Conveyor Belt Water Diverter Prevents Erosion on Gravel
Erosion on unpaved roads and trails poses significant challenges, leading to surface degradation, increased maintenance costs, and potential environmental impact. Traditional methods of erosion control often fall short in durability and effectiveness, necessitating innovative solutions. Enter the conveyor belt water diverter, a novel approach to managing water flow and minimizing erosion. These diverters are designed to channel water away from vulnerable surfaces, thereby preserving the integrity of unpaved roads and trails.
What is a Conveyor Belt Water Diverter
A conveyor belt water diverter is an innovative erosion control solution designed to manage water flow on unpaved roads, trails, and similar surfaces. Conveyor belt water diversions direct water off roads, reducing erosion by channeling it away from wheel ruts, similar to water bars or grade-breaks. At its core, the diverter is a repurposed piece of conveyor belt material, This simple yet effective mechanism plays a crucial role in preserving road integrity, preventing erosion, and maintaining the natural landscape.
The primary purpose behind using a conveyor belt water diverter is to combat the erosive forces of water on unpaved surfaces. When rainwater or runoff flows uncontrolled across such roads, it can wash away the surface material, create ruts, and lead to significant degradation over time. This not only impacts the road’s usability but also contributes to sedimentation in nearby waterways, posing environmental concerns. Conveyor belt water diverters address these issues by intercepting water flow and guiding it off the road at controlled intervals. This not only protects the road surface but also reduces the need for frequent maintenance and repairs.
The genius of the conveyor belt water diverter lies in its simplicity and effectiveness. Made from durable, weather-resistant materials, these diverters can withstand harsh conditions and heavy traffic without significant wear and tear. Their flexibility allows them to be installed on various terrains and in different configurations, making them a versatile solution for many erosion control challenges. Moreover, the use of recycled conveyor belts in their construction makes them an environmentally friendly option, contributing to waste reduction and sustainability efforts.
A conveyor belt water diverter is a practical, cost-effective, and eco-friendly solution for managing water flow and preventing erosion on unpaved roads and trails. Its adoption reflects a commitment to preserving infrastructure and the environment through innovative, sustainable practices.
5 Benefits of Conveyor Belt Water Diverter
The adoption of a conveyor belt water diverter brings multiple benefits to the management of unpaved roads and trails. These benefits not only enhance the durability and functionality of these paths but also contribute to environmental conservation efforts. Here are five key advantages:
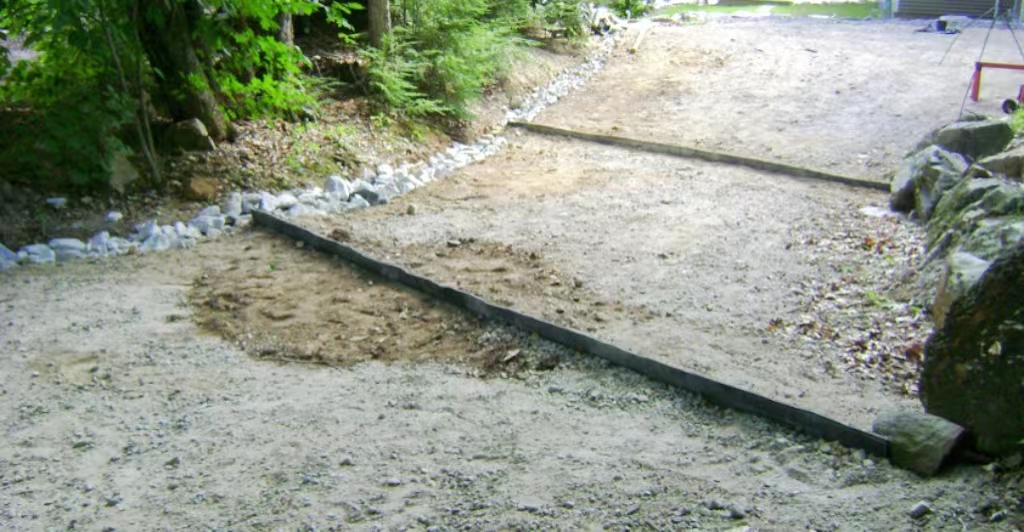
- Erosion Control: The primary benefit of a conveyor belt water diverter is its ability to significantly reduce erosion on unpaved roads. By diverting water flow away from the road surface, it prevents the water from washing away the material, thus maintaining the integrity of the road and reducing maintenance needs.
