Optimizing Operations: Roller Conveyor Drive Bands
In the realm of material handling and logistics, roller conveyors stand as the backbone of countless operations, facilitating the seamless movement of goods across various sectors. Central to their efficiency are the roller conveyor drive bands, the unsung heroes that power these systems, ensuring the smooth and continuous flow of items along the production line. These drive bands come in a myriad of forms, each tailored to meet specific operational demands and environmental conditions. From the robust and durable to the highly flexible and efficient, the variety of roller conveyor drive bands available today is vast, catering to a wide range of industrial applications. This introduction aims to shed light on the pivotal role these drive bands play in the functionality of roller conveyors and to explore the diverse types that have been developed to enhance the productivity and reliability of these indispensable systems.
Exploring the Types of Roller Conveyor Drive Bands
The efficiency and adaptability of roller conveyors in various industrial settings largely hinge on the type of roller conveyor drive bands employed. These bands, integral to the system’s operation, come in various materials and designs, each serving distinct purposes and environments.
Polyurethane Drive Bands
Polyurethane drive bands are renowned for their durability and flexibility, making them a popular choice in numerous applications. The standard clear urethane bands are prized for their elasticity and resistance to wear, suitable for light to medium-duty tasks with a temperature range typically between -30°C to 80°C and a recommended initial stretch of about 10%. On the other hand, blue high-strength urethane bands are designed for more demanding environments, offering enhanced tensile strength and resistance to chemicals and oils, with a slightly higher temperature range up to 100°C and an advised initial stretch of 15-20%.
- Clear Urethane Band 3mm: Ideal for light packaging conveyors.
- Blue High-Strength 5mm: Suited for chemical processing lines.
- Clear Urethane Band 6mm: Perfect for assembly lines with moderate loads.
- Blue High-Strength 8mm: Designed for heavy loads in automotive assembly.
- Clear Urethane Band 4mm with Anti-Static Properties: For electronic component manufacturing.
- Blue High-Strength 10mm: For heavy-duty material handling in mining operations.
Quick-Hook Twisted Round Belts
Quick-hook twisted round belts offer a unique blend of convenience and efficiency, particularly in systems requiring frequent assembly and disassembly. These belts can be quickly connected and disconnected without the need for specialized tools, making them ideal for temporary setups or systems undergoing regular maintenance.
- 6mm Twisted Round Belt: For postal sorting facilities.
- 8mm High-Grip Twisted Belt: For packaging lines with rapid changeovers.
- 5mm Quick-Hook Belt: For retail distribution conveyors.
- 7mm Twisted Round Belt with UV Resistance: For outdoor applications.
- 9mm Quick-Hook Belt: For automotive parts handling.
- 4mm Twisted Round Belt: For light-duty agricultural processing.
Heavy Duty Roller Conveyor Drive Bands
Heavy-duty roller conveyor drive bands are engineered to withstand the rigors of intense industrial environments, such as those found in mining, construction, and heavy manufacturing. These bands are characterized by their exceptional strength, resistance to abrasion, and ability to handle high loads without stretching or breaking.
- 12mm Reinforced Urethane Band: For construction material handling.
- 15mm Heavy-Duty Rubber Band: For mining conveyor applications.
- 10mm Reinforced Silicone Band: For high-temperature applications in metal processing.
- 14mm Heavy-Duty Polyurethane Band: For automotive assembly lines with heavy components.
- 16mm Reinforced Neoprene Band: For oil and gas industry conveyors.
- 18mm Ultra-Heavy-Duty Band: For aerospace parts handling.
Each type of roller conveyor drive band offers unique benefits tailored to specific industrial needs, ensuring the smooth and efficient operation of roller conveyor systems across a broad spectrum of applications.
Customization and Sizing of Roller Conveyor Drive Bands
The versatility of roller conveyor systems is greatly enhanced by the variety of roller conveyor drive bands available, not just in terms of material and type, but also in size and customization options. The right size and fit of a drive band are crucial for the optimal performance of a conveyor system, ensuring smooth operation, minimal wear, and extended lifespan of both the bands and the conveyor components.
Common Sizes and Applications
Roller conveyor drive bands come in several standard sizes, each suited to specific applications based on the load and the distance between rollers. For instance, the DB 96 size is commonly used in standard conveyor setups where the drive shaft to roller distance is between 110mm to 120mm, ideal for medium-duty material handling. The DB 90, slightly shorter, is tailored for closer roller-to-roller distances around 95-100mm, often seen in lighter applications or as an emergency substitute for drive shaft to roller setups. The PB 7 and DB 73 sizes cater to even more compact configurations, suitable for applications requiring tight roller spacing for small or delicate items.
- DB 96: Utilized in distribution centers for medium-sized packages.
- DB 90: Perfect for assembly lines with smaller product spacing.
- PB 7: Ideal for pharmaceutical conveyors handling small vials.
- DB 73: Used in electronics manufacturing for delicate component transport.
