Innovative Tools to Cut Conveyor Belt: A Comprehensive Review
Conveyor belts are indispensable components across various industries, serving as the backbone for material handling in manufacturing, mining, agriculture, and logistics. These belts facilitate the efficient transport of goods and materials, significantly enhancing productivity and operational flow. However, the dynamic nature of industrial demands often necessitates the modification of these belts to suit specific operational needs or to maintain optimal functionality. This is where the skill to cut conveyor belt comes into play, a critical maintenance task that ensures conveyor systems remain efficient, reliable, and tailored to the unique requirements of each application. Whether it’s adjusting the length for a better fit, removing worn sections to prevent operational failures, or customizing the belt for a specific task, the ability to precisely cut conveyor belts is essential for maintaining the high efficiency and customization that modern industries demand. This process not only extends the life of the conveyor system but also significantly contributes to the smooth operation of the industry’s material handling capabilities.
Reasons for Cut Conveyor Belt
The necessity to cut conveyor belt arises from various operational and maintenance requirements within industries that rely heavily on conveyor systems. Understanding these reasons can help in optimizing the performance and longevity of conveyor belts.
Wear and Tear: Addressing Efficiency and Error Reduction
Over time, conveyor belts can suffer from wear and tear due to continuous use, leading to decreased efficiency and increased error rates in material handling processes. Specific examples include:
- Surface Erosion: Continuous contact with materials can erode the surface of the belt, reducing its grip and leading to slippage.
- Edge Fraying: The edges of the belt may begin to fray due to abrasion against the conveyor structure, causing material spillage and operational inefficiencies.
- Cracking and Splitting: Exposure to harsh environmental conditions can cause the belt to crack or split, compromising its structural integrity and necessitating a cut to remove the damaged section.
Incorrect Initial Cut: Correcting Manufacturing Imperfections
Sometimes, conveyor belts may not be cut accurately during manufacturing, leading to issues that can affect the entire conveyor system. Examples of such imperfections include:
- Uneven Edges: Belts with uneven edges can cause misalignment, leading to premature wear and tear of the conveyor components.
- Incorrect Length: A belt that is too long or too short for the conveyor system can result in operational failures, requiring adjustments through cutting.
- Improper Width: Belts not cut to the precise width needed can lead to material handling inefficiencies and potential safety hazards.
Excess Width: Adjusting Belt Width for Machine Efficiency
Adjusting the width of a conveyor belt is often necessary to match the specific requirements of the machinery or the materials being transported. Situations that may require such adjustments include:
- Machine Retrofitting: When machinery is updated or retrofitted, the existing conveyor belt may need to be cut to fit the new specifications.
- Material Handling Changes: Changes in the type or size of materials being transported may necessitate a narrower belt to prevent spillage or improve containment.
- System Efficiency Optimization: Narrowing the belt can reduce energy consumption by decreasing the load on the conveyor’s motor, thereby enhancing overall system efficiency.
Material Savings: Reusing Excess Material for Cost Efficiency
Cutting conveyor belts can also be driven by the desire to save materials and reduce costs. This can be achieved through:
- Repurposing Excess Length: Excess belt material cut from longer belts can be repurposed for smaller conveyor systems or for repairs, reducing waste and saving costs.
- Customization for Specific Uses: Cutting belts to specific lengths or widths can optimize material use, ensuring that only what is necessary is utilized, thereby minimizing waste.
- Preventative Maintenance: Proactively cutting and removing worn or damaged sections of a belt before they fail can save on emergency repair costs and downtime, contributing to overall material savings.
The decision to cut conveyor belt is influenced by a variety of factors, including wear and tear, manufacturing imperfections, the need for adjustments to improve machine efficiency, and strategies for material savings. Addressing these issues through precise cutting can enhance the operational efficiency, safety, and cost-effectiveness of conveyor systems.
Preparing for Cut Conveyor Belt
Before undertaking the task to cut conveyor belt, it’s crucial to prepare adequately to ensure the process is safe, accurate, and effective. This preparation involves prioritizing safety and ensuring the measurements are precise for the longevity of the belt.
