The Essential Guide to Industrial Conveyor Pulleys
Industrial conveyor pulleys play a critical role in the efficient movement of materials across various industrial applications. These essential components are pivotal in ensuring the smooth operation of conveyor systems, which are widely used in industries such as mining, manufacturing, and logistics. There are different types of industrial conveyor pulleys, each serving a specific function within the system. Drive pulleys provide the necessary force to move the belt, tail pulleys maintain tension and alignment, and drum pulleys support and drive the belt. Understanding the distinct roles of these industrial conveyor pulleys helps in selecting the right type for specific industrial needs, enhancing both efficiency and productivity.
What are Industrial Conveyor Pulleys
Industrial conveyor pulleys are vital components in conveyor systems, which are used extensively across various industries to transport materials efficiently. These pulleys serve multiple functions, from driving the belt to maintaining tension and tracking. Understanding the roles and functions of different types of industrial conveyor pulleys is crucial for optimizing the performance and reliability of conveyor systems.
Conveyor Head and Tail Pulley
Conveyor head pulleys and tail pulleys are fundamental to the operation of a conveyor system.
Conveyor Head Pulley
The head pulley, located at the discharge end of the conveyor, plays a pivotal role in driving the belt. It is connected to a motor, which imparts the necessary force to move the belt and the materials on it. The surface of the head pulley is often coated with a material that increases friction, ensuring that the belt does not slip. This design is essential for maintaining the consistent movement of materials along the conveyor.
Conveyor Tail Pulley
At the opposite end of the conveyor system is the tail pulley. The primary function of the tail pulley is to provide tension to the belt, ensuring it remains taut and runs smoothly over the idlers and other pulleys. Additionally, the tail pulley helps in tracking the belt, ensuring it stays aligned and does not drift off course. This is crucial for preventing damage to the belt and minimizing downtime due to misalignment issues.
Conveyor Drum Pulley
The drum pulley, also known as the bend pulley, supports and drives the belt in various parts of the conveyor system. These pulleys are typically cylindrical and are placed at strategic points to help redirect the belt’s path. The drum pulley’s design allows it to handle significant loads and support the belt’s weight as it carries materials through the system. By ensuring the belt remains properly aligned and tensioned, drum pulleys play a critical role in the overall efficiency and longevity of the conveyor system.
Conveyor Drive Pulley
Drive pulleys are integral to the transmission of power within a conveyor system. They are directly connected to the motor, which drives the belt.
- Mining Operations: In mining, drive pulleys are used to transport raw materials such as ore from one location to another. The heavy-duty nature of these pulleys ensures they can handle the substantial weight and abrasive nature of the materials.
- Manufacturing Plants: Drive pulleys in manufacturing are essential for moving products along assembly lines, ensuring a steady flow of materials through different production stages.
- Food Processing: In food processing, drive pulleys are used in conveyors that handle packaging and distribution of food products, where precision and hygiene are critical.
- Recycling Facilities: Recycling plants use drive pulleys to move recyclable materials through various sorting and processing stages, ensuring efficient handling and separation.
- Logistics and Warehousing: In warehouses, drive pulleys are part of conveyor systems that move packages and goods efficiently, facilitating quick and accurate order fulfillment.
Conveyor Belt Pulley
Conveyor belt pulleys interact directly with the conveyor belt to move materials. These pulleys come in various sizes and configurations, each designed to handle specific types of belts and loads. The primary function of belt pulleys is to provide a surface around which the belt can wrap, allowing it to move continuously and smoothly. This interaction is critical for maintaining the belt’s speed and direction, ensuring that materials are transported efficiently across different sections of the conveyor system.
Conveyor Tail Pulley
The tail pulley is located at the end of the conveyor belt path and serves multiple functions. It helps in redirecting the belt back to the beginning of the conveyor loop, maintaining the belt’s tension, and ensuring proper tracking. The tail pulley’s ability to adjust tension is particularly important for preventing slack and maintaining consistent operation. Additionally, the tail pulley often has a self-cleaning feature, which removes any material build-up on the belt, reducing the risk of jams and maintaining the system’s efficiency.
