Conveyor Belt for Cement Industry: Technology Solutions
Conveyor belts play a crucial role in the cement industry by facilitating the efficient transportation of raw materials and finished products within the plant. The conveyor belt for cement industry is designed to handle heavy-duty tasks, ensuring the continuous movement of limestone, clinker, and other materials essential for cement production. The significance of conveyance systems in cement processing plants cannot be overstated, as they streamline operations, reduce manual labor, and enhance overall productivity. By utilizing a well-designed conveyor belt for cement industry, plants can achieve a smoother workflow, minimize downtime, and maintain a consistent production rate, ultimately contributing to the industry’s growth and success.
What is Conveyor Belt for Cement Industry
A conveyor belt in cement industry is an essential component designed to handle the demanding conditions of cement manufacturing. These belts are used to transport raw materials such as limestone, clinker, and gypsum, as well as finished cement products. Their primary function is to move these materials efficiently and continuously from one processing stage to another within the cement plant, significantly reducing the need for manual labor and increasing overall operational efficiency.
In a typical cement production process, raw materials are mined, crushed, and then transported to the plant via conveyor belts. Once at the plant, these materials are further processed in various stages, including grinding, mixing, and heating in kilns to produce clinker. The conveyor belts play a crucial role in each of these stages by ensuring the smooth and timely movement of materials, which is critical to maintaining a consistent production flow.
Key Features of Conveyor Belt for Cement Industry
The environment within a cement plant is harsh, characterized by heavy loads, abrasive materials, extreme temperatures, and continuous operation. As such, the conveyor belts used in this industry must be exceptionally durable and robust to withstand these challenging conditions. Below are five examples illustrating the specific requirements and features of conveyor belts designed for the cement industry:
Heat-Resistant Conveyor Belts
In the cement industry, conveyor belts often have to transport materials that are extremely hot, especially clinker, which can reach temperatures of up to 200°C (392°F). Heat-resistant conveyor belts are specifically designed to handle these high temperatures without degrading. They are made from materials that can withstand thermal stress, preventing the belt from cracking, hardening, or losing flexibility. These belts ensure that the transportation of hot materials does not interrupt the production process.
Heavy-Duty Conveyor Belts
Heavy-duty conveyor belts are essential for transporting large quantities of raw materials, such as limestone and coal, which are both bulky and heavy. These belts are constructed with high tensile strength materials and reinforced with multiple layers to handle the significant weight and pressure exerted by the materials. Their robust construction ensures longevity and reliability, reducing the frequency of maintenance and replacement.
Abrasion-Resistant Conveyor Belts
Materials like limestone and clinker are highly abrasive and can cause significant wear and tear on conveyor belts. Abrasion-resistant conveyor belts are designed with specialized covers that can withstand the continuous friction and impact of these abrasive materials. These covers are typically made from rubber compounds that offer high resistance to wear, thereby extending the life of the conveyor belt and maintaining operational efficiency.
Oil-Resistant Conveyor Belts
In some parts of the cement production process, materials may come into contact with oils or other chemical substances. Oil-resistant conveyor belts are designed to resist the deteriorating effects of oils, greases, and other chemicals. These belts are made from synthetic rubber compounds that prevent swelling, cracking, or softening when exposed to such substances. This feature is crucial for maintaining the belt’s integrity and performance in chemically harsh environments.
Fire-Resistant Conveyor Belts
Safety is a paramount concern in any industrial setting, and the cement industry is no exception. Fire-resistant conveyor belts are crucial for preventing the spread of fire in case of ignition. These belts are constructed from materials that are self-extinguishing and do not propagate flames. They are particularly important in areas where flammable materials are transported or stored. By using fire-resistant belts, cement plants can enhance their safety protocols and protect both their workforce and infrastructure.
The Importance of Conveyor Belt for Cement Industry
The conveyor belt for cement industry is a vital component that significantly contributes to the efficiency and safety of cement production. By understanding the various types of conveyor belts and their specific applications, cement plant operators can select the appropriate belts that meet their operational needs. Heat-resistant, heavy-duty, abrasion-resistant, oil-resistant, and fire-resistant conveyor belts each offer unique advantages that cater to the demands of the cement industry.
