Conveyor Belt Sweeper: Belt Cleaning Systems
Conveyor belt sweeper and cleaner brushes are essential tools for maintaining the cleanliness and efficiency of conveyor systems. These brushes effectively remove debris, dust, and material buildup from the conveyor belt surface, ensuring smooth operation and preventing damage. Regular use of a conveyor belt sweeper helps reduce maintenance costs, extend the lifespan of the belt, and improve overall system performance. Keeping conveyor belts clean is crucial for minimizing downtime, maintaining product quality, and ensuring a safe working environment.
Conveyor Belt Sweeper: Conveyor Belt Cleaning Systems
Definition and Purpose of Conveyor Belt Cleaning Systems
Conveyor belt sweeper are designed to scrape material off the conveyor belt. ensure clean conveyor belts , enhancing safety and productivity.A conveyor belt cleaning system is designed to remove material buildup and debris from the surface of conveyor belts. This system is essential for maintaining the efficiency and effectiveness of conveyor operations. The primary purpose of a conveyor belt cleaning system is to:
- Prevent Material Carryback: Material carryback refers to the residual material that sticks to the conveyor belt after the discharge point. If not removed, carryback can accumulate and cause issues such as belt misalignment, increased wear, and contamination of products.
- Reduce Maintenance Costs: Effective cleaning systems minimize the need for frequent manual cleaning and maintenance, reducing labor costs and downtime.
- Enhance Belt Longevity: By preventing material buildup and reducing wear and tear, cleaning systems extend the lifespan of conveyor belts.
- Improve Safety: Clean conveyor belts reduce the risk of accidents caused by slipping or falling materials.
- Maintain Operational Efficiency: A clean belt operates more smoothly, reducing friction and power consumption, and enhancing overall efficiency.
Key Components of a Conveyor Belt Cleaning System
A conveyor belt cleaning system typically consists of several key components, each playing a vital role in ensuring effective cleaning:
- Primary Scraper: Positioned at the head pulley, the primary scraper removes the bulk of material from the belt. It is usually made from robust materials like polyurethane or tungsten carbide.
- Secondary Scraper: Located further along the belt, the secondary scraper removes residual material that the primary scraper might have missed. This scraper provides additional cleaning to ensure a cleaner belt surface.
- Tertiary Scraper: Used in specific applications requiring extra cleaning, the tertiary scraper offers another layer of cleaning, particularly in high-demand environments.
- Conveyor Belt Sweeper: A conveyor belt sweeper is an essential component designed to sweep off fine particles and debris from the belt surface. Sweepers are typically placed at various points along the conveyor to ensure continuous cleaning.
- Roller Brushes: Roller brushes are cylindrical brushes that rotate and scrub the belt surface, removing finer particles and debris. They are often used in conjunction with scrapers for thorough cleaning.
- Spray Bars: Spray bars use high-pressure water or cleaning solution to wash the belt surface. They are particularly effective in removing sticky materials and fine particles.
- Vacuum Systems: Vacuum systems suck up fine dust and particles from the belt, ensuring a dust-free environment and reducing contamination.
- Control Systems: Modern cleaning systems are equipped with control systems that automate the cleaning process. These systems monitor belt conditions and adjust the cleaning components as needed to maintain optimal performance.
Conveyor Belt Sweeper: The Role of Roller Brushes in Conveyor Belt Cleaning
Explanation of Roller Brushes for Conveyor Belt Cleaning
Roller brushes are an integral part of conveyor belt cleaning systems. These brushes are designed to rotate and scrub the belt surface, effectively removing fine particles, debris, and material buildup. Roller brushes are typically cylindrical in shape and are mounted on a shaft that rotates, driven by the movement or a motor of the conveyor belt itself.
How Roller Brushes Help in Maintaining Conveyor Efficiency
Roller brushes contribute significantly to maintaining conveyor efficiency in several ways:
- Thorough Cleaning: Roller brushes provide thorough cleaning by scrubbing the belt surface and removing particles that primary and secondary scrapers might miss. This ensures a cleaner belt, reducing the risk of material carryback and buildup.
- Reduced Wear and Tear: By keeping the belt surface clean, roller brushes reduce the wear and tear caused by abrasive materials. This extends the lifespan of the conveyor belt and reduces maintenance costs.
