Heat Resistant Rubber Conveyor Belts Ratings
Heat resistant rubber conveyor belts play a crucial role in various industries, ensuring efficient and safe transportation of high-temperature materials. These belts are essential for handling materials such as Sinter, Coke, Phosphate, and Clinker, which can easily exceed standard temperature limits. Without a heat resistant rubber conveyor belt, the integrity and lifespan of a conveyor system can be severely compromised. In this blog post, we will explore the specifications, materials, and categories of heat resistant rubber conveyor belts, along with their temperature ratings, cover grades, and a comparison between Grade 1 and Grade 2 belts to help you make an informed decision.
The Chemical Principles of Heat Resistant Rubber
Heat-resistant rubber is essential in many industrial applications where materials are exposed to high temperatures. The chemical principles underlying the production and performance of heat-resistant rubber involve various factors, including polymer structure, cross-linking, additives, and curing processes. Here’s a detailed look at these principles:
Polymer Structure
The base polymer significantly influences the heat resistance of rubber. Common heat-resistant rubbers include:
- Silicone Rubber (VMQ): Known for its excellent heat resistance, silicone rubber can withstand temperatures up to 250°C. Its backbone structure of alternating silicon and oxygen atoms contributes to its thermal stability.
- Fluoroelastomer (FKM): These rubbers have high resistance to heat and chemicals, with service temperatures up to 300°C. The presence of fluorine atoms in the polymer chain provides enhanced thermal stability and resistance to oxidative degradation.
- Ethylene Propylene Diene Monomer (EPDM): This rubber has good heat and weather resistance due to its saturated backbone structure.
Cross-Linking (Vulcanization)
Cross-linking is the process of forming chemical bonds between polymer chains, enhancing the material’s thermal and mechanical properties. Vulcanization, typically involving sulfur, is a common method:
- Sulfur Vulcanization: Adding sulfur and accelerators forms cross-links between polymer chains, improving heat resistance and elasticity.
- Peroxide Vulcanization: Peroxides can be used to form carbon-carbon cross-links, which are more thermally stable than sulfur-based cross-links.
Additives
Various additives are used to enhance the heat resistance of rubber:
- Antioxidants: Prevent oxidative degradation at high temperatures by scavenging free radicals.
- Heat Stabilizers: Improve thermal stability by inhibiting degradation processes.
- Fillers: Carbon black and silica can enhance the thermal conductivity and mechanical properties, aiding in heat dissipation and structural integrity.
Curing Process
The curing process, including temperature and duration, affects the final properties of the rubber:
- High-Temperature Curing: Higher curing temperatures can improve the heat resistance of rubber by promoting the formation of more stable cross-links.
- Optimized Curing Time: Ensuring that the rubber is cured for the appropriate time prevents under-curing or over-curing, which can compromise thermal stability.
Thermal Degradation Mechanisms
Understanding the mechanisms of thermal degradation helps in designing heat-resistant rubber:
- Oxidative Degradation: At high temperatures, oxygen can attack the polymer chains, leading to breakage and loss of properties. Heat-resistant rubbers are formulated to resist this process.
- Thermal Scission: Direct thermal energy can break polymer bonds. Heat-resistant rubbers are designed to withstand higher energy levels without significant degradation.
The development of heat-resistant rubber involves selecting the appropriate polymer, optimizing the cross-linking process, incorporating suitable additives, and carefully controlling the curing process. These principles ensure that the rubber maintains its integrity and performance in high-temperature applications.
Heat Resistant Rubber Conveyor Belt Specifications
Explanation of Standard Conveyor Belt Specifications
Conveyor belts are essential components in numerous industrial processes, ensuring the smooth and efficient transport of materials. Standard conveyor belt specifications typically include parameters such as tensile strength, elongation, load support, cover thickness, and overall belt thickness. These specifications determine the belt’s durability, flexibility, and suitability for various applications. In general, standard conveyor belts are designed to operate at temperatures up to 80°C. Beyond this limit, the belt material can degrade, leading to reduced performance and lifespan.
Differences in Specifications for Heat Resistant Rubber Conveyor Belts
Heat resistant rubber conveyor belts are engineered to withstand higher temperatures, often required in industries such as steel, cement, and glass manufacturing.Heat resistant rubber conveyor belts endure hot cement, steel, sand, and more, handling continuous temperatures up to 160°C. These belts have enhanced specifications to resist thermal conveyor belt damage and maintain performance under extreme conditions. Below is a comparison table highlighting the key differences in specifications between standard and heat resistant rubber conveyor belts.
