Conveyor Belt Rubber Density: Measuring and Testing Explained
The performance and longevity of conveyor belts significantly depend on the quality of rubber used, specifically its density. Conveyor belt rubber density is a critical parameter that determines the belt’s structural integrity and functionality under various industrial conditions. Measured in kilograms per cubic meter (kg/m^3), this density affects key aspects of a conveyor belt’s performance, including tensile strength, elasticity, and wear resistance. High-density rubber typically offers better durability and resistance to deformations such as stretching, abrasions, or tears, thereby enhancing the conveyor belt’s efficiency and lifespan. Understanding the rubber density is essential for selecting the right conveyor belt, as it directly impacts the belt’s ability to handle different weights and speeds of materials over time, ensuring reliable and safe operations in facilities that depend heavily on automated transport systems.
The Basics of Conveyor Belt Rubber Density
Understanding the basics of conveyor belt rubber density is essential for selecting the right material for specific applications and for achieving optimal performance and durability of conveyor belts.
What is Rubber Density?
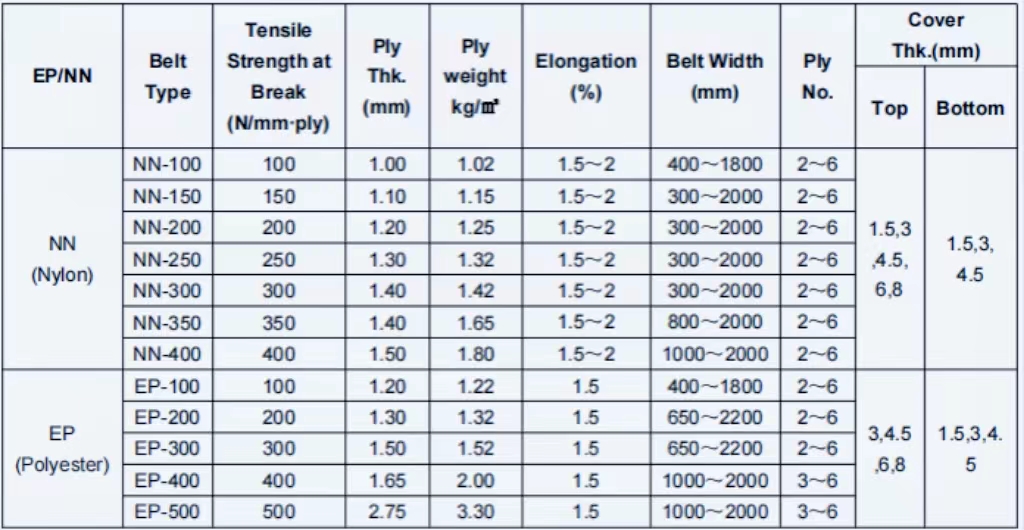
Rubber density, typically measured in kilograms per cubic meter (kg/m³), is a critical property of the rubber used in conveyor belts. It refers to the mass of the rubber material per unit volume. This measurement helps in determining how compact the rubber is, which directly influences its other physical properties, such as elasticity, strength, and wear resistance.
Importance of Conveyor Belt Rubber Density
- Load Support: Higher density rubber can support heavier loads without deformation, making it ideal for heavy-duty applications.
- Wear Resistance: Denser rubber tends to have better wear properties, which is crucial in reducing the wear and tear that occurs during the operation of conveyor belts.
- Tensile Strength: The density of rubber often correlates with its tensile strength. A denser conveyor belt can withstand greater forces and tension, enhancing its durability and lifespan.
- Impact Resistance: High-density rubber absorbs and dissipates shocks better, which is important for belts that handle large, heavy materials.
- Heat Resistance: Rubber density affects how the material reacts to heat. Denser rubbers usually exhibit better heat resistance, reducing the risk of degradation in high-temperature environments.
- Energy Efficiency: Conveyor belts with optimal rubber density require less energy to move and maintain speed, contributing to lower operational costs.
- Vibration Dampening: Denser rubber materials are effective at dampening vibrations, which helps in reducing noise and maintaining the structural integrity of the conveyor system.
- Environmental Resistance: The density of rubber can influence how it withstands environmental factors like moisture, chemicals, and UV exposure.