- Enhanced Belt Tracking: Material buildup can cause the belt to misalign or track incorrectly. Roller brushes help maintain proper belt alignment by removing debris and ensuring a smooth belt surface.
- Improved Product Quality: In industries where product contamination is a concern, such as food processing or pharmaceuticals, roller brushes ensure that the belt remains clean and free from contaminants, thereby improving product quality.
- Energy Efficiency: A clean belt experiences less friction, which reduces the energy required to drive the conveyor system. Roller brushes help maintain a low-friction surface, contributing to overall energy efficiency.
- Safety: Clean conveyor belts reduce the risk of slip and fall accidents caused by material buildup. Roller brushes enhance workplace safety by maintaining a clean and hazard-free environment.

Conveyor Belt Sweeper: Common Types of Conveyor Belt Scrapers
Various Conveyor Belt Scraper Types
Conveyor belt scrapers are essential components used to clean the belt and prevent material carryback. There are several types of scrapers, each designed for specific applications and cleaning needs. Here, we introduce the most common types of conveyor belt scrapers:
- Primary Scrapers: Also known as pre-cleaners, primary scrapers are positioned at the head pulley and are the first line of defense against material carryback. They are typically made from durable materials like polyurethane or tungsten carbide and are designed to remove the bulk of the material from the belt.
- Secondary Scrapers: Positioned further along the belt, secondary scrapers provide additional cleaning to remove residual material left by the primary scraper. These scrapers are often made from a combination of materials to enhance their cleaning efficiency.
- Tertiary Scrapers: Used in specific applications requiring extra cleaning, tertiary scrapers offer another layer of cleaning. They are particularly useful in environments with high material buildup or where thorough cleaning is critical.
- V-Plow Scrapers: V-plow scrapers are designed to clean the return side of the conveyor belt. They are mounted in a V-shape and are effective at removing material that adheres to the underside of the belt.
- Brush Scrapers: Brush scrapers use rotating brushes to clean the belt surface. They are particularly effective at removing fine particles and sticky materials.
- Belt Cleaning Systems with Conveyor Belt Sweepers: These systems combine scrapers, brushes, and sweepers to provide comprehensive cleaning. Conveyor belt sweepers play a crucial role in these systems by sweeping off fine particles and debris, ensuring a clean belt surface.
Applications and Benefits of Each Scraper Type
Primary Scrapers
Applications: Primary scrapers are used in a wide range of industries, including mining, quarrying, and bulk material handling. They are particularly effective in removing large amounts of material from the belt.
Benefits:
- Effective Material Removal: Primary scrapers remove the bulk of material, reducing carryback and preventing buildup.
- Durability: Made from robust materials, primary scrapers are designed to withstand harsh conditions and heavy-duty use.
- Reduced Maintenance: By removing large amounts of material, primary scrapers reduce the frequency of manual cleaning and maintenance.
Secondary Scrapers
Applications: Secondary scrapers are used in conjunction with primary scrapers in industries where thorough cleaning is essential, such as food processing, pharmaceuticals, and fine material handling.
Benefits:
- Enhanced Cleaning: Secondary scrapers provide additional cleaning, ensuring a cleaner belt surface.
- Improved Product Quality: By removing residual material, secondary scrapers help prevent contamination and maintain product quality.
- Extended Belt Life: Thorough cleaning reduces wear and tear, extending the lifespan of the conveyor belt.
Tertiary Scrapers
Applications: Tertiary scrapers are used in high-demand environments where thorough cleaning is critical, such as in cement plants, steel mills, and power plants.
Benefits:
- Maximum Cleaning Efficiency: Tertiary scrapers provide an additional layer of cleaning, ensuring the belt is as clean as possible.
- Reduced Downtime: By maintaining a clean belt, tertiary scrapers help reduce downtime caused by material buildup and belt misalignment.
- Enhanced Safety: A cleaner belt reduces the risk of slip and fall accidents, improving workplace safety.
V-Plow Scrapers
Applications: V-plow scrapers are used on the return side of the conveyor belt to remove material that adheres to the underside. They are commonly used in mining, aggregate, and bulk material handling industries.
Benefits:
- Effective Return Side Cleaning: V-plow scrapers clean the underside of the belt, preventing material buildup on return rollers and idlers.
