Common Causes and Types of Conveyor Belt Damage
Conveyor belts play a pivotal role in the seamless operation of numerous industries, from manufacturing and mining to logistics and food processing. These belts are the lifelines that ensure the efficient, continuous flow of goods and materials, making them indispensable for daily operations. However, the functionality and reliability of these systems can be severely compromised by conveyor belt damage. Such damage not only disrupts the flow of operations but can also lead to significant financial losses, safety hazards, and increased downtime. Recognizing the types of damage that can occur and understanding their potential impact is crucial for maintaining the operational integrity of conveyor belt systems. This introduction aims to shed light on the common issues faced by conveyor belts and the ripple effects they can have on industry operations.
Types of Conveyor Belt Damage
Conveyor belt damage can significantly impact the efficiency and safety of operations in various industries. Understanding the different types of conveyor belt damage is crucial for implementing effective maintenance strategies and ensuring the longevity of these essential components.
Impact Damage: Impact damage occurs when objects strike the conveyor belt with significant force, leading to visible impairments such as nicks, scratches, or gouges. This type of damage is common in industries where large, heavy, or sharp materials, like frozen lumps of coal, are handled. The impact can compromise the structural integrity of the belt, necessitating prompt repair or replacement to prevent further deterioration.
Entrapment Damage: Entrapment damage is characterized by materials getting trapped under or between the conveyor components, creating grooves or cuts along the belt’s edges. This often results from inadequate sealing or misalignment, allowing materials to wedge into spaces they shouldn’t. The continuous abrasion against trapped materials can accelerate the wear of the belt, leading to premature failure.
Belt-edge Damage: Belt-edge damage is primarily caused by the conveyor belt mistracking or drifting away from its intended path, resulting in frayed edges or complete separation of the belt layers. Factors contributing to mistracking include improper installation, misaligned rollers, or uneven loading. This type of damage not only affects the belt’s performance but can also pose safety risks to operators.
Delamination: Delamination refers to the separation of the layers within the conveyor belt, either between the plies of fabric or between the fabric and the top cover. This can be caused by excessive tension, poor splicing techniques, or the penetration of water or chemicals. Delamination compromises the belt’s strength and flexibility, leading to operational inefficiencies and potential breakdowns.
Worn Top Cover: The top cover of a conveyor belt can wear down due to the abrasive nature of the materials being transported. Over time, repeated loading and unloading of materials, especially those with sharp edges or rough surfaces, can erode the top layer, exposing the inner fabric or carcass. This wear can significantly reduce the belt’s lifespan and efficiency.
Heat Damage: Conveyor belts exposed to high temperatures can suffer from heat damage, manifesting as cracks, warping, or complete melting of the belt material. This is particularly prevalent in industries where hot materials are processed or transported. Heat damage not only weakens the belt but can also lead to catastrophic failures if not addressed promptly.
Junction-joint Failure: Junction-joint failure occurs at the conveyor belt transition points where the conveyor belt shifts from a flat to a troughed position. This damage is characterized by tearing or separation at the joints, often resulting from excessive tension or inadequate support. Such failures disrupt the smooth operation of the belt and can lead to significant downtime.
Camber and Belt Cupping: Camber and belt cupping result from the belt not lying flat or forming a curve across its width, often due to improper storage, handling, or tensioning. This can cause the belt to mistrack, leading to uneven wear and potential damage to both the belt and the conveyor structure. Proper installation and maintenance are key to preventing these issues.
Each type of conveyor belt damage presents unique challenges and requires specific strategies for repair and prevention. Regular inspections, proper maintenance, and immediate attention to any signs of damage are essential for minimizing operational disruptions and extending the life of conveyor belts.
Conveyor Belt Damage Detection
Early detection of conveyor belt damage is pivotal in preventing minor issues from escalating into major operational disruptions. Identifying early signs of wear and damage can significantly reduce repair costs, extend the conveyor belt’s lifespan, and maintain operational efficiency. Below, we delve into the common signs of conveyor belt damage to be vigilant about, followed by the latest technologies and methods for effective damage detection.
Common Signs of Conveyor Belt Damage to Look Out For
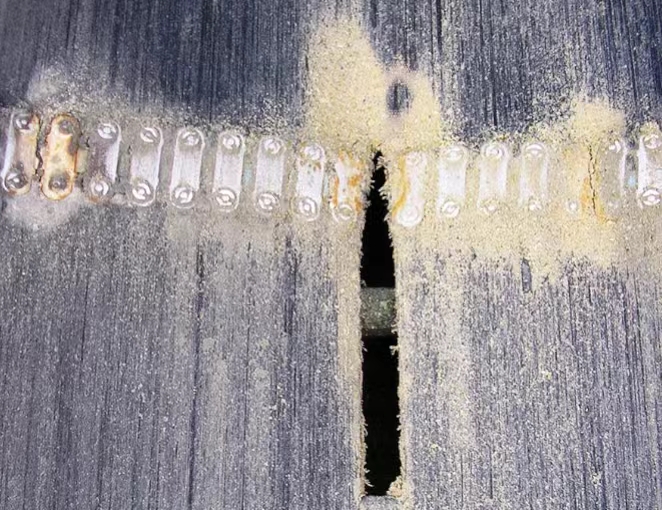
Before diving into specific signs, it’s important to understand that conveyor belt damage can manifest in various forms, each potentially leading to decreased performance, increased downtime, and safety hazards. Regular monitoring for these signs can help in taking timely corrective actions.