Specification | Standard Conveyor Belt | Heat Resistant Rubber Conveyor Belt |
---|---|---|
Temperature Resistance | Up to 80°C | Up to 200°C (T2), peaking at 400°C (T3) |
Tensile Strength | Typically 250-500 N/mm | Typically 200-400 N/mm |
Elongation | 10-15% at break | 10-20% at break |
Cover Thickness | 3-5 mm top, 1.5-2 mm bottom | 4-6 mm top, 2-3 mm bottom |
Overall Belt Thickness | 6-10 mm | 8-15 mm |
Material Composition | Natural Rubber, SBR | EPDM, Chlorobutadiene, Special Compounds |
Load Support | Moderate to High | High |
Adhesive Strength | Standard | High |
Cut and Abrasion Resistance | Moderate | High |
Importance of Selecting the Right Specifications
- Thermal Stability: In industries where materials reach extremely high temperatures, such as steel manufacturing or cement production, selecting a heat resistant rubber conveyor belt ensures that the belt can handle the heat without deforming or degrading. This stability is crucial for maintaining continuous operation and preventing costly downtime.
- Durability and Longevity: Heat resistant belts are designed with enhanced durability, meaning they can withstand harsh conditions for extended periods. This longevity reduces the need for frequent replacements, thereby lowering maintenance costs and increasing overall productivity.
- Safety: High-temperature operations pose significant safety risks. Using a heat resistant rubber conveyor belt minimizes the risk of belt failure, which can lead to accidents, material spills, or even fires. Ensuring the belt can handle the operational temperatures is vital for maintaining a safe working environment.
- Efficiency: The right belt specifications ensure efficient material transport, even at high temperatures. Heat resistant rubber conveyor belts maintain their structural integrity and performance, enabling consistent and efficient processing without interruptions caused by belt failures or slowdowns.
- Material Compatibility: Different materials react differently to heat. A heat resistant rubber conveyor belt is specifically designed to handle hot materials such as sinter, coke, and clinker without damage. This compatibility ensures that the belt and transported materials remain in optimal condition.
- Cost-Effectiveness: While heat resistant rubber conveyor belts may have a higher initial cost compared to standard belts, their extended lifespan and reduced maintenance needs make them a cost-effective choice in the long run. Investing in the right specifications can lead to significant savings over time.
- Customization Options: Heat resistant belts can be customized to meet specific industrial needs. This includes variations in thickness, tensile strength, and cover composition to match the unique requirements of different applications. Customization ensures that the belt performs optimally under specific operational conditions.
- Compliance with Industry Standards: Using heat resistant rubber conveyor belts that meet recognized industry standards (such as DIN 22102) ensures that the belts are tested and proven to perform under specified conditions. This compliance guarantees that the belts will function as expected, providing reliability and peace of mind.
Selecting the right heat resistant rubber conveyor belt specifications is critical for ensuring efficient, safe, and cost-effective operations in high-temperature industrial environments. By understanding the differences in specifications and the importance of choosing the appropriate belt for specific applications, businesses can optimize their conveyor systems and enhance overall productivity.
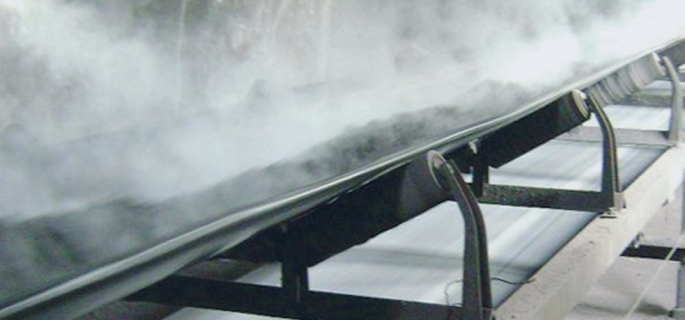
Best Heat Resistant Rubber Conveyor Belt
When selecting the best heat resistant rubber conveyor belt for industrial applications, it is essential to consider several key factors that determine its performance and durability. The following section provides detailed criteria for evaluating heat resistant rubber conveyor belts, an overview of seven leading manufacturers, and an analysis of the performance and longevity of the top-rated belts in this category.
Criteria for Determining the Best Heat Resistant Rubber Conveyor Belts
Temperature Resistance:
One of the most critical factors is the belt’s ability to withstand high temperatures without degrading. This includes not only the peak temperature resistance but also the duration for which the belt can sustain such temperatures.
Material Composition:
The quality and type of rubber used in the construction of the belt are vital. High-grade synthetic rubbers, such as EPDM (ethylene propylene diene monomer) and SBR (styrene-butadiene rubber), are commonly used for their excellent heat resistance properties.
Tensile Strength:
A high tensile strength ensures that the belt can handle heavy loads without stretching or breaking, which is crucial in high-temperature environments where materials may become heavier.
Abrasion Resistance:
The belt must also be resistant to wear and tear, as high temperatures can accelerate the abrasion process. This includes the belt’s ability to resist cuts, tears, and other forms of mechanical damage.
Flexibility:
Heat resistant rubber conveyor belts should maintain flexibility under high temperatures to ensure smooth operation without cracking or becoming brittle.
Adhesion Properties:
Good adhesion between the rubber layers and the carcass (fabric or steel cord) is essential to prevent delamination, which can occur under extreme heat conditions.
Regulatory Compliance:
Conveyor belts must meet industry standards and certifications, such as ISO, DIN, and ASTM, to ensure safety and reliability in industrial applications.
