Advantages of Conveyor Belt Bulk Material Handling
Conveyor belt bulk material handling is a critical aspect of many industrial processes. Conveyor belts play a vital role in efficiently transporting large volumes of materials across various stages of production. This system is essential in industries such as mining, agriculture, and manufacturing, where the movement of bulk materials is a constant requirement. Conveyor belt bulk material handling involves using belts to move materials horizontally or vertically within a facility. These belts are designed to handle a wide range of materials, from fine powders to large, abrasive rocks. The efficiency and reliability of conveyor belt bulk material handling systems help reduce manual labor, increase productivity, and enhance workplace safety.
Advantages of Using Conveyor Belt Bulk Material Handling
Conveyor belt bulk material handling offers numerous advantages, making it an indispensable component in many industrial sectors. This section will delve into the specific benefits, including efficiency in transporting large quantities of materials, enhanced safety compared to manual handling, and cost-effectiveness over long distances.
Efficiency in Transporting Large Quantities of Materials
One of the primary advantages of conveyor belt bulk material handling is its efficiency in moving large volumes of materials quickly and reliably. Conveyor belts are designed to handle various types of bulk materials, ranging from fine powders to large rocks, with ease. This capability significantly reduces the time required to transport materials from one point to another within a facility.
The continuous nature of conveyor belt systems means that they can operate non-stop, unlike manual handling or batch processing methods. This constant movement helps maintain a steady flow of materials, ensuring that production processes are not interrupted. Additionally, conveyor belts can be customized to operate at different speeds, allowing for the precise control of material flow rates. This adaptability ensures that materials are delivered at the right pace to meet the demands of various stages of the production process.
Safety Benefits Compared to Manual Handling
Conveyor belt bulk material handling significantly enhances workplace safety by reducing the reliance on manual labor. Manual handling of heavy or hazardous materials can lead to numerous health and safety risks, including musculoskeletal injuries, accidents, and exposure to harmful substances. Conveyor belts mitigate these risks by automating the material handling process.
Here are five specific examples of safety benefits provided by conveyor belt bulk material handling:
- Reduced Lifting and Carrying: Conveyor belts eliminate the need for workers to lift and carry heavy loads, reducing the risk of back injuries and muscle strains.
- Minimized Risk of Accidents: Automated systems reduce the likelihood of accidents caused by human error, such as dropping or mishandling materials.
- Controlled Environment Exposure: Conveyor belts can be enclosed or covered to contain dust, fumes, or other hazardous materials, protecting workers from exposure to harmful substances.
- Improved Ergonomics: By reducing repetitive manual tasks, conveyor belts help prevent ergonomic-related injuries, such as carpal tunnel syndrome and tendonitis.
- Enhanced Operational Safety: Conveyor systems can be equipped with safety features like emergency stop buttons, sensors, and guards, further protecting workers from potential hazards.
Cost-Effectiveness Over Long Distances
Another significant advantage of conveyor belt bulk material handling is its cost-effectiveness, especially over long distances. Conveyor belts provide a continuous and reliable method for transporting materials, which translates to lower operational costs compared to other methods.
Several factors contribute to the cost-effectiveness of conveyor belts:
- Energy Efficiency: Conveyor systems are designed to be energy-efficient, consuming less power than alternatives like trucks or manual labor for the same volume of material transported.
- Reduced Labor Costs: By automating the material handling process, conveyor belts reduce the need for a large workforce, leading to significant savings in labor costs.
- Maintenance Savings: Modern conveyor belts are built with durable materials and advanced engineering, resulting in lower maintenance and repair costs over time. Regular maintenance schedules and predictive maintenance technologies further extend the lifespan of conveyor systems.
- Minimized Downtime: The reliability of conveyor belt systems reduces downtime due to equipment failure or material handling delays, ensuring continuous production and minimizing financial losses.
- Scalability and Flexibility: Conveyor belt systems can be easily scaled and adapted to meet changing production needs, avoiding the costs associated with overhauling or replacing material handling infrastructure.
