Comparing Friction Roller Conveyors with Traditional Systems
Friction roller conveyors are integral components of modern material handling systems, used extensively across various industries to facilitate the smooth and efficient transport of goods. The primary function of a friction roller conveyor is to move items across a flat surface without the need for manual labor. These conveyors utilize rollers covered in a high-friction material that grips the bottom of items, propelling them forward when the rollers are turned via a motorized system. This method not only enhances the flow of operations but also minimizes the risk of damage to the items being transported, which is crucial in maintaining quality control.As industries strive for higher productivity and operational efficiency, the importance of reliable transport systems like friction roller conveyors has become increasingly prominent. They are particularly beneficial in settings such as manufacturing plants, distribution centers, and warehouses where quick and reliable transportation of heavy or bulky items is critical. The deployment of friction roller conveyors helps in achieving faster production times and reducing labor costs, making them a vital tool in the optimization of industrial operations.
What is a Friction Roller Conveyor?
A friction roller conveyor is a specialized type of conveyor system that uses rollers equipped with a high-friction surface to transport goods across a designated area. These conveyors are designed to handle items with flat, smooth bottoms, as the friction between the roller surface and the item facilitates movement without additional pushing forces. Unlike standard roller conveyors that rely on gravity or manual force, a friction drive roller conveyor utilizes the rotational motion of the friction-coated rollers to move items forward efficiently and reliably.
Comparison with Other Types of Conveyors
To highlight the unique features of friction roller conveyors, here is a detailed comparison with other common types of conveyors:
Feature | Friction Roller Conveyor | Gravity Roller Conveyor | Belt Conveyor |
---|---|---|---|
Driving Mechanism | Driven by motors applying rotational force to rollers | Utilizes gravity, needs inclined setup | Continuous belt driven by motors |
Surface Requirement | Requires flat-bottomed items for optimal performance | Works with various item shapes | Can handle a variety of item types |
Load Capacity | High load capacity due to motorized movement | Lower load capacity, dependent on slope | Medium to high load capacity |
Operational Efficiency | High efficiency and control over speed and item handling | Lower efficiency, speed varies by slope | High efficiency, smooth operation |
Cost | Generally higher cost due to motorization and technology | Lower cost, minimal mechanical parts | Higher cost due to complex setup |
Friction roller conveyors offer distinct advantages over other types. They are particularly beneficial for their controlled speed and handling capability, making them ideal for industries requiring precise movements and positioning of heavy items. Unlike belt conveyors, which can handle a range of item types but at a higher installation and maintenance cost, friction roller conveyors provide a cost-effective solution with excellent control and minimal maintenance needs for specific types of items. Similarly, while gravity conveyors are less expensive, they do not offer the same level of control or efficiency, particularly for heavier loads.
This table and the features discussed underscore the unique role that friction roller conveyors play in industrial settings, offering efficiency and reliability where other conveyor types may fall short. These conveyors are particularly adept at improving workflow and reducing labor costs, making them a preferred choice for many businesses looking to enhance their operational logistics.
Key Features of Friction Roller Conveyors
Friction roller conveyors are designed to efficiently handle and transport goods within various industrial environments, utilizing their unique construction and operational features. These conveyors are particularly valued for their ability to transport workpieces reliably through accumulating, staging, and processing points without manual intervention. Below, we explore the core characteristics that define friction roller conveyors and set them apart from other conveyor technologies.
Accumulating Transport of Workpieces
One of the standout features of friction roller conveyors is their ability to accumulate workpieces. This means that items can be gathered and held on the conveyor until they are needed downstream, without requiring continuous movement. The friction between the rollers and the item bottoms allows for controlled motion, where items can stop and start based on the workflow requirements without risk of damage or excessive force application. This feature is essential in assembly lines and packing areas where precise timing and handling are crucial.
