Conveyor Belt Rubber Weight Calculation and Chart Guide
Understanding the conveyor belt rubber weight is essential for the design, specification, and operation of conveyor systems used across various industries. The weight of the conveyor belt rubber significantly affects the performance, efficiency, and cost-effectiveness of these systems. Accurately calculating this weight ensures proper handling, installation, and function, preventing potential overloads or failures. In industrial applications, the weight impacts the motor’s power requirements and structural integrity of the conveyor setup. Moreover, knowing the specific weight per unit area helps in determining the total load that the conveyor will need to move, which directly influences the selection of the motor and the design of the framework. This knowledge is not only critical for achieving optimal operational efficiency but also for ensuring safety and longevity of the conveyor system itself.
Key Concepts and Definitions of Conveyor Belt Rubber Weight
Conveyor Belt Rubber Weight Calculator
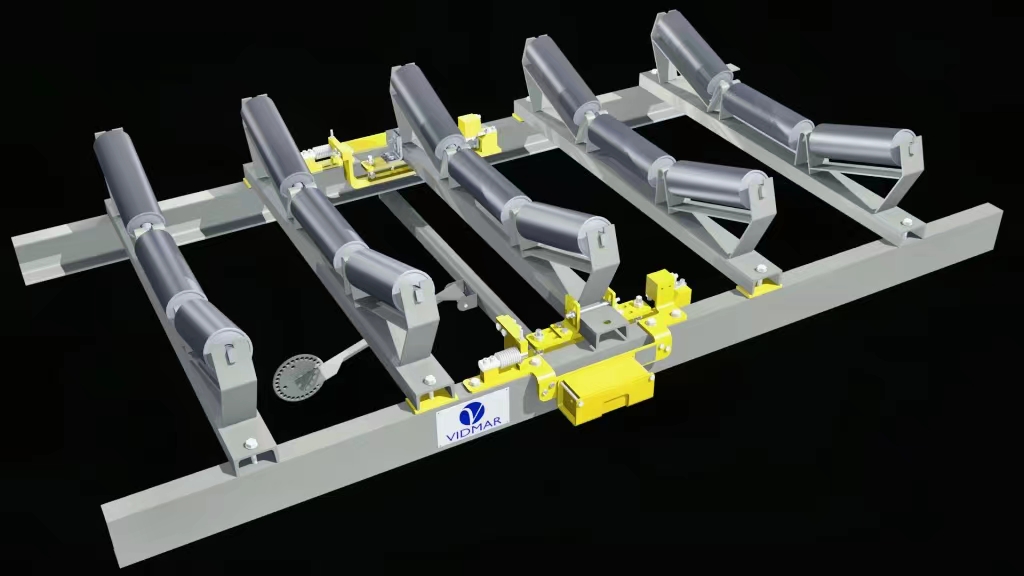
A Conveyor Belt Rubber Weight Calculator is an essential tool used in the manufacturing and engineering fields to estimate the weight of a conveyor belt. This calculator takes into account various factors such as the belt’s dimensions, including its length, width, and thickness, as well as the type of rubber material used. The significance of understanding the conveyor belt rubber weight lies in its utility for designing conveyor systems that are efficient, safe, and suitable for the intended cargo and operational conditions.
Conveyor Belt Rubber Weight in kg/meter
The term “Conveyor Belt Rubber Weight in kg/meter” refers to the weight of the conveyor belt measured per meter length, which is a standard measurement used across the industry. This measurement helps in the calculation of the total weight that the conveyor belt system can handle during operation without exceeding the limits of its design specifications. Typically, the weight of rubber conveyor belts varies depending on the thickness of the rubber cover and the structure of the belt itself (e.g., fabric belts, steel-cord belts).
Density of Rubber Conveyor Belt
The Density of Rubber Conveyor Belt is a crucial factor that significantly impacts the conveyor belt rubber weight. Density is typically expressed in kilograms per cubic meter (kg/m³) and varies based on the type of rubber composite used and the presence of other materials like steel cords or fabric layers. A higher density implies a heavier belt, which can affect the energy efficiency of the conveyor system and the load it can support. Understanding the density helps in predicting the durability and the performance efficiency of the belt under different operational stresses.
Through these concepts, engineers and designers calculate and optimize the conveyor belt rubber weight to enhance system performance and ensure durability and safety. Each component, from the weight per meter to the density of the material, plays a pivotal role in the functionality of the conveyor belt system.