Conveyor belt bulk material handling offers unparalleled efficiency, safety, and cost-effectiveness, making it a vital component in various industrial operations. By understanding and leveraging these advantages, companies can enhance their production processes, improve workplace safety, and achieve significant cost savings.
Key Considerations for Conveyor Belt Bulk Material Handling Systems
When designing and implementing conveyor belt bulk material handling systems, several critical factors must be taken into account to ensure efficiency, reliability, and safety. This section will explore these key considerations, including the assessment of material characteristics, the selection of the appropriate belt type and material, and the importance of belt speed and width.
Assessment of Material Characteristics
The first step in designing a conveyor belt bulk material handling system is to thoroughly assess the characteristics of the materials to be transported. Understanding these characteristics helps in selecting the right type of conveyor belt and ensuring that the system operates effectively.
- Weight: The weight of the material influences the choice of the conveyor belt’s strength and durability. Heavy materials require belts with higher tensile strength to prevent stretching and ensure longevity.
- Abrasiveness: Materials with high abrasiveness, such as sand or crushed rock, can cause significant wear and tear on conveyor belts. For such materials, belts with abrasion-resistant covers are necessary to extend the life of the system.
- Temperature: The operating temperature of the material can affect the choice of belt material. High-temperature materials may require belts made of heat-resistant materials, while cold temperatures may necessitate belts with low-temperature resistance.
- Moisture Content: Materials with high moisture content can affect the traction and slippage of the conveyor belt. Belts with special surface treatments or textures can help manage moisture and prevent material slippage.
- Chemical Properties: Materials that contain chemicals or have corrosive properties require belts made from chemically resistant materials to avoid degradation and ensure safe handling.
Determining the Correct Belt Type and Material
Selecting the right belt type and material is crucial for the success of a conveyor belt bulk material handling system. The choice depends on the characteristics of the material being handled and the specific requirements of the operation.
- Rubber Belts: These are commonly used for their flexibility and durability. They are suitable for a wide range of materials, including aggregates, coal, and ores.
- PVC Belts: PVC belts are ideal for handling lighter materials and applications where moisture and chemical resistance are important.
- Metal Belts: For extremely heavy or high-temperature materials, metal belts provide the necessary strength and heat resistance. They are often used in foundries and metalworking industries.
- Fabric Belts: These belts are reinforced with textile layers and are used for medium-duty applications. They offer a good balance of strength and flexibility.
- Specialty Belts: Belts with specific coatings or surface treatments, such as anti-static or flame-resistant properties, are used for specialized applications to meet safety and operational requirements.
Understanding the Importance of Belt Speed and Width
The speed and width of the conveyor belt are critical factors that influence the efficiency and effectiveness of the bulk material handling system. These parameters must be carefully calculated to match the operational needs.
- Belt Speed: The speed at which the conveyor belt moves is determined by the material flow rate requirements. Higher speeds can increase throughput but may also lead to increased wear and tear. For example, in mining operations, higher speeds are often necessary to move large volumes of material quickly.
- Material Flow Characteristics: Different materials flow at different rates. Fine powders, for instance, may require slower belt speeds to prevent dust generation, while coarse materials may be transported more efficiently at higher speeds.
- Width of the Belt: The width of the conveyor belt must accommodate the volume of material being transported. Wider belts can handle larger quantities of material, reducing the need for multiple conveyors and minimizing material spillage.
- Capacity and Load Distribution: The belt width and speed must be selected to ensure even load distribution. Uneven loads can cause belt misalignment and increase wear on the system.
- Operational Considerations: Factors such as incline, turns, and elevation changes in the conveyor path must be considered when determining belt speed and width. For example, conveyors that need to elevate material to different heights may require slower speeds and wider belts to maintain stability and prevent material rollback.
Designing an efficient and reliable conveyor belt bulk material handling system involves a comprehensive assessment of material characteristics, careful selection of the appropriate belt type and material, and precise calculation of belt speed and width. By addressing these key considerations, companies can optimize their material handling processes, enhance operational efficiency, and ensure the longevity and safety of their conveyor systems.
