Uses And Types of Conveyor Belt Material
Conveyor belts are integral to numerous industries, serving as essential components in the seamless operation of production and handling systems. The choice of material for these belts directly impacts their efficiency, cost-effectiveness, and suitability for specific environments, making the understanding of types of conveyor belt material crucial. Historically, the evolution of conveyor belt materials has transitioned from basic leather and canvas to advanced synthetics like polyurethane and rubber, each catering to distinct operational demands. This progression not only reflects technological advancements but also a deeper comprehension of material properties required to meet diverse industrial needs.
Types of Conveyor Belt Materials
Exploring the different types of conveyor belt material is essential for optimizing operations across various industries. Each material offers unique benefits and challenges, making the selection process critical for efficiency and longevity.
Rubber Conveyor Belts
- Rubber is widely acknowledged for its versatility and is a staple in conveyor belt construction. This material is renowned for its elasticity, which allows it to absorb impacts and conform to the contours of the conveying system.
- There are several subtypes of rubber conveyor belts, including synthetic options such as SBR, neoprene, and nitrile, each chosen based on their specific properties. For example, neoprene is particularly resistant to oils and chemicals, making it suitable for chemical processing environments.
- The properties of rubber conveyor belts include excellent wear resistance and the ability to handle a wide range of temperatures, making them ideal for everything from mining operations to the automotive industry, where they can endure harsh conditions and manage heavy loads.
PVC Conveyor Belts
- PVC, or polyvinyl chloride, is a type of plastic commonly used in light to medium duty conveying applications. Its key characteristics include high strength, lightweight, and good resistance to abrasion and chemicals.
- PVC conveyor belts are prevalent in industries where sanitation and cleanliness are paramount, such as food processing and pharmaceuticals. The non-toxic nature of PVC, combined with its ease of cleaning, helps maintain hygiene standards.
- Advantages of PVC belts also include low maintenance, resistance to moisture, and reduced risk of bacterial growth, enhancing their suitability for food-related applications.
Polyurethane (PU) Conveyor Belts
- Polyurethane conveyor belts are highly valued for their premium properties, including their exceptional resistance to grease, oils, and chemicals. Unlike other materials, PU is suitable for direct contact with food, adhering to FDA/USDA regulations.
- PU is predominantly used in the food industry, where cleanliness and minimal maintenance are crucial. Its non-porous surface prevents contamination and simplifies cleaning procedures.
- The high abrasion resistance and robust nature of PU ensure long-term durability and reliability in food processing operations, supporting a clean and efficient production flow.
Fabric Conveyor Belts
- Fabric belts are composed of layers of materials such as cotton, nylon, and polyester. These materials provide different levels of strength, flexibility, and resistance to environmental factors, making fabric belts adaptable to various applications.
- Fabric conveyor belts are often employed in industries where flexibility is required, such as in bakery or packaging operations. They are also used in applications demanding high-speed and precise alignments.
- Their adaptability across different environments is aided by the diverse properties of the fabrics used, such as moisture resistance in polyester and the breathability of cotton, which is beneficial in temperature-controlled settings.
Steel Cable Conveyor Belts
- Steel cable conveyor belts are designed for maximum strength and durability, utilizing high-tensile steel cables as the core material. This makes them ideal for heavy-duty applications such as mining and quarrying.
- These belts are capable of transporting heavy loads over long distances and under harsh conditions, making them an invaluable component in bulk material handling industries.
- Characteristics include high resistance to tearing and shock loads, ensuring operational reliability in environments where conventional belts might fail.
Understanding these types of conveyor belt material is crucial for selecting the right belt for specific industry requirements, ultimately affecting productivity and operational costs.
