Maximize Efficiency: The Benefits of High Speed Conveyor Rollers
In recent years, the manufacturing and distribution industries have undergone significant transformations, driven by technological innovations and the increasing demands for speed and efficiency. Central to this evolution are high speed conveyor rollers, which have become indispensable tools in modern industrial operations. These rollers are designed to facilitate the rapid movement of goods, enhancing productivity and operational efficiency. As an exemplar of excellence in this field, Woodsage Tube Products stands out. This company specializes in the production of high speed conveyor rollers, offering solutions that are tailored to meet the high demands of contemporary manufacturing environments. Their commitment to quality and innovation exemplifies the critical role these components play in the advancing landscape of industrial technology.
Speed in Conveyor Technology with High Speed Conveyor Rollers
As industries evolve, the demand for rapid and efficient production processes becomes increasingly critical. High speed conveyor rollers are pivotal in meeting these demands across various sectors. For instance, in the automotive industry, these rollers speed up the assembly line, allowing for quicker vehicle assembly. In the food processing sector, they facilitate faster packaging and handling, which is crucial for maintaining freshness. Similarly, in e-commerce warehousing, high speed conveyor rollers expedite the sorting and shipping processes, which is essential for meeting consumer expectations for rapid delivery. Lastly, in pharmaceutical manufacturing, these rollers ensure swift and clean transportation of sensitive products, enhancing throughput and safety.
Integrating high speed conveyor rollers into production lines significantly enhances operational efficiency. These systems enable a smoother and faster flow of materials, which reduces the time products spend on the conveyor, thereby increasing output and reducing bottlenecks. Additionally, the enhanced speed and efficiency contribute to reduced machine wear and downtime. Frequent stoppages and slow processing speeds often lead to increased maintenance needs; however, with high speed conveyor rollers, systems operate more reliably and continuously, minimizing disruptions and maintenance costs. This integration not only optimizes production cycles but also substantially lowers operational costs, making it a strategic investment in the future of manufacturing and distribution.
Woodsage’s Commitment to High Speed Conveyor Rollers
Woodsage has firmly established itself as a leader in the field of conveyor technology, specifically through its dedication to high speed conveyor rollers. At the heart of Woodsage’s operation is a commitment to innovative manufacturing practices designed specifically for the production of high speed conveyor rollers. By utilizing advanced automation and precision engineering techniques, Woodsage ensures that each roller meets the highest standards of speed and efficiency. Their state-of-the-art facilities are equipped with cutting-edge machinery that enables the production of rollers that are not only fast but also incredibly durable and reliable.
A key aspect of Woodsage’s market distinction is their ability to maintain short lead times and provide reliable delivery. Understanding the urgency of industrial demands, Woodsage has optimized its production processes to ensure that these high speed conveyor rollers are available when clients need them. This capability is particularly crucial for industries where downtime can result in significant financial losses. Woodsage’s streamlined logistics and supply chain management further ensure that each order is delivered on time, every time, thereby enhancing customer satisfaction and trust. This responsiveness, combined with their top-quality product offerings, positions Woodsage as a pivotal player in advancing conveyor technology.
Key Features of High Speed Conveyor Rollers
Woodsage has developed a range of high speed conveyor rollers that stand out in the market for their robust specifications and adaptability to various industrial needs. The specifications of these high speed conveyor rollers include a variety of sizes and materials tailored to enhance operational efficiency across multiple sectors. For instance, the rollers are available in diameters ranging from 1.9 inches to 3.5 inches, accommodating different scales of operations from light to heavy-duty tasks. Materials such as galvanized steel, stainless steel, and aluminum are used to cater to specific environmental conditions and load requirements. Woodsage also offers rollers with polyurethane and rubber coatings to reduce noise and increase grip during high-speed operations.
These features significantly contribute to the high-speed capabilities of the rollers. The choice of diameter directly impacts the speed at which the rollers can operate; larger diameters are typically used for moving heavier loads quickly, while smaller ones are suited for high-speed processing of lighter materials. The use of durable materials like stainless steel ensures that the rollers can withstand the wear and tear of high-speed operations without frequent maintenance. Furthermore, the material choice helps in minimizing the risk of corrosion, which is crucial in industries like food processing or pharmaceuticals where cleanliness and longevity are paramount. Lastly, the coatings like polyurethane not only prolong the life of the rollers but also enable smoother and quieter operation, which is essential in maintaining high-speed efficiency without disrupting workplace acoustics. Through these carefully engineered features, Woodsage’s high speed conveyor rollers facilitate enhanced productivity and reliability, making them a critical component in modern industrial setups.
