Detailed Flame Resistant Conveyor Belt Specification Guide
Flame resistant conveyor belt is crucial in industrial settings where fire hazards are a significant concern. These belts are designed to resist ignition and prevent the spread of flames, ensuring the safety and continuity of operations. The price of flame resistant conveyor belts is influenced by several factors, including the materials used, the belt’s size and thickness, and the specific fire resistance ratings required for the application. Additionally, the brand and manufacturer, as well as any customization or special features, can also impact the cost. Investing in a high-quality flame resistant conveyor belt is essential for maintaining a safe and efficient industrial environment.
Flame Resistant Conveyor Belt Specification
Fire resistant conveyor belts are essential in industries where the risk of fire is a significant concern. These belts are designed to prevent the spread of flames and withstand high temperatures, ensuring the safety of personnel and the integrity of the material handling process. Here, we explain the key specifications of fire resistant conveyor belts and highlight the materials and construction techniques used to achieve fire resistance.
Key Specifications of Fire Resistant Conveyor Belts
- Temperature Resistance:
- Fire resistant conveyor belts must withstand high temperatures without losing their structural integrity. These belts are typically rated for continuous operation at temperatures ranging from 150°C to 200°C. Some specialized belts can handle intermittent temperatures of up to 400°C for short periods. The temperature resistance is achieved through the use of heat-resistant materials and compounds.
- Flame Retardant Properties:
- The primary function of a flame resistant conveyor belt is to prevent the spread of flames in the event of a fire. These belts are made from materials that self-extinguish when the source of ignition is removed. Flame retardant properties are tested according to international standards such as ISO 340, EN 12882, and ASTM D378. These standards ensure that the belt meets the required safety criteria.
- Tensile Strength:
- Tensile strength refers to the maximum stress that the belt material can withstand while being stretched before breaking. Fire resistant conveyor belts typically have high tensile strength to support heavy loads and resist tearing. The tensile strength is usually measured in megapascals (MPa) and varies based on the belt’s application requirements.
- Abrasion Resistance:
- Abrasion resistance is crucial for conveyor belts exposed to abrasive materials. Fire resistant belts are designed to withstand wear and tear caused by continuous friction with the conveyed materials. Abrasion resistance is often measured by the volume loss of the belt material after a specified period of testing.
- Chemical Resistance:
- Fire resistant conveyor belts must also resist chemicals that can degrade the belt material. These belts are formulated to withstand exposure to oils, acids, and other corrosive substances commonly found in industrial environments. Chemical resistance ensures the longevity and performance of the belt.
- Electrical Conductivity:
- In certain applications, fire resistant conveyor belts are required to have antistatic properties to prevent the buildup of static electricity. These belts are designed to dissipate electrical charges safely, reducing the risk of sparks that could ignite a fire.
- Elongation at Break:
- Elongation at break is a measure of the belt’s ability to stretch without breaking. Fire resistant conveyor belts typically have low elongation at break, ensuring they maintain their shape and do not deform under load. This property is essential for maintaining consistent belt tracking and performance.
Materials and Construction Techniques for Fire Resistance
- Rubber Compounds:
- Fire resistant conveyor belts are primarily made from specially formulated rubber compounds. These compounds include additives that enhance the belt’s heat and flame resistance. Common materials used include EPDM (Ethylene Propylene Diene Monomer) and SBR (Styrene-Butadiene Rubber), which offer excellent heat resistance and durability.
- Reinforcement Layers:
- To enhance the belt’s strength and stability, fire resistant conveyor belts are reinforced with multiple layers of synthetic fabrics such as polyester, nylon, or aramid fibers. These reinforcement layers provide the necessary tensile strength to handle heavy loads and resist tearing.
- Cover Grades:
- The cover grades of fire resistant conveyor belts are designed to protect the inner layers from damage and enhance the belt’s performance. These covers are made from fire retardant rubber compounds that provide a barrier against flames and heat. The covers also contribute to the belt’s abrasion and chemical resistance.
- Fire Retardant Additives:
- Fire resistant conveyor belts contain additives that improve their flame retardant properties. These additives include halogenated compounds, phosphorus-based compounds, and metal hydroxides. These substances help the belt material self-extinguish by interfering with the combustion process and forming a protective char layer.
- Manufacturing Processes:
- The manufacturing process of fire resistant conveyor belts involves precise control of temperature, pressure, and curing time to ensure uniform distribution of the fire retardant additives. Advanced curing techniques, such as vulcanization, enhance the belt’s durability and fire resistance.