Overview of Conveyor Belt Bulk Material Handling Equipment
In the context of conveyor belt bulk material handling, various types of equipment are used alongside conveyor belts to ensure efficient, safe, and continuous operation. This section provides a detailed overview of some key equipment, such as feeders, hoppers, and silos, and explains the roles each type of equipment plays in a bulk material handling system.
Description of Equipment Used Alongside Conveyor Belts
Bulk material handling systems rely on a range of auxiliary equipment to support the transportation and processing of materials.
- Feeders:
Feeders are devices that regulate the flow of materials onto the conveyor belt. They ensure a consistent and controlled supply of materials, preventing overloading and ensuring smooth operation. - Hoppers:
Hoppers are large, funnel-shaped containers used to store bulk materials temporarily before they are fed onto the conveyor belt. They are designed to handle large quantities of materials and provide a steady feed to the conveyor system. - Silos:
Silos are tall, cylindrical structures used for storing bulk materials in large volumes. They are often used for materials like grains, cement, and minerals, providing long-term storage solutions. - Stackers and Reclaimers:
Stackers are used to pile bulk materials in a storage yard, while reclaimers are used to recover these materials and feed them back onto the conveyor belt for further processing or transportation. - Dust Collectors:
Dust collectors are systems designed to capture and remove dust generated during the handling and transportation of bulk materials. They help maintain a clean and safe working environment by reducing airborne dust levels.
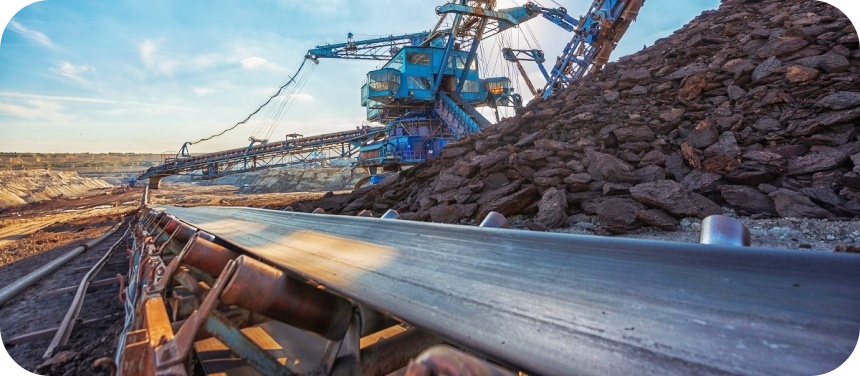
Explanation of the Roles Each Type of Equipment Plays
Each type of equipment used in conveyor belt bulk material handling systems plays a specific role in ensuring the efficiency and effectiveness of the material handling process.
- Feeders:
Feeders are crucial for maintaining a consistent flow of materials onto the conveyor belt. They help prevent bottlenecks and ensure that the conveyor operates at optimal capacity. There are different types of feeders, including apron feeders, belt feeders, and vibrating feeders, each suited for different types of materials and applications. For instance, vibrating feeders are ideal for fine materials, while apron feeders are used for heavy, coarse materials. - Hoppers:
Hoppers provide temporary storage for bulk materials and ensure a controlled feed onto the conveyor belt. They are designed to handle surges in material flow and prevent spillage. Hoppers can be equipped with features like gates and valves to control the discharge rate, ensuring a steady and consistent supply of materials to the conveyor system. - Silos:
Silos are essential for long-term storage of bulk materials. They provide a large storage capacity and help maintain the quality of stored materials by protecting them from environmental factors like moisture and contamination. Silos are often used in industries like agriculture, mining, and cement manufacturing, where large volumes of materials need to be stored and handled efficiently. - Stackers and Reclaimers:
Stackers are used to create stockpiles of bulk materials in a systematic and organized manner. They help maximize storage space and ensure easy access to materials when needed. Reclaimers, on the other hand, are used to retrieve materials from the stockpiles and feed them back onto the conveyor belt. This equipment is particularly useful in facilities with large storage yards and high material turnover rates. - Dust Collectors:
Dust collectors play a vital role in maintaining a safe and clean working environment. During the handling and transportation of bulk materials, dust can be generated, posing health and safety risks to workers. Dust collectors capture and filter out dust particles, preventing them from becoming airborne. This equipment is especially important in industries handling fine, dry materials, such as cement, flour, and chemicals.