Safety First: Emphasizing the Importance of Turning Off Power and Removing Machinery
Safety cannot be overstated when preparing to cut conveyor belt. There are several key steps to ensure a safe working environment:
- Power Shutdown: Always turn off the power supply to the conveyor system to prevent accidental activation while working.
- Lockout/Tagout (LOTO) Procedures: Apply lockout/tagout devices to the conveyor’s power sources to ensure that the system cannot be re-energized without your knowledge.
- Clear the Area: Remove any machinery or obstacles that could pose a risk during the cutting process. This ensures you have ample space to work without constraints.
- Tool Inspection: Before starting, inspect all tools for damage or wear to ensure they are safe to use. Faulty tools can lead to accidents.
- Wear Appropriate PPE: Personal Protective Equipment (PPE) such as gloves, safety glasses, and hearing protection should be worn at all times to protect against potential hazards.
- Inform Others: Make sure that all personnel in the area are aware of the maintenance activity. This prevents accidental activation of the conveyor or any interference that could compromise safety.
Measuring and Squaring: The Critical Step of Accurate Measurement and Squaring for Belt Longevity
Accurate measurement and squaring are foundational to the success of the task to cut conveyor belt. Here are specific methods to ensure precision:
- Use a Measuring Tape: Start by using a measuring tape to determine the length of the cut. Measure twice to confirm accuracy before marking.
- Marking the Cut Line: Use a chalk line or washable marker to mark where the belt will be cut. This visual guide will help ensure the cut is straight.
- Squaring the Belt: Squaring is essential for ensuring the belt tracks correctly once installed. Use a carpenter’s square or a framing square to mark a perpendicular line across the belt at the measured point. For longer belts, a laser level can project a straight line across the belt’s surface, which can then be marked for cutting.
- Centerline Method for Longitudinal Cuts: If you need to cut the belt lengthwise, finding the centerline is crucial. Measure equal distances from both edges at several points along the belt, then connect these points using a straight edge. This ensures the belt remains symmetrical and balanced.
- Double-Check Measurements: Before making any cuts, review all measurements and markings to ensure they are correct. Adjustments are much easier to make before cutting begins.
By meticulously preparing to cut conveyor belt, focusing on safety and precision, you can ensure the integrity of the belt is maintained, thereby extending its service life and optimizing the efficiency of the conveyor system. This preparation phase is as critical as the cutting itself, setting the stage for a successful modification or repair of the conveyor belt.
Tools for Cut Conveyor Belt
Selecting the right tools to cut conveyor belt is crucial for achieving a clean, precise cut while ensuring the safety of the operator and the integrity of the belt. Here’s a detailed look at the tools available for this task, along with their specific uses and considerations.
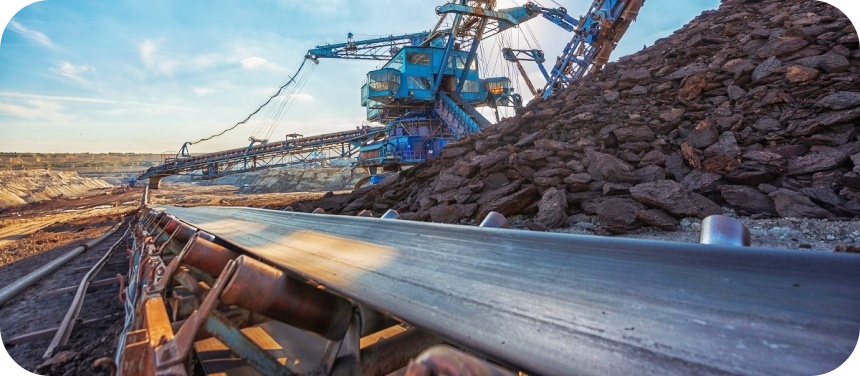
Utility Knife & Rubber Conveyor Belt Cutter: Basic Tools for Simple Cuts
For straightforward, less demanding cuts on rubber conveyor belts, basic tools like a utility knife or a specialized rubber conveyor belt cutter are often sufficient. These tools are ideal for:
- Material: Soft, non-reinforced rubber belts.
- Precision: Suitable for small adjustments or trimming.
- Cost: Economical options for infrequent or light-duty use.