- Reduced Maintenance: By keeping the return side clean, V-plow scrapers reduce the frequency of maintenance and extend the life of return rollers.
- Improved Belt Tracking: Clean return sides help maintain proper belt alignment and tracking.
Brush Scrapers
Applications: Brush scrapers are used in industries where fine particles and sticky materials are common, such as food processing, pharmaceuticals, and packaging.
Benefits:
- Thorough Cleaning of Fine Particles: Brush scrapers effectively remove fine particles and sticky materials from the belt surface.
- Reduced Contamination: By maintaining a clean belt, brush scrapers help prevent product contamination and maintain quality standards.
- Enhanced Belt Performance: Regular cleaning with brush scrapers reduces friction and wear, improving overall belt performance.
Belt Cleaning Systems with Conveyor Belt Sweepers
Applications: Comprehensive belt cleaning systems with conveyor belt sweepers are used in a wide range of industries, including mining, manufacturing, food processing, and logistics.
Benefits:
- Complete Cleaning Solution: These systems provide a combination of scrapers, brushes, and sweepers, ensuring thorough cleaning and maintenance of the conveyor belt.
- Reduced Carryback: By removing all types of material, these systems minimize carryback and prevent buildup.
- Extended Belt Life: Regular and effective cleaning reduces wear and tear, extending the lifespan of the conveyor belt.
- Improved Operational Efficiency: Clean conveyor belts operate more smoothly, reducing friction, power consumption, and maintenance needs, leading to enhanced operational efficiency.
Understanding the various components and types of conveyor belt cleaning systems is essential for maintaining the efficiency, performance, and longevity of conveyor belts. By implementing effective cleaning solutions, including primary and secondary scrapers, roller brushes, and conveyor belt sweeper, industries can ensure their conveyor systems remain in optimal condition, reducing maintenance costs, preventing material carryback, and enhancing overall productivity.
Do I Need Conveyor Belt Sweeper?
Whether you need a conveyor belt sweeper depends on your specific operational needs and the nature of your conveyor system. Here are some factors to consider:
Material Handling and Spillage
- Type of Material: If your conveyor belt handles materials prone to sticking or spilling, a sweeper can help keep the belt clean and reduce material loss.
- Amount of Material: High volume or bulk material transport can lead to significant spillage, making a sweeper beneficial.
System Efficiency and Maintenance
- System Efficiency: Clean belts operate more efficiently and have a longer lifespan. Sweepers can reduce downtime by preventing material build-up that can cause belt misalignment or damage.
- Maintenance Costs: Regular cleaning with sweepers can lower maintenance costs by reducing wear and tear on the belt and other components.
Safety and Regulatory Compliance
- Safety: Accumulated materials can create slip hazards for workers and increase the risk of fires. Sweepers enhance workplace safety by maintaining clean working environments.
- Compliance: In some industries, cleanliness standards and regulations might necessitate the use of sweepers to meet compliance requirements.
Environmental Considerations
- Dust and Debris Control: Sweepers can help manage dust and debris, improving air quality and reducing environmental impact.
- Waste Management: By efficiently collecting spillage, sweepers aid in better waste management practices.
If your operation involves frequent spillage, high-volume material handling, strict cleanliness standards, or safety concerns, investing in a conveyor belt sweeper could be highly beneficial. It’s essential to weigh the initial investment against the long-term savings and operational improvements it can provide.

Choosing the Right Conveyor Belt Scraper Blades
Choosing the right conveyor belt scraper blades is crucial for the efficiency and longevity of your conveyor belt system. Proper scraper blades can significantly reduce maintenance costs, prevent material spillage, and increase the overall productivity of your operations. When selecting the appropriate scraper blades, several factors need to be considered to ensure optimal performance.
Factors to Consider When Selecting Conveyor Belt Scraper Blades
- Material Compatibility: The scraper blade material should be compatible with the materials being conveyed. Different materials have varying levels of abrasiveness, moisture content, and temperature. For instance, handling abrasive materials like coal or ore requires harder, more durable blades, while softer materials like grains may only need a basic urethane blade.
- Conveyor Belt Material: The type of material used in the conveyor belt itself is also crucial. Certain scraper blade materials can cause wear and tear on specific belt types. For example, a metal blade might be too harsh for a fabric-based conveyor belt but suitable for a rubber-based one.
