Efficient Friction Drive Roller Conveyors for Automation
In the realm of industrial operations and logistics, conveyor systems stand as the backbone of efficient material handling, streamlining processes and enhancing productivity across various sectors. Among these systems, the friction drive roller conveyor emerges as a pivotal innovation, leveraging the fundamental force of friction to propel materials along the production line. This type of conveyor distinguishes itself by employing rollers that are directly driven by frictional contact, eliminating the need for chains or belts. This direct drive mechanism ensures a smooth, controlled movement of goods, making friction drive roller conveyors particularly suitable for environments where precision and gentle handling of materials are paramount. As industries continue to seek more efficient, reliable, and maintenance-friendly conveying solutions, the role of friction drive roller conveyors becomes increasingly significant, marking a new era in material handling technology.
What is a Friction Drive Roller Conveyor?
A friction drive roller conveyor is an advanced material handling system designed to transport goods across various distances and terrains within industrial settings. Our friction roller conveyor systems provide an economical, robust, and customizable solution for light, medium, and heavy unit handling with silent and high-performance rollers. Unlike traditional conveyor systems that may rely on chains or belts to move objects, a friction drive roller conveyor utilizes the direct contact and friction between its rollers and the objects being moved. This direct engagement ensures a smoother and more controlled transportation of goods, making it an ideal choice for delicate or precision-required operations.
The basic concept of a friction drive roller conveyor lies in its ability to adjust the amount of friction applied to the rollers, which in turn controls the speed and movement of the conveyor. This is achieved through the use of specialized drive rollers that are connected to a motor. As these drive rollers rotate, they create friction against the underside of the conveyor belt or directly against the objects on the conveyor, propelling them forward.
When compared to other types of conveyors, such as chain driven or sprocket driven rollers, friction drive roller conveyors offer several advantages. For one, they tend to operate more quietly, as there is no metal-on-metal contact as found in chain-driven systems. Additionally, they require less maintenance since there are no chains or belts that can stretch, wear out, or require tensioning. This makes friction drive roller conveyors a cost-effective solution for many industries looking to optimize their material handling processes.
Feature | Friction Drive Roller Conveyor | Chain Driven Roller Conveyor | Sprocket Driven Roller Conveyor |
---|---|---|---|
Drive Mechanism | Direct friction between rollers and objects | Chain links connecting rollers for movement | Sprockets engaging with a chain to drive rollers |
Noise Level | Lower due to lack of metal-on-metal contact | Higher due to chain movements | Moderate, depending on chain and sprocket condition |
Maintenance | Lower, with minimal moving parts | Higher, requires regular chain maintenance | Moderate, sprockets and chains need maintenance |
Suitability | Ideal for delicate or precision-required operations | Suitable for heavy-duty applications | Good for medium-duty applications with fixed paths |
Cost-Effectiveness | High, due to reduced maintenance costs | Lower, due to the need for regular maintenance | Moderate, depending on the complexity of the system |
Friction drive roller conveyors represent a significant advancement in conveyor technology, offering a blend of efficiency, quiet operation, and reduced maintenance. Their ability to gently and precisely move goods makes them a preferred choice in industries where the integrity of the conveyed items is of utmost importance.
Key Components of Friction Drive Roller Conveyors
The efficiency and reliability of a friction drive roller conveyor hinge on its key components, each playing a crucial role in the system’s overall performance. Understanding these components can provide insights into how friction drive roller conveyors maintain smooth operations and how they stand out from other conveyor types like sprocket driven rollers.
Conveyor Drive Roller
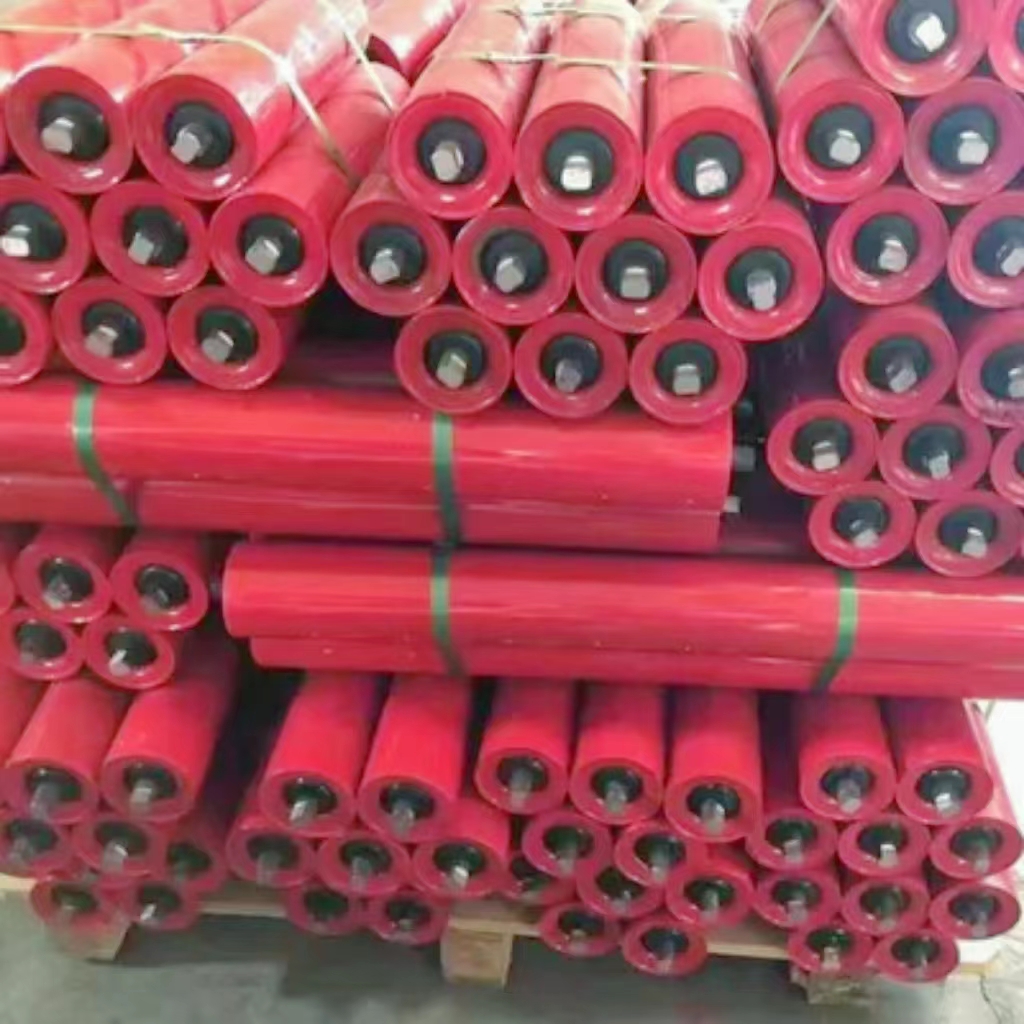
The conveyor drive roller is fundamental to the friction drive roller conveyor, acting as the primary source of motion. These rollers are intricately designed to ensure consistent and efficient movement of goods.