Despite their simplicity, achieving a straight, clean cut requires patience and steady hands. Multiple passes might be necessary to cut through the belt entirely.
Electric Belt Cutter: For Efficient and Quick Cutting
Electric belt cutters are designed for speed and efficiency, making them perfect for cutting through various conveyor belt materials, including thicker and more durable belts. Key features include:
- Material: Versatile, capable of cutting through reinforced and thick belts.
- Efficiency: Reduces the time and effort required to cut.
- Safety: Often equipped with safety features to minimize the risk of accidents.
These cutters are an investment, ideal for operations where conveyor belts need to be cut regularly or in bulk.
Flexco Belt Cutter: Highlighting Its Features and for Different Belt Types
Flexco belt cutters are renowned for their durability and precision. They are engineered to handle a wide range of conveyor belt materials and thicknesses. Here’s a summary of their features:
Feature | Description |
---|---|
Material Compatibility | Can cut through both rubber and steel-reinforced conveyor belts. |
Precision | Designed for accurate, straight cuts. |
Safety | Built-in safety features to protect the operator. |
Price Range | Varies based on model and capabilities, generally higher due to quality and brand reputation. |
Cutting with a Grinder & Circular Saw: Discussing the Feasibility and Safety
Grinders and circular saws offer the power needed to cut through the toughest conveyor belts, including steel-reinforced types. However, their use requires careful consideration of safety and feasibility:
Tool | Material Suitability | Safety Considerations |
---|---|---|
Grinder | Steel-reinforced belts | High; requires protective gear and careful handling to avoid sparks and debris. |
Circular Saw | Thick, rubber, and lightly reinforced belts | Moderate to high; demands expertise to manage kickback and ensure straight cuts. |
Both tools necessitate the use of personal protective equipment (PPE) and should only be operated by individuals experienced with their use. They offer a powerful solution for cutting conveyor belts but come with a higher risk factor that must be managed through proper safety protocols and training.
The choice of tool to cut conveyor belt depends on the material of the belt, the precision required, and the frequency of use. Each tool has its specific applications, benefits, and safety considerations, making it essential to select the right one for your needs to ensure a successful and safe cutting process.
Special Considerations for Steel-Reinforced Cut Conveyor Belts
When planning to cut conveyor belt materials, especially those reinforced with steel cords, there are unique challenges and considerations to keep in mind. These belts are designed for high strength and durability, making them more difficult to cut than their fabric-reinforced or rubber-only counterparts.
Challenges: Addressing the Difficulty of Cutting Through Steel Cords
The primary challenge in cutting steel-reinforced conveyor belts lies in the steel cords themselves. These cords are made from high-tensile steel, designed to provide significant strength and resistance to stretching, which is essential for the belt’s operational integrity. The reasons for the difficulty include:
- High Tensile Strength: The steel cords have a high resistance to being cut, requiring tools with significant cutting power.
- Tool Wear: The hardness of the steel can cause rapid wear on cutting tools, necessitating frequent replacements or the use of specialized blades.
- Safety Risks: Cutting through steel-reinforced materials can generate sparks and sharp edges, posing safety risks to the operator.
- Precision: Maintaining a straight and clean cut is more challenging due to the resistance offered by the steel cords.
- Vibration and Noise: The process can generate considerable noise and vibration, requiring additional safety measures and potentially affecting precision.
Recommended Tools: Focusing on the Best Tools for the Job
Given these challenges, selecting the right tools to cut conveyor belt materials that are steel-reinforced is crucial. Specialized mechanical belt cutting machines are often recommended for several reasons:
- Power: These machines are designed to deliver the necessary force to cut through steel cords without requiring excessive manual effort.
- Durability: Equipped with blades or cutting edges specifically made to withstand the hardness of steel, these machines can perform numerous cuts before needing maintenance.
- Safety Features: Many mechanical belt cutters come with built-in safety features, such as guards and emergency stops, to protect the operator from the potential hazards of cutting steel-reinforced belts.
- Precision: They often include guides or systems to ensure the cut is straight and accurate, which is critical for the proper alignment and operation of the conveyor belt after cutting.
- Efficiency: Designed for this specific task, these machines can significantly reduce the time and labor required to cut through steel-reinforced conveyor belts, making them a cost-effective solution for operations that frequently need to perform this task.
