Comprehensive Guide to Conveyor Belt Pulley Design
Conveyor belt pulleys are crucial components in bulk material handling systems, enabling the efficient movement of materials over long distances. The design of these pulleys involves a high degree of complexity and technical precision, as they must withstand significant operational demands and environmental conditions. Properly designed pulleys ensure the reliability and longevity of conveyor systems, minimizing downtime and maintenance costs. This blog post aims to provide a foundational understanding of conveyor belt pulley design, covering essential principles, key considerations, and advanced techniques. By the end of this belt conveyor design guide, readers will gain valuable insights into the intricacies of designing conveyor belt pulleys, enhancing their knowledge and application in real-world scenarios.
What is Conveyor Belt Pulley Design
Basics of Conveyor Belt Pulleys
Definition and Function of a Conveyor Belt Pulley
A conveyor belt pulley is a mechanical device used to change the direction of the belt in a conveyor system, to drive the belt, and to tension the belt. The pulley is usually mounted on shafts, which are then fixed to the conveyor structure, and can either drive the belt or simply guide it along its path.
The Role of Pulleys in Conveyor Belt Systems
- Driving the Belt: Drive pulleys transmit power from the motor to the conveyor belt, moving the belt forward.
- Changing Belt Direction: Tail pulleys redirect the belt back towards the drive pulley after the material has been unloaded.
- Tensioning the Belt: Snub pulleys increase the angle of contact between the belt and drive pulley for better traction.
- Supporting the Belt: Take-up pulleys maintain the tension in the belt, ensuring smooth operation.
- Adjusting Belt Alignment: Bend pulleys help guide the belt and can be used to correct alignment issues.
Types of Conveyor Belt Pulleys
- Drive Pulley: The primary pulley that drives the conveyor belt, usually connected to the motor.
- Tail Pulley: Located at the end of the conveyor belt, it redirects the belt back towards the drive pulley.
- Snub Pulley: Positioned close to the drive pulley, it increases the belt’s wrap angle around the drive pulley for better grip.
- Take-Up Pulley: Used to maintain proper tension on the belt by adjusting its position.
- Bend Pulley: Changes the direction of the belt and can be used to manage belt tension and alignment.
Key Considerations in conveyor belt pulley design
Overview of Factors Influencing the Design of Conveyor Belt Pulleys
When designing conveyor belt pulleys, several critical factors must be considered to ensure optimal performance and longevity. These include:
Material Handling Requirements: The type and characteristics of the materials being transported significantly influence conveyor belt pulley design. Factors such as material weight, size, and abrasiveness need to be considered to select appropriate materials and design specifications for the pulley.
Environmental Considerations: The operational environment plays a crucial role in pulley design. For instance, pulleys operating in harsh environments, such as those with high humidity, extreme temperatures, or exposure to corrosive substances, require materials and coatings that can withstand these conditions.
Operational Demands: The conveyor belt pulley design must accommodate the specific demands of the conveyor system, including the speed of operation, load capacity, and frequency of use. High-load or high-speed applications require robust designs to prevent premature wear and failure.
Bridging Theory with Practice: conveyor belt pulley design Complexity
Discussion on the Complexity of Design Questions
Designing conveyor belt pulleys involves a high level of complexity that often cannot be fully addressed through general discussions or basic guidelines found in forums. Each pulley design must be tailored to the specific requirements of the conveyor system and the operational environment. Questions related to load calculations, stress analysis, and material selection require detailed analysis and precise calculations.
The Necessity for Advanced Resources
To accurately design conveyor belt pulleys, engineers often rely on advanced resources, including academic papers and technical manuals, which provide in-depth theoretical knowledge and practical insights. Some essential resources include:
- “Belt Conveyors for Bulk Materials” by the Conveyor Equipment Manufacturers Association (CEMA): A comprehensive guide covering various aspects of conveyor design, including pulley design.
- “Conveyor Belt Manual” by Fenner Dunlop: Detailed information on conveyor belts and components, including pulleys.
- “The Transfer Chute Design Manual” by C.W. Roberts: Focuses on material handling and the design of components like pulleys.
- Technical papers from the International Journal of Mechanical Sciences: Provide research findings and advanced theories on mechanical design aspects relevant to pulleys.
