4 Steps to Conveyor Belt Inspection Maintenance Checklist
Understanding the importance of regular conveyor belt inspection is crucial in sustaining efficient, safe, and reliable operations within a conveyor system framework. These inspections serve as the cornerstone for detecting early signs of wear and tear, alignment issues, and potential system malfunctions. By integrating a consistent conveyor belt inspection routine, facilities can significantly mitigate the risk of unexpected downtime and costly repairs.
Furthermore, conveyor belt inspections are not just about immediate problem-solving; they represent an investment in the long-term performance of the conveyor system. Regular inspection and timely maintenance can substantially decrease the likelihood of catastrophic failures that can halt production and incur significant expenses. As such, the cost benefits of embedding conveyor belt inspection into maintenance practices cannot be overstated—it extends the belt’s lifespan, improves system reliability, and preserves the seamless flow of operations, translating directly to enhanced profitability and operational continuity.
The Importance of Conveyor Belt Inspection
Routine maintenance checks are an incredibly important aspect in maintaining the full useful working life of your conveyor. A regular maintenance program will reduce the likelihood of break-down and costly downtime. Frequency of checks will depend on conveyor usage i.e. material being handled, hours worked per day etc. Checks are recommended at regular intervals depending on the amount of working hours that the conveyor is being used for.
A main feature in extending the life of your conveyor is thorough cleaning at regular intervals to prevent material build-up particularly around the feed and discharge points (good house-keeping is essential).
Thorough conveyor belt inspection is imperative for the sustenance of an efficient and long-lasting conveyor system. Regular assessments through precise inspection belt conveyor protocols ensure the vitality and enduring performance of the conveyor operation. To contextualize the fundamental role these inspections play, we must explore their function across five key aspects:
- Prevention of System Deterioration: Just as a chain is only as strong as its weakest link, a conveyor system’s effectiveness is jeopardized by the smallest imperfection in its belt. Conveyor belt inspections are critical in detecting these minute defects before they escalate into more significant concerns, ensuring the system does not suffer from preventable deterioration.
- Cost Efficiency and Resource Optimization: Inspecting conveyor belts can lead to the timely rectification of minor issues, which, if ignored, can result in costly repairs or replacements. Regular inspection not only prevents wastage of resources on emergency fixes but also optimizes the allocation of maintenance funds.
- Productivity and Throughput Maximization: The conveyor belt inspection process is integral to maintaining the high throughput required for production efficiency. By ensuring that the conveyor belt is in pristine working condition, inspection processes safeguard against bottlenecks and delays in production.
- Safety Assurance: The safety of personnel operating around conveyor systems is paramount. Conveyor belt inspections serve as a vital preventive measure against accidents that may arise from equipment malfunction, thereby protecting workers from potential hazards associated with belt rupture or misalignment.
- Compliance With Industry Standards: Regular conveyor belt inspections ensure that the equipment meets or exceeds the rigorous standards and regulations set by industry authorities. This compliance is critical for lawful operation and for maintaining the integrity of the manufacturing process.
Conveyor belt inspections are essential for identifying signs of wear and tear such as fraying edges, surface cuts, or abrasions that compromise belt integrity. They unearth alignment issues like conveyor belt mistracking which can cause uneven wear on the belt and the infrastructure, posing a significant risk for catastrophic system failure. Additionally, conveyor belt inspection identifies other potential problems, including debris build-up, improper tensioning, and damaged rollers, all of which can result in decreased belt life and efficiency. Incorporating Conveyor Belt Life Calculation into these inspections helps predict the longevity and optimal maintenance schedule for the belt, enhancing overall operational reliability.
Wear and tear on a conveyor belt, if neglected, can lead to the belt’s failure, which might bring the entire system to a standstill, incurring significant operational losses. Misalignment can not only damage the belt but also affect other components of the system, leading to additional repair costs and potential safety risks. By detecting these signs early during a conveyor belt inspection, issues can be rectified before they amplify and jeopardize system functionality, longevity, and safety. Regular inspection is the linchpin for a healthy conveyor system, preventing major failures before they occur, and ensuring uninterrupted production and maximum operational efficacy.
Preparing for Conveyor Belt Inspection: What You Need
Conducting a thorough conveyor belt inspection is an integral part of ensuring the longevity and efficiency of your conveyor system. The process requires meticulous planning and the right set of tools and documentation to be effective. Having a comprehensive approach to conveyor belt inspection not only aids in identifying potential issues before they escalate but also contributes to the overall preventive maintenance strategy. Here’s a detailed look at the essential tools and documentation necessary for carrying out a successful conveyor belt inspection.
Essential Tools and Documentation
To embark on a conveyor belt inspection, certain tools and documentation form the backbone of the procedure, ensuring that every aspect of the conveyor belt and system is thoroughly evaluated. The essentials include:
- Conveyor Belt Inspection Checklist PDF: This checklist is the primary tool for the inspection team. It provides a detailed list of all the items and components to be inspected. The checklist typically covers belt integrity, wear and tear, alignment, tension, the condition of the rollers, and the functionality of the conveyor system’s electrical components. This document is instrumental in ensuring that no aspect of the conveyor belt and system is overlooked during the inspection.