- Durability: Made from tough, resilient materials, a conveyor belt water diverter is designed to withstand harsh weather conditions and heavy loads. Unlike traditional water bars that may degrade or become dislodged over time, conveyor belt diverters maintain their position and effectiveness, ensuring long-term erosion control.
- Cost-Effectiveness: Implementing a conveyor belt water diverter is a cost-efficient solution for erosion control. The use of recycled materials in their construction makes them an affordable option, and their durability means lower maintenance and replacement costs over time.
- Low Maintenance Requirements: Once installed, a conveyor belt water diverter requires minimal maintenance. Its robust design and materials resist wear, and it remains effective even under heavy traffic, eliminating the need for frequent checks and repairs.
- Versatility Across Terrains: The flexible nature of a conveyor belt water diverter allows it to be used on various terrains, including gravel roads, trails, and driveways. Its adaptability makes it suitable for a wide range of environments, from flat landscapes to hilly areas, providing effective water management and erosion control in diverse settings.
These benefits highlight the effectiveness of a conveyor belt water diverter in addressing the challenges of unpaved road maintenance and environmental conservation. Its ability to control erosion, combined with its durability, cost-effectiveness, low maintenance, and versatility, makes it an invaluable tool in the management of rural and wilderness areas.
Types of Conveyor Belt Water Diverters
Used Conveyor Belt Water Diverter
Benefits of Using Recycled Conveyor Belts
One of the most effective and environmentally friendly ways to manage water diversion on unpaved roads is by using recycled conveyor belts. A used conveyor belt water diverter is both cost-effective and sustainable, as it repurposes materials that would otherwise contribute to waste. Recycled conveyor belts are typically made of durable rubber or synthetic materials that can withstand harsh weather conditions and heavy traffic. This durability makes them ideal for long-term erosion control solutions.
Environmental Impact
Using a used conveyor belt water diverter significantly reduces the environmental impact compared to new materials. Recycling old belts not only cuts down on waste but also minimizes the carbon footprint associated with manufacturing new products. By repurposing these materials, communities and individuals contribute to a more sustainable environment.
Cost Savings
One of the major advantages of a used conveyor belt water diverter is the cost savings. New materials can be expensive, but recycled conveyor belts are often available at a fraction of the cost. This makes it an affordable option for individuals, farmers, and local governments looking to manage water diversion on a budget.
Availability and Sourcing
Recycled conveyor belts can be sourced from various industries, including mining, agriculture, and manufacturing. These belts are often discarded after they have served their primary purpose, but they still possess significant structural integrity for use in water diversion. Many companies and recycling centers offer used conveyor belts for sale, making it relatively easy to find the materials needed for this project.
Considerations
While the benefits are substantial, there are some considerations to keep in mind when using a used conveyor belt water diverter. First, it is important to inspect the belt for any damage or wear that could affect its performance. Ensure that the belt is free from significant tears, holes, or weaknesses that could compromise its ability to divert water effectively. Additionally, consider the size and thickness of the belt to ensure it fits the specific requirements of your project.
