Primary Belt Scraper(Cleaner): Last Longer And Cost Less
Primary belt scraper is essential components in the maintenance and efficiency of conveyor belt systems. These devices are installed at the head pulley of a conveyor belt to remove the bulk of material that adheres to the belt after it has discharged its load. This process is crucial in preventing material carryback, which can lead to several operational issues such as belt mistracking, excessive wear, and unnecessary downtime for cleaning and maintenance.Primary belt scraper is an essential component of bulk material handling system ,can remove residual material, for optimal conveyor performance. By effectively removing this residual material, primary belt scrapers play a vital role in keeping the conveyor system clean and efficient.
The 10 Roles of Primary Belt Scraper in Material Handling
Primary conveyor belt scrapers are crucial in material handling systems, ensuring the efficiency and longevity of conveyor operations. They function by removing residual material from the conveyor belt after it has discharged its load, thus preventing carryback. This process is fundamental in maintaining the smooth operation of the conveyor system, as carryback can lead to several operational challenges.
Primary belt scrapers, also known as belt cleaners, play a crucial role in material handling systems, particularly in conveyor belt operations. Here are the ten primary roles of a belt scraper:
- Material Removal: The primary function is to remove material that adheres to the conveyor belt, ensuring it is clean and reducing material buildup.
- Preventing Belt Misalignment: By removing debris, belt scrapers help maintain the belt’s proper alignment, preventing it from running off-track.
- Reducing Wear and Tear: Clean belts experience less friction and wear, prolonging the life of the belt and other conveyor components.
- Minimizing Downtime: Keeping the belt clean reduces the need for maintenance stops, thus increasing operational efficiency and reducing downtime.
- Improving Efficiency: Clean belts ensure that the conveyor system operates at peak efficiency by maintaining a smooth and unobstructed surface.
- Preventing Material Spillage: By cleaning the belt effectively, scrapers prevent material from spilling onto the return side, thus maintaining a clean and safe working environment.
- Enhancing Safety: Cleaner belts reduce the risk of accidents caused by material spillage, ensuring a safer working environment for personnel.
- Optimizing Performance: Belt scrapers help in maintaining optimal performance of the conveyor system by ensuring consistent material flow and reducing interruptions.
- Reducing Environmental Impact: By preventing material spillage and dust, belt scrapers contribute to a cleaner and more environmentally friendly operation.
- Cost Savings: By prolonging the life of the conveyor belt and reducing maintenance needs, belt scrapers contribute to significant cost savings over time.
Primary conveyor belt scrapers are indispensable components in material handling systems. They play a critical role in maintaining the efficiency, safety, and environmental compliance of conveyor operations. By effectively removing residual material from the belt, they prevent carryback, reduce material waste, enhance workplace safety, and contribute to environmental sustainability. Their durability, customization options, and ease of maintenance further enhance their value, making them a worthwhile investment for any conveyor system. With these benefits, primary belt scrapers are essential tools in achieving optimal conveyor performance and reliability.
Exploring the Best Primary Belt Scraper Options
Choosing the best primary belt scraper is crucial for maintaining the efficiency and longevity of your conveyor belt system. Primary belt scrapers are designed to remove bulk materials from the conveyor belt after the discharge point, helping to reduce material carryback, improve belt performance, and minimize maintenance costs. In this section, we will explore the key features to look for in the best primary belt scraper and highlight some leading brands and models known for their quality and reliability.
Key Features to Look for in the Best Primary Belt Scraper
When selecting a primary belt scraper, it is essential to consider several key features that can significantly impact its performance and durability. Here are some of the most important factors to keep in mind:
- Material Compatibility: The best primary belt scraper should be compatible with the type of material being conveyed. Different materials have varying levels of abrasiveness, moisture content, and stickiness, which can affect the scraper’s efficiency. For instance, materials with high moisture content or sticky properties may require scrapers with specific blade designs to effectively remove the material without damaging the belt.
