Conveyor Belt Tracking Sensor Solutions for Efficient Automation
In the realm of material handling and industrial operations, conveyor belt tracking theory plays a pivotal role in ensuring the efficiency and safety of conveyor systems. Proper tracking involves aligning the conveyor belt correctly on the pulleys and rollers to prevent it from drifting or misaligning, which can lead to a host of operational issues, including premature wear, product spillage, and potential damage to the conveyor infrastructure. The introduction of the conveyor belt tracking sensor has revolutionized this aspect of conveyor maintenance, offering a high-tech solution to an age-old problem. These sensors are instrumental in detecting even slight deviations in the belt’s path, enabling immediate corrections and preventing the belt misalignment that can disrupt production and pose safety risks. Their role underscores a critical advancement in maintaining optimal functionality and prolonging the lifespan of conveyor systems.
The Role of Conveyor Belt Tracking Sensor
Conveyor belt tracking sensors are pivotal components in the management and operation of conveyor systems, especially those handling abrasive materials like gravel. Electro-sensors belt alignment sensors, mounted along conveyor belts, provide precise tracking and system feedback, optimizing industrial systems by correcting belt misalignment and preventing drift. These sensors are designed to ensure that the conveyor belt remains aligned with the conveyor’s intended path, preventing it from drifting off course. This alignment is crucial for the smooth operation of conveyor systems, as it directly impacts both the efficiency and the longevity of the conveyor belt. By continuously monitoring the position of the conveyor belt, these sensors can instantly detect any deviation from its intended path and initiate corrective measures to realign the belt. This automated adjustment process is vital for maintaining uninterrupted operation and optimal performance of conveyor systems across various industries.
Benefits of Using Conveyor Belt Tracking Sensors
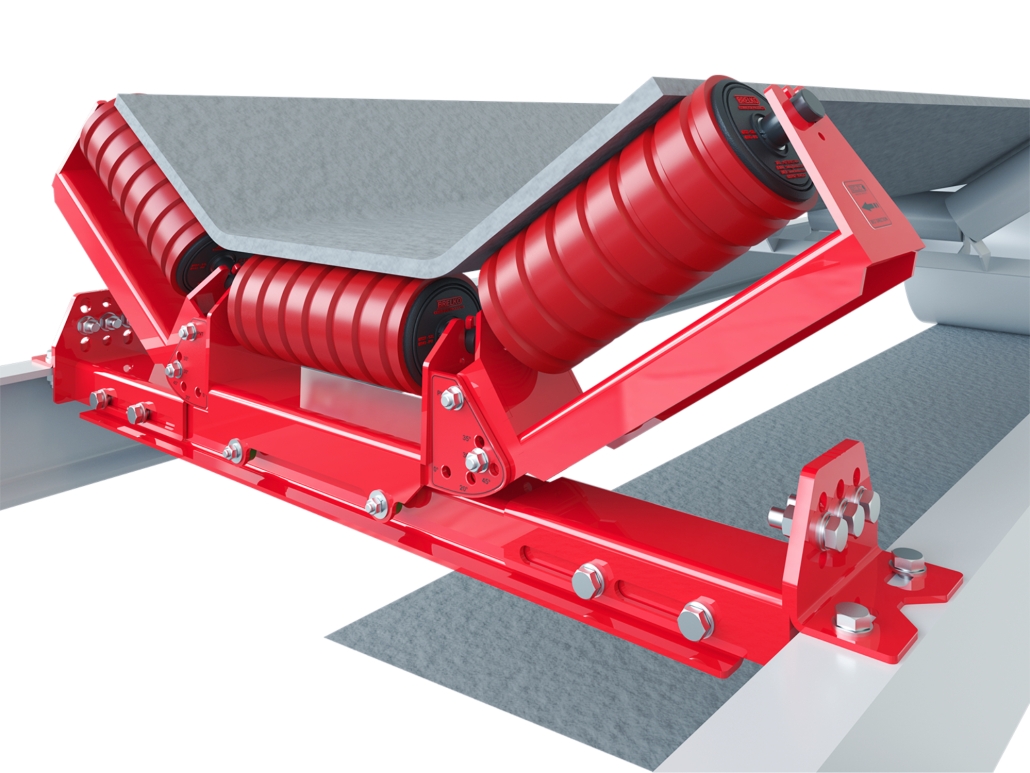
- Reduced Downtime: Conveyor belt tracking sensors significantly decrease the likelihood of operational halts caused by belt misalignment. By ensuring continuous, correct alignment, these sensors help maintain steady production flow, minimizing costly downtime.