Suitability for Flat, Smooth Bottom Surfaces
Friction roller conveyors are ideally suited for items with flat, smooth bottom surfaces. The high-friction material coating the rollers ensures that these items remain stable and move uniformly along the conveyor path. This suitability makes friction roller conveyors a preferred choice in industries such as electronics, pharmaceuticals, and food processing, where many products are packaged in uniform, flat-bottomed containers that require careful handling.
Capability to Handle Heavy Containers or Cases
Another significant advantage of friction roller conveyors is their capability to handle heavy containers or cases. Unlike belt conveyors, which can sag under excessive weight, or gravity conveyors, which rely on a slope and can thus handle limited weight, friction roller conveyors use motor-driven rollers that provide the necessary force to move heavy items along the conveyor at consistent speeds. This ability is particularly important in industries like automotive manufacturing and distribution centers where heavy and bulky items are common.
Versatility in Transporting Goods With or Without Pallets
Friction roller conveyors are highly versatile in their ability to transport goods whether they are palletized or not. The design of these conveyors allows for easy adjustment of roller spacing and friction coefficients to accommodate a wide range of item types and sizes. Whether moving boxed goods, loose components, or fully loaded pallets, friction roller conveyors can be customized to handle these various demands efficiently. This versatility ensures that businesses can use a single type of conveyor system across multiple stages of production and packaging, reducing the need for multiple conveyor types and simplifying the material handling process.
These key features—accumulating transport, suitability for flat-bottomed items, the ability to handle heavy loads, and versatility in goods transportation—make friction roller conveyors a critical component of modern industrial operations. They not only enhance the efficiency of transport systems but also contribute to the overall optimization of production and distribution workflows.
Components and Working Principle of a Friction Roller Conveyor
Friction roller conveyors are sophisticated systems that rely on several key components to transport items across facilities. Understanding these components and their working principles is essential for optimizing the efficiency and reliability of these conveyors. Here we delve into the main parts of a friction roller conveyor, providing specific examples, and explain how the friction drive mechanism operates within these systems.
Main Components of a Friction Roller Conveyor
A friction roller conveyor typically consists of the following major components:
- Friction Drive Rollers: These are the primary movers in a friction roller conveyor system. The rollers have a high-friction surface, often made from polyurethane or rubber, which grips the items being transported. This friction surface directly contacts the item’s base, moving it forward as the roller rotates.
- Conveyor Drive Rollers: Positioned at intervals along the conveyor, these rollers are connected via a motorized system that ensures synchronized rotation. Their rotation is powered by motors, which can be adjusted for speed and torque depending on the load and the required rate of movement.
- Load Rollers: These are supplementary rollers that support the weight of the transported items between the drive rollers. They ensure that the conveyor belt maintains a consistent surface level and helps distribute the load evenly, reducing wear and tear on the system.
- Motor and Gearbox Assembly: This component provides the necessary power to the drive rollers. The motor’s specifications are chosen based on the conveyor’s total load capacity and the required speed of movement. The gearbox adjusts the motor’s output to achieve the desired torque and roller speed.
- Conveyor Frame: The frame supports all the rollers, motor, and gearbox assembly. It is typically made from steel or aluminum, providing a sturdy and stable base for the entire system.
Working Principle of Friction Drive in Friction Roller Conveyors
The operation of a friction roller conveyor revolves around its ability to convert motor-driven rotational movement into linear motion to transport items. Here’s how the friction drive works:
- Motor Activation: The process begins with the activation of the conveyor’s motor, which transmits power to the drive rollers through the gearbox. The gearbox modulates the motor’s speed and torque, tailoring it to the needs of the production line.
- Rotation of Drive Rollers: As the motor powers the drive rollers, their high-friction surfaces begin to rotate. This rotation needs to be synchronized across all drive rollers to ensure smooth and consistent movement of the conveyor belt.
- Frictional Contact: The key to the system is the frictional contact between the drive rollers’ surfaces and the bottoms of the items being transported. The friction generated by this contact creates a drag force, which propels the items forward along the conveyor path.
