Types and Functions of Pulley Conveyor Systems
Pulley conveyor systems are a crucial component in material handling and industrial processes. A pulley conveyor system consists of a series of pulleys that drive and guide a continuous loop of material, typically a belt. This system facilitates the efficient movement of materials from one point to another, enhancing productivity and reducing manual labor. The importance of pulley conveyor systems lies in their ability to handle a wide range of materials, from heavy loads to delicate items, ensuring smooth and reliable transportation. Their versatility and efficiency make pulley conveyor systems indispensable in various industries, including manufacturing, mining, and logistics.
Working Principle of Pulley Conveyor Systems
Pulley conveyor systems are designed to facilitate the efficient movement and guidance of conveyor belts through a network of pulleys. The primary function of these systems is to transport materials smoothly from one location to another, leveraging the mechanical advantages of pulleys. This section provides a detailed explanation of how pulleys operate within a conveyor system, the roles of various types of pulleys, and illustrative examples of pulley conveyor system operations.
How Pulleys Move and Guide Conveyor Belts
In a pulley conveyor system, the conveyor belt is looped around a series of pulleys that rotate to move the belt and the materials on it. The pulleys act as the driving force, guiding the belt along a predetermined path. The movement of the conveyor belt is primarily driven by the rotation of the pulleys, which are powered by an external motor. The motor drives the primary pulley, which in turn moves the conveyor belt, causing it to carry materials along the conveyor’s path.
The pulleys are strategically positioned to ensure that the belt remains taut and follows a specific route. These pulleys are usually made of durable materials such as steel or aluminum, designed to withstand the stresses and strains of continuous operation.
Roles of Different Types of Pulleys
In a pulley conveyor system, there are three main types of pulleys: drive pulleys, idler pulleys, and tensioning pulleys. Each type of pulley plays a crucial role in the operation and efficiency of the system.
Drive Pulleys
The drive pulley is the most critical component in a pulley conveyor system. It is connected to the motor and provides the necessary force to move the conveyor belt. The drive pulley is typically located at the end of the conveyor system and is responsible for pulling the belt. To ensure maximum efficiency, the drive pulley is often coated with a high-friction material that increases grip, preventing the belt from slipping.
Idler Pulleys
Idler pulleys are used to support the conveyor belt and guide it along its path. Unlike drive pulleys, idler pulleys are not powered and do not contribute to the movement of the belt. Instead, they help to maintain the belt’s alignment and tension, ensuring smooth operation. Idler pulleys are strategically placed along the conveyor system to support the belt at regular intervals, reducing sagging and preventing the belt from deviating from its intended path.
Tensioning Pulleys
Tensioning pulleys are essential for maintaining the correct tension in the conveyor belt. Proper tension is crucial for the efficient operation of the pulley conveyor system, as it prevents the belt from slipping off the pulleys and ensures consistent material movement. Tensioning pulleys can be adjusted to increase or decrease the tension in the belt, accommodating changes in load or environmental conditions. These pulleys are often spring-loaded or equipped with adjustable screws, allowing for precise control of belt tension.
Illustrative Examples of Pulley Conveyor System Operations
To better understand the working principle of pulley conveyor systems, let’s consider a few illustrative examples:
- Manufacturing Assembly Lines: In manufacturing, pulley conveyor systems are used to move products along assembly lines. Drive pulleys power the conveyor belts, while idler pulleys support and guide the belts. Tensioning pulleys ensure that the belts remain taut, allowing for the smooth and efficient transportation of parts and components between different workstations.
- Mining Operations: In the mining industry, pulley conveyor systems are used to transport raw materials such as coal, ores, and minerals. The drive pulleys, connected to powerful motors, provide the necessary force to move heavy loads. Idler pulleys support the belts along extended distances, and tensioning pulleys maintain the correct belt tension, ensuring that the materials are transported efficiently and safely.
- Logistics and Warehousing: Pulley conveyor systems are widely used in logistics and warehousing for the transportation of packages and goods. Drive pulleys enable the movement of conveyor belts through loading and unloading areas, while idler pulleys maintain the alignment and tension of the belts. Tensioning pulleys ensure that the belts can handle varying loads, preventing slippage and maintaining consistent material flow.