Investing in high-quality conveyor belts designed for the cement industry not only ensures smooth and uninterrupted production processes but also minimizes downtime and maintenance costs. The durability and robustness of these belts are critical in handling the extreme conditions within cement plants, ultimately leading to increased productivity and profitability.
The conveyor belt for cement industry plays an indispensable role in the seamless operation of cement manufacturing plants. By providing a reliable means of material transportation, these belts help maintain a steady production flow, enhance safety, and contribute to the overall efficiency and success of the cement industry.
Types of Conveyor Belt for Cement Industry
The conveyor belt for cement industry is a crucial element designed to handle the diverse and rigorous demands of cement production. In cement plants, different types of conveyor belts are used to transport materials at various stages of the manufacturing process. These belts are tailored to specific requirements such as material type, load capacity, temperature resistance, and incline transport. Understanding the various types of conveyor belts and their specific applications helps optimize operations, reduce downtime, and enhance productivity.
Detailed Exploration of the Characteristics and Advantages of Each Type
Heat-Resistant Belts for Clinker Handling
Clinker, a key intermediate material in cement production, is typically transported at very high temperatures, sometimes exceeding 200°C (392°F). Heat-resistant conveyor belts are specially designed to handle these extreme temperatures without suffering from degradation.
- Material Composition: Made from heat-resistant rubber compounds that can withstand high thermal stress.
- Durability: Resistant to cracking, hardening, and other forms of wear caused by prolonged exposure to high temperatures.
- Performance: Maintains flexibility and structural integrity under heat, ensuring continuous and efficient transportation of clinker.
- Cost-Efficiency: Reduces the frequency of belt replacement and maintenance, leading to lower operational costs over time.
Heavy-Duty Belts for Limestone Transportation
Limestone is a primary raw material in cement production and is typically transported in large, heavy quantities. Heavy-duty conveyor belts are designed to handle such significant loads. Key characteristics and advantages include:
- Strength: Constructed with high tensile strength materials and multiple layers for added reinforcement.
- Load Capacity: Capable of carrying heavy loads without stretching or breaking, ensuring reliable material transport.
- Robustness: Resistant to wear and tear from constant heavy use, providing long service life.
- Efficiency: Minimizes the risk of breakdowns and interruptions, keeping the production line running smoothly.
Chevron and High-Angle Belts for Incline Transport of Loose Materials
In many cement plants, materials need to be transported at steep angles or inclines. Chevron and high-angle conveyor belts are designed for these specific applications.
- Design: Features a chevron or cleated pattern on the belt surface to prevent materials from slipping during transport.
- Incline Capability: Allows for the efficient movement of loose materials up steep slopes, maximizing space and improving plant layout.
- Versatility: Suitable for a variety of materials, including sand, gravel, and other bulk materials.
- Safety: Enhances safety by reducing the risk of material spillage and ensuring a stable transport process.

Data Displayed in Table
Below is a table summarizing the key characteristics and advantages of the different types of conveyor belts used in cement plants:
Type of Conveyor Belt | Material Composition | Key Characteristics | Advantages |
---|---|---|---|
Heat-Resistant Belts for Clinker | Heat-resistant rubber compounds | High thermal resistance, maintains flexibility | Long service life, reduced maintenance costs, efficient clinker transport |
Heavy-Duty Belts for Limestone | High tensile strength materials, reinforced layers | High load capacity, robust construction | Reliable heavy load transport, minimized downtime, durable under constant use |
Chevron and High-Angle Belts | Chevron/cleated pattern design | Prevents material slippage, suitable for steep inclines | Efficient incline transport, versatile for various materials, improved safety and plant layout |
The Uses of Conveyor Belt for Cement Industry
Conveyor belts play a vital role in the cement industry by ensuring efficient and continuous transport of materials at various stages of the cement production process. Here are the primary uses of conveyor belts in this industry:
Raw Material Handling
- Transportation from Quarry to Plant: Conveyor belts are used to transport raw materials such as limestone, clay, and other aggregates from the quarry to the cement plant.
- Stockpiling and Reclaiming: They help in stacking and reclaiming raw materials in the storage area.
Material Feeding and Pre-Processing
- Crusher Feeding: Conveyor belts transport raw materials to the crusher for initial size reduction.