Selecting the Best High Speed Conveyor Rollers
Choosing the right high speed conveyor rollers is essential for optimizing the efficiency and reliability of industrial operations. When selecting high-quality rollers, it’s important to consider the specific needs of your industry and the unique challenges it faces. Woodsage provides a wide array of high speed conveyor rollers designed to meet these varied requirements, ensuring that each business can find a solution that best fits their operational needs.
When comparing different high speed conveyor rollers, there are several key criteria to consider:
- Durability: The longevity of a roller is crucial, especially in environments with high operational demands. Woodsage rollers are constructed with robust materials like hardened steel or reinforced polymers, which are capable of withstanding heavy loads and continuous operations without degrading.
- Materials: The choice of material not only affects durability but also the suitability of the roller for specific environmental conditions. For instance, stainless steel rollers are ideal for food processing industries due to their resistance to corrosion and easy cleaning, while polymer-coated rollers might be preferred in industries requiring quiet operation.
- Manufacturing Precision: The precision with which rollers are manufactured affects their performance and efficiency. Woodsage’s rollers are produced using advanced manufacturing techniques that ensure high tolerance and exacting specifications, which contribute to better performance and reduced maintenance needs.
- Load Capacity and Speed Compatibility: It’s essential to select rollers that can handle the expected load capacity and operational speed. Woodsage offers rollers designed to operate efficiently under specific load conditions and speeds, ensuring that they maintain performance without excessive wear or energy consumption.
By carefully considering these criteria, businesses can select the high speed conveyor rollers that not only meet their current operational demands but also provide room for growth and adaptation as their industrial processes evolve. Woodsage’s commitment to providing a diverse range of high speed conveyor rollers ensures that each industry can achieve optimal productivity and efficiency.
Applications of High Speed Conveyor Rollers
High-speed conveyor rollers are versatile components crucial to the operations of diverse industries, ranging from heavy-duty industrial settings to environments requiring high precision. Their adaptability and performance characteristics make them essential in various applications:
- Automotive Assembly Lines: In the automotive industry, high speed conveyor rollers facilitate the swift movement of car parts and assemblies across the production floor. The rollers must handle significant weights and maintain a consistent speed to keep up with the production pace, ensuring that assembly processes are both efficient and timely.
- Food and Beverage Processing: For the food and beverage sector, high speed conveyor rollers are critical in processing lines where speed and hygiene are paramount. Rollers made from materials like stainless steel that are easy to clean and resist corrosion are preferred to prevent contamination and adhere to strict health standards.
- Parcel and Package Sorting Centers: E-commerce and postal services utilize high speed conveyor rollers to manage vast quantities of parcels efficiently. Chain-driven conveyor rollers and CDLR (Chain Driven Live Roller) systems are particularly useful in these settings for their ability to handle heavy loads and facilitate the rapid sorting and distribution of packages.
- Pharmaceutical Manufacturing: In pharmaceutical production, precision and cleanliness are critical. High speed conveyor rollers in these environments are designed to transport delicate products and ingredients swiftly while maintaining a contaminant-free environment. Their high-speed capabilities allow for the fast throughput necessary to meet production demands and regulatory standards.
These applications demonstrate the essential role that high speed conveyor rollers play in modern industry. Whether it’s moving heavy equipment with robust heavy-duty rollers or ensuring precise product placement in high-tech manufacturing environments, these rollers are tailored to meet specific industrial requirements. Woodsage’s offerings in this area, including their specialized chain-driven and heavy-duty rollers, underscore their capability to provide solutions across a spectrum of needs, enhancing operational efficiency and productivity across sectors.
Innovations in High Speed Conveyor Rollers
Woodsage is at the forefront of advancing technology in the field of high speed conveyor rollers, continually pushing the boundaries of what is possible with innovative materials and design strategies. Their commitment to innovation is evident in their development of specialized rollers designed for both noise reduction and enhanced efficiency, which are critical in maintaining smooth and quiet operations in various industrial environments.
