Conveyor Belt Manufacturing Process and Production Overview
The conveyor belt manufacturing process is fundamental to various industries, offering efficient material handling solutions in mining, agriculture, logistics, and beyond. With diverse specifications and ratings, conveyor belts ensure continuous, reliable transport of everything from bulk commodities to finished products. This guide provides a comprehensive overview of the conveyor belt manufacturing process, including historical context, material selection, and quality standards. By understanding each step, from compounding to vulcanization, readers will gain valuable insights into optimizing the conveyor belt manufacturing process.
Historical Evolution and Importance of the Conveyor Belt Manufacturing Process
The conveyor belt manufacturing process has undergone significant transformations over time, evolving from early leather belts to modern steel cord and flame-retardant rubber belts. These changes reflect advancements in technology, safety, and industry demands.
Early Innovations in Leather Belt Manufacturing Process
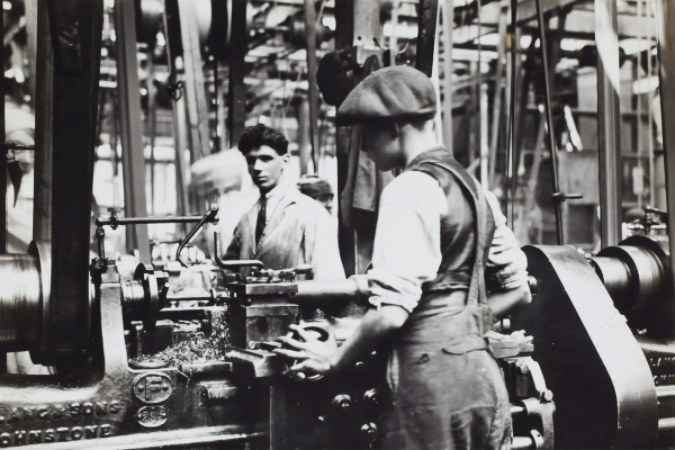
Early conveyor belts were primarily made from leather, which provided flexibility and basic material handling capabilities. The leather belt manufacturing process involved tanning and curing hides to ensure durability. These belts were commonly used in agriculture and mining for lightweight material transport. However, leather belts had limitations, such as susceptibility to stretching, degradation, and poor performance under harsh conditions.
As industrialization progressed in the late 19th and early 20th centuries, industries demanded stronger, more durable belts. This need prompted a gradual transition from leather to rubber and synthetic materials. The introduction of rubber conveyor belts marked a significant improvement in durability, strength, and elongation resistance. Fabric-reinforced and steel cord rubber belts began replacing leather belts in industrial applications due to their superior performance.
Development of Modern Conveyor Belt Manufacturing Techniques
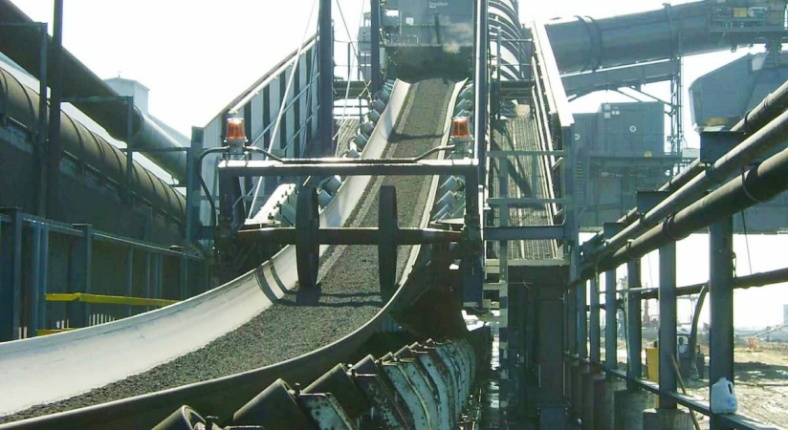
The conveyor belt manufacturing process advanced significantly in the 20th century with the development of modern manufacturing techniques. Steel cord belts, offering high tensile strength and reduced elongation, became crucial for heavy-duty and long-distance material handling. Flame-retardant compounds were also introduced, making conveyor belts safer for use in underground mining and other hazardous environments.