DIY Conveyor Belt Water Diverter
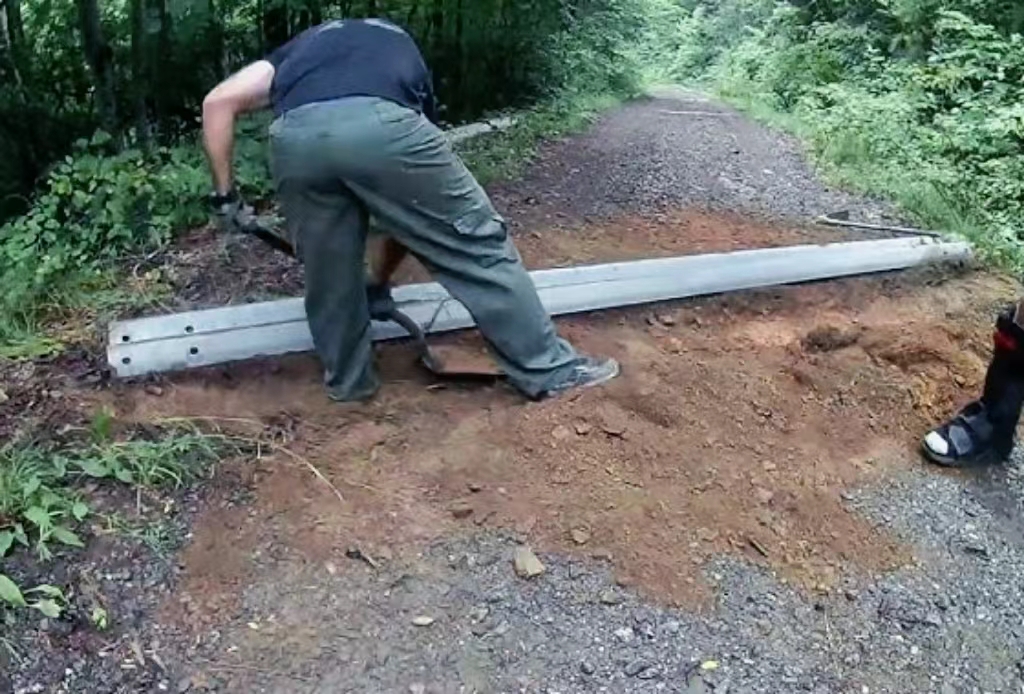
Creating a DIY conveyor belt water diverter is a straightforward and rewarding project that can be completed with basic tools and materials. This guide will walk you through the process step-by-step.
Materials Needed
To construct a DIY conveyor belt water diverter, you will need the following materials:
- A length of recycled conveyor belt (preferably 15 inches tall)
- 2×6 inch treated lumber
- Galvanized bolts and nuts
- Wide diameter washers
- Utility knife
- Drill and drill bits
- Adjustable wrenches
- Measuring tape
Step-by-Step Guide
Measure and Cut the Conveyor Belt
Measure the length of the area where you plan to install the water diverter. Cut the conveyor belt to the desired length using a utility knife. Make sure the belt is long enough to span the width of the road with some extra length for securing to the lumber.
Prepare the Treated Lumber
Cut the 2×6 inch treated lumber to match the length of the conveyor belt. This lumber will serve as the conveyor belt supporting structure.
Drill Holes in the Conveyor Belt and Lumber
Using a drill, create evenly spaced holes along the length of the conveyor belt. These holes should align with holes drilled into the treated lumber. Ensure the holes are large enough to accommodate the galvanized bolts.
Attach the Conveyor Belt to the Lumber
Secure the conveyor belt to the treated lumber using galvanized bolts, nuts, and wide diameter washers. The washers will help distribute the pressure and prevent the bolts from tearing through the rubber. Tighten the bolts with adjustable wrenches to ensure a firm attachment.
Dig the Trench
Dig a trench diagonally across the road surface where the diverter will be installed. The trench should be deep enough so that approximately 4 inches of the conveyor belt protrudes above the road surface.
Install the Water Diverter
Place the assembled conveyor belt and lumber structure into the trench. Ensure it is positioned at a 30-degree angle to the road. Backfill the trench with soil and compact it to secure the diverter in place.
Finish and Inspect
Once installed, inspect the diverter to ensure it is stable and properly positioned. Make any necessary adjustments to ensure optimal water diversion.
Benefits of a DIY Conveyor Belt Water Diverter
Creating your own conveyor belt water diverter offers several benefits. It allows for customization to fit specific project needs and provides a sense of accomplishment. Additionally, DIY projects often result in cost savings compared to purchasing pre-made solutions.
Considerations
When undertaking a DIY project, it is important to ensure you have the necessary tools and skills to complete the installation safely and effectively. If you are unsure, seeking advice from a professional or consulting detailed guides and tutorials can be beneficial.
By understanding the types of conveyor belt water diverters and how to implement them, you can effectively manage water flow and reduce erosion on unpaved roads. Whether you choose to use recycled materials or embark on a DIY project, these solutions offer practical and sustainable methods for protecting your roadways.