Customization for Optimal Performance
The ability to customize roller conveyor drive bands to specific conveyor setups is a game-changer for many operations. Cut-to-length options allow for precise sizing, eliminating slack or tension issues that can lead to inefficiencies or damage. Customization can also include the integration of features such as anti-static properties, reinforced cores for heavy-duty applications, or specific profiles to match unique roller designs.
- Anti-Static Bands for Electronic Components: Custom-sized to prevent static buildup during transport.
- Reinforced Core Bands for Heavy Loads: Designed for industrial applications with heavy components, ensuring durability.
- High-Grip Surface Bands for Slippery Items: Customized for food processing lines where moisture is present.
- Temperature-Resistant Bands for Hot or Cold Environments: Sized for applications in extreme temperatures, maintaining flexibility and strength.
- UV-Resistant Bands for Outdoor Use: Custom-cut for outdoor conveyor systems, ensuring longevity despite sun exposure.
- Chemical-Resistant Bands for Harsh Environments: Tailored for chemical processing plants, resistant to corrosive substances.
Selecting the right size and customization options for roller conveyor drive bands is essential for the efficiency and reliability of the conveyor system. It ensures that the drive bands are perfectly matched to the operational demands, leading to smoother operations, reduced maintenance requirements, and longer service life for both the bands and the conveyor system as a whole.
Diverse Applications and Advantages of Roller Conveyor Drive Bands
The utility of roller conveyor drive bands extends far beyond their basic function of propelling conveyor rollers. Their adaptability and efficiency have paved the way for innovative applications across various industries, highlighting their indispensable role in modern material handling solutions.
Reusing Roller Conveyor Drive Bands
The potential for reusing roller conveyor drive bands presents an opportunity for cost savings and environmental sustainability. However, ensuring that these used bands are still fit for purpose involves careful inspection for wear, tension retention, and overall integrity. Reused bands can find applications in:
- Light-Duty Packaging Lines: Where the stress on the bands is minimal, allowing for extended use.
- Agricultural Sorting Conveyors: For non-critical applications like sorting fruits and vegetables.
- Workshop Tool Conveyors: In environments where the conveyor usage is intermittent.
- Educational Facilities: For training and educational purposes in engineering courses.
- Prototype Testing: Where temporary conveyor setups are used for testing designs.
- Theatrical Productions: For moving props and sets where high precision is not critical.
Finding Roller Conveyor Drive Bands for Sale
When looking to purchase roller conveyor drive bands, prioritizing quality and reliability is key to ensuring long-term efficiency. High-quality drive bands can be sourced from:
- Specialized Material Handling Suppliers: Offering a wide range of sizes and materials.
- Manufacturer Direct Sales: Ensuring compatibility with specific conveyor models.
- Online Industrial Marketplaces: Where a variety of options and competitive pricing are available.
- Local Industrial Supply Stores: Providing the advantage of immediate availability.
- Custom Fabrication Shops: For tailored solutions specific to unique operational needs.
- Refurbished Material Handling Equipment Dealers: Offering tested and certified used options.
Innovative Uses of Roller Conveyor Drive Bands
The versatility of roller conveyor drive bands has led to their adoption in a variety of innovative applications, demonstrating their adaptability and efficiency:
- Automated Library Systems: For gentle handling of books and media.
- Pharmaceutical Clean Rooms: Where their non-particulate shedding properties are crucial.
- Food Processing Plants: Utilizing FDA-approved materials for direct food contact.
- High-Speed Sorting Facilities: Where their durability supports rapid item sorting.
- Robotic Assembly Lines: Integrating with robotic systems for precise component placement.
- Theme Parks: For moving props and set pieces in attractions and rides.
The applications and benefits of roller conveyor drive bands underscore their significance in the seamless operation of conveyor systems across industries. Their ability to be reused, the ease of sourcing high-quality replacements, and their innovative uses highlight the roller conveyor drive bands’ versatility and essential role in efficient material handling and beyond.
Installation and Maintenance of Roller Conveyor Drive Bands
Ensuring the optimal performance of roller conveyor systems involves not only selecting the right roller conveyor drive bands but also understanding the intricacies of their installation and ongoing maintenance. Proper installation and regular upkeep can significantly extend the life of drive bands and minimize operational disruptions.
Fitting Roller Conveyor Drive Bands: A Step-by-Step Guide
The correct installation of roller conveyor drive bands is crucial for the efficient operation of the conveyor system. Here’s a step-by-step guide to ensure proper fitting:
- Inspect the Conveyor: Before installation, check the conveyor for any damage or misalignment that might affect the drive band’s performance.
- Choose the Correct Size: Ensure the drive band selected matches the required length and width for your specific conveyor setup.
- Prepare the Tools: Gather necessary tools such as tension gauges, cutters for custom lengths, and joining kits for seamless installation.
