Top Features of an Effective Secondary Belt Scraper
The best secondary belt scraper is a critical component in modern conveyor systems, ensuring the cleanliness and efficiency of material handling operations. A secondary belt scraper is strategically installed to follow the primary scraper, providing an additional layer of cleaning to remove any residual material left on the conveyor belt. This thorough cleaning process is essential to prevent material buildup, which can lead to operational inefficiencies, increased wear and tear, and potential safety hazards.
Features of Primary Secondary Belt Scraper
Primary belt scrapers play a vital role in maintaining the cleanliness and efficiency of conveyor systems. As the first line of defense, they are responsible for removing the bulk of material from the conveyor belt, ensuring smooth and uninterrupted operation. In this section, we will take a detailed look at the features of a primary belt scraper, explore how they contribute to conveyor cleanliness, and discuss the common materials used in their construction.
Detailed Look at the Features of a Primary Belt Scraper
A primary belt scraper is designed to make initial contact with the conveyor belt, scraping off the majority of the material that adheres to the belt surface. The efficiency and effectiveness of a primary scraper are determined by several key features:
- Blade Design and Material: The blade is the most crucial component of the primary scraper. It is typically made from wear-resistant materials such as polyurethane, tungsten carbide, or stainless steel. These materials provide the durability and strength needed to withstand the abrasive nature of the conveyed material. The blade’s design, including its shape and angle, is engineered to maximize contact with the belt and ensure efficient scraping.
- Mounting System: The mounting system of a primary belt scraper is designed for easy installation, adjustment, and maintenance. It often includes tensioning mechanisms that allow the blade to maintain consistent pressure against the belt, ensuring effective cleaning. Some mounting systems are also equipped with quick-release mechanisms for rapid blade replacement, minimizing downtime.
- Compatibility with Belt Width and Speed: Primary belt scrapers are available in various sizes to accommodate different belt widths and speeds. Choosing the right scraper for a specific conveyor system is essential to ensure optimal performance. Some scrapers are also adjustable, allowing them to be used with belts of varying widths.
- Self-Adjusting Features: Advanced primary scrapers may include self-adjusting features that automatically adapt to changes in belt conditions, such as wear and tear or variations in belt tension. This ensures consistent cleaning performance without the need for frequent manual adjustments.
How Primary Belt Scrapers Contribute to Conveyor Cleanliness
Primary belt scrapers are integral to maintaining conveyor cleanliness and operational efficiency. Their primary function is to remove the bulk of the material from the belt surface, preventing carryback that can lead to various problems:
- Reduction of Material Buildup: By effectively removing material from the belt, primary scrapers prevent buildup on the conveyor components, such as pulleys, idlers, and return rollers. This reduces the risk of material accumulating and causing blockages, which can disrupt conveyor operation.
- Enhanced Conveyor Efficiency: Clean conveyor belts experience less friction and wear, leading to smoother operation and reduced energy consumption. This results in increased efficiency and lower operating costs.
- Minimized Wear and Tear: Primary scrapers help protect the conveyor belt and other components from excessive wear and tear caused by material abrasion. This extends the lifespan of the conveyor system and reduces maintenance expenses.
- Improved Workplace Safety: By preventing material spillage and buildup, primary scrapers contribute to a safer working environment. This reduces the risk of slip and fall accidents, equipment malfunctions, and other safety hazards associated with material carryback.
Common Materials Used in Primary Belt Scrapers
The materials used in the construction of primary belt scrapers are selected for their durability, wear resistance, and compatibility with the conveyed material. Common materials include:
- Polyurethane: Polyurethane is a popular choice for primary scraper blades due to its excellent wear resistance and flexibility. It can effectively handle a wide range of materials, including abrasive and sticky substances. Polyurethane blades are also less likely to damage the conveyor belt, making them suitable for delicate applications.
- Tungsten Carbide: Tungsten carbide blades are known for their exceptional hardness and durability. They are ideal for high-abrasion environments where the conveyed material is particularly tough and abrasive. Tungsten carbide blades provide long-lasting performance, reducing the frequency of blade replacements.
- Stainless Steel: Stainless steel blades offer a balance between durability and cost-effectiveness. They are resistant to corrosion and can handle a variety of materials, making them suitable for both standard and heavy-duty applications. Stainless steel blades are also easy to maintain and clean.
- Ceramic: Ceramic blades are used in extreme abrasion environments. They provide superior wear resistance and can withstand high temperatures, making them suitable for specialized applications. Ceramic blades, however, are more brittle than other materials and may require careful handling.