Factors Affecting Rubber Density
Types of Rubber Materials Used in Conveyor Belts
The choice of rubber material significantly affects the conveyor belt density and overall performance of conveyor belts. Here are six common types:
- Natural Rubber (NR): Offers good tensile strength and elasticity but varies in density based on processing.
- Styrene-Butadiene Rubber (SBR): Generally has lower density and is used for its good abrasion resistance.
- Polybutadiene Rubber (BR): Known for its high resilience, this rubber can have a range of densities based on its formulation.
- Nitrile Rubber (NBR): Favoured for its oil resistant conveyor belt, the density of NBR can be adjusted to suit specific applications.
- Ethylene Propylene Diene Monomer (EPDM): EPDM is used for its excellent weather and ozone resistance and has a moderate density.
- Silicone Rubber: Typically has a lower density and is used for high-temperature applications due to its thermal stability.
Manufacturing Processes That Influence Density
The manufacturing process also plays a crucial role in determining the conveyor belt rubber density. These include:
- Mixing Process: The type and amount of fillers used during the mixing of rubber compounds directly affect the density. Heavier fillers increase density, while lighter fillers reduce it.
- Curing Conditions: The temperature and duration of the curing process can cause changes in the rubber’s microstructure, affecting its density.
- Calendering: The calendering process, where rubber is squeezed into a thin sheet, can compact the material, potentially increasing its density.
By understanding and controlling the conveyor belt rubber density through material selection and manufacturing techniques, engineers can design conveyor belts that are better suited to their specific operational needs. This ensures enhanced performance, efficiency, and longevity of the conveyor system.
Conveyor Belt Rubber Density Specifications
To optimize the performance and longevity of conveyor systems, understanding and adhering to specific conveyor belt rubber density specifications is crucial. These specifications help in selecting the appropriate rubber material for different industrial applications.
Standard Density Ranges
Rubber density in conveyor belts typically ranges between 0.9 to 1.5 kg/m³, depending on the type of rubber and the requirements of the application. Each range has its distinct advantages and is suited for specific environments and load types.
Impact of Density Variations on Belt Performance
- Elasticity and Flexibility: Lower density rubbers are more flexible and can navigate around pulleys and bends more easily, which is crucial in packaging and sorting facilities.
- Load Carrying Capacity: Higher density rubber materials are better suited for heavy-duty applications where high load-bearing capacity is essential, such as in mining and quarrying.
- Abrasion Resistance: Increased rubber density typically enhances abrasion resistance, which is vital for belts that encounter rough materials.
- Tear Resistance: Denser rubber materials exhibit higher tear resistance, which is critical in applications involving sharp or jagged materials.
- Energy Consumption: Belts made from high-density rubber may require more energy to operate due to their increased mass and reduced flexibility.
- Cost-Efficiency: While higher density rubber may offer better durability, it can also be more costly. Choosing the right density can be a balance between performance needs and budget constraints.
- Temperature Tolerance: Denser rubber compounds generally provide better resistance to high temperatures, making them suitable for applications in environments with high thermal exposure.
Measuring Rubber Density
Accurate measurement of conveyor belt rubber density is essential for quality control and specification adherence. Here are eight techniques and tools used for this purpose:
- Hydrometer Test: A device used to measure the specific gravity of a rubber sample, which can be converted to density.
- Pycnometer: A precise volumetric flask used to determine the volume of a rubber sample, allowing for accurate density calculations.
- Ultrasonic Thickness Gauge: Used to measure the thickness of the rubber, which can help infer density when combined with other data.
- Water Displacement Method: A method where the volume of rubber is determined by the displacement of water, used for irregularly shaped samples.
- Digital Density Meters: These provide quick and accurate density readings and are suitable for routine checks during production.
- Archimedes’ Principle: This principle is applied using a balance and a suspension method to measure buoyancy and calculate density.
- Infrared Spectroscopy: While primarily used for chemical analysis, it can also provide information about the density of compounds in some contexts.
- Cone Penetration: Measures the resistance of rubber to penetration, indirectly providing density-related insights.
Conveyor Belt Rubber Density Formula
The density of rubber ((\rho)) is calculated using the formula:
ρ = mass / volume
For conveyor belts, this formula helps in determining the exact density by measuring the mass and volume of rubber samples. This calculation is critical in ensuring that the rubber meets the specific density requirements for its intended application, thereby ensuring optimal performance and durability.