The working principle of pulley conveyor systems revolves around the coordinated use of drive pulleys, idler pulleys, and tensioning pulleys to move and guide conveyor belts. These systems are essential for efficient material handling in various industries, providing reliable and smooth transportation of goods and materials.
Manufacturers of Pulley Conveyor Systems
Leading Manufacturers Specializing in Pulley Conveyor Systems
When it comes to selecting a manufacturer for pulley conveyor systems, it’s essential to consider the reputation, product range, and customer reviews of leading companies in the field. Below, we provide an overview of three top manufacturers specializing in pulley conveyor systems: Dodge, Martin Sprocket & Gear, and Baldor.
- Dodge: A division of ABB, Dodge is renowned for its high-quality pulley conveyor systems. The company offers a wide array of pulleys designed to meet various industrial needs, from standard conveyor applications to customized solutions for specific requirements.
- Martin Sprocket & Gear: With a legacy dating back to 1951, Martin Sprocket & Gear has established itself as a leader in the pulley conveyor system market. The company provides a comprehensive range of pulleys, including drum pulleys, wing pulleys, and engineered class pulleys, catering to numerous industries.
- Baldor: Another prominent player in the industry, Baldor (also a part of ABB), is known for its innovative pulley conveyor systems. Baldor’s offerings include a variety of pulley types, each engineered for durability and efficiency, ensuring reliable performance in demanding applications.
Key Features, Customization Options, and Industry Expertise
Each of these manufacturers excels in providing high-quality pulley conveyor systems, distinguished by their unique features, customization options, and extensive industry expertise.
Key Features
- Durability: All three manufacturers prioritize durability, ensuring their pulley conveyor systems can withstand harsh industrial environments and heavy usage.
- Efficiency: The pulley systems are designed to enhance the overall efficiency of conveyor operations, reducing downtime and maintenance requirements.
- Versatility: The pulleys are suitable for a wide range of applications, from mining and aggregate to food processing and packaging industries.
- Customization: Each manufacturer offers customization options to meet specific application needs, including various sizes, materials, and configurations.
- Safety: Safety features are integrated into the design to protect both the equipment and the operators, ensuring compliance with industry standards.
- Innovative Design: Continuous innovation is a hallmark of these manufacturers, with new designs and technologies regularly introduced to improve performance and reliability.
Customization Options
- Material Selection: Customers can choose from various materials, such as steel, aluminum, and composite, based on the specific requirements of their application.
- Size and Configuration: Pulleys are available in different diameters, widths, and configurations, allowing for precise matching to conveyor system specifications.
- Surface Treatments: Options such as lagging, coating, and other surface treatments are offered to enhance traction and wear resistance.
- Engineering Support: Manufacturers provide engineering support to help design and implement customized pulley solutions tailored to unique operational needs.
Industry Expertise
- Mining and Aggregate: Dodge, Martin Sprocket & Gear, and Baldor have extensive experience in the mining and aggregate industries, providing robust pulley systems designed to handle heavy loads and abrasive materials.
- Food Processing: These manufacturers also cater to the food processing industry, offering pulleys that meet stringent hygiene and safety standards.
- Manufacturing and Packaging: The manufacturing and packaging sectors benefit from the reliability and efficiency of these pulley conveyor systems, which are essential for maintaining high productivity levels.
Comparison of Different Manufacturers Based on Reputation, Product Range, and Customer Reviews
Manufacturer | Reputation | Product Range | Customer Reviews |
---|---|---|---|
Dodge | Highly reputable, part of ABB | Wide array of pulleys, including custom solutions | Positive, known for durability and support |
Martin Sprocket & Gear | Long-standing industry leader | Comprehensive range, from drum to wing pulleys | Excellent, praised for customization and quality |
Baldor | Innovator, also part of ABB | Variety of pulley types, engineered for efficiency | Very good, appreciated for innovative designs and reliability |
Choosing the right manufacturer for a pulley conveyor system involves considering factors such as reputation, product range, and customer feedback. Dodge, Martin Sprocket & Gear, and Baldor are all excellent choices, each offering unique strengths in terms of durability, efficiency, and customization options. By understanding the key features and industry expertise of these manufacturers, customers can make informed decisions to optimize their conveyor system operations.