Technological advancements like continuous vulcanization systems revolutionized the conveyor belt manufacturing process. The Rotocure system and other continuous curing methods ensured uniform curing and consistent quality by applying heat and pressure evenly. This technique eliminated variations and inconsistencies in belt curing, leading to more reliable products.
Quality control became increasingly vital as manufacturers aimed to meet international standards and customer specifications. Testing procedures assessed tensile strength, elongation, abrasion resistance, and flame-retardant properties. Modern conveyor belts are rated based on these factors, providing tailored solutions for various industries.
Raw Materials Selection and Their Role in the Conveyor Belt Manufacturing Process
Selecting the right raw materials is crucial in the conveyor belt manufacturing process. The choice of materials, from rubber compounds to reinforcing fabrics and chemical additives, directly influences the performance and durability of the final conveyor belt.
Rubber Compounds in Conveyor Belt Manufacturing
Rubber is the primary material used in the conveyor belt manufacturing process. Understanding the differences between natural and synthetic rubbers is essential for selecting compounds with the desired properties.
Natural Rubber vs. Synthetic Rubber:
Aspect | Natural Rubber | Synthetic Rubber |
---|---|---|
Source | Extracted from latex | Man-made, produced from various chemical compounds |
Types | Natural Rubber | Styrene-Butadiene Rubber (SBR): Good wear resistance and flexibility Nitrile Butadiene Rubber (NBR): Oil resistance Chloroprene Rubber (CR): Superior flame resistance (Neoprene) |
Key Properties | Excellent flexibility High tensile strength Abrasion resistance | SBR: Good wear resistance and flexibility NBR: Oil resistance CR: Flame resistance |
Ideal Applications | Conveyor belts handling cuts, impact, and heavy wear Mining and quarrying | SBR: General-purpose conveyor belts NBR: Oil-resistant belts CR: Flame-resistant belts for underground mining |
Compounding Process | Mixing natural rubber with additives like carbon black, antioxidants, and accelerators | Blending various synthetic rubbers with additives to meet specific conveyor belt specifications |
Reinforcing Materials: Fabric and Steel Cords
Reinforcing materials form the backbone of the conveyor belt, providing tensile strength and limiting elongation.Fabric plies are typically made from synthetic fibers like polyester, nylon, or aramid. Polyester offers low elongation and high tensile strength, making it suitable for belts with moderate load requirements. Nylon is highly flexible and impact-resistant, while aramid provides exceptional heat resistance. These fabric sheets are layered between rubber sheets during the conveyor belt manufacturing process to create a flexible yet strong structure.Steel cords provide high tensile strength and low elongation, making them ideal for long-distance and heavy-duty conveyor belts. They can be arranged longitudinally or in a cross-ply pattern, offering exceptional load-bearing capabilities. Galvanized steel cords are often used to prevent corrosion in harsh environments.
Chemical Compounds for Enhanced Performance
Chemical additives are essential in the conveyor belt manufacturing process, enhancing the performance and durability of the final product.Sulfur is the primary vulcanizing agent, while accelerators like CBS (Cyclohexyl Benzothiazole Sulfenamide) speed up the vulcanization process. These chemicals improve cross-linking between rubber molecules, resulting in enhanced tensile strength and flexibility.Antioxidants and antidegradants protect rubber compounds from oxidation and degradation caused by heat, light, and ozone exposure. Common antioxidants include TMQ (Trimethyl Quinoline) and IPPD (Isopropyl-Phenyl-P-Phenylenediamine).Carbon black is the primary filler, improving tensile strength and abrasion resistance. Plasticizers like paraffin oil increase flexibility, while processing aids improve compound flow during mixing.
Mixing and Compounding Process in Conveyor Belt Manufacturing
The mixing and compounding process is a crucial stage in the conveyor belt manufacturing process. It involves blending raw materials, such as rubber and chemical additives, to create compounds that meet specific mechanical and physical properties required for high-quality conveyor belts.