One significant innovation by Woodsage involves the use of novel materials that not only reduce the operational noise but also improve the longevity and durability of the rollers. For example, they employ composite materials that are lighter than traditional metals but equally robust, resulting in high speed conveyor rollers that are easier to install and maintain. These materials also exhibit excellent wear resistance, reducing the frequency of replacements and maintenance checks.
Furthermore, Woodsage has made substantial advancements in the design of shaft roller bearings, which are integral to the performance of high speed conveyor rollers. These bearings are engineered to withstand the high speeds and loads placed on them during operations without compromising efficiency. The innovative bearing designs feature enhanced sealing and lubrication retention capabilities, ensuring that the rollers can operate smoothly for extended periods without the need for frequent lubrication or servicing.
These bearings are not only about longevity but also about enhancing the overall performance of the conveyor system. They reduce friction and energy consumption, allowing the rollers to move at higher speeds with less power, which translates to increased operational efficiency and reduced environmental impact.
Together, these innovations in materials and bearing designs enable Woodsage’s high speed conveyor rollers to perform at peak efficiency, handling faster speeds and heavier loads with ease. This dedication to continuous improvement ensures that Woodsage remains a leader in the conveyor industry, providing solutions that significantly benefit their clients’ operational capabilities across various sectors.
Purchasing High Speed Conveyor Rollers
Procuring the right high speed conveyor rollers is crucial for enhancing the efficiency and reliability of your industrial operations. When considering the purchase of high speed conveyor rollers, there are several key factors to keep in mind to ensure you select the best product for your needs. The diameter of the rollers is one of the primary considerations, as it directly affects the roller’s ability to handle various loads and speeds. Larger diameters are typically suited for moving heavier loads at high speeds, whereas smaller diameters are better for lighter loads and high-speed applications where precision is required.
Material selection is another critical factor. The right materials can greatly influence the longevity, durability, and performance of the rollers. Woodsage offers rollers in a variety of materials, including steel, stainless steel, aluminum, and various plastic composites. Each material has unique benefits: steel rollers are generally more durable and suitable for heavy loads, stainless steel offers corrosion resistance, aluminum is lighter for easier handling and less stress on the conveyor system, and plastics can provide noise reduction and corrosion resistance.
Specific needs such as environmental conditions, load type, speed requirements, and maintenance capabilities should also be carefully considered. For environments with high moisture or corrosive materials, choosing a roller made from stainless steel or coated with corrosion-resistant materials is essential. For applications requiring low noise, selecting rollers with a polyurethane coating might be preferable.
Woodsage also enhances the purchasing process with their quick quote system. This service allows potential buyers to receive an immediate estimate on the cost of their specific roller needs, facilitating a faster decision-making process. Additionally, Woodsage’s customer service team is readily available to assist with any queries regarding roller specifications, ensuring that customers make the most informed choice tailored to their unique industrial requirements.
By considering these factors and utilizing Woodsage’s comprehensive customer support and quick quote system, buyers can confidently purchase high speed conveyor rollers that perfectly match their industrial needs, contributing to more efficient and reliable operations.
Maintenance and Upkeep of High Speed Conveyor Rollers
Ensuring the longevity and peak performance of high speed conveyor rollers requires regular maintenance and adherence to best practices. Effective maintenance not only extends the life of the rollers but also ensures they operate at optimal efficiency, minimizing downtime and reducing the overall cost of operations.
- Regular Inspection and Cleaning: Regularly inspect high speed conveyor rollers for signs of wear and damage, such as cracks, deformations, or accumulation of debris. Cleaning the rollers and the conveyor track regularly prevents the buildup of materials that can cause friction or damage, ensuring smooth operation.
- Lubrication: Proper lubrication is crucial for the maintenance of high speed conveyor rollers. Use the recommended type of lubricant for the bearings and make sure to apply it at intervals specified by the manufacturer. This reduces friction and wear, and helps maintain the speed and efficiency of the conveyor system.
- Alignment Checks: Misalignment can lead to uneven wear and tear on rollers and can affect the conveyor belt’s performance. Regularly check and adjust the alignment of the rollers to ensure they are straight and parallel to each other. This prevents premature wear and helps in maintaining a consistent speed and efficiency.
- Replacement of Worn Parts: Do not wait for a complete failure to replace parts that are visibly worn or damaged. Proactively replacing rollers, bearings, or other components as needed can prevent more serious issues down the line and helps in maintaining the high-speed capabilities of the conveyor system.
