The Essential Guide to Quarry Conveyor Rollers
Quarry conveyor rollers are integral components of the material handling systems used in the quarry industry. These rollers support and move conveyor belts, which transport bulk materials like sand, gravel, and crushed stone from one point to another within the quarry. The efficiency and durability of quarry conveyor rollers are crucial, as they directly influence the productivity and operational costs of quarry operations. Understanding the types, materials, and maintenance requirements of these rollers is essential for optimizing their performance and lifespan. This introduction aims to shed light on the significance and mechanics of quarry conveyor rollers in the modern quarrying environment.
What are Quarry Conveyor Rollers Systems
Quarry conveyor systems, with their various types and uses, are pivotal in optimizing the operational efficiency of a quarry. At the heart of these systems are the quarry conveyor rollers, which facilitate the movement and management of large volumes of raw materials. This section explores four distinct types of quarry conveyor rollers and their specific applications, as well as their indispensable role in the quarry industry.
Different Types and Their Uses
- Impact Rollers: Positioned at loading points, impact rollers are designed to absorb the shock and impact of heavy materials falling onto the belts, thus protecting both the conveyor belt and the quarry conveyor rollers from damage.
- Return Rollers: These are used on the underside of conveyor belts to support the return section, ensuring smooth operation and extending the lifespan of the belt and other quarry conveyor rollers.
- Troughing Rollers: Set at angles to form a trough shape on the conveyor belt, these rollers help contain materials, preventing spillage and ensuring that materials are centered and secure during transport.
- Guide Rollers: Placed on the sides of conveyor systems, guide rollers prevent the conveyor belt from slipping off track, which is crucial for maintaining the alignment and efficiency of the quarry conveyor rollers.
Importance in the Quarry Industry
- Efficiency Enhancement: Quarry conveyor rollers streamline the transportation of materials across the quarry, reducing the need for truck haulage and thus lowering operational costs.
- Safety Improvements: By automating the movement of heavy and potentially hazardous materials, quarry conveyor rollers minimize the risk of workplace accidents associated with manual handling.
- Increased Productivity: Reliable quarry conveyor rollers ensure continuous and efficient operation, which directly translates to higher productivity and increased output.
- Maintenance Reduction: Durable and well-designed quarry conveyor rollers decrease downtime caused by maintenance and repairs, ensuring consistent operations and lower maintenance costs.
Understanding these elements helps clarify why quarry conveyor rollers are not merely components but are indeed crucial to the effective functioning of quarry conveyor systems. Their design, quality, and maintenance have direct implications on the productivity and safety of quarry operations.
Case Study: Harpscreen About Quarry Conveyor Rollers
In the quarry industry, where the demand for durable and efficient machinery is at its peak, the importance of reliable quarry conveyor rollers cannot be overstated. Harpscreen exemplifies excellence in this sector, emerging as a pivotal player in the manufacturing and supply of quarry conveyor rollers and other related products.
Overview of Harpscreen
Harpscreen, founded over two decades ago, has established itself as a leading manufacturer in the quarrying industry, specializing in quarry conveyor rollers and screening media. The company has built a reputation for reliability and innovation, serving numerous quarries and mining operations across the globe. With a focus on customer needs, Harpscreen tailors its products to meet the unique demands of each quarry’s operating environment.
Harpscreen’s Specialization and Product Offerings
Harpscreen’s core specialization lies in the production of high-quality quarry conveyor rollers designed to withstand the rigorous conditions of the quarry environment. Their product lineup includes a wide range of rollers, from standard to customized solutions, engineered for optimal performance and longevity. Additionally, Harpscreen offers a variety of screening media, including woven wire, polyurethane screens, and rubber screens, thus providing comprehensive solutions for material handling and processing.
Harpscreen’s Services and Commitment to Quality
Harpscreen’s commitment to quality is evident in every aspect of their operations, from design and manufacturing to customer service and after-sales support. The company employs rigorous testing procedures to ensure that all quarry conveyor rollers meet the highest standards of durability and efficiency. Harpscreen also provides expert consultation and support services, helping clients to select the right products for their specific needs and offering guidance on maintenance practices to maximize the lifespan and effectiveness of the rollers. This dedication not only to product quality but also to customer satisfaction and continuous improvement has solidified Harpscreen’s position as a trusted leader in the quarrying industry.
Variety in Quarry Conveyor Rollers
The diversity in quarry conveyor rollers is key to accommodating the varied needs of the quarry industry, where different materials and load requirements dictate the specifications of the conveyor system. This section delves into the variety of quarry conveyor rollers available, focusing on different sizes and the role of gravity in these systems.