- Conveyor Maintenance Checklist PDF: Complementing the inspection checklist, the maintenance checklist focuses on the preventive measures and maintenance tasks that need to be performed regularly. This document helps in scheduling maintenance tasks based on the findings of the conveyor belt inspection, ensuring that each component receives the attention it requires for optimal performance and longevity.
- Conveyor Belt Maintenance PDF: This comprehensive guide provides detailed information on the standard practices for conveyor belt maintenance. It includes instructions on proper cleaning techniques, lubrication intervals, tensioning procedures, and replacement guidelines. This document serves as a reference manual for maintaining the conveyor belt in peak condition, helping to extend its service life and maintain system efficiency.
- Conveyor Inspection Documentation: Proper documentation of the inspection process and findings is crucial. This includes detailed reports on the condition of the conveyor belt and system components, any deficiencies or potential issues identified, and recommendations for corrective actions. Maintaining a record of each inspection helps in tracking the system’s health over time and planning future maintenance activities more effectively.
Upgrade your system with our efficient conveyor belts. Contact us immediately!
Implementation
Equipped with these pivotal tools and documentation, the inspection team can carry out a comprehensive conveyor belt inspection that not only identifies current issues but also anticipates future problems. By following the guidelines and checklists, technicians can ensure that each component of the conveyor system is evaluated and maintained appropriately, leading to enhanced system reliability, safety, and productivity.
Preparing for an inspection belt conveyor involves more than just understanding the technical aspects of the system; it requires a commitment to maintaining the highest standards of operation and safety. With the right tools and documentation in hand, this task becomes a structured process that significantly contributes to the conveyor system’s longevity and efficiency.
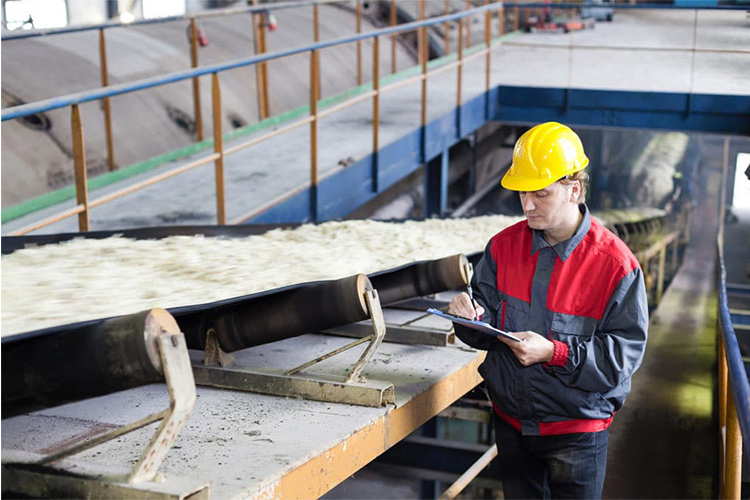
Step-by-Step Conveyor Belt Inspection Checklist
A systematic conveyor belt inspection is a cornerstone of maintaining the efficiency and longevity of the conveyor system. It encompasses a wide range of checks, from daily visual assessments to more detailed monthly analyses of critical components. Here is a detailed walkthrough of a typical inspection conveyor belt checklist, designed to ensure comprehensive evaluation and maintenance of the system.
Daily Visual and Physical Checks
- Surface Wear and Tear: Begin each day with a visual inspection of the conveyor belt’s surface. Look for signs of wear such as cuts, rips, or fraying edges. These defects can exacerbate over time, leading to belt failure.
- Alignment and Tracking: Check the alignment of the conveyor belt. Misalignment can cause uneven wear and potential damage to the belt and system. Look for signs of the belt running off to one side.
- Debris and Material Build-up: Inspect for accumulation of material on the belt and in the conveyor structure. Excessive build-up can affect belt movement and cause misalignment or unnecessary strain on the conveyor structure.
- Belt Tension: Physically check the belt tension to ensure it is neither too tight nor too slack. An improperly tensioned belt can lead to premature wear and efficiency loss.
Five Tips for Visual Inspections
Tips 1: Assess Belt Integrity
A belt visual inspection begins by looking to see if the belt is complete and if any surfaces are damaged, cracked, chipped, or gouged. Any joints in the belt should also be examined to determine that they are not separating or damaged. If the belt has cleats or sidewalls, these should be examined for signs of damage or wear and tear. The visual inspection should be extended to include the belt bed as well as drive rollers, pulleys, spindles and bearings, looking for worn or missing parts.