Primary belt scrapers are essential components in maintaining the cleanliness and efficiency of conveyor systems. Their design features, such as blade material, mounting system, and self-adjusting capabilities, play a crucial role in ensuring effective material removal. By reducing material buildup, enhancing conveyor efficiency, minimizing wear and tear, and improving workplace safety, primary belt scrapers contribute significantly to the overall performance and longevity of conveyor systems.
Advantages of Using a Secondary Belt Scraper
Key Advantages of Using Flexco Secondary Scraper
Flexco secondary scrapers offer several key advantages that make them indispensable in various industrial applications. One of the primary benefits is the significant improvement in conveyor belt cleaning efficiency. By incorporating a secondary belt scraper, the system can effectively remove residual materials that primary scrapers may miss. This ensures a cleaner belt and reduces the risk of material build-up, which can lead to belt misalignment and excessive wear.
Another advantage of the Flexco secondary scraper is its durability and robust construction. These scrapers are designed to withstand harsh working conditions and heavy usage. Made from high-quality materials, they offer excellent resistance to wear and tear, ensuring a longer service life compared to other scrapers on the market. This durability translates to lower maintenance costs and less frequent replacements, providing a cost-effective solution for conveyor belt cleaning.
Flexco secondary scrapers are also known for their easy installation and maintenance. The design allows for quick and straightforward installation, minimizing downtime and disruption to operations. Additionally, the maintenance of these scrapers is relatively simple, requiring minimal tools and effort. This ease of maintenance is particularly beneficial in high-demand industries where equipment uptime is crucial.
The effectiveness of Flexco secondary scrapers in reducing carryback is another significant advantage. Carryback, the material that sticks to the belt after it leaves the transfer point, can lead to various problems, including conveyor belt wear, increased maintenance costs, and safety hazards. By effectively removing carryback, Flexco secondary scrapers help maintain a cleaner and safer working environment. This reduction in carryback also contributes to the overall efficiency and productivity of the conveyor system.
Typical Applications for Flexco Secondary Scrapers
Flexco secondary scrapers are widely used in numerous industries due to their versatility and effectiveness. One common application is in the mining industry, where conveyor belts are essential for transporting bulk materials such as coal, ore, and aggregate. In these environments, the robust construction and efficient cleaning capabilities of Flexco secondary scrapers help maintain optimal conveyor performance and reduce downtime caused by material build-up and belt misalignment.
Another typical application is in the cement industry, where the transportation of materials like limestone, clinker, and gypsum can cause significant wear and tear on conveyor belts. Flexco secondary scrapers are particularly beneficial in these settings, as they help prevent material carryback and ensure the continuous, smooth operation of the conveyor system. This leads to improved productivity and reduced maintenance costs.
The food processing industry also benefits from the use of Flexco secondary scrapers. In this sector, maintaining a clean conveyor belt is crucial for meeting hygiene and safety standards. Flexco secondary scrapers effectively remove residual materials, ensuring that the belt remains clean and free from contaminants. This not only helps in maintaining product quality but also reduces the risk of cross-contamination and ensures compliance with industry regulations.
Additionally, Flexco secondary scrapers are used in the recycling industry, where conveyor belts transport a variety of materials, including paper, plastics, and metals. The efficient cleaning provided by these scrapers helps maintain the integrity of the conveyor system and reduces the risk of damage caused by material build-up. This leads to a more efficient recycling process and lowers operational costs.
Maintenance Tips for Flexco Secondary Scrapers
To ensure the longevity and optimal performance of Flexco secondary scrapers, regular maintenance is essential. Here are some maintenance tips to help you keep your scrapers in top condition:
- Regular Inspection: Conduct regular inspections of the scraper blades and tensioners to ensure they are in good condition. Look for signs of wear, damage, or misalignment, and address any issues promptly to prevent further damage.
- Proper Tensioning: Ensure that the scraper blades are properly tensioned. Over-tensioning can cause excessive wear on the blades and the conveyor belt, while under-tensioning can reduce the scraper’s effectiveness. Follow the manufacturer’s guidelines for correct tensioning.
- Blade Replacement: Replace scraper blades when they show signs of significant wear or damage. Worn blades can reduce cleaning efficiency and increase the risk of belt damage. Keep a stock of replacement blades to minimize downtime.
- Clean Scraper Blades: Regularly clean the scraper blades to remove any accumulated material. This helps maintain their effectiveness and prevents build-up that can lead to operational issues.