- Visible Tears and Cuts: Direct indicators of mechanical impact or sharp object damage.
- Edge Fraying: Suggests misalignment or edge wear, often due to improper tracking.
- Surface Wear: Indicates areas of high contact or abrasion, leading to thinning of the belt surface.
- Discoloration: Can signal exposure to high temperatures or chemical reactions affecting the belt material.
- Misalignment: The belt not running centrally can cause uneven wear and operational issues.
- Material Spillage: Often a consequence of belt damage, misalignment, or incorrect loading, leading to loss of materials.
- Noise Increase: Unusual sounds from the conveyor system may hint at internal damage or misalignment.
- Vibration: Excessive or abnormal vibrations can indicate underlying issues with belt integrity.
- Belt Slippage: This can be a symptom of wear, damage, or incorrect tensioning of the belt.
Technologies and Methods for Detecting Conveyor Belt Damage
The advancement in detection technologies has provided a range of tools and methods to identify and diagnose conveyor belt damage effectively. Employing these technologies can facilitate early detection, allowing for prompt maintenance actions.
- Visual Inspections: The simplest yet effective method involves regular and thorough checks by experienced personnel.
- Infrared Thermography: This technology helps in identifying hot spots caused by excessive friction, misalignment, or other issues leading to heat build-up.
- Ultrasonic Monitoring: Useful for detecting variations in belt thickness or internal damages not visible to the naked eye.
- Radiography (X-ray): Offers a deeper look into the conveyor belt’s internal structure, revealing hidden flaws or weaknesses.
- Laser Scanning: Provides accurate measurements of wear patterns, edge damage, and overall belt condition.
- Conveyor Belt Scanners: These sensors detect surface anomalies, wear patterns, and other changes indicating damage.
- Vibration Analysis: Analyzes vibration patterns to identify misalignments, imbalances, or other mechanical issues.
- Drone Inspections: Especially useful for inspecting large-scale conveyor systems, drones can spot issues from an aerial perspective, highlighting areas needing closer inspection.
Incorporating these detection methods into regular maintenance routines can significantly enhance the ability to spot and address conveyor belt damage early, ensuring the longevity and reliability of the conveyor system.
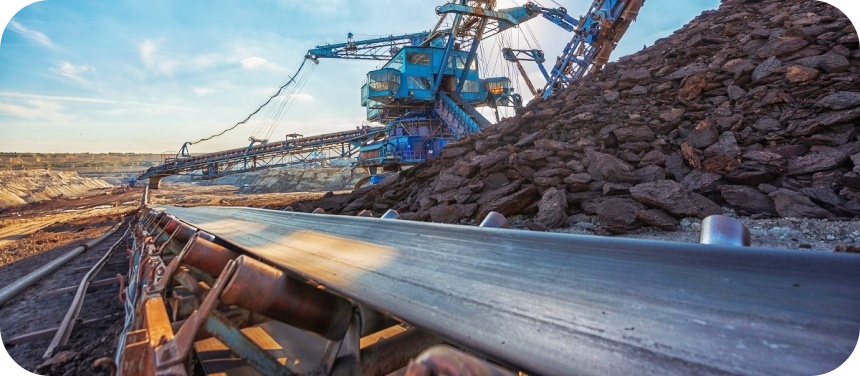
Causes of Conveyor Belt Damage
The integrity and functionality of conveyor belts are critical to the smooth operation of a wide range of industries. However, these belts are susceptible to various types of damage, which can compromise their efficiency and lead to significant operational disruptions. Understanding the multifaceted causes of conveyor belt damage is essential for developing effective preventive strategies and ensuring the longevity of the conveyor system. Below, we explore the factors contributing to conveyor belt damage, followed by an examination of how environmental conditions, operational errors, and mechanical failures play a pivotal role in this context.
Factors Contributing to Conveyor Belt Damage
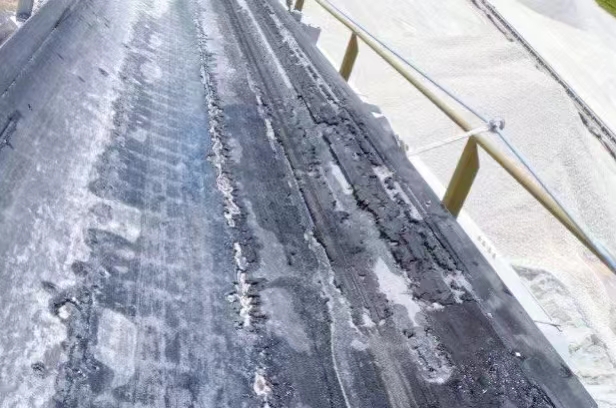
Conveyor belt damage can arise from a myriad of sources. Common causes of conveyor belt damage include large or abrasive materials, excessive wear on rollers, improper tension, foreign objects, and incomplete splicing. Each with the potential to significantly impact the belt’s performance and lifespan. Identifying these factors is the first step towards mitigating their effects.