Applications of Conveyor Belt Water Diverter
The conveyor belt water diverter finds its utility in a variety of settings, proving to be an adaptable solution for managing water flow and controlling erosion. Its applications span across different types of unpaved surfaces, each benefiting from the diverter’s ability to efficiently redirect water. Here are some key areas where a conveyor belt water diverter can be effectively used:
- Low Volume Access Roads: These roads, often found in rural or wilderness areas, are susceptible to erosion due to water runoff. A conveyor belt water diverter installed across these roads can significantly reduce the impact of water, maintaining the road’s integrity and usability.
- Driveways: Residential driveways, especially those with a gravel surface, can suffer from water damage over time. The installation of a conveyor belt water diverter helps in managing water flow, preventing the formation of ruts and erosion.
- Farm Lanes: Agricultural areas benefit greatly from the use of a conveyor belt water diverter. These lanes, used for accessing different parts of a farm, are essential for the movement of machinery and goods. Diverters help in preserving these lanes by preventing water-induced damage.
- Camp Lanes: In camping areas, pathways and access lanes are crucial for the movement of campers and equipment. A conveyor belt water diverter ensures these lanes remain navigable, even during periods of heavy rainfall, by effectively managing water runoff.
- Erosion Control and Water Bars: In addition to specific types of roads and lanes, a conveyor belt water diverter serves as an efficient alternative to traditional water bars. Its ability to be customized for different terrains and its durability make it a preferred choice for controlling erosion in various environmental settings.
- Gravel Roads, Trails, and Rural Settings: The versatility of a conveyor belt water diverter allows it to be used in managing water flow on gravel roads and trails, which are particularly vulnerable to erosion. Its effectiveness in rural settings, where maintenance resources may be limited, underscores its value in preserving these essential pathways.
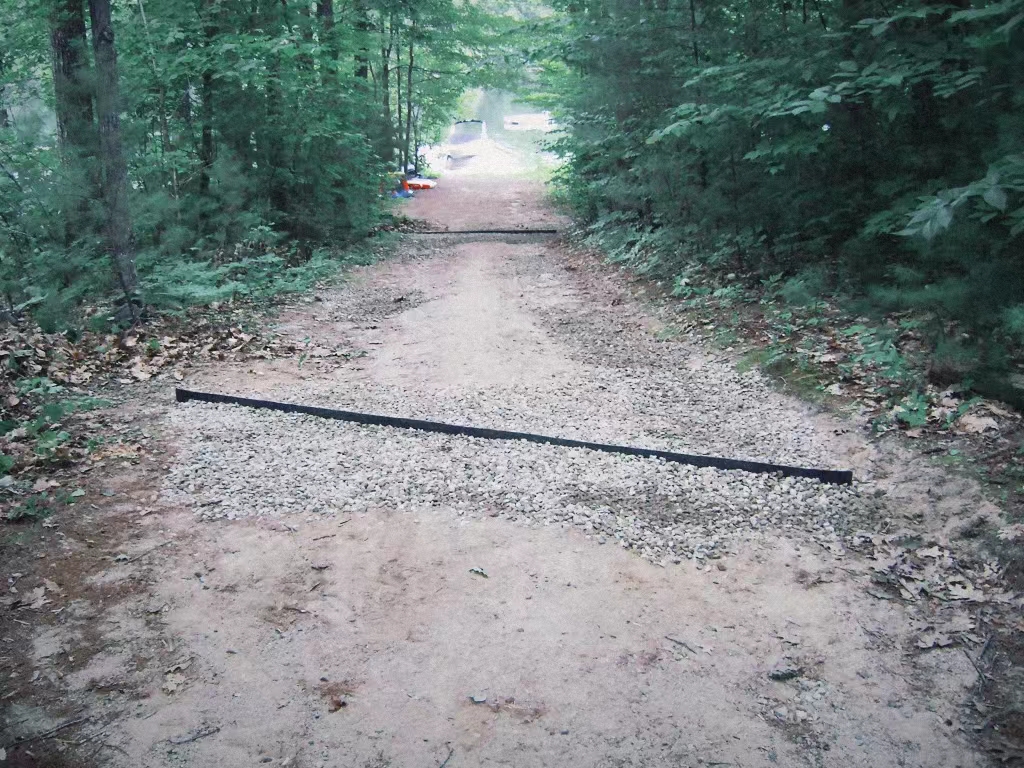
Examples of successful implementations of a conveyor belt water diverter include its use in national parks, where preserving the natural landscape while maintaining access roads is crucial, and in agricultural settings, where it helps in protecting access lanes from being washed out. These applications demonstrate the diverter’s role in not only preserving infrastructure but also in contributing to environmental conservation efforts by preventing sedimentation in nearby waterways.