Understanding the various types of industrial conveyor pulleys and their specific functions is essential for maintaining efficient and reliable conveyor systems. From driving the belt and maintaining tension to supporting the belt and ensuring proper tracking, each pulley plays a critical role in the overall performance of the conveyor system.
Industrial Conveyor Pulleys Sizes
Understanding the sizes of industrial conveyor pulleys is essential for selecting the right pulley for specific applications. The size of a pulley affects the conveyor system’s efficiency, durability, and overall performance. Different industries and applications require various pulley sizes to meet their specific needs, and knowing these requirements is crucial for optimizing conveyor system operations.
General Guide on Common Pulley Sizes
Industrial conveyor pulleys come in a range of sizes, each designed to handle different loads, speeds, and operational conditions. The size of a pulley is typically determined by its diameter and face width. Here’s a general guide to the common pulley sizes and their applications:
Small-Sized Pulleys
Diameter: 4-8 inches
Applications: Small-sized industrial conveyor pulleys are often used in light-duty applications where space is limited and the load is relatively low. These pulleys are ideal for small conveyor systems in industries such as food processing, packaging, and pharmaceutical manufacturing. They are suitable for handling lightweight materials and providing precise control over belt movement.
Medium-Sized Pulleys
Diameter: 8-16 inches
Applications: Medium-sized pulleys are versatile and commonly used in various industries, including manufacturing, warehousing, and logistics. They are suitable for handling moderate loads and speeds. These pulleys are often found in assembly lines, distribution centers, and material handling systems, where they balance efficiency and durability.
Large-Sized Pulleys
Diameter: 16-30 inches
Applications: Large-sized industrial conveyor pulleys are used in heavy-duty applications that require the transportation of large and heavy materials. Industries such as mining, quarrying, and bulk material handling commonly use these pulleys. They are designed to handle high loads, high speeds, and harsh operating conditions.
Extra-Large Pulleys
Diameter: 30 inches and above
Applications: Extra-large pulleys are used in specialized applications that require the movement of extremely heavy and bulky materials. These pulleys are often custom-designed to meet the specific needs of industries such as steel manufacturing, shipbuilding, and large-scale mining operations. They are capable of handling the highest loads and are built to withstand extreme conditions.
Factors Affecting Pulley Size Selection
When selecting the size of industrial conveyor pulleys, several factors need to be considered to ensure optimal performance and efficiency.
1. Load Capacity: The size of the pulley must match the load capacity requirements of the application. Heavier loads require larger pulleys with greater strength and durability.
2. Belt Speed: The pulley size affects the speed at which the conveyor belt moves. Larger pulleys can accommodate higher speeds, which is crucial for applications requiring fast material transport.
3. Space Constraints: The available space in the conveyor system layout can limit the size of the pulley. Smaller pulleys are ideal for compact systems, while larger pulleys require more space.
4. Operational Environment: The operating conditions, such as temperature, humidity, and exposure to corrosive materials, can influence the choice of pulley size and material. Pulleys used in harsh environments need to be larger and made from robust materials.
5. Maintenance Requirements: Larger pulleys often require less frequent maintenance due to their ability to distribute load and wear more evenly. However, they may also be more challenging to install and replace.
6. Application Specifics: Each application has unique requirements that can influence the choice of pulley size. For example, pulleys used in food processing must meet hygiene standards and may require specific materials and coatings.
Selecting the appropriate size for industrial conveyor pulleys is crucial for the efficiency and longevity of the conveyor system. By understanding the general guide on common pulley sizes and considering factors such as load capacity, belt speed, space constraints, operational environment, maintenance requirements, and application specifics, industries can ensure that their conveyor systems operate smoothly and efficiently. Whether dealing with light-duty applications or heavy-duty industrial tasks, choosing the right pulley size is essential for achieving optimal performance and minimizing downtime.
Selecting the Right Industrial Conveyor Pulleys for Your Application
Choosing the right size and type of industrial conveyor pulleys is critical for the efficiency and reliability of your conveyor system. The appropriate selection depends on various factors, each of which can significantly impact the performance and longevity of the system. Below, we will explore the key factors to consider when selecting industrial conveyor pulleys and provide five examples to illustrate their importance.