- Lubrication: Lubricate the moving parts of the scraper, such as pivot points and tensioning mechanisms, to ensure smooth operation. Use the recommended lubricant to avoid any adverse effects on the scraper or conveyor belt.
- Monitor Belt Condition: Regularly check the condition of the conveyor belt. A damaged or misaligned belt can affect the performance of the scraper. Address any belt issues promptly to ensure the scraper can function effectively.
By following these maintenance tips, you can maximize the lifespan and performance of your Flexco secondary scrapers, ensuring efficient and reliable conveyor belt cleaning.
Secondary Belt Scraper: Comprehensive Guide to Flexco Belt Cleaners PDF
Accessing and Using the Flexco Belt Cleaners PDF
Accessing and utilizing the Flexco belt cleaners PDF is straightforward and highly beneficial for anyone involved in conveyor belt maintenance. The PDF is available on the Flexco website and can be easily downloaded for offline use. To access the PDF, navigate to the Flexco website, go to the resources or downloads section, and look for the belt cleaners PDF. Once downloaded, you can open it on any device that supports PDF files, such as a computer, tablet, or smartphone.
Using the Flexco belt cleaners PDF is simple. The document is designed to be user-friendly, with a clear and organized layout. It typically includes a table of contents that allows you to quickly navigate to the section you need. The PDF is also searchable, enabling you to find specific information by entering keywords or phrases into the search function of your PDF reader.
Key Topics Covered in the Flexco Belt Cleaners PDF
The Flexco belt cleaners PDF covers a wide range of topics essential for the proper selection, installation, and maintenance of belt cleaners. Some of the key topics include:
- Introduction to Belt Cleaners: This section provides an overview of the importance of belt cleaners in maintaining efficient conveyor systems. It explains the different types of belt cleaners available and their respective advantages.
- Product Selection Guide: This comprehensive guide helps users choose the right belt cleaner for their specific application. It includes detailed descriptions of various belt cleaners, their features, and suitable applications. The guide also offers recommendations based on factors such as belt width, speed, material type, and operating conditions.
- Installation Instructions: Proper installation is crucial for the effective performance of belt cleaners. This section provides step-by-step instructions for installing different types of belt cleaners. It includes detailed diagrams and illustrations to ensure that the installation process is clear and easy to follow.
- Maintenance and Troubleshooting: Regular maintenance is essential for the longevity and performance of belt cleaners. This section offers maintenance tips and best practices to keep belt cleaners in optimal condition. It also includes troubleshooting guides to help identify and resolve common issues that may arise during operation.
- Case Studies and Testimonials: Real-world case studies and testimonials demonstrate the effectiveness of Flexco belt cleaners in various applications. These examples provide valuable insights and practical knowledge that can help users understand the benefits and performance of different belt cleaners.
- Technical Specifications: Detailed technical specifications for each belt cleaner model are provided in this section. This information includes dimensions, materials, operating parameters, and other critical details that help users make informed decisions when selecting and using belt cleaners.
Benefits of Consulting the Flexco Belt Cleaners PDF
Consulting the Flexco belt cleaners PDF offers numerous benefits that can significantly enhance the efficiency and effectiveness of your conveyor belt maintenance efforts. Some of the key benefits include:
- Informed Decision-Making: The detailed product information and selection guides in the PDF help users make informed decisions when choosing belt cleaners. By understanding the features and benefits of each model, users can select the most suitable belt cleaner for their specific needs, ensuring optimal performance and longevity.
- Improved Installation: The step-by-step installation instructions and diagrams provided in the PDF ensure that belt cleaners are installed correctly. Proper installation is crucial for the effective operation of belt cleaners, and following the guidelines in the PDF helps prevent common installation errors that can compromise performance.
- Enhanced Maintenance: Regular maintenance is essential for the continued performance of belt cleaners. The maintenance tips and best practices outlined in the PDF help users keep their belt cleaners in top condition. This proactive approach to maintenance can prevent issues before they arise, reducing downtime and extending the service life of the equipment.
- Efficient Troubleshooting: The troubleshooting guides in the PDF provide practical solutions to common issues that may occur during the operation of belt cleaners. By consulting these guides, users can quickly identify and resolve problems, minimizing downtime and ensuring the continued efficiency of their conveyor systems.
- Knowledge Sharing: The case studies and testimonials included in the PDF offer valuable insights and real-world examples of how Flexco belt cleaners perform in various applications. This knowledge-sharing helps users understand the practical benefits and effectiveness of different belt cleaners, providing them with the confidence to select and use Flexco products.