- Raw Mill Feeding: After crushing, the materials are transported to the raw mill where they are ground into fine powder.
Clinker Transport
- Kiln Feed: Conveyor belts are used to transport the raw mix to the kiln.
- Hot Clinker Transport: After the kiln process, hot clinker is transported to the cooler via heat-resistant conveyor belts.
- Clinker Storage and Handling: Belts transport cooled clinker to storage silos and handling systems.
Finished Product Handling
- Cement Grinding Feed: Conveyor belts transport clinker and other additives to the cement mill where they are ground into cement.
- Packaging and Dispatch: Finished cement is transported via belts to packing units and loading systems for dispatch.
Intermediate Processes
- Blending: Conveyor belts are used in the blending process where different materials are mixed to create the desired cement composition.
- Additive Handling: They transport various additives like gypsum, fly ash, and slag to different stages of the production process.
Waste and By-Product Handling
- Handling Bypass Dust: Conveyor belts transport bypass dust and other waste products to disposal or recycling areas.
- Alternative Fuels: In some plants, conveyor belts are used to transport alternative fuels to the kiln.
Auxiliary Systems
- Cooling Systems: Conveyor belts are used in conjunction with cooling systems to transport materials through cooling zones.
- Belt Filters: In some processes, conveyor belts are used as part of belt filter systems to dewater slurry materials.
Efficient Plant Layout
- Inter-Plant Transport: Conveyor belts facilitate the efficient layout of the plant by enabling transport between different sections without the need for multiple handling steps.
- Vertical Transport: Bucket elevators, a type of conveyor belt system, are used for vertical transport of materials.
Automation and Control
- Automated Handling Systems: Conveyor belts are integrated into automated handling systems to ensure consistent material flow and process control.
- Quality Control: Conveyor belts can be equipped with sensors and monitoring systems to maintain quality control throughout the production process.
Benefits
- Continuous Operation: Conveyor belts ensure continuous material flow, reducing downtime and increasing production efficiency.
- Reduced Labor: Automation reduces the need for manual handling, lowering labor costs and minimizing human error.
- Enhanced Safety: By automating material transport, conveyor belts reduce the risk of workplace accidents and injuries associated with manual handling.
- Cost-Effective: Over time, the use of conveyor belts leads to cost savings in terms of reduced labor, maintenance, and operational efficiency.
Conveyor belts are indispensable in the cement industry, enabling efficient, continuous, and automated transport of materials throughout the production process.
Procurement and Cost Considerations of Conveyor Belt for Cement Industry
Discussion on the Factors Affecting the Cost of Conveyor Belts for the Cement Industry
The procurement of a conveyor belt for cement industry applications involves careful consideration of various factors that influence the overall cost. Understanding these factors helps in making informed purchasing decisions that balance quality, durability, and budget constraints. Here are five key factors affecting the cost of conveyor belts for the cement industry:
Material Composition:
- The type of materials used in the construction of conveyor belts significantly impacts their cost. High-quality materials such as heat-resistant rubber compounds and reinforced steel cables are more expensive but offer superior durability and performance. For example, belts designed to withstand high temperatures or abrasive materials will generally be costlier due to the specialized materials used.
Belt Length and Width:
- The dimensions of the conveyor belt, including its length and width, directly influence the price. Longer and wider belts require more raw materials and manufacturing time, leading to higher costs. In the cement industry, belts must often span long distances and handle wide loads, which can add to the expense.
Load Capacity:
- Conveyor belts with higher load capacities are designed to transport heavy materials such as limestone and clinker. These belts are constructed with additional layers and reinforcements, making them more robust but also more expensive. Investing in belts with adequate load capacity is crucial to avoid frequent replacements and maintenance.
Customization and Special Features:
- Customized belts that meet specific operational requirements, such as those with chevron patterns for inclined transport or oil-resistant properties, tend to be more expensive. Special features that enhance performance, safety, and longevity add to the overall cost but can provide significant benefits in terms of efficiency and reduced downtime.
Brand and Supplier Reputation:
- The reputation of the brand and supplier can also affect the cost of conveyor belts. Established brands and reputable suppliers often charge a premium for their products due to their proven track record of quality and reliability. While it might be tempting to opt for cheaper alternatives, investing in well-known brands can ensure better performance and durability.