Factors to Consider When Choosing the Right Size of Conveyor Pulley
1. Load Capacity
The load capacity of the conveyor system is one of the most important factors in selecting the right pulley. The pulley must be able to handle the weight of the materials being transported without deforming or failing.
Example: In a mining operation, the conveyor system is required to transport heavy loads of ore. Selecting a pulley with a high load capacity is essential to withstand the weight and abrasive nature of the ore, ensuring the system operates smoothly without frequent breakdowns.
2. Belt Speed
The speed at which the conveyor belt moves is influenced by the size of the pulley. Larger pulleys allow for higher belt speeds, which is beneficial for applications requiring fast material transport.
Example: In a logistics and warehousing facility, the conveyor system must move packages quickly to meet high throughput demands. A larger pulley that supports higher belt speeds will help maintain the efficiency of the material handling process, ensuring timely delivery and processing of goods.
3. Environmental Conditions
The operating environment can significantly impact the selection of industrial conveyor pulleys. Factors such as temperature, humidity, and exposure to corrosive substances must be considered to ensure the pulley can withstand these conditions.
Example: In a food processing plant, conveyor pulleys are exposed to high humidity and cleaning agents. Choosing pulleys made from stainless steel or other corrosion-resistant materials ensures longevity and compliance with hygiene standards.
4. Space Constraints
The physical space available in the conveyor system layout can limit the size of the pulley. It is important to choose a pulley that fits within the available space while still meeting the operational requirements.
Example: In a compact manufacturing assembly line, space is limited. Selecting smaller pulleys that fit within the confined space but still provide adequate performance is crucial to maintaining the efficiency and functionality of the conveyor system.
5. Maintenance Requirements
The ease of maintenance and the frequency with which the pulleys need to be serviced can influence the selection process. Pulleys that require less frequent maintenance and are easier to access and replace can reduce downtime and operational costs.
Example: In a recycling facility, where conveyor systems are subjected to heavy use and harsh conditions, choosing pulleys that are durable and easy to maintain helps minimize downtime and ensures continuous operation. Pulleys with self-cleaning features and robust construction are ideal in such environments.
Practical Considerations for Selecting Industrial Conveyor Pulleys
When selecting industrial conveyor pulleys, it is also important to consider the specific needs of your application. Here are some practical steps to guide you through the selection process:
1. Assess Your Operational Requirements
Understand the specific needs of your conveyor system, including load capacity, speed, and environmental conditions. Conduct a thorough analysis of your operational requirements to identify the key specifications for the pulleys.
2. Consult with Manufacturers
Engage with reputable pulley manufacturers to get expert advice on the best options for your application. Manufacturers can provide detailed information on the performance characteristics of different pulleys and recommend suitable choices based on your needs.
3. Evaluate Material and Design
Consider the materials and design features of the pulleys. For example, pulleys made from high-strength materials like stainless steel or coated with wear-resistant finishes are ideal for demanding applications. Evaluate design features such as lagging, which can improve traction and reduce belt slippage.
4. Test and Validate
Before finalizing your selection, test the chosen pulleys in a controlled environment to validate their performance. This step helps identify any potential issues and ensures the pulleys meet your operational requirements.
5. Plan for Future Needs
Consider the future needs of your operation when selecting pulleys. Choose pulleys that can accommodate potential increases in load capacity or changes in operational conditions. This foresight helps ensure the longevity and adaptability of your conveyor system.
Selecting the right industrial conveyor pulleys for your application involves careful consideration of various factors, including load capacity, belt speed, environmental conditions, space constraints, and maintenance requirements. By thoroughly assessing these factors and following practical steps to evaluate and test pulley options, you can ensure optimal performance and reliability of your conveyor system. Investing time in selecting the appropriate pulleys not only enhances efficiency but also reduces operational costs and extends the lifespan of your equipment.