By adhering to these specifications and effectively measuring conveyor belt rubber density, manufacturers and engineers can significantly enhance the efficiency and lifespan of conveyor systems.
Technical Specifications of Conveyor Belt Rubber Density
Ensuring that conveyor belts meet specific technical specifications is crucial for their performance and longevity. This includes careful consideration of conveyor belt rubber density, which plays a significant role in the belt’s operational efficiency and durability.
EP Conveyor Belt Specification
EP (Polyester-Nylon) conveyor belts are known for their excellent balance of flexibility and strength, resulting from their fabric composition. The rubber in these belts often has a density that ranges from 1.0 to 1.5 kg/m³, providing an optimal blend of elasticity and toughness.
Benefits of Using EP Belts in Various Industrial Applications
- High Tensile Strength: EP belts are capable of handling significant weight due to the high tensile strength of the polyester and nylon weave.
- Low Elongation: These belts exhibit low elongation under load, making them ideal for long-distance conveying.
- Good Impact Resistance: The tough rubber matrix can absorb impacts, minimizing damage during heavy material handling.
- Resistance to Wear and Tear: High-density rubber compounds used in EP belts contribute to superior wear resistance.
- Adaptability to Different Weather Conditions: EP belts perform well in various environmental conditions, including exposure to moisture and UV light.
- Energy Efficiency: The inherent properties of EP belts allow for smoother operations and reduced power consumption.
- Cost-Effectiveness: Despite their superior qualities, EP belts are generally cost-effective compared to other high-performance belts.
- Maintenance Requirements: EP belts require less maintenance due to their durable construction, reducing downtime.
- Versatility in Applications: Suitable for industries ranging from mining to logistics and packaging.
- Chemical Resistance: The rubber compounds can be formulated to resist various chemicals and oils, increasing their applicability in chemical processing plants.
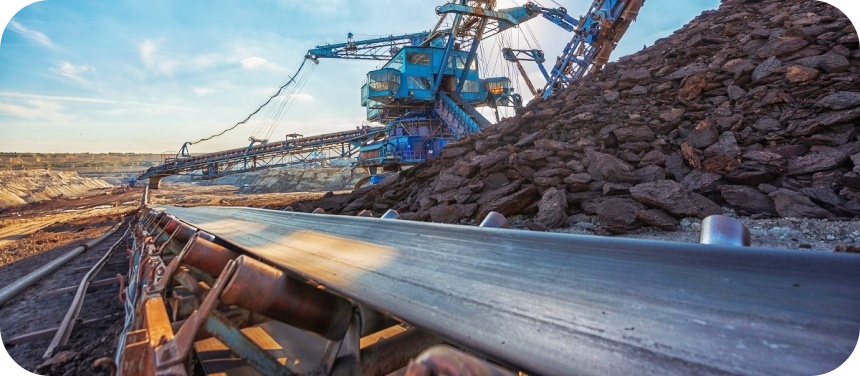
Rubber Conveyor Belt Catalogue and Standards
Rubber conveyor belt catalogues and PDF standards are essential resources that provide detailed specifications and quality benchmarks for the industry. These documents ensure that all manufactured conveyor belts meet stringent quality standards, which is crucial for safety and efficiency.
Discussion on Standard Specifications Found in Rubber Conveyor Belt Catalogues
Conveyor belt rubber catalogues often include comprehensive details on the dimensions, material types, tensile strengths, maximum load capacities, and conveyor belt rubber density. These specifications are designed to ensure that belts are suitable for a wide range of applications and meet the required safety and operational standards.
Ensuring Quality and Consistency in Conveyor Belt Manufacturing
Standards like those found in rubber conveyor belt catalogues are vital for the following reasons:
- Quality Assurance: Standards ensure that all conveyor belts are manufactured to meet high-quality benchmarks, reducing the risk of failure and extending the lifespan of the belts.
- Consistency: With detailed specifications, manufacturers can produce belts that provide consistent performance across all applications, ensuring reliability.
- Safety: Adherence to standards helps in minimizing the risk of accidents due to belt failures, which is crucial in all industries, especially in heavy-duty applications.
- Interchangeability: Standardization allows for the interchangeability of belts from different manufacturers, which can be critical for maintenance and repairs.
By following these detailed specifications and adhering to established standards, manufacturers and users of conveyor belts can ensure that the belts perform optimally across their operational lives, providing both safety and efficiency in various industrial settings.
