Selecting Conveyor Belt for Stone Crusher Systems
The conveyor belt for stone crusher is a crucial component in the stone crushing industry, playing a vital role in enhancing efficiency and productivity. These conveyor belts are designed to handle the harsh conditions of stone crushing operations, ensuring the continuous flow of materials between various crushing stages. By automating material transport, the conveyor belt for stone crusher reduces labor intensity and minimizes operational downtime. This blog post delves into the features, benefits, and integration of conveyor belts in stone crushing applications, highlighting their significance in optimizing the entire crushing process.
What Is Conveyor Belt for Stone Crusher
Conveyor belts are critical components in the stone crushing process, transporting crushed stones and aggregates between different stages of processing. These belts must be robust, durable, and capable of handling the harsh conditions of the stone crushing environment. This detailed guide covers the essential aspects of conveyor belts used in stone crushers, including their features, applications, benefits, and maintenance.
Key Features and Specifications
Durability and Strength
- High Tensile Strength: Conveyor belts for stone crushers are made from materials that provide high tensile strength, such as reinforced rubber or fabric. This ensures they can handle the heavy loads and high impact forces typical in stone crushing operations.
- Abrasion Resistance: The belts are designed to resist wear and tear from abrasive materials like crushed stones, extending their service life.
Construction Materials
- Rubber: High-quality rubber is commonly used for its flexibility, durability, and resistance to impact and abrasion.
- Fabric Reinforcement: Layers of fabric (e.g., polyester, nylon) reinforce the rubber, providing additional strength and preventing elongation under heavy loads.
- Steel Cord Reinforcement: For applications requiring extra durability, steel cords are used to reinforce the belt, providing superior tensile strength and resistance to tearing.
Width and Length
- Customizable Sizes: Conveyor belts are available in various widths and lengths to meet specific needs. Common widths range from 18 inches (450 mm) to 72 inches (1800 mm), but custom sizes can be produced to fit particular requirements.
- Standard Lengths: The length of the belt depends on the conveyor system design and can range from a few meters to several kilometers.
Heat and Chemical Resistance
- Heat Resistant Belts: Designed for high-temperature environments, these belts can handle temperatures up to 200°C or more without degrading.
- Chemical Resistant Belts: Resistant to oils, chemicals, and other corrosive substances, making them suitable for environments where such materials are present.
Impact Resistance
- Robust Design: Conveyor belts are engineered to withstand the high impact forces exerted by falling stones and aggregates.
- Shock Absorption: The belts have shock-absorbing properties to reduce damage from heavy impacts, protecting both the belt and the conveyor system.
Benefits
Increased Efficiency
- Continuous Operation: Conveyor belts enable continuous material flow, reducing downtime and increasing overall efficiency.
- Automated Material Handling: Automation minimizes manual labor and boosts productivity by ensuring a steady supply of materials to crushers and screening equipment.
Cost-Effective
- Reduced Labor Costs: Automation reduces the need for manual handling, lowering labor costs.
- Lower Maintenance Costs: Durable construction and design reduce the frequency of repairs and maintenance.
Enhanced Safety
- Reduced Manual Handling: Minimizes the need for manual lifting and transporting of heavy materials, reducing the risk of injuries.
- Consistent Operation: Provides a steady and controlled movement of materials, reducing the likelihood of accidents.
Versatility
- Adaptable to Various Stages: Suitable for use in different stages of the crushing process, from primary to tertiary crushing.
- Customizable: Can be tailored to meet specific operational needs and constraints.
Conveyor belts for stone crushers are designed to handle the rigorous demands of transporting heavy and abrasive materials. By understanding their key features, applications, and benefits, and implementing proper maintenance practices, operations can enhance productivity, safety, and cost-effectiveness. Investing in high-quality, durable conveyor belts will ensure reliable performance in the demanding environment of stone crushing.
Construction of Conveyor Belt for Stone Crusher
The construction of conveyor belts for stone crushers is designed to handle the rigorous demands of transporting heavy and abrasive materials. These belts are built to be durable, efficient, and capable of withstanding harsh operational conditions. This guide details the essential components and construction features of conveyor belts used in stone crushing operations.
Key Components
Belt Material
- Rubber
- Composition: High-quality rubber compounds are commonly used due to their flexibility, impact resistance, and durability.
- Features: Rubber belts are resistant to abrasion, impact, and various environmental conditions.
- PVC (Polyvinyl Chloride)
- Composition: PVC belts are used for specific applications where chemical resistance is crucial.
- Features: They offer good resistance to oils and chemicals and are easier to clean.
Reinforcement Layers
- Fabric Reinforcement
- Materials: Polyester, nylon, or cotton fabrics are used to reinforce the belt, providing added strength and flexibility.
- Construction: Multiple layers of fabric are embedded within the rubber to enhance the belt’s tensile strength and prevent elongation.
- Steel Cord Reinforcement
- Materials: Steel cords are used for heavy-duty applications requiring high tensile strength.
- Construction: Steel cords run longitudinally through the belt, providing superior strength and durability for handling large loads.
Top Cover
- Abrasion-Resistant Rubber: The top cover is designed to withstand the abrasive nature of the materials being transported, such as crushed stones.
- Thickness: The thickness of the top cover can vary, typically ranging from 3mm to 10mm, depending on the application requirements.
Bottom Cover
- Smooth Rubber Surface: The bottom cover is usually made of rubber, designed to provide a smooth surface that minimizes friction with the conveyor structure.
- Thickness: The bottom cover’s thickness is generally less than the top cover, ranging from 1.5mm to 6mm.