When preparing to cut conveyor belt materials that include steel reinforcement, it’s essential to understand the unique challenges posed by these durable components. By choosing specialized mechanical belt cutting machines, operations can address these challenges effectively, ensuring safety, precision, and efficiency in the maintenance and customization of their conveyor systems.
Step-by-Step Guide for Cut Conveyor Belt
Cutting a conveyor belt to size is a necessary skill for maintaining the efficiency and functionality of conveyor systems. Here’s a detailed guide on how to cut conveyor belt material, ensuring accuracy, safety, and the integrity of the belt.
Measure and Mark: Ensuring Accuracy from the Start
The first step in the process to cut conveyor belt material involves precise measurement and marking:
- Measure the Length: Use a measuring tape to determine the exact length where the belt needs to be cut. Double-check the measurement to ensure accuracy.
- Mark the Cut Line: Once you have the measurement, mark the cut line on the belt using a chalk line or a washable marker. For a straight cut, use a straight edge or a carpenter’s square as a guide when drawing the line.
Choose the Right Tool: Based on Belt Material and the Cut’s Requirements
Selecting the appropriate tool is crucial for a successful cut:
- For Rubber Belts: A sharp utility knife or a specialized rubber conveyor belt cutter might suffice.
- For Steel-Reinforced Belts: Consider using an electric belt cutter, angle grinder, or a Flexco belt cutter, which are designed to handle the toughness of steel cords.
Safety Measures: Wearing Appropriate PPE and Ensuring a Safe Environment
Before starting the cutting process, it’s essential to prioritize safety:
- Personal Protective Equipment (PPE): Wear safety glasses, durable gloves, and hearing protection to safeguard against potential hazards.
- Secure the Belt: Ensure the conveyor belt is securely fixed in place to prevent it from moving while you’re cutting.
- Check Your Surroundings: Make sure the area is clear of any unnecessary tools or objects that could interfere with the cutting process.
Cutting Process: Detailed Steps for Using Selected Tools Effectively
With the right preparations in place, proceed to cut the conveyor belt:
- Start the Cut: If using a utility knife, make a shallow initial score along the marked line. This helps guide subsequent cuts. For powered tools, begin at one end of the marked line and slowly follow it through to the other end.
- Apply Steady Pressure: Maintain steady pressure and speed to ensure a clean cut. For manual tools, multiple passes may be necessary to cut through the belt completely.
- Monitor Tool Condition: Regularly check the condition of your cutting tool. If using a blade, replace it as soon as it becomes dull to maintain efficiency and safety.
- Final Inspection: Once the cut is complete, inspect the edge for any irregularities. If necessary, use a file or sandpaper to smooth out any rough edges, especially for steel-reinforced belts where sharp steel wires might protrude.
Following this step-by-step guide to cut conveyor belt material will help ensure that the task is completed accurately and safely, maintaining the operational integrity of your conveyor system. Remember, the key to a successful cut is preparation, the right tools, and attention to safety.
Tips for a Straight Cut
Achieving a perfectly straight cut when you need to cut conveyor belt material is crucial for the belt’s performance and longevity. Here are techniques and tools that can help ensure precision and maintain belt integrity.
Techniques and Tools for a Perfectly Straight Cut
- Use a Chalk Line for Long Cuts: A chalk line is an effective tool for marking long, straight lines across the width of the conveyor belt. Snap the line against the belt surface to leave a straight, visible mark as your guide.
- Straight Edge Guide: Employing a long, straight edge or a carpenter’s square can help guide your cutting tool along the marked line, ensuring the cut remains straight throughout the process.
- Laser Level: For the utmost precision, a laser level can project a perfectly straight line across the belt’s surface. This method is particularly useful for long belts where maintaining a straight line by eye can be challenging.
Importance of Squaring and Centerline Methods for Belt Integrity
The integrity of a conveyor belt is paramount to its efficient operation. Here are five reasons why using squaring and centerline methods is essential when you cut conveyor belt material:
- Ensures Proper Alignment: A straight cut is vital for the belt to align correctly on the conveyor system. Misalignment can lead to uneven wear, increased stress on the conveyor structure, and potential system failures.