Types of Conveyor Belt Pulleys
Conveyor belt pulleys play a crucial role in the functioning of a pulley conveyor system, facilitating the movement and guidance of the conveyor belt. There are several types of pulleys used in these systems, each with its unique design and function. Understanding the different types of conveyor belt pulleys can help in selecting the right pulley for specific conveyor system requirements.
Drive Pulleys
Description: Drive pulleys are responsible for driving the conveyor belt and are usually located at the discharge end of the conveyor. They are often larger in diameter to provide enough surface area for the belt to grip.
Benefits and Applications: Drive pulleys are essential for providing the necessary power to move the conveyor belt. They are commonly used in industries such as mining, agriculture, and manufacturing, where heavy loads need to be transported over long distances.
Idler Pulleys
Description: Idler pulleys are located along the conveyor belt path and provide support and guidance to the belt. They are often smaller in size compared to drive pulleys and are used in conjunction with drive pulleys to support the belt and maintain proper tension.
Benefits and Applications: Idler pulleys help in reducing the stress on the conveyor belt and prevent it from sagging. They are widely used in industries where smooth and efficient material handling is required, such as food processing and automotive manufacturing.
Wing Pulleys
Description: Wing pulleys have an extended area on either side of the pulley, resembling wings. These wings help in guiding the belt and preventing it from running off the pulley.
Benefits and Applications: Wing pulleys are effective in applications where the conveyor belt tends to move from side to side. They are commonly used in industries such as aggregate and mining, where belt tracking is crucial.
Table Display: Types of Conveyor Belt Pulleys
Type | Description | Benefits and Applications |
---|---|---|
Drive Pulleys | Responsible for driving the conveyor belt | Provide power to move the belt; used in mining, agriculture, manufacturing |
Idler Pulleys | Provide support and guidance to the belt | Reduce stress on the belt; used in food processing, automotive manufacturing |
Wing Pulleys | Have extended wings to guide the belt | Prevent belt from running off; used in aggregate, mining |
Considerations for Selecting the Right Pulleys
When selecting pulleys for a conveyor system, several factors need to be considered to ensure optimal performance and efficiency:
- Size and Diameter: The size and diameter of the pulley should be compatible with the conveyor belt size and load requirements.
- Material: Pulleys should be made from durable materials that can withstand the operating conditions of the conveyor system.
- Pulley Face Width: The face width of the pulley should match the width of the conveyor belt to ensure proper belt tracking.
- Shaft Design: The shaft design should be sturdy enough to handle the load and provide smooth rotation of the pulley.
- Pulley Lagging: Pulley lagging can improve the grip between the pulley and the belt, reducing slippage and increasing efficiency.
By considering these factors and understanding the different types of conveyor belt pulleys available, it becomes easier to select the right pulleys for specific conveyor system requirements, ensuring smooth and efficient operation.
Conveyor Head and Tail Pulleys: Pulley Conveyor System
In a pulley conveyor system, head and tail pulleys play pivotal roles in ensuring efficient and smooth operation. Understanding the importance, functions, and common designs of these pulleys is crucial for maintaining a well-functioning conveyor system. This section delves into the significance of head and tail pulleys, their functions in driving, tensioning, and tracking the belt, and the common designs and materials used in their construction.
Importance of Head and Tail Pulleys in Conveyor Systems
Head and tail pulleys are essential components in a pulley conveyor system. They ensure the smooth movement of the conveyor belt, contributing to the overall efficiency of the material handling process. Head pulleys, located at the discharge end of the conveyor, are responsible for driving the belt and ensuring continuous material flow. Tail pulleys, positioned at the feed end, play a critical role in maintaining proper belt tension and tracking. Together, these pulleys form the backbone of the conveyor system, ensuring that materials are transported smoothly and efficiently from one point to another.
