Industrial-Grade Black Conveyor Belt Material Options Available
Conveyor belts play a pivotal role in streamlining operations across a multitude of industries, from manufacturing and mining to food processing and retail. These belts facilitate the efficient and rapid movement of goods, materials, and products over short to long distances within a facility, thereby enhancing productivity and operational efficiency. The heart of a conveyor belt’s functionality and efficiency lies in the selection of the right conveyor belt material. This choice is crucial as it directly influences the belt’s durability, flexibility, resistance to environmental conditions, and suitability for the specific types of goods it will carry. Therefore, understanding the properties and applications of various conveyor belt materials is essential for industry professionals to make informed decisions that optimize their conveyor systems for peak performance.
Conveyor Belt Material Types
The selection of conveyor belt material is a critical decision that affects the functionality, durability, and efficiency of the conveyor system. Below is a detailed overview of the main types of materials used in conveyor belts, including thermoplastics, metal, rubber, fabric, and leather, along with specific examples of each type.
Material Type | Examples | Key Properties | Common Applications |
---|---|---|---|
Thermoplastics | Polyester, Polyvinyl Chloride (PVC), Silicone, Polyethylene | Resistant to chemicals, flexible, lightweight | Food processing, packaging, pharmaceuticals |
Metal | Stainless Steel, Carbon Steel | High strength, durable, resistant to high temperatures | Mining, heavy manufacturing, metal processing |
Rubber | Natural Rubber, Synthetic Rubber | Flexible, durable, resistant to abrasion and impact | Mining, agriculture, logistics |
Fabric | Canvas, Cotton | Lightweight, flexible, cost-effective | Retail, light manufacturing, packaging |
Leather | Genuine Leather, Synthetic Leather | Durable, high grip, shock-resistant | Vintage or specialty conveyors, luxury goods manufacturing |
Each conveyor belt material offers unique benefits and is suited to specific industrial applications. For instance, thermoplastics like PVC are favored in the food processing industry due to their compliance with hygiene standards and ease of cleaning. Metals, with their unparalleled strength and durability, are the go-to choice for heavy-duty applications in mining and metal processing.
Rubber conveyor belt materials, known for their flexibility and durability, are widely used across various industries, from mining to agriculture. They are particularly valued for their ability to absorb impacts and resist abrasion, making them ideal for conveying rough and sharp materials.
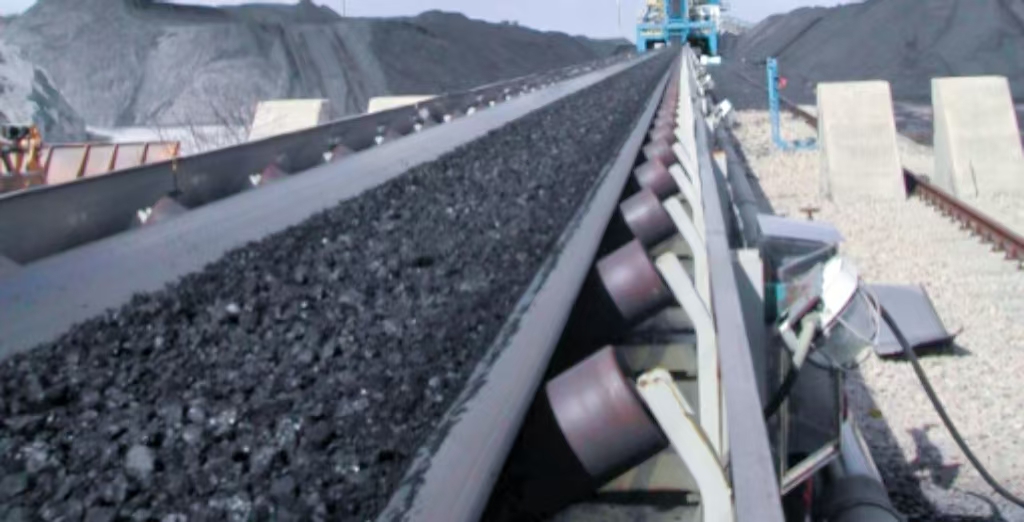
Fabric materials, such as canvas and cotton, offer a lightweight and cost-effective solution for less demanding applications. These materials are commonly found in retail and light manufacturing environments, where the emphasis is on gentle handling of goods.
Leather, with its unique aesthetic and durability, is used in specialty or vintage conveyor systems. While not as common as the other materials, leather conveyor belts find their niche in luxury goods manufacturing and applications where the conveyor belt’s appearance is a consideration.
Understanding the properties and applications of these conveyor belt material types is essential for selecting the most appropriate conveyor belt for your specific needs, ensuring optimal performance and longevity of the conveyor system.
Conveyor Belt Material Properties
Key properties
The performance and longevity of a conveyor system significantly depend on the inherent properties of the conveyor belt material. Here are six key properties that are essential for conveyor belt materials, each playing a crucial role in the belt’s functionality and durability.
- Durability: This is perhaps the most critical property, as it determines how well the conveyor belt withstands the rigors of daily operation, including wear and tear from continuous use and the weight of the materials being transported.
- Temperature Resistance: Conveyor belt materials must be able to maintain their integrity and performance characteristics across a wide range of temperatures. This is especially important in industries where belts are exposed to extreme heat or cold, such as in baking ovens or cold storage facilities.
- Moisture Resistance: In environments where exposure to water or humidity is common, the conveyor belt material must resist water absorption to prevent swelling, warping, or other moisture-related damage.
- Chemical Resistance: Many industrial processes involve exposure to chemicals, oils, and other substances that can degrade certain materials. Conveyor belt materials need to resist these chemicals to avoid premature wear or damage.
- Flexibility: The ability of a conveyor belt to flex without breaking is crucial, especially in systems where the belt must navigate around curves or inclines. Flexibility ensures smooth operation and reduces the risk of belt failure.
- Tensile Strength: This property defines the maximum load that the conveyor belt material can handle before breaking. High tensile strength is essential for belts carrying heavy loads or operating under high tension.
Impact of These Properties
These properties collectively impact the performance and longevity of conveyor belts in several ways:
- Durability and Tensile Strength ensure that the belt can handle the daily operational stresses without failing, thereby reducing downtime and maintenance costs.
- Temperature and Moisture Resistance protect the belt from environmental conditions that could lead to material degradation, ensuring consistent performance regardless of the operating environment.
- Chemical Resistance ensures that the conveyor belt material does not deteriorate when exposed to industrial chemicals, oils, and other potentially harmful substances, thereby extending the conveyor belt’s life.