Essential Mixing Equipment
The choice of mixing equipment plays a pivotal role in ensuring uniformity and consistency in the conveyor belt manufacturing process.Internal mixers, like the Banbury and Intermix mixers, are ideal for blending large batches of rubber compounds.They blend rubber, fillers, and chemicals under controlled temperature and pressure to ensure thorough dispersion of ingredients.A precisely controlled rotor speed, temperature, and pressure are vital to achieving uniformity.Mixing mills are often used as a secondary step after the internal mixer to refine the compound and adjust its plasticity.They consist of two large counter-rotating rollers that compress and shear the rubber compound, ensuring consistent batch quality.They are particularly useful for adding delicate ingredients like sulfur and accelerators late in the process to prevent premature vulcanization.
Compounding Techniques and Material Properties
Compounding techniques directly impact the final properties of the conveyor belt, such as tensile strength, elongation, and abrasion resistance.
Blending Rubber Compounds:Natural and synthetic rubbers are blended with fillers, antioxidants, accelerators, and plasticizers to achieve desired mechanical properties.Carbon black and silica fillers enhance tensile strength and abrasion resistance.Plasticizers like paraffin oil increase flexibility, while antioxidants protect against degradation.
Batch Consistency and Temperature Control:Maintaining consistent batch properties is critical, as variation can lead to uneven belt performance.Temperature control during mixing prevents premature vulcanization and ensures even dispersion of all ingredients.
Tensile Strength and Elongation:Testing involves stretching rubber samples to measure the force required to break them and the degree of elongation.Ensures the compound meets specific conveyor belt specifications.
Abrasion Resistance:Measures the compound’s ability to withstand wear and tear from abrasive materials.Abrasion resistance is critical for belts used in mining and other heavy-duty applications.
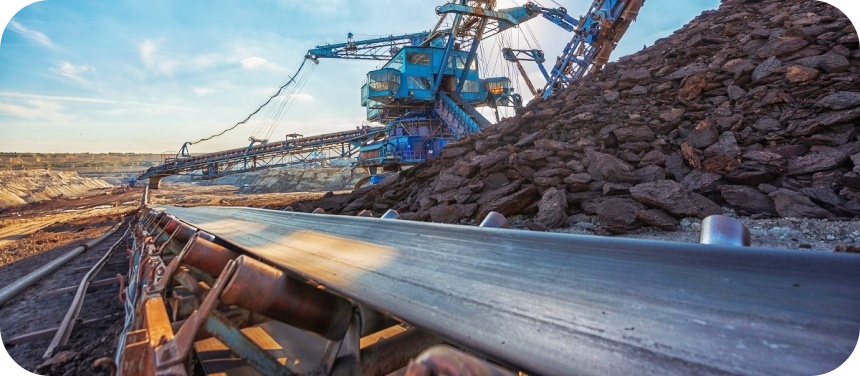
Calendering and Building Process in Conveyor Belt Manufacturing
The calendering and building process is a crucial stage in the conveyor belt manufacturing process. This phase involves rolling rubber compounds into uniform sheets and assembling them with reinforcing materials to build the belt carcass.
Calendering Rubber Sheets and Reinforcing Layers
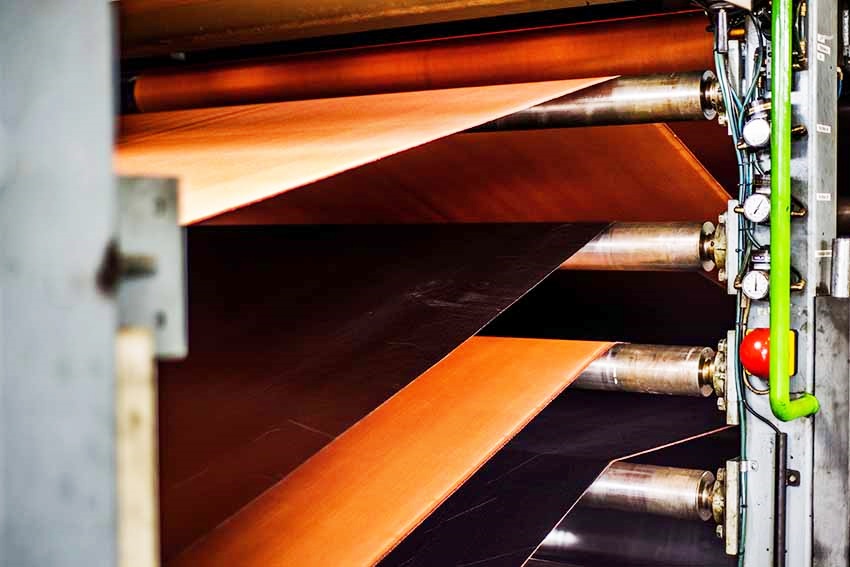
Calendering is the process of rolling rubber compounds into sheets of a specific thickness.