Conveyor belt bulk material handling systems rely on a variety of auxiliary equipment to function effectively. Feeders, hoppers, silos, stackers, reclaimers, and dust collectors each play crucial roles in ensuring the smooth, efficient, and safe transportation and storage of bulk materials. Understanding the functions and benefits of each type of equipment helps in designing and implementing effective bulk material handling systems that meet the specific needs of different industries.
Designing Conveyor Belt Bulk Material Handling Systems
Designing conveyor belt bulk material handling systems requires careful consideration of various factors to ensure they meet the specific needs of a facility. Customization and thoughtful layout planning are crucial to achieving an efficient and effective system. This section will discuss the importance of customizing designs to meet facility needs and the key considerations in layout, including elevation changes and turns.
Importance of Customizing Design to the Needs of the Facility
Every facility has unique requirements that must be addressed when designing a conveyor belt bulk material handling system. Customizing the design ensures that the system operates efficiently and effectively, minimizing downtime and maximizing productivity. Here are five examples of how customization can be tailored to meet the specific needs of different facilities:
- Material Characteristics:
Different materials have distinct characteristics that influence the design of the conveyor system. For example, a facility handling abrasive materials like sand or gravel would require belts with higher wear resistance, while a facility dealing with fragile items like glass would need gentle handling features to prevent breakage. - Throughput Requirements:
The volume of material to be transported per hour is a critical factor. Facilities with high throughput requirements, such as mining operations, need robust conveyor systems capable of handling large volumes continuously. Conversely, facilities with lower throughput may opt for smaller, more cost-effective systems. - Space Constraints:
The available space within a facility can significantly impact the design of the conveyor system. In facilities with limited space, compact and flexible conveyor designs, such as modular or telescopic conveyors, are necessary to fit within the constraints while maintaining efficiency. - Environmental Conditions:
Environmental factors, such as temperature, humidity, and dust levels, must be considered. For instance, facilities operating in extreme temperatures may require belts made from materials that can withstand these conditions, while facilities with high dust levels need enclosed or covered conveyors to prevent dust contamination. - Integration with Existing Systems:
Many facilities need to integrate new conveyor systems with existing machinery and processes. Customizing the design ensures seamless integration, reducing the need for extensive modifications and minimizing disruptions to ongoing operations.
Considerations in Layout
The layout of a conveyor belt bulk material handling system is a critical aspect of its design. Proper layout planning can enhance efficiency, reduce operational costs, and ensure the safety of the system. Key considerations in layout include elevation changes and turns.
- Elevation Changes:
Conveyor systems often need to transport materials across different elevation levels within a facility. Designing for elevation changes requires careful consideration to maintain the stability and flow of materials. Inclined conveyors, such as cleated belts or bucket elevators, can be used to move materials upwards, while gravity-assisted chutes or declines can be used for downward transportation. Properly designed elevation changes help prevent material rollback and spillage. - Turns and Bends:
Many facilities require conveyors to navigate around obstacles or fit within specific floor plans, necessitating turns and bends in the conveyor path. Designing for turns involves selecting the appropriate type of conveyor, such as belt curves or modular chain conveyors, that can handle directional changes without causing material loss or belt misalignment. Ensuring smooth transitions at bends is crucial to maintaining a consistent material flow. - Load Distribution:
Uniform load distribution across the conveyor system is essential to prevent overloading and uneven wear. Properly designed layout plans account for load distribution by placing loading and unloading points strategically and using devices like diverters and gates to control material flow. - Access and Maintenance:
Designing the layout to provide easy access for maintenance and inspection is vital for the longevity and reliability of the system. Including walkways, platforms, and access points allows maintenance personnel to perform routine checks and repairs without disrupting operations. - Safety Features:
Incorporating safety features into the layout, such as emergency stop buttons, guardrails, and safety nets, helps protect workers and equipment. Clear labeling and signaling, along with well-planned escape routes, enhance overall safety.