- Rubber-Coated Drive Rollers: These provide increased grip and reduce slippage, ideal for smooth and efficient conveyor operations.
- Motorized Drive Rollers: Integrated with internal motors, these rollers offer precise control over speed and torque.
- Grooved Drive Rollers: Designed with grooves to enhance traction and alignment, ensuring stable movement of items.
- Adjustable Drive Rollers: Allow for changes in tension and pressure to accommodate various load types and weights.
- Polyurethane Drive Rollers: Known for their durability and resistance to wear, tear, and chemicals, making them suitable for harsh environments.
Friction Drive Roller Conveyor Parts
The friction drive roller conveyor system comprises several essential parts, each contributing to the conveyor’s functionality and efficiency. Key components include:
- Rollers: The cylindrical components that directly contact and move the conveyed items. They vary in material, such as steel, plastic, or coated rollers, to suit different applications.
- Bearings: Facilitate smooth roller operation and reduce friction, crucial for the longevity and efficiency of the conveyor.
- Drive Mechanism: The system that powers the conveyor, often including motors and gearboxes, tailored to the required speed and torque.
- Frame: Supports the entire structure of the conveyor and can be made from materials like steel or aluminum for strength and durability.
- Control System: Enables precise control over the conveyor’s speed and direction, often incorporating sensors and automation for optimized performance.
Sprocket Driven Rollers
Sprocket driven rollers, while similar in function to friction drive rollers, operate differently. They use a chain and sprocket system for movement, contrasting with the direct frictional force used in friction drive systems.
- Chain Links: Connect the rollers in a sprocket driven system, providing synchronized movement.
- Sprockets: Gear-like components that engage with the chain, driving the rollers and thus moving the conveyor belt or items.
- Chain Tensioners: Maintain the correct tension in the chain to ensure efficient operation and prevent slippage or breakage.
- Lubrication System: Essential for maintaining the smooth operation of chains and sprockets, reducing wear and extending the system’s lifespan.
- Drive Shaft: Transfers power from the motor to the sprockets, integral to the movement of the conveyor.
The key components of friction drive roller conveyors, from the drive rollers to the intricate parts of the drive mechanism, play pivotal roles in ensuring the system’s efficiency and reliability. Unlike sprocket driven rollers, friction drive conveyors leverage direct contact and friction, offering a smoother and often more adaptable solution for material handling needs.
How Friction Drive Roller Conveyors Work
The operation of a friction drive roller conveyor is a marvel of engineering, utilizing the basic principle of friction to facilitate the movement of goods along its path. This section delves into the step-by-step workings of this conveyor type, highlighting the pivotal role of the conveyor drive roller.
Step-by-Step Operation
- Initialization: The process begins when the motor powering the conveyor drive rollers is activated. These rollers are strategically placed along the conveyor path to ensure consistent movement.
- Friction Generation: As the drive rollers start to rotate, they create friction against the surface of the items placed on the conveyor or against the conveyor belt itself. This friction is what propels the items forward along the conveyor path.
- Motion Transfer: The friction between the drive rollers and the items or belt causes the latter to move. The amount of friction required can be adjusted based on the weight and type of items being conveyed, ensuring a smooth transportation process.
- Speed Regulation: The speed at which the items move is directly controlled by the rotational speed of the drive rollers. This can be finely tuned to match the specific requirements of the operation, whether it’s a slow, careful movement for delicate items or a faster pace for bulk goods.
- Directional Control: The direction in which the items are conveyed can also be managed by the orientation and placement of the drive rollers. By adjusting these factors, items can be directed along straight paths or around bends as needed.
Importance of the Conveyor Drive Roller
The conveyor drive roller is crucial in maintaining efficient motion and control within a friction drive roller conveyor system.
- Consistent Movement: The drive rollers ensure that items move consistently along the conveyor, preventing jams and disruptions in the flow of goods.
- Adjustable Speed: By varying the rotational speed of the drive rollers, operators can control the conveyor speed, making it adaptable to different operational needs.