- Increased Safety: Misaligned conveyor belts can lead to hazardous situations, including material spillage and increased risk of accidents for personnel working near the conveyor. Tracking sensors mitigate these risks by maintaining proper belt alignment, enhancing workplace safety.
- Improved Material Handling Efficiency: Properly aligned belts ensure that materials are transported efficiently along the conveyor path, reducing instances of spillage or accumulation that can disrupt the material flow and impact overall productivity.
- Extended Belt Life: Frequent misalignments can cause uneven wear on the conveyor belt and the structural components of the conveyor system. Tracking sensors help prolong the life of the belt by preventing such uneven wear, thereby saving on replacement and repair costs.
- Enhanced Product Quality: By preventing spillage and ensuring consistent material handling, conveyor belt tracking sensors contribute to maintaining the quality of the materials being transported, which is particularly important in sensitive applications.
- Energy Savings: A well-aligned conveyor belt operates more smoothly and requires less energy to move materials. This efficiency translates into energy savings, reducing the overall operational costs of the conveyor system.
- Ease of Maintenance: With the implementation of conveyor belt tracking sensors, the need for manual adjustments is significantly reduced. This automation allows maintenance teams to focus on other critical aspects of the conveyor system, streamlining maintenance procedures and reducing labor costs.
Incorporating conveyor belt tracking sensors into gravel conveyor belt systems is a strategic move that enhances the operational efficiency, safety, and cost-effectiveness of these systems. By ensuring continuous, proper alignment, these sensors play a crucial role in optimizing the performance and extending the lifespan of conveyor systems.
Types of Conveyor Belt Tracking Sensor
The integration of conveyor belt tracking sensors into conveyor systems is a critical measure for ensuring the operational efficiency and longevity of the belt. These sensors are designed to address various aspects of belt tracking and alignment, significantly impacting the performance of conveyor systems. Below, we delve into the specifics of different types of conveyor belt tracking sensors, emphasizing their importance and functionality.
Conveyor Belt Tracking Sensor Replacement
Timely replacement of conveyor belt tracking sensors is crucial for several reasons:
- Accuracy Maintenance: Over time, sensors can degrade, losing their accuracy. Regular replacement ensures the system remains precise in tracking the belt’s position.
- Preventing Downtime: Faulty sensors can lead to misalignment issues, causing unexpected downtime. Proactive sensor replacement helps avoid such disruptions.
- Reducing Wear and Tear: Correctly aligned belts experience less wear, extending the belt’s life. Effective sensors play a significant role in this alignment.
- Enhancing Safety: Misaligned belts can pose safety risks. Timely sensor replacement minimizes these risks by ensuring proper belt tracking.
- Operational Efficiency: Accurate sensors contribute to the smooth operation of the conveyor, improving overall efficiency.
- Cost Savings: Preventing misalignment can save costs related to conveyor belt damage, product loss, and extensive repairs.
- System Longevity: Regular sensor maintenance and replacement contribute to the longer lifespan of the conveyor system as a whole.
Conveyor Belt Tracking Sensor Location
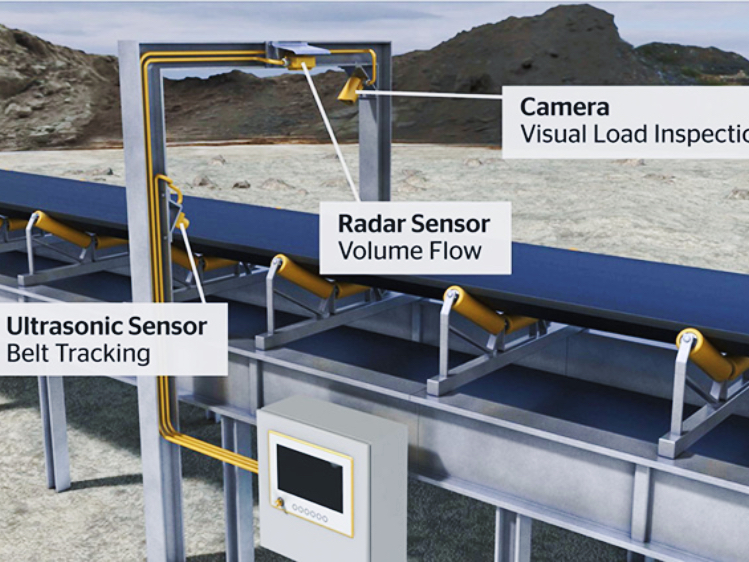
Optimal placement of conveyor belt tracking sensors is key to their effectiveness:
- Near the Tail Pulley: Sensors placed close to the tail pulley can detect misalignment early, allowing for prompt correction.