- Finite Element Analysis (FEA) software manuals: Guides on using FEA tools for detailed stress and strain analysis in conveyor belt pulley design.
By bridging theoretical knowledge with practical application, designers can create efficient, durable, and reliable conveyor belt pulleys that meet the specific needs of their systems.
Technical Aspects of Conveyor Belt Pulley Design
Pulley Diameter and Shaft Design
Calculations Involved in Determining Appropriate Pulley Diameter and Shaft Size
Determining the correct pulley diameter and shaft size is a critical aspect of conveyor belt pulley design. The pulley diameter affects the belt’s bending stress and the life of the belt. A larger diameter reduces the bending stress, increasing the belt’s lifespan. The shaft size must be adequate to handle the forces exerted by the pulley and the belt, ensuring stability and longevity of the system.
Importance of Proper Dimensioning for Performance and Longevity
- Load Capacity: A properly dimensioned pulley can handle the expected load without excessive wear or risk of failure. For example, in heavy-duty mining applications, a larger pulley diameter can distribute the load more effectively, reducing wear on the belt.
- Operational Speed: The pulley diameter must match the operational speed requirements. In high-speed applications, a smaller diameter might suffice, but this can increase belt stress. Conversely, slower applications benefit from larger diameters to minimize wear.
- Material Handling Efficiency: Correctly sized pulleys ensure efficient material handling by maintaining consistent belt tension and alignment, essential in industries like food processing where precision is critical.
- Environmental Conditions: In harsh environments, pulleys with larger diameters and robust shafts resist deformation and wear, such as in chemical processing plants where corrosive substances are present.
- Maintenance and Downtime: Properly designed pulleys reduce maintenance needs and downtime. For instance, in automated warehouses, well-dimensioned pulleys ensure uninterrupted operation, maximizing productivity.
Disc and Rim Thickness Calculation
Approach to Determining Rim Thickness Based on Factors Like Average Belt Pull and Bending Moment
Calculating the disc and rim thickness is essential to ensure the structural integrity of the pulley. The rim thickness must withstand the forces exerted by the belt pull and bending moments during operation.
- Average Belt Pull: This is the continuous force exerted by the belt. Rim thickness must accommodate this force to prevent deformation.
- Bending Moment: This occurs due to the load and tension on the belt. The rim must be thick enough to resist bending under these conditions.
- Material Strength: The material used for the rim must be considered, as different materials have varying strength properties. For example, steel rims require different thickness calculations compared to aluminum.
- Safety Factors: Including a safety margin in the thickness calculation ensures durability and reliability under unexpected load conditions.
- Manufacturing Tolerances: Real-world manufacturing variances necessitate a slightly higher thickness to account for potential discrepancies.
Advanced Design Techniques
Utilization of Computational Formulae and Modern Computing for Pulley Design
Advanced design techniques leverage computational formulae and modern computing power to optimize conveyor belt pulley design. These methods include:
- Stress and Strain Equations: Using these equations helps predict how the pulley material will behave under various loads, ensuring it can withstand operational stresses.
- Force/Moment Equilibrium Analysis: This involves calculating the forces and moments acting on the pulley to ensure it remains in equilibrium, preventing mechanical failure.
- Dynamic Simulations: Simulating the pulley’s performance under real-world conditions helps identify potential issues before manufacturing.
- Optimization Algorithms: These algorithms can refine pulley dimensions and materials for optimal performance and cost-effectiveness.
- CAD Software: Computer-Aided Design (CAD) tools enable precise modeling of pulley components within conveyor belt CAD systems, allowing for detailed analysis and adjustments.
Implementing Modern Methods: FEA and Other Techniques
Discussion on Finite Element Analysis (FEA) for Addressing Design Challenges
Finite Element Analysis (FEA) is a powerful tool in conveyor belt pulley design, allowing engineers to simulate and analyze the behavior of pulleys under various conditions. FEA helps identify stress concentrations, potential failure points, and areas requiring reinforcement.
- Stress Distribution: FEA provides detailed insights into how stress is distributed across the pulley, enabling optimization for even stress distribution.
- Material Deformation: Analyzing how materials deform under load helps in selecting appropriate materials and thicknesses.
- Thermal Effects: FEA can simulate thermal stresses that pulleys might experience in high-temperature environments, ensuring they can withstand these conditions.