- Directional Flexibility: The placement and orientation of drive rollers can be configured to guide items in various directions, offering flexibility in conveyor layout design.
- Load Handling: Drive rollers can be designed to handle different load capacities, ensuring that whether the conveyor is transporting light packages or heavy components, the movement remains stable and efficient.
- Reduced Wear and Tear: Since the system relies on friction between the rollers and the items or belt, there’s less wear and tear on the components compared to chain-driven systems, leading to lower maintenance requirements and longer service life.
The friction drive roller conveyor operates on a simple yet effective principle, with the conveyor drive roller playing a pivotal role in ensuring the system’s efficiency, adaptability, and reliability. This makes friction drive roller conveyors an invaluable asset in various material handling applications.
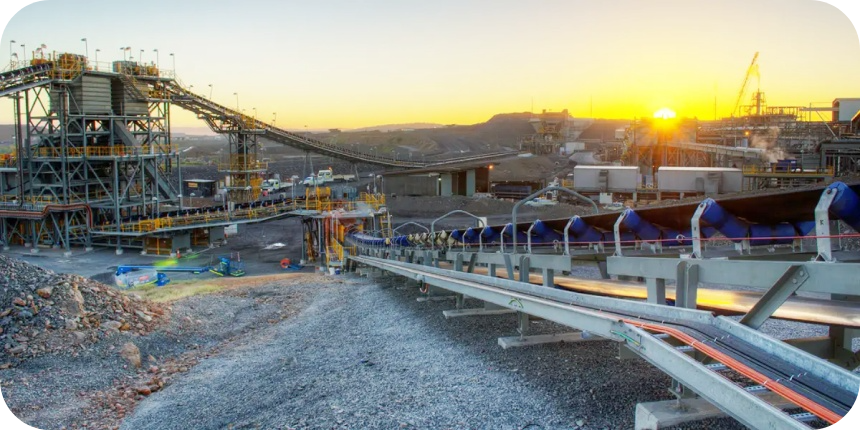
Comparison with Other Conveyor Systems
When evaluating different conveyor systems, it’s essential to understand how the friction drive roller conveyor stands out compared to other common types, such as chain-driven conveyor rollers. Each system has unique advantages and is suited for specific applications. This section will delve into a detailed comparison to highlight the strengths and use cases of friction drive roller conveyors versus chain-driven conveyor rollers and explore the design considerations for chain roller conveyors.
Friction Drive Conveyor vs. Chain Driven Conveyor Roller
Operational Mechanism
A friction drive roller conveyor operates on the principle of frictional contact between the drive roller and the material or conveyor belt, ensuring a smooth and consistent movement. In contrast, a chain-driven conveyor roller relies on chains and sprockets to transmit motion. This fundamental difference impacts several aspects of their operation and suitability for various applications.
Advantages of Friction Drive Roller Conveyor
- Quiet Operation: One of the most significant benefits of a friction drive roller conveyor is its quiet operation. The absence of chains and sprockets reduces noise, making it ideal for environments where noise levels need to be minimized, such as in food processing or assembly lines.
- Lower Maintenance: Friction drive systems typically require less maintenance than chain-driven systems. Chains and sprockets can wear out over time and need regular lubrication and adjustments. In contrast, the friction drive mechanism has fewer moving parts, reducing the frequency and cost of maintenance.
- Smooth and Continuous Flow: The friction drive roller conveyor provides a smoother and more continuous flow of materials. This characteristic is particularly beneficial in applications where precise control over the movement of items is crucial, such as in packaging or conveyor roller manufacturing processes.
- Energy Efficiency: These systems are generally more energy-efficient. The direct contact method of friction drives minimizes energy losses that can occur with chain-driven systems due to friction in the chains and sprockets.
Advantages of Chain Driven Conveyor Roller
- Heavy-Duty Applications: Chain-driven conveyor rollers are well-suited for heavy-duty applications. They can handle larger and heavier loads than friction drive systems, making them ideal for industries like automotive manufacturing and heavy equipment handling.
- Positive Drive: Chain-driven systems provide a positive drive, ensuring that the rollers move in unison with the chain. This feature is advantageous in applications where precise and synchronized movement of rollers is necessary.
- Durability: The robust nature of chains and sprockets makes chain-driven conveyors highly durable and capable of withstanding harsh operating conditions, including high temperatures and exposure to chemicals.
Use Cases
- Friction Drive Roller Conveyor: Ideal for light to medium-duty applications requiring quiet operation, smooth flow, and energy efficiency. Commonly used in packaging, food processing, electronics assembly, and other precision-oriented industries.
- Chain Driven Conveyor Roller: Best suited for heavy-duty applications where handling large, bulky, or heavy items is required. Typical applications include automotive manufacturing, heavy equipment assembly, and conveyor belt bulk material handling.
Chain Roller Conveyor Design
Designing a chain roller conveyor involves several critical considerations to ensure optimal performance and longevity. These include the selection of materials, load capacity, roller spacing, and environmental conditions.
Materials and Construction
- Chains and Sprockets: The choice of chain type (e.g., roller chains, leaf chains) and sprocket material (e.g., steel, stainless steel) is crucial. These components must be durable enough to withstand the operational demands and environmental conditions.
- Rollers: Rollers in a chain-driven conveyor need to be robust and capable of supporting the load without deformation. Materials such as steel or heavy-duty plastic are commonly used.
Load Capacity
- Load Distribution: Ensuring even load distribution across the rollers is vital to prevent undue stress on individual rollers and chains. This involves careful calculation of the roller spacing and chain tension.