- Overloading: Subjecting the belt to loads beyond its designed capacity can cause significant stress and strain, leading to structural damage.
- Material Sharpness: Sharp-edged materials can cut or gouge the belt surface, compromising its integrity and leading to potential failure.
- Impact at Loading Points: The force of materials dropping onto the belt, especially from heights, can cause immediate and severe impact damage.
- Misalignment: A belt that is not properly aligned can rub against stationary parts of the conveyor system, causing wear and tear on the edges.
- Inadequate Tensioning: Incorrect tensioning can lead to slippage or excessive stretching, both of which can damage the belt.
- Chemical Exposure: Certain chemicals can react with the belt material, weakening it and making it more susceptible to damage.
- High Temperatures: Exposure to high temperatures can alter the physical properties of the conveyor belt material, leading to deformation and reduced functionality.
- Age and Wear: Natural degradation over time due to regular use can weaken the belt, making it more prone to damage.
The Role of Environmental Conditions, Operational Errors, and Mechanical Failures
The environment in which a conveyor belt operates, along with how it is used and maintained, significantly influences its susceptibility to damage.
- Environmental Conditions: Factors such as temperature, humidity, and exposure to sunlight can accelerate the wear and tear on a conveyor belt.
- Operational Errors: Mistakes in operation, such as improper loading or handling of materials, can lead to uneven wear and increased risk of damage.
- Mechanical Failures: Failures within the conveyor system, such as seized rollers or malfunctioning idlers, can create points of increased friction and stress on the belt.
- Poor Maintenance: Neglecting regular maintenance and inspections can allow minor issues to escalate, resulting in significant damage.
- Abrasive Materials: The continuous movement of abrasive materials can erode the belt surface, diminishing its thickness and structural integrity.
- Lack of Cleaning: Accumulation of debris and residues on the belt and within the conveyor system can lead to additional wear and operational issues.
- Improper Belt Selection: Choosing a belt that is not suited to the specific demands of the application can lead to premature failure.
- Vibration: Excessive vibration from the conveyor system can lead to joint failure and damage to the belt fabric.
By closely monitoring these factors and implementing a robust maintenance schedule, it is possible to significantly reduce the incidence of conveyor belt damage, thereby ensuring the efficient and uninterrupted operation of the conveyor system.
Conveyor Belt Damage Problems and Solutions
Conveyor belt systems are integral to the operations of various industries, facilitating the efficient transport of materials. However, these systems are prone to several issues that can lead to conveyor belt damage, affecting productivity and safety. Understanding these problems and implementing effective solutions is crucial for maintaining the integrity and longevity of conveyor belts. Below, we explore common conveyor belt issues and their corresponding solutions, focusing on tracking problems, belt slippage, blockages, carryback, material spillage, and seized rollers.
Tracking Problems
Proper alignment and tracking are essential for the smooth operation of conveyor belts. Misalignment can cause uneven wear, damage to the belt edges, and potential system failure.
- Routine Alignment Checks: Regularly inspect and adjust the conveyor frame and rollers to ensure proper alignment.
- Correct Installation: Ensure that all conveyor components are installed correctly and according to manufacturer specifications.
- Use of Tracking Devices: Install conveyor belt tracking devices that automatically adjust the belt’s position to prevent misalignment.
- Load Distribution: Ensure materials are evenly distributed across the belt to avoid uneven forces and misalignment.
- Training for Operators: Provide training for operators on the correct loading techniques and signs of misalignment.
- Preventive Maintenance Schedule: Implement a preventive maintenance schedule that includes checks and adjustments for alignment.
Belt Slippage
Belt slippage reduces the efficiency of conveyor systems and can cause wear or damage to the belt.
- Adequate Tensioning: Maintain proper belt tension to prevent slippage on the conveyor belt drive pulley.
- Use of High-friction Lagging: Apply high-friction conveyor lagging to drive pulleys to increase grip and reduce slippage.
- Regular Belt Inspections: Inspect belts for wear and replace them before they become too smooth and prone to slippage.
- Environmental Controls: Control environmental factors such as moisture and dust that can affect the belt’s grip.
- Proper Belt Selection: Choose belts with appropriate surface textures and materials for the application to minimize slippage.
- Speed Adjustments: Adjust conveyor speed to match the material handling requirements and reduce the risk of slippage.
Blockages
Blockages in conveyor systems can cause downtime and damage to the belt and other components.
- Regular Cleaning: Implement a cleaning schedule to remove debris and materials that could cause blockages.
- Design Considerations: Design conveyor systems with minimal points of entrapment and easy access for cleaning.
- Installation of Scrapers: Install scrapers at strategic points to remove sticky or clinging materials from the belt.
- Vibration Systems: Use vibration systems to dislodge materials that may cause blockages.
- Monitoring Systems: Employ conveyor monitoring systems to detect blockages early and stop the conveyor before damage occurs.
- Training on Jam Removal: Train personnel on safe and effective methods for removing jams and blockages.