Industrial Conveyor Pulleys Price
When it comes to industrial conveyor pulleys, understanding the pricing dynamics is crucial for budgeting and procurement. The price of these essential components can vary significantly based on several factors, including material, size, and manufacturer. By exploring these factors in detail, you can make informed decisions and find the best value for your investment.
Factors Influencing the Price of Industrial Conveyor Pulleys
1. Material
The material used in the construction of industrial conveyor pulleys is one of the primary determinants of price. Different materials offer varying degrees of durability, corrosion resistance, and suitability for specific environments.
Steel: Steel is a common material for industrial conveyor pulleys due to its strength and durability. It is suitable for heavy-duty applications but can be susceptible to rust if not properly coated or maintained. Steel pulleys are generally more affordable than other high-end materials.
Stainless Steel: Stainless steel pulleys are more expensive than standard steel ones due to their enhanced resistance to corrosion and wear. They are ideal for environments where hygiene and durability are critical, such as food processing and pharmaceutical industries.
Aluminum: Aluminum pulleys are lightweight and corrosion-resistant, making them suitable for applications where weight reduction is essential. However, they may not offer the same level of strength as steel pulleys and are typically used in less demanding environments. Their price is often higher than steel but lower than stainless steel.
Composite Materials: Some pulleys are made from composite materials, which offer a balance of strength, weight, and corrosion resistance. These pulleys can be more expensive than those made from traditional metals but provide advantages in specific applications, such as high-temperature or highly corrosive environments.
Size
The size of industrial conveyor pulleys directly impacts their price. Larger pulleys require more material and more complex manufacturing processes, which increases their cost.
Small Pulleys: Small pulleys, typically with diameters less than 8 inches, are generally less expensive. They are used in light-duty applications where space is limited and the load is not too heavy.
Medium Pulleys: Pulleys with diameters between 8 and 16 inches are versatile and widely used across various industries. Their cost is moderate, balancing the need for strength and durability with affordability.
Large Pulleys: Large pulleys, with diameters ranging from 16 to 30 inches, are designed for heavy-duty applications. They are more expensive due to the increased material costs and the precision required in their manufacturing.
Extra-Large Pulleys: Pulleys with diameters above 30 inches are custom-made for specific, high-demand applications. These are the most expensive due to their specialized design, materials, and manufacturing requirements.
Manufacturer
The manufacturer of industrial conveyor pulleys plays a significant role in determining the price. Established manufacturers with a reputation for quality and reliability may charge a premium for their products. Here are some factors related to manufacturers that influence pricing:
Reputation and Brand: Well-known manufacturers who have built a reputation for high-quality products often charge higher prices. Their products are trusted for their durability, performance, and after-sales support.
Manufacturing Technology: Companies that invest in advanced manufacturing technologies and processes can produce high-quality pulleys that meet strict industry standards. These technologies, however, come at a cost, which is reflected in the price of the pulleys.
Customization: Manufacturers that offer customization options for specific applications may charge more. Customization ensures that the pulleys meet the exact requirements of the conveyor system, enhancing efficiency and lifespan.
Geographical Location: The location of the manufacturer can also affect pricing. Pulleys produced in regions with lower labor and material costs may be cheaper. However, it is essential to balance cost savings with quality and reliability.
Balancing Quality and Cost
When purchasing industrial conveyor pulleys, it is crucial to balance quality and cost. While it might be tempting to opt for the least expensive option, doing so can lead to higher maintenance costs and shorter lifespan, ultimately increasing the total cost of ownership. Here are some tips to balance quality and cost effectively:
Assess Your Needs: Understand the specific requirements of your application, including load capacity, environmental conditions, and operational demands. This assessment will help you choose pulleys that meet your needs without overpaying for unnecessary features.
Consider Total Cost of Ownership: Look beyond the initial purchase price and consider the total cost of ownership, including maintenance, downtime, and replacement costs. Investing in higher-quality pulleys can reduce these costs over time.
Compare Suppliers: Get quotes from multiple suppliers and compare their offerings. Look for suppliers who provide a good balance of quality, price, and after-sales support.