Calendering Process:A calender consists of two or more large, counter-rotating rollers through which the rubber compound is passed to form sheets of uniform thickness.The rollers can be heated or cooled to maintain the required temperature, which helps control the rubber compound’s viscosity and flow properties.The thickness of the resulting sheets is precisely controlled based on the intended conveyor belt specification.
Reinforcing Layers:Fabric or steel cords are applied to the rubber sheets during the calendering process to reinforce the belt carcass.
Fabric Reinforcement:Fabric layers (plies) are typically made of polyester, nylon, or aramid.Polyester offers low elongation, while nylon provides excellent flexibility and impact resistance.Fabric sheets are layered between the rubber sheets to create a flexible yet strong structure.
Steel Cord Reinforcement:Steel cords are arranged longitudinally or in a cross-ply pattern, providing superior tensile strength and low elongation.Galvanized steel cords are used to prevent corrosion.Steel cord belts are ideal for heavy-duty applications requiring high strength and minimal elongation.
Belt Building Techniques and Layer Assembly
The conveyor belt carcass is built by layering rubber sheets with fabric or steel reinforcing materials according to the required specifications. Each layer is carefully aligned to ensure uniform thickness and reinforcement distribution throughout the belt. Additional rubber sheets are applied as top and bottom covers to protect the carcass from external wear and tear.
Fabric belts are constructed with multiple layers of fabric plies, providing flexibility and adaptability for various applications. They are suitable for short to medium-length conveyor systems with moderate load requirements. On the other hand, steel cord belts are constructed with longitudinally arranged steel cords, offering high tensile strength and minimal elongation. These belts are ideal for long-distance and heavy-duty material handling, such as in mining and port operations.
Vulcanization and Curing in the Conveyor Belt Manufacturing Process
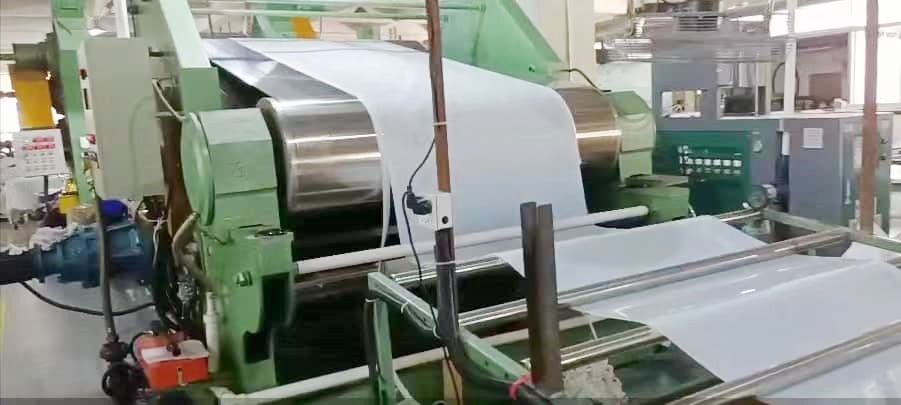
The conveyor belt manufacturing process includes rubber extrusion, fabric lamination, and calendering for optimal strength and durability. Vulcanization and curing are integral steps in the conveyor belt manufacturing process, turning raw rubber compounds into durable, cohesive conveyor belts. This process involves cross-linking rubber molecules under heat and pressure to enhance the belt’s strength, flexibility, and resistance to wear and tear.