- Dynamic Loads: Consideration of dynamic loads, such as the impact of items being placed on the conveyor or transferred from one conveyor to another, is essential. This helps in designing a system that can absorb shocks and minimize wear.
Roller Spacing
- Customizable Spacing: The ability to customize roller spacing is important to accommodate different item sizes and shapes. Proper spacing ensures that items are supported adequately and prevents them from falling through gaps or tipping over.
- Pitch and Alignment: Accurate alignment of the rollers and consistent pitch (distance between chain links) are crucial for smooth operation and longevity of the conveyor system.
Environmental Considerations
- Operating Conditions: The design must account for the operating environment, including temperature, humidity, and exposure to chemicals or abrasive materials. This influences the choice of materials and the design of protective features.
- Maintenance Access: Designing the conveyor for easy access to chains, sprockets, and rollers facilitates maintenance and reduces downtime. Features like removable side panels or accessible lubrication points can enhance maintenance efficiency.
Advantages of Friction Drive Roller Conveyors
Friction drive roller conveyors offer a multitude of benefits that make them a preferred choice in various material handling scenarios. These conveyors leverage the simplicity and efficiency of friction to provide a reliable and versatile conveying solution. Below are detailed examples of the advantages they bring to the table.
Reduced Maintenance
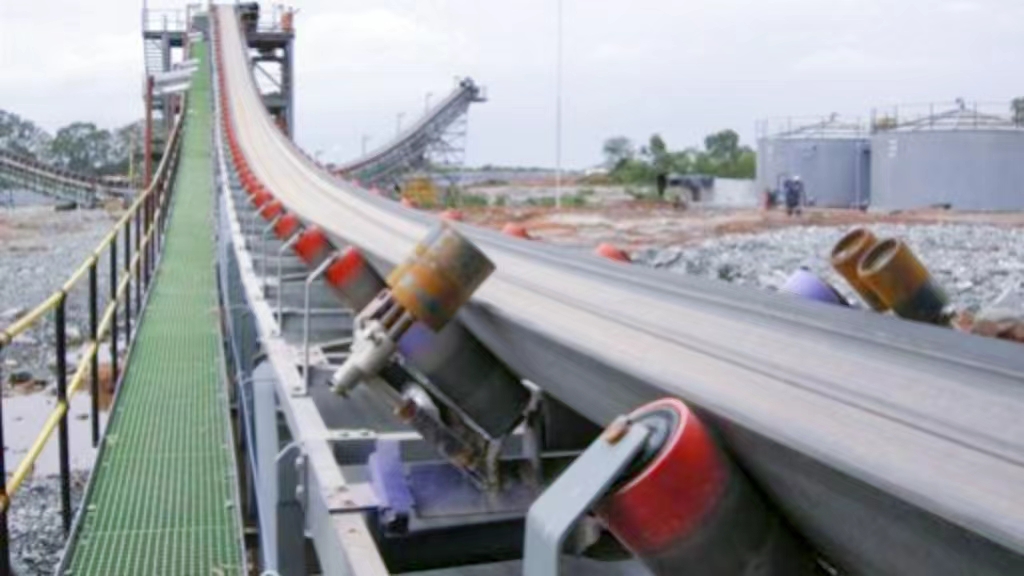
- Less Wear and Tear: The absence of chains or belts in friction drive roller conveyors minimizes the risk of wear and tear, leading to fewer breakdowns and repairs.
- Simplified Design: The straightforward design of these conveyors, with fewer moving parts, translates to less maintenance required over their lifespan.
- Durability of Components: Components such as the rollers and bearings are designed for longevity, reducing the frequency of replacements.
- Ease of Inspection: The open design allows for easy inspection and access to all parts, facilitating quick maintenance tasks.
- Self-Cleaning Mechanism: Some friction drive roller conveyors are equipped with self-cleaning features that prevent the accumulation of debris, further reducing maintenance needs.
Ease of Operation
- User-Friendly Controls: These conveyors often come with intuitive control systems, making it easy for operators to manage the speed and direction of the conveyor.
- Automated Features: Integration with automated systems allows for seamless operation, reducing the need for constant manual oversight.
- Adjustable Speed: The ability to easily adjust the conveyor speed helps in accommodating different operational requirements without complex reconfigurations.
- Quiet Operation: The friction drive mechanism operates more quietly compared to chain-driven systems, creating a more pleasant working environment.
- Reliability: The consistent performance and reduced likelihood of breakdowns ensure smooth operations with minimal interruptions.
Versatility in Handling Various Materials
- Adaptable to Different Loads: Friction drive roller conveyors can handle a wide range of load weights and sizes, from lightweight packages to heavier industrial components.
- Material Compatibility: The design can be tailored with different material rollers and coatings to accommodate various types of goods, including delicate items.
- Configurable Layouts: The flexibility in design allows these conveyors to be set up in multiple configurations, including curves and inclines, to fit different facility layouts.
- Integration Capability: These systems can be easily integrated into existing material handling setups, enhancing their functionality without major overhauls.
- Environmental Adaptability: Friction drive roller conveyors can be designed to operate efficiently in various environmental conditions, including high humidity, temperature extremes, and cleanroom settings.
The advantages of friction drive roller conveyors, from their reduced maintenance requirements and ease of operation to their versatility in handling a broad spectrum of materials, make them an invaluable asset in the realm of material handling and logistics. Their adaptability and reliability underscore their role in enhancing operational efficiency across diverse industries.