- Comprehensive Resource: The Flexco belt cleaners PDF serves as a comprehensive resource for all aspects of belt cleaner selection, installation, and maintenance. Having all this information in one document makes it easy to access and reference whenever needed, saving time and effort in finding and consulting multiple sources.
By leveraging the information and resources available in the Flexco belt cleaners PDF, users can ensure the efficient and effective maintenance of their conveyor systems, leading to improved productivity, reduced operational costs, and extended equipment life.
Primary and Secondary Belt Scraper Functions
Functions of Primary and Secondary Belt Scrapers in a Conveyor System
In any conveyor system, maintaining a clean and efficient belt is crucial for optimal performance. Primary and secondary belt scrapers play essential roles in achieving this goal. Understanding the distinct functions of these two types of scrapers can help in selecting and maintaining an effective belt cleaning system.
Primary Belt Scrapers:
Primary belt scrapers are typically positioned at the head pulley, where the belt changes direction and discharges material. The primary function of these scrapers is to remove the bulk of the material that adheres to the belt after it discharges its load. By doing so, they prevent large chunks of material from continuing along the return side of the belt, where they could cause significant wear and tear or lead to misalignment issues.
Primary scrapers are usually made of durable materials such as polyurethane or carbide-tipped blades, which can withstand the abrasive nature of the conveyed materials. Their robust construction ensures that they can handle the initial, and often heaviest, load of material removal, providing a first line of defense against carryback.
Secondary Belt Scrapers:
Secondary belt scrapers are installed further along the return side of the belt, typically a short distance from the head pulley. Their main function is to clean any residual material that the primary scraper might have missed. While the primary scraper removes the majority of the bulk material, the secondary scraper ensures that finer particles and sticky residues are effectively cleared, leaving the belt much cleaner.
Secondary scrapers often have a more flexible and adaptable design compared to primary scrapers. They can be made from a variety of materials, including rubber, polyurethane, and composite materials, which are selected based on the specific needs of the application. These scrapers are essential for achieving a higher level of cleanliness, which is critical for reducing maintenance issues and prolonging the life of the conveyor belt.
How Primary and Secondary Belt Scrapers Work Together
The synergy between primary and secondary belt scraper is what makes them so effective in maintaining a clean conveyor belt. While each scraper has a specific role, they complement each other to provide comprehensive cleaning.
Sequential Cleaning Process:
When material is conveyed along the belt, it often sticks to the surface due to various factors like moisture, material type, and belt speed. As the belt reaches the head pulley and begins to change direction, the primary scraper makes its first contact with the belt. The primary scraper, positioned at a strategic angle, scrapes off the bulk of the material. This initial scraping is crucial as it prevents large chunks of material from returning with the belt.
However, no scraper can remove 100% of the material in one pass. This is where the secondary belt scraper comes into play. As the belt moves along, the secondary scraper, positioned a short distance from the primary scraper, engages the belt. Its purpose is to remove the finer particles and any sticky residues that the primary scraper missed. This two-step cleaning process ensures that the belt is as clean as possible, reducing the likelihood of carryback and the associated problems it can cause.
Material Handling and Belt Protection:
Primary and secondary scrapers not only clean the belt but also protect it. By removing abrasive materials, primary scrapers prevent excessive wear on the belt and other conveyor components. Secondary scrapers, by cleaning off residual fine particles, further reduce the risk of wear and tear, ensuring a longer lifespan for the conveyor belt. Together, they minimize the risk of material build-up, which can lead to belt misalignment, increased maintenance, and even belt failure.
Optimizing Conveyor Performance:
The combined action of primary and secondary scrapers optimizes the overall performance of the conveyor system. A cleaner belt reduces the likelihood of material spillage, which can cause safety hazards and require additional labor to clean up. It also ensures that the conveyor operates more smoothly, with less friction and resistance, leading to lower energy consumption and operational costs. The effective removal of carryback by both scrapers improves the efficiency and reliability of the conveyor system, leading to increased productivity and reduced downtime.
Benefits of Using Both Primary and Secondary Belt Scrapers
Utilizing both primary and secondary belt scrapers in a conveyor system offers numerous benefits, contributing to the efficiency, safety, and longevity of the equipment.
Enhanced Cleaning Efficiency:
The primary benefit of using both scrapers is the significantly enhanced cleaning efficiency. Primary scrapers handle the bulk material removal, while secondary scrapers take care of the finer details. This combination ensures that the belt is thoroughly cleaned, reducing the risk of carryback and its associated issues. A cleaner belt means fewer stoppages for cleaning and maintenance, leading to increased uptime and productivity.