Tips 2: Verify That The Belt IsS Centered And Aligned on The Conveyor
Belts should be centered and aligned and not mis-tracking on the unit. Misaligned belts will be subject to accelerated wear, as well as reducing overall operating efficiency and possibly damaging other components of the conveyor. The visual inspection should also check the drive and guide components are properly installed and aligned.
Tips 3: Assess Belt Performance Under Load
A good visual inspection goes beyond merely examining a static belt to evaluating how the belt performs under load. A running belt may perform quite differently once a load is applied – the belt may mis-track, causing it to rub or abrade against other machine components. A loaded belt may also slip, causing accelerated wear and tear and reducing throughput.
Tips 4: Assess Belt Cleanliness
Sanitary belt conveyors used in food processing, pharmaceutical or other hygienic applications must be clean and free from pathogens and allergens. A visual inspection should look for signs of buildup on a belt, or the conditions which could entrap debris which could lead to the accumulation of contaminants. It is always a good idea to perform a visual inspection of a belt when the belt is being cleaned – this is the best time to identify signs of wear and tear that could trap harmful pathogens.
Tips 5: Determine How Frequently Visual Inspections Should Be Performed
The frequency with which visual inspections are carried out depends on a number of factors, including the frequency of operation (continuous or intermittent), the type of product being moved, the amount of load being carried, the cleaning regimen and chemicals used, and the operating environment, including the presence of temperature extremes, hot or cold. Frequent inspections at shorter intervals of time between inspections is preferable to inspections which are infrequent or haphazard.
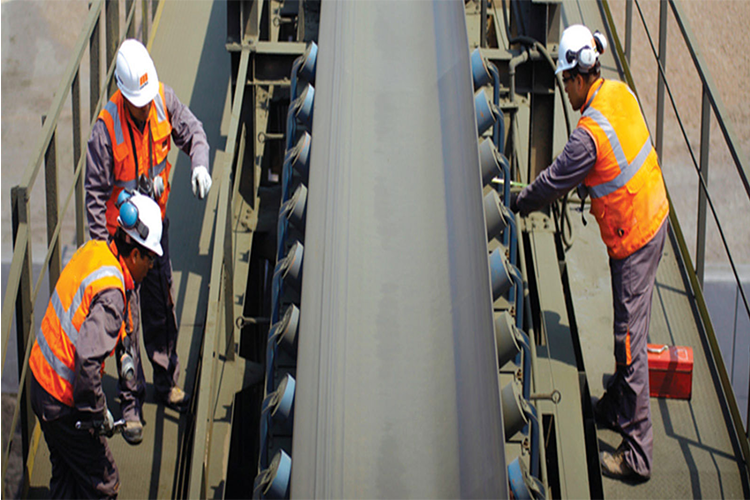
Weekly/Monthly Detailed Inspection of Critical Components
- Rollers and Pulleys: Inspect the rollers and pulleys for wear and tear, ensuring they rotate freely without excessive play or noise, which could indicate bearing failure. Check for build-up of material that could affect their operation.
- Bearings and Motors: Listen for unusual noises from bearings and motors, such as grinding or squealing. These sounds can indicate lubrication issues or impending failure. Perform a more detailed check if any issues are detected during daily operations.
- Electrical Components: Verify the condition of electrical wiring and control panels. Look for any exposed wires, signs of overheating, or corrosion. Ensure all safety guards and covers are in place and undamaged.
- Structural Components: Examine the frame and support structures for signs of wear, corrosion, or damage. Ensure all bolts and fasteners are securely tightened.
How to Effectively Perform Each Check
Visual Assessment: During visual checks, use a systematic approach, starting at one end of the conveyor and working your way to the other end. Use a flashlight to inspect hard-to-see areas and consider using a camera to document findings for subsequent analysis and comparison.
Physical Checks: When assessing physical aspects such as belt tension or roller movement, use appropriate tools like tension meters or infrared thermometers to check bearing temperatures. For parts that require manual intervention, ensure the conveyor is safely locked out to prevent accidental startup.
Component-Specific Inspection: For critical components like motors and bearings, use additional diagnostic tools where possible, such as vibration analyzers or ultrasound detectors, which can help identify issues not immediately apparent through visual or auditory inspections alone.
Documentation and Follow-Up: Document all findings from each inspection, noting any corrective actions taken or required. Schedule follow-up inspections or maintenance based on the severity of the issues identified, prioritizing those that pose the greatest risk to system operation.
By adhering to a thorough step-by-step inspection conveyor belt checklist, facilities can significantly enhance their operational efficiency, minimize downtime, and extend the lifespan of their conveyor system. Regular, disciplined inspections are key to identifying potential issues early and maintaining a safe, reliable, and productive operation.
6 Ways To Pass Conveyor Belt System Inspections
To pass conveyor belt system inspections thoroughly:
- Enhanced Maintenance: Implement a strict schedule that includes frequent and comprehensive maintenance checks to prevent and fix issues early.
- Detailed Record-Keeping: Maintain meticulous records of all maintenance actions, modifications, and checks performed on the system. This should include dates, actions taken, and individuals involved.