Applications and Industries for Friction Drive Roller Conveyors
Friction drive roller conveyors have carved a niche in various sectors, proving to be an indispensable part of the material handling processes across a wide range of industries. Their versatility and efficiency make them particularly beneficial in environments where precision, reliability, and adaptability are paramount. Here are detailed examples of applications and industries where friction drive roller conveyors excel.
Manufacturing
- Automotive Assembly Lines: Friction drive roller conveyors are used to transport parts and assemblies through different stages of vehicle assembly, from chassis construction to final inspection.
- Electronics Manufacturing: These conveyors safely handle delicate electronic components and assemblies, ensuring static-sensitive products are not damaged during the manufacturing process.
- Pharmaceutical Production: In cleanroom environments, friction drive roller conveyor transport ingredients and finished products, maintaining the stringent hygiene standards required in pharmaceutical manufacturing.
- Food and Beverage: Used in the production and packaging of food and beverage products, these conveyors handle everything from raw ingredients to finished goods, adhering to food safety standards.
- Heavy Machinery: For the manufacturing of large industrial machines and equipment, friction drive roller conveyors provide the robust support needed to move heavy components through the assembly process.
Packaging
- E-commerce Fulfillment Centers: These conveyors efficiently move products through various stages of picking, packing, and shipping in fast-paced e-commerce fulfillment environments.
- Parcel Sorting Facilities: Friction drive roller conveyors are integral to the sorting processes in parcel distribution centers, ensuring accurate and efficient handling of a high volume of parcels.
- Pharmaceutical Packaging: In pharmaceutical packaging lines, these conveyors transport products through filling, sealing, and labeling processes in a controlled environment.
- Food Packaging Lines: They are used to convey packaged food products through inspection, sealing, and boxing processes, maintaining food safety and hygiene.
- Consumer Goods Packaging: Friction drive roller conveyors facilitate the packaging of a wide range of consumer goods, from household items to electronics, ensuring products are ready for distribution.
Distribution Centers
- Retail Distribution: These conveyors move goods through receiving, storage, and shipping processes in retail distribution centers, handling a wide variety of product types and sizes.
- Automotive Parts Distribution: In automotive parts distribution centers, friction drive roller conveyors transport parts of various shapes and sizes, from small components to larger body parts.
- Cold Storage Warehousing: Specially designed friction drive roller conveyors operate efficiently in cold storage environments, moving perishable goods through storage and shipping processes.
- Furniture Distribution: These conveyors are used to handle bulky and heavy items like furniture, ensuring smooth movement through the distribution center.
- Chemical Distribution: In facilities handling chemicals and hazardous materials, friction drive roller conveyors are designed to safely transport containers and drums, adhering to strict safety standards.
In each of these applications and industries, friction drive roller conveyors bring significant benefits, including improved efficiency, reduced product damage, and enhanced workflow. Their adaptability to various operational needs and environments makes them a key component in the material handling strategies of diverse sectors.
Future Trends and Innovations in Friction Drive Roller Conveyor Systems
The field of material handling and automation is rapidly evolving, with significant advancements and innovations enhancing the efficiency, reliability, and functionality of conveyor systems. The friction drive roller conveyor, known for its smooth, quiet, and energy-efficient operation, is at the forefront of these technological developments. This section explores the emerging trends in friction drive technology and their impact on the industry.
Advancements in Friction Drive Technology
Smart Sensors and IoT Integration
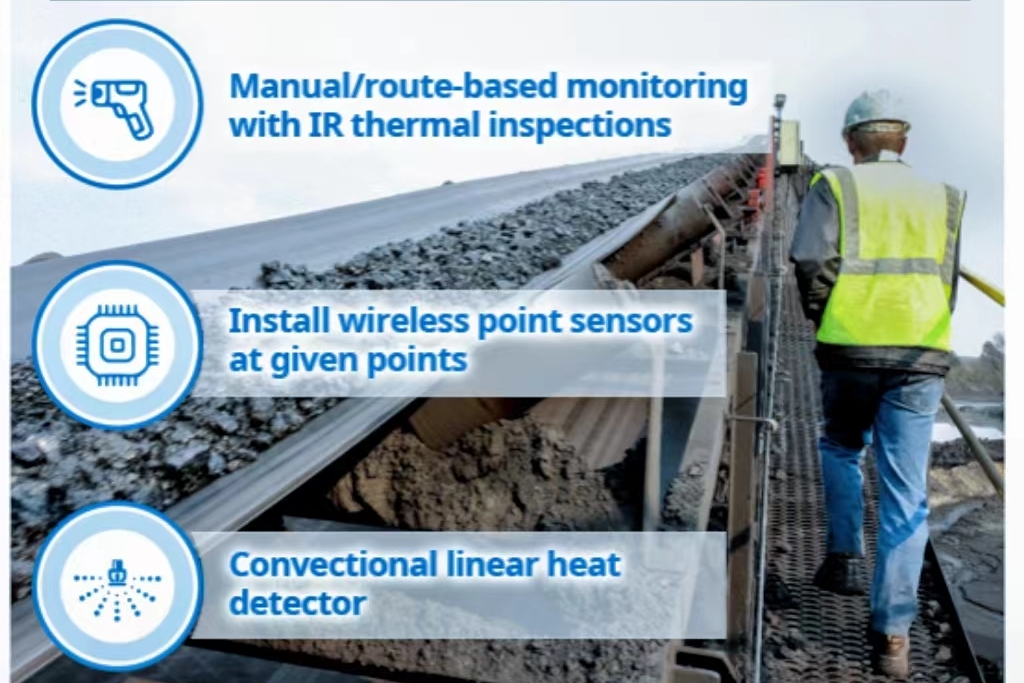
One of the most exciting advancements in friction drive roller conveyor technology is the integration of smart sensors and the Internet of Things (IoT). These sensors can monitor various parameters such as load weight, speed, temperature, and vibration in real-time. By collecting and analyzing this data, operators can gain valuable insights into the conveyor system’s performance and identify potential issues before they lead to downtime. IoT-enabled friction drive roller conveyors allow for predictive maintenance, where maintenance activities are scheduled based on the actual condition of the equipment rather than fixed intervals. This leads to reduced maintenance costs and increased system uptime.