- Surface Treatments:
- In some cases, fire resistant conveyor belts undergo surface treatments to improve their flame retardant properties. These treatments include applying fire retardant coatings or laminates that provide an additional layer of protection against flames and heat.
Fire resistant conveyor belts are designed with specific materials and construction techniques to ensure they can withstand high temperatures and prevent the spread of flames. By understanding the key specifications and the materials used in their construction, businesses can select the appropriate fire resistant conveyor belt to meet their safety and performance requirements.
Benefits of Using Flame Resistant Conveyor Belt PDF Resources
In today’s digital age, accessing information in PDF format has become a convenient and efficient way to gather and utilize data. When it comes to flame resistant conveyor belts, using PDF resources offers numerous advantages for industrial applications. This section discusses the benefits of accessing flame resistant conveyor belt information in PDF format and provides tips on how to utilize these resources effectively.
Benefits of Using Flame Resistant Conveyor Belt PDF Resources
- Comprehensive Information:
- Flame resistant conveyor belt PDF resources provide comprehensive information about the products, including specifications, features, installation guides, maintenance tips, and safety standards. These documents offer a detailed overview of the belt’s properties, helping businesses make informed decisions.
- Accessibility:
- PDF resources are easily accessible from various devices, including computers, tablets, and smartphones. This accessibility ensures that users can retrieve the information they need at any time and from any location, facilitating efficient planning and decision-making.
- Standardized Format:
- PDFs maintain a standardized format that ensures the information is presented consistently across different devices and platforms. This consistency is crucial for technical documents, as it prevents misinterpretation of data and specifications.
- Searchable Content:
- PDF documents are searchable, allowing users to quickly find specific information within the document. This feature is particularly useful for large technical manuals or product catalogs, where users can use keywords to locate relevant sections.
- Portability:
- PDFs are portable and can be easily shared via email, cloud storage, or USB drives. This portability enables businesses to distribute information to team members, suppliers, and clients efficiently, ensuring everyone has access to the necessary data.
- Cost-Effective:
- Using PDF resources reduces the need for printed materials, saving on printing and distribution costs. Additionally, digital documents are easier to update and distribute, ensuring that users always have access to the latest information.
- Interactive Features:
- Modern PDF documents can include interactive features such as hyperlinks, bookmarks, and multimedia elements. These features enhance the user experience by providing easy navigation and additional resources, such as instructional videos or external links.
Tips for Utilizing Flame Resistant Conveyor Belt PDF Resources
- Download and Organize:
- Download relevant PDF resources from trusted manufacturers and suppliers. Organize these documents in a dedicated folder on your device or cloud storage for easy access. Create subfolders for different categories, such as product specifications, installation guides, and maintenance manuals.
- Use Search Functionality:
- Take advantage of the search functionality in PDF readers to quickly find specific information. Use keywords related to your query to locate relevant sections within the document.
- Highlight and Annotate:
- Use highlighting and annotation tools available in PDF readers to mark important sections and add notes. This practice helps you quickly reference critical information and keep track of key points.
- Create Bookmarks:
- Create bookmarks for frequently accessed sections or important pages within the PDF document. Bookmarks provide quick navigation shortcuts, saving time when revisiting specific content.
- Share with Team Members:
- Share relevant PDF resources with team members to ensure everyone has access to the necessary information. Use collaboration tools and cloud storage to facilitate real-time sharing and updates.
- Print Key Sections:
- While PDFs offer the advantage of digital access, printing key sections for field use or reference during installation and maintenance can be beneficial. Ensure that printed copies are kept in a safe and accessible location.
- Regularly Update:
- Regularly check for updated versions of PDF resources from manufacturers and suppliers. Updated documents may include new specifications, safety standards, and best practices that are crucial for maintaining optimal performance and safety.
- Leverage Interactive Features:
- Utilize interactive features such as hyperlinks and embedded multimedia to access additional resources and instructional content. These features can provide valuable insights and enhance your understanding of the product.
- Store Backup Copies:
- Store backup copies of important PDF documents in multiple locations, such as local storage, cloud storage, and external drives. This practice ensures that you can access the information even in the event of data loss or technical issues.
Using flame resistant conveyor belt PDF resources offers numerous benefits, including comprehensive information, accessibility, standardized format, searchable content, portability, cost-effectiveness, and interactive features. By effectively utilizing these resources, businesses can enhance their decision-making processes, ensure proper installation and maintenance, and maintain the safety and performance of their conveyor systems.
