Rock Crusher Conveyor Belt Efficiency Guide
Rock crusher conveyor belts are essential components in the mining and construction industries. These belts serve as the lifeline, efficiently transporting crushed materials from one stage of the production process to another. By seamlessly integrating with rock crushers, these conveyor belts not only enhance productivity but also significantly reduce labor costs and operational downtime. The robust construction and customizability of rock crusher conveyor belts make them indispensable for handling a variety of materials, ensuring smooth and continuous workflow in demanding environments. Understanding the vital role of rock crusher conveyor belts is crucial for optimizing industrial processes and achieving superior efficiency in material handling operations.
Rock Crusher Conveyor Belt: Essential Components and Their Importance
Understanding the Basics
Definition and Functionality
A rock crusher conveyor belt is an integral part of the rock crushing process. It serves as a critical link between various equipment, including crushers, feeders, and screens, facilitating a continuous and automated production flow. This conveyor belt is designed to transport crushed rock and other materials efficiently from one processing stage to the next. The primary components of a rock crusher conveyor belt include the belt itself, pulleys, rollers, and the motor drive system. These components work together to move the material along the conveyor, ensuring that it reaches the desired destination within the crushing plant.
Material and Construction
Rock crusher conveyor belts are constructed from high-quality materials to withstand the demanding conditions of rock crushing operations. The belt is typically made from layers of rubber with fabric reinforcements, which provide both flexibility and strength. The outer layers of the belt are designed to resist abrasion and wear, while the inner layers provide the necessary tensile strength to handle heavy loads. For instance, a leading manufacturer like Bridgestone uses multi-ply synthetic fabric in their conveyor belts to enhance durability and performance. This construction ensures that the rock crusher conveyor belt can endure the harsh environment of a crushing plant, including exposure to sharp rocks, heavy impact loads, and varying weather conditions.
Key Features and Benefits
Customizability
One of the standout features of rock crusher conveyor belts is their customizability. Manufacturers can tailor these belts to meet specific operational requirements, including adjustments in length, width, and material composition. For example, Fenner Dunlop offers customized conveyor belts that can be designed to fit unique conveyor systems and specific material handling needs. This customizability allows for the optimization of the conveyor system, ensuring that it operates efficiently and effectively within the constraints of the crushing plant. Customizable features can also include the addition of special coatings or reinforcements to enhance the belt’s performance in specific conditions, such as high temperatures or exposure to chemicals.
Durability and Strength
Rock crusher conveyor belts are built to last, incorporating features that enhance their durability and strength. High-quality rubber is commonly used for the outer layers of the belt to provide excellent resistance to wear and tear. Reinforced fibers, such as polyester or steel cords, are embedded within the belt to provide the necessary tensile strength to handle heavy loads and resist stretching. For example, ContiTech’s steel-cord conveyor belts are known for their exceptional durability and ability to carry large loads over long distances. These belts are designed to withstand the rigors of continuous operation, reducing the need for frequent replacements and maintenance, which in turn lowers operational costs.
Installation and Maintenance
Installation Process
Proper installation of a rock crusher conveyor belt is crucial for its optimal performance and longevity. The installation process begins with preparing the conveyor frame and ensuring that all components are aligned correctly. The belt is then threaded through the conveyor system, ensuring that it is positioned correctly on the pulleys and rollers. Tensioning the belt is a critical step, as improper tension can lead to slippage or excessive wear. The belt must be tensioned according to the manufacturer’s specifications to ensure smooth operation. For instance, Metso Outotec provides detailed guidelines and support for the installation of their conveyor belts, ensuring that the installation is done correctly and efficiently.
Maintenance Tips
Regular maintenance of rock crusher conveyor belts is essential to ensure their longevity and optimal performance. Maintenance activities include regular inspections to check for signs of wear, damage, or misalignment. Cleaning the belt and removing any debris that may have accumulated is also important to prevent damage and ensure smooth operation. Lubricating the pulleys and rollers can help reduce friction and wear. In addition, it is important to monitor the belt tension and adjust it as necessary to maintain proper alignment and operation. Companies like Martin Engineering offer a range of maintenance products and services to help keep conveyor systems running smoothly, including belt cleaners, tracking systems, and maintenance training programs.