Carryback
Carryback refers to material that sticks to the belt past the discharge point, leading to cleanliness and maintenance issues.
- Primary and Secondary Cleaners: Install primary and secondary belt cleaners to effectively remove residual materials.
- Water Sprays: Use water sprays where appropriate to help dislodge sticky materials from the belt.
- Adjustable Skirting: Implement adjustable skirting that closely fits the belt profile to minimize carryback.
- Material Analysis: Analyze material properties to select the most effective cleaning systems.
- Regular Inspection and Maintenance: Regularly inspect and maintain cleaning systems to ensure their effectiveness.
- Belt Surface Selection: Choose belt surfaces that minimize material adhesion based on the properties of the materials being transported.
Material Spillage
Material spillage not only causes conveyor belt damage but also poses safety hazards and leads to material loss.
- Impact Beds and Cradles: Install conveyor impact beds and cradles to absorb the energy of falling materials at loading zones.
- Side Skirts: Use side skirts along the edges of the belt to contain materials and prevent spillage.
- Proper Loading Techniques: Ensure materials are loaded onto the belt in a controlled manner to minimize spillage.
- Conveyor Sealing Systems: Implement sealing systems at transfer points to contain materials.
- Regular Housekeeping: Conduct regular housekeeping to remove spilled materials and prevent build-up.
- Spillage Recovery Systems: Use spillage recovery systems to collect and return spilled materials to the process stream.
Seized Rollers
Seized or malfunctioning rollers can create friction points that damage the conveyor belt and reduce system efficiency.
- Lubrication Programs: Implement a lubrication program to ensure conveyor rollers and bearings are properly lubricated.
- Regular Roller Inspections: Conduct regular inspections to identify and replace seized or worn rollers.
- Use of Quality Rollers: Invest in high-quality rollers designed for the specific operating conditions.
- Alignment Checks: Ensure rollers are correctly aligned to prevent uneven wear and potential seizing.
- Temperature Monitoring: Monitor roller temperatures to detect overheating, which can indicate seizing.
- Debris Removal: Keep the conveyor area clean of debris that could jam rollers.
By addressing these common conveyor belt problems with targeted solutions, operations can enhance the efficiency, safety, and longevity of their conveyor systems, minimizing downtime and ensuring continuous productivity.
Conveyor Belt Joint Failure
Conveyor belt joint failure is a significant issue that can disrupt operations, leading to costly downtimes and repairs. Understanding the causes of joint failure and implementing effective prevention and repair techniques are crucial for maintaining the efficiency and longevity of conveyor systems. This section delves into the common causes of conveyor belt failure and outlines strategies to prevent and repair these failures.
Causes of Joint Failure
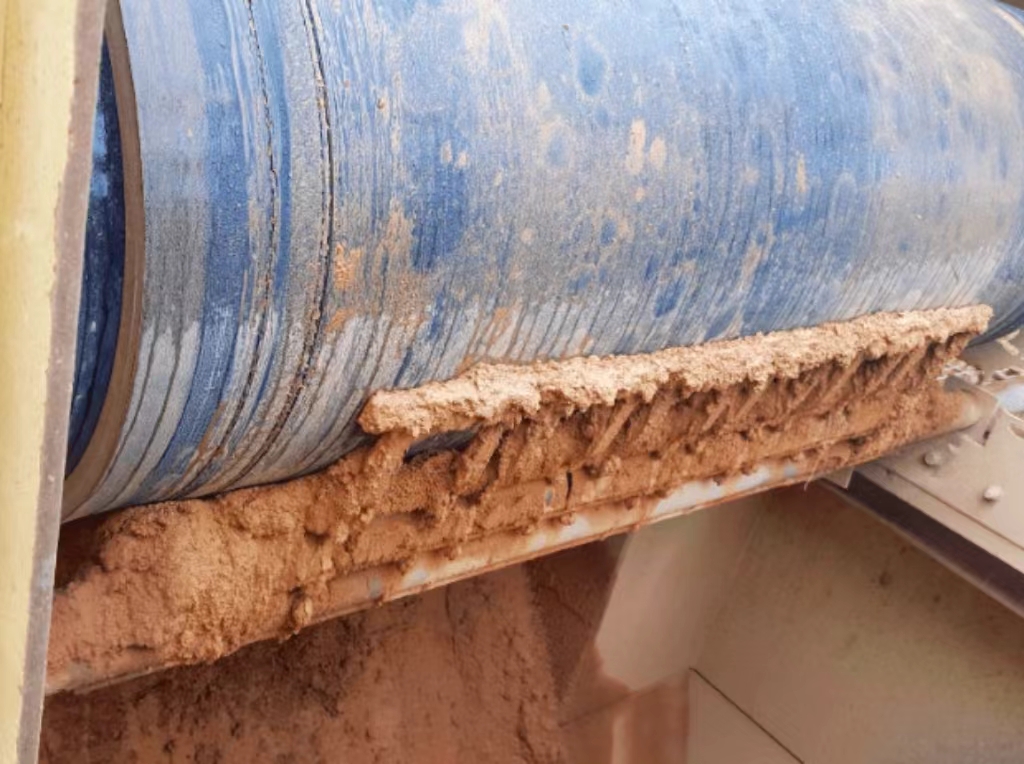
Stress Concentration:
One of the primary causes of conveyor belt joint failure is stress concentration. When there is uneven tension and load distribution across the conveyor belt, certain sections, particularly the joints, experience higher stress levels. This uneven stress can lead to accelerated wear and eventual failure of the joints.