Conveyor Belt Rubber Weight Chart
A Conveyor Belt Rubber Weight Chart is a crucial tool used by engineers and designers in the conveyor belt industry to select the appropriate conveyor belt based on its rubber weight specifications. These charts provide detailed information on the weight of conveyor belts per meter squared, taking into account different widths, thicknesses, and rubber densities.
Description of a Typical Conveyor Belt Rubber Weight Chart
A typical Conveyor Belt Rubber Weight Chart contains a matrix or a set of tables that list conveyor belt dimensions alongside their corresponding weights. The primary dimensions included are the width and thickness of the belt, which are typically measured in millimeters (mm) or inches (in), whereas the weight is provided in kilograms per meter (kg/m) or pounds per foot (lbs/ft). Each entry in the chart corresponds to the total weight of a one-meter length of conveyor belt with specific dimensions and made of a specific rubber compound, reflecting a particular density measured in kg/m³.
How to Use a Conveyor Belt Rubber Weight Chart Effectively
To use a Conveyor Belt Rubber Weight Chart effectively, follow these steps:
- Identify Belt Dimensions: Determine the necessary width and thickness of the conveyor belt based on the application’s requirements, such as the type of material to be transported and the total load expected on the belt.
- Match to Chart Specifications: Locate these dimensions in the chart to find the corresponding weight. Charts are usually organized in a grid format, with widths listed along one axis and thicknesses along the other.
- Consider Rubber Density: Ensure that the rubber density assumed in the chart matches or closely approximates the density of the rubber material used in the belt being considered. If the densities differ, adjustments might be needed to get an accurate weight estimate.
- Cross-Reference Multiple Sources: If available, compare the data with multiple charts from different manufacturers to confirm consistency and accuracy.
Examples of Interpreting Data from a Conveyor Belt Rubber Weight Chart
Let’s consider a chart with the following entries for a rubber conveyor belt’s width (in meters), thickness (in millimeters), and the respective weight (in kilograms per meter):
Width (m) | Thickness (mm) | Weight (kg/m) |
---|---|---|
0.5 | 10 | 1.5 |
0.5 | 15 | 2.25 |
0.5 | 20 | 3.0 |
1.0 | 10 | 3.0 |
1.0 | 15 | 4.5 |
1.0 | 20 | 6.0 |
Example Interpretations
- Basic Selection:For a belt 0.5 meters wide and 10 mm thick, the weight per meter is 1.5 kg.
- Increased Thickness:Increasing the thickness to 15 mm, while keeping the width constant at 0.5 meters, increases the weight to 2.25 kg per meter.
- Increased Width:For a belt that is 1.0 meter wide and 10 mm thick, the weight doubles compared to a 0.5-meter wide belt of the same thickness, totaling 3.0 kg per meter.
- Double Dimension Change:A belt 1.0 meter wide and 20 mm thick weighs 6.0 kg per meter, demonstrating how both increased width and thickness proportionally increase the weight.
- Comparison for Specification Matching:Comparing belts of 15 mm thickness, the weight for a 1.0 meter wide belt (4.5 kg/m) is exactly double that of a 0.5 meter wide belt (2.25 kg/m), illustrating consistent scaling within the chart.
- Application-Specific Selection:For heavy-duty applications requiring robust support, choosing a belt 1.0 meter wide and 20 mm thick (weight 6.0 kg/m) would be appropriate, while lighter applications could suffice with a 0.5 meter wide, 10 mm thick belt (weight 1.5 kg/m).
Using these interpretations, engineers can efficiently select a conveyor belt that not only meets the physical and operational requirements of their systems but also optimizes the overall weight to improve performance and reduce costs. This meticulous approach to selecting based on the conveyor belt rubber weight ensures that the system is both effective and economical.
Factors Affecting Conveyor Belt Rubber Weight
The conveyor belt rubber weight can be influenced by several factors that affect the selection, design, and operational efficiency of conveyor systems. Understanding these factors helps in predicting how a conveyor belt performs under various operational conditions and in different environments.