Designing a conveyor belt bulk material handling system involves a comprehensive understanding of the facility’s unique needs and careful planning of the system layout. By customizing the design and considering factors like elevation changes, turns, load distribution, access, and safety, companies can create efficient, reliable, and safe material handling systems that meet their operational requirements.
Conveyor Belt Bulk Material Handling System Components
Effective conveyor belt bulk material handling systems rely on several key components working together seamlessly. Each component plays a crucial role in ensuring the system’s efficiency, reliability, and safety. This section will detail these key components, including belts, rollers, frames, and drives, and discuss their maintenance requirements.
Detailing the Key Components of a Conveyor System
- Belts:
The belt is the primary component of a conveyor system, responsible for carrying materials from one point to another. Belts are made from various materials, including rubber, PVC, and metal, each suited to different types of bulk materials. For example, rubber belts are commonly used for their durability and flexibility, PVC belts are preferred for lightweight materials and applications requiring chemical resistance, and metal belts are chosen for their strength and heat resistance in heavy-duty applications. - Rollers:
Rollers support and guide the conveyor belt, ensuring smooth and efficient movement. There are two main types of rollers: carrying rollers, which support the loaded belt, and return rollers, which support the empty belt on its return journey. Rollers can be made from materials like steel, rubber, or plastic, and they often include bearings to reduce friction and wear. - Frames:
The frame is the structure that supports the entire conveyor system. It provides stability and alignment for the belt and rollers. Frames are typically made from steel or aluminum, offering strength and durability to withstand the weight and movement of bulk materials. Modular frame designs allow for easy assembly, disassembly, and customization to fit specific layout requirements. - Drives:
Drives are the components that power the conveyor belt, ensuring continuous movement of materials. They consist of motors, gearboxes, and drive pulleys. The type and size of the drive depend on the conveyor’s length, load capacity, and speed requirements. Electric motors are commonly used for their efficiency and controllability, while hydraulic and pneumatic drives are used in specific applications requiring variable speed and torque. - Idlers:
Idlers are additional rollers placed at regular intervals along the conveyor to support the belt and material load. They help maintain belt alignment and reduce sagging. Idlers can be categorized into various types, such as troughing idlers, which support the belt in a trough shape to center the material load, and flat idlers, which support the return side of the belt.
Maintenance Requirements for Each Component
Regular maintenance of conveyor belt bulk material handling system components is essential to ensure their longevity and efficient operation. Each component has specific maintenance needs:
- Belts:
Belts require regular inspection for signs of wear, damage, or misalignment. Routine cleaning is necessary to remove any build-up of material that could affect belt performance. Tension adjustments are also crucial to prevent slippage and ensure proper tracking. For rubber belts, checking for cracks or tears and repairing them promptly can extend their lifespan. - Rollers:
Rollers should be regularly inspected for wear, misalignment, and lubrication issues. Bearings within the rollers need periodic lubrication to reduce friction and prevent overheating. Replacing worn-out or damaged rollers promptly helps maintain smooth belt operation and prevents additional strain on the drive system. - Frames:
The frame should be checked for structural integrity and alignment. Regular tightening of bolts and inspection for corrosion or damage ensures that the frame remains stable and secure. Cleaning the frame and removing any debris prevents potential blockages and maintains a safe operating environment. - Drives:
Drives require regular inspection and maintenance of motors, gearboxes, and drive pulleys. Ensuring that the motor and gearbox are properly lubricated and free from excessive wear can prevent breakdowns. Drive belts and chains should be checked for proper tension and alignment. Additionally, monitoring the electrical components for any signs of overheating or electrical faults is essential for safety and efficiency. - Idlers:
Idlers need regular checks for alignment, wear, and lubrication. Ensuring that the idlers are properly aligned helps prevent belt misalignment and reduces wear on both the belt and idlers. Lubricating the bearings within idlers can extend their operational life and maintain smooth belt movement.