Tips on Procuring Used Conveyor Belts as a Cost-Saving Measure
For cement plants operating on tight budgets, procuring used conveyor belts can be a viable cost-saving measure. However, it requires careful evaluation to ensure that the belts are still functional and reliable. Here are five tips for procuring used conveyor belts:
Inspection for Wear and Tear:
- Thoroughly inspect the used conveyor belts for signs of wear and tear, such as cracks, fraying, or significant abrasions. Ensure that the belts are in good condition and have sufficient remaining lifespan to justify the purchase.
Check for Structural Integrity:
- Assess the structural integrity of the belts, including the strength of the splices and the condition of the reinforcement layers. Weak splices and compromised reinforcements can lead to belt failure under heavy loads, making the investment unworthy.
Evaluate Previous Usage Conditions:
- Understand the previous usage conditions of the belts, including the type of materials transported and the operational environment. Belts used in less abrasive or less demanding conditions are likely to have a longer remaining lifespan compared to those used in harsher environments.
Seek Reliable Suppliers:
- Purchase used belts from reputable suppliers who specialize in refurbishing and reselling industrial conveyor belts. These suppliers often conduct thorough inspections and maintenance to ensure the belts meet certain quality standards before resale.
Consider Compatibility and Specifications:
- Ensure that the used conveyor belts match the specifications and requirements of your cement plant’s operations. This includes dimensions, load capacity, and any special features required for your specific applications.
The Importance of Investing in High-Quality, Durable Belts to Mitigate Long-Term Costs
While procuring used belts can offer short-term cost savings, investing in high-quality, durable conveyor belts is essential for mitigating long-term costs and ensuring the smooth operation of cement plants.
Reduced Maintenance Costs:
- High-quality belts require less frequent maintenance and repairs, resulting in lower ongoing maintenance costs. Durable belts are designed to withstand the rigors of the cement industry, minimizing the need for constant attention and upkeep.
Longer Service Life:
- Investing in durable belts ensures a longer service life, reducing the frequency of replacements. This not only saves money on purchasing new belts but also minimizes downtime associated with belt replacements.
Enhanced Operational Efficiency:
- Reliable and high-performing belts contribute to smoother and more efficient operations. By reducing the risk of belt failures and breakdowns, cement plants can maintain a consistent production flow and avoid costly interruptions.
Safety Improvements:
- High-quality belts are often designed with safety features that reduce the risk of accidents and injuries. Fire-resistant belts, for example, can prevent the spread of fires in case of ignition, enhancing overall plant safety and reducing potential liabilities.
Better Load Handling:
- Durable belts with higher load capacities and specialized features can handle the heavy and abrasive materials typical of cement production more effectively. This ensures that the belts perform optimally under demanding conditions, enhancing overall productivity.
The Role and Importance of Conveyor Belt for Cement Industry Procurement
Procurement and cost considerations play a vital role in the effective operation of conveyor belts in the cement industry. By understanding the factors affecting costs, such as material composition, dimensions, load capacity, customization, and supplier reputation, industry professionals can make informed purchasing decisions. Procuring used belts offers a cost-saving option, provided that thorough inspections and evaluations are conducted.
Investing in high-quality, durable conveyor belts is crucial for long-term cost savings, operational efficiency, and safety. The benefits of reduced maintenance costs, longer service life, enhanced efficiency, improved safety, and better load handling underscore the importance of prioritizing quality in procurement decisions.
A strategic approach to procuring conveyor belts for cement industry applications ensures that cement plants can operate smoothly, efficiently, and safely, ultimately contributing to their overall success and profitability.

Selecting the Best Conveyor Belt for Cement Industry
Criteria for Selecting the Best Conveyor Belt Tailored to Specific Cement Industry Needs
Selecting the best conveyor belt for cement industry applications involves a comprehensive understanding of the operational requirements and the unique challenges faced by cement plants. The right conveyor belt not only enhances efficiency but also ensures the longevity and safety of the entire conveyor system. Here are some key criteria to consider when selecting a conveyor belt for cement industry needs:
Material Compatibility:
- The belt material must be compatible with the types of materials it will transport. For instance, rubber belts are suitable for general material handling, while heat-resistant belts are essential for transporting hot clinker. Compatibility ensures optimal performance and minimizes wear and tear.