Functions of Head Pulleys in Driving the Belt and Tail Pulleys in Tensioning and Tracking
Head Pulleys
- Driving the Belt: The primary function of the head pulley is to drive the conveyor belt. It is connected to a motor that provides the necessary power to move the belt. The head pulley is often lagged with rubber or other high-friction materials to enhance grip and prevent slippage. This ensures that the belt moves consistently and efficiently.
- Ensuring Smooth Material Discharge: Positioned at the discharge end, the head pulley is crucial for the smooth release of materials from the conveyor belt. Its rotation ensures that materials are effectively discharged into the next phase of the process, whether that be another conveyor, a hopper, or a processing machine.
- Maintaining Belt Alignment: By driving the belt, the head pulley also helps maintain its alignment. Proper alignment is essential to prevent belt drift and ensure that materials are transported accurately along the designated path.
Tail Pulleys
- Tensioning the Belt: The tail pulley is responsible for maintaining proper belt tension. Adequate tension is crucial for the efficient operation of the pulley conveyor system, as it prevents the belt from sagging or slipping off the pulleys. Tail pulleys are often equipped with tensioning mechanisms that allow for easy adjustment to maintain optimal tension.
- Tracking the Belt: In addition to tensioning, the tail pulley plays a vital role in tracking the belt. Proper belt tracking ensures that the belt stays centered on the pulleys, preventing misalignment and potential damage. Tail pulleys are designed to facilitate minor adjustments to the belt’s path, ensuring smooth and accurate tracking.
- Supporting Belt Return: Located at the feed end, the tail pulley supports the return side of the conveyor belt. This ensures that the belt is properly aligned and tensioned as it re-enters the conveying section, contributing to the overall stability and efficiency of the system.
Common Designs and Materials Used for Head and Tail Pulleys
Head Pulleys
- Lagged Head Pulleys: To enhance grip and prevent slippage, head pulleys are often lagged with materials such as rubber, ceramic, or urethane. Lagging increases friction between the pulley and the belt, ensuring efficient power transmission.
- Crowned Head Pulleys: These pulleys have a slightly convex surface, which helps in maintaining belt alignment. The crowned shape encourages the belt to center itself, reducing the risk of misalignment.
- Drum Head Pulleys: Drum pulleys are cylindrical and are the most common design for head pulleys. They provide a consistent surface for the belt to wrap around, ensuring smooth operation.
Tail Pulleys
- Flat Tail Pulleys: Flat tail pulleys provide a stable surface for the belt, ensuring proper tension and tracking. They are commonly used in various conveyor systems for their simplicity and effectiveness.
- Wing Tail Pulleys: Wing pulleys have a unique design with wings or fins that extend from the center to the edges. This design helps to shed material buildup, making them ideal for applications where debris accumulation is a concern.
- Tapered Tail Pulleys: These pulleys have a tapered shape that helps in centering the belt and improving tracking. Tapered tail pulleys are particularly useful in applications where precise belt alignment is crucial.
- Rubber-Coated Tail Pulleys: Similar to lagged head pulleys, some tail pulleys are coated with rubber to increase friction and improve belt tracking and tensioning.
- Adjustable Tail Pulleys: Equipped with tensioning mechanisms, adjustable tail pulleys allow for easy modifications to the belt tension and tracking, ensuring optimal performance in varying conditions.
- Split Tail Pulleys: Split pulleys are designed for easy installation and maintenance, allowing them to be mounted or dismounted without disturbing the belt or other components.
Head and tail pulleys are integral components of a pulley conveyor system, playing crucial roles in driving, tensioning, and tracking the conveyor belt. Understanding their functions, designs, and materials can help in selecting the right pulleys for specific conveyor system requirements, ensuring efficient and reliable material handling operations.
