How Are Conveyor Belts Made: Manufacturing Process Explained
Conveyor belts are integral components in a myriad of industries, streamlining operations in manufacturing, mining, agriculture, and logistics, to name a few. These belts facilitate the efficient transport of goods and materials over short and long distances, playing a pivotal role in production lines and material handling systems. The question of how are conveyor belts made unveils the intricate processes and diverse materials involved in their creation. From the initial selection of raw materials to the final stages of vulcanization and inspection, the manufacturing of conveyor belts is a complex procedure that requires precision and expertise. This complexity is further amplified by the variety of materials used, including rubber, fabric, and steel, each chosen for its specific properties to meet the unique demands of different applications. Understanding the manufacturing process sheds light on the durability and reliability of conveyor belts in various industrial settings.
What is Conveyor Belt Materials and How Are Conveyor Belts Made
Delving into how conveyor belts are made requires a comprehensive understanding of the materials that form the backbone of these essential industrial components. The choice of material significantly influences the belt’s performance, durability, and application suitability. Here, we explore the main materials used in conveyor belt construction and the role of additives in enhancing belt strength.
Main Materials in Conveyor Belt Construction
- Rubber: Rubber is the most prevalent material in conveyor belt construction, prized for its elasticity, resilience, and ability to withstand various environmental conditions. Natural rubber, or latex, is harvested from rubber trees and processed into a durable material suitable for the demanding conditions of conveyor systems. Synthetic rubbers, such as SBR (Styrene-Butadiene Rubber) and NBR (Nitrile Butadiene Rubber), offer specific advantages like oil and chemical resistance.
- Thermoplastics: Materials like PVC (Polyvinyl Chloride) and PU (Polyurethane) are used in environments where flexibility, hygiene, and resistance to chemicals are paramount. PVC belts are common in food processing industries due to their ease of cleaning, while PU belts offer superior resistance to wear, tear, and various chemicals.
- Metal: Metal belts, made from stainless steel or carbon steel, are chosen for their strength, heat resistance, and durability. They are ideal for high-temperature applications or environments where the belt’s strength is critical, such as in heavy manufacturing or mining.
- Fabric: Fabrics like nylon, polyester, and cotton are used for their flexibility, cost-effectiveness, and suitability for a range of applications. These materials are often used as reinforcement layers within rubber belts to enhance conveyor belt tensile strength and reduce elongation.
- Leather: Leather belts, though less common in heavy industrial applications, are valued in specific niches for their natural grip, durability, and aesthetic appeal. They are often found in packaging and light manufacturing environments.
Comparative Analysis of Popular Conveyor Belt Materials
Material | Flexibility | Durability | Resistance | Application Examples |
---|---|---|---|---|
Rubber | High | High | Varied | Mining, Manufacturing |
PVC | Medium | Medium | Chemicals | Food Processing |
PU | High | High | Wear, Tear | Chemical Processing |
Stainless Steel | Low | Very High | Heat | High-Temperature Processes |
Nylon | High | Medium | Abrasion | Packaging, Light Manufacturing |
Enhancing Conveyor Belt Strength with Additives
- Fabric: Fabrics like nylon and polyester are woven into the belt’s carcass, providing tensile strength and reducing stretch. This ensures the belt can carry heavy loads without deforming.
- Steel: Steel cords or meshes are incorporated into a steel cord rubber conveyor belt designed for heavy-duty applications, offering unmatched strength and durability. These belts are essential in mining and heavy material handling where the risk of cuts and impacts is high.
- Polyester: Polyester fibers are used for their low stretch, high strength, and good resistance to mildew and abrasion. They are often used in the belt carcass to maintain belt shape under load.
- Fiberglass: Fiberglass is used in belts requiring low stretch, high strength, and good resistance to heat. It’s particularly useful in high-temperature environments where other materials might degrade.
- Kevlar: For extreme applications, Kevlar can be used as an additive to provide high tensile strength, resistance to heat, and durability. Its use is more niche due to its cost but is invaluable in high-performance belts.