- Transfer of Motion: The rotational motion of the rollers is converted into linear motion of the items. This motion can be finely controlled through adjustments in motor speed and torque, allowing for precise handling of the items, regardless of their weight.
- Continuous Operation: The conveyor continues to operate as long as the motor runs, with sensors and control systems in place to adjust the flow of items based on immediate production needs.
This friction-driven method is highly effective for moving heavy or bulky items, providing a significant advantage over gravity and manually pushed conveyor systems. It allows for greater control over item speed and alignment, which is critical in automated and semi-automated production environments. By understanding these components and their functions, industries can better utilize friction roller conveyors to enhance their operational efficiency and throughput.
Types of Friction Roller Conveyors
Friction roller conveyors are versatile and adaptable to various industrial needs, which has led to the development of different types based on their driving mechanisms and intended use. Understanding the differences between these can help facilities choose the most appropriate type for their specific requirements. This section discusses the primary types of friction roller conveyors, including chain-driven and sprocket-driven systems, and introduces the Interroll brand’s 3800 series as a notable example.
Primary Types of Friction Roller Conveyors
The table below summarizes the key differences between chain-driven roller conveyors, sprocket-driven rollers, and standard friction roller conveyors:
Type | Driving Mechanism | Common Uses | Features |
---|---|---|---|
Chain-Driven Rollers | Uses a chain to link rollers together, powered by motors | Heavy loads, such as pallets and drums | High durability, can operate at various speeds |
Sprocket-Driven Rollers | Rollers are equipped with sprockets that mesh with a chain | High-speed applications, assembly lines | Provides precise control, reduces slippage |
Standard Friction Roller Conveyors | High-friction rollers driven by motorized belts | Varied, including packaging and manufacturing lines | Flexible setup, moderate speed control |
Case Example: Interroll 3800 Series
A notable example of advanced friction roller conveyor technology is the Interroll 3800 series. This series exemplifies high-efficiency and adaptability in handling materials across various industries. Here are some specific attributes and benefits:
- Design and Build: The Interroll 3800 series features robust design with sprocket-driven rollers which enhance the conveyor’s reliability and reduce maintenance needs. The sprockets are integral to the rollers, ensuring a smooth mesh with the driving chain, which translates to less downtime and higher throughput.
- Versatility: This series is versatile enough to handle products of different sizes and weights, making it suitable for industries ranging from pharmaceuticals to automotive manufacturing. The adjustable roller speed also allows for the accommodation of sensitive materials that require gentle handling to avoid damage.
- Energy Efficiency: These conveyors are designed to minimize energy consumption. The efficient transfer of power from the motor to the rollers through the sprockets ensures that the system does not waste energy, which can lead to cost savings over time.
- Durability and Maintenance: Made with high-quality materials, the 3800 series is built to last. The sprocket-driven mechanism minimizes wear and tear on the chain and the rollers, which in turn reduces the frequency and cost of maintenance.
The Interroll 3800 series demonstrates the effectiveness of using advanced sprocket-driven friction roller conveyors in modern industrial setups. It stands out for its reliability, efficiency, and the ability to be customized to meet specific operational needs. Whether for high-speed processing, heavy-load carrying, or efficient transport of goods, the 3800 series provides a compelling solution that showcases the best of what friction roller conveyors can offer. This example underlines the importance of selecting the right type of conveyor to meet the specific demands of various industrial applications.
Price Considerations for Friction Roller Conveyors
When planning to purchase or upgrade a friction roller conveyor system, understanding the various factors that influence the price is crucial. The cost can vary widely depending on the specifications, quality, and capabilities of the system. Here, we discuss five key factors that affect the price of friction roller conveyors and provide practical tips for budgeting and cost-saving during the selection process.