- Flexibility allows the conveyor belt to adapt to the specific layout of the conveyor system, including turns and elevation changes, without compromising the integrity of the belt.
Understanding these properties and their impact on conveyor belt performance is essential for selecting the right conveyor belt material for specific industrial applications, ensuring efficient and reliable conveyor system operation.
Rubber Conveyor Belt Material
Rubber conveyor belts are integral to various industrial operations, offering versatility and durability unmatched by other conveyor belt materials. The industrial rubber conveyor belt is a prime example of this robustness and adaptability.A deep dive into the different types of rubber conveyor belts reveals a range of applications, each with its own set of advantages and limitations. Understanding these distinctions is crucial for selecting the most appropriate rubber conveyor belt for specific industrial needs.
Rubber Belt Type | Applications | Advantages | Limitations |
---|---|---|---|
Natural Rubber Belts | General conveying, agricultural applications | High elasticity and tensile strength, excellent abrasion resistance | Poor resistance to oils, fats, and some chemicals |
Styrene-Butadiene Rubber (SBR) Belts | Light to medium aggregate conveying, packaging | Good abrasion resistance, cost-effective, moderate resistance to heat and chemicals | Not suitable for extreme temperatures or harsh chemical environments |
Nitrile Rubber (NBR) Belts | Recycling, metal processing, applications involving oils and fats | Excellent oil and fat resistance, good abrasion resistance, suitable for high-temperature applications | Higher cost compared to SBR, less flexible at low temperatures |
Ethylene Propylene Diene Monomer (EPDM) Belts | Outdoor applications, heat-exposed environments | Superior resistance to weathering, heat, and ozone, maintains flexibility at low temperatures | Poor resistance to petroleum-based oils and solvents |
Butadiene Rubber (BR) Belts | Low-temperature applications, conveying in cold environments | High resistance to low temperatures, good abrasion resistance | Limited resistance to heat and chemicals, less flexible than natural rubber |
PVC Conveyor Belt Material
PVC Conveyor Belt
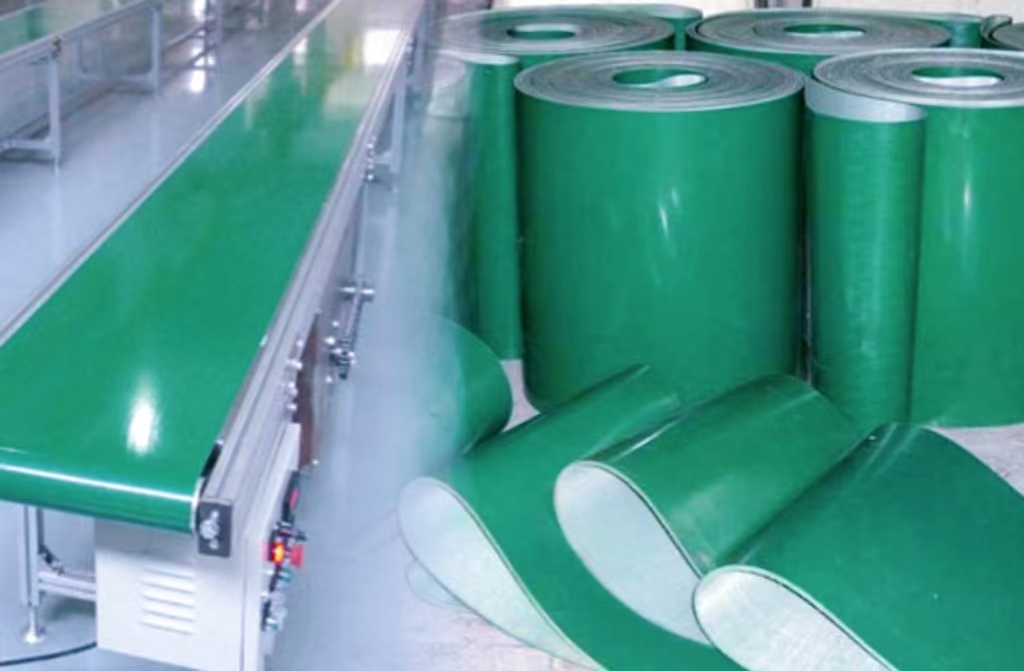
Polyvinyl Chloride (PVC) is a popular choice for conveyor belt material due to its unique blend of properties that cater to a wide array of industrial applications. Below is a detailed overview of PVC conveyor belts, highlighting their properties, advantages, and how they compare to other types of conveyor belt materials.
Aspect | PVC Conveyor Belt | Comparison with Other Materials |
---|---|---|
Properties | Durable, chemically resistant, flexible, cost-effective, low maintenance | Rubber belts may offer higher durability and temperature resistance; fabric belts are lighter but less durable; TPU belts provide superior resistance to oils and chemicals but are more expensive. |
Advantages | Cost-efficiency, versatility, suitable for a wide range of applications, easy to maintain | Offers a balanced solution between the high durability of rubber and the light-duty application of fabric belts; more economical than TPU in general applications. |
Typical Applications | Food processing, pharmaceuticals, manufacturing, distribution centers | Rubber belts are preferred in heavy-duty applications; fabric belts in light applications; TPU belts in applications requiring high chemical resistance. |
PVC vs. Other Conveyor Belt Materials
- Durability: PVC belts provide sufficient durability for many applications, though rubber belts may be chosen for extreme conditions.
- Chemical Resistance: PVC offers good resistance to many chemicals, making it suitable for various industries, though TPU belts excel in environments with high exposure to oils and aggressive chemicals.
- Flexibility: PVC belts maintain flexibility, ensuring smooth operations, comparable to rubber but more flexible than many fabric belts.
- Cost-Effectiveness: One of the key advantages of PVC conveyor belts is their cost-effectiveness, providing a reliable solution at a lower price point compared to rubber and TPU belts.
- Maintenance: PVC belts are known for their low maintenance requirements, contributing to lower operational costs over time.
PVC conveyor belt material stands out for its versatility, balancing cost, durability, and performance. It serves as an excellent choice for a wide range of industrial applications, from food processing to distribution centers, offering a practical solution that meets the needs of various operations while ensuring efficiency and cost savings.ings.
Discover the unmatched durability and performance of our conveyor belts—contact us today!