Each material and additive is chosen based on the specific requirements of the application, ensuring the conveyor belt performs optimally under the intended conditions.
The Conveyor Belt Manufacturing Process and How Are Conveyor Belts Made
Understanding how are conveyor belts made involves delving into the detailed manufacturing process, which is both intricate and critical for ensuring the final product’s quality and performance. This process is divided into several key steps, each playing a vital role in the conveyor belt’s construction.
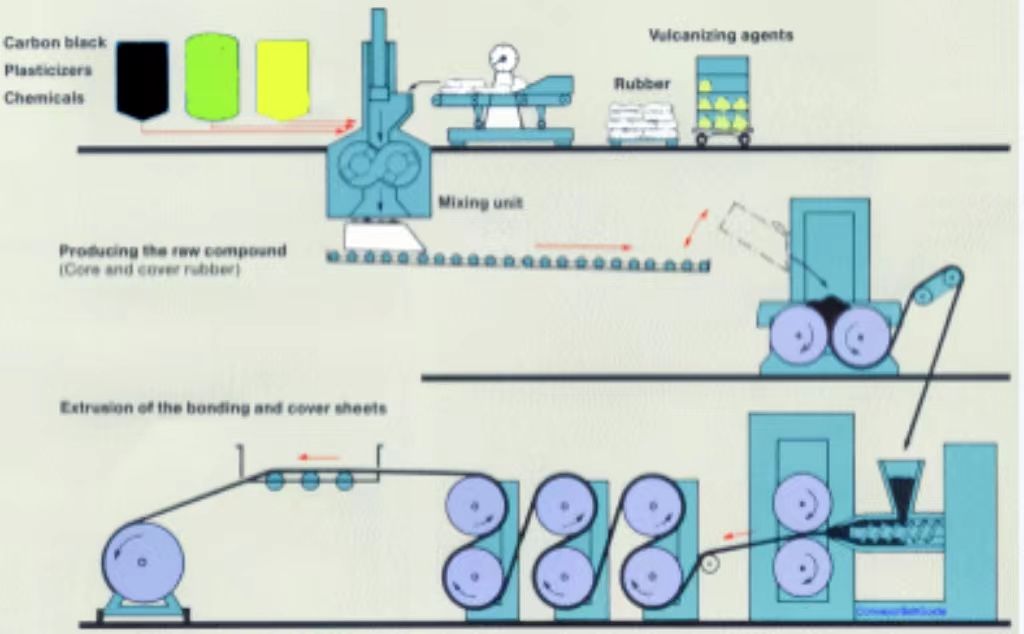
Step 1: Mixing
The journey of conveyor belt manufacturing begins with the mixing process, where rubber is blended with various substances to achieve a specific, uniform blend. This step is crucial because the rubber’s inherently adhesive nature makes it challenging to achieve a consistent mixture. Internal mixers play a pivotal role here, ensuring that the rubber and additives are thoroughly combined. The goal is to create a homogenous compound that possesses the desired properties for the intended application, such as flexibility, durability, and resistance to environmental factors.
Step 2: Calendaring
Following mixing, the calendaring process involves the fabric coating, cover sheeting, and bonding processes. This step is essential for forming the conveyor belt’s structure and ensuring its strength and durability. The importance of drying the fabric before coating cannot be overstated, as it prevents several potential issues during vulcanization, such as:
- Blistering: Moisture trapped in the fabric can turn into steam during vulcanization, causing blisters in the rubber.
- Delamination: Insufficient drying can lead to poor adhesion between the fabric and rubber, causing layers to separate.
- Weak Bonding: Properly dried fabric ensures optimal penetration of the rubber compound, resulting in strong mechanical bonds.
- Inconsistent Properties: Moisture can affect the curing process, leading to uneven properties across the belt.
- Reduced Lifespan: Trapped moisture can accelerate degradation of the fabric and rubber, reducing the belt’s overall lifespan.
- Quality Control Issues: Moisture can lead to variations in thickness and texture, complicating quality control.