Sidewalls and Cleats
- Sidewalls: Raised edges that prevent materials from spilling off the sides of the belt, especially useful in inclined or declined conveyors.
- Cleats: Transverse partitions attached to the belt surface to prevent material rollback, enhancing the belt’s ability to carry materials on steep inclines.
Edge Reinforcement
- Construction: Reinforced edges prevent the belt from fraying and provide additional strength to handle heavy loads and impacts.
Construction Process
Material Selection
- Choosing Rubber Compounds: Selecting the appropriate rubber compounds for the top and bottom covers based on the material being transported and environmental conditions.
- Reinforcement Material: Deciding between fabric or steel cord reinforcement depending on the load capacity and application requirements.
Layering Process
- Calendering: The rubber and fabric or steel cords are processed through a calendering machine to create a uniform layer.
- Layer Assembly: Multiple layers of rubber and reinforcement materials are assembled to form a cohesive belt structure.
Vulcanization
- Process: The assembled layers are subjected to heat and pressure in a vulcanization press to bond the materials together.
- Result: This process creates a durable, unified belt that can withstand high tensile loads and harsh conditions.
Finishing
- Edge Trimming: The edges of the belt are trimmed to ensure uniformity and prevent fraying.
- Surface Treatment: The surface may undergo additional treatments for improved abrasion resistance or to add special features like cleats or sidewalls.
Quality Control
- Inspection: Finished belts are inspected for defects, uniformity, and adherence to specifications.
- Testing: Belts may be tested for tensile strength, abrasion resistance, and other performance metrics to ensure they meet required standards.
Benefits of Well-Constructed Conveyor Belts
Durability
- Longer Lifespan: High-quality materials and construction methods extend the lifespan of the belt, reducing the need for frequent replacements.
- Resistance to Wear and Tear: Robust construction resists damage from abrasive materials and heavy loads.
Efficiency
- Smooth Operation: Properly constructed belts ensure smooth and efficient material transport, minimizing downtime and operational disruptions.
- Consistent Performance: High-quality belts maintain their performance over time, ensuring consistent material flow.
Safety
- Reduced Risk of Failures: Durable construction reduces the risk of belt failures, which can cause accidents and injuries.
- Improved Handling: Features like sidewalls and cleats enhance material handling, reducing the likelihood of spillage and associated hazards.
The construction of conveyor belts for stone crushers involves the careful selection of materials, precise layering, vulcanization, and rigorous quality control to ensure durability, efficiency, and safety. Understanding the key components and construction process is essential for selecting the right conveyor belt for specific stone crushing applications. High-quality, well-constructed conveyor belts contribute significantly to the productivity and reliability of stone crushing operations.
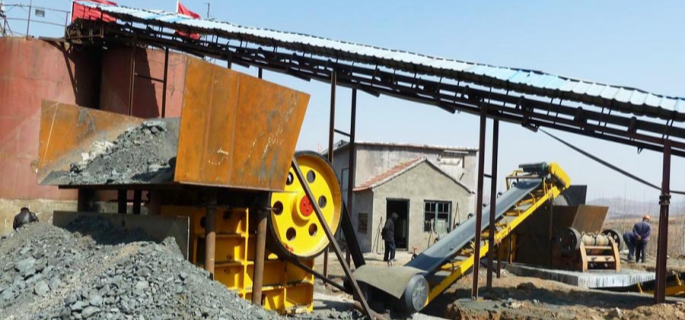
Applications of Conveyor Belt for Stone Crusher
Conveyor belts are essential in stone crusher operations, facilitating the transport of materials through various stages of crushing, screening, and final processing. Their versatility and efficiency make them indispensable in ensuring smooth, continuous, and automated material handling. This guide explores the diverse applications of conveyor belts in stone crusher operations.
Primary Crushing Stage
Feed Conveyor
- Function: Transports raw stones from the feed hopper to the primary crusher.
- Benefits:
- Automates the material feeding process, reducing manual labor.
- Ensures a steady flow of materials into the crusher, preventing overloading and interruptions.
Discharge Conveyor
- Function: Moves crushed material from the primary crusher to the secondary crushing stage.
- Benefits:
- Efficiently transports large quantities of material.
- Reduces the need for manual handling and increases throughput.
Secondary Crushing Stage
Transfer Conveyor
- Function: Connects the primary crusher to the secondary crusher, ensuring continuous material flow.
- Benefits:
- Maintains a seamless operation between crushing stages.
- Enhances productivity by ensuring a consistent supply of materials.
Screening Conveyor
- Function: Transports materials to and from screening equipment for size classification.
- Benefits:
- Allows for the separation of materials into different sizes for further processing or final use.
- Improves the efficiency of the screening process by automating material movement.
Tertiary Crushing and Final Processing
Stacking Conveyor
- Function: Used for stacking crushed materials into piles for further processing or storage.
- Benefits:
- Creates organized stockpiles of processed materials.
- Facilitates efficient use of storage space and easy retrieval of materials.
Loading Conveyor
- Function: Assists in loading the final product into transport vehicles or storage areas.
- Benefits:
- Speeds up the loading process, reducing downtime.
- Ensures safe and efficient transfer of materials to trucks or storage units.
Additional Applications
Recycling and Reprocessing
- Function: Conveyor belts are used to transport recycled materials back into the crushing process for reprocessing.
- Benefits:
- Enhances resource utilization by reprocessing waste materials.
- Reduces environmental impact by minimizing waste.
Mobile Crushing Units
- Function: Conveyor belts are integrated into mobile crushing units to transport materials within portable setups.