The key components of a conveyor belt bulk material handling system, including belts, rollers, frames, drives, and idlers, each play a vital role in the system’s overall performance. Proper and regular maintenance of these components ensures the system operates efficiently, reduces downtime, and extends the lifespan of the equipment. By understanding the functions and maintenance requirements of each component, facilities can optimize their bulk material handling processes and maintain a safe and productive working environment.
Selection of Belt Conveyors of Conveyor Belt Bulk Material Handling
The selection of belt conveyors for conveyor belt bulk material handling is a crucial process that requires careful consideration of various factors. Choosing the right conveyor belt ensures efficiency, safety, and longevity of the handling system. This section will discuss the factors influencing the selection of conveyor belts and provide examples of different types of belt conveyors suitable for various applications.
Factors that Influence the Selection of Conveyor Belts
Several key factors must be considered when selecting conveyor belts for bulk material handling systems. These factors help determine the most suitable belt for specific operational needs, ensuring optimal performance and durability.
- Material Characteristics:
The properties of the bulk material being handled significantly influence the choice of conveyor belt. Characteristics such as weight, size, abrasiveness, temperature, and moisture content dictate the type of belt material and design. For example, highly abrasive materials like coal or minerals require belts with high abrasion resistance, while materials with high moisture content may need belts with special surface treatments to prevent slippage. - Load Capacity:
The load capacity of the conveyor belt must be sufficient to handle the maximum weight of the materials being transported. Overloading a belt can lead to premature wear, damage, and potential system failure. Ensuring that the belt can support the load requirements is crucial for maintaining system integrity and performance. - Operational Environment:
The environment in which the conveyor system operates affects the selection of the belt. Factors such as temperature extremes, exposure to chemicals, and outdoor conditions (such as rain, snow, or UV radiation) require belts made from materials that can withstand these conditions. For instance, belts operating in high-temperature environments need to be heat-resistant, while those exposed to chemicals must be chemically resistant. - Belt Speed and Length:
The speed and length of the conveyor belt are critical considerations. Higher belt speeds increase the system’s throughput but may also increase wear and tear on the belt. Similarly, longer conveyor belts require robust construction to handle the increased tension and potential sagging. Selecting a belt that matches the required speed and length ensures efficient and reliable operation. - Maintenance and Serviceability:
The ease of maintenance and serviceability of the conveyor belt is another important factor. Belts that are easy to inspect, clean, and repair help minimize downtime and extend the system’s operational life. Features such as modular designs or quick-release mechanisms can simplify maintenance tasks and reduce overall maintenance costs.
Different Types of Belt Conveyors Suitable for Various Applications
There are several types of belt conveyors designed to meet the specific needs of different applications in conveyor belt bulk material handling. Each type offers unique advantages suited to particular operational requirements.
- Flat Belt Conveyors:
Flat belt conveyors are the most common type used in bulk material handling. They consist of a continuous belt supported by rollers or a flat pan along its length. Flat belt conveyors are versatile and suitable for transporting a wide range of materials, from lightweight to heavy items, in various industries, including manufacturing, agriculture, and mining. - Cleated Belt Conveyors:
Cleated belt conveyors feature raised sections or “cleats” that help secure materials on the belt and prevent them from sliding back, especially on inclined paths. These conveyors are ideal for transporting loose or bulk materials, such as grains, pellets, and powders, over steep inclines. - Modular Belt Conveyors:
Modular belt conveyors use interlocking plastic or metal modules instead of a continuous belt. This design offers flexibility in configuring the conveyor to different layouts, including curves and elevation changes. Modular belts are easy to clean and maintain, making them suitable for applications in food processing, packaging, and pharmaceuticals. - Incline/Decline Belt Conveyors:
Incline and decline belt conveyors are designed to move materials between different elevation levels. They are equipped with cleats or textured surfaces to prevent material rollback. These conveyors are commonly used in warehouses, distribution centers, and production lines where materials need to be transported up or down inclines. - Curved Belt Conveyors:
Curved belt conveyors allow materials to be transported around corners or obstacles without the need for additional transfer points. These conveyors are essential in facilities with complex layouts where straight-line conveyors cannot be used. Curved belt conveyors are used in various industries, including parcel handling, automotive, and food and beverage processing.