- Blade Material: The material of the scraper blade is crucial for its durability and effectiveness. Common materials for scraper blades include polyurethane, carbide, and stainless steel. Polyurethane blades are flexible and resistant to wear, making them suitable for lighter applications. Carbide blades, on the other hand, are highly abrasion-resistant and ideal for heavy-duty applications. Stainless steel blades offer a good balance between durability and flexibility.
- Adjustability: The best primary belt scrapers should be easily adjustable to maintain optimal contact with the conveyor belt. This ensures consistent cleaning performance and helps to extend the lifespan of both the scraper and the belt. Look for scrapers with easy-to-use adjustment mechanisms that allow for quick and precise positioning.
- Mounting System: The mounting system of the scraper is another important consideration. A robust and secure mounting system ensures that the scraper remains in place during operation, providing consistent cleaning performance. Some scrapers come with universal mounting brackets that can be easily adapted to fit different conveyor systems.
- Ease of Maintenance: Regular maintenance is essential for ensuring the longevity and efficiency of the primary belt scraper. Look for scrapers that are designed for easy maintenance, with features such as quick-release mechanisms for blade replacement and accessible adjustment points. This will help to minimize downtime and reduce maintenance costs.
- Cost-Effectiveness: While it is important to invest in a high-quality scraper, it is also essential to consider the cost-effectiveness of the solution. The best primary belt scrapers should offer a good balance between performance, durability, and cost. Look for scrapers that provide long-lasting performance and require minimal maintenance, helping to reduce overall operating costs.
Leading Brands and Models Known for Quality and Reliability
Several leading brands and models of primary belt scrapers are known for their quality and reliability. Here are some of the top options to consider:
- Flexco Primary Belt Scrapers: Flexco is a well-known brand in the conveyor belt industry, offering a wide range of primary belt scrapers designed for various applications. Their scrapers are known for their durability, ease of maintenance, and efficient cleaning performance. Flexco’s carbide-tipped blades are particularly popular for heavy-duty applications, providing excellent abrasion resistance and long-lasting performance.
- Martin Engineering Primary Belt Scrapers: Martin Engineering is another reputable brand offering high-quality primary belt scrapers. Their scrapers are designed to provide efficient material removal and reduce carryback, helping to improve conveyor belt performance. Martin Engineering offers a variety of scraper models with different blade materials and designs to suit various applications.
- Metso Primary Belt Scrapers: Metso is a global leader in the mining and construction industries, known for their innovative conveyor belt solutions. Their primary belt scrapers are designed to provide reliable and efficient cleaning performance, reducing material carryback and improving belt lifespan. Metso’s scrapers are available in various configurations to meet the specific needs of different applications.
- Richwood Primary Belt Scrapers: Richwood is a trusted name in conveyor belt cleaning systems, offering high-performance primary belt scrapers designed to withstand the toughest conditions. Their scrapers feature durable blade materials and robust mounting systems, ensuring consistent cleaning performance and long-lasting durability.
- ASGCO Primary Belt Scrapers: ASGCO provides a range of primary belt scrapers known for their quality and reliability. Their scrapers are designed to effectively remove material from the conveyor belt, reducing carryback and improving overall system efficiency. ASGCO offers various scraper models with different blade materials and designs to suit different applications.