Material Type
The type of rubber compound used in the conveyor belt significantly affects its weight. Rubber materials typically used in conveyor belts include:
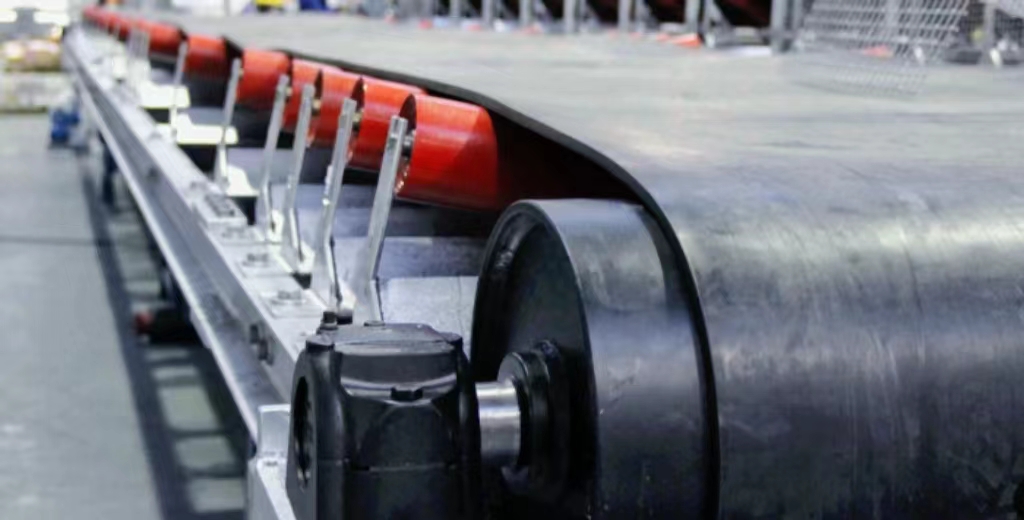
- Natural Rubber: Tends to be lighter, which might result in a lower conveyor belt rubber weight per meter compared to synthetic rubbers, due to its lower density.
- Synthetic Rubber: Such as SBR (Styrene Butadiene Rubber) or Neoprene, these materials are generally denser and hence contribute to a heavier conveyor belt. The specific gravity of these materials can vary significantly, typically ranging from 1.1 to 1.5 kg/m³.
Belt Type
The construction of the conveyor belt also plays a crucial role in its weight:
- Fabric Core Belts: These belts, made with layers of fabric such as polyester or nylon, are lighter as the fabric itself has a relatively low density.
- Steel-Reinforced Belts: Incorporating steel cords or mesh, these belts are considerably heavier due to the high density of steel compared to rubber and fabric materials.
Environmental Factors
Environmental conditions such as temperature and humidity can affect the conveyor belt rubber weight by altering the rubber’s density:
- Temperature: Higher temperatures can cause the rubber to expand, slightly reducing its density and therefore its weight per unit volume.
- Humidity: Increased humidity levels can lead to rubber absorbing moisture, which might increase the weight temporarily if the water content significantly alters the overall density.
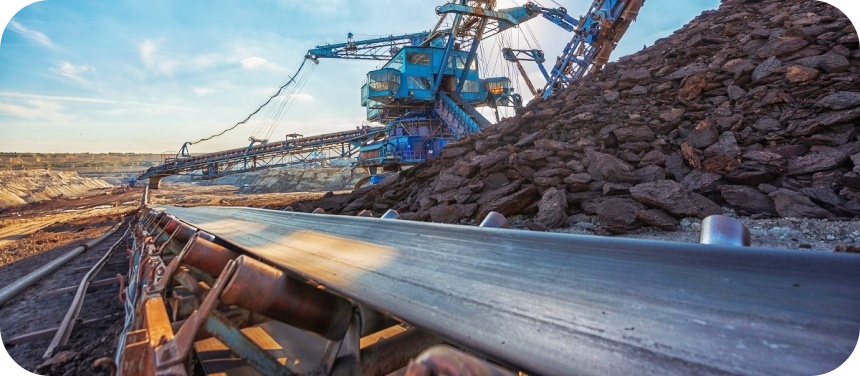
Other Influential Factors
Several additional factors can influence the conveyor belt rubber weight, including:
- Belt Thickness: Thicker belts will naturally weigh more due to the increased volume of material (rubber and possibly other composites like fabric or steel).
- Belt Width: Wider belts have a greater area and thus use more material, which increases the total weight.
- Rubber Density: Depending on the specific type of rubber used, the density can vary, directly affecting the weight. For instance, rubber compounds filled with mineral fillers or recycled materials may have different densities compared to virgin rubber.
- Manufacturing Process: The method used to produce the conveyor belt can also impact its weight. For example, belts cured under high pressure tend to have a more compact and denser structure, increasing their weight.
- Additives and Fillers: The inclusion of additives such as carbon black, silica, or other reinforcing agents can alter the density and therefore the weight of the rubber material. These substances are often added to enhance the properties of the rubber, such as its tensile strength and durability, but they also affect its mass.