Advantages and Disadvantages of Different Conveyor Belt Material
Rubber
Advantages:
Rubber is one of the most commonly used materials for conveyor belts due to its high durability, flexibility, and excellent shock absorption properties. These attributes make rubber conveyor belts particularly suitable for heavy-duty applications where they are exposed to significant wear and tear. Rubber belts can withstand high impacts and are resistant to various environmental factors, such as moisture and chemicals. They also provide a good grip, which is essential for transporting materials over inclines or declines.
Disadvantages:
The primary disadvantages of rubber conveyor belts are their weight and cost. Rubber is heavier compared to other materials, which can result in higher energy consumption to drive the conveyor system. This increased weight also makes installation and maintenance more challenging. Additionally, high-quality rubber belts can be more expensive than other options, making them a less cost-effective choice for certain applications.
PVC (Polyvinyl Chloride)
Advantages:
PVC conveyor belts are lightweight, cost-effective, and resistant to a wide range of chemicals. These properties make PVC belts ideal for industries such as food processing and pharmaceuticals, where hygiene and chemical resistance are crucial. PVC belts are also easy to clean and maintain, contributing to their popularity in environments that require strict cleanliness standards.
Disadvantages:
While PVC belts are suitable for many applications, they are less durable under heavy loads compared to rubber or steel cord belts. PVC belts can wear out more quickly when subjected to high stress or abrasive materials. Additionally, they are not as flexible as rubber, which can limit their use in applications that require frequent bending or flexing of the belt.
PU (Polyurethane)
Advantages:
Polyurethane (PU) conveyor belts are known for their high wear resistance, lightweight nature, and versatility. PU belts are highly resistant to cuts and abrasions, making them suitable for applications involving sharp or rough materials. They are also resistant to oil, grease, and other chemicals, which enhances their durability in harsh environments. The versatility of PU belts allows them to be used in a wide range of industries, from packaging to automotive.
Disadvantages:
The main drawback of PU conveyor belts is their cost. PU belts can be more expensive than PVC or fabric belts, which can be a consideration for budget-conscious operations. Additionally, while PU belts are durable, they may not offer the same level of flexibility as rubber belts, which can be a limitation in certain applications.
Fabric
Advantages:
Fabric conveyor belts are a low-cost and flexible option, making them suitable for light to medium-duty applications. They are often used in industries such as agriculture and logistics, where the loads are not excessively heavy. Fabric belts are easy to handle and install, and they offer good resistance to impacts and wear.
Disadvantages:
The main disadvantage of fabric conveyor belts is their lower load capacity and durability compared to rubber or steel cord belts. Fabric belts can wear out more quickly under heavy loads or in abrasive conditions. They may also require more frequent maintenance and replacement, which can increase the overall cost of operation.
Steel Cord
Advantages:
Steel cord conveyor belts are extremely strong and durable, making them ideal for long-distance and heavy load transportation. These belts are capable of withstanding high tensile forces and are highly resistant to cuts, abrasions, and impacts. Steel cord belts are often used in mining and other heavy-duty industries where reliability and longevity are paramount.
Disadvantages:
The primary disadvantages of steel cord conveyor belts are their weight and cost. Steel cord belts are heavier than other types, which can lead to higher energy consumption and more challenging installation processes. Additionally, the initial cost of steel cord belts can be higher than other materials, although their durability and low maintenance needs can offset this over time.
Used Conveyor Belt Material
The market for used conveyor belt material is an integral part of the recycling and sustainability efforts within the industrial sector. This market not only supports environmental initiatives but also offers economic advantages to various industries looking to optimize their operations cost-effectively.
Environmental and Economic Benefits
The reuse of conveyor belt material significantly reduces the environmental impact by diverting waste from landfills and decreasing the demand for new raw materials.Besides,Opting for used conveyor belt material can lead to substantial cost savings, as these materials are often available at a lower price point compared to new ones, without compromising on functionality for many applications.
Considerations When Opting for Used Conveyor Belt Material
- Application Suitability: Assess whether the used conveyor belt material is appropriate for your specific application, considering factors such as the type of goods it will carry and the environmental conditions it will be exposed to.
- Material Condition: Examine the condition of the used conveyor belt material to ensure it has not been excessively worn or damaged, which could affect its performance and longevity.
- Compatibility: Ensure that the used conveyor belt material is compatible with your existing conveyor system, including the size, width, and tensile strength requirements.
- Safety Standards: Verify that the used conveyor belt material meets all relevant safety standards and regulations, particularly if it will be used in food processing or other sensitive applications.
- Environmental Compliance: Confirm that the process of repurposing the used conveyor belt material complies with environmental regulations and standards, supporting your company’s sustainability goals.
- Supplier Reputation: Source used conveyor belt material from reputable suppliers who can provide detailed information about the material’s history, condition, and previous applications.
- Longevity Expectations: Consider the expected lifespan of the used conveyor belt material in your specific application to ensure it offers a viable long-term solution.
- Maintenance Requirements: Be aware that used conveyor belt material may require more frequent maintenance or repairs, and factor these potential costs into your decision-making process.
- Quantity and Availability: Check the availability of the used conveyor belt material in the quantities you need and consider any lead times that may impact your project timeline.
- Post-Use Disposal: Plan for the eventual disposal of the used conveyor belt material, ensuring that it can be recycled or repurposed again to minimize environmental impact.
By carefully considering these factors, businesses can effectively leverage the benefits of used conveyor belt material, contributing to environmental sustainability while achieving cost savings and operational efficiency.
Conveyor Belt Material Near Me
Finding reliable suppliers and manufacturers of conveyor belt material locally can be a crucial step in ensuring the efficiency and longevity of your conveyor system.
Tips to Help You Locate Quality Conveyor Belt Material
- Online Directories and Marketplaces: Utilize industrial supply directories and online marketplaces to find listings of conveyor belt material suppliers in your area.
- Industry Associations: Contact associations related to the conveyor industry, as they often have directories of member companies that include suppliers and manufacturers of conveyor belt materials.
- Trade Shows and Expos: Attend industry-specific trade shows and expos where suppliers and manufacturers showcase their products, offering a great opportunity to find conveyor belt material locally.
- Referrals: Ask for referrals from industry peers or businesses that operate similar conveyor systems. Personal recommendations can lead you to reputable local suppliers.
- Local Industrial Parks: Visit local industrial parks where manufacturers and suppliers are likely to be located, and inquire directly.
- Search Engines: Use search engines with specific geographic filters or keywords like “conveyor belt material near me” to find local suppliers.
- Social Media and Forums: Explore industry-specific forums and social media groups where members might share recommendations for local suppliers.
- Local Business Directories: Check local business directories, both online and in print, for listings of conveyor belt material suppliers.