Leading Manufacturers and Their Top Products
ContiTech
ContiTech offers a range of heat resistant rubber conveyor belts, including the CONTIFLEX Vulkan range, designed for high-temperature environments. These belts are known for their durability and ability to operate in temperatures up to 200°C.
Fenner Dunlop
Fenner Dunlop’s UsFlex and HeatGuard series are renowned for their high performance in extreme conditions. The HeatGuard series, in particular, can handle temperatures up to 400°F (204°C) and is designed for heavy-duty applications.
Bridgestone
Bridgestone provides heat resistant conveyor belts that can withstand temperatures up to 180°C. Their belts are engineered for superior heat and abrasion resistance, ensuring a long service life.
Yokohama
Yokohama’s heat resistant conveyor belts are crafted from special compounds that offer excellent resistance to heat and abrasion. Their high-temperature belts are suitable for a variety of applications, including cement plants and steel mills.
Goodyear
Goodyear, now part of Continental, produces the Pathfinder and PyroShield series, which are designed to perform in high-temperature conditions. These belts are known for their exceptional heat resistance and durability.
Smiley Monroe
Smiley Monroe offers a range of heat resistant belts that can handle temperatures up to 200°C. Their ToughFlex and Flexicon belts are popular choices for industries requiring high-temperature operation.
Dunlop Conveyor Belting
Dunlop’s Betahete and Deltahete belts are designed for extreme heat resistance, withstanding temperatures up to 350°C. These belts offer a combination of strength, durability, and heat resistance, making them suitable for harsh environments.
Performance and Durability of Top-Rated Heat Resistant Belts
Heat resistant rubber conveyor belts are engineered to perform under high-temperature conditions while maintaining their structural integrity and operational efficiency. The performance of these belts is determined by their ability to resist heat-induced degradation, maintain flexibility, and resist abrasion and mechanical damage.
Temperature Endurance:
The top-rated heat resistant rubber conveyor belts can endure continuous exposure to temperatures ranging from 150°C to 350°C, depending on the specific belt design and material composition. This endurance is crucial for industries such as metal processing, cement manufacturing, and power generation, where extreme temperatures are commonplace.
Longevity:
High-quality heat resistant rubber conveyor belts are designed to offer extended service life, even in the most demanding environments. The use of advanced rubber compounds and reinforcing materials ensures that these belts can withstand the rigors of high-temperature operation without significant wear and tear.
Cost-Efficiency:
While the initial investment in high-performance heat resistant rubber conveyor belts may be higher, their durability and reduced maintenance requirements lead to lower overall operational costs. This cost-efficiency makes them a preferred choice for industries that require reliable and long-lasting conveyor solutions.
Selecting the best heat resistant rubber conveyor belt involves careful consideration of various performance criteria and an understanding of the leading manufacturers and their products. By choosing belts that offer superior temperature resistance, tensile strength, abrasion resistance, and flexibility, industries can ensure optimal performance and longevity in high-temperature applications.
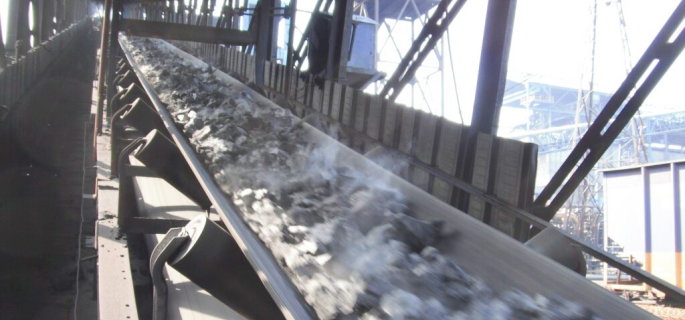
How to Choose Heat Resistant Rubber Conveyor Belt
Choosing the right heat-resistant rubber conveyor belt involves several key considerations to ensure optimal performance and longevity. Here are the steps to guide you in selecting the appropriate belt:
Determine the Temperature Range
- Identify the Maximum Temperature: Assess the highest temperature your belt will be exposed to, including any spikes in temperature.
- Consider Continuous Temperature: Ensure the belt can handle continuous exposure to high temperatures without degradation.
Assess the Material Being Transported
- Type of Material: Consider the type of material (e.g., cement, steel, sand) and its specific properties.
- Abrasiveness: Determine if the material is abrasive and if additional wear resistance is necessary.
Choose the Right Cover Material
- Heat-Resistant Compounds: Select belts made with specialized heat-resistant rubber compounds such as EPDM, silicone, or fluoroelastomers.
- Quality of Cover: Ensure the cover material can withstand the identified temperature range and material abrasiveness.
Evaluate the Belt Structure
- Textile Layers: Consider the number and type of textile layers (plies) for strength and durability.
- Thickness and Weight: Ensure the belt’s thickness and weight are suitable for your conveyor system.
Check Chemical Resistance
- Chemical Exposure: If the materials transported involve chemicals, select a belt with suitable chemical resistance properties.
Review Manufacturer Specifications
- Manufacturer Recommendations: Follow the manufacturer’s guidelines and recommendations for heat resistance and material compatibility.