Reduced Maintenance Costs:
By effectively removing material from the belt, both primary and secondary scrapers reduce the wear and tear on the conveyor system. This reduction in wear extends the life of the belt and other components, such as pulleys and idlers, leading to lower maintenance costs. Additionally, less material build-up means less frequent need for manual cleaning, saving both time and labor costs.
Improved Safety:
Material carryback can create hazardous conditions around the conveyor system, including spillage that can cause slip and trip hazards. By ensuring a cleaner belt, primary and secondary scrapers help maintain a safer working environment. This is particularly important in industries where materials can be hazardous or create significant dust, such as mining, cement, and recycling.
Optimal Conveyor Performance:
The reduction of material build-up on the return side of the belt ensures that the conveyor system operates more smoothly and efficiently. This reduces the strain on the motor and other mechanical components, leading to lower energy consumption and better overall performance. The optimized performance also means that the conveyor can operate at higher speeds if needed, increasing throughput and productivity.
Environmental Benefits:
A cleaner conveyor system means less spillage and material waste, contributing to more environmentally friendly operations. This is particularly important in industries where the materials being conveyed can have environmental impacts, such as mining and waste management. By minimizing waste and ensuring efficient material handling, primary and secondary scrapers support sustainable operational practices.
The combination of primary and secondary belt scrapers provides a comprehensive solution for maintaining clean and efficient conveyor systems. Each type of scraper plays a critical role in the cleaning process, and together they offer enhanced cleaning efficiency, reduced maintenance costs, improved safety, optimal performance, and environmental benefits. Understanding the functions and benefits of these scrapers can help in making informed decisions about conveyor system maintenance and optimization.
Secondary Belt Scraper: Efficient Cleaning with Martin Scraper Blades
Overview of Martin Scraper Blades
Martin Engineering is a well-known name in the bulk material handling industry, recognized for its high-quality products and innovative solutions. Martin scraper blades are an integral part of their offering, designed to provide efficient and effective cleaning for conveyor belts. These blades are engineered to tackle the toughest cleaning challenges, ensuring that conveyor systems operate smoothly and efficiently.
Types of Martin Scraper Blades:
Martin offers a variety of scraper blades to meet different needs and applications. Their product range includes:
- Primary Scraper Blades: These are designed to be installed at the head pulley to remove the bulk of the material from the belt. Martin primary scraper blades are known for their robust construction and ability to handle high-volume material removal.
- Secondary Scraper Blades: Positioned further along the return side of the belt, Martin secondary scraper blades focus on removing residual fine particles and sticky materials that primary scrapers may miss. These blades ensure a higher level of cleaning efficiency.
- Specialty Scraper Blades: Martin also offers specialty blades designed for specific applications, such as high-temperature environments or belts conveying particularly abrasive materials. These blades are made from specialized materials to withstand extreme conditions and provide long-lasting performance.
Materials and Construction:
Martin scraper blades are made from high-quality materials to ensure durability and effectiveness. Common materials include polyurethane, carbide, and stainless steel. Polyurethane blades are flexible and resistant to wear, making them ideal for general-purpose cleaning. Carbide-tipped blades offer superior abrasion resistance and are suitable for high-wear applications. Stainless steel blades provide excellent resistance to corrosion and are often used in harsh or wet environments.
Benefits of Using Martin Scraper Blades in Conveyors
The use of Martin scraper blades in conveyor systems offers several benefits that enhance operational efficiency and reduce maintenance costs.
Superior Cleaning Performance:
Martin scraper blades are designed to provide superior cleaning performance, effectively removing both bulk material and fine residues from conveyor belts. This ensures that the belt remains clean and free from material build-up, reducing the risk of carryback and associated issues.
Durability and Longevity:
The high-quality materials and construction of Martin scraper blades ensure their durability and longevity. These blades can withstand harsh working conditions and abrasive materials, providing long-lasting performance and reducing the frequency of replacements. This durability translates to lower maintenance costs and less downtime for blade changes.
Versatility:
Martin offers a wide range of scraper blades to suit different applications and operating conditions. Whether dealing with high-volume material removal, fine particle cleaning, or specific environmental challenges, there is a Martin scraper blade designed to meet the need. This versatility makes Martin blades suitable for various industries, including mining, cement, recycling, and food processing.