The selection of belt conveyors for conveyor belt bulk material handling involves careful consideration of material characteristics, load capacity, operational environment, belt speed and length, and maintenance requirements. Understanding these factors and the different types of belt conveyors available allows for the design of efficient, reliable, and cost-effective material handling systems tailored to specific industrial needs.
Implementing Conveyor Belt Bulk Material Handling Systems
Implementing conveyor belt bulk material handling systems involves a series of critical steps to ensure the system is installed correctly and operates efficiently. This process includes detailed planning, precise installation, and comprehensive training for operators and maintenance personnel. This section will outline the steps for installation and implementation of a new conveyor belt system and discuss the importance of training for those involved in its operation and maintenance.
Steps for Installation and Implementation of a New Conveyor Belt System
- Initial Assessment and Planning:
The first step in implementing a conveyor belt bulk material handling system is conducting a thorough assessment of the facility’s requirements. This includes evaluating the types of materials to be handled, the volume of materials, the layout of the facility, and any specific operational challenges. Detailed planning involves creating a blueprint of the conveyor system, specifying the type of conveyor belts, and determining the placement of auxiliary equipment such as feeders, hoppers, and silos. - Design and Customization:
Based on the initial assessment, the next step is designing the conveyor system. This involves selecting the appropriate conveyor belts and customizing them to meet the specific needs of the application. Customization may include adding cleats, sidewalls, or special coatings to the belts, as well as designing the layout to accommodate elevation changes, turns, and space constraints. Manufacturers and engineers collaborate to ensure the design meets all operational and safety requirements. - Procurement of Equipment:
Once the design is finalized, the necessary equipment is procured. This includes the conveyor belts, rollers, frames, drives, and any additional components required for the system. It is crucial to source high-quality equipment from reputable manufacturers to ensure the reliability and longevity of the system. - Installation:
The installation process begins with preparing the site, which may involve clearing the area, setting up foundations, and installing support structures. The conveyor frames and support structures are then assembled, followed by the installation of rollers and drives. The conveyor belts are carefully aligned and tensioned to ensure smooth operation. During installation, it is essential to follow manufacturer guidelines and industry standards to prevent any issues that could affect the system’s performance. - Integration and Testing:
After installation, the conveyor system is integrated with other equipment in the facility. This may involve connecting the conveyors to feeders, hoppers, silos, and other processing machinery. Comprehensive testing is conducted to ensure the system operates as intended. This includes checking belt alignment, load capacity, speed, and safety features. Any issues identified during testing are addressed and resolved before the system is put into full operation. - Final Inspection and Commissioning:
A final inspection is carried out to verify that the entire system meets all design specifications and safety standards. Once the inspection is completed and any necessary adjustments are made, the conveyor system is commissioned for full operation. This marks the completion of the installation process and the start of regular operations.
Training for Operators and Maintenance Personnel
Training is a vital component of implementing a conveyor belt bulk material handling system. Proper training ensures that operators and maintenance personnel understand how to use and maintain the system effectively, minimizing downtime and extending the system’s lifespan.
- Operator Training:
Operators are trained on the safe and efficient use of the conveyor system. This includes understanding the controls and monitoring systems, recognizing and responding to operational issues, and adhering to safety protocols. Training sessions often cover topics such as starting and stopping the conveyor, adjusting belt speed, handling material spills, and using emergency stop mechanisms. Hands-on training with real-life scenarios helps operators become proficient in managing the system under various conditions. - Maintenance Training:
Maintenance personnel receive detailed training on the upkeep and repair of the conveyor system. This includes routine inspection procedures, lubrication of moving parts, tensioning and aligning belts, and replacing worn or damaged components. Maintenance training emphasizes preventive measures to avoid common issues and extends the service life of the system. Technicians are also trained to troubleshoot and resolve mechanical and electrical problems that may arise during operation. - Safety Training:
Both operators and maintenance personnel undergo safety training to ensure they are aware of potential hazards and know how to mitigate risks. This training covers the use of personal protective equipment (PPE), understanding safety signage and signals, and emergency response procedures. Emphasizing safety helps prevent accidents and injuries, creating a safer working environment.