Description of Different Sizes
Quarry conveyor rollers come in various sizes to handle different volumes and weights of materials. The table below showcases two common sizes and their typical applications:
Roller Size | Diameter | Typical Load Capacity | Common Applications |
---|---|---|---|
4" Conveyor Roller | 4 inches | Up to 800 lbs | Medium-duty material handling |
1" Diameter Roller | 1 inch | Up to 100 lbs | Light-duty operations such as screening processes |
These dimensions illustrate the versatility in the quarry conveyor rollers’ design, allowing them to be tailored to specific tasks, from heavy-duty material transport to lighter screening activities. The diameter and length of a roller influence its load-bearing capacity and are chosen based on the volume and weight of the materials to be transported.
Gravity’s Role in Roller Conveyors
Gravity plays a crucial role in the function of roller conveyors, particularly in systems designed to utilize natural forces for the movement of materials. Gravity roller conveyors are an economical and energy-efficient option, particularly suitable for downward or inclined conveying paths. In these setups, quarry conveyor rollers are spaced in a way that supports the weight of the material but allows free movement down the conveyor line without additional power, reducing energy costs and maintenance requirements.
The selection of quarry conveyor rollers in terms of size and type (gravity or powered) is critical for optimizing efficiency and reducing operational costs in quarry operations. Proper understanding and implementation of these components ensure that material handling processes are both effective and cost-efficient.
Industrial and Heavy Duty Quarry Conveyor Rollers
In the demanding environment of a quarry, the durability and robustness of industrial and heavy-duty quarry conveyor rollers are critical. This section discusses the characteristics of these rollers, along with their uses and benefits in industrial applications.
Explanation of Heavy-Duty Quarry Conveyor Rollers
Heavy-duty quarry conveyor rollers are designed to handle the extreme conditions of the quarry industry. These rollers are built with thicker steel tubes, high-load capacity bearing, and solid steel axels to withstand heavy weights and continuous operation. Their robust construction helps minimize downtime and maintenance costs, ensuring continuous material flow. The coatings and materials used in these rollers are also selected to resist wear and corrosion, which is essential in harsh working environments.
Uses and Benefits of Industrial Quarry Conveyor Rollers
- Increased Load Capacity: Industrial quarry conveyor rollers are capable of supporting significantly higher loads compared to standard rollers. This capability is crucial in quarries where large volumes of heavy materials like rock and aggregate need to be moved efficiently.
- Reduced Maintenance Needs: Due to their robust construction, heavy-duty rollers require less frequent replacements and can operate under higher stress without failure. This durability translates into lower maintenance costs and less operational downtime.
- Enhanced Productivity: With the ability to handle more material at faster rates, industrial rollers contribute to enhanced productivity. They are essential in high-throughput applications where speed and efficiency are paramount.
- Adaptability to Harsh Environments: Industrial quarry conveyor rollers are designed to perform in the adverse conditions of quarries, including exposure to dust, water, and varying temperatures. Their design includes features like sealed bearings and specialized lubrication to cope with such environments.
By choosing the right type of quarry conveyor rollers—whether for new installations or upgrades—quarries can achieve better efficiency, reliability, and profitability. The substantial benefits of employing heavy-duty and industrial rollers make them indispensable in the rugged terrain of quarry operations.
Replacement Quarry Conveyor Rollers
The regular replacement of quarry conveyor rollers is a critical maintenance task that ensures the smooth and efficient operation of conveyor systems in the quarry industry. This section outlines the importance of this practice, the procedures involved, and how companies like Quarry Parts and Ultimation Inc. support these maintenance efforts.
Importance and Procedures for Roller Replacement
- Maintaining System Efficiency: Worn or damaged rollers can cause conveyor belts to operate inefficiently, leading to potential slowdowns or halts in production. Regular replacement keeps the system running smoothly.
- Preventing Damage to Conveyor Belts: Damaged rollers can lead to uneven belt wear or cause the conveyor belt to deviate from its intended path, which might result in costly belt damage or replacements.
- Reducing Downtime: Proactively replacing quarry conveyor rollers helps avoid unscheduled downtime caused by sudden roller failures. This planned maintenance allows for better scheduling and less interruption to operations.
- Ensuring Worker Safety: Faulty rollers can pose risks to safety. Ensuring all rollers are in good condition helps prevent accidents caused by malfunctioning equipment.
Procedures for Replacement:
- Inspection: Regularly inspect rollers for signs of wear, such as visible damage or unusual noise, and measure performance against established performance metrics.
- Removal: Safely disconnect the power supply and use appropriate tools to remove the damaged or worn rollers without affecting the structural integrity of the conveyor.