A well-maintained rock crusher conveyor belt can significantly enhance the efficiency and productivity of a crushing plant. Regular maintenance not only extends the life of the conveyor belt but also helps prevent costly downtime and repairs. By investing in high-quality materials and proper installation and maintenance practices, operators can ensure that their rock crusher conveyor belts perform reliably and efficiently in even the most demanding conditions.
Rock Crusher Conveyor Belt: Integral Part of the Conveyor System
Role in the Conveyor System
Integration with Conveyor Belts
A rock crusher conveyor belt is fundamental to the integration of the crushing and conveying process, streamlining operations within a crushing plant. The conveyor belt acts as a continuous transporter of materials between the different stages of crushing and screening. When rocks are fed into the crusher, they are broken down into smaller pieces, which are then transported via the conveyor belt to further stages of processing or directly to storage areas. This integration ensures a seamless flow of materials, reducing the need for manual handling and thereby increasing efficiency.
For example, in a typical setup at a mining site, a rock crusher conveyor belt system will consist of a series of conveyors connecting the primary crusher, secondary crushers, and screening equipment. Companies like Metso and Sandvik provide advanced conveyor systems designed to work seamlessly with their rock crushers, ensuring that materials are efficiently transported through each stage of the crushing process. The automation provided by these integrated systems significantly reduces the risk of material spillage and ensures a consistent feed rate, which is critical for maintaining optimal crusher performance.
Types of Rock Crushers
There are various types of rock crushers that work in conjunction with conveyor belts, each designed for specific applications and material types. The most common types include:
- Jaw Crushers: These are used for primary crushing and can handle large rocks and boulders. They work by compressing the material between a stationary piece of steel and a moving one.
- Cone Crushers: These crushers are used for secondary or tertiary crushing, reducing the size of the material even further after it has passed through a jaw crusher. They operate by squeezing the material between an eccentrically gyrating spindle and a concave hopper.
- Impact Crushers: Used for primary or secondary crushing, impact crushers utilize the force of impact to break down materials. They are particularly effective for processing softer rocks and materials.
- Gyratory Crushers: Similar to jaw crushers, gyratory crushers are used for primary crushing but can handle a higher capacity and more abrasive materials.
Manufacturers like Terex and McCloskey International offer a range of rock crushers designed to integrate seamlessly with conveyor belts, providing customized solutions for different types of materials and production requirements.
Efficiency and Productivity
Boosting Efficiency
The combination of rock crushers and conveyor belts is crucial for boosting efficiency in rock crushing operations. The automated nature of these systems reduces the need for manual intervention, allowing for continuous operation and minimizing downtime. The use of a rock crusher conveyor belt ensures that materials are consistently fed into the crusher, optimizing the crushing process and preventing bottlenecks.
For instance, at a large-scale mining operation, using an integrated conveyor system with rock crushers can lead to a significant increase in production capacity. A study by Sandvik revealed that the implementation of their conveyor belt systems in conjunction with their rock crushers resulted in a 30% increase in production efficiency. This is largely due to the ability to maintain a steady flow of materials, reducing the time lost in manual handling and transportation.
Reducing Labor Costs
The automation provided by a rock crusher conveyor belt system also leads to a substantial reduction in labor costs. By automating the transportation of materials between different stages of the crushing process, the need for manual labor is minimized. This not only reduces labor costs but also enhances safety by limiting the exposure of workers to potentially hazardous environments.
For example, a mining company utilizing a fully integrated conveyor and crushing system reported a 20% reduction in labor costs. This was achieved by reallocating personnel from material handling roles to more skilled positions within the operation, thereby optimizing labor resources. Additionally, the reduction in manual handling also decreased the incidence of workplace injuries, contributing to overall operational safety and efficiency.
The integration of rock crusher conveyor belts with crushing equipment is a game-changer for the mining and construction industries. By ensuring a seamless flow of materials, these systems enhance productivity, reduce labor costs, and contribute to safer working conditions. Companies that invest in advanced conveyor belt systems, such as those offered by Metso, Sandvik, and Terex, stand to benefit significantly from increased efficiency and reduced operational costs.