Energy Efficiency Enhancements
Energy efficiency is a critical focus area in the development of friction drive roller conveyor systems. Advances in motor technology and power management systems have led to significant improvements in the energy consumption of these conveyors. Modern friction drive systems are designed to operate at variable speeds, adjusting the power output based on the load requirements. This not only reduces energy usage but also extends the lifespan of the conveyor components by minimizing wear and tear. Additionally, regenerative braking systems are being incorporated to capture and reuse energy during the braking process, further enhancing the overall energy efficiency.
Advanced Materials and Coatings
The use of advanced materials and coatings is another trend shaping the future of friction drive roller conveyors. High-performance polymers and composites are being used to manufacture rollers and other critical components, offering superior durability, reduced weight, and enhanced resistance to wear and environmental factors. Innovative coatings, such as anti-static and low-friction coatings, are being applied to roller surfaces to improve performance and reduce maintenance needs. These materials and coatings not only enhance the longevity and reliability of the conveyors but also allow them to operate effectively in harsh or specialized environments.
Modular and Scalable Designs
Modularity and scalability are becoming increasingly important in the design of friction drive roller conveyors. Modern systems are designed with interchangeable modules that can be easily added, removed, or reconfigured to meet changing operational requirements. This modular approach allows businesses to belt weigh scale their conveyor systems up or down as needed, providing flexibility and cost savings. Scalable designs also enable faster installation and integration of new technologies, ensuring that the conveyor systems can adapt to future advancements and changes in production processes.
Impact on the Industry
Increased Efficiency and Productivity
The advancements in friction drive roller conveyor technology are significantly enhancing the efficiency and productivity of material handling operations. Smart sensors and IoT integration allow for real-time monitoring and optimization, ensuring that conveyors operate at peak efficiency. Energy-efficient designs reduce operational costs, while advanced materials and coatings minimize maintenance requirements. These improvements collectively lead to higher throughput and more reliable operations, allowing businesses to meet increasing demand and maintain a competitive edge.
Enhanced Safety and Ergonomics
Safety and ergonomics are critical considerations in material handling, and the latest innovations in friction drive roller conveyors are addressing these aspects comprehensively. The quiet operation of friction drive systems reduces noise levels in the workplace, creating a more comfortable and safer environment for workers. Advanced sensors can detect and respond to potential hazards, such as jams or overloads, preventing accidents and equipment damage. Ergonomically designed components and modular configurations also make it easier for workers to interact with and maintain the conveyor systems, reducing the risk of injuries.
Sustainability and Environmental Impact
Sustainability is a growing concern across industries, and the advancements in friction drive roller conveyor technology are contributing to more sustainable material handling solutions. Energy-efficient designs and regenerative braking systems reduce energy consumption and carbon emissions. The use of recyclable materials and environmentally friendly coatings further minimizes the environmental impact of these systems. As businesses increasingly prioritize sustainability, the adoption of advanced friction drive roller conveyors can help them achieve their environmental goals and comply with regulatory requirements.
Adoption of Automation and Robotics
The integration of friction drive roller conveyors with automation and robotics is transforming material handling and warehousing operations. Automated guided vehicles (AGVs) and robotic arms can be seamlessly integrated with conveyor systems to automate the movement, sorting, and handling of materials. This integration enhances operational efficiency, reduces labor costs, and improves accuracy. As automation technology continues to advance, the role of friction drive roller conveyors in fully automated and intelligent material handling systems will become even more prominent.
Selection and Customization of Friction Drive Roller Conveyors
Choosing the right friction drive roller conveyor for your specific needs involves considering various factors to ensure optimal performance and efficiency. Customization options further allow these systems to be tailored to meet unique operational requirements, enhancing their functionality and adaptability across different applications.
Tips for Selection
- Assess Load Requirements: Evaluate the weight, size, and type of materials the conveyor will handle. Ensure the selected friction drive roller conveyor can accommodate the maximum load without compromising on speed or efficiency.
- Consider Conveyor Length and Speed: Determine the required length of the conveyor and the desired speed of material transport. This will help in selecting a conveyor with the appropriate drive power and roller density.
- Evaluate Environmental Conditions: If the conveyor will operate in specific environmental conditions such as extreme temperatures, humidity, or cleanliness requirements, ensure the selected system is designed to withstand these conditions.
- Review Integration Needs: Consider how the friction drive roller conveyor will integrate with existing systems. Compatibility with current material handling setups is crucial for seamless operation.
- Analyze Safety and Compliance Requirements: Ensure the conveyor meets all relevant safety standards and regulatory requirements, especially in industries such as food processing or pharmaceuticals, where specific guidelines must be followed.
Customization Options
- Roller Materials and Coatings: Customize the rollers with different materials (e.g., steel, plastic, rubber) and coatings to suit the type of materials being conveyed and to address specific needs such as grip, noise reduction, or chemical resistance.