Practical Considerations
When designing or selecting a conveyor belt based on conveyor belt rubber weight, it’s important to consider these factors comprehensively. The choice of material, type of belt, and environmental conditions not only determine the belt’s suitability for the intended application but also impact the operational costs and longevity of the conveyor system. By carefully analyzing these factors, engineers can optimize the design to achieve the best performance and cost-efficiency. This approach ensures that the conveyor system is robust, reliable, and capable of handling the intended load under varying conditions.
Importance of Accurate Weight Calculations for Conveyor Belt Rubber Weight
Accurately calculating the conveyor belt rubber weight is crucial for several operational and financial aspects of conveyor belt systems. The weight of conveyor belt rubber affects not only the economics of the conveyor system but also its efficiency and safety. Below, we explore the reasons why precise weight calculations are vital.
Cost Implications
The conveyor belt rubber weight significantly influences both shipping and installation costs. Conveyor belts are typically large and heavy, making transportation costs considerably high. Accurate weight information ensures that companies can plan for optimal shipping methods, avoid excess fees for overweight shipments, and adequately prepare for the handling requirements upon delivery. During installation, the weight of the conveyor belt dictates the type of machinery and manpower required. Underestimating the weight might result in inadequate equipment being used, leading to delays and increased costs in hiring additional resources or equipment.
Operational Efficiency
Accurate calculations of conveyor belt rubber weight are essential for maintaining operational efficiency. The weight impacts the balance of the conveyor system; an imbalance can cause uneven wear and tear, increasing maintenance costs and downtime. Furthermore, the weight determines the motor’s load, affecting energy consumption. An overestimated weight calculation might lead to an oversized motor that consumes more electricity than necessary, whereas an underestimated weight could lead to motor overload and potentially costly failures. Therefore, precise weight assessments help in selecting the right motor that balances efficiency and cost-effectiveness.
Safety
The safety of conveyor systems heavily relies on the accurate estimation of conveyor belt rubber weight. Overestimating the weight can lead to the design and implementation of overly robust conveyor belt support structures, unnecessarily increasing project costs. More critically, underestimating the weight can result in the selection of support components that are not strong enough to handle the load, posing serious safety risks to operational staff and the facility. This can lead to structural failures, which may cause injuries, halt production, and necessitate expensive repairs and legal liabilities.
Understanding the exact conveyor belt rubber weight is imperative not just for the economic rationale, but also for the operational reliability and safety of the conveyor system. Ensuring precise weight calculations before installation equips planners and engineers with the necessary information to optimize design and logistics, enhance safety, and control expenditures effectively.
Recommended Products for Optimal Conveyor Belt Rubber Weight
Selecting the right conveyor belt is crucial for operational efficiency and cost management. The following table lists the top 5 conveyor belts recommended based on conveyor belt rubber weight, emphasizing durability, cost-effectiveness, and manufacturer reliability. These selections are favored in industry reviews and are known for their robust performance and longevity.
Rank | Product Name | Durability | Cost-Effectiveness | Manufacturer Reliability | Key Feature |
---|---|---|---|---|---|
1 | UltraDuty Steel-Reinforced Belt | High | Moderate | Excellent | Optimal conveyor belt rubber weight for heavy loads |
2 | MaxFlex Fabric Core Conveyor Belt | Moderate | High | Very Good | Lightweight with excellent weight distribution |
3 | ProGrade Synthetic Rubber Belt | Good | High | Good | Resistant to chemicals and temperature variations |
4 | EcoSmart Balanced Weight Belt | Moderate | Very High | Excellent | Eco-friendly materials, balanced conveyor belt rubber weight |
5 | HeavyLoad Iron-Core Conveyor Belt | Very High | Moderate | Very Good | Designed for extreme environments and heavy-duty usage |
Analysis of Recommended Products
1. UltraDuty Steel-Reinforced Belt:
- Durability: This belt is particularly valued for its high durability. Steel reinforcements are ideal for handling significant weights and sharp objects that might cut or pierce softer belts.
- Cost-Effectiveness: While not the cheapest, its longevity and reduced need for replacements make it cost-effective in the long run.
- Manufacturer Reliability: Known for robust construction and reliable performance under demanding conditions.
- Key Feature: Maintains optimal conveyor belt rubber weight even under extreme operational stress, ensuring safety and efficiency.