- Certifications and Standards: Check for industry certifications and standards compliance.
Consult with Experts
- Professional Advice: Seek advice from conveyor belt experts or manufacturers to ensure the best fit for your specific application.
- Custom Solutions: Consider custom-made solutions if your requirements are unique or demanding.
Selecting the right heat-resistant rubber conveyor belt involves understanding the temperature range, material properties, and specific requirements of your application. By considering these factors, you can choose a belt that ensures reliable performance and longevity in high-temperature environments.
Heat Resistant Rubber Conveyor Belt Material
Detailed Description of the Materials Used in Heat Resistant Conveyor Belts
The effectiveness and durability of a heat resistant rubber conveyor belt largely depend on the materials used in its construction. These belts are specially engineered with advanced rubber compounds designed to withstand high temperatures and harsh operational conditions. The primary materials used in the manufacturing of heat resistant rubber conveyor belts include Ethylene Propylene Diene Monomer (EPDM) and chlorobutadiene (Neoprene), among other specialized rubber compounds.
EPDM is widely known for its excellent heat resistance and flexibility, making it a popular choice for heat resistant conveyor belts. Chlorobutadiene, also known as Neoprene, offers a unique combination of heat resistance, chemical stability, and mechanical strength, making it ideal for heavy-duty applications. Additionally, other rubber compounds, such as nitrile rubber and silicone, may be used in specific applications requiring enhanced resistance to chemicals and extreme temperatures.
Comparison Between EPDM, Chlorobutadiene Gum, and Other Rubber Compounds
To better understand the advantages and applications of different rubber compounds used in heat resistant conveyor belts, let’s compare EPDM, chlorobutadiene, and other rubber materials.
Material | Heat Resistance | Chemical Resistance | Mechanical Properties | Applications |
---|---|---|---|---|
EPDM | Up to 200°C | Excellent | High flexibility, good tensile strength | Steel, cement, and glass industries |
Chlorobutadiene (Neoprene) | Up to 150°C | Very Good | High tensile strength, good elongation | Heavy-duty applications, mining, and construction |
Nitrile Rubber | Up to 120°C | Excellent | Moderate tensile strength, good abrasion resistance | Oil and gas, automotive industries |
Silicone Rubber | Up to 250°C | Good | High thermal stability, excellent flexibility | Food processing, pharmaceuticals, and electronics |
Benefits of Using These Specific Materials for Heat Resistance and Durability
- High Heat Resistance: The primary benefit of using materials like EPDM and chlorobutadiene in heat resistant rubber conveyor belts is their ability to withstand high temperatures. EPDM can handle continuous temperatures up to 200°C, making it ideal for industries that process extremely hot materials. Chlorobutadiene, with its heat resistance up to 150°C, is suitable for moderately high-temperature applications.
- Chemical Stability: EPDM and chlorobutadiene offer excellent chemical resistance, which is crucial in environments where belts may be exposed to various chemicals and solvents. This stability ensures that the belts maintain their integrity and performance even in harsh chemical conditions.
- Mechanical Strength: Both EPDM and chlorobutadiene provide high mechanical strength, including good tensile strength and elongation properties. This strength allows the belts to withstand heavy loads and mechanical stress without deforming, making them suitable for demanding industrial applications.
- Durability and Longevity: The superior durability of EPDM and chlorobutadiene ensures a longer lifespan for heat resistant rubber conveyor belts. These materials resist wear and tear, reducing the frequency of belt replacements and maintenance, leading to cost savings and increased operational efficiency.
- Flexibility: EPDM, in particular, is known for its flexibility, which is beneficial in applications requiring belts to navigate complex conveyor systems with numerous turns and bends. This flexibility prevents cracking and tearing, enhancing the belt’s longevity.
- Abrasion Resistance: The abrasion-resistant properties of chlorobutadiene make it ideal for applications involving abrasive materials such as rocks, sand, and minerals. This resistance ensures that the belt surface remains intact, preventing material loss and ensuring efficient transport.
- Thermal Stability: Silicone rubber, used in specific applications, offers exceptional thermal stability, handling temperatures up to 250°C. This makes it suitable for industries like food processing and electronics, where high thermal stability is critical.
- Versatility: The variety of rubber compounds available allows for customization based on specific industrial requirements. Whether the need is for higher heat resistance, enhanced chemical resistance, or greater mechanical strength, there is a suitable material for every application.
- Compliance with Standards: Heat resistant rubber conveyor belts made from these advanced materials often comply with industry standards such as DIN 22102, ensuring they meet stringent performance and safety criteria. This compliance guarantees reliability and effectiveness in high-temperature environments.
The materials used in the construction of heat resistant rubber conveyor belts, such as EPDM and chlorobutadiene, provide exceptional heat resistance, chemical stability, mechanical strength, and durability. These properties make them indispensable in industries that require the efficient and safe transport of hot materials. By understanding the benefits and applications of these materials, businesses can select the most suitable heat resistant rubber conveyor belt for their specific needs, ensuring optimal performance and longevity.