Flame Resistant Conveyor Belt: Key Features of Fire Resistant Belt
Fire resistant belts are essential in industries where the risk of fire is a significant concern. These belts are designed with specific features that enhance their ability to prevent the spread of flames and withstand high temperatures. In this section, we outline the essential features that make a conveyor belt fire resistant and explain how these features contribute to safety and efficiency in high-risk environments.
Flame Retardant Materials
One of the primary features of a fire resistant belt
is the use of flame retardant materials. These materials are specially formulated to resist ignition and self-extinguish when the source of ignition is removed. Common flame retardant materials used in fire resistant belts include:
- EPDM (Ethylene Propylene Diene Monomer): Known for its excellent heat resistance and flame retardant properties.
- SBR (Styrene-Butadiene Rubber): Offers good flame resistance and durability.
- Neoprene: Provides excellent flame resistance and chemical stability.
The use of these materials ensures that the belt can operate safely in high-temperature environments and prevent the spread of fire.
High Temperature Resistance
Fire resistant belts are designed to withstand high temperatures without losing their structural integrity or performance. These belts can operate continuously at temperatures ranging from 150°C to 200°C, with some specialized belts capable of handling intermittent temperatures up to 400°C. High temperature resistance is achieved through the use of heat-resistant rubber compounds and reinforcement materials.
Self-Extinguishing Properties
A critical feature of fire resistant belts is their self-extinguishing properties. In the event of a fire, these belts are designed to stop burning once the source of ignition is removed. This self-extinguishing capability is crucial for preventing the spread of flames and minimizing damage to equipment and facilities. Fire resistant belts are tested and certified according to international safety standards, ensuring they meet the required safety criteria.
Reinforcement Layers
Fire resistant belts are reinforced with multiple layers of synthetic fabrics, such as polyester, nylon, or aramid fibers. These reinforcement layers provide the necessary tensile strength to handle heavy loads and resist tearing. The reinforced construction enhances the belt’s durability and ensures it can withstand the mechanical stresses associated with material handling in high-risk environments.
Chemical and Abrasion Resistance
In addition to their flame retardant properties, fire resistant belts are designed to resist chemicals and abrasion. These belts can withstand exposure to oils, acids, and other corrosive substances commonly found in industrial environments. Abrasion resistance is also essential for preventing wear and tear caused by continuous friction with the conveyed materials. The combination of chemical and abrasion resistance ensures the longevity and performance of the belt.
Low Elongation at Break
Fire resistant belts typically have low elongation at break, meaning they maintain their shape and do not deform under load. Low elongation is crucial for maintaining consistent belt tracking and performance, reducing the risk of belt slippage and operational disruptions. This feature ensures that the belt can operate efficiently in high-risk environments, where precise material handling is essential.
Electrical Conductivity
In certain applications, fire resistant belts are required to have antistatic properties to prevent the buildup of static electricity. These belts are designed to dissipate electrical charges safely, reducing the risk of sparks that could ignite a fire. Antistatic properties are particularly important in environments where flammable materials or gases are present.
Enhanced Safety Features
Fire resistant belts are designed with enhanced safety features to protect personnel and equipment. These features include:
- Fire Retardant Coatings: Some fire resistant belts are coated with fire retardant materials to provide an additional layer of protection against flames and heat.
- Protective Covers: Fire resistant belts often have protective covers made from flame retardant rubber compounds. These covers protect the inner layers of the belt and enhance its fire resistance.
- Reduced Smoke Emission: Fire resistant belts are formulated to produce minimal smoke when exposed to fire. Reduced smoke emission is crucial for maintaining visibility and safety in the event of a fire.
Compliance with Safety Standards
Fire resistant belts are manufactured to comply with international safety standards, such as ISO 340, EN 12882, and ASTM D378. These standards specify the testing and certification requirements for flame retardant properties, ensuring that the belts meet the required safety criteria. Compliance with these standards provides assurance that the belts are suitable for use in high-risk environments.
Long-Term Durability
The combination of flame retardant materials, reinforcement layers, and enhanced safety features ensures the long-term durability of fire resistant belts. These belts are designed to withstand harsh operating conditions and maintain their performance over extended periods. Long-term durability reduces the need for frequent replacements, minimizing downtime and maintenance costs.
Fire resistant belts are essential for ensuring safety and efficiency in high-risk environments. Key features such as flame retardant materials, high temperature resistance, self-extinguishing properties, reinforcement layers, chemical and abrasion resistance, low elongation at break, electrical conductivity, enhanced safety features, compliance with safety standards, and long-term durability make these belts a reliable choice for various industrial applications. By understanding these features, businesses can select the appropriate fire resistant belt to meet their safety and performance requirements, ensuring reliable and efficient material handling operations.