- Consultants and Contractors: Speak with consultants and contractors who specialize in conveyor systems; they often have connections with local suppliers.
- Manufacturing Extension Partnerships: Contact your state’s Manufacturing Extension Partnership (MEP) center, which provides support to manufacturing businesses and may have information on local suppliers.
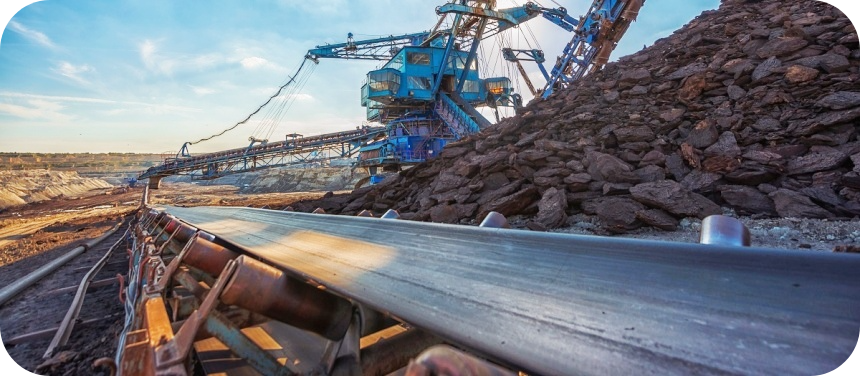
Importance of Sourcing Quality Materials for Conveyor Belt Construction and Maintenance
- Durability: High-quality materials ensure that the conveyor belt can withstand the operational demands, reducing the risk of breakdowns and extending the belt’s lifespan.
- Safety: Quality conveyor belt materials are less likely to fail, reducing the risk of accidents and ensuring the safety of workers and the materials being transported.
- Efficiency: Superior materials contribute to the smooth and efficient operation of the conveyor system, minimizing energy consumption and operational costs.
- Compliance: Quality materials are more likely to meet industry standards and regulatory requirements, ensuring compliance and avoiding potential legal issues.
- Maintenance Costs: Investing in quality conveyor belt materials can reduce the frequency and cost of maintenance and repairs.
- Reputation: Using reliable and durable conveyor belt materials can enhance your company’s reputation for quality and reliability.
- Customization: High-quality suppliers often offer more options for customization, allowing you to get conveyor belt materials tailored to your specific needs.
- Support and Service: Reputable suppliers of quality materials usually provide better customer support and after-sales service, ensuring assistance when needed.
Sourcing quality conveyor belt material from reputable local suppliers ensures that your conveyor system operates efficiently, safely, and cost-effectively, contributing to the overall success of your operations.
Conveyor Belt Material Manufacturers
The landscape of conveyor belt material manufacturers is diverse, with several leading companies setting the standard through innovation, quality, and service. These manufacturers are pivotal in driving advancements in conveyor belt technology, ensuring that industries have access to the most efficient, durable, and reliable materials.
Leading Manufacturers
Gram Conveyor
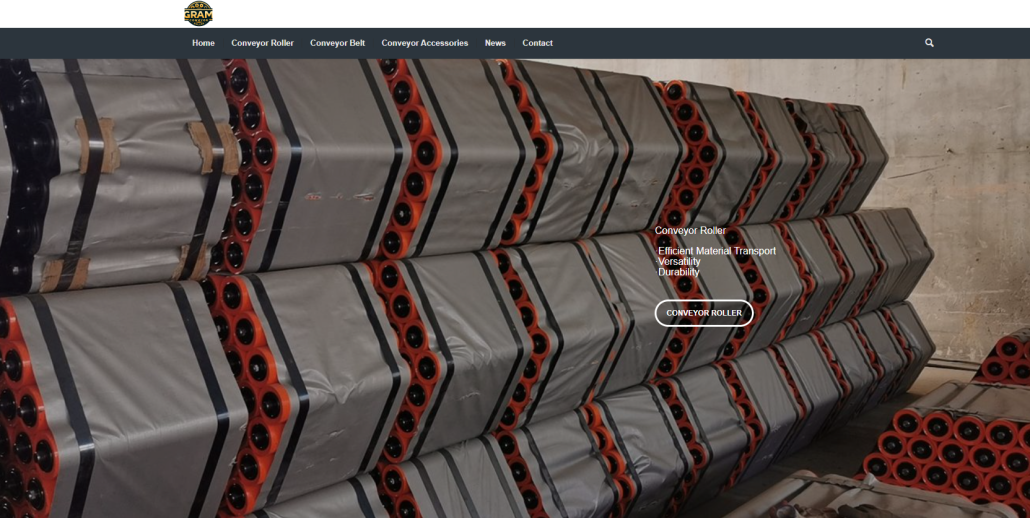
At Gram Conveyor, we specialize in providing comprehensive conveyor solutions tailored to meet the diverse needs of our clients. Our product range includes Conveyor Rollers, such as Mining Conveyor Belts, Steel Cord Conveyor Belts, Nylon Conveyor Belts, and Fabric Conveyor Belts. We also offer robust Conveyor Belts and a variety of Conveyor Accessories. With a focus on innovation and customer satisfaction, we cater to diverse industries, ensuring efficient material handling and enhanced operational performance. Our commitment to excellence makes us a trusted partner for your conveyor needs.
ContiTech AG

A division of Continental AG, ContiTech is renowned for its high-quality, innovative conveyor belt solutions that cater to various industries, including mining, construction, and food processing. Their use of advanced materials and technology sets them apart.