Practical Applications of Conveyor Belt Rubber Density
Understanding the practical implications of conveyor belt rubber density is crucial for optimizing conveyor system performance across various industries.
Density and Conveyor Belt Performance
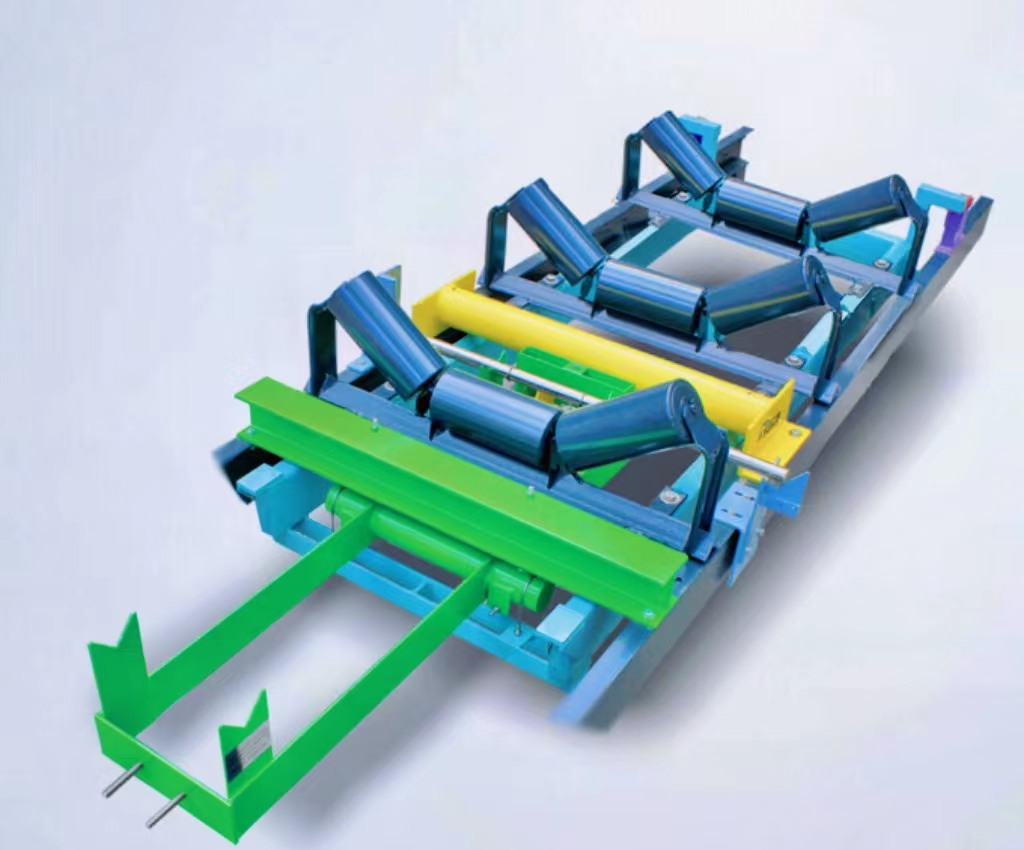
The rubber density of a conveyor belt significantly affects its operational characteristics, such as tensile strength, flexibility, and wear resistance:
- Tensile Strength: Higher density rubbers generally provide greater tensile strength, which is crucial for belts that must withstand heavy loads or high tension.
- Flexibility: Lower density rubber tends to be more flexible, which is beneficial for belts that operate over smaller pulleys or require tight bends.
- Wear Resistance: Increased rubber density typically correlates with better wear resistance, making these belts more durable under abrasive conditions.
Case Studies Where Specific Rubber Densities are Preferred
- Mining Industry: High-density rubber belts are used due to their enhanced wear resistance and ability to handle sharp, heavy materials.
- Food Processing: Lower density rubber belts are preferred for their flexibility and ease of cleaning, important in an industry requiring frequent sanitation.
- Packaging Facilities: Medium density rubber is often chosen for its balance between strength and flexibility, accommodating various packaging sizes and weights.
- Airport Baggage Handling: Durable, high-density rubber is necessary to withstand the heavy and continuous load of luggage, providing longevity and reducing maintenance needs.