Comparison with Other Water Diversion Methods
Rubber Razor Water Diverter
Overview
The rubber razor water diverter is a versatile and durable solution designed to manage water runoff on unpaved roads and driveways. Made from high-quality rubber, this type of diverter effectively channels water away from the road surface, reducing erosion and maintaining the integrity of the road.
Comparison with Conveyor Belt Water Diverter
When comparing the rubber razor water diverter with the conveyor belt water diverter, several key differences and similarities emerge. Both are highly effective at managing water flow and preventing erosion, but they differ in materials, installation processes, and durability.
- Materials: The rubber razor water diverter is typically made from new, high-quality rubber designed specifically for water diversion purposes. In contrast, the conveyor belt water diverter often utilizes recycled conveyor belts, making it a more environmentally friendly option.
- Durability: Both diverters offer excellent durability. However, the conveyor belt water diverter, being made from industrial-grade materials, may offer superior resistance to heavy traffic and harsh weather conditions.
- Installation: Installing a rubber razor water diverter is generally straightforward and can be done without heavy machinery. It involves laying the diverter across the desired area and securing it in place. The conveyor belt water diverter, on the other hand, often requires more preparation, including cutting and securing the belt to treated lumber and possibly using machinery to dig trenches for installation.
- Cost: The cost of a rubber razor water diverter can be higher due to the use of new materials. In contrast, the conveyor belt water diverter is usually more cost-effective, particularly when using recycled belts.
Water Bars for Gravel Driveway
Pros and Cons Compared to Conveyor Belt Water Diverters
Water bars are a traditional method for diverting water off gravel driveways and roads. These structures are built by creating a mound of soil or gravel across the road, angled to direct water flow off the surface.
Pros
- Simplicity: Water bars are relatively simple to construct using materials readily available on-site, such as gravel and soil.
- Cost: The cost is generally low, as it often involves repurposing existing materials without the need for specialized equipment.
Cons
- Maintenance: Water bars require regular maintenance to remain effective. Over time, they can become worn down by traffic and weather, necessitating frequent repairs.
- Durability: They are less durable than conveyor belt water diverters. Heavy traffic and severe weather conditions can quickly degrade a water bar, reducing its effectiveness.
- Effectiveness: While effective for small-scale water diversion, water bars may not handle large volumes of water as efficiently as a conveyor belt water diverter.
Comparison
- Materials: Conveyor belt water diverters use durable, recycled rubber materials, making them more robust compared to the soil and gravel used in water bars.
- Installation: Installing a water bar is easier and quicker but may not provide the long-term reliability of a conveyor belt water diverter.
- Maintenance: Conveyor belt water diverters require less frequent maintenance, making them a more sustainable option for long-term use.
Driveway Water Diverter
Other Options for Driveway Water Management
There are several other methods available for managing water runoff on driveways, each with its own set of benefits and drawbacks.
French Drains
French drains are a popular solution for managing water around driveways. They consist of a trench filled with gravel and a perforated pipe that redirects water away from the driveway.
- Pros: Highly effective at managing large volumes of water, long-lasting.
- Cons: More expensive to install, requires significant excavation and professional installation.
Surface Drains
Surface drains are installed at the edge of the driveway to capture and redirect water.
- Pros: Effective for managing runoff from paved driveways, relatively easy to install.
- Cons: Can become clogged with debris, requiring regular maintenance.
Permeable Pavers
Permeable pavers allow water to seep through the driveway surface, reducing runoff.
- Pros: Environmentally friendly, reduces water runoff.
- Cons: More expensive than traditional paving materials, may require professional installation.
Comparison with Conveyor Belt Water Diverter
- Effectiveness: Conveyor belt water diverters provide a straightforward, effective solution for unpaved driveways, especially those prone to significant erosion.
- Cost: Generally more affordable than French drains and permeable pavers, particularly when using recycled materials.
- Maintenance: Requires less maintenance than surface drains and water bars, offering a longer-lasting solution with minimal upkeep.