Step 3: Laminating
Laminating involves adhering multiple layers of materials together to form a belt blank. This step is critical for ensuring the belt’s structural integrity and operational reliability. Maintaining consistent tension during laminating is crucial because it prevents the formation of wrinkles and ensures uniform thickness and strength across the belt. Inconsistent tension can lead to weak spots, premature wear, and potential failure under load, emphasizing the need for precision in this phase of manufacturing.
Step 4: Vulcanizing
Vulcanization is the transformative step where the rubber compound’s properties are enhanced through a controlled heating process. This step cross-links the rubber’s molecular structure, resulting in increased strength, elasticity, and resistance to environmental factors. Vulcanization ensures that the conveyor belt can withstand the rigors of its intended use, from heavy loads to extreme temperatures and abrasive conditions.
Step 5: Inspecting/Packing
The final step in how it’s made conveyor belt is the thorough inspection and packing of the finished product. Quality checks are imperative to ensure that the conveyor belt meets all specifications, including size, physical performance, and appearance. This step safeguards against defects and ensures that only belts meeting the highest standards are delivered to customers. After passing inspection, the belts are carefully packed for shipping, marking the end of the manufacturing process and the beginning of their operational life in various industries.
Leather Belt Manufacturing Process
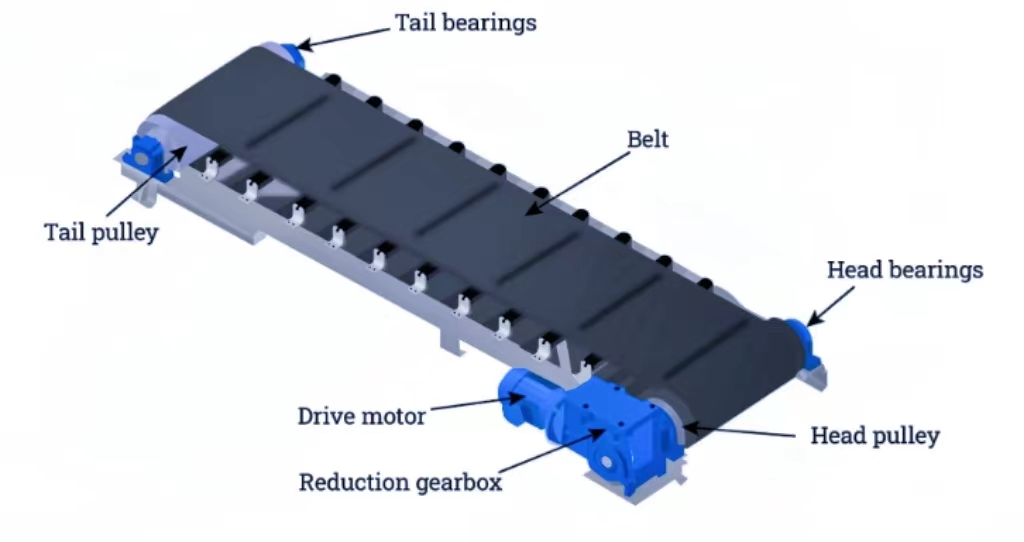
In understanding the question “how are conveyor belts made,” it’s insightful to also explore the leather belt manufacturing process, which shares similarities in terms of material preparation and precision. Below is a detailed look into how leather belts are crafted.
Material Preparation
The first step in the leather belt manufacturing process is selecting high-quality leather. The leather is typically sourced from cowhide, known for its durability and strength. The chosen hide undergoes tanning, a process that converts the raw animal skin into a stable material that will not decompose. There are two primary tanning methods: vegetable tanning and chrome tanning. Vegetable tanning uses natural tannins from tree bark and other plant sources, resulting in a leather that is rich in color and patinas over time. Chrome tanning, on the other hand, uses chromium salts, which produces a more pliable leather with a consistent color.
Once tanned, the leather is thoroughly inspected to ensure it is free from imperfections and has the right thickness. This step is crucial as the quality of the raw material directly impacts the durability and aesthetics of the finished belt.