Batch Vulcanization Techniques
Batch vulcanization is a traditional curing method involving heat and pressure in a mold or press.In press vulcanization, the belt carcass is placed in a large vulcanizing press or mold. The mold is closed and heated to temperatures ranging from 140°C to 160°C while pressure is applied, ensuring that the rubber compound flows evenly and firmly adheres to the reinforcing layers. This process typically lasts between 30 and 60 minutes, depending on the belt’s thickness and specification.Accurate control of temperature, pressure, and curing time is essential to ensure uniform cross-linking of the rubber molecules. Deviations in these parameters can result in under-cured or over-cured belts, compromising performance and longevity. Continuous monitoring and precise calibration of these variables are necessary to maintain the desired conveyor belt specification.
Continuous Vulcanization Methods
Continuous vulcanization provides a more efficient alternative to batch vulcanization, especially for long belts requiring uniform curing.In continuous vulcanization using Rotocure machines, the belt carcass passes through heated rollers that apply heat and pressure continuously. The belt is fed through the rollers, where it is heated evenly, allowing for consistent vulcanization throughout its length. The cured belt then exits the machine as a continuous product, ready for cutting and finishing.Continuous vulcanization provides several advantages, including efficiency, uniform curing, and customization. The streamlined curing process significantly reduces production time, making it ideal for manufacturing long belts. Uniform heat and pressure application ensures consistent vulcanization, eliminating variations that can occur in batch processes. Furthermore, curing parameters can be easily adjusted to meet specific conveyor belt specifications, enhancing the overall quality.
Quality Control in the Conveyor Belt Manufacturing Process
Quality control is a critical component of the conveyor belt manufacturing process, ensuring that finished belts meet stringent performance, durability, and safety standards. This involves testing the conveyor belts for tensile strength, elongation, adhesion, and abrasion resistance, among other properties.
Key Testing Methods for Conveyor Belt Ratings
Various tests are conducted to assess the performance characteristics and durability of conveyor belts.
Tensile Strength and Elongation Testing Procedures:A sample is clamped between two jaws and pulled until it breaks, measuring the force required.The resulting value is expressed in Newtons per millimeter (N/mm) or pounds per inch (lbs/in).Measures the degree of stretch before the sample breaks, expressed as a percentage of the original length.Helps ensure the belt meets the required elongation specifications for its intended application.Tests the bond strength between the rubber covers and the reinforcing layers (fabric or steel cords).A sample is peeled at a consistent speed, and the force required to separate the layers is measured.
Tear Resistance and Abrasion Resistance:Assesses the belt’s ability to resist tearing from cuts or sharp objects.An “initiated tear test” measures the force required to propagate a pre-existing cut in the belt.Evaluates the belt’s resistance to wear due to friction.The belt sample is placed under a rotating drum, and the mass loss after a set number of rotations is measured.
Conveyor Belt Ratings and Specifications
Conveyor belt ratings and specifications are standardized by international bodies to ensure uniformity and safety across different industries.
What Are ISO, DIN, and Other International Standards:
Standard | Description |
---|---|
ISO Standards | ISO 14890: Specifies requirements for rubber conveyor belts. Defines tensile strength, elongation, and adhesion requirements for various belt types. |
DIN Standards | DIN 22102: Defines standards for textile conveyor belts, including tear resistance and longitudinal flexibility. |
Other Standards | AS 1332 (Australia) BS 490 (UK) JIS K6322 (Japan) provide similar specifications. |
Flame Resistance, Oil Resistance, and Heat Resistance Ratings:
Aspect | Description |
---|---|
Flame Resistance | Evaluates the belt's ability to self-extinguish when exposed to an open flame. Mandatory for belts used in underground mining and other hazardous environments. |
Oil Resistance | Assesses the belt's resistance to swelling or degradation when exposed to oils and chemicals. |
Heat Resistance | Tests the belt's ability to withstand high temperatures without significant degradation. Essential for belts used in foundries and other high-temperature applications. |
Conveyor Belt Thickness and Elongation Standards
The thickness and elongation standards directly impact a conveyor belt’s load capacity and durability.Thicker belts generally offer higher tensile strength and abrasion resistance.However, increased thickness also reduces flexibility, affecting the belt’s ability to navigate small pulleys and curves.Manufacturers must balance these factors based on application requirements.Fabric belts typically have higher elongation limits due to their inherent flexibility. The elongation percentage generally ranges from 1% to 2.5% under full load.Steel cord belts are designed for minimal elongation, often below 0.5%, providing superior load capacity and dimensional stability over long distances.Elongation limits are specified in the conveyor belt manufacturing process to ensure belts meet the operational requirements of different industries.