Easy Installation and Maintenance:
Martin scraper blades are designed for easy installation and maintenance. Their user-friendly design allows for quick and straightforward installation, minimizing downtime and ensuring that the conveyor system can be up and running quickly. Additionally, the maintenance of these blades is relatively simple, requiring minimal tools and effort. This ease of installation and maintenance is particularly beneficial in high-demand industries where equipment uptime is crucial.
Improved Safety:
By effectively cleaning the conveyor belt, Martin scraper blades help maintain a safer working environment. They reduce the risk of material spillage, which can create slip and trip hazards. This is particularly important in industries where materials can be hazardous or create significant dust, such as mining and cement.
Installation and Maintenance Tips for Martin Scraper Blades
Proper installation and maintenance are key to maximizing the performance and lifespan of Martin scraper blades. Here are some tips to ensure optimal performance:
Installation Tips:
- Follow Manufacturer Guidelines: Always refer to the manufacturer’s installation guidelines and instructions. This ensures that the scraper blades are installed correctly and function as intended.
- Correct Positioning: Ensure that the scraper blades are positioned correctly relative to the conveyor belt. Proper positioning is crucial for effective material removal and preventing damage to the belt.
- Adjust Tension Appropriately: Proper tensioning of the scraper blades is essential for optimal performance. Over-tensioning can cause excessive wear on both the blades and the belt, while under-tensioning can reduce the effectiveness of the scraper. Follow the manufacturer’s recommendations for correct tensioning.
Maintenance Tips:
- Regular Inspections: Conduct regular inspections of the scraper blades to check for signs of wear or damage. Inspect the blades, tensioners, and mounting hardware to ensure they are in good condition and functioning properly.
- Clean Blades Regularly: Regularly clean the scraper blades to remove any accumulated material. This helps maintain their effectiveness and prevents build-up that can lead to operational issues.
- Replace Worn Blades: Replace scraper blades when they show signs of significant wear or damage. Worn blades can reduce cleaning efficiency and increase the risk of belt damage. Keep a stock of replacement blades to minimize downtime.
- Monitor Belt Condition: Regularly check the condition of the conveyor belt. A damaged or misaligned belt can affect the performance of the scraper blades. Address any belt issues promptly to ensure the scrapers can function effectively.
- Lubrication: Lubricate the moving parts of the scraper, such as pivot points and tensioning mechanisms, to ensure smooth operation. Use the recommended lubricant to avoid any adverse effects on the scraper or conveyor belt.
By following these installation and maintenance tips, you can maximize the performance and lifespan of your Martin scraper blades, ensuring efficient and reliable conveyor belt cleaning. This proactive approach to maintenance helps prevent issues before they arise, reducing downtime and extending the service life of the equipment.
Secondary Belt Scraper: Durable Polyurethane Belt Scraper Benefits
Characteristics of Polyurethane Belt Scrapers
Polyurethane belt scrapers are an essential component in the conveyor belt systems used in various industries such as mining, manufacturing, and bulk material handling. These scrapers are made from a versatile synthetic material called polyurethane, which is known for its exceptional properties. Polyurethane exhibits a unique combination of elasticity, toughness, and resistance to wear and tear, making it ideal for demanding industrial applications.
One of the primary characteristics of polyurethane belt scrapers is their flexibility. Unlike metal scrapers, polyurethane scrapers can conform to the contours of the conveyor belt, providing a more effective and thorough cleaning action. This flexibility also helps to prevent damage to the conveyor belt surface, which can occur with rigid metal scrapers.
Another key characteristic is their resistance to abrasion. Conveyor belts often transport materials that can cause significant wear, such as sharp rocks, minerals, and other abrasive substances. Polyurethane’s high resistance to abrasion ensures that the belt scrapers have a longer service life, reducing the frequency of replacements and maintenance.
Polyurethane belt scrapers also have excellent resistance to chemicals and oils. This makes them suitable for use in environments where the conveyor belt might come into contact with various chemicals or oily substances. The chemical resistance of polyurethane ensures that the scrapers do not degrade or lose their effectiveness when exposed to these substances.
Additionally, polyurethane belt scrapers are known for their durability in extreme temperatures. They can maintain their performance in both very high and very low temperatures, making them versatile for different operational environments. This thermal stability is crucial for industries that operate in harsh climates or where the temperature fluctuates significantly.
Advantages of Using Polyurethane Belt Scrapers
The use of polyurethane belt scrapers offers several significant advantages over other types of belt scrapers. These advantages include improved efficiency, cost savings, and enhanced safety.