Heat Resistant Rubber Conveyor Belt Categories
Breakdown of Heat Resistance Categories (T1, T2, T3) and Their Temperature Ratings
Heat resistant rubber conveyor belts are categorized based on their ability to withstand various temperature ranges. This categorization helps industries select the appropriate belt that meets their operational temperature requirements, ensuring both efficiency and longevity. The three primary categories of heat resistance for these belts are T1, T2, and T3.
- T1 – Medium Heat Resistance: Suitable for temperatures up to 150°C, with peak temperatures reaching 180°C.
- T2 – Heat Resistance: Suitable for temperatures up to 180°C, with peak temperatures reaching 200°C.
- T3 – Ultra High Heat Resistance: Suitable for temperatures up to 200°C, with peak temperatures reaching 400°C for continuous operation.
Detailed Explanation of Each Category
T1 – Medium Heat Resistance: Up to 150°C, Peaking at 180°C
T1 heat resistant rubber conveyor belts are designed for environments where the temperature of the transported material does not exceed 150°C. These belts can handle short-term peaks of up to 180°C, making them suitable for a variety of medium-temperature applications.
Characteristics:
- Made from rubber compounds that provide moderate heat resistance.
- Typically used in industries where the material temperature fluctuates but generally remains below 150°C.
- Good balance between cost and performance for medium-temperature applications.
Applications:
- Cement industry: Transporting clinker and other semi-finished products.
- Foundries: Handling molds and sand.
- Metal processing: Conveying materials such as sintered ore and pellets.
T2 – Heat Resistance: Up to 180°C, Peaking at 200°C
T2 heat resistant rubber conveyor belts are engineered for higher temperature environments, capable of withstanding continuous temperatures up to 180°C and short-term peaks up to 200°C. These belts are more robust and durable compared to T1 belts, making them suitable for harsher conditions.
Characteristics:
- Constructed with rubber compounds that offer higher heat resistance and durability.
- Designed for industries where materials regularly reach temperatures around 180°C.
- Enhanced mechanical strength to withstand the rigors of high-temperature transport.
Applications:
- Steel industry: Transporting hot steel products.
- Glass manufacturing: Conveying hot glass products.
- Ceramic industry: Moving tiles and other ceramic products through high-temperature processes.
T3 – Ultra High Heat Resistance: Up to 200°C, Peaking at 400°C
T3 heat resistant rubber conveyor belts are designed for the most extreme temperature conditions. These belts can handle continuous temperatures up to 200°C and can withstand peak temperatures up to 400°C, making them the most resilient and durable option for high-temperature applications.
Characteristics:
- Utilizes advanced rubber compounds with superior heat resistance.
- Suitable for the most demanding industrial processes where material temperatures frequently exceed 200°C.
- High durability and resistance to thermal degradation, ensuring a long lifespan even under extreme conditions.
Applications:
- Heavy metal industry: Handling materials like molten metals and hot slags.
- Energy sector: Transporting ash and other by-products from power plants.
- Chemical industry: Conveying chemicals and materials through high-temperature processing stages.
Application Examples for Each Category
Understanding the specific applications of each heat resistance category helps in selecting the right heat resistant rubber conveyor belt for various industrial needs.
T1 – Medium Heat Resistance Applications:
- Cement Industry: Clinker transport is a critical process where T1 belts are used due to their ability to handle the moderate heat generated during cement production.
- Foundries: In foundries, molds and sand are often transported at temperatures that fit within the T1 range, ensuring smooth operation without belt degradation.
- Metal Processing: In metal processing plants, sintered ore and pellets are moved efficiently using T1 belts that can manage the medium heat levels.
T2 – Heat Resistance Applications:
- Steel Industry: Steel production involves extremely high temperatures. T2 belts are ideal for transporting hot steel products through various stages of production.
- Glass Manufacturing: The glass manufacturing process requires belts that can endure the heat from molten glass, making T2 belts a perfect choice.
- Ceramic Industry: The production and processing of ceramic tiles involve high heat, and T2 belts provide the necessary resistance to ensure durability and efficiency.
T3 – Ultra High Heat Resistance Applications:
- Heavy Metal Industry: T3 belts are indispensable in the heavy metal industry, where they transport molten metals and hot slags, enduring extreme heat without compromising performance.
- Energy Sector: Power plants produce ash and other by-products at very high temperatures. T3 belts are used to handle these materials safely and efficiently.
- Chemical Industry: The chemical industry often involves high-temperature processes. T3 belts are essential for transporting chemicals and materials through these stages without degradation.
The selection of the appropriate heat resistant rubber conveyor belt category (T1, T2, or T3) depends on the specific temperature requirements of the industrial application. By understanding the characteristics and applications of each category, industries can ensure optimal performance, longevity, and safety in their material handling processes.