- Along the Edges: Sensors positioned along the belt edges are effective in monitoring side-to-side movement and alignment.
- At Strategic Points: Placement at various strategic points along the conveyor ensures comprehensive monitoring of the belt’s path.
- Return Side: Installing sensors on the return side helps in detecting misalignment issues that might not be visible on the carrying side.
- Load Zones: Sensors near load zones can ensure the belt remains aligned under varying load conditions.
Belt Alignment Sensor
Belt alignment sensors are specifically designed to maintain the conveyor belt’s proper path:
- Detection Capability: These sensors can detect slight deviations from the belt’s intended path, triggering corrective measures.
- Versatility: Suitable for various belt widths and speeds, ensuring broad applicability.
- Immediate Response: They provide real-time feedback, allowing for instant adjustments.
- Durability: Built to withstand harsh conditions, ensuring long-term reliability.
- Integration: Easily integrated into existing control systems for seamless operation.
- Customization: Available in various configurations to meet specific conveyor requirements.
- Preventative Maintenance: Help in identifying potential issues before they escalate into major problems.
Conveyor Belt Misalignment Sensor
Conveyor belt misalignment sensors specifically address belt drift:
- Sensitive Detection: Highly sensitive to belt position changes, ensuring early detection of misalignment.
- Automated Correction: Can trigger automated adjustments to realign the belt, minimizing manual intervention.
- Continuous Monitoring: Offer 24/7 monitoring of belt alignment, enhancing operational reliability.
- Compatibility: Work with a range of conveyor designs and belt types.
- Easy Installation: Designed for straightforward installation and integration into existing systems.
- Adjustment Precision: Allow for precise adjustments to the conveyor’s tracking mechanisms.
- Data Collection: Capable of collecting data for analysis, helping to predict and prevent future alignment issues.
Edge Detection Sensors
Edge detection sensors are designed to monitor the position of the conveyor belt edges to prevent the belt from drifting off course. These sensors are crucial for:
- Precision: They provide high accuracy in detecting the belt’s edge position.
- Adaptability: Capable of working with various belt materials and colors.
- Real-time Alerts: Offer immediate feedback when the belt begins to drift, allowing for quick adjustments.
- Durability: Constructed to withstand harsh environments and continuous operation.
RFID Tracking Sensors
RFID (Radio Frequency Identification) tracking sensors utilize RFID tags placed along the conveyor belt to monitor its position and track its movement. These sensors offer:
- Comprehensive Monitoring: Allows for tracking the belt’s position along its entire length.
- Data Collection: Gathers extensive data on belt movement and alignment for analysis and predictive maintenance.
- Integration: Easily integrates with existing RFID systems for inventory and process management.
- Efficiency: Enhances operational efficiency by ensuring optimal belt alignment.
Ultrasonic Sensors
Ultrasonic sensors use sound waves to detect the position of the conveyor belt and any potential misalignment. They are characterized by:
- Versatile Detection: Capable of detecting a wide range of materials and surface types.
- Distance Measurement: Can measure the distance to the belt edges for precise alignment.
- Environmentally Robust: Effective in noisy, dusty, and humid environments.
- Adjustable Range: The detection range can be adjusted to suit different conveyor setups.
Each type of conveyor belt tracking sensor plays a vital role in maintaining the efficiency, safety, and longevity of conveyor systems. By ensuring timely sensor replacement, optimal sensor placement, and utilizing specific sensors for alignment and misalignment, conveyor systems can operate smoothly, reducing downtime and maintenance costs.