Factors Affecting the Price of Friction Roller Conveyors
- Length and Width of the Conveyor: The size of the friction roller conveyor significantly impacts the price. Larger conveyors require more materials for construction and more sophisticated support structures, driving up costs.
- Load Capacity: Higher load capacities require more robust construction materials, enhanced motor capabilities, and sturdier roller designs, all of which increase the cost.
- Motor Type and Power: The type of motor (AC vs. DC) and its power rating can affect the price. High-power motors that offer speed variability and can handle heavy loads are typically more expensive.
- Material of Construction: The choice of materials (steel, aluminum, plastic) affects both the durability and the cost. High-grade materials that ensure longevity and reliability of the conveyor will cost more initially but might save money in long-term maintenance and replacement costs.
- Custom Features: Customizations such as adjustable speeds, integration with existing production lines, and special roller coatings for handling delicate items can significantly increase the price.
Tips for Budgeting and Cost-Saving When Selecting a Friction Roller Conveyor
- Evaluate Your Needs: Clearly define what you need in terms of load capacity, speed, and size. Opting for more capabilities than you actually need can unnecessarily increase costs.
- Choose Standardized Systems When Possible: Custom solutions are typically more expensive. If a standardized conveyor meets your needs, it can significantly reduce costs.
- Consider Total Cost of Ownership: Include maintenance, energy consumption, and potential downtime in your budgeting. A cheaper system that requires frequent repairs or consumes more energy might end up being more expensive over its lifespan.
- Look for Modular Designs: Conveyors that offer modular components can be more cost-effective to repair and upgrade, allowing for better customization and adaptability without replacing the entire system.
- Compare Quotes: Get detailed quotes from multiple suppliers. Ensure that these quotes are comprehensive, including not only purchase price but also installation costs, maintenance fees, and warranty terms.
By understanding these price factors and implementing these budgeting tips, you can make an informed decision that balances cost with efficiency, ensuring that your friction roller conveyor provides the best value for its price. This careful planning will help in selecting a system that not only meets your immediate needs but also adjusts to future requirements with minimal additional investment.
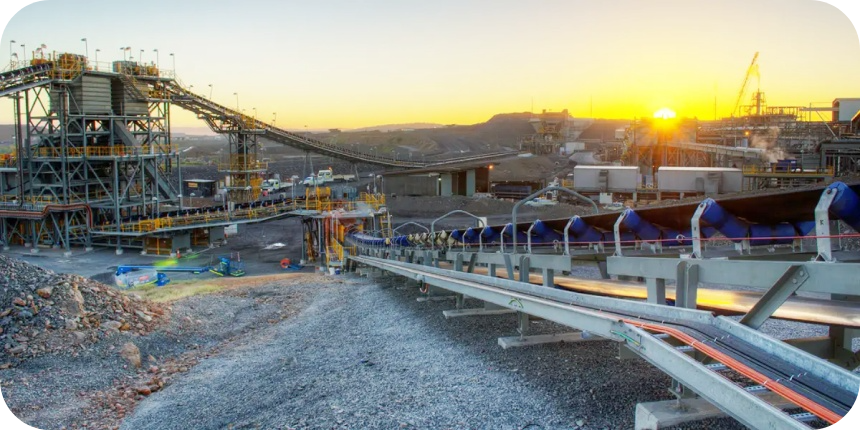
Purchasing Used Friction Roller Conveyors
Opting for a used friction roller conveyor can be a cost-effective solution for many businesses looking to enhance their material handling systems without the hefty price tag of a new unit. However, while the initial savings can be significant, there are several considerations to keep in mind to ensure that the purchase meets your operational needs without causing additional issues down the line.
Benefits of Purchasing Used Friction Roller Conveyors
- Lower Cost: The most apparent benefit is the reduced cost. Used friction roller conveyors can be significantly cheaper than new ones, sometimes saving up to 50% of the cost depending on the condition and age of the equipment.