- Uneven Tension: If the tension across the belt is not uniform, certain parts of the belt bear more load than others, causing stress to concentrate at specific points, especially the joints. This can happen due to misaligned pulleys, improper belt tensioning, or variations in load distribution.
- Load Distribution: Conveyor systems that frequently handle heavy or uneven loads can cause significant stress on the belt joints. Overloading or sudden impacts from heavy materials can exacerbate this issue, leading to joint failure.
Improper Splicing:
Splicing is the process of joining two ends of a conveyor belt. If not done correctly, splicing can be a weak point in the belt, leading to premature failure.
- Poor Techniques: Inadequate splicing techniques, such as improper adhesive application or incorrect use of splicing tools, can result in weak joints. This can cause the joint to fail under normal operational stresses.
- Incorrect Materials: Using substandard or incompatible materials for splicing can compromise the joint’s integrity. For instance, using the wrong type of adhesive or splicing materials that do not match the belt’s specifications can lead to weak joints that are prone to failure.
Environmental Factors:
Environmental conditions can significantly impact the durability and performance of conveyor belt joints.
- Temperature Fluctuations: Extreme temperatures can cause the materials in the belt joints to expand and contract, leading to weakening and eventual failure. High temperatures can degrade adhesives, while low temperatures can make the materials brittle.
- Moisture: Exposure to moisture can lead to the degradation of splicing materials, especially if the materials are not designed to withstand wet conditions. Moisture can also cause rust and corrosion in the metallic components of the joints.
- Chemicals: Chemical exposure can weaken the belt materials and adhesives used in the joints. This is particularly relevant in industries where the conveyor belts are exposed to harsh chemicals regularly.
Prevention and Repair Techniques
Proper Splicing Methods:
Using the right splicing methods is critical for creating strong and durable joints.
- High-Quality Materials: Ensure that the materials used for splicing, such as adhesives, fasteners, and splicing kits, are of high quality and compatible with the belt specifications. High-quality materials provide better adhesion and durability, reducing the risk of joint failure.
- Professional Techniques: Employing professional splicing techniques ensures that the joints are properly aligned and secured. This includes following the manufacturer’s guidelines for splicing and using the correct tools and methods for the specific type of belt.
Regular Inspections:
Routine inspections are essential for identifying early signs of stress or wear in conveyor belt joints.
- Early Detection: Regularly inspecting the belt joints can help detect issues such as small cracks, signs of wear, or uneven tension before they lead to more significant problems. Early detection allows for timely repairs, preventing more severe damage and costly downtime.
- Preventive Maintenance: Implementing a preventive maintenance schedule that includes regular checks of the belt tension, alignment, and condition of the splices can significantly extend the lifespan of the conveyor belt.
Environmental Protection:
Protecting conveyor belt joints from environmental factors is crucial for maintaining their integrity and performance.
- Protective Covers: Using protective covers can shield the belt joints from harsh environmental conditions, such as extreme temperatures, moisture, and chemicals. These covers provide an additional layer of protection, preventing direct exposure to damaging elements.
- Resistant Materials: Selecting materials that are resistant to the specific environmental conditions of the operation can enhance the durability of the belt joints. For example, using moisture-resistant adhesives and materials in humid environments or chemical-resistant components in industries with harsh chemical exposure.
How to Fix Conveyor Belt Damage
Addressing conveyor belt damage effectively is crucial for maintaining the operational efficiency and safety of conveyor systems. A systematic approach to repairing common types of conveyor belt damage not only extends the belt’s life but also prevents potential downtimes. Here, we provide a detailed guide on how to fix conveyor belt damage, including a decision-making framework for when to repair versus when to replace parts of the conveyor belt.
Step-by-Step Guide on Repairing Common Types of Conveyor Belt Damage
- Identify the Damage: Conduct a thorough inspection of the conveyor belt to identify all areas of damage, noting their types and extents.
- Clean the Area: Before any repair, clean the damaged area to remove any debris, dust, or contaminants that could interfere with the repair process.
- Cut Damaged Sections: For tears or cuts, carefully cut out the damaged section using appropriate tools, ensuring straight edges for easier patching.
- Choose the Right Repair Material: Select a repair material that matches the belt’s properties, such as rubber patches for rubber belts.
- Apply Repair Material: For cuts and small holes, apply the repair material according to the manufacturer’s instructions, ensuring a secure bond.
- Vulcanize the Repair: For larger repairs, vulcanization may be necessary to restore the conveyor belt’s strength and flexibility. This process requires specialized equipment and expertise.
- Reinforce Edges: If the damage is near the belt’s edge, consider reinforcing the area to prevent further fraying or tearing.
- Test the Repair: After the repair, run the conveyor belt empty to ensure the repair holds under tension and the belt runs smoothly.