Packaging and Dispatch in the Conveyor Belt Manufacturing Process
The packaging and dispatch stages are essential components of the conveyor belt manufacturing process, ensuring that belts are cut, finished, and delivered to customers in optimal condition.
Cutting and Finishing Conveyor Belts
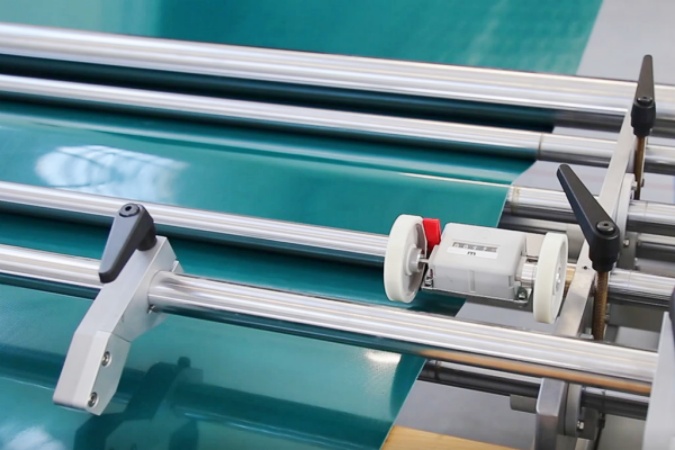
Once vulcanized and quality-checked, conveyor belts are cut and finished according to customer specifications. Cutting machines with high-precision blades are used to slice the belts into desired widths and lengths, ensuring precise dimensions for the specific application. For specialized purposes like inclined conveying or high-temperature resistance, belts may be cut into unique profiles or have additional features integrated.
Protective coatings may be applied to enhance resistance against oil, heat, or abrasion. For instance, belts used in mining or underground environments might receive flame-retardant coatings to meet stringent safety standards. Labels containing vital information, such as belt specifications, ratings, and handling instructions, are affixed to facilitate identification and traceability throughout the supply chain. Proper labeling also provides clear installation and maintenance guidelines to ensure the conveyor belts are used and maintained correctly.
Rolling, Packaging, and Shipping
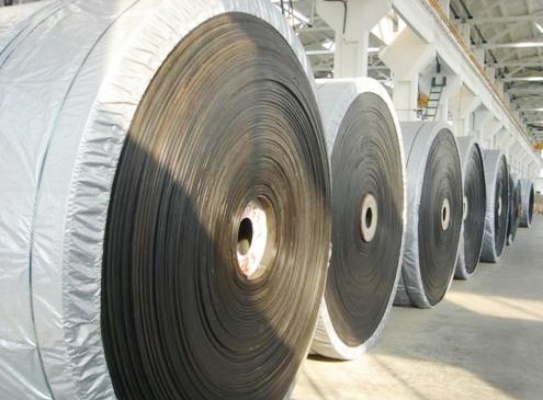
After cutting and finishing, conveyor belts are carefully rolled into compact coils for efficient transportation. Rolling the belts ensures they remain free of creases, cuts, or other damage. A core or spindle may be used to support the roll and maintain its shape. Once rolled, the belts are wrapped in protective packaging, like plastic film or kraft paper, to prevent contamination and damage during shipping. Some belts are packed in wooden crates or boxes, providing extra protection for international shipments.
Shipping labels are attached, indicating the belt type, size, and handling instructions to ensure safe and accurate unloading upon arrival. Manufacturers also include safety and installation instructions for end-users, providing guidelines on how to unroll, splice, and install the conveyor belts properly. Maintenance advice is often included to help extend the conveyor belt’s lifespan and ensure it operates efficiently throughout its service life.
Special Considerations of Conveyor Belt Manufacturing Process
Importance of Selecting the Correct Material (Rubber, Fabric, Metal) Based on Application:
- Application-Specific Requirements: The choice of material for a conveyor belt is crucial to ensure that it meets the specific demands of the application. Different materials offer varying levels of strength, flexibility, and durability, which can significantly impact the performance and longevity of the belt.
