes to pulley conveyors, the size of the pulleys plays a crucial role in the system’s overall functionality and efficiency. Standard pulley sizes are typically defined by their diameter and width, with common ranges varying depending on the application and industry requirements.
Typical Pulley Size Ranges:
- Diameter: Pulley diameters can range from as small as 50 millimeters (2 inches) to over 1 meter (40 inches). Smaller pulleys are generally used in light-duty applications, while larger pulleys are necessary for heavy-duty industrial processes.
- Width: The width of a pulley is determined by the width of the conveyor belt it supports. Standard widths can range from 300 millimeters (12 inches) to over 2 meters (80 inches), accommodating various belt sizes.
Impact on Conveyor Functionality:
The size of the pulley directly impacts the conveyor system’s performance. Larger pulleys can handle heavier loads and higher speeds, making them ideal for demanding applications. They also provide better belt traction and reduce the risk of slippage. Conversely, smaller pulleys are more suitable for lighter loads and slower speeds, offering greater flexibility in compact spaces.
Selecting the Right Pulley Size:
Choosing the correct pulley size involves considering several factors:
- Load Capacity: The weight and volume of the materials being transported dictate the size of the pulley. Heavier loads require larger pulleys to ensure adequate support and minimize wear.
- Speed: Conveyor speed is another critical factor. High-speed applications benefit from larger pulleys, which can maintain stability and reduce the risk of conveyor belt damage.
- Conveyor Length: The length of the conveyor system affects tension and alignment. Longer conveyors may require larger pulleys to maintain proper tension and prevent belt sagging.
Material and Design Innovations
The materials and design of pulley conveyors have evolved significantly, leading to enhanced efficiency, durability, and performance. Various materials are used in the construction of pulleys, each offering distinct advantages.
Materials Used:
- Steel: Steel is a common material for pulleys due to its strength and durability. It can withstand high loads and harsh operating conditions, making it ideal for heavy-duty applications. Steel pulleys are often coated with protective layers to resist corrosion and wear.
- Rubber Coatings: Rubber lagging on steel pulleys improves grip and reduces belt slippage. The rubber surface provides better traction, minimizes wear on the belt, and extends the pulley’s lifespan.
- Ceramics: Ceramic lagging is used in applications where extreme wear resistance is required. Ceramic-coated pulleys offer superior durability and are suitable for abrasive environments.
- Aluminum: Lightweight and corrosion-resistant, aluminum pulleys are used in industries where hygiene and cleanliness are paramount, such as food processing and pharmaceuticals.
Design Innovations:
Modern pulley designs incorporate several innovations to enhance conveyor efficiency and durability:
- Wing Pulleys: Wing pulleys feature a unique design with vanes or fins that allow debris to fall through the pulley rather than accumulating on the belt. This self-cleaning feature reduces maintenance and improves conveyor belt life.
- Crowned Pulleys: These pulleys have a slightly tapered design, with the center diameter larger than the edges. The crown helps to center the belt on the pulley, improving tracking and reducing the risk of misalignment.
- Spiral Drum Pulleys: Spiral drum pulleys have a helical groove pattern that helps to shed water, mud, and other contaminants, preventing build-up and maintaining belt traction.
- Custom Engineered Pulleys: Customization allows pulleys to be tailored to specific applications, considering factors like load, speed, and environmental conditions. Custom pulleys can be designed with specific materials, coatings, and dimensions to optimize performance.
Benefits of Material and Design Innovations
The advancements in materials and design have led to several benefits for pulley conveyor systems:
- Increased Efficiency: Improved materials and innovative designs reduce friction, enhance grip, and ensure smoother operation, resulting in higher conveyor efficiency.
- Extended Lifespan: Durable materials like steel and ceramics, combined with protective coatings, extend the lifespan of pulleys, reducing the need for frequent replacements.
- Reduced Maintenance: Features like self-cleaning wing pulleys and crowned designs minimize maintenance requirements, saving time and costs associated with conveyor upkeep.
- Enhanced Performance: Custom-engineered pulleys tailored to specific applications ensure optimal performance, whether in high-speed, heavy-load, or corrosive environments.