- Prevents Tracking Issues: A conveyor belt that isn’t cut straight may start to track off to one side, causing it to rub against the conveyor frame or structure, leading to damage to both the belt and the system.
- Maximizes Belt Life: Even and straight cuts reduce the risk of edge fraying and material fatigue, extending the operational life of the belt.
- Improves Load Distribution: A straight cut ensures that the load is evenly distributed across the belt width, preventing premature wear and tear in localized areas and enhancing the efficiency of material transport.
- Facilitates Easier Splicing: When joining two ends of a conveyor belt or repairing a section, a straight cut is crucial for a successful splice. Irregular cuts can make splicing difficult, compromising the strength and integrity of the belt at the splice point.
Achieving a straight cut when you cut conveyor belt material is not just about aesthetics; it’s about maintaining the belt’s functionality, efficiency, and longevity. Employing the right techniques and tools for marking and cutting, along with understanding the importance of squaring and centerline methods, are fundamental steps in ensuring the integrity and performance of your conveyor system.
Inquire About Conveyor Belt Warranty and Support.
Maintenance and Replacement for Cut Conveyor Belt
Proper maintenance and timely decision-making on whether to cut conveyor belt for repair or opt for a replacement are crucial for the longevity and efficiency of conveyor systems. Understanding when each action is appropriate can save time and maintain the quality of your operation.
When to Consider Cutting for Repair vs. Opting for a Replacement Belt
Deciding between cutting a conveyor belt for repair or replacing it entirely depends on several factors:
- Extent of Damage: Minor damages such as small tears or wear can often be repaired by cutting the damaged section and splicing the belt. However, extensive damage across large areas or throughout the belt’s structure usually necessitates a complete replacement.
- Age and Condition of the Belt: If the conveyor belt is relatively new and in good condition, except for the damaged area, cutting and repairing may be the most cost-effective solution. For older belts showing signs of significant wear, replacement might be more prudent to prevent future failures.
- Operational Impact: Consider the impact on operations. If a repair can be done quickly and effectively without significantly disrupting operations, it may be preferred. However, if the belt’s integrity is compromised, replacing it might be necessary to avoid operational downtime in the future.
- Cost Considerations: Evaluate the cost of repair versus replacement. While cutting and repairing a belt may seem less expensive upfront, the long-term costs of potential future failures and additional repairs should also be considered.
Introduction to Replacement Conveyor Belts as a Time-Saving and Quality-Maintaining Alternative
Replacement conveyor belts offer a time-saving and quality-maintaining alternative to repairs, especially when the belt’s integrity is compromised. Here are key considerations for opting for a replacement:
- Improved Technology: New conveyor belts often incorporate improved materials and technology that can enhance the efficiency and longevity of your conveyor system.
- Warranty and Support: Replacement belts typically come with a manufacturer’s warranty and support, offering peace of mind and protection against future issues.
- Operational Efficiency: A new belt can restore your conveyor system to its optimal operational efficiency, reducing energy consumption and maintenance costs.
- Customization Opportunities: Opting for a replacement provides an opportunity to reassess the needs of your operation and select a belt that is better suited to your current requirements, whether it’s a different material, width, or design.
- Preventative Maintenance: Replacing an aging or damaged belt before it fails can prevent unexpected downtime, ensuring continuous operation and productivity.
The decision to cut conveyor belt for repair or to replace it entirely is a critical aspect of conveyor system maintenance. Assessing the condition of the belt, the extent of the damage, operational impacts, and cost considerations will guide this decision. While repairs can be effective for minor issues, replacement conveyor belts offer a fresh start, potentially with improved features and efficiency that can benefit your operation in the long run.
FAQs About Cut Conveyor Belt
The best way to cut a conveyor belt involves a combination of preparation, precise measurement, and the use of appropriate cutting tools. Initially, ensure the conveyor belt is stationary and safely secured to prevent any movement during the cutting process. The key to a successful cut is accurate measurement and marking of the area to be cut, ensuring that the cut will be straight and fit the intended use. Utilize a straight edge or a chalk line to mark the cut line clearly.