Pulley Conveyor System
Wheel conveyor systems are a critical component in the world of material handling, often working in tandem with pulley conveyor systems to enhance overall efficiency. These systems use a series of wheels to facilitate the movement of goods and materials, offering distinct advantages in various industrial applications. This section provides an overview of wheel conveyor systems, their integration with pulley conveyor systems, advantages in handling heavy loads, and examples of industries where they are widely used.
Wheel Conveyor Systems and Their Integration with Pulley Conveyor Systems
Wheel conveyor systems are designed to transport materials using a series of wheels mounted on axles. The wheels provide a low-friction surface, allowing for easy movement of items with minimal effort. These systems are typically used for handling loads that are either too heavy for manual movement or require precise positioning during transport.
In many industrial settings, wheel conveyor systems are integrated with pulley conveyor systems to create a comprehensive material handling solution. While pulley conveyor systems use belts and pulleys to move materials over long distances and across various levels, wheel conveyor systems are often employed in areas where precise control and positioning of items are crucial. The combination of these systems allows for seamless transition of materials between different stages of the production or assembly process, enhancing overall efficiency and productivity.
Advantages of Wheel Conveyors in Handling Heavy Loads and Facilitating Smooth Material Flow
- Efficient Load Handling: Wheel conveyor systems are particularly effective in handling heavy loads. The wheels distribute the weight evenly, reducing the strain on individual components and ensuring smooth operation even with bulky or heavy items.
- Low Friction Movement: The design of wheel conveyor systems minimizes friction, making it easier to move items with minimal effort. This low-friction movement is especially beneficial in applications where items need to be transported quickly and efficiently.
- Durability: Wheel conveyors are constructed from robust materials such as steel or high-strength plastic, ensuring durability and long-term performance even in demanding environments.
- Versatility: These systems can be customized to suit a wide range of applications. They can be configured in various layouts, including straight, curved, and inclined paths, to accommodate different operational needs.
- Ease of Maintenance: Wheel conveyor systems are relatively simple in design, which makes them easy to maintain. The wheels and axles can be quickly replaced if needed, minimizing downtime and ensuring continuous operation.
- Integration with Other Systems: Wheel conveyors can be easily integrated with other material handling systems, including pulley conveyor systems. This integration allows for efficient material flow and streamlined operations across different stages of the production process.
Examples of Industries Where Wheel Conveyor Systems Are Widely Used
- Manufacturing: In manufacturing plants, wheel conveyor systems are used to transport components and finished products between different stages of the production line. They facilitate smooth and efficient movement of materials, contributing to higher productivity and reduced lead times.
- Warehousing and Distribution: Wheel conveyors are commonly used in warehouses and distribution centers to move goods from storage areas to shipping docks. Their ability to handle heavy loads and provide low-friction movement makes them ideal for these high-demand environments.
- Automotive Industry: In the automotive industry, wheel conveyor systems are used to transport car parts and assemblies. Their durability and efficiency are essential for handling the heavy components typically found in this industry.
- Food and Beverage Industry: Wheel conveyors are used in food processing and packaging facilities to move products through various stages of production. Their smooth operation ensures that delicate items are transported without damage.
- E-commerce and Retail: In e-commerce and retail distribution centers, wheel conveyors facilitate the movement of packages and parcels. Their ability to handle diverse load types and sizes makes them versatile for these fast-paced environments.
- Aerospace: In aerospace manufacturing, wheel conveyor systems are used to transport large and heavy aircraft components. Their robust construction and efficient load handling capabilities are critical in maintaining the precision and safety standards required in this industry.
Wheel conveyor systems play a vital role in enhancing the efficiency and productivity of material handling processes across various industries. When integrated with pulley conveyor systems, they offer a comprehensive solution that ensures smooth and efficient movement of materials. The advantages of wheel conveyors, such as efficient load handling, low friction movement, durability, versatility, ease of maintenance, and seamless integration, make them an indispensable component in modern industrial operations.
Applications and Benefits of Pulley Conveyor Systems
Pulley conveyor systems are integral to numerous industries, offering versatile solutions for material handling. This section explores various applications of pulley conveyor systems across sectors such as manufacturing, logistics, and mining. Additionally, we delve into the benefits these systems provide, such as increased efficiency, reduced manual labor, and improved safety. We also present case studies and real-world examples that showcase successful implementations of pulley conveyor systems.