- Performance and Efficiency: Using the correct material enhances the efficiency of the conveyor system. For instance, rubber belts are ideal for heavy-duty applications due to their high tensile strength and durability, while fabric belts may be more suitable for light to medium-duty tasks where flexibility and cost-effectiveness are important.
- Cost Implications: Selecting the appropriate material can also affect the overall cost. While some materials may have a higher initial cost, their durability and performance can lead to long-term savings by reducing maintenance and replacement costs.
Considerations for Temperature, Moisture, and Chemical Resistance:
- Temperature Resistance: Conveyor belts used in high-temperature environments, such as metal processing or baking industries, must be made from materials that can withstand extreme heat without degrading. Materials like heat-resistant rubbers or special heat-resistant resins are often used in these applications.
- Moisture Resistance: In applications where the conveyor belt is exposed to moisture or operates in wet environments, materials that are resistant to water absorption and hydrolysis are essential. This prevents the belt from weakening or deteriorating over time. Materials such as PVC or polyurethane are commonly used for their moisture-resistant properties.
- Chemical Resistance: For industries like chemical manufacturing or food processing, where the belt may come into contact with various chemicals, selecting a material that is resistant to chemical corrosion is critical. Rubber belts with specific chemical-resistant formulations or belts made from stainless steel are often chosen for these environments.
Use of Stainless Steel or Heat-Resistant, Non-Contaminating Plastic Resins:
- Stainless Steel Belts: Stainless steel conveyor belts are preferred in food and beverage processing due to their durability, corrosion resistance, and ease of cleaning. They do not rust and can withstand the rigorous cleaning processes required to maintain hygiene standards.
- Heat-Resistant Resins: In processes where the belt is exposed to high temperatures, such as baking or cooking, heat-resistant plastic resins are used. These materials can endure high temperatures without releasing harmful substances or degrading, ensuring the safety and quality of the food products.
Compliance with FDA or USDA Regulations:
- Material Safety: Materials used in conveyor belts for food processing must comply with FDA or USDA regulations to ensure they are safe for contact with food. This includes using materials that do not leach harmful chemicals and are resistant to bacterial growth.
- Ease of Cleaning: The design and material of the conveyor belt should allow for easy cleaning and sanitization to maintain food safety standards. Belts made from materials that are non-porous and smooth are preferred as they do not harbor bacteria and can be cleaned thoroughly.
- Documentation and Certification: Manufacturers must provide proper documentation and certification that their conveyor belts meet the necessary regulatory standards. This helps food processing companies maintain compliance with industry regulations and avoid potential legal issues.
These special considerations ensure that conveyor belts are tailored to meet the specific needs of different industries, enhancing performance, safety, and regulatory compliance.
Discover our durable conveyor belts – reach out today!
Innovations and Future Trends in the Conveyor Belt Manufacturing Process
The conveyor belt manufacturing process is evolving rapidly, driven by the need for sustainable practices, advanced materials, and predictive technologies. Innovations in sustainability initiatives and technological advancements are shaping the future of conveyor belt manufacturing.
Sustainability Initiatives and Eco-Friendly Materials
Sustainability is becoming increasingly important in the conveyor belt manufacturing process. Manufacturers are implementing recycling programs to repurpose used belts and reduce waste. Recycled rubber compounds are incorporated into new belts, decreasing the reliance on virgin materials and promoting a circular economy. Sustainable fillers like rice husk ash and renewable silica are being used to develop eco-friendly rubber compounds, reducing environmental impact while maintaining high-quality standards.
Furthermore, efficient manufacturing processes have been developed to reduce the carbon footprint. Continuous vulcanization systems, such as Rotocure machines, streamline the curing process, significantly improving energy efficiency. Water-based adhesives and coatings are replacing traditional solvent-based alternatives, cutting down on emissions and health hazards. These initiatives not only lower production costs but also help manufacturers meet stringent environmental regulations.