While there are various methods available for managing water runoff and preventing erosion on driveways, the conveyor belt water diverter stands out for its cost-effectiveness, durability, and low maintenance requirements. Whether you opt for recycled materials or a DIY approach, this solution offers a reliable way to protect your driveway from water damage and erosion.
Conveyor Belt Water Diverter: Installation Guide
Installing a conveyor belt water diverter is a straightforward process that requires some basic materials and tools. Proper installation ensures effective water diversion and prolongs the lifespan of both the diverter and the road. Here’s a step-by-step guide on constructing and installing a conveyor belt water diverter:
Materials and Tools Required:
- Conveyor belt material, cut to the required length and width.
- Treated lumber for anchoring the belt into the ground.
- Bolts, nuts, and washers to secure the conveyor belt to the lumber.
- Tools such as a drill, saw, hammer, and adjustable wrench.
Preparation:
- Measure the road or trail width to determine the length of the conveyor belt and lumber needed.
- Cut the conveyor belt to the desired length, considering extra width for anchoring.
Constructing the Diverter:
- Lay the cut conveyor belt flat on the ground.
- Place the treated lumber along the edges of the belt, leaving an adequate portion of the belt exposed for effective water diversion.
- Drill holes through the belt and lumber at intervals and secure them together using bolts, nuts, and washers.
Installation:
- Choose the installation site carefully, ideally at a point where water runoff is a known issue.
- Excavate a trench across the road or trail at a diagonal angle, ensuring it is deep enough to bury the lower part of the diverter.
- The trench should have a slight downward angle to facilitate water flow away from the road.
- Place the constructed diverter in the trench, with the exposed part of the conveyor belt facing upwards.
- Backfill the trench, compacting the soil around the diverter to secure it in place.
Considerations for Effective Water Diversion:
- Ensure the diverter is installed at a minimum angle of 30 degrees to the road to effectively divert water.
- Space multiple diverters at intervals based on the slope of the road and the volume of water runoff.
- The depth of the trench and the angle of installation are crucial for the diverter’s effectiveness. Adjust these based on specific site conditions.
Following these steps will result in a well-installed conveyor belt water diverter that effectively manages water flow, reducing erosion and maintaining the integrity of unpaved roads and trails. Regular inspection and minor adjustments may be required to ensure the diverter continues to function optimally over time.
Cost and Availability of the Conveyor Belt Water Diverter
The cost and availability of conveyor belt water diverters are influenced by several factors, including the source of materials, the size of the diverter, and the specific requirements of the installation site. Understanding these aspects can help in planning and budgeting for the implementation of these erosion control solutions.
Price Range:
- The cost of a conveyor belt water diverter can vary widely. Factors affecting price include the length and width of the conveyor belt material, the quality of the material (new vs. used), and additional components such as treated lumber and hardware for installation.
- Generally, using recycled or repurposed conveyor belt material can significantly reduce costs compared to purchasing new materials. Prices for used conveyor belts can be much lower, making this an economical choice for erosion control projects.
Factors Affecting Cost:
- Material Source: New conveyor belt materials are more expensive than used or repurposed belts. Many suppliers offer used conveyor belts that are still in good condition at a fraction of the cost of new materials.
- Size and Specifications: Larger and wider conveyor belts, which cover more area and require more material, will cost more. The specific requirements of the project, such as the need for belts resistant to certain environmental conditions, can also affect the price.
- Installation Requirements: The complexity of the installation can impact the overall cost. Sites that require extensive preparation or custom fitting may incur higher costs.
Sourcing Conveyor Belt Water Diverters:
- New Materials: Suppliers of industrial conveyor systems often sell new conveyor belt materials. While this option offers high-quality materials, it is also the most expensive.
- Used Materials: Many companies specialize in selling used conveyor belts that are ideal for water diversion projects. These suppliers often source belts from industries that no longer need them, offering a sustainable and cost-effective option.
- Local Quarries and Mines: Some local quarries and mines may have surplus or used conveyor belts available at low cost or even for free. It’s worth contacting these operations to inquire about available materials.
Finding Conveyor Belt Water Diverters for Sale:
- Online Marketplaces: Websites that specialize in industrial supplies or used materials often list conveyor belts. These platforms can connect buyers with sellers across regions, expanding the options for sourcing materials.