Bridgestone Corporation
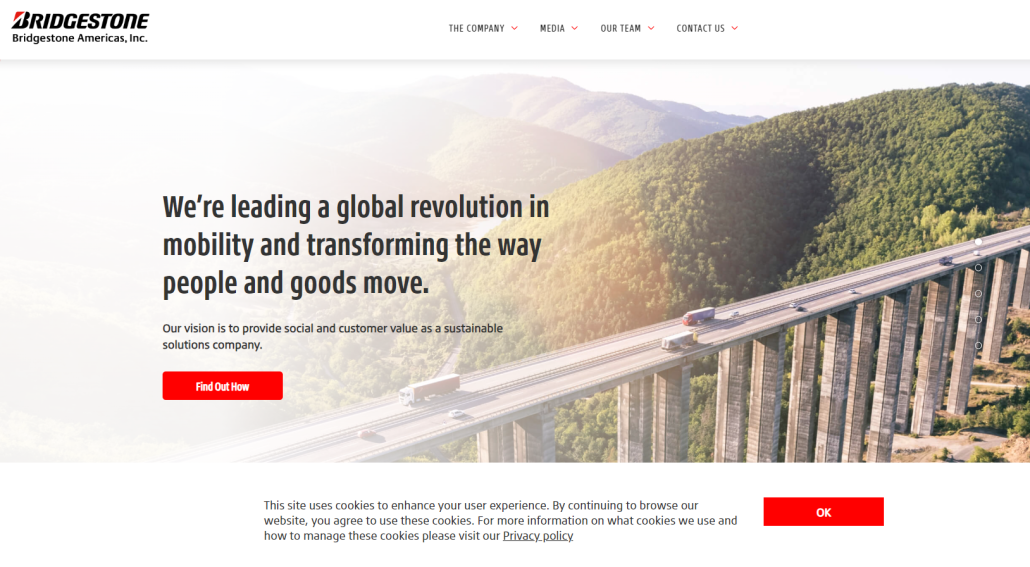
Bridgestone is a global leader known for its development of high-strength and environmentally friendly conveyor belt materials. Their commitment to sustainability and innovation in rubber compounds makes them a preferred choice.
Fenner Group
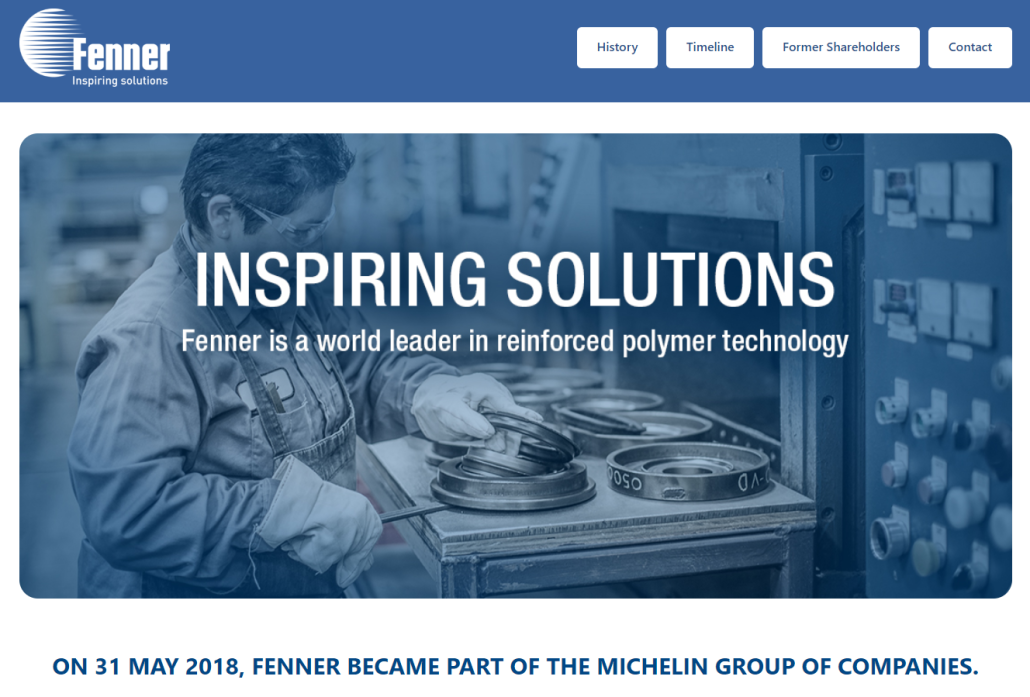
Fenner is recognized for its precision-engineered conveyor belt solutions designed for efficiency and longevity. Their products are tailored to meet specific industry needs, from heavy-duty mining to light industrial applications.
Habasit
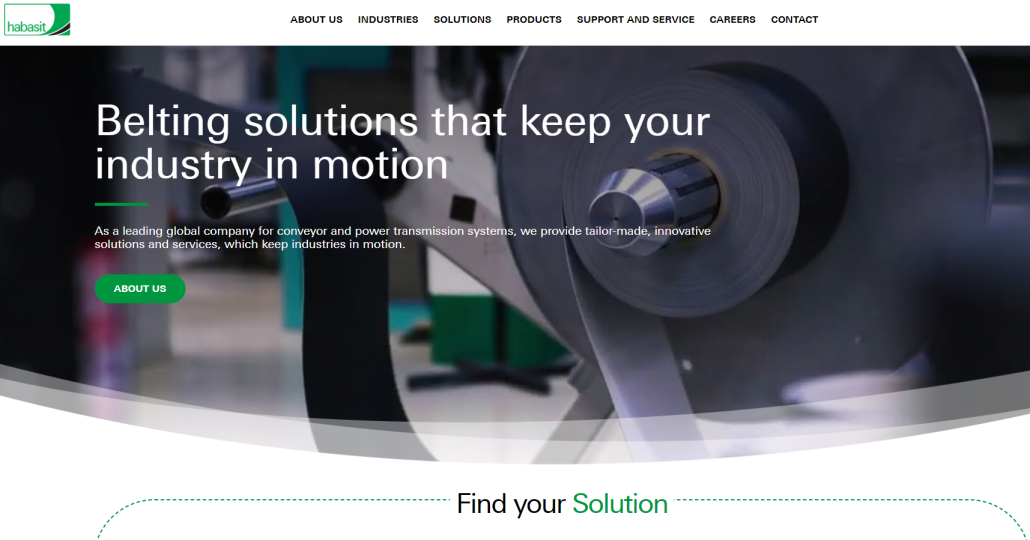
Specializing in lightweight conveyor belting, Habasit’s products are integral to the food, textile, and packaging industries. Their focus on customization and material innovation ensures optimal conveyor performance.