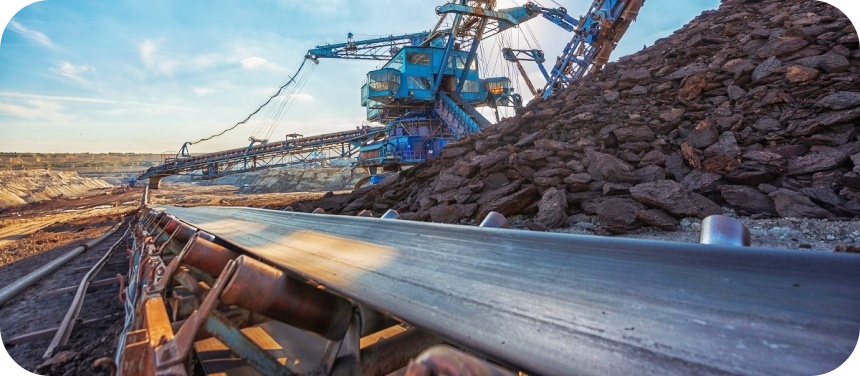
Advantages of Different Types of Conveyor Belt Materials
Advantages of Different Types of Conveyor Belt Materials
Each type of conveyor belt material has distinct advantages that make it suitable for specific applications. Here’s an overview of the advantages of various conveyor belt materials:
Rubber Conveyor Belts
Advantages:
- Durability: Highly resistant to wear and tear, making them suitable for heavy-duty applications.
- Flexibility: Can withstand high impact and abrasive materials.
- Versatility: Suitable for a wide range of industries, including mining, construction, and manufacturing.
- Heat Resistance: Some rubber belts are designed to withstand high temperatures, making them ideal for certain industrial processes.
PVC Conveyor Belts
Advantages:
- Chemical Resistance: Resistant to many chemicals and oils, making them ideal for food processing and packaging.
- Ease of Cleaning: Smooth surface allows for easy cleaning, essential for hygienic applications.
- Cost-Effective: Generally less expensive than other types of conveyor belts.
- Lightweight: Easier to install and maintain due to their lighter weight.
Polyurethane (PU) Conveyor Belts
Advantages:
- Food-Grade Quality: Safe for food handling due to their non-toxic and non-reactive properties.
- Oil and Fat Resistance: Excellent resistance to oils, fats, and other food-related substances.
- Flexibility: High flexibility and excellent mechanical properties.
- Longevity: High resistance to abrasion and cuts, leading to longer service life.
Fabric Conveyor Belts
Advantages:
- Lightweight: Easier to handle and install compared to heavier materials.
- Flexibility: Can easily navigate around bends and corners, making them suitable for complex conveyor systems.
- Cost-Effective: Generally more affordable than steel cable or rubber belts.
- Customizable: Can be manufactured in various strengths and thicknesses to suit different applications.
Steel Cable Conveyor Belts
Advantages:
- High Tensile Strength: Capable of carrying very heavy loads over long distances.
- Durability: Extremely durable and resistant to punctures, tears, and abrasion.
- Stability: Maintains its shape and structural integrity under heavy loads and harsh conditions.
- Temperature Resistance: Can withstand extreme temperatures, making them ideal for demanding industrial environments.
The choice of conveyor belt material depends on the specific needs of the application. Rubber belts offer durability and versatility for heavy-duty use, while PVC and PU belts are preferred in the food and pharmaceutical industries for their hygienic properties. Fabric belts are flexible and cost-effective for lighter applications, and steel cable belts provide unparalleled strength and durability for the most demanding tasks.

Uses of Different Types of Conveyor Belt Materials
Conveyor belts are essential components in a variety of industries for efficient material handling. Different materials used in conveyor belts offer distinct advantages, making them suitable for specific applications. Here’s a detailed overview of the uses of various types of conveyor belt materials:
Rubber Conveyor Belts
Material: Rubber (Natural or Synthetic)
Uses:
- Mining and Quarrying: Rubber conveyor belts are widely used in mining operations for transporting ore, coal, and other bulk materials.
- Construction: Suitable for moving heavy construction materials like sand, gravel, and cement.
- Agriculture: Used for handling grains, seeds, and other agricultural products.
- Manufacturing: Ideal for heavy-duty applications in manufacturing plants where durability and resistance to abrasion are crucial.
PVC Conveyor Belts
Material: Polyvinyl Chloride (PVC)
Uses:
- Food Processing: PVC belts are suitable for food-grade applications due to their smooth surface and ease of cleaning.
- Pharmaceuticals: Used in pharmaceutical manufacturing for transporting products in a hygienic manner.
- Logistics and Warehousing: Commonly used in warehouses for sorting and moving packaged goods.