- Specialty Suppliers: Companies that focus on erosion control and environmental protection solutions may offer conveyor belt water diverters as part of their product lineup.
- Local Networking: Reaching out to local industries, agricultural operations, or construction companies can uncover sources of conveyor belts suitable for diversion projects.
The cost and availability of conveyor belt water diverters depend on a variety of factors, with options ranging from new, high-quality materials to repurposed belts that offer significant savings. By researching and exploring different sources, project managers can find the most cost-effective and suitable materials for their erosion control needs.
Maintenance and Longevity of the Conveyor Belt Water Diverter
The effectiveness and lifespan of a conveyor belt water diverter are directly influenced by proper maintenance and installation practices. While these diverters are designed for durability and long-term use, certain measures can ensure they continue to function efficiently over the years.
Maintenance Requirements:
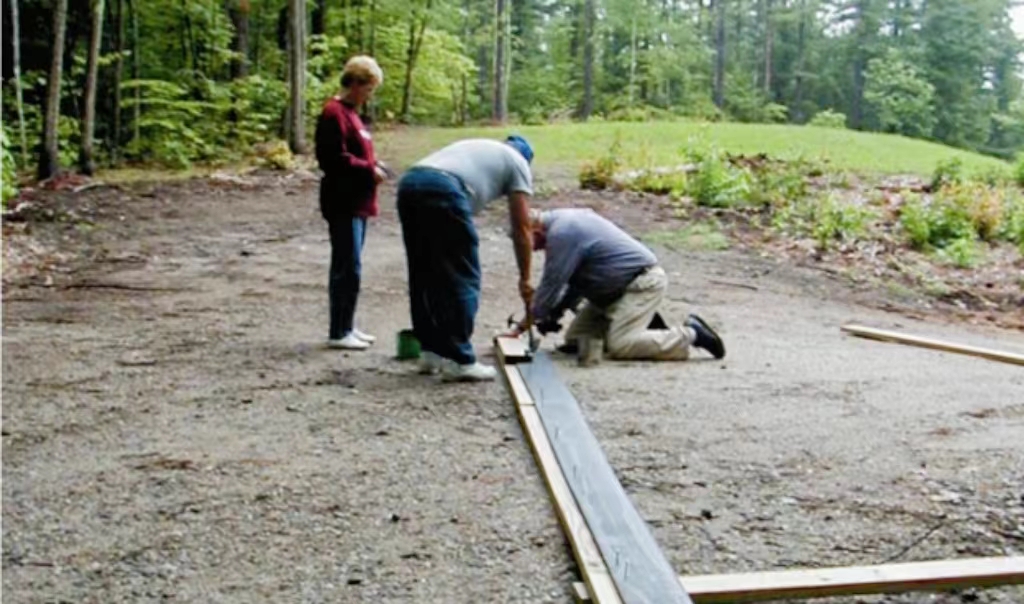
- Regular Inspections: Periodic checks are crucial for identifying wear and tear, sediment buildup, or any damage that might impede the diverter’s ability to channel water effectively. Inspections should be more frequent after heavy rainfall or snowmelt.
- Clearing Debris: Over time, debris such as leaves, branches, and sediment can accumulate around the diverter, reducing its effectiveness. Regular clearing of this debris ensures that water continues to flow smoothly off the road.
- Bolt Tightening: The bolts securing the conveyor belt to the anchoring lumber may loosen due to the vibration of passing traffic or natural settling. Checking and tightening these bolts during inspections will help maintain the structural integrity of the diverter.
- Belt and Lumber Condition: Exposure to the elements can cause the conveyor belt and treated lumber to wear over time. Monitoring their condition and replacing any severely worn or damaged parts is essential for maintaining performance.
Expected Lifespan:
- The lifespan of a conveyor belt water diverter can vary based on several factors, including the quality of the materials used, the volume and speed of traffic over the diverter, and the harshness of the environmental conditions. Generally, with proper maintenance, a conveyor belt water diverter can last several years before needing significant repairs or replacement.
- The durability of the conveyor belt material itself is a key factor in the diverter’s longevity. High-quality, industrial-grade conveyor belts designed for heavy use are more resistant to wear and can significantly extend the life of the diverter.
Maximizing Longevity:
- Quality Installation: Ensuring that the diverter is installed correctly from the start is crucial for its long-term effectiveness. This includes proper placement, securing, and angling of the diverter to optimize water flow and minimize damage.