- Quick Availability: Used equipment typically comes with shorter lead times. If a supplier has the right conveyor in stock, it can be delivered and installed much quicker than ordering a new build, which can be ideal for companies needing to ramp up operations quickly.
- Depreciation: Like cars, new conveyors depreciate as soon as they’re installed. Purchasing a used conveyor allows you to avoid the initial depreciation hit.
- Proven Performance: A used conveyor has a track record that can be inspected before purchase. New systems might come with teething problems that only become evident after they are operational.
- Environmental Impact: Buying used is a form of recycling, which can be a crucial part of maintaining an environmentally friendly policy by reducing the demand for raw materials and energy used in manufacturing new equipment.
Potential Drawbacks of Purchasing Used Systems
- Maintenance and Repair Costs: Used conveyors may require more maintenance or need repairs sooner than new ones. The initial savings should be weighed against the potential costs of upkeep.
- Limited Lifespan: Depending on its previous use, a used conveyor might not last as long as a new system would, potentially leading to earlier replacement needs.
- Obsolete Technology: The technology of the used conveyor might be outdated, making integration with modern systems difficult and limiting the upgrade options.
- Hidden Damage: There may be wear and tear that isn’t immediately apparent, potentially leading to failures under operation that can disrupt production.
- No Warranty: Typically, used conveyors do not come with a manufacturer’s warranty, which means any repairs or faults would immediately incur additional costs.
Advice on What to Look for When Considering a Pre-Owned Conveyor
When considering purchasing a used friction roller conveyor, keep the following points in mind to ensure that you make a sound investment:
- Assess Overall Condition: Check for signs of wear and tear, such as rust on metal parts, wear on the rollers, and the condition of the motor and gearbox. Inspect for any modifications or repairs already done, as these could affect performance and compatibility.
- Verify Age and Usage: Understand the history of the conveyor including its age, previous environments (e.g., harsh, corrosive environments), and usage levels. This information can be a good indicator of its future longevity.
- Check for Compatibility: Ensure the conveyor fits with your existing systems. Dimensions, motor type, control systems, and roller type must be compatible with your needs to avoid additional expenses for adaptation.
- Request a Test Run: If possible, see the conveyor in operation with your own products or simulate the conditions under which you will use it. This test can reveal potential issues that are not apparent during a static inspection.
- Consider Supplier Reputation: Purchase from a reputable dealer who is known for quality used equipment. They should be willing to provide maintenance records, the operational history of the conveyor, and a limited warranty if possible.
Purchasing a used friction roller conveyor can be a great way to save money and quickly augment your production capabilities, but it comes with risks that need to be carefully managed. By meticulously inspecting potential purchases and considering how well they meet your specific needs, you can make the most of the benefits while mitigating the drawbacks.
Sourcing Friction Roller Conveyor Parts
Maintaining a friction roller conveyor in optimal working condition is crucial for ensuring efficient operations and prolonging the system’s lifespan. Using high-quality parts for repairs and maintenance can lead to significant benefits in terms of performance and durability. This section provides guidance on how to source the right parts for your friction roller conveyor and discusses the importance of component quality in maintaining system longevity and performance.
Importance of Quality Parts in Friction Roller Conveyor Systems
- Reduced Downtime: High-quality parts are less likely to fail under normal operating conditions, which reduces downtime caused by breakdowns and repairs. This reliability is crucial in production environments where every minute of downtime translates to lost revenue.
- Extended Equipment Life: Using parts that meet or exceed the original specifications can extend the life of a friction roller conveyor. Well-made rollers, bearings, and motors wear down more slowly, which delays the need for potentially costly overhauls or replacements.
- Improved Performance: Quality parts ensure that the conveyor operates at its intended efficiency. Poor-quality components might not perform as well, leading to slowed down production lines or increased wear on other parts of the conveyor.
- Safety: High-quality conveyor parts also improve the overall safety of the equipment. Reliable components are less likely to malfunction in ways that could pose hazards to workers, such as sudden stops, spills, or jams that might cause injuries.