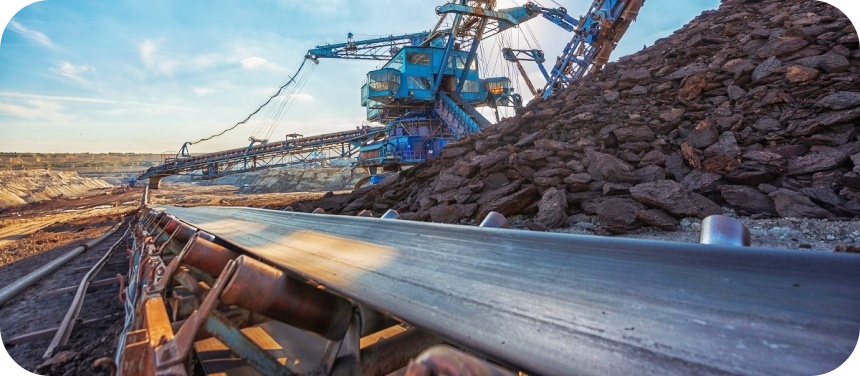
Advanced Conveyor Belt Tracking Sensor Solutions
The integration of advanced tracking solutions with conveyor belt tracking sensors represents a significant leap forward in conveyor belt technology. These systems ensure precise alignment and efficient operation of conveyor belts, minimizing downtime and enhancing productivity. Below, we delve into some of the most innovative solutions in this domain.
Pneumatic Belt Tracking System
Pneumatic belt tracking systems work in harmony with conveyor belt tracking sensors to provide dynamic belt alignment. This synergy is characterized by:
- Automatic Adjustments: Utilizes air pressure to make real-time adjustments to the belt’s position.
- Immediate Response: Responds instantly to sensor feedback, correcting misalignments as they occur.
- Versatility: Suitable for various belt widths and speeds, ensuring broad applicability.
- Low Maintenance: Pneumatic systems require minimal maintenance, reducing long-term operational costs.
- Energy Efficiency: Consumes less energy compared to mechanical alignment systems.
- Durability: Designed to withstand harsh industrial environments.
- Integration Ease: Easily integrates with existing conveyor systems and tracking sensors.
Flexco Belt Tracker
Flexco’s belt tracking solutions are renowned for their effectiveness and integration with sensor technology, offering:
- Precision Tracking: Ensures the belt remains on its intended path, reducing wear and tear.
- Sensor Compatibility: Seamlessly works with various types of tracking sensors for enhanced alignment accuracy.
- Easy Installation: Designed for quick and straightforward installation on existing conveyor systems.
- Adjustability: Features adjustable components to cater to different belt sizes and operational requirements.
- Robust Construction: Built to endure the demanding conditions of industrial environments.
- Comprehensive Support: Comes with expert technical support for installation and maintenance.
Conveyor Belt Trainer
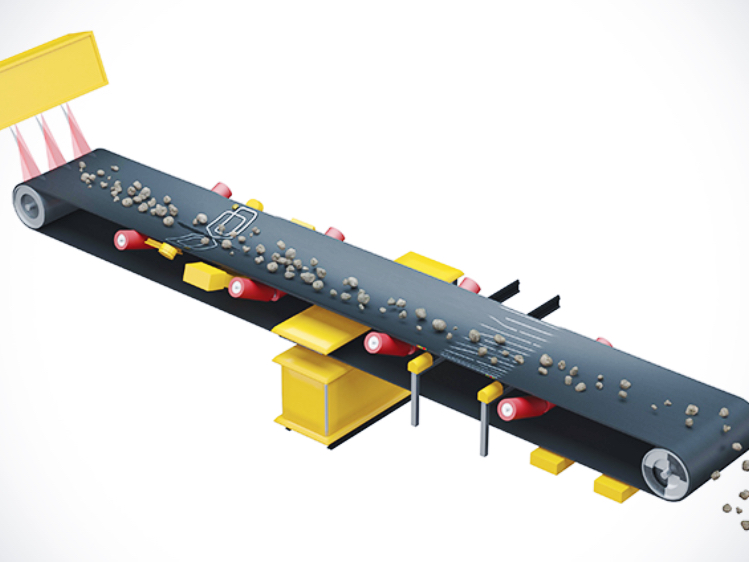
Conveyor belt trainers are essential for maintaining belt alignment, complementing sensor feedback through:
- Continuous Monitoring: Works continuously to monitor belt alignment and adjust as needed.
- Sensor Integration: Receives input from tracking sensors to make precise adjustments.
- Minimizes Downtime: Reduces the likelihood of belt-related stoppages and associated downtime.
- Enhances Belt Life: Proper alignment extends the life of the conveyor belt.
- Improves Safety: Reduces the risk of accidents caused by belt misalignment.
- Operational Efficiency: Ensures smooth and efficient belt operation, improving overall system productivity.