- Install the Drive Band: Carefully loop the drive band over the drive shaft and rollers, ensuring it sits evenly without twisting.
- Adjust Tension: Use a tension gauge to adjust the drive band to the recommended tension level to prevent slippage or overstretching.
- Test the Conveyor: Run the conveyor system to ensure the drive band is properly aligned and operating smoothly without any unusual noises or vibrations.
Maintenance Tips for Roller Conveyor Drive Bands
Regular maintenance of roller conveyor drive bands is essential to prolong their lifespan and ensure continuous operation. Here are best practices for maintaining these crucial components:
- Regular Inspections: Conduct periodic inspections for signs of wear, fraying, or damage, particularly in high-stress areas.
- Cleanliness: Keep the drive bands and conveyor components clean from debris and dust that can cause abrasion and premature wear.
- Proper Tensioning: Regularly check and adjust the tension of the drive bands to prevent slippage and ensure efficient power transmission.
- Lubrication: Ensure that rollers and shafts are adequately lubricated to reduce friction and wear on the drive bands.
- Avoid Overloading: Ensure the conveyor system is not overloaded beyond its capacity, which can strain and damage the drive bands.
- Replacement Schedule: Establish a schedule for replacing drive bands based on their condition and operational hours to prevent unexpected failures.
By adhering to these installation and maintenance guidelines, the longevity and efficiency of roller conveyor drive bands can be significantly enhanced, contributing to the smooth and reliable operation of the entire conveyor system.
Selecting the Ideal Roller Conveyor Drive Bands for Your System
The process of choosing the right roller conveyor drive bands is pivotal to the operational efficiency and longevity of your conveyor system. This selection is influenced by a myriad of factors, each playing a crucial role in ensuring the conveyor meets the demands of your specific application.
Critical Considerations for Drive Band Selection
When selecting roller conveyor drive bands, it’s essential to evaluate several key factors to ensure compatibility with your system’s requirements:
- Load Capacity: Assess the maximum weight the conveyor will need to support. Heavier loads necessitate drive bands with greater tensile strength to prevent elongation or breakage.
- Environmental Conditions: Consider the operating environment. Extreme temperatures, exposure to chemicals, or abrasive conditions require drive bands made from materials that can withstand these elements without degrading.
- Conveyor Speed: The operational speed of the conveyor influences the type of drive band needed. High-speed applications may require drive bands with specialized materials or designs to maintain performance without excessive wear.
- Conveyor Dimensions: The length and width of the conveyor system play a significant role in determining the appropriate drive band size and strength to ensure efficient power transmission across the system.
- Product Characteristics: The nature of the products being conveyed (e.g., their weight, size, and fragility) can dictate the required properties of the drive bands to ensure gentle and secure transportation.
- Maintenance and Replacement: Opt for drive bands that are not only durable but also easy to maintain and replace, minimizing potential downtime for your operations.
The Influence of Conveyor Components on Drive Band Selection
The compatibility and performance of roller conveyor drive bands are also significantly affected by the conveyor components with which they interact:
- Conveyor Roller Bearings: High-quality bearings ensure the smooth operation of rollers, reducing friction and wear on the drive bands, thereby extending their service life.
- Rollex Conveyor Rollers: Renowned for their precision and durability, Rollex rollers can enhance drive band performance by providing consistent, smooth motion and reducing the risk of slippage or misalignment.
- Conveyor Drive Rollers: The material and surface texture of drive rollers can greatly influence the effectiveness of drive bands, affecting their grip and overall efficiency in power transmission.
- Drive Shaft Alignment: Properly aligned drive shafts ensure even tension across the drive band, preventing uneven wear and extending the lifespan of the band.
- Roller Surface Texture: The texture of conveyor rollers can impact the traction of drive bands. A surface that’s too smooth might lead to slippage, while too rough a texture can cause excessive wear.
- Roller Diameter: The diameter of the rollers can affect the drive band’s performance. Larger diameters typically reduce the bending stress on the band, which can lead to a longer operational life.
By carefully considering these factors and understanding the role of various conveyor components, you can make an informed decision when selecting roller conveyor drive bands, ensuring they are perfectly suited to your system’s needs and operational demands.
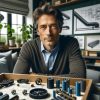
Jordan Smith, a seasoned professional with over 20 years of experience in the conveyor system industry. Jordan’s expertise lies in providing comprehensive solutions for conveyor rollers, belts, and accessories, catering to a wide range of industrial needs. From initial design and configuration to installation and meticulous troubleshooting, Jordan is adept at handling all aspects of conveyor system management. Whether you’re looking to upgrade your production line with efficient conveyor belts, require custom conveyor rollers for specific operations, or need expert advice on selecting the right conveyor accessories for your facility, Jordan is your reliable consultant. For any inquiries or assistance with conveyor system optimization, Jordan is available to share his wealth of knowledge and experience. Feel free to reach out at any time for professional guidance on all matters related to conveyor rollers, belts, and accessories.