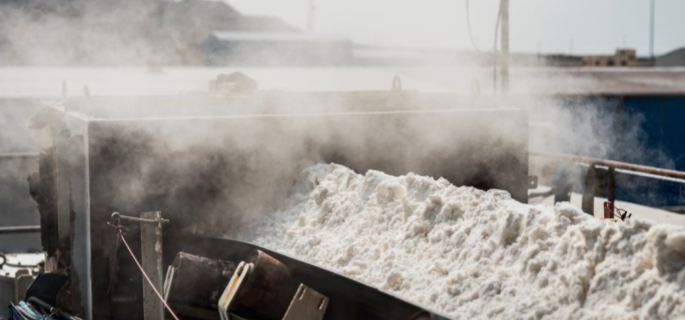
Conveyor Belt Temperature Rating
Explanation of the Importance of Temperature Ratings in Conveyor Belts
Temperature ratings are a critical factor in the selection and performance of conveyor belts, especially in industries where materials are transported at high temperatures. The heat resistant rubber conveyor belt is designed to withstand various temperature ranges, ensuring that it maintains its structural integrity and functionality under thermal stress.
Heat can have a significant impact on the physical properties of the conveyor belt, including its tensile strength, elongation, and overall durability. When a conveyor belt is exposed to temperatures beyond its rated capacity, it can lead to premature aging, cracking, hardening, or even melting. Therefore, understanding and choosing the correct temperature rating for a heat resistant rubber conveyor belt is essential to prevent operational failures and costly downtime.
Discussion on How Temperature Ratings Affect Belt Performance and Lifespan
The performance and lifespan of a heat resistant rubber conveyor belt are directly influenced by its temperature rating. Here’s how temperature ratings impact these aspects:
Performance:
- Maintaining Structural Integrity: A properly rated heat resistant rubber conveyor belt will maintain its structural integrity even under continuous exposure to high temperatures. This means the belt will not deform, crack, or suffer from surface hardening, ensuring smooth operation.
- Consistent Material Transport: The belt’s ability to consistently transport materials without sticking or degrading at high temperatures ensures uninterrupted workflow and productivity.
- Reduced Downtime: By using a belt with an appropriate temperature rating, the risk of unexpected breakdowns is minimized, thereby reducing operational downtime and associated costs.
Lifespan:
- Prolonged Durability: Belts with correct temperature ratings are designed to withstand thermal stress, which extends their operational lifespan. This reduces the need for frequent replacements and lowers maintenance costs.
- Resistance to Thermal Degradation: High temperatures can cause standard belts to degrade quickly. A heat resistant rubber conveyor belt with a suitable rating will resist thermal degradation, ensuring it remains effective over a longer period.
- Retained Mechanical Properties: The belt retains its mechanical properties, such as tensile strength and elasticity, which are crucial for its performance under heavy loads and high-speed conditions.
Industry Standards for Temperature Ratings (e.g., DIN 22102)
Industry standards, such as DIN 22102, provide guidelines for the temperature ratings of conveyor belts. These standards ensure that the belts meet specific requirements for performance and safety in high-temperature environments.
DIN 22102: This standard specifies the requirements for textile conveyor belts used in various industrial applications, including their ability to handle high temperatures. It categorizes heat resistant rubber conveyor belts based on their maximum continuous operating temperature and peak temperature resistance. The standard helps in the classification of belts into categories such as T1, T2, and T3, which we discussed earlier.
Temperature Rating Categories
T1 – Medium Heat Resistance:
- Continuous Operating Temperature: Up to 150°C.
- Peak Temperature: Up to 180°C.
- Application: Suitable for medium heat environments, such as cement plants and foundries.
T2 – High Heat Resistance:
- Continuous Operating Temperature: Up to 180°C.
- Peak Temperature: Up to 200°C.
- Application: Ideal for industries with higher heat requirements, such as steel and glass manufacturing.
T3 – Ultra High Heat Resistance:
- Continuous Operating Temperature: Up to 200°C.
- Peak Temperature: Up to 400°C.
- Application: Designed for the most extreme heat conditions, such as heavy metal industries and energy sectors.
Choosing the Right Temperature Rating
When selecting a heat resistant rubber conveyor belt, it is essential to consider the specific temperature requirements of the application. Here are some factors to consider:
- Material Temperature: Assess the average and peak temperatures of the materials being transported.
- Operational Environment: Consider the ambient temperature and other environmental factors that might influence the belt’s temperature exposure.
- Duration of Exposure: Determine how long the belt will be exposed to high temperatures during operation.
Benefits of Proper Temperature Rating
- Enhanced Safety: Using a belt with the correct temperature rating reduces the risk of thermal damage, which can lead to safety hazards.
- Improved Efficiency: Belts that perform well under the specified temperature conditions ensure efficient material handling.
- Cost Savings: Investing in a properly rated heat resistant rubber conveyor belt minimizes maintenance and replacement costs, leading to overall cost savings.
Understanding and selecting the appropriate temperature rating for a heat resistant rubber conveyor belt is crucial for ensuring optimal performance, longevity, and safety in high-temperature industrial applications. By adhering to industry standards like DIN 22102 and considering the specific needs of the application, industries can achieve efficient and reliable material transport even under extreme thermal conditions.