Flame Resistant Conveyor Belt: Trelleborg Conveyor Belt Solutions
Trelleborg is a renowned manufacturer known for its high-quality conveyor belts, catering to a wide range of industrial applications. With a legacy of innovation and a commitment to excellence, Trelleborg has established itself as a leader in the conveyor belt industry. Their products are designed to meet the rigorous demands of various industries, ensuring durability, efficiency, and safety.
Trelleborg’s Flame Resistant Conveyor Belts
One of Trelleborg’s standout offerings is its range of flame resistant conveyor belts. These belts are specifically engineered to perform reliably in environments where fire hazards are a concern. The flame resistant conveyor belts from Trelleborg are designed to meet stringent safety standards, providing peace of mind for industries such as mining, chemical processing, and manufacturing.
Specific Products and Solutions
Trelleborg offers a variety of flame resistant conveyor belts, each tailored to meet specific industrial needs. These include:
- Fire Shield Conveyor Belts: These belts are designed to withstand high temperatures and are ideal for use in environments with a high risk of fire. The Fire Shield belts incorporate advanced materials and technologies to provide superior flame resistance and durability.
- Heat Resistant Conveyor Belts: While not exclusively flame resistant, these belts are built to endure extreme heat conditions, making them suitable for applications where both heat and fire resistance are necessary.
- Customized Solutions: Trelleborg also provides customized flame resistant conveyor belts to meet the unique requirements of different industries. Their engineering team works closely with clients to develop bespoke solutions that ensure optimal performance and safety.
Trelleborg’s flame resistant conveyor belts are known for their reliability and long service life, making them a preferred choice for industries that prioritize safety and performance.
Flame Resistant Conveyor Belt: Conveyor Belt Cover Grades
What Are Conveyor Belt Cover Grades
Conveyor belt cover grades refer to the classification of the outer layer of the conveyor belt based on its material properties and performance characteristics. The cover grade is crucial as it determines the belt’s resistance to various factors such as abrasion, heat, and fire. Understanding the different cover grades is essential for selecting the right belt for specific applications, especially when it comes to flame resistant conveyor belts.
Importance of Conveyor Belt Cover Grades
The cover grade of a conveyor belt plays a vital role in its overall performance and longevity. The right cover grade ensures that the belt can withstand the operational environment’s demands, minimizing wear and tear and reducing the risk of premature failure. For flame resistant conveyor belts, the cover grade is particularly important as it directly impacts the belt’s ability to resist fire and heat.
Different Cover Grades for Flame Resistant Conveyor Belts
There are several conveyor belt cover grades, each designed to meet specific requirements. The following are some common grades used in flame resistant conveyor belts:
- Grade S: This grade is specifically formulated for excellent resistance to fire and is often used in underground mining and other high-risk environments. Grade S covers are designed to prevent the spread of flame and reduce the risk of ignition.
- Grade V: Known for its superior heat resistance, Grade V is suitable for applications where the belt is exposed to high temperatures. While not exclusively flame resistant, it provides a good balance between heat and fire resistance.
- Grade F: This grade combines high abrasion resistance with flame resistance, making it ideal for heavy-duty applications where both durability and safety are critical. Grade F covers are commonly used in industries such as steel and cement manufacturing.
- Grade C: Designed for chemical resistance, Grade C covers also offer flame resistance, making them suitable for environments where chemical exposure and fire hazards coexist.
Each of these grades has specific properties that make them suitable for different applications. Selecting the appropriate cover grade for a flame resistant conveyor belt is crucial for ensuring safety and optimal performance in high-risk environments.
Flame Resistant Conveyor Belt: Role of Trelleborg Sealing in Conveyor Belt Performance
Importance of Sealing in Conveyor Belt Performance
Sealing is a critical aspect of conveyor belt performance, directly impacting the belt’s longevity, efficiency, and reliability. Proper sealing helps prevent contaminants such as dust, dirt, and moisture from entering the belt system, reducing wear and tear on the components. Additionally, effective sealing can enhance the belt’s resistance to harsh environmental conditions, contributing to its overall durability.
Trelleborg’s Contributions to Conveyor Belt Sealing Technology
Trelleborg has made significant advancements in conveyor belt sealing technology, developing innovative solutions that improve the performance and lifespan of conveyor belts. Some of Trelleborg’s notable contributions include:
- Advanced Sealing Materials: Trelleborg uses high-performance materials for their sealing solutions, ensuring excellent resistance to wear, chemicals, and extreme temperatures. These materials are designed to provide a robust barrier against contaminants, enhancing the belt’s durability.