- Customizable Solutions: Available in various configurations to suit specific conveyor systems and applications.
Conveyor Belt Self Alignment System
Automated systems that adjust belt alignment in real-time based on sensor data are at the forefront of conveyor technology:
- Real-Time Adjustments: Automatically adjusts the belt’s alignment in response to sensor data.
- Predictive Maintenance: Utilizes data analytics to predict alignment issues before they occur.
- High Accuracy: Ensures precise belt alignment, minimizing potential for error.
- Integration with IoT: Can be integrated into IoT platforms for enhanced monitoring and control.
- User-Friendly Interface: Often features an intuitive interface for monitoring and adjustments.
- Reduced Manual Intervention: Minimizes the need for manual adjustments, saving time and labor.
- Long-Term Reliability: Enhances the reliability and longevity of the conveyor system.
These advanced tracking solutions, when integrated with conveyor belt tracking sensors, offer a comprehensive approach to maintaining optimal belt alignment. By leveraging these technologies, industries can achieve higher efficiency, safety, and productivity in their conveyor belt operations.
Implementing Conveyor Belt Tracking Sensor
The implementation of conveyor belt tracking sensors is a critical step in optimizing the performance and reliability of gravel conveyor belt systems. These sensors play a vital role in ensuring the belt remains aligned, thus preventing downtime and maintaining operational efficiency. Below, we explore the key considerations and best practices for choosing, installing, calibrating, and maintaining these essential components.
Choosing the Right Sensor
Selecting the appropriate conveyor belt tracking sensor involves several factors:
- Type of Conveyor: The design and function of the conveyor system influence sensor choice. For instance, sensors for a heavy-duty mining conveyor may differ from those used in a packaging line.
- Belt Material: The sensor must be compatible with the conveyor belt material, whether it’s rubber, fabric, or metal, to accurately detect and correct misalignments.
- Operational Environment: Environmental conditions such as temperature, humidity, dust, and exposure to chemicals determine the sensor’s durability and protective requirements.
- Conveyor Speed and Load: Sensors must be capable of accurately tracking the belt under varying speeds and loads without false triggering or delays in response.
- Integration Capability: The sensor should seamlessly integrate with the existing conveyor control system, allowing for real-time adjustments and monitoring.
Installation and Calibration
Ensuring the correct installation and calibration of conveyor belt tracking sensors is crucial for their effective operation:
- Follow Manufacturer Guidelines: Always adhere to the installation instructions provided by the sensor manufacturer to ensure correct placement and function.
- Optimal Placement: Sensors should be strategically placed where they can best detect belt misalignment, typically near the tail or head pulleys and along critical points of the conveyor path.
- Secure Mounting: Properly secure the sensors to prevent vibration or environmental factors from affecting their accuracy.
- Calibration for Sensitivity: Calibrate the sensors to the specific characteristics of the belt and load, ensuring they are sensitive enough to detect misalignments without generating false positives.
- Test Under Load: Perform initial testing under various operational conditions, including different loads and speeds, to fine-tune sensor settings.
- Regular Calibration Checks: Schedule periodic calibration checks to maintain sensor accuracy over time, adjusting settings as necessary based on wear and operational changes.
Maintenance and Troubleshooting
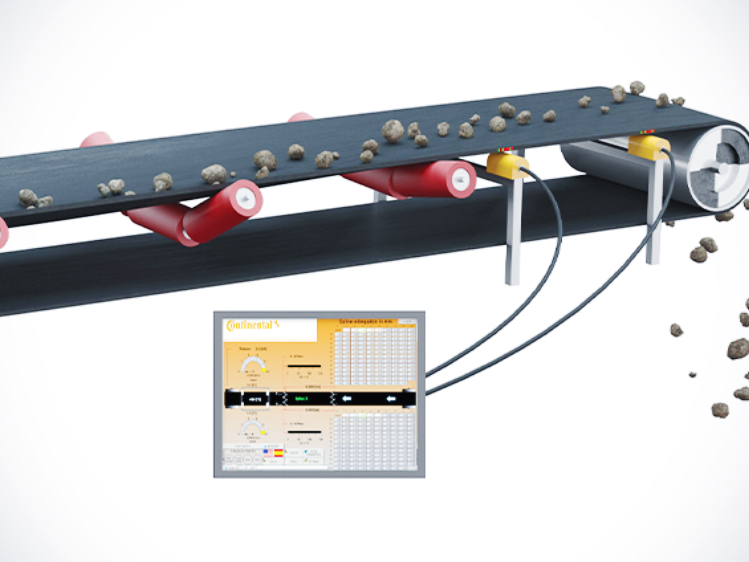
Regular maintenance and effective troubleshooting are essential for the longevity and reliability of conveyor belt tracking sensors:
- Routine Inspections: Conduct regular inspections to check for physical damage, loose connections, and signs of wear on the sensors.