Conveyor Belt Selection Guide
Selecting the right rubber density for conveyor belts is vital to meet the specific needs of different industrial operations. Here are 12 tips and 8 considerations to guide your selection process:
Tips on Selecting the Right Rubber Density
- Assess the Weight of Materials: Choose higher density rubber for heavier materials to prevent belt deformation.
- Consider Belt Speed: High-speed belts benefit from higher density rubber for better wear resistance.
- Evaluate Pulley Diameter: Smaller pulleys require more flexible, thus lower density rubber belts.
- Check Operational Duration: Continuous operations may need higher density rubber for increased durability.
- Analyze the Impact of Materials: Materials that impact the belt heavily necessitate higher density rubber to absorb shocks.
- Factor in Environmental Conditions: UV light, ozone, chemicals, and temperature extremes require belts with specific rubber densities that can withstand these conditions.
- Plan for Maintenance: Lower maintenance needs can often be met with higher density belts.
- Budget Considerations: Although higher density rubber might be more expensive, it could be cost-effective in the long run due to lower replacement rates.
- Compliance with Safety Standards: Ensure the chosen rubber density meets industry-specific safety standards.
- Future Scalability: Consider future changes in load or operational conditions that might require different densities.
- Consult with Experts: Leverage industry experts’ knowledge to match rubber density with conveyor belt needs.
- Test Samples: Where possible, test different rubber densities under actual operating conditions.
Considerations for Belt Selection
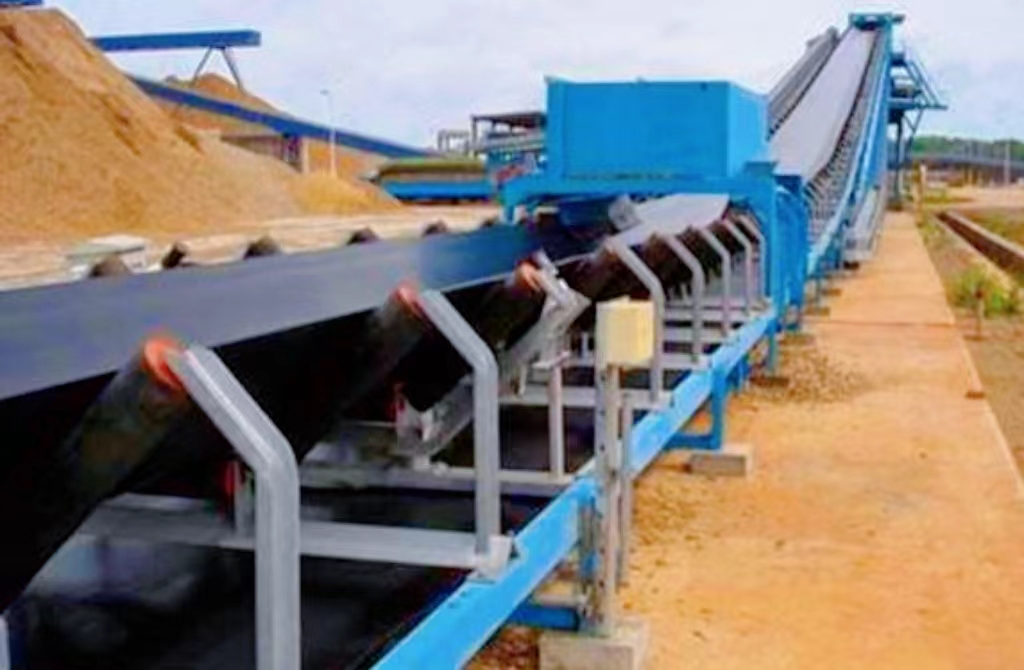
- Load Capacity: Higher density rubber supports heavier loads without stretching excessively.
- Operational Environment: Assess environmental factors like temperature, moisture, and chemical exposure that affect rubber performance.
- Material Type: The type of material being conveyed can dictate the required rubber density due to wear considerations.
- Operational Noise: Lower density rubber can reduce operational noise, an important factor in certain environments.
- Installation Space: Space constraints might limit the choice of belt thickness and, consequently, density.
- Energy Efficiency: Consider the energy cost of operating heavier (higher density) versus lighter (lower density) belts.
- Regulatory Requirements: Some industries have specific conveyor belt regulations that dictate the type of conveyor belts that can be used.