- Benefits:
- Provides flexibility and mobility in various crushing environments.
- Facilitates on-site processing and reduces transportation costs.
Dust Suppression Systems
- Function: Conveyor belts can be equipped with dust suppression systems to control dust generated during material transport.
- Benefits:
- Improves air quality and reduces health hazards for workers.
- Complies with environmental regulations and standards.
Industry-Specific Applications
Mining
- Application: Conveyor belts are used to transport ores and aggregates from mining sites to processing plants.
- Benefits:
- Enhances efficiency in moving large volumes of materials over long distances.
- Reduces operational costs and labor requirements.
Construction
- Application: Conveyor belts transport construction materials such as sand, gravel, and crushed stone on-site.
- Benefits:
- Streamlines material handling in construction projects.
- Increases productivity and reduces manual labor.
Quarrying
- Application: Conveyor belts move extracted materials from the quarry to the crushing plant.
- Benefits:
- Ensures efficient transport of raw materials for processing.
- Improves the overall efficiency of quarrying operations.
Conveyor belts are integral to the efficiency and effectiveness of stone crusher operations, serving various functions across different stages of material processing. Their applications in primary, secondary, and tertiary crushing, as well as in recycling and mobile units, highlight their versatility and importance. By automating material handling, reducing labor costs, and enhancing productivity, conveyor belts are essential for the successful operation of stone crushing plants in mining, construction, and quarrying industries. Investing in high-quality conveyor belts tailored to specific applications ensures optimal performance and operational efficiency.
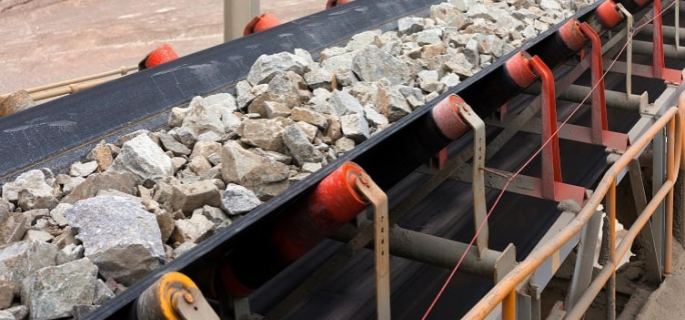
Conveyor Belt for Stone Crusher:In Detial
High-Performance RC Conveyor Belt 1:14
Material and Durability
The conveyor belt for stone crusher applications requires robust construction and durable materials to withstand the harsh conditions of the crushing environment. RC conveyor belts, particularly the 1:14 models, are engineered using high-grade materials like reinforced rubber and synthetic compounds. These materials are chosen for their exceptional resistance to wear and tear, ensuring the conveyor belt for stone crusher can endure the constant abrasion from sharp, heavy stones. For instance, companies like Bridgestone and Bando Chemical Industries utilize proprietary rubber formulations that provide superior tensile strength and flexibility, extending the belt’s lifespan significantly. This durability is crucial in reducing downtime and maintenance costs, allowing continuous and efficient stone crushing operations.
Load Capacity
The load capacity of the stone crusher conveyor belt is a critical factor in its performance. RC conveyor belts are designed to handle substantial loads, with capacities tailored to meet the demands of stone crushing operations. A typical RC conveyor belt 1:14 can support loads ranging from several hundred kilograms to multiple tons, depending on the specific requirements of the crushing plant. For example, Mitsuboshi Belting Ltd. offers belts capable of transporting up to 2000 kg per hour, ensuring that large volumes of stone can be moved efficiently from one processing stage to another. This high load capacity is essential for maintaining a steady workflow and optimizing the throughput of the crusher.
Speed and Efficiency
Speed and efficiency are paramount in the stone crushing industry, and the RC conveyor belt 1:14 is designed to enhance both. These conveyor belts operate at variable speeds, allowing precise control over material flow. The integration of advanced motor technologies, such as variable frequency drives (VFDs), enables the adjustment of belt speed to match the operational needs of the crusher. Companies like ContiTech and Fenner Dunlop provide conveyor belts that can achieve speeds up to 5 meters per second, ensuring rapid and consistent material transport. This high-speed capability reduces bottlenecks and increases the overall productivity of the stone crushing process.
RC Crusher Integration
Compatibility
The seamless integration of RC crushers with the conveyor belt for stone crusher is vital for efficient operations. RC crushers are designed with specific features that enable smooth interfacing with conveyor systems. For instance, the discharge heights and angles of RC crushers are engineered to align perfectly with the conveyor belt, ensuring a smooth transfer of crushed materials. Brands like Terex and Metso offer crushers with adjustable discharge settings that can be fine-tuned to match the specifications of the conveyor belt, preventing material spillage and ensuring a continuous flow.
Operational Efficiency
Integrating an RC crusher with a stone crusher conveyor belt significantly optimizes the crushing process. This integration allows for automated and synchronized operations, where the crusher and conveyor belt work in tandem to achieve maximum efficiency. By using sensors and automation controls, the material feed rate can be regulated to prevent overloading the crusher, thereby reducing wear and tear. For example, Sandvik’s automated control systems enable real-time adjustments to the conveyor speed based on the crusher’s throughput, ensuring optimal performance and reducing operational costs.