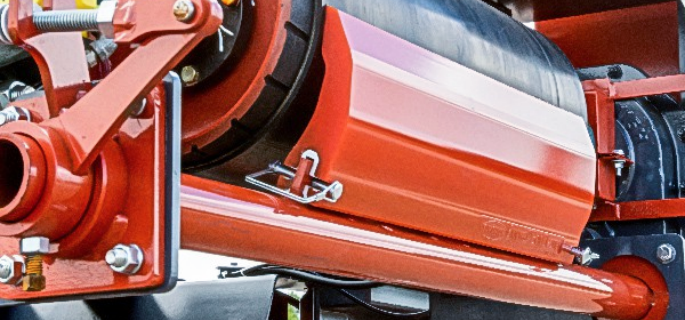
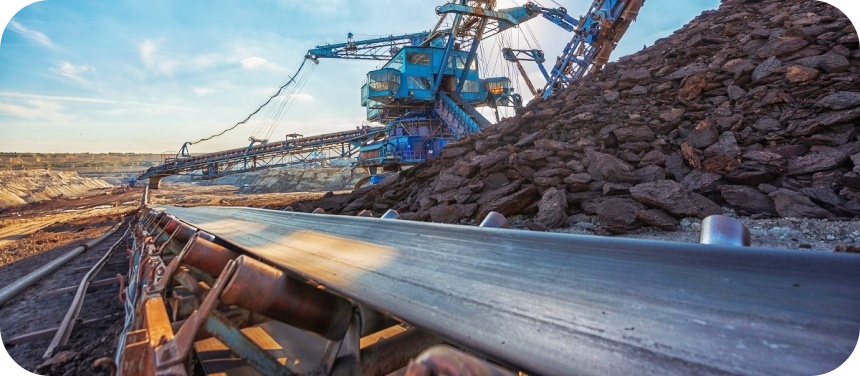
Primary Belt Scraper for Sale: What to Look For
When looking for a primary belt scraper for sale, it is important to consider several factors to ensure you select the right scraper for your needs. Here are some tips on selecting the right primary belt scraper and where to find them for sale, including online and offline options.
Tips on Selecting the Right Primary Belt Scraper for Your Needs
- Assess Your Conveyor System Requirements: Before purchasing a primary belt scraper, it is essential to assess the specific requirements of your conveyor system. Consider factors such as the type of material being conveyed, belt speed, and belt width. Understanding these requirements will help you select a scraper that is compatible with your system and provides optimal performance.
- Consider the Operating Environment: The operating environment can significantly impact the performance and durability of the primary belt scraper. Factors such as temperature, humidity, and exposure to chemicals can affect the scraper’s materials and performance. Ensure that the scraper you choose is designed to withstand the conditions of your operating environment.
- Evaluate Scraper Features and Specifications: Review the features and specifications of different primary belt scrapers to determine which one best meets your needs. Consider factors such as blade material, adjustability, mounting system, and ease of maintenance. Selecting a scraper with the right features will ensure efficient cleaning performance and long-lasting durability.
- Read Reviews and Testimonials: Reading reviews and testimonials from other users can provide valuable insights into the performance and reliability of different primary belt scrapers. Look for feedback on factors such as cleaning efficiency, ease of maintenance, and overall satisfaction. This information can help you make an informed decision and choose a scraper that meets your expectations.
- Consult with Experts: If you are unsure which primary belt scraper is best for your needs, consider consulting with experts or suppliers. They can provide valuable advice and recommendations based on their experience and knowledge of different scraper models and applications. This can help you select a scraper that provides optimal performance and value.
- Maintenance and Cost:Consider how easy it is to maintain and replace parts of the scraper. Balance the initial purchase price with long-term maintenance costs.
- Manufacturer Reputation and Compliance:Select a scraper from a reputable manufacturer to guarantee quality and reliability. Ensure it meets industry standards and regulations.
- Belt Width Compatibility:Ensure the scraper is appropriate for your conveyor belt’s width for efficient cleaning.
- Environmental Resilience:Select materials that can endure the specific environmental challenges of your workplace, like high temperatures or corrosive elements.
Where to Find Primary Belt Scrapers for Sale
Primary belt scrapers are available for sale through various online and offline channels. Here are some of the best places to find primary belt scrapers for sale:
- Online Retailers and Marketplaces: Many online retailers and marketplaces offer a wide range of primary belt scrapers for sale. Websites such as Amazon, eBay, and industrial supply stores like Grainger and McMaster-Carr provide a variety of scraper models and brands to choose from. Shopping online allows you to compare prices, read reviews, and make informed decisions from the comfort of your home or office.
- Manufacturer Websites: Many primary belt scraper manufacturers sell their products directly through their websites. Brands such as Flexco, Martin Engineering, Metso, Richwood, and ASGCO offer detailed product information and the option to purchase scrapers online. Buying directly from the manufacturer ensures that you are getting genuine products and may provide access to additional resources such as installation guides and technical support.