- Fatigue Analysis: Predicting the fatigue life of the pulley helps in designing for long-term durability.
- Design Iterations: FEA allows for rapid iterations and adjustments, speeding up the design process and improving accuracy.
Reference to Classical Methods and Modern Techniques in Pulley Design
Classical methods in pulley design include empirical formulas and hand calculations, which provide a foundational understanding. However, modern techniques enhance these methods by incorporating advanced simulations and computational tools, leading to more precise and reliable designs.
- Empirical Formulas: These are used as initial approximations and are refined using modern techniques.
- Hand Calculations: These provide a quick check of initial design concepts before detailed analysis.
- Computational Fluid Dynamics (CFD): This can be used to analyze airflow and cooling around pulleys in high-temperature applications.
- Vibration Analysis: Ensures the pulley design minimizes vibrations that could lead to noise and mechanical wear.
- Material Science Advances: New materials and coatings are continually developed, improving pulley performance and durability.
By integrating both classical and modern methods, engineers can create robust, efficient, and durable conveyor belt pulley designs that meet the demands of contemporary industrial applications.
Practical Applications and Examples of Conveyor Belt Pulley Design
Conveyor belt pulley design is pivotal in various industries, ensuring the efficiency and reliability of conveyor systems. This section presents detailed case studies and hypothetical scenarios where conveyor belt pulley design principles are applied, demonstrating their practical significance.
Case Study 1: Mining Industry
In the mining industry, conveyor systems are essential for transporting extracted minerals from the mines to processing plants. A mining company faced frequent pulley failures due to the harsh operating conditions, including heavy loads, abrasive materials, and extreme environmental factors.
Application of Design Principles:
- Material Handling Requirements: The pulleys were designed with larger diameters to reduce belt stress and wear, accommodating the heavy loads of ore.
- Environmental Considerations: Stainless steel was selected for the pulley material to resist corrosion from moisture and chemical exposure.
- Operational Demands: The pulleys were equipped with reinforced shafts and bearings to handle the continuous operation and high load capacity.
Outcome: The redesigned pulleys significantly reduced downtime and maintenance costs, improving the overall efficiency and reliability of the conveyor system.
Case Study 2: Food Processing Industry
A food processing plant needed a conveyor system to transport delicate food products without damage. The challenge was to design pulleys that maintained gentle handling while ensuring hygienic standards.
Application of Design Principles:
- Material Handling Requirements: The pulleys were designed with smooth surfaces and larger diameters to minimize belt tension and prevent product damage.
- Environmental Considerations: Food-grade stainless steel was used to meet hygiene standards and withstand frequent cleaning.
- Operational Demands: The pulleys were designed for easy disassembly and cleaning to ensure compliance with food safety regulations.
Outcome: The new pulley design facilitated gentle product handling, maintained hygiene standards, and reduced product waste.
Case Study 3: Packaging Industry
A packaging facility required a high-speed conveyor system for moving packaged goods. The existing system experienced frequent misalignment and slippage issues, causing operational inefficiencies.
Application of Design Principles:
- Material Handling Requirements: The pulleys were designed with a high coefficient of friction surface to improve belt traction and prevent slippage.
- Environmental Considerations: The design included sealed bearings to protect against dust and debris from the packaging process.
- Operational Demands: The pulleys were engineered to support high-speed operation without compromising alignment.
Outcome: The improved conveyor belt pulley design eliminated slippage and misalignment issues, resulting in smoother and more efficient conveyor operation.
Case Study 4: Chemical Processing Industry
A chemical processing plant needed a conveyor system to transport corrosive materials. The pulleys in the existing system deteriorated quickly due to chemical exposure, leading to frequent replacements and downtime.
Application of Design Principles:
- Material Handling Requirements: The pulleys were designed with coatings resistant to the specific chemicals used in the process.
- Environmental Considerations: Materials like Teflon-coated steel were chosen to withstand the corrosive environment.
- Operational Demands: The design included robust seals to prevent chemical ingress into the pulley bearings.
Outcome: The chemically resistant pulleys extended the lifespan of the conveyor system and reduced maintenance frequency, enhancing overall productivity.
Case Study 5: Airport Baggage Handling
An airport needed a reliable conveyor system for baggage handling. Frequent system failures caused delays and customer dissatisfaction.