- Packaging: Ideal for light to medium-weight packaging operations.
Polyurethane (PU) Conveyor Belts
Material: Polyurethane (PU)
Uses:
- Food Industry: PU belts are food-grade and resistant to oils and fats, making them ideal for processing meat, poultry, and baked goods.
- Textile Industry: Used in textile manufacturing for handling fabrics without damaging them.
- Pharmaceuticals: Preferred in environments requiring high hygiene standards due to their resistance to chemicals and ease of cleaning.
- Automotive: Utilized in automotive assembly lines for transporting parts and components.
Fabric Conveyor Belts
Material: Woven Fabric (Polyester, Nylon, Cotton)
Uses:
- General Manufacturing: Used in various manufacturing processes where flexibility and tensile strength are required.
- Paper and Printing Industry: Ideal for transporting paper and printed materials without causing damage.
- Baggage Handling: Commonly used in airports for baggage handling systems.
- Agriculture: Employed for handling lightweight agricultural products and materials.
Steel Cable Conveyor Belts
Material: Steel Cables Embedded in Rubber or Polymer
Uses:
- Mining: Essential for heavy-duty mining applications due to their high tensile strength and durability.
- Ports and Terminals: Used in bulk handling systems at ports for loading and unloading ships.
- Steel Industry: Suitable for transporting heavy and abrasive materials like steel coils and scrap metal.
- Power Plants: Used in coal-fired power plants for moving coal to the combustion chambers.
The selection of conveyor belt material depends on the specific requirements of the industry and the type of materials being transported. Each material offers unique properties that make it suitable for particular applications, ensuring efficient and reliable operation.
Key Factors in Types of Conveyor Belt Material Selection
When selecting conveyor belts, understanding the different types of conveyor belt material is crucial for ensuring optimal performance and efficiency in various industrial applications. The choice of material affects not only the durability and maintenance requirements of the conveyor system but also its cost and environmental impact.
What is the Types of Conveyor Belt Material
There are several types of conveyor belt material, each with unique properties that make them suitable for different applications. These materials include rubber, PVC, polyurethane, metal, and fabric. Each material offers varying degrees of strength, flexibility, resistance to chemicals, and suitability for different temperatures and environmental conditions.
Importance of Choosing the Right Material
- Operational Efficiency: The right conveyor belt material ensures that the system operates smoothly and efficiently without frequent breakdowns, which can lead to costly downtime.
- Durability: Materials like rubber and metal are prized for their durability and are able to withstand harsh conditions, including high impacts, abrasive materials, and extreme temperatures.
- Cost-Effectiveness: Choosing the correct material from the start can significantly reduce the overall cost of ownership by minimizing the need for replacements and repairs.
- Maintenance Needs: Some materials require more maintenance than others. For example, fabric belts might need regular cleaning and adjustments to maintain their grip and overall functionality.
- Environmental Suitability: Certain materials are better suited for specific environmental conditions. For instance, PVC belts are preferred in damp or wet environments due to their water resistance.
- Compliance with Safety Standards: Using the appropriate material can help ensure that the conveyor system complies with local and international safety standards, reducing the risk of accidents.
- Energy Consumption: Some materials, such as lightweight polyurethane, reduce the energy consumption of the conveyor system due to their reduced weight.
- Noise Reduction: Materials like fabric are often used in environments where reducing operational noise is crucial.
- Chemical Resistance: In industries where chemicals are used or produced, materials resistant to acids, bases, and solvents are necessary to prevent degradation of the belt.
- Thermal Resistance: For applications involving high temperatures, materials that can withstand prolonged exposure to heat without losing integrity are essential.
Criteria for Material Selection
- Durability: The selected material must be capable of handling the operational stresses of the application, including wear and tear from the conveyed materials.
- Cost: Initial investment vs. long-term savings should be balanced. More durable materials might be more expensive upfront but can offer savings over time due to lower replacement rates.
- Maintenance Needs: Consider how much maintenance each type of conveyor belt material requires. Lower maintenance materials can be more cost-effective in the long run.
- Environmental Factors: It is essential to consider the environmental impact of the material, including its production and disposal. Eco-friendly materials are increasingly preferred to meet corporate sustainability goals.