Rock Crusher Conveyor Belt: Applications in RC Models
Miniaturized Conveyor Belts
Introduction to 1:14 Scale Conveyor Belts
1:14 scale conveyor belts are miniature versions of the full-sized rock crusher conveyor belts used in industrial applications. These scaled-down models are designed for use in remote control (RC) models, which are often utilized for educational, hobbyist, and demonstration purposes. The primary function of these miniaturized conveyor belts is to simulate the operation of a real conveyor system, allowing enthusiasts and professionals to observe and understand the mechanics and efficiency of rock crusher conveyor belts on a smaller scale.
Design and Functionality
The design of 1:14 scale conveyor belts closely mimics that of their full-sized counterparts. They are typically constructed using durable materials such as rubber and plastic, which provide flexibility and strength, essential for replicating the functionality of a real conveyor system. The belts are mounted on a series of pulleys and rollers, which are driven by a small electric motor, allowing the belt to move continuously and transport materials.
For example, a well-known manufacturer, Lesu Model, produces highly detailed 1:14 scale conveyor belts that are used in RC construction models. These miniaturized conveyor belts are designed to carry small quantities of material, such as sand or gravel, mimicking the operation of a real rock crusher conveyor belt. The belts can be customized in terms of length and width to fit different RC models, making them versatile for various applications.
The functionality of these miniaturized conveyor belts includes the ability to adjust the speed and direction of the belt, similar to full-sized conveyor systems. This feature allows users to simulate different operational conditions and observe how changes in speed or direction affect the efficiency of the conveyor system. The detailed design and functionality of these 1:14 scale conveyor belts provide a realistic representation of industrial conveyor systems, making them valuable tools for both hobbyists and professionals.
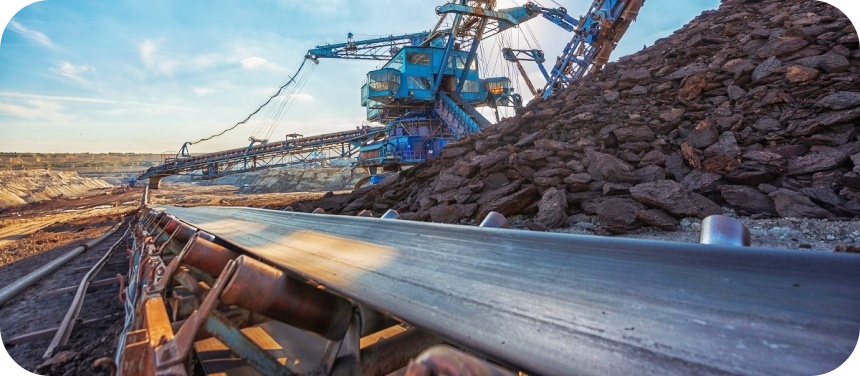
Creating Accurate RC Models
Designing RC Models
Designing RC models that incorporate rock crusher conveyor belts involves a detailed and precise process to ensure that the models accurately replicate real-life conveyor systems. The first step in the design process is to create a detailed blueprint of the RC model, which includes specifications for the conveyor belt, rock crusher, and other components. This blueprint serves as a guide for constructing the model, ensuring that all parts fit together seamlessly and function as intended.
For instance, RC4WD, a leading manufacturer of RC construction equipment, designs and produces RC models with integrated rock crusher conveyor belts. Their models are based on real industrial equipment, and the design process involves close attention to detail to ensure that the RC models operate similarly to their full-sized counterparts. This includes scaling down the dimensions of the conveyor belt and crusher, while maintaining the correct proportions and functionality.
Materials and Construction
The materials and construction techniques used in RC models are crucial for accurately replicating real conveyor systems. High-quality materials such as reinforced rubber, plastic, and metal are commonly used to construct the conveyor belts and other components. These materials provide the necessary durability and flexibility to ensure that the RC models can withstand regular use and accurately simulate the operation of a real rock crusher conveyor belt.
For example, the conveyor belts in RC models produced by Tamiya, another renowned manufacturer, are made from reinforced rubber, which mimics the properties of industrial conveyor belts. The use of metal for the frame and pulleys ensures that the model is sturdy and reliable. The construction process involves precision engineering to assemble the components accurately, ensuring that the conveyor belt operates smoothly and efficiently.
In addition to materials and construction techniques, the integration of electronic components is essential for the functionality of RC models. Small electric motors are used to drive the conveyor belts, while remote control systems allow users to operate the models and adjust the speed and direction of the belts. These electronic components are carefully integrated into the design to ensure that the RC models function reliably and provide a realistic simulation of industrial conveyor systems.