Load Capacity:
- The conveyor belt must be able to handle the weight of the materials being transported. Load capacity is a critical factor, especially in the cement industry where heavy raw materials like limestone and clinker are commonly moved. Ensuring the belt can support these weights prevents premature failure and extends its lifespan.
Temperature Resistance:
- High-temperature resistance is crucial for conveyor belts that transport hot materials such as clinker. Belts must maintain their integrity and performance despite prolonged exposure to high temperatures. This prevents deformation, cracking, and other heat-related damage.
Abrasion Resistance:
- Conveyor belts in cement plants must endure significant abrasion from materials like limestone, clinker, and gypsum. Abrasion-resistant belts are designed to withstand this constant wear, maintaining their structural integrity and reducing the need for frequent replacements.
Chemical Resistance:
- Some materials and processes in cement production can involve chemicals that may degrade the conveyor belt. Belts with chemical-resistant properties ensure durability and longevity in such environments.
Belt Type and Design:
- The specific design features of the belt, such as cleats, chevrons, or special patterns, can enhance material transport efficiency. For example, chevron belts are ideal for inclined transport, preventing material rollback and spillage.
The selection of the best conveyor belt for cement industry applications is a critical decision that impacts the efficiency, durability, and safety of cement production operations. By considering key criteria such as material compatibility, load capacity, temperature resistance, abrasion resistance, and chemical resistance, cement plants can ensure that they choose the most suitable conveyor belt for their specific needs.
Spotlight on Different System Components in Conveyor Belt for Cement Industry
Overview of Belt Conveyor Roles within a Cement Processing Plant
The conveyor belt for cement industry plays a pivotal role in the smooth and efficient operation of a cement processing plant. These belts are integral to the transport of raw materials, intermediate products, and finished goods throughout the various stages of cement production. The primary roles of belt conveyors in a cement plant include:
Raw Material Transport:
- Belt conveyors are used to transport raw materials such as limestone, clay, and sand from the quarry to the processing areas. These belts ensure a continuous and reliable supply of raw materials to the crushers and grinders, which is essential for maintaining steady production rates.
Intermediate Product Handling:
- During the production process, materials such as crushed limestone and preheated raw meal are transported between different processing units. Belt conveyors facilitate the movement of these intermediate products to the kilns, where they are transformed into clinker.
Finished Product Conveyance:
- Once the clinker is produced and cooled, it is ground into cement and transported to storage silos. Belt conveyors ensure that the finished cement is efficiently moved to storage areas and loading points for distribution.
Waste Material Management:
- Belt conveyors also play a crucial role in handling waste materials and by-products generated during cement production. These belts transport waste to designated disposal or recycling areas, helping maintain a clean and organized plant environment.
Loading and Unloading Operations:
- In cement plants, belt conveyors are used for loading and unloading raw materials and finished products onto trucks, railcars, and ships. This enhances the efficiency of logistics and distribution operations, ensuring timely delivery to customers.
The Reclaimer and Its Function in a Cement Plant’s Ecosystem
A reclaimer is a vital component of the conveyance system in a cement plant, designed to recover and transport bulk materials stored in stockpiles. Reclaimers work in tandem with conveyor belts to ensure a continuous supply of raw materials to the production process. The primary functions of a reclaimer in a cement plant’s ecosystem include:
Stockpile Management:
- Reclaimers are used to manage and retrieve materials from stockpiles, such as limestone, clay, and coal. They ensure that the right amount of material is fed into the production process, maintaining consistency and efficiency.
Material Homogenization:
- By systematically reclaiming materials from different layers of a stockpile, reclaimers help in homogenizing the raw materials. This homogenization is crucial for producing a consistent quality of cement.
Automated Operation:
- Modern reclaimers are equipped with automated systems that allow for precise control and monitoring of material retrieval. This automation reduces the need for manual intervention and enhances the overall efficiency of the material handling process.
Integration with Conveyor Belts:
- Reclaimers work seamlessly with conveyor belts to transport materials to different parts of the cement plant. This integration ensures a smooth and continuous flow of materials, minimizing production interruptions.