- Blade Design and Configuration: The design and configuration of the scraper blade should match the specific needs of your conveyor system. There are primary, secondary, and tertiary blades designed to handle different levels of cleaning. Primary blades typically deal with bulk material removal, while secondary and tertiary blades provide finer cleaning to ensure minimal material residue.
- Operating Conditions: The environment in which the conveyor belt operates can greatly influence the choice of scraper blades. Factors like temperature extremes, humidity, and exposure to chemicals should be considered. Blades that are resistant to these conditions will last longer and perform better.
- Maintenance and Replacement: Consider how easy it is to maintain and replace the scraper blades. Blades that require less frequent maintenance and are easier to replace can save time and reduce downtime in your operations. Quick-release mechanisms and modular designs are beneficial features to look for.
- Cost-effectiveness: While it might be tempting to go for the cheapest option, it’s important to weigh the initial cost against the longevity and performance of the scraper blades. High-quality blades might be more expensive upfront but can offer better value over time through reduced maintenance and longer life spans.
Materials and Design Options for Scraper Blades
The materials used for scraper blades vary widely, each offering unique benefits suited to different applications. Common materials include:
- Polyurethane: Known for its flexibility and resistance to wear, polyurethane is ideal for light to medium-duty applications. It is gentle on conveyor belts and can handle a variety of materials without causing damage.
- Carbide: Tungsten carbide blades are extremely durable and resistant to abrasion. They are suitable for heavy-duty applications involving highly abrasive materials. These blades offer long service life but can be more expensive.
- Steel: Steel blades, particularly hardened steel, are robust and can handle very abrasive materials. They are less flexible than polyurethane and can be harsh on some conveyor belts, so they are best used in heavy-duty applications where belt wear is not a significant concern.
- Ceramic: Ceramic blades provide exceptional wear resistance and are ideal for applications involving very abrasive materials. They offer a long service life but are typically more costly.
Design options for scraper blades include:
- Straight Blades: Simple and effective, straight blades are used in primary cleaning positions to remove the bulk of the material.
- Angled Blades: These are designed to improve cleaning efficiency by applying different pressure points on the conveyor belt surface.
- Segmented Blades: Segmented or modular blades allow for parts of the blade to be replaced individually, which can be more cost-effective and easier to maintain.
- Spring-loaded Blades: These blades can adapt to belt variations and maintain consistent pressure, enhancing cleaning efficiency and blade life.
Conveyor Belt Sweeper: Benefits of Flexco Belt Cleaners
Flexco is a well-known name in the conveyor belt cleaning industry, offering a wide range of products designed to improve the efficiency and longevity of conveyor belt systems. Their belt cleaners are recognized for their innovative design, high-quality materials, and effective performance.
Flexco Belt Cleaners
Flexco belt cleaners are engineered to provide optimal cleaning performance for a variety of conveyor belt applications. They offer a comprehensive range of primary, secondary, and tertiary belt cleaners designed to handle different cleaning requirements and belt types. Whether dealing with light, medium, or heavy-duty applications, Flexco has a solution tailored to meet the specific needs of each operation.
Key Features and Advantages of Using Flexco Belt Cleaners
- High-Quality Materials: Flexco uses premium materials in their belt cleaners, such as high-grade polyurethane and tungsten carbide. These materials ensure durability and effective cleaning, even in the most challenging environments.
- Innovative Design: Flexco belt cleaners are designed with features that enhance their performance and ease of use. For example, their Quick-Change systems allow for fast and easy blade replacement, minimizing downtime and maintenance efforts.
- Versatility: Flexco offers a wide range of belt cleaners that can be used in various applications, from mining and aggregate to food processing and recycling. Their products are designed to handle different materials, belt types, and operating conditions.
- Efficiency: By effectively removing carryback, Flexco belt cleaners help reduce material buildup on conveyor belts and other components. This results in less wear and tear on the belt, reducing maintenance costs and extending the life of the conveyor system.
- Improved Safety: Cleaner conveyor belts mean less material spillage, which can pose safety hazards. Flexco belt cleaners help maintain a safer work environment by minimizing spillage and reducing the risk of accidents.
- Energy Savings: Efficient cleaning reduces the strain on the conveyor system, leading to lower energy consumption. This not only saves on operational costs but also contributes to a more sustainable operation.