- Clean Regularly: Keep sensors clean from dust, debris, and buildup that could impair their function. Use appropriate cleaning methods based on the sensor type and environmental conditions.
- Update Firmware: For sensors with firmware, ensure that the latest updates are installed to improve performance and add new features.
- Monitor Performance: Use system logs and alerts to monitor sensor performance, identifying patterns that may indicate issues.
- Address Issues Promptly: When a sensor issue is detected, address it promptly to prevent further impact on conveyor belt operations.
- Seek Expert Assistance: For complex issues, consult with the sensor manufacturer or a conveyor system specialist to ensure accurate diagnosis and repair.
Implementing conveyor belt tracking sensors with careful consideration to selection, installation, calibration, and maintenance can significantly enhance the efficiency and safety of gravel conveyor belt systems. By following these guidelines, operators can ensure their conveyor belts remain aligned, reducing downtime and maximizing productivity.
Get in touch for durable and reliable conveyor belts.
Case Studies and Applications of Conveyor Belt Tracking Sensor
The implementation of conveyor belt tracking sensors across various industries has led to significant improvements in operational efficiency, safety, and productivity. These real-world examples illustrate the versatility and effectiveness of conveyor belt tracking sensors in addressing common tracking issues.
Real-World Examples
- Mining Industry: In a large-scale mining operation, conveyor belt tracking sensors were installed to address persistent misalignment issues that led to belt damage and material spillage. The sensors provided real-time adjustments, significantly reducing downtime and maintenance costs.
- Food and Beverage: A food processing plant integrated conveyor belt tracking sensors to ensure strict hygiene standards by preventing product spillage and contamination. The sensors helped maintain precise belt alignment, crucial for the plant’s operational efficiency.
- Manufacturing: In an automotive parts manufacturing facility, tracking sensors were used to optimize the alignment of conveyor belts transporting critical components. This resulted in improved product quality and a reduction in scrap rates.
- Packaging: The packaging company employed conveyor belt tracking sensors to solve issues related to belt drift that caused package misalignment and inefficiencies in the packaging process. The sensors ensured accurate and consistent package handling.
- Recycling Plant: To handle the diverse and unpredictable nature of recycled materials, a recycling facility implemented tracking sensors, which adapted to changes in load and belt speed, enhancing the sorting process’s efficiency and reliability.
- Airport Baggage Handling: Conveyor belt tracking sensors were crucial in an airport’s baggage handling system to prevent luggage from falling off the conveyor due to misalignment, improving passenger satisfaction and operational reliability.
Integration with Conveyor Components
The integration of conveyor belt tracking sensors with other conveyor components creates comprehensive solutions that enhance conveyor system performance:
- Pneumatic Belt Tracking System: Sensors work in tandem with pneumatic systems to provide dynamic, on-the-fly adjustments to belt alignment, offering a responsive solution to varying operational conditions.
- Conveyor Belt Gripper: Sensors ensure that the gripper mechanism accurately aligns with the conveyor belt, preventing damage to the belt edges and ensuring secure handling of materials.
- Self-Alignment Systems: Tracking sensors are integral to automated self-alignment systems, providing the necessary feedback for real-time adjustments and maintaining optimal belt alignment.
- Impact Beds and Skirting: Sensors help adjust the positioning of impact beds and skirting to match the belt’s alignment, reducing wear and spillage.
- Idler Rollers and Pulleys: The data from tracking sensors guide the adjustment of idler rollers and pulleys, ensuring they are positioned correctly to maintain belt alignment.
- Load Distribution: Sensors monitor the belt’s alignment under varying load distributions, adjusting other conveyor components to compensate for shifts in load and prevent belt drift.
These case studies and applications underscore the critical role of conveyor belt tracking sensor in solving alignment issues and enhancing the efficiency of conveyor systems across industries. By integrating these sensors with other conveyor components, operators can achieve a holistic solution that ensures the longevity and reliability of their conveyor systems.