Choosing high-quality high speed conveyor rollers can significantly reduce the frequency and complexity of maintenance needed. Here are four reasons why investing in high-quality rollers is beneficial:
- Durability: High-quality rollers are typically made from superior materials that can withstand the high demands of conveyor operations without failing, thereby reducing the need for frequent replacements.
- Reduced Downtime: Superior build quality ensures that rollers perform consistently over longer periods, minimizing the risk of downtime due to failures or maintenance issues.
- Lower Maintenance Costs: While high-quality rollers might have a higher upfront cost, the longer life and reduced maintenance needs make them more cost-effective in the long run.
- Enhanced Performance: High-quality high speed conveyor rollers are designed to meet specific operational demands efficiently, which means they are more likely to maintain their performance standards even under high load and speed conditions.
By following these maintenance tips and choosing high-quality high speed conveyor rollers, businesses can ensure efficient, reliable, and cost-effective operations across various industrial applications.
FAQs About High Speed Conveyor Rollers
Conveyor rollers come in various types, each designed to meet specific industrial needs. The primary types include:
Gravity Rollers: These are the simplest form, using gravity to move items across the horizontal or slightly inclined paths. They are ideal for lightweight packages and have low installation and maintenance costs.
Powered Rollers: These rollers are motorized and can move items uphill, downhill, or horizontally without manual effort. They are typically used in large industrial applications.
Grooved Rollers: Designed with grooves that can accommodate round belts for driving the rollers, these are used in lightweight applications and help in guiding the product.
Tapered Rollers: These are used in curves on conveyor systems to maintain the orientation and positioning of items as they move along the track.
Impact Rollers: Positioned at points where products are loaded onto the conveyor, impact rollers are reinforced to absorb the shock and impact of loading operations.
Each type of roller offers distinct advantages and is chosen based on the specific requirements of the conveyor system, such as the weight of the materials, the speed of movement needed, and the environment in which the conveyor will operate.
The primary purpose of rollers in a conveyor system is to facilitate the easy and efficient movement of goods across a facility. Rollers provide support and surface movement as products or materials are transferred from one point to another. They help in reducing friction and making the transportation process smoother, faster, and less labor-intensive. Rollers are crucial in automating processes and increasing productivity in manufacturing, packaging, and distribution centers. They are also adaptable to different materials and environmental conditions, depending on the type of roller material used. This adaptability ensures that irrespective of the operational demands, there is a roller system capable of meeting those needs effectively.
A power roller conveyor, also known as a motorized roller conveyor, is a type of conveyor system where individual rollers are powered by motors, which allows for the movement of goods along the conveyor path without manual force. This system is particularly useful in handling heavy loads or where controlled movement of items is necessary. Power roller conveyors are configurable for speed and can be designed to start and stop according to the operational needs, making them highly efficient for assembly lines, sorting operations, and other automated processes. They can be either chain-driven or belt-driven, depending on the application, and are known for their precision and reliability in continuous use settings.
The HS (Harmonized System) code for conveyor rollers is essential for international trade and customs declarations. The specific HS code for conveyor rollers can vary by country and specific product details, but generally, they fall under the heading 8431, which is used for parts of lifting, handling, loading or unloading machinery. For conveyor rollers, a typical HS code might be 843139, which refers to other parts of elevators and conveyors. Importers and exporters need this code to comply with international shipping regulations and to determine tariffs and duties. It’s important to consult the latest customs tariff codes specific to the country of import or export to ensure accuracy in documentation and compliance.
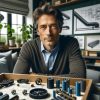
Jordan Smith, a seasoned professional with over 20 years of experience in the conveyor system industry. Jordan’s expertise lies in providing comprehensive solutions for conveyor rollers, belts, and accessories, catering to a wide range of industrial needs. From initial design and configuration to installation and meticulous troubleshooting, Jordan is adept at handling all aspects of conveyor system management. Whether you’re looking to upgrade your production line with efficient conveyor belts, require custom conveyor rollers for specific operations, or need expert advice on selecting the right conveyor accessories for your facility, Jordan is your reliable consultant. For any inquiries or assistance with conveyor system optimization, Jordan is available to share his wealth of knowledge and experience. Feel free to reach out at any time for professional guidance on all matters related to conveyor rollers, belts, and accessories.