Efficiency in Material Handling:
- By optimizing the retrieval and transport of materials, reclaimers contribute significantly to the overall efficiency of the cement production process. They help in reducing material handling times and improving the throughput of the plant.
Impact of Conveyance Systems on the Efficiency and Output of Cement Processing
Effective conveyance systems, including the conveyor belt for cement industry, have a profound impact on the efficiency and output of cement processing. Here are five examples illustrating their impact:
Enhanced Production Flow:
- Efficient conveyance systems ensure a continuous flow of materials through the various stages of cement production. This continuity reduces bottlenecks and production downtimes, leading to higher overall output. For example, a well-maintained conveyor belt system can transport raw materials from the quarry to the processing plant without delays, ensuring that the production process remains uninterrupted.
Improved Material Handling Efficiency:
- Conveyance systems streamline the handling of bulk materials, reducing the need for manual labor and minimizing handling times. Automated conveyor belts can transport large quantities of materials quickly and efficiently, enhancing the overall productivity of the plant. For instance, the use of conveyor belts for transporting clinker from the kiln to the cooler speeds up the cooling process, allowing for quicker transition to the grinding stage.
Cost Savings:
- By reducing manual labor and minimizing material handling times, conveyance systems contribute to significant cost savings. Automated systems also reduce the likelihood of human error, leading to fewer operational disruptions and maintenance issues. For example, the use of heavy-duty conveyor belts for transporting limestone can reduce wear and tear on equipment, lowering maintenance costs and extending the lifespan of the machinery.
Consistency and Quality Control:
- Conveyance systems play a crucial role in maintaining the consistency and quality of the cement produced. By ensuring a steady and controlled supply of raw materials, conveyor belts help maintain the proper mix and composition required for high-quality cement. For example, the use of automated reclaimers and conveyor belts for raw material homogenization ensures that the materials fed into the kiln are of consistent quality, leading to uniform clinker production.
Safety and Environmental Benefits:
- Modern conveyance systems are designed with safety and environmental considerations in mind. Enclosed conveyor belts reduce dust and spillage, minimizing the environmental impact and improving the working conditions within the plant. Safety features, such as emergency stop systems and protective guards, reduce the risk of accidents and injuries. For example, the use of fire-resistant conveyor belts in high-temperature areas enhances plant safety and protects personnel from potential hazards.
The conveyor belt for cement industry and other conveyance system components are integral to the efficient and effective operation of cement plants. From transporting raw materials and intermediate products to handling waste and finished goods, these systems ensure a continuous and streamlined production process.
Reclaimers, working in conjunction with conveyor belts, optimize material retrieval and homogenization, contributing to consistent quality and efficient production. The impact of conveyance systems on the efficiency and output of cement processing is significant, enhancing production flow, improving material handling efficiency, reducing costs, ensuring consistency and quality control, and providing safety and environmental benefits.
By investing in high-quality conveyance systems and maintaining them properly, cement plants can achieve higher productivity, lower operational costs, and improved overall performance, ultimately contributing to the success and sustainability of the cement industry.

Case Studies and Success Stories of Conveyor Belt for Cement Industry
The conveyor belt for the cement industry has been pivotal in transforming the operations of many cement plants around the world. Real-world case studies and success stories highlight the significant improvements in efficiency, safety, and profitability that can be achieved through the implementation of advanced conveyor belt systems.
Nagoya Cement Plant
Nagoya Cement Plant, located in a region with harsh environmental conditions, faced challenges with the transportation of hot clinker from the kiln to the cooler. The traditional conveyor belts used were prone to frequent breakdowns due to high temperatures, leading to production delays and increased maintenance costs.
Solution: The plant invested in heat-resistant conveyor belts designed specifically for the cement industry. These belts could withstand temperatures up to 250°C without degrading.
Impact:
- Improved Reliability: The heat-resistant belts significantly reduced breakdowns, ensuring a more consistent production flow.
- Reduced Maintenance Costs: The durability of the new belts decreased the frequency of maintenance, leading to cost savings.
- Increased Productivity: With fewer interruptions, the plant saw a 15% increase in overall productivity.
Osaka Cement Manufacturing
Osaka Cement Manufacturing was experiencing inefficiencies in transporting limestone from the quarry to the processing plant. The existing conveyor belts were not robust enough to handle the heavy loads, resulting in frequent wear and tear.