Intralox
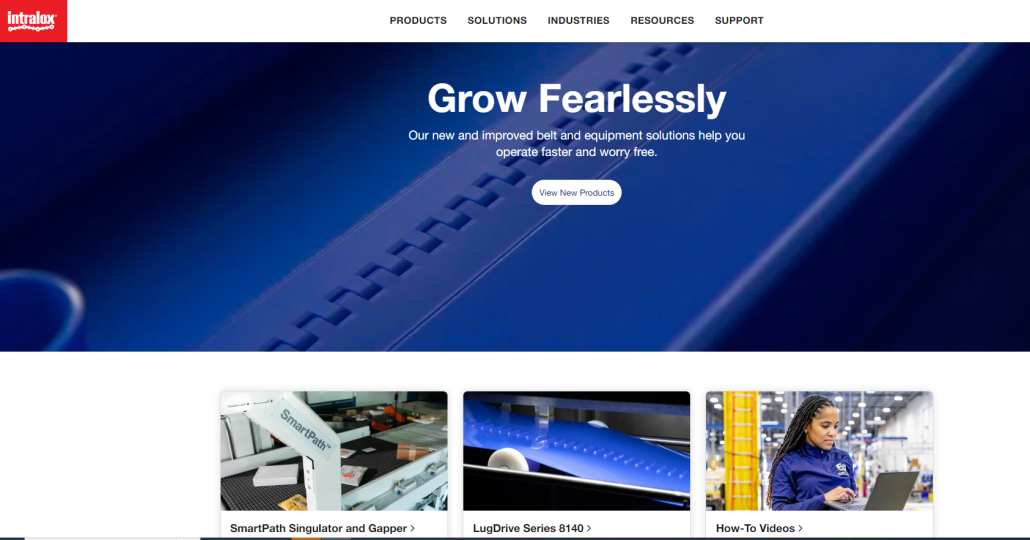
Intralox leads in modular plastic conveyor belt technology, offering solutions that enhance line efficiency and product handling. Their commitment to problem-solving and modular design sets them apart in the industry.
Innovations in Conveyor Belt Materials
- Eco-Friendly Materials: Manufacturers are increasingly focusing on developing conveyor belt materials that are environmentally friendly, using recycled materials and reducing energy consumption during production.
- Smart Belting Technologies: The integration of sensors and IoT technology into conveyor belt materials is a significant trend. These smart belts can monitor their own health, predict maintenance needs, and even optimize conveyor performance in real-time.
- High-Performance Compounds: Advances in rubber and plastic compounds have led to conveyor belt materials that are more durable, resistant to extreme temperatures, chemicals, and wear, extending the life of conveyor systems.
- Energy-Efficient Designs: Manufacturers are creating materials and designs that reduce the energy consumption of conveyor systems. Low-rolling resistance rubber, for example, minimizes the energy needed to move the belt, leading to cost savings and reduced environmental impact.
- Hygienic and Safe Materials: Especially in the food processing industry, manufacturers are innovating with materials that are easy to clean, resist bacterial growth, and comply with strict hygiene standards.
Conveyor belt material manufacturers play a crucial role in the efficiency and effectiveness of conveyor systems across industries. Through continuous innovation and a commitment to quality, these manufacturers are ensuring that conveyor belts meet the evolving needs of businesses, enhancing productivity and operational efficiency.
Types of Conveyor Belt Joints
The integrity and performance of a conveyor system are significantly influenced by the type of joints used to connect sections of conveyor belt material. The choice of joint type is crucial, as it must complement the material’s properties and the application’s specific requirements.
Primary Types of Conveyor Belt Joints
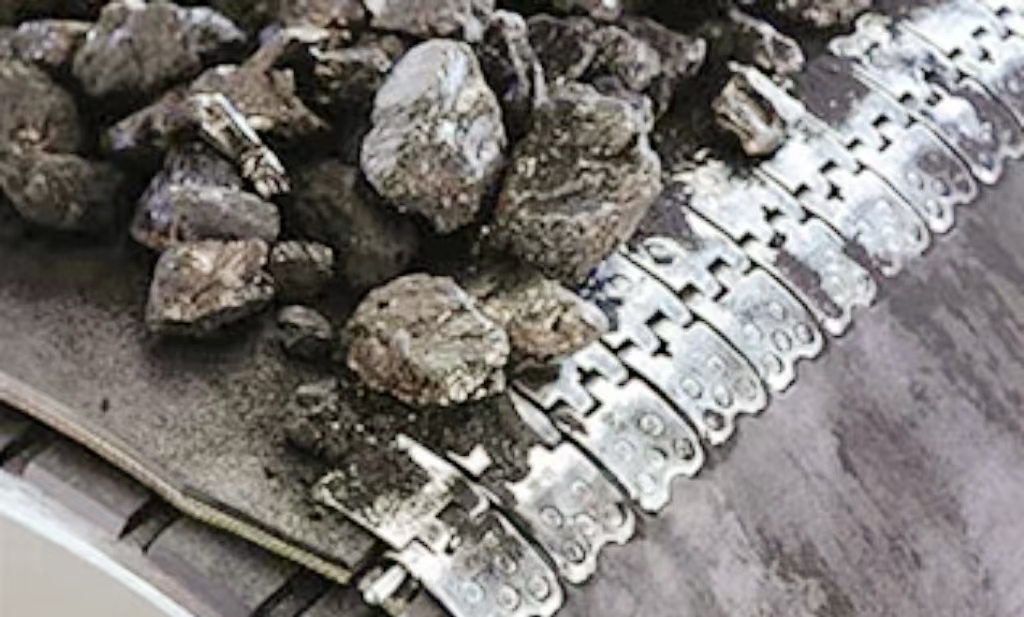
Joint Type | Description | Suitable for Conveyor Belt Material | Significance |
---|---|---|---|
Vulcanized Joints | Utilizes heat and pressure to splice the belt ends together, creating a strong, seamless bond. | Rubber, Thermoplastics | Ideal for heavy-duty applications; provides a smooth surface that minimizes wear on the belt and conveyed materials. |
Mechanical Fastening | Involves metal fasteners or plastic rivets to join the belt ends, allowing for easy installation and repair. | Rubber, Fabric, PVC | Suitable for applications where frequent belt changes or repairs are expected; allows for quick and easy maintenance. |
Finger Joints | The belt ends are cut into interlocking 'fingers' and bonded together, offering flexibility and strength. | Fabric, Lightweight Rubber | Common in light to medium-duty applications; provides a balance between strength and flexibility. |
Peek Joints | Employed in belts made from thermoplastic materials, involving welding the belt ends together. | Thermoplastics (e.g., PU, PVC) | Ensures a strong bond without compromising flexibility; suitable for applications requiring a high degree of hygiene. |
Skived Joints | The belt ends are thinned and overlapped, then bonded, creating a flat, low-profile joint. | Rubber, Thermoplastics | Reduces the risk of snagging or catching on conveyed materials; ideal for applications where a smooth joint is critical. |
Significance of Choosing the Right Type of Joint
Selecting the appropriate joint type for conveyor belt material is paramount for several reasons:
- Durability and Strength: The joint must withstand the operational stresses placed upon the belt, including load weight, speed, and environmental conditions, without failing.
- Operational Efficiency: A well-chosen joint ensures smooth belt operation, minimizing disruptions and maintenance requirements, which can impact productivity.