Various Applications of Pulley Conveyor Systems
Manufacturing
In the manufacturing sector, pulley conveyor systems are essential for the efficient movement of raw materials, components, and finished products. Companies like Siemens and Caterpillar use these systems to streamline production lines, ensuring that materials are transported smoothly and consistently between different stages of manufacturing. The ability to handle diverse load types and sizes makes pulley conveyor systems ideal for complex assembly processes, where precision and reliability are paramount.
Logistics
The logistics industry relies heavily on pulley conveyor systems for the rapid and efficient movement of goods within warehouses and distribution centers. Major logistics companies such as FedEx and DHL use these systems to facilitate sorting, packing, and shipping processes. By automating material handling, pulley conveyor systems help these companies meet tight delivery schedules and manage large volumes of parcels with minimal human intervention.
Mining
In mining operations, pulley conveyor systems are used to transport bulk materials such as coal, ore, and aggregates over long distances. Companies like Rio Tinto and BHP employ these systems in their mining operations to enhance the efficiency of material extraction and processing. The robust construction and high load-bearing capacity of pulley conveyor systems make them well-suited for the harsh conditions and heavy demands of the mining industry.
Benefits of Pulley Conveyor Systems
- Increased Efficiency: Pulley conveyor systems significantly boost operational efficiency by automating the movement of materials. This automation reduces the time and effort required for manual handling, allowing companies to increase their throughput and productivity.
- Reduced Manual Labor: By minimizing the need for manual material handling, pulley conveyor systems help reduce labor costs and decrease the risk of worker injuries. This not only improves workplace safety but also allows companies to allocate their workforce to more strategic tasks.
- Improved Safety: Pulley conveyor systems enhance safety by eliminating many of the hazards associated with manual lifting and transporting of heavy loads. Features such as emergency stop mechanisms and safety guards further contribute to a safer working environment.
- Versatility: Pulley conveyor systems are highly adaptable, capable of handling a wide range of materials and loads. This versatility makes them suitable for diverse applications across various industries, from manufacturing and logistics to mining and beyond.
- Reliability: These systems are designed for durability and long-term performance, ensuring reliable operation even under demanding conditions. Regular maintenance and advancements in technology continue to improve the reliability and lifespan of pulley conveyor systems.
- Cost-Effectiveness: While the initial investment in pulley conveyor systems can be substantial, the long-term benefits such as increased efficiency, reduced labor costs, and improved safety lead to significant cost savings over time.
Case Studies and Real-World Examples
Toyota Motor Corporation
Toyota Motor Corporation implemented pulley conveyor systems in its manufacturing plants to enhance the efficiency of its production lines. The integration of these systems allowed for the smooth and continuous movement of automotive parts, reducing production bottlenecks and increasing overall output. This implementation resulted in significant improvements in productivity and cost savings for the company.
Amazon Fulfillment Centers
Amazon’s fulfillment centers utilize advanced pulley conveyor systems to manage the high volume of orders processed daily. These systems enable rapid sorting and transportation of packages, ensuring timely delivery to customers. The automation provided by pulley conveyor systems has been instrumental in Amazon’s ability to scale its operations and maintain its competitive edge in the e-commerce industry.
Vale S.A.
Vale S.A., a leading mining company, uses pulley conveyor systems to transport iron ore from its mines to processing facilities. The implementation of these systems has improved the efficiency of ore transportation, reduced operational costs, and minimized environmental impact by reducing the need for truck transport. Vale’s successful use of pulley conveyor systems exemplifies their effectiveness in the mining sector.
UPS Supply Chain Solutions
UPS Supply Chain Solutions implemented pulley conveyor systems in their logistics centers to optimize the sorting and distribution of packages. The automation provided by these systems has enabled UPS to handle increased package volumes during peak seasons, ensuring timely deliveries and improved customer satisfaction.