- Installation: Install the new rollers, ensuring they are correctly aligned and securely fastened to prevent any movement that could lead to premature wear.
- Testing: After replacement, test the conveyor system to ensure it is running smoothly and the new rollers are functioning correctly.
How Companies Like Quarry Parts and Ultimation Inc. Facilitate the Replacement Process
Companies specializing in conveyor components, such as Quarry Parts and Ultimation Inc., play a crucial role in facilitating the replacement of quarry conveyor rollers. They offer:
- Wide Range of Products: These companies provide a broad selection of rollers, ensuring that they have the correct size and type of roller for various conveyor systems.
- Custom Solutions: For unique or heavy-duty applications, they offer custom-designed rollers that meet specific operational requirements.
- Technical Support: They provide expert advice and support, helping quarries identify the right rollers for their needs and assisting with installation procedures.
- Logistical Support: With efficient supply chains, these companies ensure timely delivery of replacement rollers to minimize downtime for quarries.
These services are integral to maintaining the operational integrity of quarry conveyor systems, ensuring that replacement procedures are as efficient and effective as possible.
Used Quarry Conveyor Rollers and Their Benefits
In an industry where cost management is crucial for profitability, the use of used quarry conveyor rollers can be a viable and economically advantageous strategy. This section discusses the practicality of integrating used rollers into quarry operations and the associated benefits.
Discussion on Used Quarry Conveyor Rollers
Used quarry conveyor rollers are typically sourced from dismantled or upgraded systems, offering an economical alternative to purchasing new equipment. Before being reintroduced into operations, these rollers undergo rigorous inspections to ensure they meet operational standards. They are evaluated for structural integrity, bearing performance, and overall wear. Only rollers that pass these stringent assessments are considered suitable for reuse, ensuring they can effectively perform under the demanding conditions of quarry environments.
Benefits and Cost-Effectiveness
- Reduced Initial Investment: One of the primary advantages of opting for used quarry conveyor rollers is the significantly lower cost compared to new rollers. This reduction in capital expenditure is particularly beneficial for smaller operations or those looking to expand their system without a substantial budget.
- Environmental Sustainability: Utilizing used rollers contributes to environmental conservation by reducing waste and the demand for new raw materials. This practice supports sustainability initiatives within the industry, aligning with global efforts to minimize the environmental footprint of industrial activities.
- Availability and Convenience: Used rollers are often readily available, providing a quick solution for replacement needs without the lengthy lead times associated with new equipment manufacturing. This availability can be crucial in minimizing downtime during unscheduled maintenance or repairs.
- Testing and Proven Performance: Since used quarry conveyor rollers have already been operational, they have a proven track record of performance. This can offer an additional layer of reassurance compared to new rollers, which, while manufactured to high standards, have yet to be tested in the field.
Incorporating used quarry conveyor rollers into a conveyor system can be a smart, economical choice that benefits both the operation and the environment. With proper inspection and maintenance, these rollers can continue to provide reliable service, making them an attractive option for cost-conscious quarry operators.
Buying Quarry Conveyor Rollers
Purchasing the right quarry conveyor rollers is crucial for the efficiency and longevity of conveyor systems in the quarry industry. This section provides insights into the factors to consider when buying these vital components and explains the importance of brackets in their installation.
Factors to Consider When Buying Quarry Conveyor Rollers
- Material Quality and Type: The material from which the rollers are made determines their durability and suitability for different environments. Steel rollers are common for their strength and durability, especially in harsh quarry conditions, whereas plastic rollers might be used in less demanding situations.
- Load Capacity: It is essential to choose rollers that can handle the expected load capacity. Overloading rollers can lead to rapid wear and failure, so understanding the weight of materials that the conveyor will carry is crucial.
- Operating Environment: The environment in which the rollers will operate influences the choice of material and type of roller. For example, rollers used in damp or highly abrasive environments may require special coatings or materials like stainless steel to prevent corrosion and wear.
- Compatibility with Existing Systems: The rollers must be compatible with the existing conveyor system. This includes the size, mounting setups, and the type of bearings used, to ensure seamless integration and operation.
Importance of Brackets in Quarry Conveyor Rollers’ Installation
- Support and Stability: Brackets provide critical support and stability to conveyor rollers, ensuring that they remain aligned and secure during operation. Properly installed brackets help prevent the rollers from shifting, which can cause uneven wear and potential malfunction.
- Adjustability: Brackets often allow for adjustability in the positioning of the rollers, enabling fine-tuning of the conveyor belt’s tension and tracking. This adjustability is crucial for maintaining optimal performance and extending the life of both the belt and the rollers.