The sizes and specifications of conveyor pulleys in pulley conveyor systems are vital to their overall performance and efficiency. Standard sizes and customizations allow for tailored solutions that meet specific application requirements. Material choices and design innovations further enhance the durability, efficiency, and lifespan of pulley conveyors, making them indispensable components in various industrial processes. By selecting the right pulley sizes and leveraging advanced materials and designs, operators can achieve optimal conveyor performance and reliability.
Major Pulley Conveyor Manufacturers
Leading Brands in the Pulley Conveyor Market
The pulley conveyor industry is dominated by several well-known manufacturers who have established themselves as leaders through their commitment to quality, innovation, and customer service. Among these, Gram Conveyor, PROK, and Heinrich Brothers stand out as prominent names.
Gram Conveyor
Gram Conveyor is a leading name in the pulley conveyor industry, known for its cutting-edge solutions and exceptional engineering. The company specializes in custom-designed conveyor pulleys that address unique industry challenges. Their product range includes high-speed rollers, low-noise rollers, and energy-efficient models, making them suitable for various applications such as automotive, logistics, and pharmaceuticals.
What sets Gram Conveyor apart is their dedication to innovation and customer satisfaction. They invest heavily in research and development to introduce new technologies and improve existing products. Their focus on quality and reliability ensures that their pulleys meet the highest standards of performance and durability. Moreover, Gram Conveyor’s customer-centric approach means they work closely with clients to develop tailored solutions that optimize operational efficiency.
PROK
PROK is a global leader in the manufacture of conveyor pulley components, with a reputation for producing high-quality products that meet the demanding needs of various industries. The company has a rich history of innovation and excellence, dating back to its founding. PROK’s products are known for their durability, reliability, and superior performance, making them a preferred choice for many industrial applications.
What sets PROK apart is its focus on continuous improvement and technological advancement. The company invests heavily in research and development to stay at the forefront of the industry, introducing new materials, designs, and manufacturing techniques that enhance the efficiency and longevity of their pulley conveyors. PROK also places a strong emphasis on customer satisfaction, offering comprehensive support and services to ensure their products meet the specific needs of each client.
Heinrich Brothers
Heinrich Brothers is another leading name in the pulley conveyor industry, known for its high-quality products and exceptional customer service. With decades of experience, Heinrich Brothers has built a solid reputation for delivering reliable and efficient conveyor solutions. The company offers a wide range of conveyor belt pulleys designed to cater to various industrial requirements.
Heinrich Brothers distinguishes itself through its commitment to customization and customer-centric approach. The company works closely with clients to understand their unique needs and develop tailored solutions that optimize their conveyor systems’ performance. This personalized service, combined with the company’s expertise and innovative products, has made Heinrich Brothers a trusted partner for many businesses.
In summary, these leading brands—Gram Conveyor, PROK, and Heinrich Brothers—have set high standards in the pulley conveyor market through their dedication to quality, innovation, and customer satisfaction. Their products are engineered to meet the diverse needs of various industries, ensuring reliable and efficient material handling solutions.
Custom Solutions and Services
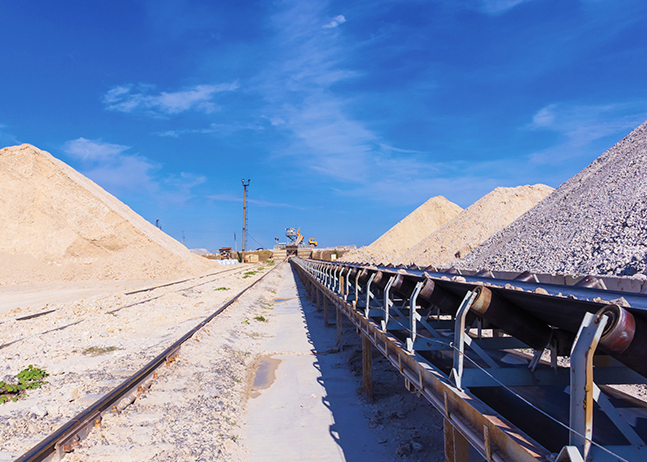
Major pulley conveyor manufacturers like Gram Conveyor, PROK and Heinrich Brothers offer a range of custom solutions and services to meet the diverse needs of their clients. These services include custom engineering, design consultations, and ongoing support to ensure the optimal performance of pulley conveyor systems.