Look for Warranties and Support: Choose manufacturers who offer warranties and robust after-sales support. This ensures that you have recourse if the pulleys fail prematurely and can help you maintain your conveyor system effectively.
The price of industrial conveyor pulleys is influenced by several factors, including material, size, and manufacturer. By understanding these factors and carefully evaluating your specific needs, you can make informed purchasing decisions that balance quality and cost. Investing in the right pulleys can enhance the efficiency and longevity of your conveyor system, ultimately saving you money in the long run.
Finding Quality and Affordability in Industrial Conveyor Pulleys
Purchasing industrial conveyor pulleys involves balancing quality and affordability to ensure you get the best value for your investment. High-quality pulleys enhance the efficiency and lifespan of conveyor systems, while affordability ensures that you stay within budget. Here are some tips and examples on how to achieve this balance effectively.
Tips on Balancing Quality and Cost
1. Understand Your Requirements
Before purchasing industrial conveyor pulleys, it’s essential to understand the specific requirements of your application. Consider factors such as load capacity, belt speed, environmental conditions, and maintenance needs. By having a clear understanding of these requirements, you can select pulleys that are not only suitable but also cost-effective.
2. Evaluate Material Options
Different materials offer varying levels of durability, strength, and resistance to environmental factors. Evaluating the material options can help you find pulleys that meet your needs without overpaying for unnecessary features.
3. Compare Multiple Suppliers
Getting quotes from multiple suppliers can provide a broader perspective on pricing and quality. Look for suppliers with good reputations, positive customer reviews, and competitive pricing.
4. Consider the Total Cost of Ownership
While the upfront cost is important, the total cost of ownership includes maintenance, downtime, and replacement expenses. Higher-quality pulleys often reduce these long-term costs by requiring less frequent maintenance and lasting longer.
5. Leverage Warranties and Support
Warranties and robust after-sales support can provide peace of mind and ensure that you are covered in case of premature failures or defects. Look for suppliers who offer comprehensive warranties and reliable support services.
Practical Steps for Finding Quality and Affordability
1. Perform a Needs Analysis
Conduct a thorough analysis of your operational needs. Document the specific requirements for load capacity, environmental conditions, and operational demands. This step helps you identify the essential features needed in the pulleys.
2. Research and Vet Suppliers
Research potential suppliers, read reviews, and ask for references. Vetting suppliers ensures that you partner with reputable companies that deliver on their promises of quality and affordability.
3. Request Detailed Quotations
Request detailed quotations from multiple suppliers. These should include a breakdown of costs, materials, customization options, and warranty terms. Comparing these quotes side-by-side helps you identify the best value.
4. Conduct a Cost-Benefit Analysis
Analyze the cost-benefit of each option. Consider not only the upfront cost but also the long-term benefits such as reduced maintenance, longer lifespan, and improved efficiency. This holistic view ensures that you choose pulleys that offer the best overall value.
5. Test Before Full Deployment
If possible, test a small batch of pulleys before making a large purchase. This testing phase allows you to evaluate the performance and durability of the pulleys in real-world conditions, ensuring they meet your expectations.
Balancing quality and affordability when purchasing industrial conveyor pulleys requires a strategic approach. By understanding your requirements, evaluating material options, comparing multiple suppliers, considering the total cost of ownership, and leveraging warranties and support, you can find pulleys that offer the best value. Performing a needs analysis, researching suppliers, requesting detailed quotations, conducting cost-benefit analyses, and testing before full deployment are practical steps that can guide you in making informed decisions. Investing time in this process ensures that you select high-quality pulleys that enhance the efficiency and longevity of your conveyor system while staying within budget.
Industrial Conveyor Pulleys Manufacturers
When it comes to selecting industrial conveyor pulleys, choosing the right manufacturer is crucial. Leading manufacturers like Superior Industries, Martin, Precision Pulley & Idler, and ASGCO have established themselves as trusted providers of high-quality conveyor pulleys. This overview will delve into the unique offerings and benefits provided by these companies, helping you make informed decisions for your conveyor system needs.