FAQs about Conveyor Belt Tracking Sensor
In conveyor belt systems, various sensors are employed to ensure efficient and safe operation. Among these, conveyor belt tracking sensors are pivotal. These sensors, often incorporating technologies such as infrared, laser, ultrasonic, and RFID, are designed to monitor the alignment and position of the conveyor belt continuously. Their primary function is to detect any deviation from the intended path and initiate corrective actions to realign the belt. This capability is crucial in preventing operational issues such as material spillage, uneven wear on the belt, and potential damage to the conveyor infrastructure. The choice of sensor technology depends on several factors, including the type of conveyor system, the material being transported, environmental conditions, and the specific requirements of the operation. For instance, infrared sensors are favored for their non-contact measurement capabilities, making them suitable for environments where minimal interference with the conveyor operation is desired. Laser sensors, known for their precision, are ideal for applications requiring high accuracy in belt alignment. Ultrasonic sensors, which use sound waves to detect belt position, offer versatility across different conveyor types and conditions.
A conveyor belt tracker is a device or system designed to keep the conveyor belt aligned on its intended path during operation. It plays a critical role in preventing the belt from drifting or misaligning, which can lead to several operational problems, including premature wear, material spillage, and damage to the conveyor structure. Conveyor belt trackers work by applying corrective forces to the belt or its supporting structures, guiding the belt back to its correct alignment. These devices can be mechanical, employing rollers or guides that physically steer the belt, or automated, using sensors and control systems to adjust the belt’s position dynamically. The effectiveness of a conveyor belt tracker depends on its ability to respond to belt misalignment promptly and accurately, minimizing downtime and maintenance requirements. In many modern conveyor systems, belt trackers are integrated with advanced sensor technologies, allowing for real-time monitoring and adjustment of the belt alignment, enhancing the efficiency and reliability of the conveyor operation.
The belt tracking method refers to the techniques and procedures used to maintain the alignment of a conveyor belt, ensuring it runs straight on the pulleys and through the conveyor structure. Effective belt tracking involves several key steps, starting with the proper installation and tensioning of the belt. The conveyor structure itself must be level and square, and the pulleys and rollers should be aligned and perpendicular to the belt’s direction of travel. In operational terms, belt tracking methods can be manual, requiring periodic adjustments by maintenance personnel, or automated, utilizing conveyor belt tracking sensors and control systems to make real-time adjustments. Automated tracking systems are increasingly preferred for their ability to promptly correct misalignment, reducing the risk of downtime and enhancing overall conveyor efficiency. Regardless of the method, the goal of belt tracking is to ensure the smooth, efficient, and safe operation of the conveyor system, extending the life of the belt and minimizing operational disruptions.
Fixing a belt tracker involves identifying and correcting issues that prevent the conveyor belt from maintaining proper alignment. The process typically starts with a thorough inspection of the conveyor system to identify potential causes of misalignment, such as uneven wear on the belt, incorrect tensioning, or misaligned pulleys and rollers. Once the cause is identified, corrective actions can be taken:
Adjust Tension: Ensure the belt is tensioned correctly. Over or under-tensioning can lead to tracking issues.
Align Pulleys and Rollers: Check that all pulleys and rollers are properly aligned and perpendicular to the belt’s path. Adjust as necessary.
Inspect Belt Wear: Look for signs of uneven wear or damage on the belt, which can indicate tracking problems. Replace the belt if it is significantly worn or damaged.
Clean the Conveyor: Remove any debris or buildup on the belt, pulleys, and rollers, as these can cause the belt to misalign.
Use Tracking Devices: Install or adjust existing conveyor belt trackers or tracking sensors. These devices can help maintain alignment by automatically adjusting the belt’s position.
Monitor and Adjust: After making adjustments, run the conveyor belt and observe its alignment. Make further adjustments as needed until the belt tracks correctly.
In many cases, fixing a belt tracker requires a combination of these steps, along with continuous monitoring to ensure the belt remains aligned. For complex or persistent tracking issues, consulting with a conveyor system specialist or the manufacturer may provide additional insights and solutions.
Several types of sensors are used on conveyor belts to ensure efficient operation and safety. Here are some common sensors:
Belt Alignment Sensors: These sensors detect misalignment of the conveyor belt. They are typically mounted along the conveyor and provide feedback to automatically adjust the belt’s position, preventing drift and damage.
Speed Sensors: These sensors monitor the speed of the conveyor belt. They ensure that the belt is operating at the correct speed and can detect any deviations that may indicate a problem with the system.