- Staff Training: Continuously train operational staff on the latest safety protocols and maintenance procedures to ensure everyone is knowledgeable about how to maintain and operate the conveyor system safely.
- Regular Cleaning Regime: Develop a regular cleaning schedule to keep the conveyor and surrounding area free from debris and potential hazards, which could compromise the system’s integrity and operation.
- Adherence to Standards: Ensure the system meets industry standards and regulations. Stay updated with any changes in legislation or guidelines relevant to conveyor operations.
- Proactive Pre-Inspection Reviews: Before an inspection, conduct a comprehensive review of the entire system to identify and correct any potential issues.
These detailed steps help ensure that your conveyor belt system remains in optimal condition and passes inspections with flying colors.
Conveyor Belt Inspection and Maintenance Schedule
Maintaining a well-defined conveyor belt maintenance schedule is crucial for the optimal performance and longevity of conveyor systems. This structured approach to maintenance not only helps in preventing unexpected breakdowns but also significantly increases the operational efficiency of conveyor belts. Here’s a comprehensive understanding of the significance of establishing a preventive maintenance schedule for conveyor belts from three essential aspects, followed by guidance on creating a maintenance plan that aligns with the manufacturer’s guidelines and operational workload.
Significance of Establishing a Preventive Maintenance Schedule
- Extended Lifespan of the Conveyor Belt: Regular maintenance plays a pivotal role in extending the overall lifespan of the conveyor belt. By identifying and rectifying minor issues such as misalignments, wear and tear, and lubrication needs on a scheduled basis, the likelihood of major failures that can shorten the belt’s life is greatly reduced.
- Operational Efficiency and Reliability: A conveyor belt running in top condition without unexpected stops ensures operational efficiency and reliability. Preventive maintenance schedules help in keeping the conveyor system’s performance consistent, which is crucial for meeting production targets and maintaining the flow of operations without costly downtime.
- Safety Enhancement: Conveyor systems are powerful machines that can pose significant safety risks if not properly maintained. Regular inspection and maintenance reduce the risk of accidents caused by equipment malfunction, protecting employees from potential injuries and ensuring compliance with safety regulations.
Creating a Conveyor Belt Maintenance Schedule
Based on the Manufacturer’s Guidelines
- Consult the Manufacturer’s Manual: Begin by thoroughly reviewing the conveyor system’s manual provided by the manufacturer. This document contains critical information about maintenance intervals, lubrication schedules, part replacement guidelines, and other specific maintenance recommendations.
- Identify Critical Components: Pay special attention to the manufacturer’s advice on critical components that require regular inspection and maintenance, such as motors, belts, rollers, and bearings. These components are often under significant stress and are crucial to the conveyor’s operation.
Factoring in Operational Workload
- Assess Operational Demands: Evaluate the operational workload of the conveyor system, including the number of operational hours per day, the type of materials being conveyed, and the environment in which the conveyor operates. For instance, conveyor systems in harsh environments or those handling abrasive materials may require more frequent inspections and maintenance.
- Customize the Maintenance Schedule: Using the manufacturer’s guidelines as a base, adjust the maintenance schedule to fit the unique operational demands of your system. Increase the frequency of inspections for high-use systems or those in demanding conditions. Schedule maintenance tasks during planned downtime to minimize operational disruption.
Detailed Maintenance Plan
- Daily Checks: Include visual inspections for signs of wear and damage, cleaning of critical areas to prevent material build-up, and verification of proper alignment and tension.
- Weekly to Monthly Reviews: Schedule more in-depth inspections of specific components such as bearings, motors, and electrical systems. Perform lubrication and adjustments as recommended by the manufacturer.
- Quarterly to Annual Audits: Plan for comprehensive audits of the conveyor system. These might include professional inspections, belt replacements, or upgrades to components that are showing signs of age or are near the end of their service life.
- Documentation and Continuous Improvement: Keep detailed records of all maintenance activities, including what was done, when, and by whom. Review this documentation regularly to identify trends, potential problem areas, and opportunities for improvements.
By diligently following a conveyor belt maintenance schedule that is tailored to the system’s specific needs and operational workload, organizations can ensure their conveyor systems operate efficiently, safely, and with minimal unplanned downtime. This proactive approach to conveyor belt inspection and maintenance is an essential strategy for any facility relying on these systems for their day-to-day operations.