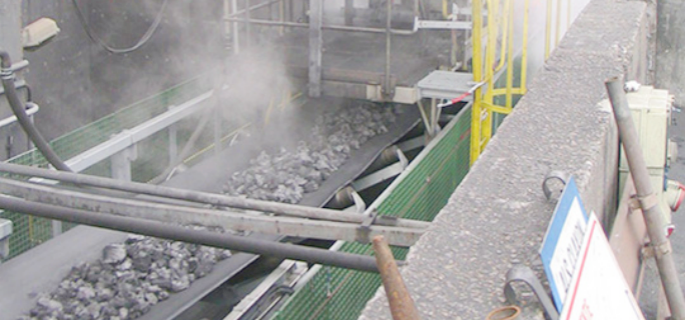
Heat Resistant Rubber Conveyor Belt Grades
Conveyor belt cover grades play a crucial role in determining the belt’s performance and durability in various applications. These cover grades are designed to withstand specific environmental conditions and types of materials being transported. Understanding the differences between cover grades is essential for selecting the right conveyor belt for your application.
Different Conveyor Belt Cover Grades and Their Significance
- Grade M: This is a general-purpose cover grade suitable for conveying most materials, excluding highly abrasive or sharp-edged materials. It offers moderate abrasion resistance and is commonly used in industries such as agriculture, recycling, and wood processing.
- Grade N: Grade N covers are designed for conveying non-abrasive materials with no sharp edges. They offer good resistance to abrasion and are suitable for industries such as packaging, food processing, and general manufacturing.
- Grade S: Grade S covers are designed for conveying abrasive materials with small particle sizes. They offer excellent abrasion resistance and are commonly used in industries such as mining, sand and gravel, and aggregate processing.
- Grade R: Grade R covers are specifically designed for conveying highly abrasive materials. They offer superior abrasion resistance and are ideal for industries such as mining, cement manufacturing, and steel production.
- Grade AR: Grade AR covers are designed for conveying materials with high abrasion and impact resistance. They offer the highest level of abrasion resistance and are suitable for industries such as quarrying, construction, and heavy-duty bulk material handling.
Comparison Between Grade 1 and Grade 2 Conveyor Belts
Grade 1 Conveyor Belts:
- Higher Cut and Gouge Resistance: Grade 1 conveyor belts are designed to resist cutting and gouging, making them ideal for applications where sharp objects may come into contact with the belt.
- Suitable Applications: Grade 1 belts are commonly used in industries such as mining, steel production, and heavy-duty bulk material handling.
Grade 2 Conveyor Belts:
- Better Abrasion Resistance: Grade 2 conveyor belts offer superior abrasion resistance, making them suitable for applications where the belt is exposed to abrasive materials.
- Suitable Applications: Grade 2 belts are commonly used in industries such as aggregate processing, sand and gravel, and recycling.
Recommendations for Selecting the Appropriate Cover Grade Based on the Application
When selecting a conveyor belt cover grade, it is important to consider the following factors:
- Material Characteristics: Consider the type and size of the materials being conveyed, as well as their abrasiveness and impact resistance.
- Operating Conditions: Evaluate the temperature, humidity, and other environmental factors that may affect the belt’s performance.
- Belt Speed and Tension: Determine the belt speed and tension requirements for the application to ensure the selected cover grade can withstand the operational demands.
By considering these factors and selecting the appropriate conveyor belt cover grade, you can ensure optimal performance, longevity, and reliability in your material handling operations.
Grade 1 vs Grade 2 Heat Resistant Rubber Conveyor Belt
In-Depth Comparison of Grade 1 and Grade 2 Conveyor Belts
When it comes to selecting the right heat resistant rubber conveyor belt for your application, understanding the differences between Grade 1 and Grade 2 conveyor belts is crucial. Here, we provide a detailed comparison to help you make an informed decision.
Table: Comparison of Grade 1 and Grade 2 Conveyor Belts
Criteria | Grade 1 Conveyor Belt | Grade 2 Conveyor Belt |
---|---|---|
Cut and Gouge Resistance | Higher resistance to cutting and gouging | Lower resistance compared to Grade 1 |
Abrasion Resistance | Moderate abrasion resistance | Better abrasion resistance |
Impact Resistance | Moderate impact resistance | Better impact resistance |
Recommended Use Cases | Applications with sharp objects and abrasive materials | Applications with high abrasion and impact potential |
Industries | Mining, steel production, heavy-duty bulk material handling | Aggregate processing, sand and gravel, recycling |
Temperature Range | Up to 150°C, peaking at 180°C | Up to 150°C, peaking at 180°C |
Belt Speed | Suitable for moderate to high belt speeds | Suitable for moderate to high belt speeds |
Tension Requirements | Moderate tension requirements | Moderate tension requirements |
Cost | Generally lower cost compared to Grade 2 | Generally higher cost compared to Grade 1 |
Discussion on Specific Use Cases and Advantages of Each Grade
Grade 1 Conveyor Belt:
- Use Cases: Ideal for applications where the conveyor belt is exposed to sharp objects or materials that can cause cutting and gouging.