By carefully considering these factors and the types of conveyor belt material available, businesses can significantly enhance their operations’ effectiveness and efficiency, leading to better overall performance and reduced costs.
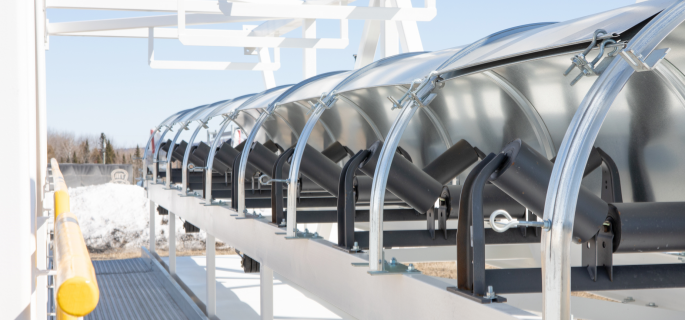
Types of Conveyor Belt Joints
Understanding the different types of conveyor belt joints is crucial when considering the types of conveyor belt material used in industrial settings. Conveyor belt joints play a significant role in the performance and longevity of a conveyor belt system, directly impacting its operational efficiency and maintenance needs.
Importance of Conveyor Belt Joints
Conveyor belt joints are critical because they affect the belt’s integrity, durability, and flexibility. A well-chosen and properly implemented joint can significantly extend the lifespan of the conveyor belt, enhance its performance, and reduce the risk of downtime due to joint failure. The right type of joint depends on the conveyor belt material, the environmental conditions, and the specific operational demands of the system.
Overview of Common Joint Types
- Mechanical Fastening: This joint type involves the use of metal fasteners or plastic rivets. Mechanical fasteners are quick to install and can be used on almost any type of conveyor belt material, making them highly versatile. However, they may be more vulnerable to catching and tearing when used with finer materials.
- Vulcanization: Vulcanization creates a seamless joint by chemically bonding the ends of the belt through heat and pressure. This method is highly durable and less likely to snag or catch compared to mechanical joints. Vulcanized joints are particularly effective for rubber belts where a smooth, strong splice is required.
- Welding: Welding is used for thermoplastic belts and involves melting the belt ends together. This technique offers a strong bond that maintains the integrity of the belt’s material, providing good durability and strength. It is ideal for food processing applications where cleanliness and minimal joint contamination are important.
Comparison of Joint Methods
- Strength: Vulcanized joints are generally considered the strongest, providing a bond that is nearly as strong as the original material. Welded joints also offer high strength, especially in thermoplastic materials. Mechanical fasteners, while strong, might not match the strength of welded or vulcanized joints and are more suitable for temporary or emergency repairs.
- Flexibility: Vulcanized and welded joints maintain the flexibility of the belt better than mechanical fasteners, which can introduce stiffness at the joint point. This makes vulcanization and welding better suited for applications requiring belts to navigate curves and bends.
- Application Suitability: Mechanical fasteners are quick to install and easy to repair, making them suitable for applications where downtime needs to be minimized. Vulcanization is preferred in applications requiring long-term durability and minimal joint failure, such as in heavy-duty mining or milling operations. Welding is ideal for applications requiring sanitary conditions or where the belt material must withstand high temperatures or chemical exposure.
Incorporating the types of conveyor belt material into the decision about which joint type to use is essential. Different materials react differently to each joint type, affecting the overall system’s performance. For example, thermoplastic materials are ideal for welding, whereas rubber belts are best suited for vulcanization to ensure the joint handles the material’s stress and wear conditions effectively. By considering these factors, organizations can ensure that their conveyor systems are both efficient and durable, with minimized risks and optimized performance.
Conveyor Belt Innovations and Trends: Exploring Types of Conveyor Belt Material
In the dynamic field of conveyor systems, ongoing innovations in the types of conveyor belt material and technology are reshaping how businesses approach material handling and processing. These advancements are not only enhancing operational efficiency but also contributing significantly to environmental sustainability.
Recent Advances in Conveyor Belt Materials and Technology
- High-Performance Materials: New synthetic materials are being developed to offer greater durability, heat resistance, and chemical resistance than traditional materials.