Custom Engineering:
Custom engineering is a critical service offered by leading manufacturers, allowing them to design pulley conveyors that meet specific application requirements. This process involves a detailed analysis of the client’s operational needs, including load capacities, environmental conditions, and other factors that impact the conveyor system’s performance. By leveraging their technical expertise and advanced manufacturing capabilities, companies like Gram Conveyor, PROK and Heinrich Brothers can create custom pulley conveyors that deliver superior efficiency and reliability.
Design Consultations:
Design consultations are another valuable service provided by major pulley conveyor manufacturers. These consultations involve working closely with clients to assess their current conveyor systems and identify areas for improvement. Manufacturers can recommend the best pulley designs, materials, and configurations to enhance the system’s performance and extend its lifespan. This collaborative approach ensures that the final product is tailored to the client’s specific needs and operational goals.
Ongoing Support:
Ongoing support is essential for maintaining the performance and reliability of conveyor pulleys systems. Leading manufacturers offer comprehensive support services, including installation assistance, maintenance, and troubleshooting. This support helps clients address any issues that may arise and ensures that their conveyor systems continue to operate at peak efficiency. Companies like Gram Conveyor, PROK and Heinrich Brothers provide extensive training and resources to help clients properly maintain and manage their pulley conveyors, reducing downtime and extending the equipment’s lifespan.
Case Study: Customized Pulley Solutions
A case study highlighting the benefits of custom solutions and services involves a mining operation that required a specialized conveyor pulleys system to handle high-capacity loads and abrasive materials. The client approached PROK for a solution that could withstand the harsh operating conditions and deliver reliable performance.
PROK’s engineering team conducted a thorough assessment of the mining operation’s requirements and designed a custom pulley conveyor system with reinforced steel pulleys and ceramic lagging to enhance durability and grip. The system also included custom-designed idler pulleys to support the heavy loads and maintain proper alignment.
The result was a highly efficient and durable pulley conveyor system that significantly improved the mining operation’s productivity and reduced maintenance costs. This case study demonstrates the value of working with leading manufacturers to develop customized solutions that meet specific industrial needs.
Major pulley conveyor manufacturers like Gram Conveyor, PROK and Heinrich Brothers play a crucial role in the industry by providing high-quality products, innovative solutions, and exceptional customer service. Their ability to offer custom engineering, design consultations, and ongoing support ensures that clients receive tailored conveyor systems that enhance their operational efficiency and reliability. By partnering with these leading brands, businesses can achieve optimal performance and longevity for their pulley conveyor systems.
Pulley Conveyors for Sale
When it comes to purchasing pulley conveyors, it’s essential to make informed decisions to ensure you get the best value and performance for your investment. Here’s a detailed guide to help you navigate the process:
Where to Buy
Tips on Finding Reliable Suppliers
- Research and Reviews: Start by researching potential suppliers online. Look for customer reviews and testimonials to gauge the reliability and quality of their products. Websites like ThomasNet, Alibaba, and industry-specific forums can be valuable resources.
- Industry Reputation: Choose suppliers with a solid reputation in the industry. Companies with long-standing histories and a track record of delivering high-quality products are often more reliable.
- Certifications and Standards: Verify that the suppliers comply with industry standards and certifications. This ensures that the pulley conveyors meet safety and quality benchmarks.
- Customer Support: Good customer support is crucial. Look for suppliers who offer comprehensive support services, including installation, maintenance, and troubleshooting.
- Product Range: Select suppliers that offer a wide range of pulley conveyors. This allows you to find the exact specifications and customization options you need for your application.
Considerations for Purchasing New vs. Used Pulley Conveyors
- New Pulley Conveyors:
- Pros: New pulley conveyors come with the latest technology, full warranties, and customer support. They are built to current standards, ensuring optimal performance and safety.