- Industrial Supply Distributors: Industrial supply distributors often carry a range of primary belt scrapers and other conveyor system components. Companies such as Motion Industries, Applied Industrial Technologies, and MSC Industrial Supply offer a variety of scraper models and can provide expert advice and support. Purchasing through a distributor can also offer benefits such as bulk pricing and local availability.
- Trade Shows and Expos: Industry trade shows and expos are excellent places to find primary belt scrapers for sale. These events provide an opportunity to see different scraper models in action, meet with manufacturers and suppliers, and learn about the latest innovations in conveyor belt cleaning technology. Attending trade shows can help you make informed purchasing decisions and establish valuable connections within the industry.
- Local Suppliers and Dealers: Local suppliers and dealers often carry primary belt scrapers and other conveyor system components. Purchasing from a local supplier can provide benefits such as faster delivery times, personalized service, and the ability to see the products in person before making a purchase. Look for suppliers and dealers in your area who specialize in conveyor systems and industrial equipment.
Selecting the right primary belt scraper is essential for maintaining the efficiency and longevity of your conveyor system. By considering factors such as material compatibility, blade material, adjustability, mounting system, ease of maintenance, and cost-effectiveness, you can choose a scraper that meets your needs and provides optimal performance. With a wide range of options available from leading brands and various purchasing channels, you can find the perfect primary belt scraper to enhance your conveyor system’s performance and reliability.
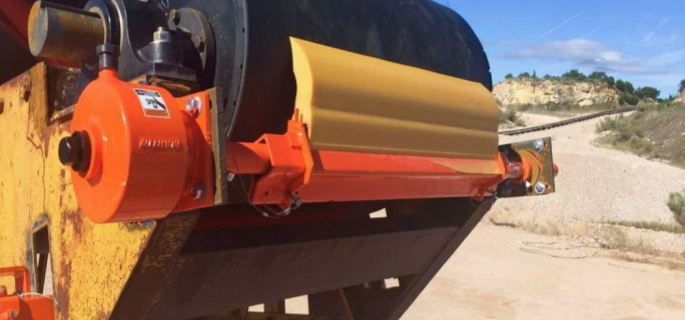
Primary Belt Scraper: Types of Conveyor Belt Scrapers
Conveyor belt scrapers are essential tools in maintaining the efficiency and longevity of conveyor systems by removing residual material from the belt. There are various types of conveyor belt scrapers, each designed to handle different materials and operational conditions. Understanding the types of scrapers and their specific use cases can help in selecting the most suitable scraper for your system.
Primary Belt Scraper
The primary belt scraper is the first line of defense against material carryback. Installed at the head pulley, it removes the bulk of the material that sticks to the belt after discharge. The primary belt scraper is designed to handle a wide range of materials and operating conditions, making it a versatile choice for many conveyor systems.Primary belt cleaners are installed at the head pulley to remove the bulk of the material from the belt. They are typically made of durable materials such as polyurethane or carbide.
Benefits:
- Efficiently removes bulk materials.
- Reduces material carryback.
- Enhances conveyor system efficiency.
Use Cases:
- Suitable for removing coarse, bulk materials.
- Ideal for applications where the material is relatively dry and non-sticky.
- Commonly used in mining, aggregate, and bulk material handling industries.
Secondary Belt Scraper
Secondary belt scrapers are installed after the primary belt scraper to provide additional cleaning. They are designed to remove any remaining material that the primary scraper may have missed, ensuring a more thorough cleaning of the conveyor belt. Secondary belt scrapers typically have more flexible blades and are positioned closer to the return side of the belt.Secondary belt cleaners are installed after primary cleaners to provide additional cleaning. They are designed to remove any remaining material.
Benefits:
- Provides additional cleaning for finer materials.
- Ensures a higher level of belt cleanliness.
- Reduces maintenance costs and downtime.
Use Cases:
- Effective for removing finer materials and sticky substances.
- Used in conjunction with primary scrapers to achieve optimal cleaning efficiency.
- Suitable for applications where the material has high moisture content or is sticky.