- Eco-friendly Materials: The introduction of sustainable materials that are recyclable and have a lower environmental impact is becoming more prevalent.
- Energy-efficient Belts: Innovations such as energy-optimized rubber compounds that reduce power consumption by minimizing rolling resistance are gaining traction.
- Self-healing Materials: Some of the latest types of conveyor belt material have self-healing properties, where minor cuts and abrasions can automatically repair themselves, thus extending the belt’s life.
- Smart Belts: Integration of sensors and IoT technology into conveyor belts is allowing for real-time monitoring of belt health, tracking of materials, and predictive maintenance.
- Improved Splicing Techniques: Advances in splicing technology ensure that joints are stronger and less prone to failure, which is crucial for maintaining the integrity of high-performance belts.
- Antimicrobial Belts: In industries where hygiene is paramount, such as food and pharmaceuticals, conveyor belts with antimicrobial properties are being developed to prevent the growth of bacteria and fungus.
- Modular Belt Designs: These designs offer improved flexibility and ease of maintenance. Modular belts can be quickly repaired or reconfigured, reducing downtime and operational costs.
Contact us for custom conveyor belt projects.
Impact on Efficiency and Environmental Sustainability
- Reduced Energy Consumption: The development of low-rolling-resistance compounds in conveyor belt materials significantly lowers energy costs and consumption, reflecting a direct improvement in operational efficiency.
- Longer Lifespan: Advanced materials and technologies extend the service life of conveyor belts, which reduces the frequency of replacement and the associated waste and costs.
- Enhanced Material Handling: Smart conveyor systems that adjust their speed and operation based on real-time data can handle materials more efficiently and reduce spillage and waste.
- Recycling and Reusability: New materials designed to be recycled contribute to circular economy principles, significantly reducing waste and supporting sustainability goals.
- Decreased Maintenance: Belts designed with advanced materials and smart technologies require less frequent maintenance, thereby reducing the use of hazardous cleaning chemicals and the manpower required for upkeep.
- Environmental Protection: The use of eco-friendly materials minimizes the environmental footprint of manufacturing and disposing of conveyor belts.
- Improved Worker Safety: Enhanced materials and smarter systems contribute to safer work environments by reducing the risk of accidents associated with belt malfunctions.
- Compliance with Regulations: New materials and technologies help companies comply with increasingly stringent environmental and safety regulations.
- Customization for Specific Needs: The development of specific materials for unique industrial applications allows for optimized conveyor solutions that are both efficient and environmentally friendly.
- Noise Reduction: Advances in belt materials and design contribute to quieter operation, which is beneficial for employee health and reduces noise pollution.
- Temperature and Chemical Resistance: Innovations in materials that can withstand extreme temperatures and harsh chemicals expand the range of applications for conveyor belts, making them suitable for challenging industrial environments.
- Global Impact: As these technologies and materials are adopted globally, the overall environmental and operational efficiency on a larger scale improves, setting new standards in the conveyor belt industry.
These innovations in the types of conveyor belt material and technology are pivotal in driving the conveyor belt industry towards a more efficient and sustainable future.
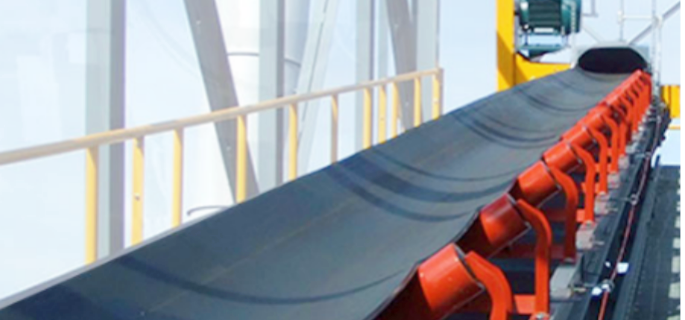
FAQs about Types of Conveyor Belt Material
Conveyor belts can be made from a variety of materials, each selected to match the specific needs of the movement process and the items to be transported. Typically, materials include:
Rubber: Rubber is commonly used for its flexibility, resistance to wear, and ability to handle items with irregular surfaces.