The successful implementation of conveyor belt bulk material handling systems requires meticulous planning, precise installation, and comprehensive training for operators and maintenance personnel. By following these steps and investing in thorough training, facilities can achieve efficient, reliable, and safe operation of their conveyor systems, enhancing productivity and reducing operational costs.
Discover why our conveyor belts are industry-leading.
FAQs About Conveyor Belt Bulk Material Handling
Bulk materials are typically handled using belt conveyors due to their versatility and efficiency. Belt conveyors can transport a wide variety of bulk materials, including coal, ore, sand, grain, and gravel. They are preferred for their ability to cover long distances, handle large capacities, and operate continuously. Other types of conveyors used in bulk material handling include screw conveyors, which are ideal for moving fine materials or powders, and bucket elevators, which are used for vertical transportation of bulk materials. Additionally, drag chain conveyors are used for heavy and abrasive materials, while pneumatic conveyors are suited for moving lightweight bulk materials through pipelines using air pressure.
The material handling capacity of a conveyor depends on several factors, including the width and speed of the belt, the type of material being transported, and the incline angle of the conveyor. Generally, the capacity is measured in tons per hour (TPH) or cubic feet per minute (CFM). For instance, a standard belt conveyor with a width of 24 inches operating at a speed of 100 feet per minute can handle approximately 500 to 1,000 tons of material per hour, depending on the Conveyor belt rubber density and particle size. Manufacturers provide detailed capacity charts and formulas to calculate the exact handling capacity based on specific operational parameters.
Yes, a conveyor is a type of material handling equipment designed to transport materials from one location to another within a facility. Conveyors are essential in various industries, including mining, agriculture, manufacturing, and logistics, for their ability to move bulk materials efficiently and safely. They reduce manual labor, increase productivity, and enhance safety by automating the transportation process. There are different types of conveyors, such as belt conveyors, screw conveyors, and roller conveyors, each suited to specific material handling needs. As material handling equipment, conveyors are integral to streamlining processes and improving operational efficiency.
The bulk material handling process involves several steps to move, store, and manage large quantities of materials in industries such as mining, agriculture, and manufacturing. The process begins with the extraction or collection of materials, which are then transported using conveyors to various processing or storage areas. Equipment like feeders, hoppers, and silos are used to regulate and store materials. Conveyors, including belt conveyors, screw conveyors, and bucket elevators, play a crucial role in transporting materials across different stages. Once the materials reach their destination, they may be processed, packaged, or loaded for shipment. The entire process is designed to be efficient, minimizing manual handling and ensuring the safe and reliable movement of bulk materials through the production or distribution chain. Regular maintenance and monitoring of the equipment are essential to prevent downtime and ensure smooth operations.
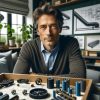
Jordan Smith, a seasoned professional with over 20 years of experience in the conveyor system industry. Jordan’s expertise lies in providing comprehensive solutions for conveyor rollers, belts, and accessories, catering to a wide range of industrial needs. From initial design and configuration to installation and meticulous troubleshooting, Jordan is adept at handling all aspects of conveyor system management. Whether you’re looking to upgrade your production line with efficient conveyor belts, require custom conveyor rollers for specific operations, or need expert advice on selecting the right conveyor accessories for your facility, Jordan is your reliable consultant. For any inquiries or assistance with conveyor system optimization, Jordan is available to share his wealth of knowledge and experience. Feel free to reach out at any time for professional guidance on all matters related to conveyor rollers, belts, and accessories.