V-Plow Scraper
The V-plow scraper is designed to prevent material buildup on the return side of the belt. It is typically installed before the tail pulley and is shaped like a “V” to deflect material off the belt. This type of scraper is essential for protecting the tail pulley and other components from damage caused by material buildup.V-plow cleaners are designed to prevent material buildup on the return side of the belt. They are shaped like a “V” to deflect material off the belt, protecting the tail pulley and other components from damage.
Benefits:
- Prevents material buildup on the return side of the belt.
- Protects conveyor components from damage.
- Reduces maintenance costs and downtime.
Use Cases:
- Ideal for preventing material buildup on the return side of the belt.
- Used in applications where material spillage is a concern.
- Commonly used in bulk material handling and mining operations.
Diagonal Plow Scraper
Diagonal plow scrapers are similar to V-plow scrapers but are installed diagonally across the return side of the belt. This design allows the scraper to remove material from one side of the belt and direct it off the conveyor. Diagonal plow scrapers are effective in preventing material buildup and protecting conveyor components.Diagonal plow cleaners are installed diagonally across the return side of the belt to remove material from one side of the belt and direct it off the conveyor. They are effective in preventing material buildup and protecting conveyor components.
Benefits:
- Removes material from one side of the belt.
- Prevents material buildup on the return side of the belt.
- Protects conveyor components from damage.
Use Cases:
- Effective for removing material from one side of the belt.
- Suitable for applications where material spillage is a concern.
- Used in mining, aggregate, and bulk material handling industries.
Rotary Brush Scraper
Rotary brush scrapers use rotating brushes to clean the conveyor belt. These scrapers are typically installed after primary and secondary scrapers to remove fine particles and dust from the belt. Rotary brush scrapers are effective in achieving a high level of cleanliness, especially for belts carrying fine or powdery materials.Rotary brush cleaners use rotating brushes to clean the conveyor belt. They are effective in removing fine particles and dust from the belt, achieving a high level of cleanliness.
Benefits:
- Effective in removing fine particles and dust.
- Provides a high level of belt cleanliness.
- Suitable for applications requiring stringent hygiene standards.
Use Cases:
- Ideal for removing fine particles and dust.
- Suitable for applications where a high level of belt cleanliness is required.
- Commonly used in food processing, pharmaceuticals, and chemical industries.
Tungsten Carbide Scraper
Tungsten carbide scrapers are known for their durability and high abrasion resistance. They are typically used in heavy-duty applications where the conveyed material is highly abrasive. Tungsten carbide scrapers can withstand harsh operating conditions and provide long-lasting performance.
Use Cases:
- Suitable for heavy-duty applications with highly abrasive materials.
- Ideal for mining, quarrying, and bulk material handling industries.
- Effective in environments with harsh operating conditions.
Water Sprays and Wash Boxes
Water sprays and wash boxes use water to clean the conveyor belt. They are effective in removing sticky materials and fine particles, providing a thorough cleaning of the belt.
Benefits:
- Effective in removing sticky materials and fine particles.
- Provides a thorough cleaning of the belt.
- Suitable for applications where water can be used for cleaning.
Air Knives
Air knives use a high-velocity stream of air to blow off residual material from the conveyor belt. They are effective in removing fine particles and dust without the use of water or brushes.
Benefits:
- Removes fine particles and dust.
- Does not require water or brushes.
- Suitable for applications where water cannot be used.
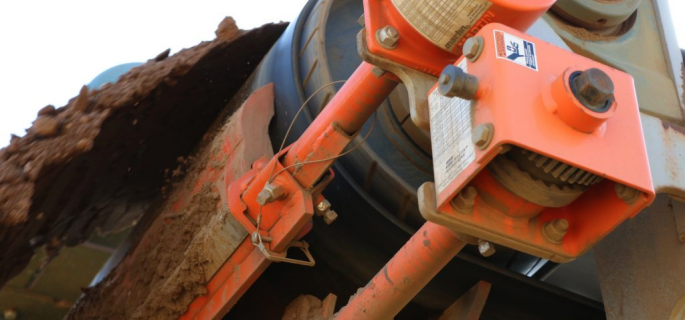
Primary Belt Scraper: Enhancing Efficiency with Conveyor Belt Cleaners
Using conveyor belt cleaners in conjunction with primary belt scrapers is crucial for maintaining the efficiency and reliability of conveyor systems. Conveyor belt cleaners are designed to remove residual material from the belt, reducing carryback and minimizing maintenance costs. There are various types of conveyor belt cleaners, each offering unique benefits.