When to Repair vs. When to Replace Parts of the Conveyor Belt
The decision to repair or replace a damaged conveyor belt hinges on several factors, including the severity of the damage, the cost implications of both options, and the potential impact on operational downtime. A well-considered approach can help maintain the balance between operational efficiency and cost-effectiveness. Below is a table that outlines general guidelines for making informed decisions on whether to repair or replace parts of a conveyor belt based on the type of damage encountered.
Type of Damage | Repair | Replace |
---|---|---|
Small Cuts and Abrasions | Yes, if less than 10% of the belt width is affected. | No |
Large Tears or Holes | Yes, with professional vulcanization. | Yes, if the damage compromises more than 25% of the belt's width or length. |
Edge Wear | Yes, if minor and can be trimmed without affecting belt integrity. | Yes, if severe and causing misalignment or operational issues. |
Delamination | Yes, for small areas with surface vulcanization. | Yes, if widespread, affecting the belt's structural integrity. |
Severe Heat Damage | No, due to compromised material properties. | Yes |
Deep Structural Damage | No, as repairs may not restore original strength. | Yes |
Repeated Repairs in the Same Area | No, indicates underlying issues. | Yes |
Seized Rollers Damage | Yes, if rollers can be replaced or repaired. | Yes, if belt damage is extensive due to seized rollers. |
This table serves as a guideline for making informed decisions regarding conveyor belt maintenance. However, the specific circumstances of the damage, such as the belt’s age, the cost of downtime, and the availability of replacement parts, should also be considered. In many cases, consulting with a conveyor belt specialist can provide valuable insights into the most cost-effective and operationally efficient course of action.
Conveyor Belt Damage Repair and Maintenance
The maintenance of conveyor belts is a critical aspect of managing industrial and manufacturing operations efficiently. Proper care and timely repair are essential to prevent conveyor belt damage, which can lead to significant operational disruptions and financial losses. Implementing a set of best practices for the regular maintenance of conveyor belts not only helps in extending their lifespan but also ensures they operate at peak efficiency. Furthermore, being prepared with a set of scheduled maintenance and emergency repair tips can significantly mitigate the impact of any unforeseen issues. Below, we explore the foundational practices for maintaining conveyor belts and provide actionable tips for scheduled maintenance and emergency repairs.
Best Practices for Maintaining Conveyor Belts to Prevent Damage
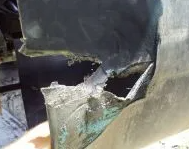
Maintaining conveyor belts in optimal condition requires a proactive approach to prevent damage and wear. These best practices are designed to ensure the longevity and reliability of your conveyor system.
- Routine Inspections: Regularly scheduled inspections are crucial for identifying potential issues before they lead to significant damage.
- Maintain Cleanliness: Keeping the conveyor belt and its environment clean prevents the build-up of materials that can cause damage.
- Proper Tensioning: Correct tensioning of the conveyor belt is essential to avoid slippage and excessive wear.
- Alignment Verification: Regular checks for alignment help prevent the belt from drifting, which can cause edge damage and uneven wear.
- Lubrication of Components: Proper lubrication of moving parts reduces friction, wear, and the risk of overheating.
- Load Management: Ensuring that the conveyor belt is not overloaded protects it from undue stress and strain.
- Educate Personnel: Training for operators and maintenance staff on proper conveyor belt care can prevent accidental damage.
- Environmental Considerations: Protecting the conveyor belt from adverse environmental conditions helps in preserving its integrity.
Scheduled Maintenance and Emergency Repair Tips
A well-planned maintenance schedule, complemented by effective emergency repair strategies, is key to minimizing downtime and maintaining operational efficiency.
- Maintenance Planning: Develop a maintenance schedule that includes regular checks and servicing based on the manufacturer’s recommendations and usage patterns.
- Spare Parts Inventory: Keeping a stock of essential spare parts ensures quick replacements and repairs, reducing downtime.
- Quality Repair Materials: Use only high-quality materials for repairs to ensure the durability and reliability of the conveyor belt.
- Expert Vulcanization Services: For serious damage, professional vulcanization can restore the conveyor belt’s structural integrity.
- Emergency Procedures: Establish clear emergency stop procedures to minimize damage in case of a malfunction.
- Documentation: Maintain detailed records of maintenance and repairs for historical reference and future planning.
- Performance Monitoring: Closely monitor the conveyor belt’s performance post-repair to ensure the issue has been effectively resolved.
- Immediate Misalignment Correction: Address any detected misalignment promptly to prevent further damage.
- Emergency Repair Kits: Equip your facility with emergency repair kits for quick fixes to minor issues.
- Specialist Consultation: For complex problems, consulting with conveyor belt specialists can provide insights into the most effective solutions.
Adopting these maintenance and repair practices ensures that conveyor belts remain in optimal condition, contributing to the smooth and efficient operation of your facility. Regular attention and proactive measures are indispensable for the long-term health and performance of conveyor systems.
Find the perfect conveyor belt – inquire now!