- Custom Sealing Solutions: Trelleborg offers customized sealing solutions tailored to specific applications and environmental conditions. Their engineering team works closely with clients to develop seals that meet the unique challenges of each operation, ensuring optimal performance and longevity.
- Innovative Seal Designs: Trelleborg’s seal designs incorporate advanced features such as self-lubricating properties and enhanced flexibility. These designs improve the seal’s effectiveness and reduce the need for frequent maintenance, contributing to the overall efficiency of the conveyor system.
- Integrated Sealing Systems: Trelleborg provides integrated sealing systems that combine multiple sealing technologies to offer comprehensive protection for conveyor belts. These systems are designed to address various challenges, from preventing dust ingress to withstanding high-pressure washdowns.
Trelleborg’s sealing solutions are essential for maintaining the performance and reliability of flame resistant conveyor belts. By preventing contaminants from compromising the belt system, these seals help ensure safe and efficient operations in high-risk environments.
Trelleborg’s commitment to innovation and quality is evident in their range of flame resistant conveyor belts and advanced sealing solutions. By understanding the different conveyor belt cover grades and the importance of sealing, industries can make informed decisions that enhance the safety, performance, and longevity of their conveyor systems. Whether you need a standard flame resistant conveyor belt or a customized solution, Trelleborg’s products are designed to meet the highest standards of safety and reliability.
FAQs about Flame Resistant Conveyor Belt
A heat resistant conveyor belt is specifically designed to transport materials at high temperatures. These belts are made from special materials that can withstand heat without degrading or losing structural integrity. Heat resistant conveyor belts are commonly used in industries such as metallurgy, cement, and steel where they transport hot materials like clinker, coke, and sinter. The belts are engineered to maintain their durability and performance even when exposed to temperatures ranging from 100°C to 200°C or higher, ensuring safe and efficient operation under extreme conditions.
Flame resistant and fire resistant are terms often used interchangeably but they have distinct meanings. Flame resistant refers to materials that can withstand ignition and prevent the spread of flames. These materials are designed to self-extinguish once the flame source is removed, thus reducing the risk of fire spreading. Fire resistant, on the other hand, refers to materials that can withstand exposure to fire for a certain period without losing their structural integrity. Fire resistant materials can endure higher temperatures and longer exposure times compared to flame resistant materials. In the context of conveyor belts, flame resistant belts are used to prevent fire initiation, while fire resistant belts are designed to maintain functionality during a fire.
The best method to extinguish a fire in a conveyor belt involves using a combination of fire suppression systems and manual intervention. Automatic fire suppression systems, such as water spray or foam-based systems, can quickly detect and extinguish fires at their early stages. In addition, CO2 or dry chemical extinguishers can be effective for localized fires. It is crucial to shut down the conveyor belt immediately to prevent the fire from spreading. Regular maintenance and inspections can also help in early detection and prevention of potential fire hazards. Ensuring that the conveyor belt is made of fire-resistant materials adds an extra layer of safety.
Conveyor belt fires can be caused by a variety of factors. Common causes include overheating due to friction, electrical malfunctions, and the presence of flammable materials on or near the belt. Misalignment of the belt can cause it to rub against fixed structures, generating heat and eventually igniting a fire. Accumulation of combustible materials like dust, grease, and debris can also contribute to fire hazards. Regular maintenance, proper alignment, and cleaning of the conveyor belt system are essential to prevent such incidents. Additionally, using flame resistant and fire resistant conveyor belts can significantly reduce the risk of fire.
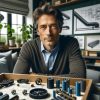
Jordan Smith, a seasoned professional with over 20 years of experience in the conveyor system industry. Jordan’s expertise lies in providing comprehensive solutions for conveyor rollers, belts, and accessories, catering to a wide range of industrial needs. From initial design and configuration to installation and meticulous troubleshooting, Jordan is adept at handling all aspects of conveyor system management. Whether you’re looking to upgrade your production line with efficient conveyor belts, require custom conveyor rollers for specific operations, or need expert advice on selecting the right conveyor accessories for your facility, Jordan is your reliable consultant. For any inquiries or assistance with conveyor system optimization, Jordan is available to share his wealth of knowledge and experience. Feel free to reach out at any time for professional guidance on all matters related to conveyor rollers, belts, and accessories.