- Advantages: Offers higher resistance to cutting and gouging, ensuring longer belt lifespan and reduced maintenance costs. Suitable for industries such as mining, steel production, and heavy-duty bulk material handling.
Grade 2 Conveyor Belt:
- Use Cases: Suitable for applications where the conveyor belt is exposed to high levels of abrasion and impact.
- Advantages: Provides better abrasion and impact resistance, making it ideal for industries such as aggregate processing, sand and gravel, and recycling. Although generally more expensive than Grade 1 belts, Grade 2 belts offer superior performance in demanding environments.
Factors to Consider When Choosing Between Grade 1 and Grade 2 Belts for Heat Resistance
- Material Characteristics: Consider the type and size of materials being conveyed, as well as their abrasiveness and impact potential.
- Operating Conditions: Evaluate the temperature, humidity, and other environmental factors that may affect the belt’s performance.
- Belt Speed and Tension: Determine the belt speed and tension requirements for the application to ensure the selected belt can withstand the operational demands.
- Cost Considerations: Factor in the initial cost of the belt as well as potential maintenance and replacement costs over its lifespan.
- Industry Standards: Ensure that the selected belt meets industry standards and specifications for heat resistance and durability.
- Manufacturer Reputation: Choose a reputable manufacturer known for producing high-quality, durable conveyor belts.
- Application Specifics: Consider any unique requirements or challenges of your application that may influence the choice between Grade 1 and Grade 2 belts.
- Consultation with Experts: Seek advice from conveyor belt experts or manufacturers to ensure you select the most suitable belt for your specific application.
By carefully considering these factors and understanding the differences between Grade 1 and Grade 2 conveyor belts, you can make an informed decision that meets your heat resistance needs and ensures optimal performance and durability in your material handling operations.
FAQs about Heat Resistant Rubber Conveyor Belt
A heat-resistant conveyor belt is a specialized type of conveyor belt that is designed to withstand high temperatures. These belts are tailored to transport materials like sinter, coal, clinker, and cement, which can reach temperatures from 60°C to above 250°C during various stages of the production process. The core function of a heat-resistant conveyor belt is to maintain its structural integrity and durability under prolonged exposure to high temperatures. This ensures a continuous and efficient operation in industrial applications where standard conveyor belts might fail due to the heat, leading to downtime and increased maintenance costs.
For temperature resistance, conveyor belts are categorized into different grades based on their capacity to withstand specific temperature ranges. These grades include:
HR – T1 Grade: Suitable for temperatures up to 120°C.
HR – T2 / SHR Grade: Designed for applications where temperatures can reach up to 150°C, making it ideal for slightly higher thermal demands.
HR – T3 / UHR Grade: This grade caters to extreme conditions, offering resistance to temperatures up to 200°C.
Pyroshield Grades: For even higher temperature applications, Pyroshield 250 and Pyroshield 300 are used for temperatures up to 250°C and 300°C respectively. Choosing the correct grade is crucial for the safety, efficiency, and longevity of the conveyor system in high-temperature environments.
Conveyor belts are engineered to operate within specific temperature ranges to cater to industrial needs. Standard conveyor belts typically handle temperatures up to 60°C-80°C. However, heat-resistant variants are designed to manage a broader temperature range based on their grade:
Medium Heat Resistance (T1): Up to 120°C
High Heat Resistance (T2/SHR): Up to 150°C
Ultra High Heat Resistance (T3/UHR): Up to 200°C
Pyroshield: Specifically designed for temperatures up to 250°C and 300°C.
The precise temperature range of a conveyor belt depends on its material composition, structure, and the nature of the thermal environment in which it operates.
The rubber used in conveyor belts is chosen based on its compatibility with the operational environment and the nature of the materials being transported. Heat-resistant conveyor belts often utilize rubber materials such as:
EPDM (Ethylene Propylene Diene Monomer): Known for its outstanding heat, ozone, and weather resistance, making it ideal for high-temperature applications.
Chlorobutadiene Rubber: Offers excellent heat resistance and is used in grades designed for medium to ultra-high temperature ranges.
SBR (Styrene Butadiene Rubber): Commonly used in standard conveyor belts for its good abrasion resistance and ability to perform in milder temperatures.
The selection of rubber material contributes significantly to the conveyor belt’s heat resistance, durability, and overall performance in challenging industrial settings.
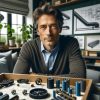
Jordan Smith, a seasoned professional with over 20 years of experience in the conveyor system industry. Jordan’s expertise lies in providing comprehensive solutions for conveyor rollers, belts, and accessories, catering to a wide range of industrial needs. From initial design and configuration to installation and meticulous troubleshooting, Jordan is adept at handling all aspects of conveyor system management. Whether you’re looking to upgrade your production line with efficient conveyor belts, require custom conveyor rollers for specific operations, or need expert advice on selecting the right conveyor accessories for your facility, Jordan is your reliable consultant. For any inquiries or assistance with conveyor system optimization, Jordan is available to share his wealth of knowledge and experience. Feel free to reach out at any time for professional guidance on all matters related to conveyor rollers, belts, and accessories.