Superior Industries Conveyor Pulleys
Superior Industries is renowned for its innovation and quality in the conveyor pulley market. One of their standout products is the Crown Face Conveyor Pulley, which offers several benefits designed to enhance the performance and longevity of conveyor systems.
1. Enhanced Belt Tracking: The Crown Face design ensures better belt tracking by naturally centering the belt as it moves. This reduces the risk of belt misalignment and extends the life of both the belt and the pulley.
2. Increased Traction: The unique design of Crown Face Conveyor Pulleys provides increased traction between the belt and the pulley. This minimizes slippage and improves the efficiency of the conveyor system.
3. Reduced Maintenance: Superior Industries’ pulleys are designed to reduce maintenance needs. The Crown Face design minimizes wear and tear on the belt, leading to less frequent maintenance and lower operational costs.
4. Versatility: These pulleys are suitable for a wide range of applications, from mining to manufacturing, making them a versatile choice for many industries.
5. Customization: Superior Industries offers customization options for their Crown Face Conveyor Pulleys, allowing customers to tailor the pulleys to their specific needs and operational requirements.
ASGCO’s Conveyor Pulleys
ASGCO is another leading name in the mining conveyor pulleys market, known for offering a variety of pulley types with specific features tailored to different applications.
1. Drum Pulleys: ASGCO’s drum pulleys are designed for heavy-duty applications, offering robust construction and high load capacity. They are ideal for use in mining and bulk material handling.
2. Wing Pulleys: ASGCO’s wing pulleys feature a unique design that helps to shed material, reducing build-up and maintaining smooth operation. These pulleys are particularly useful in environments where materials are prone to sticking to the belt.
3. Spiral Pulleys: The spiral design of ASGCO’s pulleys helps in cleaning the belt and preventing material carryback, improving the overall efficiency of the conveyor system.
4. Custom Pulleys: ASGCO offers custom-designed pulleys to meet specific operational requirements, ensuring that customers get the exact solution they need for their conveyor systems.
5. Advanced Coatings: Many of ASGCO’s pulleys come with advanced coatings that enhance their durability and resistance to wear and corrosion, making them suitable for use in harsh environments.
Selecting the right manufacturer for industrial conveyor pulleys is crucial for ensuring the efficiency and longevity of your conveyor systems. Superior Industries, Martin, Precision Pulley & Idler, and ASGCO each offer unique products and benefits that cater to a wide range of industrial needs. By understanding the specific offerings and advantages of these leading manufacturers, you can make informed decisions and select pulleys that provide the best balance of quality, performance, and affordability for your applications.
Key Features of Industrial Conveyor Pulleys
Industrial conveyor pulleys are essential components in a wide range of conveyor systems, providing the necessary support and movement for materials across various industries. The effectiveness and longevity of these pulleys depend significantly on their design and construction. Below, we explore the key features of industrial conveyor pulleys that contribute to their durability and efficiency.
Heavy-Duty Construction and Design Considerations for Durability
One of the primary attributes of industrial conveyor pulleys is their heavy-duty construction. This feature ensures that the pulleys can withstand the rigors of demanding industrial environments, such as mining, manufacturing, and bulk material handling. Here are some critical aspects of heavy-duty construction and design:
1. Robust Materials
Industrial conveyor pulleys are typically made from high-strength materials such as steel, stainless steel, and composite materials. Steel is favored for its strength and durability, making it ideal for heavy-duty applications. Stainless steel offers additional benefits like corrosion resistance, which is crucial in environments where moisture or chemicals are present. Composite materials provide a lightweight yet strong alternative, suitable for specific applications that require reduced weight.
2. Precision Manufacturing
The precision manufacturing of mining conveyor pulleys ensures that each component meets exact specifications and tolerances. This precision is vital for maintaining the balance and smooth operation of the conveyor system. Advanced manufacturing techniques, such as CNC machining and laser cutting, are often employed to achieve the necessary accuracy and consistency.
3. Reinforced End Discs
Reinforced end discs add extra strength to the pulley structure, preventing deformation and ensuring stable operation under heavy loads. These discs are typically welded to the pulley shell, creating a solid and reliable connection that can handle significant stress and strain.