- Compatibility with Belt Material: The joint type must be compatible with the conveyor belt material to maintain the belt’s integrity and performance characteristics. For instance, vulcanized joints are preferred for rubber belts due to their strength and flexibility, while mechanical fastening might be more suitable for belts that require frequent modifications or repairs.
- Application Requirements: The specific demands of the application, such as the need for sanitary conditions in food processing or resistance to chemicals in manufacturing, can dictate the most appropriate joint type.
The choice of joint type is a critical consideration in the design and maintenance of conveyor systems, directly impacting the performance, reliability, and longevity of the conveyor belt material. Understanding the properties and requirements of different conveyor belt materials is essential in selecting the most suitable joint type for any given application.
Conveyor Belt Material Selection
Selecting the right conveyor belt material is a critical decision that significantly impacts the efficiency, safety, and longevity of a conveyor system. Various factors must be considered to ensure that the chosen material meets the specific demands of the application environment, load type, conveyor type, and industry requirements. Here we explore these factors in detail and provide case studies to illustrate the importance of careful material selection in different industrial contexts.
Factors to Consider
- Application Environment: The environmental conditions, such as temperature, humidity, exposure to chemicals, or abrasive materials, can greatly influence the choice of conveyor belt material. For instance, silicone is preferred in high-temperature applications, while PVC might be chosen for its chemical resistance.
- Load Type: The nature of the materials being transported, including their weight, shape, and abrasiveness, dictates the required durability and strength of the conveyor belt material. Heavy or sharp items might necessitate a sturdy metal belt, whereas lighter goods could be accommodated by fabric or rubber belts.
- Conveyor Type: The design of the conveyor system, including its length, width, speed, and the presence of inclines or curves, affects the flexibility and tensile strength required of the conveyor belt material.
- Industry Requirements: Specific industries have unique requirements, such as food-grade materials for the food processing industry or flame-resistant materials for mining applications.
Case Studies
Food Processing Industry:
At Baker’s Delight, a leading bakery known for its artisanal bread and pastries, a specialized conveyor belt was needed to withstand high temperatures and ensure easy cleaning. They selected a silicone conveyor belt from BeltPro Industries for its exceptional heat resistance and non-stick properties. This choice not only ensured efficient operation but also met the stringent hygiene standards crucial to their business.
Mining Industry:
Mountain Mining Co. faced the challenge of transporting sharp and heavy materials in their mining operation. They required a conveyor belt with high tensile strength and excellent abrasion resistance. After careful consideration, they chose a steel-reinforced rubber belt from MineBelt Solutions. This durable belt proved capable of withstanding the harsh mining environment, ensuring long-lasting and reliable performance.
Pharmaceutical Industry:
PharmaTech Inc., a renowned pharmaceutical company, needed a conveyor belt suitable for their cleanroom environment, emphasizing easy sterilization. They opted for a polyurethane (PU) conveyor belt from CleanBelt Technologies. Known for its resistance to chemicals and ease of cleaning, this belt met the stringent hygiene standards of the pharmaceutical industry, ensuring safe and contamination-free operations.
Packaging Industry:
PackPro Industries, a dynamic packaging facility, required a flexible conveyor belt to handle products of various shapes and sizes. They selected a modular plastic conveyor belt from FlexiBelt Solutions for its versatility and ease of maintenance. This belt’s ability to accommodate changes in the production line ensured seamless operations and enhanced productivity.
Agriculture Industry:
GreenFields Agro, a leading agricultural business, needed a conveyor belt for transporting grain. They chose a fabric conveyor belt with a high-grip surface from AgroBelt Systems. This belt’s design prevented slippage and ensured gentle handling of the grain, significantly reducing waste and damage while maintaining the quality of their products.
Recycling Industry:
EcoRecycle Plant required a conveyor belt capable of handling a variety of materials, including metals, plastics, and paper, without suffering damage. They selected a durable rubber conveyor belt with high impact resistance from RecycleBelt Technologies. This robust belt withstood the diverse materials processed at the plant, contributing to efficient and reliable recycling operations.
These case studies illustrate the importance of considering various factors when selecting conveyor belt material, ensuring that the chosen material is perfectly suited to the application’s specific demands. By carefully matching the conveyor belt material to the operational requirements, businesses can optimize their conveyor systems for maximum efficiency, safety, and longevity.
Get the best deals on high-quality conveyor belts. Inquire now!
Types of Conveyor Belt in Industry
The diversity of industries that utilize conveyor systems is matched by the variety of conveyor belt materials designed to meet specific operational needs and regulatory requirements. From food processing to mining and packaging, each sector demands conveyor belts with unique properties to ensure efficiency, safety, and compliance. This discussion highlights how different conveyor belt materials are tailored to industry-specific applications and the critical role these materials play in maintaining safety and regulatory standards, particularly in sensitive industries like food processing.
Food Processing Industry
- Material Requirements: Conveyor belt materials in the food processing industry must be non-toxic, easy to clean, and resistant to bacteria growth to ensure food safety. Materials like polyurethane (PU), polyvinyl chloride (PVC), and silicone are commonly used due to their compliance with food safety regulations.
- Role in Safety and Compliance: In food processing, the conveyor belt material must meet stringent hygiene standards set by regulatory bodies like the FDA and USDA. The right material selection is crucial to prevent contamination and ensure that the food products are safe for consumption.
Mining Industry
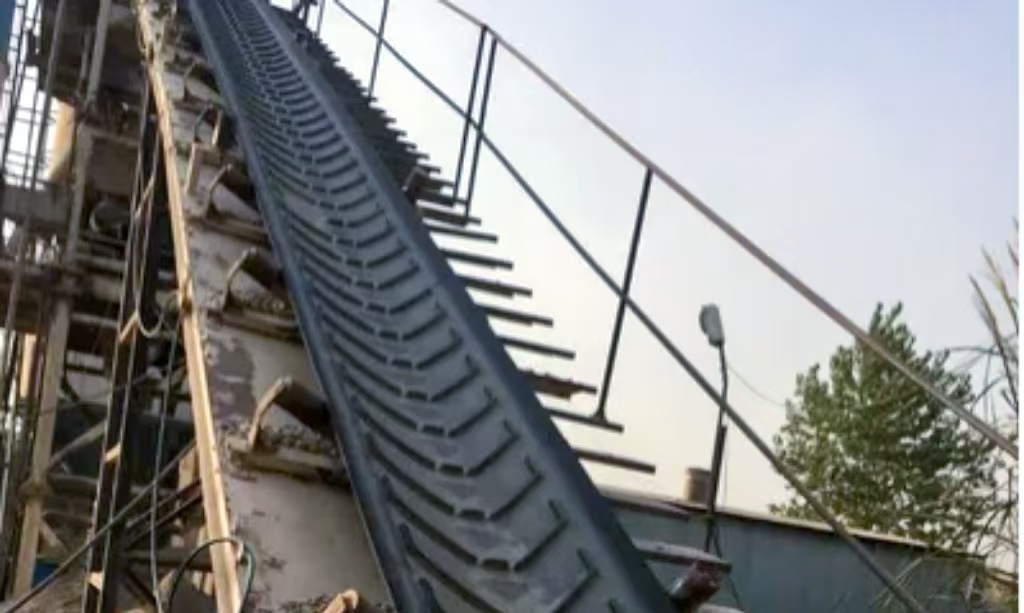
- Material Requirements: The harsh conditions of the mining industry require conveyor belts that are durable, abrasion-resistant, and capable of handling heavy loads. Rubber conveyor belts reinforced with metal or synthetic fabrics are typically used to withstand the tough mining environment.