- Adjustable Speed Controls: Incorporate variable speed drives to allow for easy adjustments to the conveyor speed, accommodating different operational phases or product types.
- Conveyor Layout Configurations: Design the conveyor layout with custom curves, inclines, or declines to fit the available space and to meet specific process flow requirements.
- Specialized Drive Mechanisms: Opt for specialized drive mechanisms, such as high-torque drives for heavy loads or precision drives for delicate handling, to enhance the conveyor’s performance in specific applications.
- Integrated Automation and Sensing Technologies: Equip the friction drive roller conveyor with sensors, barcode readers, or RFID technology for tracking and automation purposes, enabling advanced control over material flow and inventory management.
By carefully selecting and customizing a friction drive roller conveyor, businesses can achieve a highly efficient and tailored material handling solution that meets their specific operational needs. This strategic approach ensures that the conveyor not only performs optimally but also integrates seamlessly into the broader material handling system, contributing to overall productivity and efficiency.
Maintenance and Safety for Friction Drive Roller Conveyors
Maintaining friction drive roller conveyors is crucial for ensuring their longevity and safe operation. Regular inspections and timely part replacements are key practices that prevent potential breakdowns and accidents, ensuring the conveyor system runs smoothly and efficiently.
Maintenance Guidelines
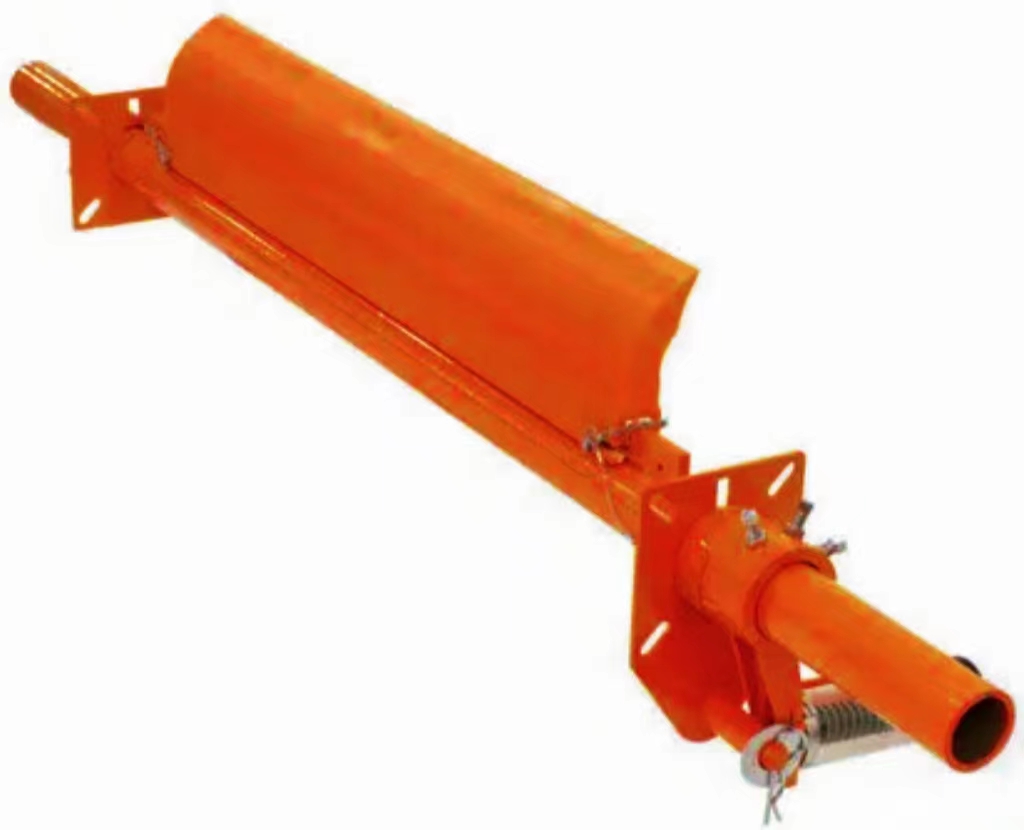
- Regular Cleaning: Keep the rollers and conveyor path clear of debris and dust that can accumulate and cause friction inconsistencies or roller jamming.
- Lubrication: Although friction drive roller conveyors have fewer parts that require lubrication compared to chain-driven systems, it’s important to regularly lubricate bearings and any other moving parts to reduce wear and tear.
- Roller Inspection: Check rollers for signs of wear, damage, or misalignment. Damaged rollers can cause material handling roller conveyor inefficiencies and pose safety risks.
- Drive Mechanism Check: Regularly inspect the drive mechanism, including motors and any drive belts, for signs of wear or fatigue. Ensure that the drive mechanism is properly aligned and functioning efficiently.
- Electrical System Maintenance: For powered systems, ensure that all electrical connections are secure and that there are no exposed wires or potential electrical hazards. Regularly test control systems to ensure they are functioning correctly.
Safety Measures and Inspections
- Emergency Stops: Ensure that emergency stop mechanisms are easily accessible along the conveyor and that they are tested regularly to ensure functionality.
- Guardrails and Barriers: Install guardrails or barriers where necessary to prevent accidental contact with moving parts of the conveyor.
- Warning Signs and Labels: Clearly label operational controls, emergency stops, and any areas where caution is required. Use warning signs to indicate potential hazards associated with the conveyor.
- Training: Provide comprehensive training for all operators and maintenance personnel on the safe operation and maintenance procedures for the friction drive roller conveyor.