4. Heavy-Duty Bearings
Bearings play a crucial role in the functionality of conveyor pulleys. Industrial conveyor pulleys are equipped with heavy-duty bearings designed to handle high loads and harsh operating conditions. These bearings reduce friction, enhance the pulley’s rotation efficiency, and extend the overall lifespan of the pulley.
5. Protective Coatings
To further enhance durability, industrial conveyor pulleys often feature protective coatings. These coatings protect against wear, corrosion, and abrasion, which are common in industrial environments. Common coatings include epoxy, polyurethane, and galvanized finishes, each offering specific benefits depending on the application’s requirements.
Innovations for Belt Training and Efficiency
In addition to robust construction, modern industrial conveyor pulleys incorporate various innovations to improve belt training and overall system efficiency. These innovations help ensure that the conveyor belt remains aligned and operates smoothly, reducing maintenance costs and downtime.
1. Crowned Face Design
The crowned face design is a common innovation in conveyor pulleys, where the center of the pulley is slightly larger in diameter than the edges. This design helps center the conveyor belt, reducing the risk of misalignment and ensuring consistent tracking. Proper belt alignment minimizes wear and tear on both the belt and the pulley, enhancing the system’s efficiency and lifespan.
2. Wing Pulleys
Wing pulleys are designed with a unique structure that helps shed material buildup from the belt. The wings on the pulley prevent material from accumulating, which can cause belt slippage and misalignment. This self-cleaning feature is particularly beneficial in environments where materials are sticky or prone to buildup, such as in recycling or aggregate handling.
3. Spiral Pulleys
Spiral pulleys feature a helical design that helps clean the conveyor belt and improve traction. The spiral grooves move materials toward the edges of the pulley, preventing buildup and maintaining efficient belt operation. This design is especially useful in applications where fine materials are transported, and cleanliness is critical.
4. Rubber Lagging
Rubber lagging involves covering the pulley surface with a layer of rubber, which increases friction between the pulley and the belt. This added friction improves traction, reduces belt slippage, and enhances the pulley’s ability to transmit power effectively. Rubber lagging also provides a cushioning effect, absorbing shock and reducing wear on the belt.
5. Adjustable Tensioning Systems
Modern conveyor pulleys often incorporate adjustable tensioning systems that allow for easy adjustment of belt tension. Proper tensioning is crucial for maintaining optimal belt performance and preventing issues such as slippage and misalignment. Adjustable systems provide flexibility and ease of maintenance, ensuring the conveyor system operates at peak efficiency.
The key features of industrial conveyor pulleys, such as heavy-duty construction and innovative design elements, play a vital role in ensuring their durability and efficiency. Robust materials, precision manufacturing, reinforced end discs, heavy-duty bearings, and protective coatings contribute to their longevity and reliability in demanding environments. Innovations like crowned face designs, wing pulleys, spiral pulleys, rubber lagging, and adjustable tensioning systems enhance belt training and operational efficiency. By understanding these features, industries can select the right pulleys to optimize their conveyor systems, reducing maintenance costs and improving overall productivity.
Applicable Industries for Industrial Conveyor Pulleys
Industrial conveyor pulleys are integral components in numerous industries, playing a crucial role in material handling and transportation systems. Their robust construction and versatile design make them suitable for a wide range of applications. This section highlights several key industries where industrial conveyor pulleys are indispensable, providing specific examples to illustrate their importance and functionality.
Mining
The mining industry heavily relies on industrial conveyor pulleys to transport raw materials such as coal, ore, and aggregates. The harsh and demanding conditions of mining operations require pulleys that can withstand significant stress and abrasive environments.
Coal Mining: In coal mining operations, conveyor pulleys are used to move large quantities of coal from extraction sites to processing plants. Heavy-duty pulleys with reinforced bearings and durable coatings are essential to handle the heavy loads and abrasive coal dust.
Aggregate Mining: In the extraction of aggregates like sand, gravel, and crushed stone, conveyor pulleys facilitate the efficient transport of materials to crushers, screens, and washing plants. Wing pulleys are often used to prevent material buildup and maintain smooth operation.