The development of accurate RC models with rock crusher conveyor belts requires a combination of detailed design, high-quality materials, and precise construction techniques. These models provide valuable insights into the operation of conveyor systems and are widely used for educational, hobbyist, and demonstration purposes. By replicating the functionality of real conveyor belts, these RC models offer a practical and engaging way to explore the mechanics and efficiency of rock crusher conveyor belts.
Rock Crusher Conveyor Belt: Enhancing Screening and Sorting
rc Screening Plant: Integrating Conveyor Belts
Role of Conveyor Belts in Screening Plants
A rock crusher conveyor belt plays a vital role in screening plants, where it is used to sort and process materials effectively. In a typical screening plant setup, the rock crusher conveyor belt transports crushed materials from the crusher to various screening units. These units are designed to separate materials based on size, quality, and other characteristics. The conveyor belt ensures a continuous flow of materials, which is crucial for the efficiency and productivity of the screening process.
For example, in a mining operation, a rock crusher conveyor belt system might transport crushed ore from a primary crusher to a series of screening units. Each unit screens the material to different specifications, with oversize material being returned to the crusher for further processing, and undersize material being conveyed to the next stage. This multi-stage process is essential for producing materials that meet specific size and quality requirements, which are critical for downstream processing or end-use applications.
The integration of conveyor belts in screening plants offers several benefits. Firstly, it significantly reduces the need for manual handling of materials, which improves safety and reduces labor costs. Conveyor belts also ensure a consistent and controlled flow of materials, which enhances the efficiency of the screening process. This consistency is crucial for maintaining the quality and uniformity of the final product.
Furthermore, modern screening plants often incorporate advanced technologies such as automated controls and sensors. These technologies work in conjunction with conveyor belts to monitor the material flow, detect blockages or inefficiencies, and adjust the system in real-time to optimize performance. For instance, automated systems can adjust the speed of the conveyor belt or the settings of the screening units to ensure optimal throughput and material quality.
Companies like Powerscreen and Terex provide advanced screening equipment that integrates seamlessly with rock crusher conveyor belts, ensuring smooth and efficient operation. Their equipment is designed to handle the rigorous demands of screening operations, with features like robust construction, easy maintenance, and user-friendly interfaces. By combining high-quality screening equipment with reliable conveyor belt systems, these companies help mining and aggregate operations achieve their production goals with maximum efficiency and minimal downtime.
The role of conveyor belts in screening plants is indispensable. They facilitate the efficient transport and sorting of materials, enhance safety, reduce labor costs, and contribute to the overall productivity of the screening process. With advancements in technology and equipment, the integration of conveyor belts in screening operations continues to evolve, offering even greater benefits and efficiencies.
Efficiency in Sorting
The use of rock crusher conveyor belts in screening plants significantly enhances sorting efficiency. Conveyor belts ensure a consistent and controlled flow of materials to the screening units, which minimizes downtime and reduces the risk of blockages. This consistent flow allows screening plants to operate at optimal capacity, increasing the throughput and quality of the sorted material.
For instance, a screening plant equipped with a rock crusher conveyor belt system can process up to 500 tons of material per hour, depending on the size and type of material being screened. This high throughput is achieved because the conveyor belt system can handle large volumes of material continuously, reducing the need for manual handling and increasing the efficiency of the sorting process.
In addition, the automation provided by rock crusher conveyor belts reduces the labor required for material handling. This not only lowers operational costs but also enhances workplace safety by limiting the exposure of workers to potentially hazardous materials. Overall, the integration of conveyor belts into screening plants is a key factor in achieving efficient and effective material sorting.
rc Trommel: Advanced Sorting Techniques
Introduction to RC Trommels
RC trommels, or rotary screens, are advanced sorting machines used in screening and sorting operations. These cylindrical screens rotate to separate materials based on size, allowing for efficient sorting of different grades of material. RC trommels are commonly used in conjunction with rock crusher conveyor belts to enhance the sorting process in various industries, including mining, construction, and recycling.
For example, Doppstadt and McCloskey International are leading manufacturers of RC trommels, offering a range of models designed to handle different types of material and processing requirements. These trommels can process large volumes of material, making them ideal for high-capacity screening operations.