- Longevity and Replacement Frequency: Assess how often belts might need to be replaced based on their density and operational wear and tear.
By considering these tips and factors, businesses can make informed decisions about the appropriate conveyor belt rubber density to use, ensuring optimal performance, durability, and cost-efficiency in their conveyor systems.
Calculation and Conversion Tools about Conveyor Belt Rubber Density
The precision in designing and manufacturing conveyor belts can be greatly enhanced by using various calculation and conversion tools. These tools help estimate key characteristics like weight and thickness, taking into account the conveyor belt rubber density, which is crucial for performance and durability.
Conveyor Belt Weight and Thickness Calculators
Using a Conveyor Belt Weight Calculator
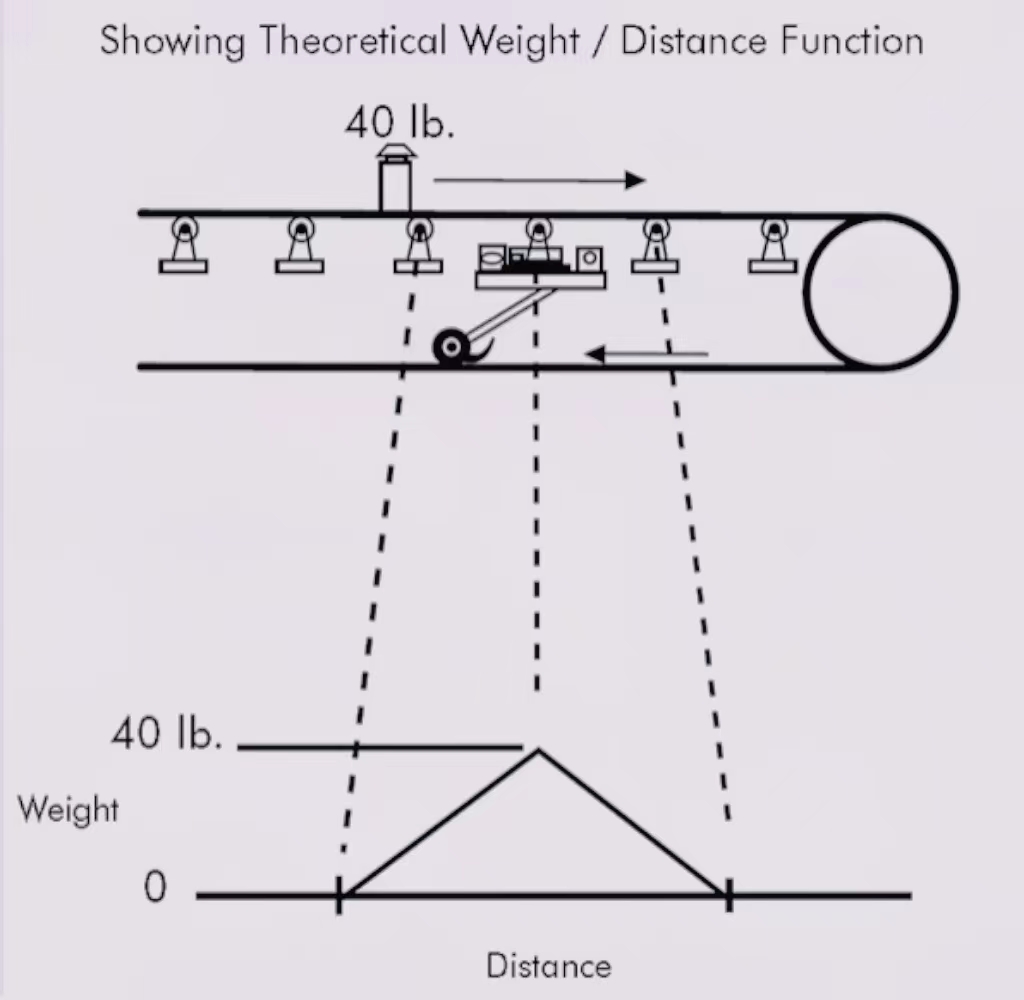
A conveyor belt weight calculator can provide an accurate estimation of the belt’s weight per meter, which is essential for handling and installation procedures. Here’s how to use this tool:
- Input Specifications: Enter the dimensions of the belt, including length, width, and nominal thickness.