Conveyor Belt Sweeper: Installation and Maintenance of Conveyor Belt Cleaning Systems
Proper installation and maintenance of conveyor belt cleaning systems are essential for ensuring their effectiveness and longevity. A well-installed and maintained system can significantly reduce downtime, enhance productivity, and lower operational costs.
Steps for Installing Conveyor Belt Cleaning Systems
- Pre-Installation Planning: Before installation, conduct a thorough assessment of your conveyor system to determine the most suitable type of belt cleaner and its optimal placement. Consider factors such as the type of material being conveyed, the conveyor belt’s speed and width, and the operating environment.
- Preparation: Ensure that the conveyor belt is stopped and properly locked out before beginning the installation process. Gather all necessary tools and equipment, and carefully read the manufacturer’s installation instructions.
- Positioning the Belt Cleaner: Install the belt cleaner in the recommended position relative to the conveyor belt. This typically involves placing primary cleaners at the head pulley and secondary cleaners further down the belt to ensure thorough cleaning.
- Mounting the Belt Cleaner: Securely mount the belt cleaner to the conveyor frame using the provided hardware. Ensure that the cleaner is aligned properly with the belt to maximize cleaning efficiency.
- Adjusting the Blade: Adjust the scraper blade to make proper contact with the conveyor belt. The blade should apply enough pressure to remove material effectively but not so much that it causes excessive wear on the belt.
- Testing and Calibration: After installation, run the conveyor belt to test the cleaner’s performance. Make any necessary adjustments to the blade alignment and pressure to achieve optimal cleaning.
Maintenance Tips to Ensure Longevity and Efficiency
- Regular Inspections: Conduct regular inspections of the conveyor belt cleaning system to identify any signs of wear or damage. Check the condition of the scraper blades, mounting hardware, and other components.
- Blade Replacement: Replace scraper blades as needed to maintain effective cleaning performance. Follow the manufacturer’s recommendations for blade replacement intervals based on the type of material being conveyed and the operating conditions.
- Cleaning and Lubrication: Keep the belt cleaner and its components clean and free from debris. Lubricate any moving parts as recommended by the manufacturer to prevent friction and wear.
- Alignment Checks: Periodically check the alignment of the scraper blade to ensure it is making proper contact with the conveyor belt. Misalignment can lead to ineffective cleaning and increased wear on the belt and blade.
- Adjustments: Make any necessary adjustments to the scraper blade pressure and alignment to maintain optimal cleaning performance. Over time, the blade may need to be repositioned to compensate for wear.
- Documentation and Record Keeping: Maintain detailed records of all maintenance activities, including inspections, blade replacements, and adjustments. This documentation can help track the performance of the cleaning system and identify any recurring issues.
Selecting the right conveyor belt scraper blades and ensuring proper installation and maintenance of conveyor belt cleaning systems are critical for maximizing the efficiency and longevity of your conveyor operations. By considering factors such as material compatibility, operating conditions, and maintenance requirements, you can choose the most suitable scraper blades for your needs. Flexco belt cleaners offer a range of high-quality, innovative solutions designed to enhance conveyor performance and reduce operational costs. Following best practices for installation and maintenance will ensure that your conveyor belt cleaning systems operate effectively and efficiently for years to come.

Troubleshooting Common Issues with Conveyor Belt Sweeper
A well-functioning conveyor belt sweeper is crucial for maintaining the efficiency and longevity of conveyor belt systems. However, like any piece of industrial equipment, conveyor belt cleaners can encounter various issues that impede their performance. Understanding how to identify and resolve these problems, along with implementing preventive measures, can save time and reduce maintenance costs.
Identifying and Resolving Common Problems with Conveyor Belt Cleaners
- 1.Inadequate Cleaning Performance Symptoms: Residual material on the conveyor belt, material build-up on pulleys, and increased spillage.
- Causes:
- Incorrect blade pressure or alignment.
- Worn or damaged scraper blades.
- Inappropriate blade material for the conveyed material.
- Solutions:
- Adjust Blade Pressure: Ensure the scraper blade applies adequate pressure to the belt. Too much pressure can cause excessive wear, while too little can result in poor cleaning.
- Check Blade Alignment: Verify that the blade is correctly aligned with the conveyor belt. Misalignment can lead to uneven cleaning and increased wear.