Solution: The company switched to heavy-duty conveyor belts with higher tensile strength and reinforced layers.
Impact:
- Enhanced Load Handling: The new belts could easily handle the heavy limestone loads, reducing strain and wear.
- Operational Efficiency: The improved load handling capability streamlined operations, cutting down material transport time by 20%.
- Extended Belt Lifespan: The reinforced belts had a longer service life, reducing the need for frequent replacements and saving on costs.
Tokyo Cement Works
Tokyo Cement Works faced issues with material spillage and inefficient handling of fine particulate materials during the grinding process. This not only caused material loss but also created a dusty environment, posing health risks to workers.
Solution: The plant installed abrasion-resistant conveyor belts with an enclosed design to minimize spillage and dust emission.
Impact:
- Reduced Material Loss: The enclosed belts significantly minimized spillage, ensuring that more material reached the intended destination.
- Health and Safety Improvements: By reducing dust emission, the new belts improved the working environment, enhancing worker safety.
- Cost Efficiency: With less material loss and fewer health-related disruptions, the plant saved on both material costs and health expenditures.
Sapporo Cement Industries
Sapporo Cement Industries aimed to improve the efficiency of its raw material handling system, which involved transporting a variety of materials with different properties. The existing conveyor system lacked versatility and was prone to frequent adjustments.
Solution: The company adopted a series of chevron and high-angle conveyor belts designed for incline transport of loose materials.
Impact:
- Versatility: The chevron belts efficiently handled materials of different properties without requiring frequent adjustments.
- Improved Transport Efficiency: The high-angle belts enabled smooth transport on steep inclines, optimizing space and improving material flow.
- Operational Continuity: The versatile system reduced downtime caused by belt adjustments, enhancing overall operational continuity.
Kobe Cement Corporation
Kobe Cement Corporation faced significant downtime due to frequent belt failures in the preheater tower, where high temperatures and abrasive materials took a toll on the conveyor belts.
Solution: The plant upgraded to specialized fire-resistant and abrasion-resistant conveyor belts suitable for high-temperature environments.
Impact:
- Increased Safety: The fire-resistant belts enhanced safety by preventing the spread of fires in high-temperature areas.
- Durability: The abrasion-resistant belts withstood the harsh conditions, reducing the frequency of belt replacements.
- Higher Productivity: With more reliable belts, the plant experienced fewer disruptions, boosting productivity by 10%.
The Impact of Conveyor Belts on the Profitability and Productivity of Cement Producers
The implementation of advanced conveyor belt systems tailored for the cement industry has a profound impact on the profitability and productivity of cement producers. Here are five key examples illustrating this impact:
- Operational Efficiency: By investing in conveyor belts designed for specific needs, such as heat resistance or heavy-duty load handling, cement plants can achieve smoother and more efficient operations. For example, heat-resistant belts in Nagoya Cement Plant reduced breakdowns, leading to uninterrupted production and higher output.
- Cost Savings: Durable and reliable conveyor belts reduce the need for frequent replacements and maintenance. Osaka Cement Manufacturing’s switch to heavy-duty belts resulted in significant cost savings by extending the lifespan of the belts and reducing maintenance requirements.
- Enhanced Safety: Conveyor belts with specialized safety features, such as fire resistance and enclosed designs, improve worker safety and reduce health risks. Tokyo Cement Works saw improved health and safety conditions, which contributed to lower health-related costs and a safer working environment.
- Increased Productivity: Advanced conveyor belts minimize downtime and disruptions, leading to higher productivity levels. The introduction of versatile chevron belts at Sapporo Cement Industries
FAQs About Conveyor Belt for Cement Industry
Conveyor belts are widely used across various industries to facilitate the efficient and smooth transportation of materials. One of the primary industries that heavily relies on conveyor belts is the cement industry. Conveyor belts in cement plants are essential for moving raw materials like limestone, clay, and sand, as well as intermediate products such as clinker, and finished cement products. Besides the cement industry, conveyor belts are extensively used in mining, where they transport ores and minerals, and in the food industry, where they help in moving raw ingredients and finished products through different stages of processing. Additionally, the manufacturing and logistics sectors utilize conveyor belts to streamline assembly lines and distribution processes. Conveyor belts also play a crucial role in the automotive, pharmaceutical, and packaging industries by enhancing productivity and reducing manual labor.