Packaging
The packaging industry utilizes conveyor systems extensively to move products through various stages of the packaging process. Industrial conveyor pulleys ensure the smooth and efficient transport of goods, enhancing productivity and accuracy.
Automated Packaging Lines: In automated packaging lines, conveyor pulleys are essential for moving products quickly and accurately from one station to another. Crown face pulleys help maintain belt alignment, ensuring that packages are correctly positioned for labeling, filling, and sealing operations.
Sorting Systems: Conveyor pulleys are critical in sorting systems where products are categorized and directed to different destinations. Adjustable tensioning systems in pulleys help maintain consistent belt tension, ensuring precise sorting and minimizing downtime.
Food Processing
Food processing plants require conveyor systems that meet strict hygiene standards and ensure safe and efficient transport of food products. Industrial conveyor pulleys designed for food processing applications must be durable, easy to clean, and resistant to corrosion.
Meat Processing: In meat processing plants, stainless steel conveyor pulleys are used to move products through various stages, including cutting, packaging, and freezing. The corrosion resistance and hygiene properties of stainless steel are crucial for maintaining food safety standards.
Bakery Operations: Conveyor pulleys in bakeries transport dough, baked goods, and packaging materials. Rubber lagging on pulleys provides additional traction, ensuring smooth movement of products and reducing the risk of contamination.
Recycling
The recycling industry benefits significantly from the use of industrial conveyor pulleys, which help in the efficient sorting and processing of recyclable materials. The robust construction of these pulleys ensures they can handle the heavy loads and abrasive materials typical in recycling operations.
Material Recovery Facilities (MRFs): In MRFs, conveyor pulleys are used to transport and sort various recyclable materials such as paper, plastic, and metals. Spiral pulleys help clean the conveyor belts, preventing material buildup and ensuring efficient operation.
Scrap Metal Processing: Conveyor pulleys in scrap metal processing plants handle heavy and abrasive metal pieces. Heavy-duty construction and protective coatings are essential to withstand the harsh conditions and prevent wear and tear.
Manufacturing
In manufacturing industries, conveyor systems with mining conveyor pulleys are vital for moving raw materials, components, and finished products through different stages of production. The efficiency and reliability of these pulleys directly impact production timelines and costs.
Automotive Manufacturing: In automotive plants, conveyor pulleys move parts and assemblies through various production stages, from stamping to final assembly. Precision-engineered pulleys ensure smooth and reliable operation, reducing downtime and increasing productivity.
Electronics Manufacturing: Conveyor pulleys in electronics manufacturing transport delicate components and finished products. Adjustable tensioning systems help maintain proper belt tension, ensuring accurate and damage-free movement of sensitive items.
Industrial conveyor pulleys are indispensable across a wide range of industries, including mining, packaging, food processing, recycling, and manufacturing. Their robust design and versatility enable them to handle the specific demands and challenges of these industries. Whether it’s moving heavy loads in mining operations, ensuring hygiene in food processing, or facilitating efficient sorting in recycling plants, industrial conveyor pulleys play a critical role in enhancing the efficiency and productivity of conveyor systems. By understanding the unique requirements of each industry, companies can select the appropriate pulleys to optimize their operations and achieve long-term success.
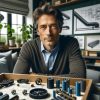
Jordan Smith, a seasoned professional with over 20 years of experience in the conveyor system industry. Jordan’s expertise lies in providing comprehensive solutions for conveyor rollers, belts, and accessories, catering to a wide range of industrial needs. From initial design and configuration to installation and meticulous troubleshooting, Jordan is adept at handling all aspects of conveyor system management. Whether you’re looking to upgrade your production line with efficient conveyor belts, require custom conveyor rollers for specific operations, or need expert advice on selecting the right conveyor accessories for your facility, Jordan is your reliable consultant. For any inquiries or assistance with conveyor system optimization, Jordan is available to share his wealth of knowledge and experience. Feel free to reach out at any time for professional guidance on all matters related to conveyor rollers, belts, and accessories.