Application of Design Principles:
- Material Handling Requirements: The pulleys were designed to handle varying baggage weights and sizes smoothly.
- Environmental Considerations: The pulleys were designed to withstand frequent start-stop cycles and high usage rates.
- Operational Demands: High-strength materials and robust construction were used to ensure durability and reduce the risk of failure.
Outcome: The robust conveyor belt pulley design minimized system failures and improved the overall efficiency and reliability of the baggage handling process.
By applying these detailed principles of conveyor belt pulley design in real-world scenarios, industries can achieve significant improvements in efficiency, reliability, and cost-effectiveness. These examples demonstrate the importance of considering material handling requirements, environmental conditions, and operational demands in the design process.
FAQs About Conveyor Belt Pulley Design
Designing a conveyor pulley involves several critical steps to ensure it meets the operational and environmental requirements. First, determine the application’s load capacity and the belt’s speed. Select appropriate materials for the pulley, considering factors such as the weight and abrasiveness of the material being transported. Next, calculate the necessary pulley diameter and shaft size, ensuring they can handle the expected loads and operational stresses. Consider the type of bearings and mounting methods that will be used. Additionally, the rim thickness must be calculated based on factors like average belt pull and bending moments. Use computational tools and simulations to validate the design, ensuring it can withstand operational stresses and environmental conditions. Finally, incorporate safety factors to accommodate unexpected loads or operational variations, ensuring the pulley’s durability and reliability.
The formula for calculating the belt pull on a conveyor is essential for determining the necessary power and strength requirements of the system. The basic formula is:
Belt Pull (F)=T1−T2 where T1 is the tight side tension and T2 is the slack side tension. To find these tensions, additional calculations are needed based on the conveyor’s parameters. For example, T1 can be calculated using: T1=P/V+T2 where P is the power requirement of the conveyor (in watts), and V is the belt speed (in meters per second). T2 is often derived from the friction and load on the conveyor system. It’s also crucial to consider other factors like the weight of the belt, the material being transported, and the length of the conveyor when calculating these tensions.
Conveyor systems use various types of pulleys to achieve different functions. The primary types include:
Drive Pulley: This pulley is connected to the motor and provides the driving force to move the conveyor belt. It’s usually located at the discharge end of the conveyor.
Tail Pulley: Positioned at the opposite end of the drive pulley, the tail pulley helps return the belt to the drive pulley after the material has been unloaded.
Snub Pulley: Located near the drive pulley, this pulley increases the belt’s wrap angle around the drive pulley, improving traction and power transmission.
Take-Up Pulley: Used to maintain proper tension in the conveyor belt, take-up pulleys can adjust to ensure the belt runs smoothly and consistently.
Bend Pulley: Used to change the direction of the belt, bend pulleys are typically found in complex conveyor layouts where the belt needs to navigate around corners or obstacles.
Each type of pulley serves a specific role in ensuring the conveyor system operates efficiently and reliably.
Calculating the speed of a conveyor pulley involves understanding the relationship between the motor speed, the pulley diameter, and the belt speed. The basic formula to determine the belt speed is: Belt Speed (V)=(π×D×RPM )/60 where V is the belt speed (in meters per second), D is the pulley diameter (in meters), and RPM is the rotational speed of the pulley (in revolutions per minute). This formula assumes there is no slippage between the belt and the pulley. If slippage occurs, the actual belt speed will be slightly less than calculated. It’s also important to consider factors like the load on the conveyor, the type of material being transported, and the operational environment, as these can influence the effective speed of the system.
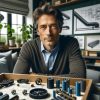
Jordan Smith, a seasoned professional with over 20 years of experience in the conveyor system industry. Jordan’s expertise lies in providing comprehensive solutions for conveyor rollers, belts, and accessories, catering to a wide range of industrial needs. From initial design and configuration to installation and meticulous troubleshooting, Jordan is adept at handling all aspects of conveyor system management. Whether you’re looking to upgrade your production line with efficient conveyor belts, require custom conveyor rollers for specific operations, or need expert advice on selecting the right conveyor accessories for your facility, Jordan is your reliable consultant. For any inquiries or assistance with conveyor system optimization, Jordan is available to share his wealth of knowledge and experience. Feel free to reach out at any time for professional guidance on all matters related to conveyor rollers, belts, and accessories.