Several companies specialize in the manufacturing of industrial conveyor belts, each offering a range of products tailored to specific industry needs. Renowned manufacturers include ContiTech, a division of Continental AG, known for their high-quality, durable conveyor belts suitable for various applications including the cement industry. Fenner Dunlop is another major player, providing heavy-duty conveyor belts designed for mining, quarrying, and bulk material handling. Habasit, headquartered in Switzerland, produces conveyor belts that cater to the food, textile, and logistics industries, emphasizing reliability and performance. Flexco is well-regarded for its innovative conveyor belt solutions that focus on splicing and mechanical fasteners. Sparks Belting Company also offers a wide array of conveyor belts for different industrial applications, with a focus on customization and efficiency. These manufacturers leverage advanced technologies and materials to produce conveyor belts that enhance operational efficiency and durability across various industries.
Conveyor belts come in various types, each designed to meet specific industrial needs and conditions. Heat-resistant belts are crucial in industries like cement and steel, where they transport materials at high temperatures without degrading. Heavy-duty belts are designed to carry heavy loads, making them ideal for industries like mining and construction. Abrasion-resistant belts are essential for handling rough and abrasive materials such as minerals and aggregates, ensuring longevity and reliability. Chevron belts feature a patterned surface, making them perfect for transporting materials up steep inclines without slippage. Food-grade belts are made from non-toxic materials and are easy to clean, making them suitable for food processing applications. Oil-resistant belts are used in environments where exposure to oils and chemicals is frequent, preventing material degradation. Lastly, fire-resistant belts are used in industries where safety from fire hazards is paramount, ensuring that the belts do not propagate flames and contribute to safer working environments.
A concrete conveyor is a specialized type of conveyor belt system designed specifically for the transportation of concrete. These conveyors are used in construction sites and concrete production plants to move concrete efficiently from one location to another. Concrete conveyors can be either portable or stationary, depending on the specific requirements of the project. Portable concrete conveyors are often used for smaller projects and can be easily moved around the site, whereas stationary conveyors are used in larger projects or permanent installations. The primary function of a concrete conveyor is to streamline the delivery process, reducing the need for manual labor and increasing the speed of concrete placement. These systems can transport concrete horizontally, vertically, or at inclined angles, ensuring that the material is delivered precisely where it is needed. Concrete conveyors are equipped with special features to handle the heavy, abrasive nature of concrete, such as reinforced belts and robust construction, ensuring durability and reliable performance in demanding construction environments.
In the cement industry, conveyor belts are essential equipment used to transport materials through various stages of production. Common types of conveyor belts include fabric conveyor belts, steel cord conveyor belts, heat-resistant conveyor belts, and sidewall conveyor belts. Fabric conveyor belts are flexible and suitable for light to medium-duty tasks. Steel cord conveyor belts offer high strength and durability for heavy materials and long distances. Heat-resistant conveyor belts are used in high-temperature environments, such as clinker transport. Sidewall conveyor belts are ideal for steep or vertical transport, preventing material slippage. These conveyor belts enhance production efficiency, reduce labor costs, and ensure safety by providing continuous material flow through crushing, grinding, kiln operations, and packaging. Selecting the right conveyor belt type is crucial for achieving efficient and safe cement production.
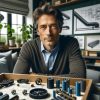
Jordan Smith, a seasoned professional with over 20 years of experience in the conveyor system industry. Jordan’s expertise lies in providing comprehensive solutions for conveyor rollers, belts, and accessories, catering to a wide range of industrial needs. From initial design and configuration to installation and meticulous troubleshooting, Jordan is adept at handling all aspects of conveyor system management. Whether you’re looking to upgrade your production line with efficient conveyor belts, require custom conveyor rollers for specific operations, or need expert advice on selecting the right conveyor accessories for your facility, Jordan is your reliable consultant. For any inquiries or assistance with conveyor system optimization, Jordan is available to share his wealth of knowledge and experience. Feel free to reach out at any time for professional guidance on all matters related to conveyor rollers, belts, and accessories.