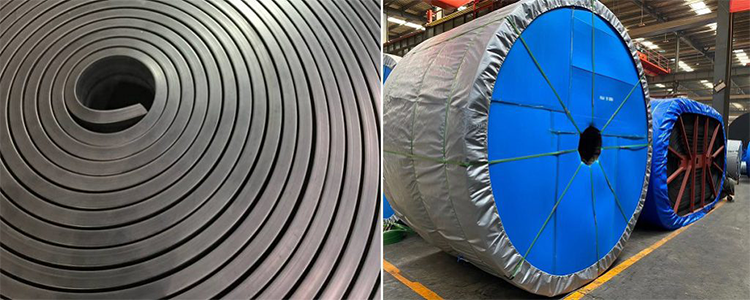
Conveyor Belt Maintenance Jobs: Ensuring Upkeep
The routine maintenance of conveyor belts is essential for the seamless operation of modern industrial and manufacturing workflows. Properly executed conveyor belt inspection and maintenance jobs not only ensure the longevity of the conveyor system but also significantly enhance safety and efficiency. This section provides an overview of common maintenance tasks necessary for keeping the conveyor belt in optimal condition and underscores the importance of trained maintenance personnel, along with strategies for structuring effective maintenance teams.
Common Conveyor Belt Maintenance Tasks
Regular maintenance of a conveyor belt system encompasses a variety of tasks, each critical to ensuring the performance and reliability of the system. These tasks typically include:
- Belt Inspection and Repair: The core of conveyor belt maintenance involves regular inspections for wear, tears, or misalignment. Any identified issues such as small tears or worn areas need immediate repair to prevent further damage.
- Cleaning: Effective cleaning is crucial to avoid material build-up that can alter the belt’s path and add unnecessary strain to the system. This includes removing debris from rollers, pulleys, and the belt itself.
- Lubrication: Proper lubrication of moving parts, such as rollers and bearings, ensures smooth operation and reduces wear. It’s important to use the correct type of lubricant as specified by the equipment manufacturer.
- Tension Adjustment: Maintaining the correct belt tension is critical. Too much tension can lead to excessive wear on belts and bearings, while too little tension can cause the belt to slip off the pulleys.
- Alignment Checks: Regularly checking the belt alignment prevents uneven wear and can significantly extend the life of the belt. Misalignment can also lead to material spillage and operational inefficiencies.
Importance of Trained Maintenance Personnel
The complexity of conveyor systems, with their myriad mechanical and electrical components, necessitates a high level of expertise for effective maintenance. Trained maintenance personnel are not only adept at identifying and rectifying potential issues before they escalate but are also essential for ensuring that maintenance tasks are carried out safely and in compliance with regulatory standards. In the absence of skilled personnel, seemingly minor issues can quickly evolve into costly downtimes or hazardous situations.
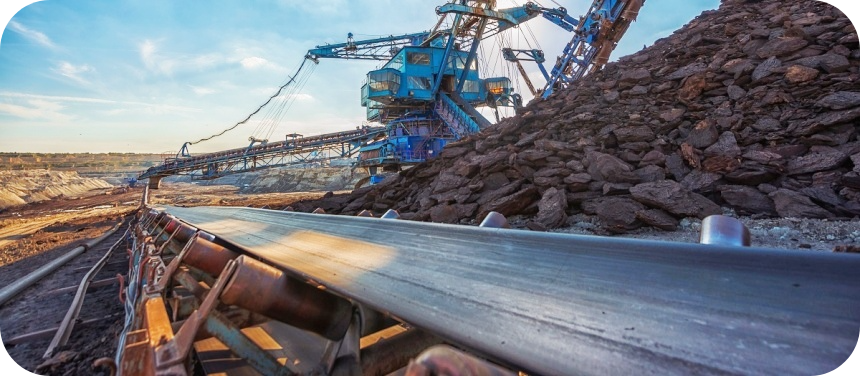
Structuring Effective Maintenance Teams
To ensure comprehensive coverage and timely execution of conveyor belt inspection reports and maintenance tasks, it’s crucial to structure your maintenance teams effectively. Here are some strategies:
- Skill Diversification: Ensure your team comprises individuals with a range of skills covering mechanical, electrical, and possibly even hydraulic and pneumatic systems. This diversity enables the team to address the wide variety of tasks involved in conveyor maintenance efficiently.
- Continuous Training: Regularly provide your team with training opportunities to keep them up-to-date with the latest maintenance techniques, safety standards, and innovations in conveyor technology. This investment in training not only improves the quality of maintenance but also enhances team morale and job satisfaction.
- Shift Scheduling: Depending on the scale of operations, consider organizing maintenance personnel into shifts that cover all operating hours, ensuring that expert help is always available to quickly address any emerging issues.
- Specialization vs. Generalization: For larger teams, consider developing specialized sub-teams focused on specific areas such as inspection, mechanical repairs, or electrical troubleshooting. For smaller teams, a more generalized approach where each member is capable of a broad spectrum of tasks might be more practical.
Regular and thorough conveyor belt maintenance is indispensable for the efficient and safe operation of conveyor systems. By prioritizing the development and structuring of skilled maintenance teams, organizations can significantly enhance their operational reliability, extending the lifespan of their conveyor systems and minimizing both downtime and safety risks.