Cutting and Shaping
After preparing the leather, the next step involves cutting it to the desired width and length. This is typically done using a strap cutter or a die cutter for precision. The standard width for a leather belt ranges from 1 to 2 inches, depending on the style and use. The length is measured based on the intended waist size of the user, with extra length added for adjustments.
Once cut, the edges of the leather strip are often beveled to create a smooth, rounded edge that is comfortable to wear and looks polished. This is done using an edge beveler tool. The leather strip is then skived, a process that thins the ends of the leather to reduce bulk when folded over for buckles and keepers.
Stitching and Assembly
The assembly process begins with attaching the buckle to one end of the leather strip. The end of the leather is folded over the buckle’s bar and stitched or riveted in place. High-quality belts often feature hand stitching using strong, waxed thread. This type of stitching not only adds durability but also provides a distinctive aesthetic detail.
Next, belt holes are punched at the other end of the strip using a hole punch tool. These holes are evenly spaced and aligned to ensure a snug fit. The belt may also include a keeper loop, which holds the loose end of the belt in place once fastened.
For belts with a lining, the inner layer is glued to the leather strip before stitching. This lining adds strength and durability, ensuring the belt maintains its shape over time.
Finishing
The finishing process involves several steps to enhance the appearance and durability of the belt. The edges are often burnished, a process that smooths and seals them using friction and heat. This can be done manually with a hand burnisher or with a machine.
The leather is then polished using leather conditioners or waxes, which nourish the material and bring out its natural luster. Some belts may also be dyed or stained to achieve the desired color. The finishing touches include embossing or stamping logos or designs onto the belt for branding or decorative purposes.
The leather belt manufacturing process is meticulous and involves multiple stages of preparation, cutting, stitching, and finishing. This detailed approach ensures that each belt is not only functional but also a high-quality accessory. By understanding this process, we gain deeper insight into how are conveyor belts made, as both processes emphasize precision, quality materials, and craftsmanship.
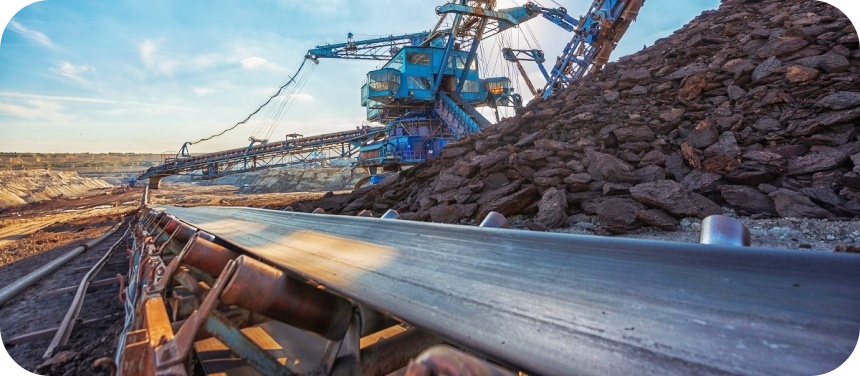
Special Considerations in Conveyor Belt Manufacturing and How Are Conveyor Belts Made
When exploring how are conveyor belts made, it’s crucial to consider the special requirements and challenges that arise in manufacturing conveyor belts for diverse applications. These considerations significantly influence the choice of materials, design, and manufacturing processes to meet specific industry standards and operational demands.
Specific Requirements for Food and Beverage Processing Conveyor Belts
- FDA or USDA Approval: Conveyor belts used in food and beverage processing must comply with FDA (Food and Drug Administration) or USDA (United States Department of Agriculture) regulations to ensure they are safe for direct contact with food products. This involves using materials that are non-toxic, non-absorbent, and resistant to the growth of bacteria and mold. The approval process is stringent, requiring thorough testing and documentation to verify that the materials used do not leach harmful substances into food.
- Ease of Cleaning: To prevent food contamination and comply with hygiene standards, conveyor belts in the food industry must be designed for easy and effective cleaning. This includes smooth surfaces that minimize the adherence of food particles, resistance to cleaning chemicals, and the ability to withstand high-pressure washdowns without degrading.