2. MaxFlex Fabric Core Conveyor Belt:
- Durability: Offers moderate durability with enhanced flexibility to prevent snaps under tension.
- Cost-Effectiveness: Highly cost-effective due to lower initial investment and maintenance costs.
- Manufacturer Reliability: Reputable manufacturer with a focus on innovative lightweight designs.
- Key Feature: Its light conveyor belt rubber weight makes it easy to install and reduces strain on the motor, saving energy.
3. ProGrade Synthetic Rubber Belt:
- Durability: Good durability with added resistance to corrosive chemicals and variable temperatures.
- Cost-Effectiveness: Cost-efficient for facilities dealing with harsh chemicals or extreme heat.
- Manufacturer Reliability: Reliable performance backed by a solid warranty.
- Key Feature: The conveyor belt rubber weight is designed to handle expansion and contraction without losing integrity.
4. EcoSmart Balanced Weight Belt:
- Durability: Designed to be durable while using sustainable materials.
- Cost-Effectiveness: The use of recycled materials helps reduce costs, making it very economically viable.
- Manufacturer Reliability: Excellent reliability with a focus on sustainable production methods.
- Key Feature: Features a perfectly balanced conveyor belt rubber weight, which enhances system stability and efficiency.
5. HeavyLoad Iron-Core Conveyor Belt:
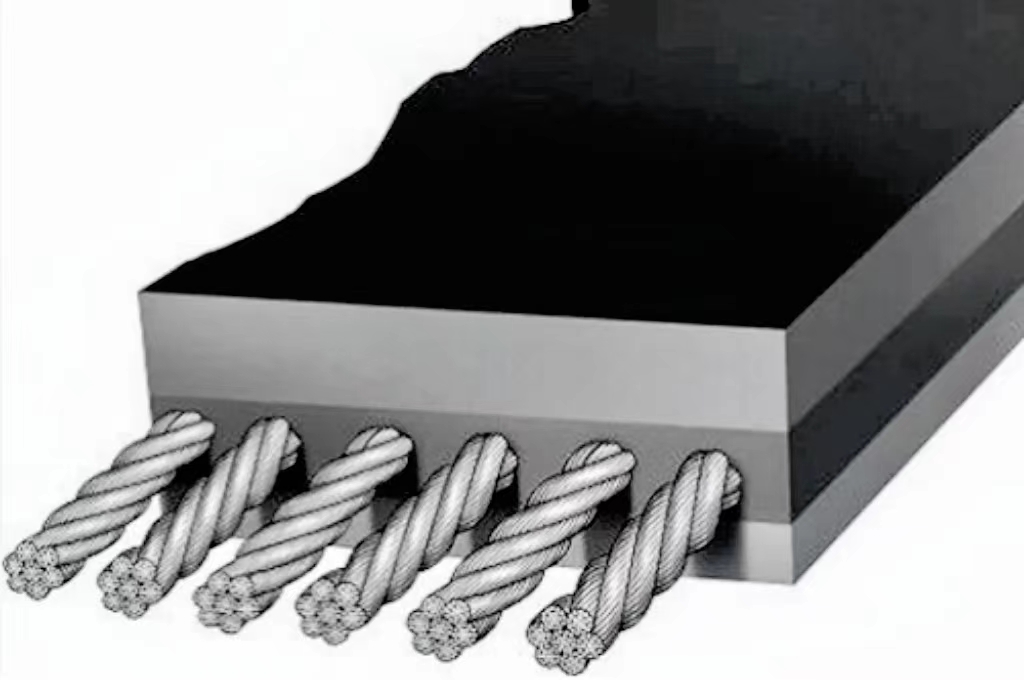
- Durability: Extremely high durability, best for mining operations or any systems requiring movement of particularly heavy materials.
- Cost-Effectiveness: More expensive upfront but pays off in environments where lesser belts fail quickly.
- Manufacturer Reliability: Known for extreme duty belts that seldom fail even under harsh conditions.
- Key Feature: Its conveyor belt rubber weight supports heavy-duty use with an iron core for maximum strength and load capacity.
Each of these products has been chosen for their exemplary performance in key areas critical to the operational success of conveyor systems. When selecting a conveyor belt, consider the specific needs of your operation, including the desired conveyor belt rubber weight, to ensure maximum efficiency and safety.