Maintenance and Upkeep
Maintaining both the RC crusher and the conveyor belt for stone crusher is crucial for long-term performance. Regular inspections and preventative maintenance routines help in identifying potential issues before they escalate. Lubrication of moving parts, checking for belt tension, and ensuring the alignment of the conveyor belt are some of the key maintenance tasks. Companies like Bridgestone offer maintenance services and tools designed specifically for conveyor belts used in stone crushing, providing kits that include everything from replacement parts to specialized lubricants. Implementing these maintenance practices not only prolongs the lifespan of the equipment but also minimizes unexpected downtimes, ensuring a smooth and efficient operation.
Conveyor Belt for Stone Crusher: Scaling Up with 1:14 Scale Conveyor
Design and Specifications
Scale Model Design
The design of the stone crusher conveyor belt, particularly the 1:14 scale model, is meticulously crafted to meet the rigorous demands of stone crushing operations. These conveyors are built with high-quality materials to ensure durability and longevity. The 1:14 scale design provides a realistic and functional model that replicates the actual working conditions of full-sized conveyors. Companies like Mitsuboshi Belting Ltd. focus on precision engineering to create scale models that accurately represent the operational capabilities of their larger counterparts. The design includes reinforced frames, robust rollers, and heavy-duty belts that can handle the constant impact and abrasion from stone materials.
Technical Specifications
The technical specifications of the conveyor belt for stone crusher, especially the 1:14 scale model, are designed to optimize performance and efficiency. Typically, these conveyors have dimensions that are proportional to their full-sized versions, ensuring they can be effectively used in simulation and testing environments. For instance, a 1:14 scale conveyor might feature a belt width of 50 mm, a length of 2 meters, and be powered by a 5.5 kW motor. These specifications allow the conveyor to move significant amounts of stone material, mimicking the capabilities of industrial conveyors. The belt speed can vary from 0.5 to 1.5 meters per second, providing flexibility in operation to match the needs of the stone crushing process.
Customization Options
Customization is a critical aspect of the stone crusher conveyor belt, allowing it to meet specific operational requirements. Manufacturers such as ContiTech and Fenner Dunlop offer a range of customization options for their 1:14 scale conveyors. These options include adjustable belt widths, variable belt speeds, and different motor configurations to suit various crushing environments. For example, clients can choose between rubber or PVC belts depending on the nature of the stone material being processed. Additionally, the conveyor frames can be customized to fit unique installation sites, ensuring seamless integration with existing stone crushing equipment. These customization capabilities enhance the versatility and efficiency of the conveyor system, making it an indispensable component of modern stone crushing operations.
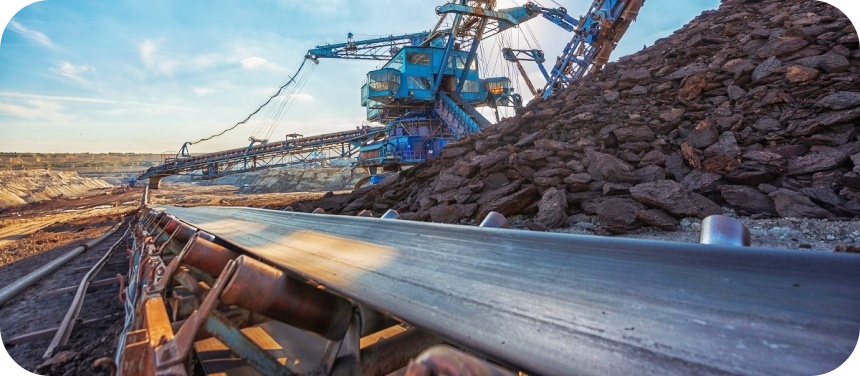
Application and Efficiency
Versatile Applications
The 1:14 scale conveyor belt for stone crusher excels in a wide range of applications within the stone crushing industry. Its versatile design allows it to be used in different stages of the crushing process, from primary crushing to tertiary crushing. For instance, in primary crushing, the conveyor belt efficiently transports large boulders from the crusher to the next processing stage. In secondary and tertiary crushing, the conveyor handles smaller, more refined materials. Companies like Terex and Metso have successfully integrated these scale conveyors into their stone crushing plants, demonstrating their capability to handle various types of stone, including granite, limestone, and basalt. This versatility makes the 1:14 scale conveyor an essential tool for optimizing crushing operations and improving overall plant efficiency.
Efficiency Metrics
The efficiency of the conveyor belt for stone crusher is measured through various metrics, including throughput rates and energy consumption. High throughput rates are achieved through the conveyor’s ability to move large volumes of stone material quickly and consistently. For example, a well-designed 1:14 scale conveyor can achieve throughput rates of up to 500 tons per hour, significantly enhancing the productivity of the stone crushing operation. Energy consumption is another critical metric, with efficient conveyor designs incorporating energy-saving technologies such as variable frequency drives (VFDs). These drives allow for the precise control of motor speed, reducing energy consumption during low-load conditions. Companies like Sandvik have implemented these technologies in their conveyor systems, resulting in reduced operational costs and improved energy efficiency. The combination of high throughput and low energy consumption makes the 1:14 scale stone crusher conveyor belt a highly efficient solution for modern stone crushing plants.