- Role in Safety and Compliance: In mining, conveyor belt material must also be selected with safety in mind, ensuring resistance to fire and static electricity to prevent accidents in potentially hazardous conditions.
Packaging Industry
- Material Requirements: Conveyor belts in the packaging industry need to be versatile to handle various products and packaging materials. Materials like PVC and lightweight fabrics are favored for their flexibility, low maintenance, and efficiency in transporting packaged goods.
- Role in Safety and Compliance: While safety regulations in the packaging industry may not be as stringent as in food processing or mining, conveyor belt materials still need to ensure the safe and smooth transport of goods, preventing damage to the products and injuries to workers.
Other Industries
- Agriculture: Conveyor belts made of fabric or rubber materials are used for the gentle handling of agricultural products like grains and vegetables, ensuring minimal damage during transport.
- Recycling: Durable rubber conveyor belts are preferred in recycling plants to handle a variety of materials, including metals, plastics, and paper, contributing to efficient recycling processes.
- Pharmaceuticals: The pharmaceutical industry requires conveyor belts made of materials that are easy to sterilize and resistant to chemical contamination, such as PU and certain grades of stainless steel, to maintain product purity.
The selection of conveyor belt material is a critical decision that directly impacts the operational efficiency, safety, and regulatory compliance of industries relying on conveyor systems. By understanding the specific needs of each industry and the properties of different conveyor belt materials, businesses can ensure that their conveyor systems enhance productivity while adhering to the highest safety and quality standards.
FAQs about Conveyor Belt Material
Conveyor belts are versatile components used in a variety of industries, and their materials can vary significantly based on the application. Generally, conveyor belts are made from materials that provide a balance between durability, flexibility, and cost-effectiveness. The hard black rubber material blends neoprene, nitrile, and SBR, reinforced with durable cloth fabric, making it highly affordable and strong. The most common materials include rubber, PVC (Polyvinyl Chloride), polyurethane, and fabric such as nylon or polyester. Rubber belts, for instance, are prized for their durability and elasticity, making them suitable for heavy-duty applications. PVC belts are popular in food industry applications due to their resistance to chemicals and ease of cleaning. Polyurethane belts offer excellent resistance to wear, tear, and various chemicals, making them ideal for both food processing and industrial environments. Fabric belts, often used in combination with other materials, provide additional strength and flexibility. The choice of material depends on several factors, including the type of goods being transported, the environment (e.g., temperature, presence of chemicals), and the required speed and efficiency of the conveyor system.
Metal is often used in conveyor belts either as the primary material or as a reinforcing component. The most commonly used metal is steel, including both carbon steel and stainless steel. Carbon steel is known for its strength and durability, making it suitable for heavy-duty applications and environments where the belt may be subject to high levels of stress and wear. Stainless steel, on the other hand, is used in environments where resistance to corrosion is necessary, such as in food processing or chemical industries. Stainless steel belts are also appreciated for their ease of cleaning and maintenance, making them ideal for applications where hygiene is a priority. In some cases, other metals such as aluminum may be used for specific applications where lightweight properties are desired, though these are less common.
The composition of a conveyor belt can be complex, as it often involves several layers and materials to provide the desired properties and performance. A typical conveyor belt consists of a top cover, a carcass, and a bottom cover. The top cover is designed to protect the belt from wear, abrasion, and impact while also offering resistance to substances it may come into contact with. The carcass is the core of the belt, providing structural strength and shape. It is usually made from fabrics like polyester, nylon, or cotton, or from metal wires or meshes in the case of metal belts. The bottom cover mirrors the top cover but is often designed to minimize friction as the belt moves over conveyor rollers or surfaces. Additionally, belts may include special features like cleats or sidewalls for handling particular types of materials or for operating on inclines. The specific composition and materials used in a conveyor belt are carefully selected based on the application’s requirements, including load capacity, speed, environmental conditions, and the nature of the materials being transported.
The raw materials used in the production of conveyor belts include polymers, fabrics, metals, and various additives. Polymers such as rubber (natural or synthetic), PVC, and polyurethane are common for the belt’s body and covers, providing flexibility, durability, and resistance to various environmental factors. Fabrics like nylon, polyester, and cotton are used to reinforce the belt, offering strength and stability. Metals, primarily steel (carbon or stainless), are used in belts for added strength, particularly in applications requiring resistance to heavy loads or sharp objects. Additives play a crucial role in enhancing the properties of conveyor belts; these can include plasticizers to improve flexibility, antioxidants to prevent degradation, and flame retardants to increase safety in fire-prone environments. The choice of raw materials is critical to the belt’s performance, lifespan, and suitability for specific applications, ensuring that it meets the operational demands of the industry it serves.
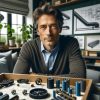
Jordan Smith, a seasoned professional with over 20 years of experience in the conveyor system industry. Jordan’s expertise lies in providing comprehensive solutions for conveyor rollers, belts, and accessories, catering to a wide range of industrial needs. From initial design and configuration to installation and meticulous troubleshooting, Jordan is adept at handling all aspects of conveyor system management. Whether you’re looking to upgrade your production line with efficient conveyor belts, require custom conveyor rollers for specific operations, or need expert advice on selecting the right conveyor accessories for your facility, Jordan is your reliable consultant. For any inquiries or assistance with conveyor system optimization, Jordan is available to share his wealth of knowledge and experience. Feel free to reach out at any time for professional guidance on all matters related to conveyor rollers, belts, and accessories.