Importance of Using Conveyor Belt Cleaners
Conveyor belt cleaners play a vital role in ensuring the efficient operation of conveyor systems. They help in reducing material carryback, which can cause several issues, including:
- Increased Wear and Tear: Material carryback can lead to increased wear and tear on conveyor components, such as pulleys, idlers, and the belt itself. This can result in higher maintenance costs and shorter equipment lifespan.
- Belt Mistracking: Residual material on the belt can cause it to mistrack, leading to operational inefficiencies and potential damage to the conveyor system.
- Safety Hazards: Material carryback can create hazardous working conditions by causing spillage and dust accumulation, increasing the risk of accidents and health issues for workers.
- Environmental Concerns: Material spillage can lead to environmental contamination and non-compliance with regulatory standards.
By using conveyor belt cleaners in conjunction with primary belt scrapers, these issues can be mitigated, resulting in a more efficient and safe conveyor system.
Industry Applications For Primary Belt Cleaners
Primary belt cleaners are utilized across various industries where conveyor belts are essential for material handling. Here are some key industry applications:
- Mining Industry: Used to clean conveyor belts that transport raw minerals and ores, reducing downtime and ensuring efficient material flow.
- Aggregate and Quarrying: Essential for removing debris and material carryback on belts transporting gravel, sand, and crushed stone.
- Cement Industry: Helps in maintaining clean belts in the transport of raw materials like limestone and gypsum, as well as finished cement products.
- Power Generation: Utilized in coal-fired power plants to clean belts transporting coal to boilers and other areas, reducing the risk of fire and improving operational efficiency.
- Steel and Iron Industry: Important for removing carryback in belts transporting raw materials like iron ore, pellets, and coke, as well as finished steel products.
- Food Processing: Ensures hygiene and cleanliness in conveyor belts used for transporting food products, preventing contamination and ensuring compliance with health regulations.
- Recycling and Waste Management: Helps in the efficient transport of recyclables and waste materials, reducing blockages and maintaining clean conveyor belts.
- Bulk Material Handling: Applied in industries handling bulk materials such as chemicals, fertilizers, and grains to ensure clean and efficient belt operation.
- Construction: Used in the transport of construction materials like concrete and asphalt, ensuring clean belts and preventing material buildup.
- Pulp and Paper Industry: Essential for removing residue from belts transporting wood chips, pulp, and finished paper products, ensuring smooth operation and reducing maintenance needs.
These applications highlight the versatility and importance of primary belt cleaners in maintaining efficient and safe operations across diverse industries.
Primary Belt Scraper Maintenance
Maintaining primary belt scrapers is crucial to ensure their effectiveness and extend their lifespan. Here are some key maintenance practices:
- Regular Inspection: Conduct routine inspections to check for wear, damage, or misalignment. This should be done frequently, depending on the operational conditions and the type of material being handled.
- Cleaning: Keep the scraper and surrounding area clean to prevent material buildup that can interfere with the scraper’s performance.
- Adjustment: Regularly adjust the tension and alignment of the scraper to ensure it maintains proper contact with the conveyor belt. This helps in effective cleaning and prevents uneven wear.
- Replacement of Blades: Inspect scraper blades for wear and replace them as needed. Worn or damaged blades can reduce cleaning efficiency and may damage the conveyor belt.
- Lubrication: Ensure that any moving parts are properly lubricated as per the manufacturer’s recommendations to prevent rust and ensure smooth operation.
- Check for Material Compatibility: Ensure that the scraper material is compatible with the type of material being transported to prevent premature wear or chemical damage.