- Enter Rubber Density: Include the conveyor belt rubber density, typically given in kg/m³, which directly influences the weight calculation.
- Calculate: The tool computes the weight per meter by integrating the belt’s volume (area multiplied by thickness) with the rubber density.
Understanding 4 Ply Conveyor Belt Thickness
The thickness of a conveyor belt, such as a “4 ply” belt, indicates the number of layers of fabric or rubber compounding, known as plies, embedded within the belt. Here’s the correlation with rubber density:
- Ply Composition: Each ply layer typically has a uniform thickness, and the type of rubber used influences its density.
- Total Thickness: The total thickness of a 4 ply belt is the sum of the individual plies and the rubber matrix. Higher rubber densities typically imply more durable, albeit heavier, belts.
- Performance Implication: The thickness and density affect the belt’s ability to withstand wear, tension, and environmental factors.
Using Density in Design and Quality Control
Density in Conveyor Belt Design
Engineers utilize rubber density measurements to tailor conveyor belt designs for specific operational needs:
- Material Selection: Choosing rubber compounds with the appropriate density ensures the belt can handle expected loads and operational stresses.
- Structural Integrity: Higher density materials may be used in areas of the belt where higher wear is anticipated or where less stretching is desired.
- Energy Efficiency: Calculating the optimal rubber density can help in reducing the energy consumption of the conveyor system by minimizing the belt’s weight while maintaining strength.
Contact us for the best deals on conveyor belts.
Roles of Density in Quality Control Processes
Rubber density plays several critical roles in the quality control processes of conveyor belt manufacturing:
- Consistency Check: Density measurements ensure that the rubber compounds mixed for the belts are consistent with design specifications.
- Compliance with Standards: Adhering to international standards often requires specific density values, which need to be verified during quality control.
- Durability Testing: Higher density rubbers are generally tested for enhanced durability characteristics such as resistance to wear and tear.
- Performance Simulation: Simulations using specific density values can predict how the belt will perform under various load conditions.
- Batch Quality: Each batch of rubber is tested for density to ensure uniform quality and performance across production.
- Environmental Resistance: Density measurements help predict how well the belt will withstand environmental factors like temperature and chemical exposure.
- Load Capacity Verification: Ensuring the belt can carry the specified load without deforming or failing prematurely requires accurate density data.
- Lifecycle Assessment: Density plays a role in predicting the lifecycle of the belt, influencing decisions on warranty and replacement intervals.
- Innovation and Improvement: Ongoing density evaluations drive improvements in rubber compounds and conveyor belt designs.
By effectively utilizing these calculation and conversion tools and incorporating conveyor belt rubber density into design and quality control, manufacturers can enhance the performance, safety, and reliability of their conveyor systems.
FAQs about Conveyor Belt Rubber Density
The density of rubber used in conveyor belts typically varies depending on the type of rubber compound being used. Generally, the density of natural rubber ranges from 0.92 to 0.98 g/cm³. However, for conveyor belts, rubber compounds are usually reinforced with various materials and additives to enhance their performance characteristics, leading to densities that can range from about 1.1 to 1.3 g/cm³. These variations in density are crucial as they directly influence the belt’s durability, flexibility, and its ability to withstand different working environments. For applications that demand specific performance standards, such as high tensile strength or exceptional resistance to abrasion, manufacturers might use specialized rubber compounds with tailored densities to meet these requirements. When selecting a conveyor belt, understanding its rubber density is vital for ensuring that the belt is suitable for the intended application, as it affects the belt’s overall strength and longevity.
Rubber conveyor belts are engineered to meet diverse industrial requirements, and their specifications can widely vary. Common specifications include belt width, thickness, layer number, tensile strength, cover rubber quality, and abrasion resistance. Belt width can range from a few inches to several feet, accommodating different bulk material sizes and throughput requirements. Thickness and the number of layers (plies) contribute to the belt’s load-bearing capacity and impact resistance. Tensile strength, expressed in pounds per inch of width (PIW) or Newton per millimeter (N/mm), indicates the belt’s longitudinal strength. Cover rubber is graded by its ability to resist wear, tear, and environmental factors, such as exposure to oils, chemicals, and UV light. Higher grades of abrasion-resistant cover materials are chosen for harsh conditions to prolong the belt’s operational life. These specifications are critical for ensuring that the conveyor belt performs efficiently in its designated application, providing reliability and safety in material handling processes.