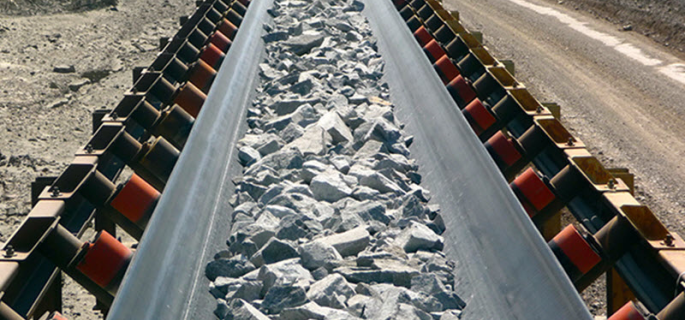
Conveyor Belt for Stone Crusher: RC Model Design Considerations
Engineering and Construction
RC Model Engineering
Designing an RC model for a conveyor belt for stone crusher involves several engineering challenges that require innovative solutions. The scale model must accurately replicate the performance and durability of full-sized industrial conveyors while being compact and lightweight. Engineering teams from companies like Bridgestone and ContiTech focus on miniaturizing components without compromising on strength or functionality. One major challenge is ensuring that the smaller motors and gears can handle the significant torque and load stresses associated with stone crushing. Advanced conveyor belt CAD software and finite element analysis (FEA) are used to simulate and optimize the design, addressing potential stress points and ensuring structural integrity. This meticulous engineering process ensures that the RC conveyor model can perform reliably under demanding conditions.
Material Selection
The choice of materials for the stone crusher conveyor belt is crucial for both durability and performance. In RC model design, selecting materials that offer a balance between strength and weight is essential. High-strength polymers and reinforced composites are often used for the frame and structural components. For the conveyor belt itself, materials like PVC or rubber with embedded nylon threads are preferred due to their flexibility and wear resistance. Companies like Mitsuboshi Belting Ltd. use advanced rubber compounds that provide excellent abrasion resistance and tensile strength, ensuring the belt can handle the abrasive nature of crushed stones. Additionally, corrosion-resistant materials are used for parts exposed to dust and moisture, enhancing the model’s longevity.
Prototype Testing
Prototype testing is a critical phase in the development of an RC conveyor belt for stone crusher. This process involves rigorous testing under simulated operational conditions to validate the design and performance. For instance, prototypes are subjected to continuous load tests to ensure they can handle the weight and impact of stone materials over extended periods. Vibration and shock tests are also conducted to assess the durability of the components and the overall stability of the conveyor system. Companies like Terex and Metso conduct field tests using actual stone crushing setups to gather real-world performance data. Feedback from these tests is used to refine the design, addressing any weaknesses and improving the overall reliability and efficiency of the RC model.
Innovative Features
Advanced Features
Modern RC models of conveyor belts for stone crushers are equipped with a range of advanced features that enhance their functionality and ease of use. One significant innovation is the integration of remote control capabilities, allowing operators to adjust the conveyor speed and direction from a distance. This feature is particularly useful in hazardous environments where direct manual control is impractical. Automated adjustments are another innovative feature, with sensors and control systems that can dynamically alter the conveyor’s operation based on the load and flow of materials. For example, sensors can detect blockages or overloads and automatically adjust the belt speed to prevent damage and maintain efficiency. Companies like Sandvik incorporate these advanced features into their RC models, providing users with greater control and flexibility.
User Experience
User-friendly design is a key consideration in the development of RC conveyor belts for stone crushers. The aim is to make the operation as intuitive and straightforward as possible. Simple interface controls, clear indicator lights, and ergonomic remote control units are some of the design elements that enhance the user experience. Additionally, quick-release mechanisms and modular components make maintenance and repairs easier, reducing downtime. Practical examples include easy-to-access tensioning systems that allow users to quickly adjust belt tension without specialized tools. Companies like Fenner Dunlop prioritize user feedback during the design process, ensuring that the final product meets the practical needs of operators in the field. This focus on user experience ensures that the RC stone crusher conveyor belt is not only effective but also convenient and efficient to operate.
Conveyor Belt for Stone Crusher: RC Screening Plant Integration
Design and Functionality
Screening Plant Design
The design of RC screening plants is crucial for their effective integration with the conveyor belt for stone crusher. These screening plants are engineered to handle the rugged conditions of stone crushing operations while maintaining high efficiency and reliability. Key design elements include robust frames made from high-strength steel, which can withstand the vibrations and impacts typical in these environments. The screens themselves are often made from durable materials like manganese steel or polyurethane, which offer excellent wear resistance. Companies such as Terex and Metso focus on creating modular designs that can be easily adapted to different stone sizes and types, ensuring versatility in various crushing applications. For example, Terex’s Cedarapids line of screening plants is renowned for its high-performance and durability, capable of handling large volumes of material with ease.
Functional Integration
Functional integration between RC screening plants and the conveyor belt for stone crusher is essential for a seamless crushing process. The screening plant is typically placed downstream of the crusher, where it can efficiently separate the crushed material into different size fractions. This integration allows for continuous material flow, reducing the need for manual handling and improving overall efficiency. The conveyor belt for stone crusher plays a pivotal role in this setup by transporting the screened material to the next stage of processing or storage. Advanced control systems, such as the IC™ process control system developed by Metso, enable synchronized operation between the crusher, conveyor, and screening plant, ensuring optimal performance and minimal downtime.
Efficiency Gains
The integration of a screening plant with a conveyor belt for stone crusher offers significant efficiency gains. By automating the material sorting process, the system can handle higher volumes of stone with greater accuracy and speed. This not only increases the throughput of the crushing plant but also enhances the quality of the final product by ensuring consistent particle size. For instance, studies have shown that integrated systems can improve processing capacity by up to 30%. In a specific case, Kleemann’s MOBISCREEN series screening plants, when integrated with conveyor systems, demonstrated a substantial increase in efficiency, reducing the need for manual sorting and improving overall production rates. Furthermore, the automated nature of the system reduces the need for manual intervention, leading to lower labor costs and reduced risk of human error.