Innovative Solutions to Prevent Conveyor Belt Damage
The durability and efficiency of conveyor systems are paramount in industrial operations, where the goal is to minimize downtime and maintain high productivity levels. Conveyor belt damage is a significant concern that can disrupt operations and lead to costly repairs or replacements. To combat this issue, the industry has turned to innovative solutions, incorporating modern technologies and designs specifically aimed at reducing the incidence of wear and tear. These advancements not only extend the life of conveyor belts but also enhance their performance under various operational conditions. Furthermore, the development and implementation of modular plastic conveyor chains mark a transformative shift in conveyor technology, providing a robust alternative to traditional belt materials with distinct advantages. Let’s delve into the specifics of these modern solutions and the unique benefits offered by modular plastic conveyor chains.
Modern Technologies and Designs to Minimize Conveyor Belt Damage
The introduction of new technologies and thoughtful designs has revolutionized the way conveyor systems are constructed and maintained, directly addressing the root causes of conveyor belt damage.
- Introduction: Embracing cutting-edge technologies and innovative designs is essential for reducing conveyor belt damage. These advancements target the vulnerabilities of traditional systems, offering solutions that enhance durability and operational efficiency.
- Self-Healing Materials: Some modern conveyor belts are made from materials that can self-repair minor cuts and abrasions, significantly prolonging their lifespan.
- Advanced Monitoring Systems: Utilizing sensors and AI to monitor belt health in real-time allows for predictive maintenance, preventing damage before it occurs.
- Improved Material Composition: The development of belts with enhanced material compositions that are more resistant to abrasion, tearing, and extreme temperatures.
- Dynamic Alignment Features: Conveyor systems equipped with dynamic alignment features automatically adjust to maintain optimal belt positioning, reducing wear.
- Eco-friendly Materials: The use of sustainable, eco-friendly materials that are durable and less prone to damage, supporting green initiatives.
- Customizable Belt Surfaces: Tailoring the surface texture of conveyor belts to match the specific needs of the materials being transported reduces slippage and wear.
Introduction to Modular Plastic Conveyor Chains and Their Benefits
Modular plastic conveyor chains represent a leap forward in conveyor belt technology, offering a versatile and durable solution that addresses many of the limitations of traditional belts.
- Overview: Modular plastic conveyor chains have emerged as a game-changer in the industry, providing a flexible and robust alternative to conventional conveyor belts. Their unique design and material properties offer a range of benefits that enhance system reliability and efficiency.
- High Resistance to Damage: These chains are highly resistant to physical damage, including cuts, abrasions, and impacts, making them ideal for harsh operational environments.
- Ease of Maintenance and Repair: The modular design allows for easy replacement of individual links or sections, significantly reducing maintenance time and costs.
- Versatile Application: Their adaptable nature makes modular plastic chains suitable for a wide range of applications, including curved, inclined, and even spiral conveyors.
- Hygienic Solutions: The non-porous nature of plastic makes these chains particularly suitable for industries requiring high standards of hygiene, such as food and pharmaceuticals.
- Reduced Operational Noise: Plastic chains operate more quietly than metal counterparts, contributing to a better working environment.
- Cost Efficiency Over Time: While the initial investment may be higher, the long-term savings in maintenance and replacement costs render modular plastic conveyor chains a cost-effective choice.
By integrating these innovative solutions into conveyor systems, industries can significantly mitigate the risk of conveyor belt damage, ensuring smoother operations and longer service life. The shift towards modern technologies and the adoption of modular plastic conveyor chains highlight the industry’s commitment to improving efficiency and reducing operational challenges.
FAQs about Conveyor Belt Damage
Impact damage on conveyor belts occurs when materials being loaded onto the belt drop from a height, striking the belt with significant force. This type of damage is characterized by tears, cuts, or indentations on the surface or edges of the belt. It is a common issue in industries where heavy or sharp objects are handled, such as mining, quarrying, and other bulk material handling sectors. Impact damage not only compromises the structural integrity of the conveyor belt but also reduces its operational efficiency and lifespan. Over time, repeated impacts can weaken the belt to the point where it becomes susceptible to further damage and potential failure. Preventing impact damage involves using impact beds or plates at loading zones to absorb the force of falling materials, ensuring that the drop height is minimized, and materials are loaded gently onto the belt.
A conveyor belt can rip due to several factors, including sharp objects becoming lodged in the belt, heavy impact from material loading, improper belt splicing, and excessive belt tension. Sharp objects, either from the materials being conveyed or from external sources, can cut or pierce the belt as it moves. Heavy impacts, especially at loading zones, can cause significant tears or rips. Improperly spliced belts are weaker at the splice points, making them more prone to tearing under stress. Excessive tension overstretches the belt, reducing its resistance to tearing. To prevent rips, it’s crucial to regularly inspect the belt for sharp objects, ensure proper loading techniques, use correct splicing methods, and maintain appropriate belt tension.
The most common problem of belt conveyors is misalignment, where the belt drifts off its intended path, leading to uneven wear, material spillage, and potential damage to the belt and conveyor structure. Misalignment can be caused by several factors, including improper installation, worn or seized rollers, and uneven loading of materials. Other common issues include belt slippage, where the belt does not grip the pulleys properly; blockages from material build-up; and wear and tear from abrasive materials. Regular maintenance, including alignment checks, cleaning, and inspections, can help prevent these problems and ensure the conveyor operates efficiently.