- Replace Worn Blades: Inspect blades regularly and replace them when they show signs of wear or damage. Use blades made from materials suitable for the specific application to enhance cleaning efficiency.
- 2.Excessive Wear on Blades or Belt Symptoms: Rapid deterioration of scraper blades or noticeable wear patterns on the conveyor belt.
- Causes:
- Excessive blade pressure.
- Use of inappropriate blade material.
- Misalignment of the scraper blade.
- Solutions:
- Adjust Pressure: Reduce the pressure applied by the scraper blade to decrease wear on both the blade and the conveyor belt.
- Use Correct Blade Material: Ensure the blade material is suitable for the conveyor belt and the material being conveyed. Softer materials like urethane can reduce wear on the belt.
- Realign Blade: Regularly check and adjust the alignment of the scraper blade to ensure even contact with the belt surface.
- 3.Blade Chatter or Vibration Symptoms: Noisy operation, inconsistent cleaning performance, and visible vibration of the blade.
- Causes:
- Blade not securely mounted.
- Improper tension or alignment.
- Worn or uneven belt surface.
- Solutions:
- Secure Mounting: Ensure the blade is firmly mounted and all fasteners are tightened.
- Adjust Tension and Alignment: Correct the tension and alignment of the blade to eliminate chatter and ensure smooth operation.
- Inspect Belt Surface: Check for wear or damage on the belt surface that could cause vibration. Repair or replace the belt if necessary.
- 4.Material Build-up on Cleaner Symptoms: Material accumulation on the scraper blade and surrounding components, leading to reduced cleaning efficiency.
- Causes:
- Sticky or wet materials.
- Inadequate cleaning frequency.
- Ineffective blade design for the material type.
- Solutions:
- Increase Cleaning Frequency: Adjust the cleaning frequency to prevent material build-up. For particularly sticky or wet materials, more frequent cleaning may be necessary.
- Choose Appropriate Blade Design: Select a scraper blade designed to handle the specific material type. Some designs are better suited for sticky materials and can help reduce build-up.
- Install Secondary Cleaners: Consider installing secondary or tertiary belt cleaners to handle residual material and prevent build-up.
- 5.Corrosion or Damage to Components Symptoms: Rust or other signs of corrosion on metal parts, physical damage to cleaner components.
- Causes:
- Exposure to harsh chemicals or extreme environmental conditions.
- Use of inappropriate materials for the operating environment.
- Solutions:
- Use Corrosion-Resistant Materials: Choose cleaner components made from corrosion-resistant materials such as stainless steel or specialized coatings.
- Protective Coatings: Apply protective coatings to vulnerable parts to prevent corrosion.
- Environmental Controls: Implement measures to control the operating environment, such as reducing exposure to moisture or chemicals.
Preventive Measures to Avoid Future Issues
- Regular Maintenance and Inspection Establish a routine maintenance schedule that includes regular inspections of the conveyor belt cleaner. Check for signs of wear, damage, and proper alignment. Regular maintenance helps identify potential problems before they become major issues.
- Proper Installation Ensure that the conveyor belt sweeper is installed correctly according to the manufacturer’s guidelines. Proper installation is critical for optimal performance and can prevent many common issues related to misalignment and inadequate pressure.
- Choose the Right Cleaner for the Application Selecting the appropriate conveyor belt cleaner for your specific application is essential. Consider factors such as the type of material being conveyed, the operating environment, and the conveyor belt’s speed and width. Using the right cleaner reduces the likelihood of problems related to inadequate cleaning and excessive wear.
- Training and Education Provide proper training for personnel responsible for operating and maintaining the conveyor belt cleaner. Educated operators are more likely to detect and address issues early, reducing downtime and maintenance costs.
- Environmental Controls Control environmental factors that could affect the performance of the conveyor belt cleaner. For instance, reducing dust levels and controlling moisture can prevent material build-up and corrosion. Implementing these controls can extend the lifespan of both the cleaner and the conveyor system.
- Documentation and Record-Keeping Maintain detailed records of maintenance activities, inspections, and any issues encountered with the conveyor belt sweeper. This documentation helps track performance over time and can provide valuable insights for troubleshooting and preventive maintenance.
- Use High-Quality Parts Invest in high-quality replacement parts and blades. Using inferior parts may save money initially but can lead to increased wear and frequent replacements, ultimately costing more in the long run.