Operational Synergy
Workflow Optimization
Combining RC screening plants with the conveyor belt for stone crusher optimizes the workflow of the crushing operation. The automated transport of materials between the crusher and the screening plant ensures a continuous and efficient process. This setup minimizes bottlenecks and maximizes the utilization of the crushing equipment. Additionally, real-time monitoring and adjustments can be made to the conveyor speed and screen settings, allowing the system to adapt to varying material conditions. Companies like Bando Chemical Industries provide advanced monitoring systems that track the performance of the conveyor belt and screening plant, offering insights that can be used to further optimize operations. For example, Bando’s monitoring systems have been shown to improve operational efficiency by up to 20% by providing real-time data and analytics.
Performance Metrics
Measuring the performance improvements from integrating screening plants with conveyor belts involves various metrics. Key performance indicators include throughput rate, energy consumption, and product quality. Throughput rate measures the volume of material processed per hour, which is significantly enhanced by the integrated system. Energy consumption is monitored to ensure the system operates efficiently, with lower power requirements translating to cost savings. Product quality is assessed by analyzing the consistency of the screened material sizes. According to data from Fenner Dunlop, integrated systems can reduce energy consumption by up to 20% while maintaining high product quality standards. For instance, a study showed that a properly integrated screening and conveyor system in a stone crushing plant could handle up to 500 tons per hour, significantly boosting productivity.
Case Studies
Real-world examples demonstrate the effectiveness of integrating screening plants with conveyor belts for stone crusher operations. In a quarry in Texas, an integrated system from Metso, which included an advanced screening plant and conveyor belt, resulted in a 25% increase in processing capacity and a 15% reduction in operational costs. Similarly, a stone crushing plant in Germany using equipment from Terex reported a 30% improvement in throughput and significant reductions in downtime due to the automated system’s reliability. Another notable example is from a Japanese company, Okada, which implemented an integrated conveyor and screening system that improved material handling efficiency by 40%, highlighting the transformative potential of this approach. These case studies highlight the tangible benefits of combining screening plants with conveyor belts, showcasing their potential to transform stone crushing operations.
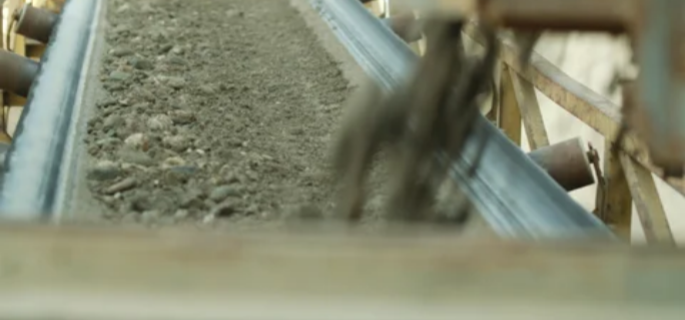
Leading Crusher Conveyor Belt Manufacturers
Crusher conveyor belts are essential components in stone crushing operations, providing the means to transport materials through various stages of processing. Several leading manufacturers specialize in producing high-quality, durable conveyor belts designed to withstand the rigorous demands of the stone crushing industry. This guide highlights some of the top crusher conveyor belt manufacturers known for their reliability and innovation.
Top Crusher Conveyor Belt Manufacturers
GRAM Conveyor
- Overview: A leading manufacturer of conveyor belts with a reputation for quality and innovation.
- Products: Offers a comprehensive range of conveyor belts designed for various applications.
- Features: Superior wear resistance, high tensile strength, and custom solutions for specific needs.
- Applications: Mining, construction, and material handling.
Continental AG (ContiTech)
- Overview: Continental AG, through its ContiTech division, is a global leader in rubber and plastics technology.
- Products: Offers a wide range of conveyor belts designed for heavy-duty applications, including stone crushers.
- Features: High tensile strength, excellent abrasion resistance, and heat-resistant options.
- Applications: Suitable for various industries, including mining, quarrying, and construction.
Fenner Dunlop
- Overview: Part of the Michelin Group, Fenner Dunlop has a rich history of providing conveyor solutions for over 150 years.
- Products: Known for their durable and high-performance conveyor belts, including fabric and steel cord options.
- Features: High durability, low elongation, and resistance to wear and impact.
- Applications: Ideal for demanding applications in mining and quarrying.
Goodyear (Veyance Technologies Inc.)
- Overview: Known for its innovative rubber products, Goodyear conveyor belts are reliable and high-quality.
- Products: Provides a variety of conveyor belts suitable for heavy-duty applications in stone crushing.
- Features: Durable, abrasion-resistant, and designed to handle high loads and impacts.
- Applications: Mining, aggregate, and industrial material handling.
Habasit
- Overview: A global manufacturer specializing in high-quality conveyor belts with innovative solutions.
- Products: Offers a wide range of conveyor belts, including those designed for heavy-duty and harsh environments.
- Features: Strong, flexible, and resistant to wear and tear.
- Applications: Food processing, logistics, packaging, and manufacturing.
Sempertrans (Semperit AG Holding)
- Overview: A division of Semperit Group, Sempertrans is known for its robust and durable conveyor belts.
- Products: Provides a broad range of belts, including textile and steel cord belts suitable for stone crushing.
- Features: High strength, excellent resistance to abrasion, and long lifespan.
- Applications: Mining, cement, steel, and power plants.
Phoenix Conveyor Belt Systems (Part of Continental AG)
- Overview: Specializes in high-performance conveyor belts for various industrial applications.