One of the most notable advantages is the improved cleaning efficiency. The flexible nature of polyurethane allows the scrapers to maintain continuous contact with the conveyor belt, effectively removing debris, residues, and carryback. This thorough cleaning helps to prevent material buildup, which can cause belt misalignment and other operational issues. By keeping the conveyor belt clean, polyurethane scrapers enhance the overall efficiency of the conveyor system.
Cost savings are another major benefit of polyurethane belt scrapers. Due to their durability and resistance to wear, these scrapers have a longer lifespan compared to metal or rubber scrapers. This longevity reduces the need for frequent replacements and lowers maintenance costs. Furthermore, the reduced wear on the conveyor belt itself can lead to longer belt life and fewer belt replacements, resulting in additional cost savings.
Polyurethane belt scrapers also contribute to enhanced safety in the workplace. Material buildup on conveyor belts can create hazardous conditions, such as belt slippage or blockages, which can lead to accidents and injuries. By ensuring the conveyor belt remains clean and free of obstructions, polyurethane scrapers help to maintain a safer working environment.
Moreover, the reduced need for maintenance and replacements means that workers spend less time performing potentially hazardous tasks near moving machinery. This decrease in maintenance activities not only improves safety but also allows workers to focus on other important tasks, increasing overall productivity.
Typical Applications for Polyurethane Belt Scrapers
Polyurethane belt scrapers are used in a wide range of industries due to their versatility and effectiveness. Some typical applications include mining, aggregate processing, bulk material handling, and manufacturing.
In the mining industry, conveyor belts are used to transport mined materials such as coal, ore, and aggregates. These materials can be highly abrasive, making polyurethane scrapers an ideal choice for cleaning the belts. The durability and abrasion resistance of polyurethane ensure that the scrapers can withstand the harsh conditions of mining operations and provide reliable performance over time.
Aggregate processing plants also benefit from the use of polyurethane belt scrapers. These facilities handle large volumes of materials such as sand, gravel, and crushed stone. The effective cleaning provided by polyurethane scrapers helps to prevent material carryback, which can cause operational issues and reduce the efficiency of the processing equipment.
In bulk material handling applications, polyurethane belt scrapers are used to clean conveyor belts that transport a variety of materials, including grains, fertilizers, and chemicals. The chemical resistance of polyurethane makes these scrapers suitable for use in environments where the materials being transported may contain corrosive substances.
Manufacturing industries that use conveyor belts for transporting parts and products also utilize polyurethane belt scrapers. The flexibility and durability of polyurethane make these scrapers effective for maintaining clean belts, ensuring smooth and efficient production processes.
Innovative Secondary Belt Scraper Solutions
Durt Hawg Belt Scraper
The Durt Hawg belt scraper is a cutting-edge solution designed to address the challenges of keeping conveyor belts clean and free of material carryback. Developed with advanced engineering and high-quality materials, Durt Hawg scrapers are known for their effectiveness, durability, and ease of use.
Durt Hawg belt scrapers are specifically engineered to provide superior cleaning performance. They are available in various configurations to suit different types of conveyor systems and applications. Whether it’s a primary, secondary, or tertiary scraper, Durt Hawg offers a comprehensive range of solutions to meet the needs of diverse industries.
One of the distinguishing features of Durt Hawg belt scrapers is their innovative design. These scrapers are equipped with replaceable blades made from high-performance materials such as polyurethane and carbide. The modular design allows for easy replacement of worn blades, ensuring that the scraper maintains optimal performance without the need for complete replacement.
Key Benefits of Durt Hawg Belt Scrapers
Durt Hawg belt scrapers offer several key benefits that make them a preferred choice for many industrial applications. These benefits include enhanced cleaning efficiency, extended service life, and simplified maintenance.
The enhanced cleaning efficiency of Durt Hawg scrapers is achieved through their precise design and high-quality materials. The scraper blades are designed to maintain consistent contact with the conveyor belt, effectively removing material carryback and reducing the risk of buildup. This improved cleaning action helps to maintain the efficiency and reliability of the conveyor system, reducing downtime and maintenance costs.
Extended service life is another significant benefit of Durt Hawg belt scrapers. The use of durable materials such as polyurethane and carbide ensures that the scraper blades can withstand harsh operating conditions and resist wear and tear. This durability translates to longer intervals between blade replacements, reducing the overall cost of ownership.