- Regular Safety Audits: Conduct regular safety audits to identify potential hazards or areas for improvement in the conveyor’s operation and maintenance procedures.
Part Replacements
- Roller Replacements: Replace worn or damaged rollers immediately to prevent conveyor malfunctions and potential safety hazards.
- Bearing Replacements: Bearings are critical for smooth roller operation. Replace any bearings that show signs of wear or damage to maintain optimal performance.
- Drive Component Upgrades: Periodically assess the drive components for upgrades or replacements, especially if the conveyor is subject to high loads or continuous operation.
- Control System Updates: Keep control systems updated and replace any faulty components to ensure the conveyor operates safely and efficiently.
- Wear Parts Inventory: Maintain an inventory of critical wear parts for quick replacements, minimizing downtime and ensuring continuous, safe operation.
Adhering to these maintenance and safety guidelines ensures that friction drive roller conveyors operate efficiently and safely, contributing to a productive material handling environment. Regular attention to these aspects not only prolongs the life of the conveyor but also safeguards the well-being of the operators and maintenance personnel.
Contact us now for premium conveyor roller solutions.
FAQs About Friction Drive Roller Conveyor
A friction roller conveyor is a type of material handling system that utilizes the principle of friction to move items along its path. Unlike traditional conveyor systems that may rely on chains or belts, friction roller conveyors use rollers that are driven by frictional force to transport goods. This system is particularly effective for transporting items with a flat bottom surface, as the contact between the item and the rollers allows for smooth movement across the conveyor. Friction roller conveyors are known for their versatility and efficiency, making them suitable for a wide range of industries, including manufacturing, packaging, and distribution. They offer the advantage of controlled movement of goods, which can be particularly beneficial in environments where precise positioning of items is required.
Conveyors that use friction drive for conveying are typically known as friction drive roller conveyors or friction-driven conveyors. In these systems, the movement of goods is facilitated by the frictional force generated between the rollers and the items being transported. The rollers are powered and create a frictional grip on the items placed on the conveyor, propelling them forward. This method of conveying is highly efficient and can be used in various applications, from light-duty packaging lines to heavy-duty industrial environments. Friction drive conveyors are appreciated for their simplicity, ease of maintenance, and the ability to accommodate a wide range of product sizes and weights.
Conveyor rollers come in various types, each designed to meet specific operational needs and applications. The most common types include:
Gravity Rollers: These rollers rely on gravity to move items and are typically used in manual or non-powered conveyor systems.
Powered Rollers: Powered by motors, these rollers move items along the conveyor without manual intervention, suitable for automated systems.
Grooved Rollers: Designed with grooves to accommodate drive belts, these rollers are often used in belt conveyor systems.
Tapered Rollers: Ideal for curves and corners in conveyor systems, tapered rollers ensure smooth transitions and maintain item orientation.
Impact Rollers: Positioned at conveyor loading zones, impact rollers absorb the shock and impact of heavy items being dropped onto the conveyor.
Plastic Rollers: Made from durable plastics, these rollers are lightweight, corrosion-resistant, and suitable for various environments, including food processing.
Each type of roller offers unique benefits and is chosen based on the specific requirements of the conveyor system and the materials being transported.
A conveyor belt uses friction in several ways to transport items efficiently from one point to another. The friction between the belt and the drive pulley is crucial for the belt to move. The drive pulley is powered, and as it rotates, friction between its surface and the belt causes the belt to move along with it. Additionally, the friction between the items being conveyed and the surface of the belt prevents the items from sliding off as the belt moves. This frictional grip is essential for maintaining the position and orientation of items on the belt, especially when the conveyor is inclined or moving at high speeds. Conveyor belts are designed with surfaces that optimize this friction to ensure efficient transport of a wide range of materials.
A friction drive system is a type of mechanical drive system that relies on the frictional force between two surfaces to transmit power. In these systems, the drive is typically provided by a rotating roller or wheel that makes contact with another surface, such as a conveyor belt or a roller within a conveyor system. The friction between the surfaces allows for the transfer of motion and power without the need for gears or chains. This method is particularly useful in applications where a smooth and controlled movement is required, such as in conveyor systems used in manufacturing, warehousing, and distribution centers.
Friction on a conveyor belt refers to the resistance encountered when the belt moves over rollers or other supporting surfaces. This frictional force is essential for the proper functioning of the conveyor system as it helps to maintain the motion of the belt and ensures the smooth transfer of materials. In a conveyor system, the friction between the belt and the rollers or the drive mechanism can be adjusted to achieve the desired speed and performance. High friction can lead to increased wear and tear on the belt and rollers, while too little friction can cause slippage and inefficient operation. Therefore, balancing friction is crucial for optimizing the performance and longevity of a conveyor system.
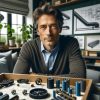
Jordan Smith, a seasoned professional with over 20 years of experience in the conveyor system industry. Jordan’s expertise lies in providing comprehensive solutions for conveyor rollers, belts, and accessories, catering to a wide range of industrial needs. From initial design and configuration to installation and meticulous troubleshooting, Jordan is adept at handling all aspects of conveyor system management. Whether you’re looking to upgrade your production line with efficient conveyor belts, require custom conveyor rollers for specific operations, or need expert advice on selecting the right conveyor accessories for your facility, Jordan is your reliable consultant. For any inquiries or assistance with conveyor system optimization, Jordan is available to share his wealth of knowledge and experience. Feel free to reach out at any time for professional guidance on all matters related to conveyor rollers, belts, and accessories.