- Products: Offers a range of belts, including steel cord, textile, and special-purpose belts.
- Features: Superior strength, flexibility, and durability.
- Applications: Mining, tunneling, cement, and steel industries.
Dunlop Conveyor Belting
- Overview: Renowned in Europe for its high-quality conveyor belts designed for various industrial applications.
- Products: Known for their durability and performance, including belts for high-temperature and oil-resistant applications.
- Features: Excellent abrasion resistance, high tensile strength, and long service life.
- Applications: Mining, agriculture, and heavy industry.
Considerations for Choosing a Conveyor Belt Manufacturer
Quality and Durability
- Material Quality: Ensure the manufacturer uses high-quality materials for durability and longevity.
- Construction: Look for belts with strong reinforcement layers (fabric or steel cord) to handle heavy loads and harsh conditions.
Customization Options
- Tailored Solutions: Choose manufacturers that offer custom solutions to meet specific operational needs and constraints.
- Special Features: Consider belts with special features like heat resistance, chemical resistance, and anti-abrasive properties.
Reputation and Experience
- Industry Expertise: Select manufacturers with a proven track record and extensive experience in producing conveyor belts for the stone crushing industry.
- Customer Reviews: Look for positive reviews and testimonials from other businesses in the same industry.
Technical Support and Warranty
- After-Sales Service: Ensure the manufacturer provides comprehensive after-sales support, including technical assistance and maintenance advice.
- Warranty: Check for warranties that cover manufacturing defects and premature failures.
Cost and Value
- Pricing: Compare prices, but also consider the value offered in terms of quality, durability, and support.
- Total Cost of Ownership: Evaluate the overall cost, including initial purchase price, maintenance, and potential downtime costs.
Selecting the right manufacturer for conveyor belts in stone crusher operations is critical for ensuring efficiency, durability, and cost-effectiveness. Leading manufacturers like Continental AG, Fenner Dunlop, Bridgestone, and others provide high-quality, reliable conveyor belts designed to meet the demanding needs of the stone crushing industry. By considering factors such as material quality, customization options, reputation, and support, businesses can make informed decisions and invest in conveyor belts that enhance their operational performance and longevity.
Your ideal conveyor belts await. Contact us for details!
Maintenance Tips of Conveyor Belt for Stone Crusher Operations
Regular maintenance of conveyor belts is crucial to ensure the efficient and uninterrupted operation of stone crusher systems. Proper maintenance practices help in prolonging the lifespan of the belts, preventing unexpected breakdowns, and enhancing overall productivity. This guide provides essential maintenance tips for conveyor belts used in stone crusher operations.
1. Regular Inspections
- Visual Inspections
- Frequency: Conduct visual inspections daily or weekly.
- What to Check: Look for signs of wear, tears, misalignment, or any visible damage to the belt surface and edges.
- Benefits: Early detection of issues can prevent minor problems from becoming major failures.
- Detailed Inspections
- Frequency: Perform detailed inspections monthly or quarterly.
- What to Check: Inspect the condition of splices, belt tension, pulley alignment, and the state of the belt surface.
- Benefits: Thorough inspections help in identifying less obvious issues that might affect belt performance.
2. Cleaning
- Regular Cleaning
- Frequency: Clean the belt surface and surrounding areas weekly or as needed.
- What to Clean: Remove debris, dust, and material buildup from the belt and rollers.
- Benefits: Clean belts run more efficiently, and removing buildup prevents additional wear and potential belt slippage.
- Belt Scrapers and Cleaners
- Installation: Use belt scrapers and cleaners to continuously remove material buildup during operation.
- Benefits: Keeps the belt surface clean, reducing maintenance needs and preventing material from causing wear.
3. Lubrication
- Bearing and Pulley Lubrication
- Frequency: Lubricate bearings and pulleys according to the manufacturer’s recommendations, typically monthly.
- What to Use: Use lubricants specified by the manufacturer to ensure compatibility.
- Benefits: Proper lubrication reduces friction and wear, ensuring smooth operation and extending component life.
4. Belt Alignment and Tension
- Regular Alignment Checks
- Frequency: Check belt alignment weekly or as needed.
- What to Check: Ensure the belt runs straight and is centered on the pulleys.
- Benefits: Proper alignment prevents uneven wear, reduces the risk of belt slipping off track, and enhances operational efficiency.
- Adjusting Belt Tension
- Frequency: Check and adjust belt tension monthly or as required.
- What to Look For: Ensure the belt is not too tight or too loose; it should have adequate tension for optimal performance.
- Benefits: Correct tension prevents slippage, reduces wear, and prolongs the life of the belt and pulleys.
5. Splice and Repair Maintenance
- Splice Inspections
- Frequency: Inspect belt splices monthly or as needed.
- What to Check: Look for signs of splice separation, cracking, or wear.
- Benefits: Maintaining healthy splices ensures the belt’s structural integrity and prevents unexpected breaks.
- Timely Repairs
- When to Repair: Repair any minor tears or damage immediately upon detection.
- How to Repair: Use appropriate repair methods and materials recommended by the belt manufacturer.
- Benefits: Prompt repairs prevent damage from worsening and extend the belt’s service life.
6. Roller and Pulley Maintenance
- Roller Inspections
- Frequency: Inspect rollers monthly or as needed.
- What to Check: Ensure rollers are free of debris, spinning freely, and not showing signs of excessive wear or damage.
- Benefits: Well-maintained rollers reduce belt friction and wear, improving overall efficiency.
- Pulley Maintenance
- Frequency: Inspect pulleys monthly or as needed.