- Resistance to Oils and Fats: Many food products contain oils and fats that can degrade certain conveyor belt materials. Therefore, belts used in food processing must be made from materials that are resistant to these substances to maintain their integrity and prevent contamination.
- Temperature Resistance: Food processing often involves exposure to extreme temperatures, from baking and frying to freezing. Conveyor belts must be able to withstand these temperature extremes without cracking, melting, or becoming brittle. This requires the use of materials specifically formulated for thermal stability.
Challenges in Manufacturing Conveyor Belts for Diverse Applications
Manufacturing conveyor belts to meet the varied demands of different industries presents several challenges, particularly in terms of flexibility and accommodating small or irregularly shaped objects. The table below highlights these challenges and the considerations involved in addressing them:
Challenge | Industry/Application | Consideration |
---|---|---|
Flexibility | Packaging and sorting | Belts must be designed to navigate tight turns and elevation changes without compromising the stability or orientation of the products. |
Small Objects | Electronics, pharmaceuticals | Conveyor belts must have a smooth, flat surface to prevent small items from getting stuck or falling through gaps. |
Irregular Shapes | Recycling, agriculture | Belts need to accommodate a wide range of shapes and sizes without causing damage or jams. This may involve custom-designed surfaces or adjustable guides. |
Heavy Loads | Mining, construction | Enhanced strength and durability are required to withstand the weight and abrasiveness of heavy materials, often necessitating reinforced materials and construction techniques. |
Understanding how are conveyor belts made with these special considerations in mind is essential for manufacturers to deliver products that not only meet the technical specifications but also address the practical challenges of diverse industrial applications. This tailored approach ensures that conveyor belts can perform effectively and reliably, regardless of the environment in which they are used.
Rubber Conveyor Belt Manufacturers
In exploring “how are conveyor belts made,” it is essential to highlight the key players in the industry who are at the forefront of manufacturing high-quality rubber conveyor belts. These manufacturers are renowned for their innovative approaches, quality standards, and comprehensive product ranges.
Top Manufacturers
- ContiTech AG: ContiTech, a division of Continental AG, is a leading manufacturer of rubber and plastic products, including conveyor belts. They are known for their extensive research and development efforts, resulting in high-performance conveyor belts designed for a variety of industries. ContiTech offers belts that cater to specific needs, such as heat-resistant, flame-retardant, and abrasion-resistant belts, ensuring they meet the highest quality standards.
- Fenner Dunlop: Fenner Dunlop is another major player in the conveyor belt industry, particularly known for its strong presence in the mining sector. They offer a wide range of conveyor belts, including steel cord, fabric, and solid woven belts. Fenner Dunlop emphasizes durability and reliability, providing belts that are designed to withstand the harshest conditions.
- Bridgestone Corporation: Bridgestone, widely recognized for its tire products, also manufactures high-quality rubber conveyor belts. Their conveyor belts are designed for a variety of applications, including heavy-duty industrial use. Bridgestone focuses on producing belts that offer excellent resistance to wear and tear, ensuring long service life and reduced maintenance costs.
- Goodyear Engineered Products: Now known as Veyance Technologies, this company offers a comprehensive range of rubber conveyor belts. Their products are engineered to meet the specific demands of various industries, from construction and mining to agriculture and manufacturing. Veyance Technologies prides itself on innovation and quality, ensuring their conveyor belts provide optimal performance and reliability.
- Sempertrans: A division of the Semperit Group, Sempertrans specializes in the manufacturing of high-quality conveyor belts for industrial applications. They offer a broad range of products, including textile and steel cord belts, designed to handle a wide variety of materials and operating conditions. Sempertrans is known for its commitment to sustainability and innovation, continuously developing new technologies to enhance belt performance.