Integration with Conveyor Belts
The integration of rock crusher conveyor belts with RC trommels enhances sorting efficiency by ensuring a continuous and controlled feed of material into the trommel. The conveyor belt transports the material from the crusher to the trommel, where it is screened and sorted. This integration allows for a seamless flow of material, reducing downtime and improving the overall efficiency of the sorting process.
For example, a rock crusher conveyor belt system feeding material into an RC trommel can process up to 1000 tons of material per hour, depending on the size and type of material. The consistent feed provided by the conveyor belt ensures that the trommel operates at optimal capacity, maximizing the throughput and quality of the sorted material.
The combination of rock crusher conveyor belts and RC trommels also allows for greater flexibility in the sorting process. Conveyor belts can be adjusted to control the speed and direction of the material flow, enabling operators to fine-tune the sorting process to meet specific requirements. This flexibility is particularly important in operations where different grades of material need to be separated efficiently and accurately.
The integration of rock crusher conveyor belts with advanced sorting equipment like RC trommels represents a significant advancement in material processing and sorting technology. By ensuring a continuous and controlled flow of material, these systems enhance the efficiency and effectiveness of screening operations, leading to higher productivity and better quality of sorted materials.
Discover top-quality conveyor belts for your industrial needs.
FAQs about Rock Crusher Conveyor Belt
A rock crusher conveyor belt is a critical component in the mining and construction industries. It is a belt that moves rock and aggregate materials from one location to another, often through a series of crushers that break down large rocks into smaller, more manageable pieces. These belts are made of durable materials designed to withstand the harsh conditions of rock crushing, including abrasion, impact, and exposure to heavy loads. The primary function of the conveyor belt is to ensure the efficient and continuous transport of materials, optimizing productivity and reducing manual handling. Rock crusher conveyor belts come in various sizes and specifications, tailored to meet the specific needs of different crushing applications.
The strongest conveyor belt available today is typically made from steel cord or aramid (a type of strong, heat-resistant synthetic fiber) materials. These belts are engineered to handle the highest tensile forces and are used in the most demanding applications, such as heavy-duty mining and quarry operations. Steel cord conveyor belts, in particular, offer exceptional strength, flexibility, and resistance to impact and wear, making them ideal for transporting large quantities of rock and other materials over long distances. They are designed to operate in extreme conditions, withstanding significant stress and providing reliable performance. The high strength and durability of these belts contribute to reduced maintenance costs and increased operational efficiency.
Grade 1 and grade 2 conveyor belts refer to the levels of quality and durability of the materials used in their construction. Grade 1 conveyor belts are designed to offer superior abrasion resistance, making them suitable for handling sharp and heavy materials like rocks in crusher applications. They are built to last longer and withstand more wear and tear compared to grade 2 belts. Grade 2 conveyor belts, on the other hand, provide good durability and performance but are typically used in less demanding environments where the materials being transported are not as abrasive or heavy. The choice between grade 1 and grade 2 belts depends on the specific requirements of the operation, with grade 1 being preferred for more rugged and challenging conditions.
Grounding a conveyor belt is essential for safety, particularly in environments where static electricity can build up and pose a risk of sparks or electrical shocks. To ground a conveyor belt, you need to establish a conductive path from the belt to the ground. This can be achieved by attaching grounding brushes or straps to the conveyor frame and ensuring they make contact with the belt’s surface. These brushes or straps are connected to a grounding rod or the plant’s grounding system. Additionally, it is crucial to regularly inspect and maintain the grounding components to ensure they remain effective. Proper grounding not only enhances safety but also helps prevent damage to the belt and associated equipment from static discharge.
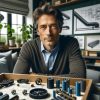
Jordan Smith, a seasoned professional with over 20 years of experience in the conveyor system industry. Jordan’s expertise lies in providing comprehensive solutions for conveyor rollers, belts, and accessories, catering to a wide range of industrial needs. From initial design and configuration to installation and meticulous troubleshooting, Jordan is adept at handling all aspects of conveyor system management. Whether you’re looking to upgrade your production line with efficient conveyor belts, require custom conveyor rollers for specific operations, or need expert advice on selecting the right conveyor accessories for your facility, Jordan is your reliable consultant. For any inquiries or assistance with conveyor system optimization, Jordan is available to share his wealth of knowledge and experience. Feel free to reach out at any time for professional guidance on all matters related to conveyor rollers, belts, and accessories.