- Material Selection: Choosing high-quality, durable materials for both the conveyor belt and the anchoring lumber can prevent premature wear. Opting for materials suited to the local climate and environmental conditions can also extend the diverter’s service life.
- Adaptive Maintenance: Being responsive to the specific challenges of the installation site, such as adjusting the diverter’s position or configuration based on observed water flow patterns or erosion, can help maintain its effectiveness over time.
A conveyor belt water diverter represents a sustainable and effective solution for controlling water flow and preventing erosion on unpaved roads. With proper maintenance and attention to detail during installation, these diverters can provide reliable service for many years, making them a valuable investment in road infrastructure and environmental conservation.
FAQs about Conveyor Belt Water Diverter
Conveyor belt protection devices are integral components designed to ensure the operational integrity and safety of a conveyor system. These devices help in preventing accidents, minimizing downtime, and safeguarding the conveyor belt from potential damage. Among the most critical conveyor belt protection devices are:
Emergency Stop Switches: These are strategically placed along the conveyor belt and allow operators to immediately halt the conveyor’s operations in case of an emergency. This rapid response capability is crucial for preventing accidents and mitigating damage.
Belt Misalignment Switches: Misalignment switches are designed to detect when the conveyor belt has deviated from its intended path. This deviation can lead to significant belt damage and inefficiency in operations. Once misalignment is detected, the system can either alert operators or automatically halt operations to prevent further damage.
Speed Monitors: These devices monitor the speed of the conveyor belt, ensuring it operates within the designated speed parameters. Any deviation from the set speed can indicate potential issues, such as mechanical failures or blockages, prompting immediate investigation and action.
Belt Rip Detectors: Rip detectors are essential for identifying tears or rips in the conveyor belt. Early detection of belt damage allows for prompt system shutdown, preventing further damage to the belt and reducing material spillage.
Zero Speed Switches: These switches are designed to detect the cessation of belt movement, indicating a potential system failure. By alerting operators to the stoppage, zero speed switches play a crucial role in preventing damage to the conveyor system and its components.
Conveyor belts are sophisticated systems designed for the efficient transport of materials across various sections of production, processing, or packaging facilities. The knowledge of conveyor belts encompasses understanding their design, operation, and maintenance to ensure they function optimally. Key aspects include:
Types of Conveyor Belts: There are several types of conveyor belts, including flat belts, modular belts, and cleated belts, each designed for specific applications and material handling requirements. The choice of belt depends on factors such as the nature of the material, the required speed, and the direction of transport.
Material and Design: Conveyor belts are made from various materials, including rubber, PVC, fabric, and metal, tailored to the application’s needs. The design considerations include belt width, thickness, tensile strength, and surface texture, all of which determine the belt’s durability and efficiency.
Maintenance Practices: Regular maintenance is crucial for the longevity and reliability of conveyor belts. This includes routine inspections for wear and tear, adjustments to ensure proper alignment, and timely replacement of damaged or worn parts. Proper maintenance helps in preventing breakdowns and minimizing operational disruptions.
Safety Measures: Safety is paramount in the operation of conveyor belts. This involves installing safety guards and emergency stop systems, training operators on safe practices, and adhering to regulatory standards to prevent accidents and injuries.
Understanding these fundamental aspects of conveyor belts is essential for anyone involved in their operation, maintenance, or management, ensuring that the conveyor system meets its performance and safety objectives.
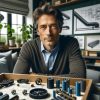
Jordan Smith, a seasoned professional with over 20 years of experience in the conveyor system industry. Jordan’s expertise lies in providing comprehensive solutions for conveyor rollers, belts, and accessories, catering to a wide range of industrial needs. From initial design and configuration to installation and meticulous troubleshooting, Jordan is adept at handling all aspects of conveyor system management. Whether you’re looking to upgrade your production line with efficient conveyor belts, require custom conveyor rollers for specific operations, or need expert advice on selecting the right conveyor accessories for your facility, Jordan is your reliable consultant. For any inquiries or assistance with conveyor system optimization, Jordan is available to share his wealth of knowledge and experience. Feel free to reach out at any time for professional guidance on all matters related to conveyor rollers, belts, and accessories.