- Cons: The initial cost is higher compared to used options. However, this can be offset by lower maintenance costs and longer lifespan.
- Used Pulley Conveyors:
- Pros: Used pulley conveyors are more affordable and can be a good option for short-term projects or tight budgets. They can often be found in good condition with significant cost savings.
- Cons: Used conveyors may have wear and tear, limited warranties, and outdated technology. There is also a higher risk of mechanical issues, leading to increased maintenance costs.
Factors to Consider
Quality and Durability
- Materials and Construction: Check the materials used in the construction of the pulleys. High-quality steel and robust manufacturing processes ensure durability and longevity, especially in demanding environments like mining and quarries.
- Load Capacity: Ensure the pulleys are designed to handle the load requirements of your application. Heavy-duty pulleys are necessary for high-capacity operations.
Manufacturer Support and Warranties
- Warranty Terms: Understand the warranty terms provided by the manufacturer. A comprehensive warranty can protect against manufacturing defects and ensure long-term reliability.
- After-Sales Support: Evaluate the level of after-sales support offered. This includes availability of spare parts, maintenance services, and technical assistance. Strong support can minimize downtime and keep your operations running smoothly.
Customization Options
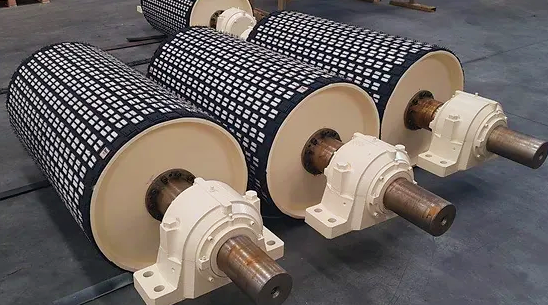
- Tailored Solutions: Look for suppliers that offer customization options to tailor the pulley conveyors to your specific needs. Customizations might include size, material, surface treatments, and additional features like integrated sensors or special coatings.
- Design Flexibility: Ensure the supplier is flexible in design modifications. This is especially important if you have unique operational requirements or space constraints that standard pulleys cannot accommodate.
By considering these factors and conducting thorough research, you can confidently purchase pulley conveyors that meet your operational needs and provide reliable performance. Whether opting for new or used conveyors, the key is to prioritize quality, support, and customization to achieve the best results for your investment.
FAQs About Pulley Conveyor
A pulley on a conveyor is a mechanical component used to drive and support the conveyor belt. Pulleys play a critical role in the overall function of conveyor systems, ensuring the smooth and efficient movement of materials. They work by providing the necessary tension and support to the conveyor belt, allowing it to transport goods over various distances. Pulleys are typically made of robust materials like steel and can be coated with rubber or other materials to enhance grip and reduce wear. By rotating, these pulleys move the belt forward, thereby enabling the continuous flow of materials in industrial applications.
Conveyor pulleys come in various types, each serving a specific function within the conveyor system. The main types of conveyor pulleys include:
Drive Pulley (Head Pulley): This pulley is located at the discharge end and drives the conveyor belt forward.
Tail Pulley: Positioned at the receiving end, this pulley returns the conveyor belt and helps maintain proper tension and alignment.
Idler Pulley: Also known as return pulleys, these support the conveyor belt along its return path and help prevent sagging or misalignment.
Snub Pulley: This pulley increases the angle of contact between the belt and the drive pulley, improving traction and belt control.
Bend Pulley: Used to change the direction of the belt, often found in longer conveyor systems to help manage belt tension. Understanding these different pulleys and their roles is essential for maintaining an efficient conveyor system.
The head pulley, also known as the drive pulley, is crucial in a conveyor system. Located at the discharge end of the conveyor, its primary purpose is to drive the conveyor belt forward. It achieves this by being connected to a motor that provides the necessary torque to rotate the pulley, thus moving the belt and the materials it carries. The head pulley is often coated with rubber or another high-friction material, known as lagging, to enhance grip and prevent slippage. This ensures efficient and reliable operation, making the head pulley an integral component for the overall performance and functionality of the conveyor system.