Maintenance Tips for Preserving Conveyor Belt Rubber Weight and Quality
Maintaining the optimal conveyor belt rubber weight and quality is essential for the longevity and efficiency of your conveyor system. Proper maintenance not only extends the lifespan of the conveyor belt but also ensures it operates at peak performance. Here are ten practical tips to help you preserve the optimal weight and quality of your conveyor belts:
- Regular Inspections: Conduct thorough inspections of the conveyor belt rubber weight and structure at scheduled intervals. Look for signs of wear, tear, and damage. Early detection of issues can prevent them from escalating into costly repairs.
- Correct Tensioning: Ensure the conveyor belt is properly tensioned. Incorrect tensioning can lead to unnecessary stress on the belt, affecting its weight distribution and overall performance. A belt that’s too tight can suffer from premature wear, while one that’s too loose may slip or sag.
- Alignment Checks: Regularly check and adjust the alignment of the conveyor belt. Misalignment can cause uneven wear, which may alter the conveyor belt rubber weight and lead to inefficiencies in operation or even pose a safety risk.
- Cleanliness: Keep the conveyor belt and surrounding area clean. Accumulation of debris can affect the balance and weight of the belt, leading to increased energy consumption and wear.
- Lubrication: Properly lubricate all moving parts in accordance with the manufacturer’s recommendations. Adequate lubrication reduces friction, which can affect the conveyor belt’s weight distribution and operational efficiency.
- Avoid Overloading: Do not exceed the recommended load capacity. Overloading the conveyor belt can alter its conveyor belt rubber weight distribution, lead to stretching or tearing, and reduce its lifespan.
- Repair Damages Promptly: Address any damage to the conveyor belt as soon as possible. Small issues can quickly become significant problems that can change the belt’s weight characteristics and operational capability.
- Quality Replacement Parts: Use high-quality replacement parts for repairs and maintenance. Inferior components can affect the conveyor system’s balance, leading to adjustments in the conveyor belt rubber weight and potentially causing more frequent breakdowns.
- Professional Training: Ensure that all personnel involved in the maintenance and operation of the conveyor system are adequately trained. Knowledgeable staff can better identify potential issues and perform effective maintenance.
- Record Keeping: Keep detailed records of all maintenance activities, inspections, and repairs. This documentation can help identify patterns or recurring issues, contributing to better long-term maintenance strategies and weight management of the conveyor belt.
In addition to these tips, regularly adjusting for balance and alignment is critical. This entails checking the rollers, pulleys, and other components to ensure they are in proper working order and correctly aligned. Such adjustments help distribute the conveyor belt rubber weight evenly, reducing wear and improving efficiency.
By following these maintenance tips, you can ensure the longevity, safety, and efficiency of your conveyor system, preserving the optimal weight and quality of your conveyor belts.
Durable conveyor belts for all your industrial needs. Inquiry now!
Case Studies and Practical Applications: Conveyor Belt Rubber Weight
Industry Examples
Understanding the conveyor belt rubber weight is crucial in various industries, from mining to manufacturing, as it directly impacts operational efficiency and safety. Below are some real-life examples demonstrating the importance of accurate belt weight data:
Mining Industry
In the mining sector, conveyor belts are essential for transporting raw materials. The weight of the conveyor belt affects the overall load capacity of the system. For instance, a mining company in Australia faced frequent belt breakdowns due to underestimating the conveyor belt rubber weight. By recalculating the belt weight and upgrading their systems accordingly, they significantly reduced downtime and increased their material transport efficiency.
Manufacturing Industry
A large automotive parts manufacturer struggled with inconsistent conveyor belt performance, leading to production delays. Upon investigating, they found discrepancies in the conveyor belt rubber weight data used for system design. By using a detailed weight chart and accurate calculations, they optimized their conveyor system. This adjustment not only stabilized the production line but also improved the lifespan of their conveyor belts.
Food Processing Industry
In the food processing industry, conveyor belts are used to transport delicate products. A bakery in the United States encountered issues with belt tension and alignment, affecting the quality of their products. They realized that an incorrect estimation of the conveyor belt rubber weight was the root cause. After consulting a weight calculator and adjusting their system, they achieved smoother operations and consistent product quality.