PVC (Polyvinyl Chloride): Chosen for its durability and resistance to chemicals; often used in food processing or pharmaceutical industries to maintain a sterile environment.
Polyurethane: Known for its hygienic properties, excellent for food conveyance due to its resistance to oils, fats, and chemicals.
Fabric: Often used as a reinforcement layer within belts, made from materials like nylon, polyester, or Kevlar.
Steel: Integrated usually as cables or mesh, adds tensile strength, commonly used in heavy-duty applications.
Specialty applications may call for advanced materials such as silicone for heat resistance, or thermoplastic polyurethane for added flexibility and smooth operation.
The diversity of conveyor belt types reflects the varied scenarios and materials for which conveyance is required. Main types of conveyor belts include:
Flat Belt Conveyors: Utilized widely due to simplicity and versatility.
Modular Belt Conveyors: Made up of individual plastic modules and excellent for sharp inclines or curves.
Cleated Belt Conveyors: Feature raised cleats for keeping materials secured during inclines or declines.
Curved Belt Conveyors: Designed to curve around corners and improve path flexibility.
Incline/Decline Belt Conveyors: Adjust for elevation changes, aiding in transporting goods between levels.
Sanitary and Washdown Conveyors: Built to withstand high-pressure washing in food processing plants.
The choice of conveyor belt type will depend on the operational requirements, including direction of travel, load weight, environmental conditions, and the need for speed and efficiency.
The “best” material for a conveyor system varies widely depending on the specific requirements of the operation. Here are a few considerations:
Durability: UHMWPE (Ultra High Molecular Weight Polyethylene) is renowned for wear and impact resistance.
Sanitation: FDA-approved materials such as certain grades of stainless steel are ideal for food processing applications.
Versatility: Rubber often offers the best mix of flexibility, grip, and durability for general purpose use.
Heat Resistance: High-temperature applications might require specialty materials like Teflon or silicone.
Ultimately, the best material for a conveyor system must align with the environmental conditions, the type of items being moved, the speed of operation, regulatory requirements, and the wear expected from the conveyed materials.
Metals used in conveyor belts are typically selected for their strength, durability, and suitability to the application’s environment. Commonly used metals include:
Steel: Offers high tensile strength and is often used in heavy-duty applications. It can be coated for added corrosion resistance.
Stainless Steel: Popular in the food industry for its resistance to corrosion and ease of cleaning. Its non-reactive properties make it food-safe.
Aluminum: Lightweight and corrosion-resistant, making it suitable for lighter-duty applications and those requiring lower belt mass.
In instances where the belt is not made purely of metal, steel or stainless steel cables might also be incorporated within rubber or plastic belts to add strength and support, especially when high pulling forces are involved, or when the belt spans long distances.
The material of a conveyor belt shaft is typically made from steel, due to its high strength, durability, and resistance to wear and deformation under heavy loads. Steel shafts can be crafted from various types, including carbon steel and stainless steel, each chosen based on the specific operational requirements. Carbon steel shafts are widely used for their cost-effectiveness and excellent mechanical properties, while stainless steel shafts are preferred in environments where corrosion resistance is critical, such as in food processing, pharmaceutical, and chemical industries. Additionally, some conveyor belt shafts may be coated or treated to enhance their performance characteristics, such as applying a hard chrome plating for increased wear resistance or using specialized coatings to reduce friction. Overall, the choice of material ensures the conveyor system operates efficiently and reliably under diverse conditions.
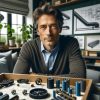
Jordan Smith, a seasoned professional with over 20 years of experience in the conveyor system industry. Jordan’s expertise lies in providing comprehensive solutions for conveyor rollers, belts, and accessories, catering to a wide range of industrial needs. From initial design and configuration to installation and meticulous troubleshooting, Jordan is adept at handling all aspects of conveyor system management. Whether you’re looking to upgrade your production line with efficient conveyor belts, require custom conveyor rollers for specific operations, or need expert advice on selecting the right conveyor accessories for your facility, Jordan is your reliable consultant. For any inquiries or assistance with conveyor system optimization, Jordan is available to share his wealth of knowledge and experience. Feel free to reach out at any time for professional guidance on all matters related to conveyor rollers, belts, and accessories.