Manufacturing Excellence
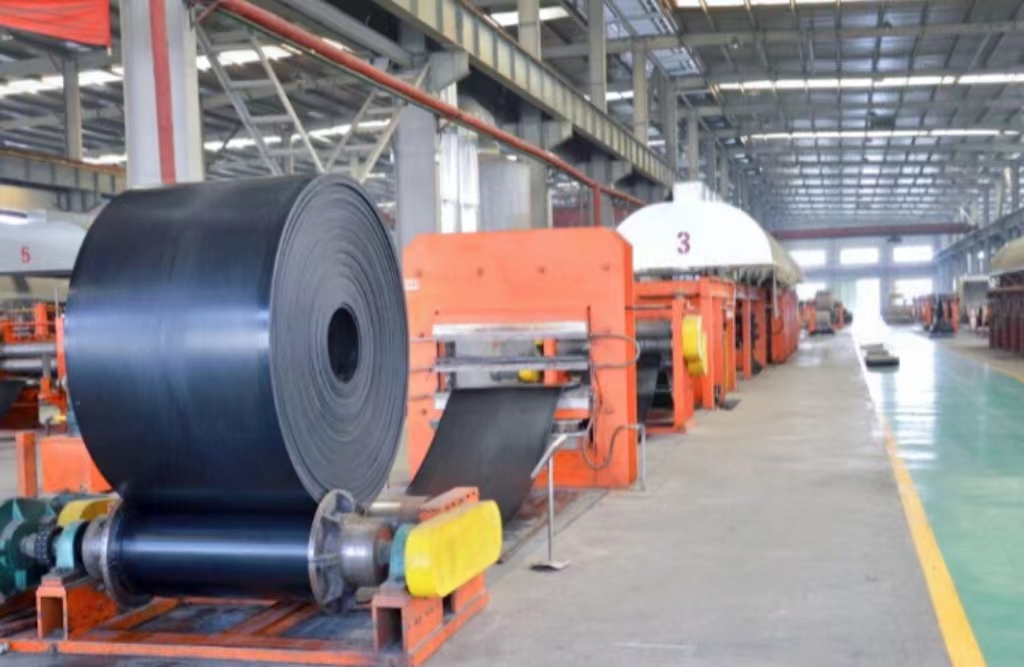
When discussing “how are conveyor belts made,” it’s important to note the manufacturing excellence demonstrated by these top manufacturers. Their commitment to quality and innovation ensures that the conveyor belts produced are reliable, durable, and suited to the specific needs of various industries.
- Research and Development: Leading manufacturers invest heavily in research and development to create advanced materials and manufacturing processes. This results in conveyor belts that can withstand extreme conditions, such as high temperatures, heavy loads, and abrasive materials. Innovations in rubber compounds and reinforcement technologies ensure that the belts provide superior performance and longevity.
- Quality Standards: Adherence to stringent quality standards is a hallmark of top conveyor belt manufacturers. They implement rigorous testing procedures to ensure that each belt meets or exceeds industry standards. This includes testing for tensile strength, elongation, abrasion resistance, and temperature resistance. By maintaining high-quality standards, these manufacturers ensure that their conveyor belts offer reliable performance and reduce the risk of operational downtime.
- Sustainability: Environmental responsibility is increasingly important in the manufacturing sector. Leading conveyor belt manufacturers are adopting sustainable practices, such as using eco-friendly materials and reducing waste during the production process. They are also developing energy-efficient manufacturing techniques that minimize the environmental impact of their operations.
- Customization: To meet the specific requirements of different industries, manufacturers offer customizable conveyor belt solutions. This includes tailoring the belt’s dimensions, material composition, and reinforcement structure to suit the particular application. Customization ensures that the conveyor belts provide optimal performance and durability in their intended environment.
Understanding “how are conveyor belts made” involves recognizing the expertise and innovation of leading manufacturers. Companies like ContiTech, Fenner Dunlop, Bridgestone, Goodyear Engineered Products, and Sempertrans exemplify manufacturing excellence through their commitment to quality, research and development, sustainability, and customization. These manufacturers ensure that their conveyor belts meet the diverse needs of industries worldwide, providing reliable and efficient material handling solutions.