Success Stories
Case Study 1: Coal Mining Operation
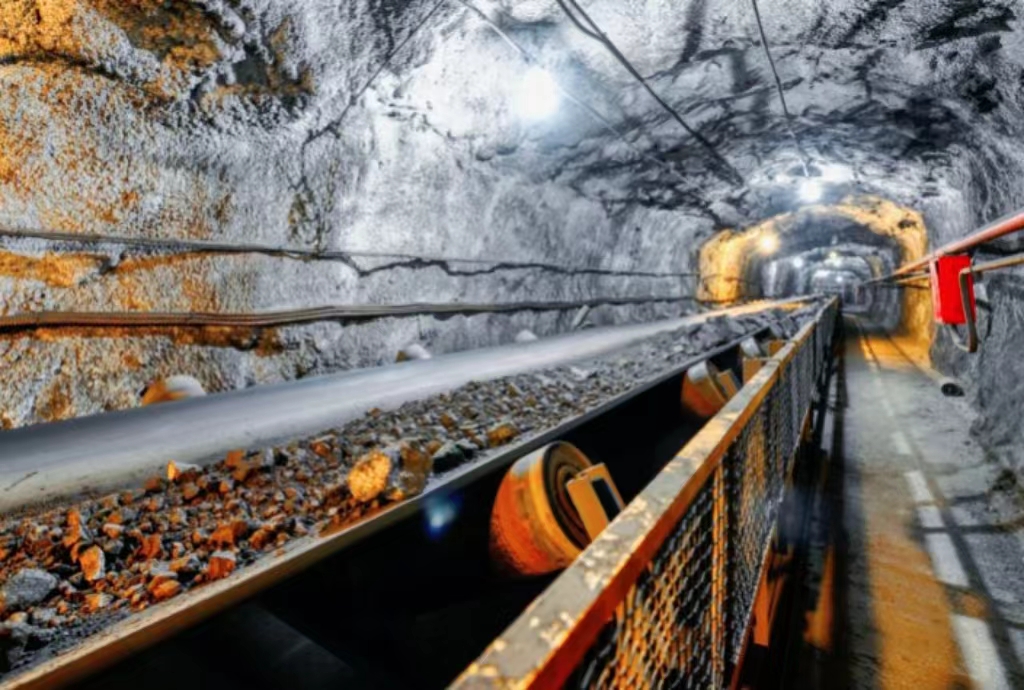
BlackGold Mining Company in South Africa faced significant operational challenges due to frequent conveyor belt failures. The primary issue was the miscalculation of the conveyor belt rubber weight, leading to overloading and subsequent belt wear and tear. The company decided to use an advanced weight calculator from BeltPro Solutions to determine the precise weight of their conveyor belts. With this accurate data, they replaced their existing belts with ones that could handle the actual load. This change resulted in a 40% reduction in downtime and maintenance costs, ultimately boosting their productivity and profitability.
Case Study 2: Automotive Parts Manufacturer
AutoParts GmbH, an automotive parts manufacturer in Germany, experienced frequent production halts due to conveyor belt issues. Their initial calculations of the conveyor belt rubber weight were based on outdated data, which led to excessive strain on the belts. By employing a comprehensive weight chart from BeltMetrics, they were able to enhance the belt’s performance. This optimization led to a 30% increase in production efficiency and a 20% decrease in operational costs. The company’s management praised the decision, highlighting the critical role of accurate belt weight data in their success.
Case Study 3: Food Processing Company
Maple Foods Inc., a food processing company in Canada, used conveyor belts to move large quantities of packaged goods. However, they faced challenges with belt slippage and inconsistent product flow. The root cause was identified as the inaccurate estimation of the conveyor belt rubber weight. By utilizing a detailed weight calculator from ConveyorTech, the company recalculated the belt weight and adjusted their conveyor system. This adjustment not only resolved the slippage issues but also improved the overall efficiency of their production line. The company’s quality assurance team noted a significant improvement in product handling and reduced waste.
Practical Applications
Accurately calculating the conveyor belt rubber weight has several practical applications across industries. Here are some key benefits and applications:
- Optimized Load Management: Knowing the exact weight of the conveyor belt helps in optimizing the load capacity, preventing overloading and reducing wear and tear on the system.
- Improved System Design: Accurate weight data is crucial for designing conveyor systems that are efficient and durable. It helps in selecting the right materials and components for the system.
- Cost Savings: By preventing belt failures and reducing maintenance costs, companies can achieve significant cost savings. Accurate belt weight calculations lead to longer belt life and fewer replacements.
- Enhanced Safety: Ensuring that the conveyor belt weight is correctly calculated enhances the overall safety of the operation. It prevents accidents caused by belt breakages or system overloads.
- Increased Efficiency: With precise weight calculations, conveyor systems operate more smoothly and efficiently, leading to higher productivity and better resource management.
Understanding and accurately calculating the conveyor belt rubber weight is essential for optimizing industrial operations. Whether it’s through using advanced weight calculators, detailed weight charts, or real-life industry applications, accurate belt weight data ensures better performance, safety, and cost efficiency across various sectors.