Conveyor Belt Inspection Report: Keeping Records
Maintaining diligent records through a conveyor belt inspection report is an indispensable part of the conveyor belt maintenance strategy. These reports not only serve as a historical record of the conveyor system’s condition but also play a critical role in decision-making concerning maintenance, upgrades, and replacements. Documenting findings and actions taken during each conveyor belt inspection is crucial for several reasons, which we will explore from three main aspects. Furthermore, we will provide tips on maintaining accurate and useful inspection reports that can significantly benefit long-term system health analysis and planning.
Importance of Documenting Inspection Findings and Actions
- Facilitates Proactive Maintenance: Detailed records of conveyor belt inspections allow maintenance teams to track the progression of wear and other issues. By analyzing these trends over time, teams can predict potential failures and schedule preventive maintenance, thereby minimizing unexpected downtime and extending the lifespan of the conveyor belt.
- Ensures Regulatory Compliance and Safety: Many industries are subject to strict regulatory standards regarding equipment maintenance and operation, which includes conveyor systems. Having a thorough and up-to-date conveyor belt inspection report ensures that all necessary inspections and maintenance actions are documented, demonstrating compliance with safety regulations. This documentation is also vital in the event of a safety incident, as it provides evidence of due diligence in maintaining the equipment.
- Optimizes Budgeting and Planning: By regularly documenting the condition of the conveyor belt and its components, organizations can more accurately forecast maintenance and replacement costs. This insight is invaluable for budgeting purposes and helps in making informed decisions about investments in new equipment or upgrades to existing systems. Knowing when to repair or replace can result in substantial cost savings and ensure capital is allocated efficiently.
Tips for Maintaining Accurate and Useful Inspection Reports
- Standardize the Report Format: Use a standardized format for all conveyor belt inspection reports to ensure consistency and ease of reading. This format should include sections for basic information (date, inspector, location) as well as detailed findings, recommended actions, and deadlines for any necessary follow-up.
- Incorporate Visual Records: Whenever possible, include photographs or videos in the inspection reports. Visual records can provide clear evidence of the issues found and help in monitoring changes over time. They can also be useful for explaining the situation to non-technical stakeholders.
- Utilize Digital Tools: Leveraging digital tools and software for creating and storing conveyor belt inspection reports can greatly enhance their accuracy and accessibility. Many systems allow for real-time entry of findings, the inclusion of digital images, and even predictive analytics to forecast future maintenance needs.
- Involve Multiple Perspectives: Encourage inspectors to include their observations and recommendations in the reports. Different team members might notice different issues, so it’s beneficial to have a variety of perspectives. Additionally, involving operators and maintenance personnel in the review process can provide practical insights into the operational impact of any identified issues.
- Regular Review and Action: Ensure that inspection reports are not just filed away, but actively reviewed and acted upon. Schedule regular meetings to discuss recent reports, prioritize actions based on criticality, and allocate resources. Progress on addressing the items listed in the reports should be tracked and documented as well.
By meticulously documenting each conveyor belt inspection and maintaining organized, accessible reports, organizations can create a powerful tool for the continuous improvement of their conveyor systems. This level of attention to detail not only supports operational excellence but also contributes to a culture of safety, reliability, and efficiency.
Enhancing Conveyor Belt Inspection with Technology
As we delve deeper into the digital age, the power of technology to optimize operational processes continues to grow. The field of conveyor belt inspection is not immune to these advancements. Implementing technology into the conveyor belt inspection process can provide numerous benefits, making inspections more efficient, accurate, and safer. This provides significant advantages when planning maintenance and managing overall operations. Let’s explore how software, sensors, and other innovative technology advancements can revolutionize the conveyor belt inspection process.
Utilizing Inspection and Maintenance Management Software
The use of digital software specifically designed for conveyor belt inspection and maintenance management can greatly enhance inspection efficiency and accuracy. These programs offer functionality for real-time data input and storage, removing the need for paperwork and enabling instant accessibility of information to the entire team. Furthermore, they often provide a user-friendly interface with capabilities to annotate, categorize, and photograph findings directly into the system.
More advanced software solutions offer features such as predictive analytics, drawing on the collected inspection data to forecast maintenance needs and potential future issues. These predictive features allow teams to proactively address problems before they occur, significantly reducing unexpected downtime.
Harnessing the Power of Sensors
Sensors represent another significant technological breakthrough impacting the conveyor belt inspection process. Installing sensors on the conveyor system allows for real-time monitoring of various performance metrics such as temperature, vibration, belt speed, and alignment. This continuous stream of data can be analyzed to detect early signs of malfunction before they escalate into major issues.
For example, thermographic sensors can detect excessive heat in bearings that may indicate excessive friction and imminent failure. Similarly, vibration conveyor belt sensors can help identify misalignments or reduce belt tension. Incorporating sensor technology into conveyor belt inspection adds an automated layer of protection, offering a continuous monitoring solution that can significantly reduce the risk of malfunction and enhance system longevity.
Implementing Artificial Intelligence and Machine Learning
The integration of Artificial Intelligence (AI) and Machine Learning (ML) has the potential to take conveyor belt inspections to a new level. These technologies can process and analyze data from sensors and other inputs far more quickly and accurately than human, learning from each dataset to refine their predictive capabilities over time.