For the cutting itself, the choice of tool depends on the belt’s material. For rubber or fabric belts, a sharp utility knife or a specialized conveyor belt cutter can be effective. These tools allow for a controlled and clean cut. It’s crucial to make several gentle passes with the knife instead of trying to cut through in one go, which can lead to uneven edges or personal injury.
Safety cannot be overstated; always wear appropriate personal protective equipment (PPE), including gloves and eye protection, to safeguard against accidents. In summary, the best way to cut a conveyor belt is through careful preparation, accurate measurement, and the cautious use of cutting tools, all while prioritizing safety.
The best tool for cutting conveyor belts depends largely on the type of belt material you’re working with. For standard rubber and fabric conveyor belts, a sharp utility knife or a professional-grade conveyor belt cutter is often sufficient. These tools offer precision and are relatively easy to control, making them suitable for most conveyor belt materials.
For more durable materials, such as steel-reinforced conveyor belts, more robust tools like electric belt cutters or angle grinders equipped with a cutting disc are recommended. Electric belt cutters provide a powerful and efficient way to cut through tough materials, ensuring a clean cut with minimal effort. Angle grinders, while effective, require a steady hand and appropriate safety measures due to their power and the potential for generating sparks.
Regardless of the tool chosen, ensuring it is well-maintained and the blade is sharp is crucial for achieving a clean, straight cut. Dull blades can lead to jagged cuts, potential damage to the belt, and increased risk of injury. Always prioritize safety by using the tool according to the manufacturer’s instructions and wearing suitable PPE.
Cutting a steel cord conveyor belt requires tools capable of handling its reinforced structure. The most effective tools for this task are high-powered angle grinders with a suitable cutting disc, electric belt cutters designed for heavy-duty materials, or specialized mechanical belt-cutting tools. These tools can efficiently slice through the steel cords without causing damage to the remaining belt structure.
Before cutting, it’s essential to accurately measure and mark the cutting line, ensuring the cut will be straight and align with your requirements. Using a chalk line or a long straight edge can help in marking a precise line. When cutting, it’s crucial to wear appropriate PPE, including gloves, eye protection, and ear protection, due to the high noise levels and potential for flying debris.
Given the toughness of steel cord conveyor belts, applying steady and controlled pressure during the cut is important. Rushing the process can lead to uneven cuts or damage to the tool. After making the initial cut, inspect the edges for any fraying or steel wires that may need trimming or smoothing to ensure a clean finish.
Measuring and cutting a conveyor belt accurately is crucial for the belt’s proper installation and operation. Start by determining the length and width required for your specific application. Use a measuring tape to measure the belt length needed, marking the start and end points directly on the belt with a chalk or washable marker. For the width, ensure that the measurement is consistent along the length of the cut to maintain the belt’s integrity and functionality.
To ensure a straight cut, use a long straight edge or a chalk line to mark the cutting line across the belt. The straight edge can guide your cutting tool and ensure the cut remains aligned. For the actual cutting process, select a tool that matches the belt material, as discussed in previous questions.
When cutting, proceed slowly and with control, especially if using a utility knife or similar tool, to prevent deviation from the marked line. For thicker or reinforced belts, using an electric cutter or angle grinder may require multiple passes to complete the cut without compromising the belt’s structure or safety.
In all cases, double-check measurements before cutting, as mistakes can lead to material waste or operational issues. Proper measurement and cutting techniques, combined with the right tools, ensure a clean, straight cut that maintains the conveyor belt’s integrity and functionality.
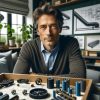
Jordan Smith, a seasoned professional with over 20 years of experience in the conveyor system industry. Jordan’s expertise lies in providing comprehensive solutions for conveyor rollers, belts, and accessories, catering to a wide range of industrial needs. From initial design and configuration to installation and meticulous troubleshooting, Jordan is adept at handling all aspects of conveyor system management. Whether you’re looking to upgrade your production line with efficient conveyor belts, require custom conveyor rollers for specific operations, or need expert advice on selecting the right conveyor accessories for your facility, Jordan is your reliable consultant. For any inquiries or assistance with conveyor system optimization, Jordan is available to share his wealth of knowledge and experience. Feel free to reach out at any time for professional guidance on all matters related to conveyor rollers, belts, and accessories.