PepsiCo
PepsiCo integrated pulley conveyor systems into its bottling plants to streamline the production and packaging of beverages. These systems have facilitated the efficient movement of bottles and cans through various stages of production, from filling and labeling to packaging and palletizing. The result has been increased production capacity and reduced operational costs for PepsiCo.
Caterpillar Inc.
Caterpillar Inc. uses pulley conveyor systems in its manufacturing facilities to transport heavy machinery parts. The robust design and high load-bearing capacity of these systems have enabled Caterpillar to improve the efficiency of its assembly processes and reduce the risk of damage to critical components. The successful implementation of pulley conveyor systems has contributed to Caterpillar’s reputation for producing reliable and high-quality construction equipment.
Pulley conveyor systems offer a wide range of applications and benefits across various industries. Their ability to increase efficiency, reduce manual labor, and improve safety makes them an invaluable asset in modern material handling operations. The real-world examples and case studies presented here highlight the successful implementation of pulley conveyor systems, demonstrating their significant impact on enhancing productivity and operational effectiveness.
FAQs about Pulley Conveyor System
A pulley in conveyor systems is a wheel mechanism that supports the movement and direction of the conveyor belt. This essential component is mounted on a shaft, allowing rotational movement which, in turn, drives the conveyor belt around the conveyor’s frame. Pulleys are strategically placed within the conveyor design, including at the ends where the belt curves back on itself, to facilitate smooth and efficient operations. They play a crucial role in the tensioning and guiding of the conveyor belt, ensuring steady and reliable transportation of materials across different sections of the system.
While both pulleys and rollers are cylindrical components used in conveyor systems, their functions significantly differ. A pulley is primarily used to drive the conveyor belt, changing its direction and maintaining its tension. It is an active component in the system, characterized by its ability to transfer rotational motion to the belt. On the other hand, a roller is a passive component, providing support to the conveyor belt or the materials being transported. Rollers facilitate smooth movement by reducing friction and are typically found throughout the conveyor path, supporting the belt and materials from underneath or side-by-side in roller conveyors.
The pulley system in conveyors serves several critical functions:
Directional Change: Pulleys guide the conveyor belt and change its direction, especially at the tail and head ends of the conveyor.
Tensioning: They maintain the right amount of tension on the belt, which is necessary for effective material handling without slippage.
Driving Force: Drive pulleys, connected to motors, provide the necessary force to move the conveyor belt and the materials on it.
Support and Guide: Snub pulleys increase the angle of wrap on the drive pulley, enhancing friction between the belt and the pulley. Guide pulleys keep the belt on track, preventing it from wandering off the intended path.
Conveyor systems can be classified into three primary types based on their design and the materials they handle:
Belt Conveyors: These systems use continuous belts to transport materials or products from one point to another. They’re versatile and can be used for horizontal transportation or inclined/declined applications, depending on the material’s nature.
Roller Conveyors: Comprising a series of rollers, these conveyors are ideal for moving solid, rigid items. They can be powered (for automatic transportation) or unpowered (manual movement or gravitational force).
Chain Conveyors: These are designed for heavy-duty applications, using chains to move materials along a specific path. They’re suited for transporting large or heavy items and are often used in assembly lines, automotive industries, and heavy manufacturing.
Each type of conveyor has its unique applications, benefits, and considerations, making them suitable for different industrial needs.
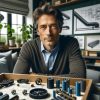
Jordan Smith, a seasoned professional with over 20 years of experience in the conveyor system industry. Jordan’s expertise lies in providing comprehensive solutions for conveyor rollers, belts, and accessories, catering to a wide range of industrial needs. From initial design and configuration to installation and meticulous troubleshooting, Jordan is adept at handling all aspects of conveyor system management. Whether you’re looking to upgrade your production line with efficient conveyor belts, require custom conveyor rollers for specific operations, or need expert advice on selecting the right conveyor accessories for your facility, Jordan is your reliable consultant. For any inquiries or assistance with conveyor system optimization, Jordan is available to share his wealth of knowledge and experience. Feel free to reach out at any time for professional guidance on all matters related to conveyor rollers, belts, and accessories.