AI-powered visual inspection tools can be trained to perform visual checks of conveyor components for signs of wear, misalignment, or other potential issues. They can accurately identify even slight changes or inconsistencies that might be missed during manual inspections. This not only enhances the accuracy of inspections but also allows for the reallocation of human resources to higher-value tasks.
Leveraging Drones and Robotics
The use of drones and robotics in the conveyor belt inspection process presents a unique opportunity to enhance safety and efficiency. Drones equipped with high-resolution cameras or other sensor technology can perform visual inspections of difficult-to-reach or hazardous areas without risking worker safety. They can quickly cover large areas and provide real-time visual feedback to the operator.
Robotic technologies can also be used to perform regular maintenance tasks such as cleaning or adjusting components, ensuring consistent performance while minimizing human error and reducing the potential for workplace injuries.
Integrating technology into the conveyor belt inspection process delivers multiple benefits, notably enhanced efficiency, improved accuracy, and a safer work environment. Harnessing the potential of software, sensors, AI, drones, and robotics can transform maintenance practices, resulting in significant cost savings, improved operational uptime, and overall better management of conveyor belt systems.
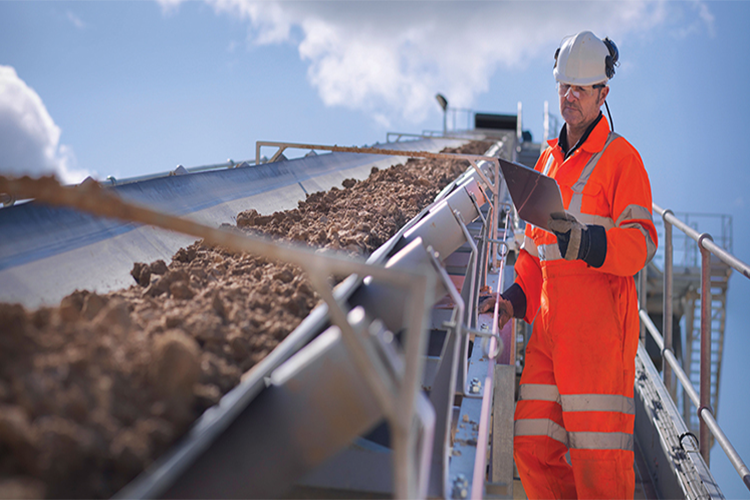
Common Pitfalls in Conveyor Belt Inspection and How to Avoid Them
Conveyor belt inspections are critical for ensuring the operational efficiency and safety of a conveyor system. However, the process is susceptible to various common pitfalls that can undermine its effectiveness, leading to potential equipment failure or safety hazards. Identifying these common mistakes and understanding how to avoid them can significantly improve conveyor belt maintenance practices. Let’s explore some typical problems encountered during conveyor belt inspection and provide solutions to prevent them.
Insufficient Frequency of Inspections
One of the most common mistakes is not conducting conveyor belt inspections frequently enough. Regular wear and tear, environmental factors, and operational loads can all contribute to the degradation of a conveyor belt over time. Insufficient inspection frequency can result in missed issues that escalate into major problems.
How to Avoid: Implement a structured inspection schedule based on the manufacturer’s recommendations and operational experience. High-use or critical conveyor systems may require more frequent inspections. Utilizing maintenance management software can help in setting reminders and keeping track of inspection timelines.
Overlooking Minor Issues
Another prevalent issue is the tendency to overlook minor problems during conveyor belt inspection, such as small tears, minor misalignments, or slight wear on components. While these may seem inconsequential at the moment, they can lead to more significant issues if not addressed promptly.
How to Avoid: Adopt a culture of ‘zero tolerance’ for any defects, regardless of size. Train inspection teams to understand the potential long-term impact of minor issues and the importance of addressing them quickly. Detailed checklists can help ensure no component is overlooked.
Lack of Detailed Documentation
Failure to document the findings of a conveyor belt inspection accurately and in detail can lead to repetitive issues and make tracking the maintenance history difficult. Adequate documentation is essential for understanding the evolution of conveyor belt conditions over time.
How to Avoid: Ensure that every conveyor belt inspection is followed by comprehensive documentation, including descriptions of issues found, photographs, and recommended actions. Utilize digital tools that facilitate easy recording and retrieval of inspection reports. This ensures all team members have access to up-to-date information.
Skilled Personnel Shortage
Conducting effective conveyor belt inspections requires a certain level of skill and expertise, which is lacking if personnel aren’t adequately trained. This can lead to misidentification of issues or overlooking potential problems.
How to Avoid: Invest in regular training for maintenance staff and inspectors. Consider certification programs that equip individuals with the necessary knowledge to perform thorough inspections. Additionally, leveraging experienced external professionals for periodic inspections can complement internal efforts and bring fresh perspectives to maintenance routines.