- Cost-Effectiveness Over Time: While higher-quality parts may have a greater upfront cost, their longer lifespan and the reduced likelihood of causing further damage to the conveyor system can make them more cost-effective in the long run.
Guidance on Sourcing the Right Parts
- Know Your Conveyor’s Specifications: Before purchasing new parts, make sure you have all the details of your conveyor’s model, specifications, and the specific parts you need. This includes dimensions, material specifications, and part numbers if available.
- Choose Reputable Suppliers: Source parts from reputable suppliers known for quality. Suppliers should offer parts that meet or exceed OEM (Original Equipment Manufacturer) standards.
- Verify Quality Certifications: Look for parts that come with quality certifications. Certifications such as ISO (International Organization for Standardization) confirm that the parts have been manufactured to high standards.
- Consider Compatibility: Make sure that the parts are compatible with your friction roller conveyor. Using incompatible parts can lead to poor performance and might even damage the conveyor.
- Assess Warranty and Support: Choose suppliers who offer warranties on their parts. A warranty can provide peace of mind and protection from potential defects. Additionally, good supplier support can help resolve any issues that might arise during the replacement process.
- Bulk Ordering: If possible, consider bulk ordering for essential parts. This approach not only ensures that you have critical parts on hand when needed but can also reduce the overall cost through bulk discounts.
- Seek Expert Advice: If you are uncertain about the type of parts your conveyor needs, seek advice from a maintenance expert or consult with the manufacturer. They can offer insights specific to your system that will help in choosing the correct parts.
By following these guidelines, you can effectively source the right parts to maintain your friction roller conveyor, ensuring it continues to operate efficiently and safely for years to come. Quality parts are an investment in the productivity and longevity of your material handling system.
Advancements in Friction Roller Conveyor Technology
The field of material handling is continually evolving, and friction roller conveyors are at the forefront of this technological advancement. Recent developments have significantly enhanced the efficiency, safety, and functionality of these systems. This section explores some of the latest advancements in friction roller conveyor technology, particularly the integration of smart technologies and improvements in system components that boost operational capabilities.
Integration of Smart Technology in the Interroll 3800 Series
One of the most notable advancements in friction roller conveyor technology is the integration of smart technology in systems like the Interroll 3800 series. These smart conveyors are equipped with sensors and control units that enable real-time monitoring and automated adjustments.
- Self-Optimizing System: The conveyor can automatically adjust the roller speed based on the flow of items, reducing bottlenecks and improving overall efficiency.
- Energy Efficiency: Smart friction roller conveyors can dynamically adjust power use based on the load, significantly reducing energy consumption when the conveyor is not fully loaded.
- Predictive Maintenance: Through the use of IoT (Internet of Things) sensors, these conveyors can predict when maintenance is needed, preventing breakdowns before they occur and extending the lifespan of the system.
- Enhanced Safety Features: Integration of safety sensors that can detect human presence and stop the conveyor to prevent accidents, enhancing the safety of operations.
These smart systems not only improve the functionality of friction roller conveyors but also contribute to more sustainable operations by optimizing energy use and reducing waste.
Technological Advancements Improving Efficiency and Safety
The latest technological advancements in friction roller conveyor systems not only enhance their intelligence but also their physical components, contributing to greater efficiency and safety:
- Advanced Roller Designs: New materials and designs for rollers that reduce friction and wear, enhancing the longevity and reliability of the conveyor.
- Modular and Scalable Designs: Conveyors are now being designed with modularity in mind, allowing for easier scalability and customization. This adaptability means systems can be expanded or reconfigured with minimal downtime and disruption.
- Improved Motor Technologies: The use of highly efficient, brushless DC motors provides better speed control, lower heat generation, and reduced energy consumption.
- Sophisticated Control Systems: Advanced controllers that integrate seamlessly with enterprise resource planning (ERP) systems, allowing for better data analytics and system control.