- Ease of Maintenance: With robust and appropriately designed brackets, the maintenance of quarry conveyor rollers becomes more manageable. Brackets designed for easy access facilitate quicker roller changes and adjustments, reducing downtime and maintenance costs.
- Enhanced Durability: Brackets also contribute to the overall durability of the conveyor system. They absorb some of the vibrations and shocks during operation, which protects the rollers and the conveyor belt from excessive wear and damage.
Selecting the right quarry conveyor rollers involves careful consideration of these factors to ensure the efficiency, reliability, and longevity of the conveyor system. Additionally, understanding the role of brackets in the installation and operation of these rollers is essential for maintaining the structural integrity and operational efficiency of the conveyor system.
FAQs About Quarry Conveyor Rollers
Conveyor rollers are essential components of conveyor systems, and they come in various types to accommodate different industrial needs. The main types include:
Gravity Rollers: These are the simplest form of conveyor rollers and use gravity to move products along a conveyor. They are ideal for lightweight packages and have a simple, cost-effective design.
Driven Rollers: Powered by motors or chains, driven rollers are essential for handling heavy loads and can control the speed and direction of the conveyor belt.
Impact Rollers: Positioned at loading points, impact rollers are designed to absorb the shock and weight of materials falling onto the belt, thus protecting both the belt and other rollers from damage.
Troughing Rollers: These are configured to form a trough on the conveyor belt, helping to keep materials in place during transport, especially useful in the bulk material handling industry.
Each type serves specific functions and is selected based on the operational requirements of the conveyor system, including load capacity, environmental conditions, and material characteristics.
Rollers for the mining industry are designed to withstand harsh conditions found in mining operations. They must be robust, corrosion-resistant, and capable of handling heavy loads. Key features include:
High Load Capacity: Mining rollers support heavy loads of mined materials, such as ore and coal, which are abrasive and heavy.
Durability: These rollers are manufactured from materials that resist wear and corrosion, such as reinforced steel or specialized alloys, to ensure longevity in hostile mining environments.
Sealed Bearings: To prevent dust and debris from causing malfunctions, rollers in the mining industry often feature sealed bearings that protect the internal mechanisms.
The effectiveness of these rollers directly affects the efficiency and safety of mining operations, making them critical for cost-effective and reliable material handling in the mining sector.
Rollers in a conveyor system serve several crucial functions:
Supporting the Conveyor Belt: Rollers provide a stable and flat surface for the conveyor belt to move smoothly.
Facilitating Material Transport: By allowing the conveyor belt to move efficiently and with less friction, rollers help to transport materials from one point to another with minimal effort.
Controlling Speed and Direction: In powered conveyor systems, rollers can help regulate the speed and direction of the belt, enhancing the control over material flow.
Reducing Operational Strain: Properly functioning rollers distribute the weight of materials evenly, reducing wear and tear on the conveyor belt and motor.
Effective rollers are key to maximizing the performance and longevity of a conveyor system, emphasizing the importance of selecting the right type of roller for specific applications.
Identifying the best roller conveyor manufacturer depends on several factors, including industry reputation, product quality, customer service, and technical expertise. Companies like Hytrol, Interroll, and Fenner Drives are often regarded highly within the industry due to their:
Innovative Designs: These manufacturers offer a range of conveyor solutions that incorporate the latest technology and materials.
Robust Product Quality: They are known for manufacturing durable and reliable conveyor rollers that meet or exceed industry standards.
Comprehensive Customer Support: From pre-sales advice to after-sales service, these companies provide excellent customer support to ensure their products meet the specific needs of their clients.
Global Reach and Accessibility: They have extensive distribution networks, ensuring that their products are accessible worldwide and support is available when needed.
When choosing a manufacturer, consider their specialization in your industry and their ability to provide tailored solutions that meet your specific requirements.
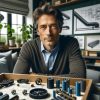
Jordan Smith, a seasoned professional with over 20 years of experience in the conveyor system industry. Jordan’s expertise lies in providing comprehensive solutions for conveyor rollers, belts, and accessories, catering to a wide range of industrial needs. From initial design and configuration to installation and meticulous troubleshooting, Jordan is adept at handling all aspects of conveyor system management. Whether you’re looking to upgrade your production line with efficient conveyor belts, require custom conveyor rollers for specific operations, or need expert advice on selecting the right conveyor accessories for your facility, Jordan is your reliable consultant. For any inquiries or assistance with conveyor system optimization, Jordan is available to share his wealth of knowledge and experience. Feel free to reach out at any time for professional guidance on all matters related to conveyor rollers, belts, and accessories.