Proximity Sensors: Used to detect the presence or absence of objects on the conveyor belt. They help in controlling the flow of materials and ensuring that the belt does not run empty or overload.
Load Cells: These sensors measure the weight of the materials on the conveyor belt. They help in monitoring the load to prevent overloading and ensure efficient material handling.
Temperature Sensors: These sensors monitor the temperature of the conveyor belt and the materials being transported. They are crucial in applications where temperature control is essential to prevent damage or spoilage.
Vibration Sensors: These sensors detect unusual vibrations in the conveyor system, which can indicate mechanical issues such as bearing failures or misalignment.
Optical Sensors: Used for detecting the position and movement of the belt and materials. They can help in ensuring precise control and alignment.
Tension Sensors: These sensors monitor the tension of the conveyor belt to ensure it is neither too tight nor too loose, which can affect the belt’s performance and lifespan.
Tracking a conveyor belt is essential for maintaining efficient operation and preventing damage. Here are some best practices for tracking a conveyor belt:
Regular Inspections: Conduct regular inspections of the conveyor system to identify any signs of misalignment or wear. Look for signs of belt drift, uneven wear, or damage to the belt and components.
Adjusting the Tension: Ensure that the belt tension is correctly adjusted. The belt should have enough tension to stay aligned but not so much that it causes excessive wear or stress on the system.
Using Tracking Devices: Install belt tracking devices such as self-aligning idlers, training idlers, and belt tracking rollers. These devices automatically correct the belt’s alignment and keep it centered on the conveyor.
Alignment of Components: Ensure that all conveyor components, such as rollers, pulleys, and idlers, are properly aligned. Misaligned components can cause the belt to drift and become misaligned.
Load Distribution: Ensure that the load on the conveyor belt is evenly distributed. Uneven loading can cause the belt to shift and become misaligned.
Cleaning and Maintenance: Keep the conveyor system clean and free of debris. Buildup of materials on the belt or components can cause misalignment and other issues.
Using Sensors: Utilize sensors such as belt alignment sensors and proximity sensors to monitor the belt’s position and detect any misalignment. These sensors can provide feedback for automatic adjustments.
Tracking a conveyor belt with return rollers involves several steps to ensure that the belt remains properly aligned during operation. Here’s how to track a conveyor belt using return rollers:
Inspect the System: Begin by inspecting the entire conveyor system, including the return rollers, for any signs of wear, damage, or misalignment. Ensure that the return rollers are in good condition and properly aligned.
Adjust the Return Rollers: If the belt is drifting to one side, adjust the return rollers to guide the belt back to the center. This is typically done by slightly skewing the return rollers in the direction that you want the belt to move.
Check the Tension: Ensure that the belt tension is correctly adjusted. Return rollers can help maintain the tension, but the overall belt tension should be checked and adjusted as necessary.
Install Tracking Rollers: Consider installing tracking rollers or self-aligning return idlers. These devices help to automatically correct any misalignment by guiding the belt back to the center as it passes over the return rollers.
Monitor the Belt Path: Regularly monitor the path of the conveyor belt to ensure it is running straight and true. Use belt alignment sensors to detect any deviations and make adjustments as needed.
Adjust Loading Points: Ensure that the loading points are correctly aligned and that materials are evenly distributed on the belt. Uneven loading can cause the belt to shift and become misaligned.
Regular Maintenance: Perform regular maintenance on the return rollers and other components. Clean any buildup of materials that could affect the alignment and ensure that all components are in good working order.
By following these steps, you can effectively track a conveyor belt using return rollers, ensuring smooth and efficient operation of the conveyor system.
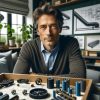
Jordan Smith, a seasoned professional with over 20 years of experience in the conveyor system industry. Jordan’s expertise lies in providing comprehensive solutions for conveyor rollers, belts, and accessories, catering to a wide range of industrial needs. From initial design and configuration to installation and meticulous troubleshooting, Jordan is adept at handling all aspects of conveyor system management. Whether you’re looking to upgrade your production line with efficient conveyor belts, require custom conveyor rollers for specific operations, or need expert advice on selecting the right conveyor accessories for your facility, Jordan is your reliable consultant. For any inquiries or assistance with conveyor system optimization, Jordan is available to share his wealth of knowledge and experience. Feel free to reach out at any time for professional guidance on all matters related to conveyor rollers, belts, and accessories.