- Monitoring Wear Patterns: Keep an eye on wear patterns on both the scraper and the conveyor belt. Uneven wear might indicate a need for adjustment or a different type of scraper blade.
- Regular Training: Train maintenance personnel on proper maintenance procedures and the importance of regular checks and adjustments.
- Documentation: Keep detailed records of inspections, maintenance activities, and any replacements. This helps in identifying patterns and scheduling preventive maintenance.
- Manufacturer Guidelines: Follow the manufacturer’s maintenance guidelines and recommendations for specific belt scraper models to ensure optimal performance.
By adhering to these maintenance practices, you can ensure that primary belt scrapers perform effectively, prolong their lifespan, and maintain the efficiency and safety of the conveyor system.
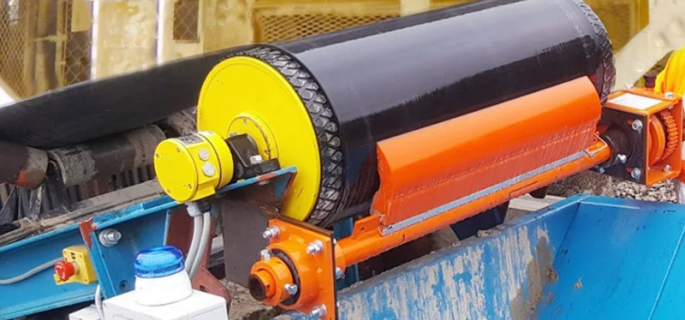
Secondary Belt Scraper: An Essential Addition
Secondary belt scrapers are an essential addition to any conveyor belt cleaning system. They complement primary belt scrapers by providing additional cleaning, ensuring that any residual material left by the primary scraper is removed. This results in a cleaner belt and a more efficient conveyor system.
Secondary Belt Scrapers and Their Role
Secondary belt scrapers are installed after the primary belt scraper to provide a second line of defense against material carryback. They are designed to remove any remaining material that the primary scraper may have missed, ensuring a more thorough cleaning of the conveyor belt. Secondary belt scrapers typically have more flexible blades and are positioned closer to the return side of the belt, allowing them to effectively clean the belt without causing damage.
Role of Secondary Belt Scrapers:
- Enhanced Cleaning Efficiency: Secondary belt scrapers provide additional cleaning, removing finer materials and sticky substances that the primary scraper may have missed. This results in a cleaner belt and reduces material carryback.
- Reduced Maintenance Costs: By ensuring a more thorough cleaning of the conveyor belt, secondary scrapers help to reduce wear and tear on conveyor components, resulting in lower maintenance costs and longer equipment lifespan.
- Improved Belt Performance: A cleaner belt operates more efficiently, reducing the risk of belt mistracking and other operational issues. This enhances the overall performance and reliability of the conveyor system.
- Increased Safety: By reducing material carryback and spillage, secondary belt scrapers help to create a safer working environment, minimizing the risk of accidents and health issues for workers.
How Secondary Belt Scrapers Complement Primary Scrapers to Achieve Optimal Cleaning
Secondary belt scrapers are designed to work in conjunction with primary scrapers to achieve optimal cleaning of the conveyor belt. While primary scrapers remove the bulk of the material from the belt, secondary scrapers provide additional cleaning to ensure that any remaining material is removed.
Complementary Cleaning Action:
- Primary Scrapers: Primary belt scraper is installed at the head pulley to remove the bulk of the material from the belt. They are designed to handle a wide range of materials and operating conditions, making them a versatile choice for many conveyor systems.
- Secondary Scrapers: Secondary belt scrapers are installed after the primary scrapers to provide additional cleaning. They have more flexible blades and are positioned closer to the return side of the belt, allowing them to effectively remove finer materials and sticky substances.
Benefits of Combined Cleaning:
- Thorough Cleaning: The combination of primary and secondary scrapers ensures a more thorough cleaning of the conveyor belt, reducing material carryback and improving belt cleanliness.