- Safety Mechanisms: Newer models include enhanced safety features such as emergency stops, barriers, and handrails to protect workers operating near the conveyor.
These advancements are designed to meet the increasing demands of modern industries for systems that are not only efficient and robust but also flexible and easy to integrate with existing operations. The smart technology in friction roller conveyors like the Interroll 3800 series exemplifies how these improvements can significantly impact the effectiveness of material handling solutions, making them safer, more efficient, and more adaptable to the needs of businesses today. By leveraging these technologies, companies can achieve higher productivity, better reliability, and enhanced safety, all of which are crucial for competitive operations in various industrial sectors.
Installation, Maintenance, and Safety for Friction Roller Conveyors
Proper installation, regular maintenance, and adherence to safety standards are crucial for maximizing the efficiency, durability, and safety of friction roller conveyors. This section provides detailed guidelines on how to install these systems, essential maintenance routines, and the safety features that should be implemented to comply with industrial standards.
Basic Installation Tips for a Friction Roller Conveyor
Installing a friction roller conveyor correctly is fundamental to its operation and efficiency.
- Level and Alignment: Ensure that the conveyor is perfectly level across its length. Use a spirit level during installation to check this. Proper alignment prevents uneven roller wear and reduces the risk of the conveyor belt slipping.
- Secure Mounting: Anchor the conveyor frames securely to the floor. This stabilization prevents movement of the conveyor, which can lead to misalignment and inefficient operation.
- Electrical Requirements: Verify that the electrical installations meet the power requirements of the conveyor system. This includes checking motor specifications and ensuring that your facility provides adequate power supply without overloading the system.
- Roller Spacing: Adjust the spacing of the rollers according to the size and weight of the items that will be transported. Incorrect spacing can lead to item slippage or blockages, reducing the system’s efficiency.
- Test Before Use: Once installed, run the conveyor system without load to ensure all components are working correctly. Check for any unusual noises or vibrations, which could indicate installation errors that need to be addressed.
Maintenance Routines to Enhance Durability and Efficiency
Regular maintenance is essential to keep a friction roller conveyor running smoothly. The following routines can help enhance its durability and efficiency:
- Regular Cleaning: Keep the rollers and conveyor belt clean from dust, debris, and residues, which can cause wear and tear or even jam the system.
- Lubrication: Periodically lubricate the bearings and rollers to reduce friction and prevent overheating, which can degrade the system over time.
- Tighten Connections: Routinely check and tighten bolts and screws, as vibration can loosen connections over time.
- Inspect Wear Items: Regularly inspect rollers, belts, and motors for signs of wear. Replace worn parts promptly to maintain optimal performance.
- Alignment Checks: Periodically verify that the conveyor is aligned and level to avoid uneven wear or tracking issues.
Safety Features and Compliance Standards
Safety is paramount when operating any heavy machinery, including friction roller conveyors. Implementing these safety features and complying with standards can prevent accidents and injuries:
- Emergency Stops: Install easily accessible emergency stop buttons along the conveyor belt to allow for quick shutdowns in case of an emergency.
- Guardrails: Use guardrails along the sides of the conveyor to prevent items from falling off, which can cause damage or injury.
- Safety Signs: Place clear, visible safety signs around the conveyor area to warn of potential hazards and provide instructions for safe operation.
- Regular Safety Audits: Conduct regular safety inspections and audits to ensure all safety measures are in place and effective.
- Training: Provide thorough training for all operators on the correct use of the conveyor, emphasizing the importance of safety precautions.
Compliance with local and international standards, such as those set by OSHA (Occupational Safety and Health Administration) in the U.S., is also crucial. These standards ensure that the installation and operation of friction roller conveyors meet safety requirements that protect workers and the work environment.
By following these detailed installation guidelines, maintaining the conveyor system regularly, and adhering to established safety protocols, you can ensure that your friction roller conveyor operates efficiently, lasts longer, and contributes positively to your operational success.