The head pulley and tail pulley serve distinct but complementary roles within a conveyor system. The head pulley, located at the discharge end, is responsible for driving the conveyor belt forward. It is connected to a motor that provides the necessary power to rotate the pulley, thereby moving the belt and the materials on it. The surface of the head pulley is often treated with rubber lagging to enhance grip and prevent belt slippage.
In contrast, the tail pulley is situated at the receiving end of the conveyor system. Its primary function is to provide a return path for the conveyor belt and help maintain proper tension and alignment. The tail pulley ensures that the belt remains taut and runs smoothly, preventing sagging and misalignment. Unlike the head pulley, the tail pulley is usually not driven by a motor but is often adjustable to allow for tension control. By working together, the head and tail pulleys ensure efficient and consistent operation of the conveyor system.
Conveyor pulleys can be categorized into several types based on their functions and placement within the conveyor system. The primary types include:
Drive Pulley (Head Pulley): This is the main pulley that drives the conveyor belt. It is usually located at the discharge end of the conveyor and is powered to move the belt.
Return Pulley (Tail Pulley): Positioned at the opposite end of the drive pulley, the return or tail pulley redirects the belt back towards the drive pulley. It maintains tension and alignment of the belt.
Snub Pulley: Positioned close to the drive pulley, the snub pulley increases the belt’s wrap angle around the drive pulley, enhancing traction and reducing slippage.
Bend Pulley: Used to change the direction of the belt, bend pulleys can be placed along the conveyor to redirect the belt’s path. They are not typically powered.
Take-Up Pulley: This type of pulley is used in conjunction with a take-up system to maintain proper tension in the belt. It can be found at the end or middle of the conveyor system.
Wing Pulley: Designed for handling bulk materials, wing pulleys are typically used in environments where debris needs to be expelled from the conveyor belt to prevent build-up and damage.
Each type of pulley plays a crucial role in ensuring the efficient operation of the conveyor system, contributing to the movement, tension, and alignment of the conveyor belt.
An idler pulley conveyor is a type of conveyor system that uses idler pulleys to support the conveyor belt and maintain its alignment. Unlike drive pulleys, idler pulleys are not powered; their primary function is to provide support and guide the belt along its path. Idler pulleys are strategically placed throughout the conveyor system to ensure smooth and efficient belt operation.
Key characteristics and functions of idler pulleys in a conveyor system include:
Support: Idler pulleys provide continuous support to the conveyor belt, preventing sagging and ensuring that the belt remains flat and properly aligned.
Guidance: They help guide the belt along the conveyor’s path, maintaining the correct trajectory and preventing misalignment or derailment.
Tension Maintenance: Idler pulleys assist in maintaining the appropriate tension in the conveyor belt, ensuring optimal performance and reducing wear and tear.
Load Distribution: By distributing the weight of the transported materials evenly across the belt, idler pulleys help prevent excessive stress on specific sections of the conveyor, prolonging its lifespan.
Idler pulleys come in various shapes and sizes, including flat, troughing, and impact idlers, each designed to perform specific functions within the conveyor system. Their versatile nature makes them essential components in many conveyor applications, ranging from bulk material handling to unit packaging.
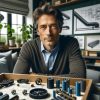
Jordan Smith, a seasoned professional with over 20 years of experience in the conveyor system industry. Jordan’s expertise lies in providing comprehensive solutions for conveyor rollers, belts, and accessories, catering to a wide range of industrial needs. From initial design and configuration to installation and meticulous troubleshooting, Jordan is adept at handling all aspects of conveyor system management. Whether you’re looking to upgrade your production line with efficient conveyor belts, require custom conveyor rollers for specific operations, or need expert advice on selecting the right conveyor accessories for your facility, Jordan is your reliable consultant. For any inquiries or assistance with conveyor system optimization, Jordan is available to share his wealth of knowledge and experience. Feel free to reach out at any time for professional guidance on all matters related to conveyor rollers, belts, and accessories.