- Reduced Wear and Tear: By removing more material from the belt, the combined action of primary and secondary scrapers helps to reduce wear and tear on conveyor components, resulting in lower maintenance costs and longer equipment lifespan.
- Improved Efficiency: A cleaner belt operates more efficiently, reducing the risk of belt mistracking and other operational issues. This enhances the overall performance and reliability of the conveyor system.
- Enhanced Safety: By reducing material carryback and spillage, the combined action of primary and secondary scrapers helps to create a safer working environment, minimizing the risk of accidents and health issues for workers.
Secondary belt scrapers are an essential addition to any conveyor belt cleaning system. They complement primary scrapers by providing additional cleaning, ensuring that any residual material left by the primary scraper is removed. This results in a cleaner belt, reduced maintenance costs, improved belt performance, and increased safety. By understanding the role of secondary scrapers and how they complement primary scrapers, you can achieve optimal cleaning and efficiency for your conveyor system.
Easily connect with us for all your conveyor cleaner needs.
FAQs about Primary Belt Scraper
A primary scraper is a device used in material handling systems, particularly on conveyor belts, to remove the bulk of material sticking to the belt. Positioned at the head pulley, primary scrapers are the first line of defense against carryback, which refers to the material that clings to the belt and is carried back along its return path. By effectively removing this material, primary scrapers help prevent build-up and reduce the risk of damage to the conveyor system.
Belt scrapers are essential tools in maintaining conveyor belt systems. They are used to remove residual material that sticks to the belt after the bulk of the load has been discharged. This helps prevent material carryback, which can cause several issues such as belt mistracking, premature wear of conveyor components, and increased maintenance costs. By keeping the belt clean, scrapers also improve the efficiency and longevity of the conveyor system, reduce material wastage, and enhance workplace safety by minimizing spillage and dust.
The angle of a primary scraper is typically set between 90 to 95 degrees relative to the belt surface. This angle is crucial for maximizing the scraper’s efficiency in removing material from the belt without causing excessive wear on the belt or the scraper itself. The exact angle can vary depending on the type of material being conveyed and the design of the scraper. Proper adjustment of this angle ensures optimal performance and extends the lifespan of both the scraper and the conveyor belt.
Cleaning a conveyor belt involves several steps to ensure it operates efficiently and safely. Here are the key steps:
Shut Down and Lock Out: Ensure the conveyor system is shut down and locked out to prevent accidental startup during cleaning.
Remove Large Debris: Manually remove any large pieces of material or debris from the belt surface.
Apply Scrapers: Use primary and secondary scrapers to remove adhered material from the belt.
Brush and Vacuum: Use brushes or vacuum systems to clean finer particles and dust from the belt.
Wash: For thorough cleaning, wash the belt with water and appropriate cleaning agents. Ensure the cleaning solution is compatible with the belt material to avoid damage.
Inspect and Maintain: Regularly inspect the belt and scrapers for wear and damage, and replace or adjust components as needed. By following these steps, you can maintain a clean and efficient conveyor belt system, reducing downtime and extending the lifespan of the equipment.
Primary scrapers are for initial cleaning. Secondary scrapers provide additional belt cleaning in a different location on the conveyor.
It usually depends on the environment; some will wear out a scraper faster than others. You should replace blades when they become ineffective.
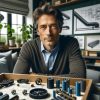
Jordan Smith, a seasoned professional with over 20 years of experience in the conveyor system industry. Jordan’s expertise lies in providing comprehensive solutions for conveyor rollers, belts, and accessories, catering to a wide range of industrial needs. From initial design and configuration to installation and meticulous troubleshooting, Jordan is adept at handling all aspects of conveyor system management. Whether you’re looking to upgrade your production line with efficient conveyor belts, require custom conveyor rollers for specific operations, or need expert advice on selecting the right conveyor accessories for your facility, Jordan is your reliable consultant. For any inquiries or assistance with conveyor system optimization, Jordan is available to share his wealth of knowledge and experience. Feel free to reach out at any time for professional guidance on all matters related to conveyor rollers, belts, and accessories.