Secure your conveyor belts with our expert help now.
FAQs About How Are Conveyor Belts Made
The manufacturing of a conveyor belt involves a multi-step process that ensures durability, flexibility, and suitability for various industrial applications. Initially, the process begins with the mixing of raw materials, where rubber is blended with specific compounds to achieve desired properties. This mixture is then processed in an internal mixer to ensure a homogeneous blend. Following mixing, the calendaring process takes place, where the rubber is pressed into long, thin sheets and coated onto fabrics to create layers. These layers are then laminated together, ensuring each layer is precisely aligned and bonded under controlled tension. The most critical step, vulcanization, follows, where the belt undergoes a heating process to cure the rubber, enhancing its strength, elasticity, and resistance to wear and tear. Finally, the conveyor belt is inspected for quality in terms of size, physical performance, and appearance before being packed and shipped. This meticulous process ensures that the conveyor belts meet the rigorous demands of various industrial environments.
Conveyor belts are made from a variety of materials, each selected for its specific properties and suitability for different applications. The main materials include thermoplastics, metals, rubber, fabrics, and leather. Thermoplastics used can be polyester, polyvinyl chloride, silicone, and polyethylene. Metals typically involve stainless steel and carbon steel, while fabrics might include canvas or cotton. Rubber composites are particularly popular due to their flexibility, resistance, and seamless construction. These materials might be combined with additives like fabric, steel, polyester, or fiberglass to enhance the belt’s strength. The choice of material affects the conveyor belt’s durability, resistance to temperatures, moisture, chemicals, and its overall performance in various industrial settings.
Rubber conveyor belts are made through a five-step process: mixing, calendering the belt carcass, laminating fabric or steel cables, and vulcanizing to create the final product. Calendering in the conveyor belt manufacturing process is a crucial step that involves pressing the rubber compound into thin, long sheets and then coating these sheets onto fabrics. This process is essential for creating the multiple layers of the conveyor belt, including the inner carcass and the outer covers. The fabric, which forms the belt’s backbone, is first dried to prevent blistering and delamination during subsequent vulcanization. The rubber compound must thoroughly penetrate the fabric’s structure to ensure a strong mechanical bond. Temperature control is critical during this phase to maintain the quality of the coating. Additionally, the calendering process may include skimming, where a thin film of rubber is glued onto the fabric, and cover rubber sheeting, where the compound rubber is formed into a film with specific dimensions and surface quality. This meticulous process ensures the conveyor belt’s durability and performance.
The construction of a belt conveyor system involves several key components that work together to move materials efficiently from one point to another. The main elements include the conveyor belt, pulleys (drive and idler), rollers, frame, and the drive unit. The conveyor belt, made from layers of materials like rubber, fabric, and steel, is the carrying medium. Pulleys are used to support and drive the belt; the drive pulley provides the motion, while the idler pulleys guide and support the belt. Rollers are spaced along the conveyor frame to support the belt and material being conveyed. The frame provides the structural support for the entire system and is typically made from steel or aluminum. The drive unit powers the conveyor, and its design depends on the conveyor’s length, load, and speed requirements. Together, these components form a conveyor system that can transport a wide range of materials across various distances and configurations, making it an indispensable part of many industrial operations.
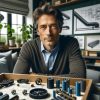
Jordan Smith, a seasoned professional with over 20 years of experience in the conveyor system industry. Jordan’s expertise lies in providing comprehensive solutions for conveyor rollers, belts, and accessories, catering to a wide range of industrial needs. From initial design and configuration to installation and meticulous troubleshooting, Jordan is adept at handling all aspects of conveyor system management. Whether you’re looking to upgrade your production line with efficient conveyor belts, require custom conveyor rollers for specific operations, or need expert advice on selecting the right conveyor accessories for your facility, Jordan is your reliable consultant. For any inquiries or assistance with conveyor system optimization, Jordan is available to share his wealth of knowledge and experience. Feel free to reach out at any time for professional guidance on all matters related to conveyor rollers, belts, and accessories.