Conveyor belts pose several hazards, including entanglement, where loose clothing, hair, or body parts can get caught in the moving parts; pinch points, where individuals can get trapped between the belt and rollers or pulleys; and falling objects from improperly secured materials. Additionally, improper operation or maintenance can lead to electrical hazards, fire risks from accumulated combustible dust or material spillage, and slip, trip, and fall hazards from spilled materials around the conveyor. To mitigate these risks, it’s essential to implement safety measures such as guards and barriers, emergency stop controls, regular maintenance, and safety training for operators and maintenance personnel. Safety protocols should comply with industry standards and regulations to protect workers and ensure safe operation.
Preventing conveyor belt damage is essential for maintaining the efficiency and longevity of conveyor systems. Here are several strategies to ensure your conveyor belts remain in good condition:
Regular Maintenance and Inspections
Routine Inspections: Regularly inspect the conveyor belt for signs of wear and tear, such as fraying, cracking, or unusual noises. Early detection of issues can prevent minor problems from becoming major repairs.
Scheduled Maintenance: Implement a maintenance schedule that includes checking the belt alignment, tension, and cleanliness. Ensure that all moving parts are lubricated and functioning correctly.
Proper Belt Tension and Alignment
Correct Tensioning: Ensure the belt is properly tensioned according to the manufacturer’s specifications. Over-tensioning can cause excessive wear, while under-tensioning can lead to slippage and misalignment.
Alignment: Regularly check and adjust the belt alignment. Misalignment can cause the belt to run off track, leading to edge wear and potential belt damage.
Use of Quality Components
Quality Rollers and Pulleys: Use high-quality rollers and pulleys that match the belt specifications. Worn or improperly installed components can cause uneven wear and damage to the belt.
Impact Beds and Skirting: Install impact beds at loading points to absorb shock and reduce belt wear. Proper skirting will prevent material spillage and reduce belt damage caused by material buildup.
Belt Cleaning and Material Handling
Regular Cleaning: Keep the belt clean by using scrapers and brushes to remove material buildup. Accumulated debris can cause abrasion and damage to the belt surface.
Proper Material Loading: Ensure materials are loaded evenly and centrally on the belt. Uneven loading can cause the belt to misalign and wear unevenly.
Environmental Considerations
Protection from Elements: Protect the conveyor belt from harsh environmental conditions such as extreme temperatures, UV radiation, and chemical exposure. Use covers or enclosures where necessary.
Dust Control: Implement dust control measures to prevent the accumulation of abrasive dust particles that can wear down the belt.
Conveyor systems can pose various hazards that may lead to injuries if proper safety measures are not in place. Here are some common injuries caused by conveyors:
Mechanical Injuries
Entanglement: Workers can become entangled in moving parts of the conveyor, such as rollers, belts, and pulleys. Loose clothing, jewelry, or long hair can get caught, leading to severe injuries.
Crushing and Pinching: Hands, fingers, and other body parts can be crushed or pinched between conveyor components, such as between the belt and rollers or at nip points where the belt contacts the rollers.
Shearing: Shearing injuries can occur when body parts come into contact with moving parts that cut or tear, such as infeed and discharge points or during maintenance.
Falls and Slips
Falls from Height: Workers can fall from elevated conveyor platforms or walkways. Proper guarding, handrails, and safety harnesses should be used to prevent such falls.
Slips and Trips: Spilled materials or improperly placed tools can create slip and trip hazards around conveyors. Regular housekeeping and clear walkways are essential to prevent these injuries.
Strain and Overexertion
Lifting Injuries: Manual handling of heavy or awkward items around conveyors can lead to strains, sprains, and musculoskeletal injuries. Proper lifting techniques and mechanical aids should be used to minimize these risks.
Repetitive Motion: Repetitive tasks associated with conveyor operations, such as sorting or packaging, can lead to repetitive strain injuries (RSIs). Ergonomic workstations and job rotation can help reduce these risks.
Chemical and Dust Exposure
Chemical Burns: Exposure to hazardous chemicals used in conveyor maintenance or cleaning can cause burns or respiratory issues. Proper personal protective equipment (PPE) and ventilation should be used.
Dust Inhalation: Inhalation of dust generated by conveyed materials can cause respiratory problems. Dust control measures, such as extraction systems and masks, should be implemented to protect workers.
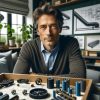
Jordan Smith, a seasoned professional with over 20 years of experience in the conveyor system industry. Jordan’s expertise lies in providing comprehensive solutions for conveyor rollers, belts, and accessories, catering to a wide range of industrial needs. From initial design and configuration to installation and meticulous troubleshooting, Jordan is adept at handling all aspects of conveyor system management. Whether you’re looking to upgrade your production line with efficient conveyor belts, require custom conveyor rollers for specific operations, or need expert advice on selecting the right conveyor accessories for your facility, Jordan is your reliable consultant. For any inquiries or assistance with conveyor system optimization, Jordan is available to share his wealth of knowledge and experience. Feel free to reach out at any time for professional guidance on all matters related to conveyor rollers, belts, and accessories.