Polyurethane (PU) belts, known for their versatility and durability, feature a density that can vary slightly depending on the formulation and the specific application they are designed for. Generally, the density of PU for conveyor belts hovers around 1.2 g/cm³. This value might fluctuate based on the addition of certain fillers, plasticizers, or other additives intended to enhance particular properties such as flexibility, abrasion resistance, or tensile strength. PU belts are favored in many industries for their excellent chemical resistance, superior abrasion resistance compared to rubber, and their ability to maintain performance characteristics in extreme temperatures and environments. The relatively high density of PU belts contributes to their robustness and effectiveness in conveying products, especially in applications requiring precision, cleanliness, and minimal maintenance. When considering a PU belt for specific needs, it’s important to consult with the manufacturer regarding the exact density and how it affects the belt’s application suitability.
Conveyor belts utilize a variety of rubber types, each selected for its unique properties and suitability for different conveying applications. Natural rubber (NR) is often used for belts requiring flexibility and high tensile strength. Styrene Butadiene Rubber (SBR) is popular for its good abrasion resistance and cost-effectiveness, making it ideal for general-purpose belts. Butadiene Rubber (BR) is sought after for its low-temperature flexibility. Nitrile Rubber (NBR) is used in applications needing resistance to oils, fats, and other chemicals. Ethylene Propylene Diene Monomer (EPDM) rubber is chosen for its exceptional weather and ozone resistance. The specific rubber compound used in a conveyor belt is carefully tailored to the belt’s intended application – whether that involves resistance to abrasion, chemicals, temperature extremes, or the need for food-grade materials. Understanding the differences among these rubber types helps in selecting the most appropriate conveyor belt for industrial processes, ensuring optimal performance and longevity under the desired operating conditions.
Conveyor belts are typically made from a variety of rubber compounds, each chosen based on the specific requirements of the application. The most common types of rubber used in conveyor belts include natural rubber, styrene-butadiene rubber (SBR), and nitrile rubber (NBR). Natural rubber is known for its excellent elasticity and resistance to abrasion, making it ideal for general-purpose conveyor belts. SBR is a synthetic rubber that offers good abrasion resistance and durability, often used in applications where the belt needs to withstand rough handling and wear. NBR is another synthetic rubber that provides excellent resistance to oils and chemicals, making it suitable for environments where the belt might come into contact with these substances. Additionally, specialized rubbers such as EPDM (ethylene propylene diene monomer) are used for heat-resistant conveyor belts, while neoprene is chosen for its flame-retardant properties. The specific rubber compound used can greatly influence the belt’s performance, durability, and suitability for different industrial applications.
The weight of a rubber conveyor belt can vary significantly based on its length, width, thickness, and the type of rubber used. Generally, the weight of a conveyor belt is measured in pounds per foot or kilograms per meter. For instance, a standard rubber conveyor belt might weigh around 1.5 to 2 pounds per foot for a belt that is 24 inches wide and 3/8 inch thick. This translates to approximately 2.2 to 3 kilograms per meter. Heavier duty belts designed for industrial applications can weigh significantly more. For example, a reinforced rubber conveyor belt used in mining or heavy industrial applications might weigh between 3 to 4 pounds per foot, or about 4.5 to 6 kilograms per meter. The weight is also influenced by additional factors such as the presence of reinforcing materials like steel or fabric, which add to the overall mass. It’s important to know the exact specifications of the belt to accurately determine its weight, as this information is crucial for proper installation and support within the conveyor system.
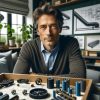
Jordan Smith, a seasoned professional with over 20 years of experience in the conveyor system industry. Jordan’s expertise lies in providing comprehensive solutions for conveyor rollers, belts, and accessories, catering to a wide range of industrial needs. From initial design and configuration to installation and meticulous troubleshooting, Jordan is adept at handling all aspects of conveyor system management. Whether you’re looking to upgrade your production line with efficient conveyor belts, require custom conveyor rollers for specific operations, or need expert advice on selecting the right conveyor accessories for your facility, Jordan is your reliable consultant. For any inquiries or assistance with conveyor system optimization, Jordan is available to share his wealth of knowledge and experience. Feel free to reach out at any time for professional guidance on all matters related to conveyor rollers, belts, and accessories.