Achieve seamless operations with our top-tier conveyor belts. Get in touch today!
Relying Solely on Visual Inspections
While visual inspections are an essential component of conveyor belt maintenance, relying solely on them can result in missed internal damages or issues that are not visible on the surface, such as those within the rollers or hidden by the conveyor structure.
How to Avoid: Integrate the use of technology into the conveyor belt inspection process. Utilize sensors, drones, and other diagnostic tools to identify issues that are not apparent through visual inspection alone. Regular use of these technologies can detect problems early and prevent costly downtimes.
By recognizing and addressing these common pitfalls in conveyor belt inspection, organizations can significantly enhance the accuracy and effectiveness of their maintenance routines. Proactive and preventive maintenance based on thorough and regular inspections can prolong the life of conveyor systems, improve safety, and reduce operational costs.
FAQs about Conveyor Belt Inspection
The frequency of conveyor belt inspections depends largely on the usage, the environment, and the critical nature of the conveyor system. Conveyor belts used heavily or in extreme environmental conditions may require more frequent inspections than those used less intensively or in more benign environments.
As a rule of thumb, a daily visual inspection should be conducted to identify any visible wear, damage, or misalignment. More detailed inspections, such as checking the condition of rollers, pulleys, bearings, and other critical components, should be performed on a weekly or monthly basis, depending on operational requirements.
To ensure optimal operational efficiency and safety, it’s also recommended to adhere to the manufacturer’s recommendations for inspection and maintenance schedules. Furthermore, you should adjust your inspection schedule based on any issues identified in previous inspections, as these might indicate a need for more frequent checks.
Checking the quality of a conveyor belt involves a comprehensive inspection of its different aspects. At the most basic level, a visual inspection should be conducted. This includes checking the belt surface for any visible wear and tear, cuts or punctures, or signs of misalignment or slippage.
Beyond this, physical checks should be performed to evaluate the integrity of the belt. This implies checking the belt’s tension, ensuring it’s not too tight or too loose, which could lead to damage or ineffective operation. Moreover, rollers and pulleys should be inspected for any signs of wear or damage.
Technological tools can also aid in checking the belt’s internal condition. For example, a belt scanner can detect internal damage, belt thickness, and splice integrity. Lastly, flexible steel cords that are embedded in the belt for strength should be checked using a magnetic detector to ensure they are intact and not corroded.
A conveyor maintenance checklist should include all essential components and steps necessary
for efficient operation. Here are some items to include in your maintenance checklist:
Visual Inspection: Check the conveyor belt for visible signs of wear, tears, or seams. Inspect for signs of misalignment or slippage and check belt lacing.
Drive Chain and Sprockets: Check for proper alignment, worn sprockets, and correct chain tension.
Rollers and Pulleys: Check for wear, proper alignment, and any signs of wobble. Inspect bearings for signs of overheating or unusual noise.
Guarding: Ensure guards are in place and secure.
Structure: Inspect the overall condition of the conveyor structure, looking for corrosion, damage, or loose bolts.
Cleanliness: Check for material spillage and clean as necessary.
Electrical Systems: Check for proper functioning of motors, controls, and other electrical components.
Lubrication: Ensure all necessary parts are adequately lubricated according to the manufacturer’s specifications.
Conveyors should be tested to ensure that they are functioning properly and safely. The process typically begins with a visual inspection to check for visible signs of wear, damage, or misalignment. The test should then proceed to mechanical checks, such as:
Operational Test: The conveyor should be run for several cycles to confirm proper operation. The belt’s transition at the pulleys, its stability under load, and its stopping capability should be observed during these cycles.
Load Test: Place items on the conveyor and observe their movement. This test can reveal problems like belt slippage, inadequate tension, or other issues that may not be evident without a load.
Safety Test: All safety devices should be tested – including warning signals, alarms, emergency stops, and guards.
Electrical Test: Check all motor functions, digital controls, and other electrical components.
Final Inspection: After testing, all parts should be re-inspected. Any new issues identified during testing can then be addressed.
A well-maintained conveyor not only ensures operations run smoothly but also extends the useful lifespan of the equipment.
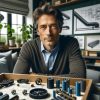
Jordan Smith, a seasoned professional with over 20 years of experience in the conveyor system industry. Jordan’s expertise lies in providing comprehensive solutions for conveyor rollers, belts, and accessories, catering to a wide range of industrial needs. From initial design and configuration to installation and meticulous troubleshooting, Jordan is adept at handling all aspects of conveyor system management. Whether you’re looking to upgrade your production line with efficient conveyor belts, require custom conveyor rollers for specific operations, or need expert advice on selecting the right conveyor accessories for your facility, Jordan is your reliable consultant. For any inquiries or assistance with conveyor system optimization, Jordan is available to share his wealth of knowledge and experience. Feel free to reach out at any time for professional guidance on all matters related to conveyor rollers, belts, and accessories.