FAQs about Conveyor Belt Rubber Weight
The weight of a conveyor belt is determined by its dimensions, material, and construction. Typically, the weight is measured in terms of pounds per inch-width and length (PIW). For instance, a belt that is 36 inches wide and 80 feet long with a PIW of 10 would weigh 36 (width) * 80 (length) * 10 (PIW) = 28,800 pounds. To calculate conveyor belt rubber weight, use the Continental Belting calculator with belt width, thickness, length, and top/bottom cover values for accurate results. It’s important to note that various conveyor belt materials and styles will have different PIW values. For example, fabric conveyor belts, steel cord conveyor belts, and solid woven conveyor belts will each have distinctive weights per unit length and width. Knowing the precise weight of a conveyor belt is crucial for calculating the load that the conveyor system is able to handle efficiently and safely.
Conveyor belts are commonly made using various types of rubber to meet different demands of the operational environment. The most frequently used polymers are Natural Rubber (NR), Styrene Butadiene Rubber (SBR), Polybutadiene Rubber (BR), and Nitrile Butadiene Rubber (NBR). Natural rubber is valued for its elasticity and resistance to abrasion, which is useful when conveying materials that cause wear. SBR is often employed for moderate conditions as it provides good abrasion resistance and is more economical. NBR, also known as Nitrile, is chosen for applications involving oils, fats, and waxes due to its resistance to these substances. Sometimes, rubber compounds are used to enhance properties like temperature and chemical resistance, depending on the application requirements.
The density of belt rubber typically ranges between 0.9 to 1.3 grams per cubic centimeter (g/cm³). This can vary based on the type of rubber and the compounding ingredients used during manufacturing. For instance, the addition of fillers, plasticizers, and other additives can influence the density of the rubber. In the context of conveyor belts, a higher density rubber might provide more wear resistance but could also lead to a heavier belt, which impacts the energy efficiency of the conveyor system. On the other hand, lower density rubber may offer advantages like flexibility and impact absorption, beneficial for certain applications. Manufacturers might provide the exact density specifications for the types of rubber used in their conveyor belts.
The counterweight in a conveyor belt is used to create adequate tension in the belt. The goal is to maximize friction between the belt and the drive pulley, thereby preventing slippage.
To calculate the conveyor counterweight, you need to know the tension required for the belt to operate under the optimal speed, and this is dependent on factors like the belt material, dimensions, and loading conditions. The formula used is Te = Lf + (Lm.Wm) + (2.Mi.Wm), where Te is the effective tension, Lf is the load due to the friction in the idler bearings, Lm is the length of the belt, Wm is the weight of the material, and Mi is the load due to the belt on each idler.
This will give you the required tension, which you would then use to calculate the counterweight required. You can do this by multiplying Te with the length of the conveyor belt, and then dividing by the acceleration due to gravity to get the weight required in Newtons.
Please note that these calculations can get complex, and it’s often advantageous to use conveyor design software or consult with engineering professionals. Individuals should ensure they fully understand all parameters before calculating the counterweight for safety purposes.
The weight of a rubber conveyor belt depends on its width, thickness, and length, as well as the weight of its carcass and covers. For example, a 9/16″ thick belt that is 48″ wide typically weighs around 14.4 pounds per foot. To accurately determine the weight, you can use the Continental Belting conveyor belt weight calculator, which takes into account the belt’s width, thickness, length, and the top and bottom cover values. The total weight per foot of the belt, including the carcass and covers, can vary but an average figure is approximately 5.2344 pounds per foot.
Last Updated on June 14, 2024 by Jordan Smith
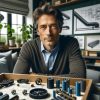
Jordan Smith, a seasoned professional with over 20 years of experience in the conveyor system industry. Jordan’s expertise lies in providing comprehensive solutions for conveyor rollers, belts, and accessories, catering to a wide range of industrial needs. From initial design and configuration to installation and meticulous troubleshooting, Jordan is adept at handling all aspects of conveyor system management. Whether you’re looking to upgrade your production line with efficient conveyor belts, require custom conveyor rollers for specific operations, or need expert advice on selecting the right conveyor accessories for your facility, Jordan is your reliable consultant. For any inquiries or assistance with conveyor system optimization, Jordan is available to share his wealth of knowledge and experience. Feel free to reach out at any time for professional guidance on all matters related to conveyor rollers, belts, and accessories.