Durt Hawg belt scrapers are also designed for simplified maintenance. The modular design allows for quick and easy replacement of scraper blades, minimizing downtime and maintenance efforts. The replaceable blade system ensures that only the worn parts need to be replaced, rather than the entire scraper assembly. This not only reduces maintenance costs but also makes it easier for operators to keep the conveyor system running smoothly.
Installation and Maintenance of Durt Hawg Belt Scrapers
Installing Durt Hawg belt scrapers is a straightforward process that can be completed with minimal disruption to the conveyor system. The scrapers are designed to be compatible with a wide range of conveyor configurations, making them easy to integrate into existing systems.
The first step in the installation process is to select the appropriate Durt Hawg scraper for the specific application. This involves considering factors such as the type of material being transported, the operating conditions, and the desired level of cleaning efficiency. Once the appropriate scraper is selected, the installation can proceed.
The scraper is mounted to the conveyor frame using the provided hardware. The modular design of Durt Hawg scrapers allows for adjustable mounting, ensuring that the scraper blades are properly aligned with the conveyor belt. This alignment is crucial for achieving optimal cleaning performance and preventing damage to the belt.
After the scraper is installed, it is important to regularly inspect and maintain the system to ensure continued performance. This involves checking the condition of the scraper blades and replacing them as needed. The replaceable blade system makes this maintenance task quick and easy, reducing downtime and keeping the conveyor system operating efficiently.
In addition to regular blade replacement, it is also important to periodically check the overall condition of the scraper assembly and make any necessary adjustments. This includes ensuring that the scraper blades maintain consistent contact with the conveyor belt and that the mounting hardware is secure.
FAQs about Secondary Belt Scraper
Primary scrapers are positioned at the head pulley, where the conveyor belt discharges its material. Their main function is to remove the majority of the carryback, which is the material that sticks to the belt and returns with it. These scrapers are typically heavy-duty and designed to handle large quantities of bulk material. Secondary scrapers, on the other hand, are installed further along the conveyor system, often after the belt has passed over the head pulley and through the primary scraper. The role of secondary scrapers is to remove any residual material that the primary scraper may have missed. This ensures a cleaner belt and helps to prevent material buildup on other parts of the conveyor system, which can lead to maintenance issues and operational inefficiencies.
A belt scraper’s primary function is to clean the conveyor belt by removing any residual material that adheres to its surface. This cleaning process is crucial because it helps to prevent the carryback of materials, which can cause various operational problems, including material buildup on the belt, rollers, and other components of the conveyor system. By effectively removing carryback, belt scrapers help to maintain the efficiency and longevity of the conveyor system, reduce maintenance costs, and minimize the risk of belt misalignment and other issues that can lead to downtime.
There are generally two main types of scrapers used in conveyor belt systems: primary scrapers and secondary scrapers. Primary scrapers are installed at the head pulley to remove the bulk of the carryback material. Secondary scrapers are installed further along the conveyor system to clean any remaining material that the primary scraper may have missed. Additionally, some systems may use tertiary scrapers for even finer cleaning, ensuring the belt is as clean as possible before it returns to the loading point. The choice and combination of scrapers depend on the specific needs of the conveyor system and the type of material being transported.
Belt scrapers are commonly made from a variety of materials, depending on the application and the type of material being conveyed. The most commonly used materials include polyurethane, carbide, and rubber. Polyurethane scrapers are popular because of their durability and flexibility, making them suitable for a wide range of applications. Carbide scrapers are used for more demanding applications where abrasion resistance is critical, such as in mining or heavy-duty industrial environments. Rubber scrapers are often used for lighter applications and are valued for their cost-effectiveness and ease of maintenance. The choice of material for belt scrapers is crucial to ensure optimal performance and longevity, tailored to the specific needs of the conveyor system.
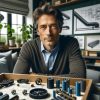
Jordan Smith, a seasoned professional with over 20 years of experience in the conveyor system industry. Jordan’s expertise lies in providing comprehensive solutions for conveyor rollers, belts, and accessories, catering to a wide range of industrial needs. From initial design and configuration to installation and meticulous troubleshooting, Jordan is adept at handling all aspects of conveyor system management. Whether you’re looking to upgrade your production line with efficient conveyor belts, require custom conveyor rollers for specific operations, or need expert advice on selecting the right conveyor accessories for your facility, Jordan is your reliable consultant. For any inquiries or assistance with conveyor system optimization, Jordan is available to share his wealth of knowledge and experience. Feel free to reach out at any time for professional guidance on all matters related to conveyor rollers, belts, and accessories.