- What to Check: Check for alignment, wear, and build-up of material on pulleys.
- Benefits: Proper pulley maintenance ensures efficient belt movement and reduces the risk of belt damage.
7. Monitoring and Documentation
- Regular Monitoring
- What to Monitor: Keep track of belt performance, any unusual noises, vibrations, or changes in belt tracking.
- Benefits: Continuous monitoring helps in early detection of issues and timely intervention.
- Documentation
- What to Document: Maintain records of all inspections, maintenance activities, repairs, and replacements.
- Benefits: Detailed documentation helps in tracking belt health, planning maintenance schedules, and improving operational strategies.
Effective maintenance of conveyor belts in stone crusher operations is essential for ensuring their reliability and efficiency. Regular inspections, cleaning, proper lubrication, maintaining correct alignment and tension, timely repairs, and consistent monitoring are key practices to keep conveyor belts in optimal condition. Implementing these maintenance tips will help in minimizing downtime, reducing repair costs, and enhancing the overall productivity of the stone crushing operations.
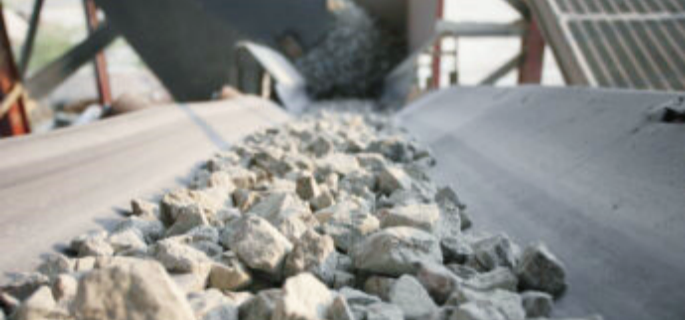
FAQs about Conveyor Belt for Stone Crusher
A conveyor belt for stone crusher is a critical component used in the stone crushing industry to transport materials between various stages of the crushing process. These conveyor belts are designed to handle the tough conditions of a stone crusher environment, including the constant impact of sharp, heavy stones. Made from durable materials like reinforced rubber or synthetic compounds, the conveyor belt for stone crusher ensures the continuous and efficient movement of crushed stone, reducing manual handling and operational downtime. This automation enhances productivity by providing a consistent flow of materials, making the overall crushing process more streamlined and efficient. Conveyor belts for stone crushers are engineered to be robust and long-lasting, capable of withstanding the high wear and tear associated with stone crushing operations.
In a conveyor belt for stone crusher system, the primary machine used to crush stones is typically a jaw crusher. Jaw crushers are designed to handle large, hard materials by applying compressive force to break down stones into smaller, more manageable pieces. This type of crusher is highly effective in the initial stages of stone processing. Other machines that can be part of the conveyor belt for stone crusher system include impact crushers, which use high-speed impact to fracture stones, and cone crushers, which use a gyrating spindle to crush stones against a fixed outer wall. These crushers are essential for creating different aggregate sizes required for various construction and industrial applications. The choice of crusher depends on the specific needs of the operation, such as the type of stone being processed and the desired end product size.
Choosing the right belt for a conveyor belt for stone crusher involves several considerations to ensure optimal performance and longevity. First, assess the type and size of the stones being transported. The belt material must be durable enough to withstand the abrasive nature of the stones. Reinforced rubber belts are commonly used due to their strength and flexibility. Next, consider the load capacity required. The belt must support the weight of the materials without excessive wear or risk of breaking. Manufacturers like Mitsuboshi Belting Ltd. offer belts capable of handling heavy loads up to 2000 kg per hour. Additionally, evaluate the belt’s resistance to environmental conditions, such as temperature and moisture. Customization options, including belt width and speed, should also be factored in to match the specific requirements of the stone crusher setup. Finally, consult with suppliers like ContiTech or Fenner Dunlop to get expert recommendations and ensure the selected belt meets all operational needs.
The strongest conveyor belt for stone crusher applications is typically made from reinforced rubber or steel cord. Reinforced rubber belts, such as those offered by Bridgestone, incorporate multiple layers of synthetic fabric or steel mesh, providing exceptional tensile strength and resistance to impact and abrasion. These belts can handle the heavy loads and harsh conditions of stone crushing environments. Steel cord conveyor belts, available from manufacturers like ContiTech, are known for their superior strength and durability, making them ideal for high-capacity operations. They feature steel cords embedded within the rubber, which provide unmatched strength and allow the belt to carry substantial weights over long distances. Such belts are designed to endure extreme operational demands and ensure long-term reliability, reducing the frequency of maintenance and replacements. Choosing the strongest conveyor belt for stone crusher applications ensures maximum efficiency and longevity, vital for maintaining continuous and effective crushing operations.
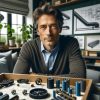
Jordan Smith, a seasoned professional with over 20 years of experience in the conveyor system industry. Jordan’s expertise lies in providing comprehensive solutions for conveyor rollers, belts, and accessories, catering to a wide range of industrial needs. From initial design and configuration to installation and meticulous troubleshooting, Jordan is adept at handling all aspects of conveyor system management. Whether you’re looking to upgrade your production line with efficient conveyor belts, require custom conveyor rollers for specific operations, or need expert advice on selecting the right conveyor accessories for your facility, Jordan is your reliable consultant. For any inquiries or assistance with conveyor system optimization, Jordan is available to share his wealth of knowledge and experience. Feel free to reach out at any time for professional guidance on all matters related to conveyor rollers, belts, and accessories.