Reach out today for custom conveyor roller solutions.
FAQs About Friction Roller Conveyor
A friction roller conveyor is a type of powered conveyor system used widely in various industries for transporting goods across a facility. The system utilizes rollers that are covered with a high-friction material which contacts the bottom surface of the items being moved. This design allows the conveyor to move items smoothly and efficiently by converting the rotational motion of the rollers into linear motion, which propels the items along the length of the conveyor.
Friction roller conveyors are especially useful in situations where control over the speed and positioning of the transported items is crucial. They are commonly used in packaging lines, distribution centers, and manufacturing facilities where precise movement and handling of products are required. The high-friction surface of the rollers ensures that the items do not slip off the conveyor, even when accelerations or decelerations occur.
A friction roller is an integral component of various types of conveyors, particularly friction roller conveyors. It is essentially a roller that has a high-friction surface material, usually rubber or polyurethane. This friction surface is key to the conveyor’s operation as it directly contacts the items being transported, thereby facilitating their movement along the conveyor system.
The primary purpose of a friction roller is to provide enough grip to move items forward without slipping, making it suitable for handling goods with smooth and flat bottoms. The rollers are spaced evenly along the conveyor frame and are often motor-driven, allowing for the precise control of movement speed which is necessary for various industrial applications.
A friction drive conveyor is a specific type of conveyor that employs a series of rollers covered in friction material to propel items forward. This system differs from traditional belt conveyors where a continuous belt does the moving. In a friction drive conveyor, the drive force is transmitted through direct contact between the friction rollers and the item bottoms.
This method of propulsion is highly efficient as it minimizes slippage between the rollers and the items. Friction drive conveyors are particularly advantageous for transporting heavy or bulky items that require careful handling, such as in automotive assembly lines or heavy appliance manufacturing processes. The capability to precisely control the speed and torque of each roller means that items can be moved at consistent speeds, aligned properly, and spaced accurately.
Conveyor rollers come in various types, each designed for specific applications based on the load requirements, environmental conditions, and desired movement mechanism. Here are some of the common types of conveyor rollers:
Gravity Rollers: These rollers operate without motor power, using gravity to move items along the conveyor. They are suitable for lightweight items and must be installed at a slight decline to facilitate movement.
Motorized Rollers: Also known as drive rollers, these are powered by motors which provide the force needed for movement. They are used in heavy-duty applications where manual movement is not feasible.
Grooved Rollers: These rollers have grooves that can accommodate belts for increased traction. They are typically used in belt conveyor systems.
Sprocketed Rollers: Sprocketed rollers are equipped with sprockets and are designed to interact with chains in chain conveyor systems. They provide high torque and are suitable for moving very heavy loads.
Tapered Rollers: Tapered rollers are designed to make curves and turns. They are wider at one end which allows the conveyor to alter the path of the items being transported without manual intervention.
Each type of roller is crucial in its respective conveyor system, providing efficient and effective movement of goods in different industrial settings. Understanding the specific needs of your application is essential in selecting the right type of conveyor roller.
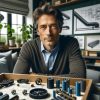
Jordan Smith, a seasoned professional with over 20 years of experience in the conveyor system industry. Jordan’s expertise lies in providing comprehensive solutions for conveyor rollers, belts, and accessories, catering to a wide range of industrial needs. From initial design and configuration to installation and meticulous troubleshooting, Jordan is adept at handling all aspects of conveyor system management. Whether you’re looking to upgrade your production line with efficient conveyor belts, require custom conveyor rollers for specific operations, or need expert advice on selecting the right conveyor accessories for your facility, Jordan is your reliable consultant. For any inquiries or assistance with conveyor system optimization, Jordan is available to share his wealth of knowledge and experience. Feel free to reach out at any time for professional guidance on all matters related to conveyor rollers, belts, and accessories.