- Monitor Belt Tension and Alignment Regularly check and adjust the tension and alignment of the conveyor belt. Proper tension and alignment are crucial for the effective operation of the conveyor belt sweeper and can prevent many common issues.
By understanding and addressing these common issues with conveyor belt cleaners, and by implementing robust preventive measures, you can ensure that your conveyor belt sweeper operates efficiently and effectively. This approach not only enhances the performance and longevity of the cleaner but also contributes to the overall productivity and reliability of your conveyor belt system.

FAQs about Conveyor Belt Sweeper
Cleaning a conveyor belt is essential for maintaining its performance and longevity. To clean a conveyor belt, follow these steps:
Turn Off and Lockout: Always ensure the conveyor belt is turned off and locked out to prevent accidental movement during cleaning.
Remove Debris: Manually remove large debris or materials stuck on the belt using appropriate tools.
Apply Cleaning Solution: Use a cleaning solution suitable for the type of material transported on the belt. For food-grade belts, use a food-safe cleaner. Apply the solution evenly across the belt surface.
Scrub the Belt: Use brushes or scrapers to scrub the belt thoroughly. Pay special attention to areas with heavy buildup or stains.
Rinse: Rinse the belt with water to remove the cleaning solution and any loosened debris.
Dry the Belt: Allow the belt to air dry or use a clean, dry cloth to wipe it down. Ensure it is completely dry before restarting the conveyor.
Regular cleaning prevents contamination, reduces wear, and extends the life of the conveyor belt.
A scraper in a belt conveyor is a device used to remove material adhering to the surface of the conveyor belt. Scrapers are typically positioned at strategic points, such as the head pulley, to clean the belt as it completes its loop. There are different types of scrapers, including primary and secondary scrapers.
Primary Scrapers: Installed at the head pulley, these scrapers remove the bulk of material from the belt.
Secondary Scrapers: Positioned further along the belt, secondary scrapers remove any residual material missed by the primary scraper.
Scrapers are essential for preventing material buildup, reducing carryback, and maintaining the efficiency and cleanliness of the conveyor system.
A belt cleaner, also known as a conveyor belt scraper, is a device designed to clean the conveyor belt’s surface as it travels around the head pulley. Belt cleaners come in various designs and materials, including polyurethane, tungsten carbide, and rubber. They are critical for ensuring that the conveyor belt remains free of debris and material buildup.
Belt cleaners are categorized into different types:
Primary Cleaners: Located at the head pulley, they remove the majority of the material.
Secondary Cleaners: Positioned after the primary cleaner, they provide additional cleaning to remove residual materials.
Tertiary Cleaners: Used in specific applications requiring extra cleaning.
Using belt cleaners helps reduce maintenance costs, prevent belt wear, and improve overall conveyor performance.
Conveyor belt safety devices are essential for protecting workers and ensuring safe operation of conveyor systems. These devices include:
Emergency Stop Devices: These devices allow workers to quickly stop the conveyor belt in case of an emergency. Examples include pull cords and push buttons strategically placed along the conveyor.
Safety Guards: Physical barriers that prevent access to dangerous areas of the conveyor, such as pinch points, drive mechanisms, and return rollers.
Belt Alignment Devices: Also known as belt tracking devices, these sensors and switches detect belt misalignment and trigger corrective actions or alarms to prevent damage and accidents.
Overload Protection Devices: These sensors monitor the load on the conveyor belt and shut down the system if it becomes overloaded, preventing mechanical damage and accidents.
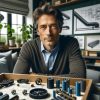
Jordan Smith, a seasoned professional with over 20 years of experience in the conveyor system industry. Jordan’s expertise lies in providing comprehensive solutions for conveyor rollers, belts, and accessories, catering to a wide range of industrial needs. From initial design and configuration to installation and meticulous troubleshooting, Jordan is adept at handling all aspects of conveyor system management. Whether you’re looking to upgrade your production line with efficient conveyor belts, require custom conveyor rollers for specific operations, or need expert advice on selecting the right conveyor accessories for your facility, Jordan is your reliable consultant. For any inquiries or assistance with conveyor system optimization, Jordan is available to share his wealth of knowledge and experience. Feel free to reach out at any time for professional guidance on all matters related to conveyor rollers, belts, and accessories.