Technological Advances in Conveyor Belt Manufacturing
Technological advancements are playing a crucial role in enhancing the conveyor belt manufacturing process. Smart conveyor belts equipped with embedded sensors allow for predictive maintenance. These sensors monitor belt health in real-time, measuring parameters like temperature, wear, elongation, and vibration. By providing early warning signs of potential issues, predictive maintenance enables operators to address problems before they lead to costly downtime or accidents.
In addition to predictive maintenance, new lightweight, high-strength materials like aramid and carbon fiber are transforming the industry. Aramid belts, five times lighter than steel cord belts, offer comparable tensile strength, making them ideal for long-distance and high-speed conveying. Carbon fiber belts, known for their exceptional resistance to corrosion and temperature extremes, increase durability in challenging environments. These materials contribute to energy efficiency and help conveyor belts meet stricter conveyor belt specifications and ratings.
FAQs about Conveyor Belt Manufacturing Process
Belts are manufactured through a series of well-defined stages in the conveyor belt manufacturing process. First, raw materials such as natural and synthetic rubber compounds, fabric plies, and steel cords are mixed and compounded to create a rubber base with specific properties. The compounding process involves blending these rubber compounds with additives like carbon black, antioxidants, and accelerators to achieve the desired strength, flexibility, and resistance properties.
Once the rubber compound is prepared, it undergoes calendering, where it is rolled into sheets and layered with reinforcing materials like fabric or steel cords. The layered structure is then assembled into a belt carcass. This carcass is vulcanized to form a cohesive, durable structure, which can be achieved through either batch or continuous vulcanization methods.
After vulcanization, the belts are cut to customer specifications, and protective coatings or labels are applied. The final step involves rolling, packaging, and dispatching the belts to customers, often with detailed installation and maintenance instructions to ensure proper use.
Calendering is a crucial step in the conveyor belt manufacturing process, where rubber compounds are rolled into sheets of uniform thickness and reinforced with fabric or steel cords. The calender consists of counter-rotating rollers that compress the rubber compound, forming sheets of specific thickness according to conveyor belt specifications.
During the calendering process, the rubber sheets are layered with reinforcing materials like polyester or nylon fabric or steel cords. Fabric plies provide flexibility, while steel cords offer superior tensile strength and low elongation. The rubber sheets adhere firmly to these reinforcing materials, forming the belt carcass. After calendering, additional layers of rubber are added as top and bottom covers to protect the carcass from wear and environmental factors. The final product is a strong, durable conveyor belt ready for vulcanization and finishing.
Calendering ensures that the reinforcing materials are uniformly distributed throughout the belt carcass, providing consistent tensile strength, elongation resistance, and load-bearing capabilities. Properly calibrated rollers, temperature control, and mixing mills are essential for producing high-quality conveyor belts during the calendering process.
In the conveyor belt manufacturing process, a variety of materials are used, each chosen for their specific properties to create high-quality conveyor belts. The primary materials include:
Rubber Compounds:
Natural Rubber: Offers excellent flexibility, tensile strength, and abrasion resistance.
Synthetic Rubber (e.g., SBR, NBR, CR): Provides specialized properties like oil, heat, and flame resistance.
Reinforcing Materials:
Fabric Plies (e.g., Polyester, Nylon, Aramid): Provide flexibility and strength.
Steel Cords: Offer high tensile strength and low elongation.
Chemical Additives:
Accelerators, antioxidants, and antidegradants enhance durability and flexibility.
Fillers like carbon black improve abrasion resistance.
Rubber compounds are blended, calendered, and vulcanized to produce conveyor belts that meet specific industry requirements for tensile strength, elongation, and resistance to heat, abrasion, and chemicals. Fabric or steel cords are layered during the calendering process to reinforce the rubber sheets, providing strength and flexibility. Additional chemical compounds like sulfur, plasticizers, and processing aids are used to improve durability, flexibility, and resistance to various environmental factors.
V-belts are manufactured using a process similar to conveyor belts but with specific adjustments to achieve the desired V-shape. Here’s a step-by-step overview of how V-belts are manufactured in the conveyor belt manufacturing process:
Compounding and Mixing:Rubber compounds are blended to achieve desired properties like flexibility and tensile strength. Reinforcing materials like polyester or aramid cords are selected for their tensile strength and low elongation.
Calendering and Building:Rubber sheets are calendered and layered around reinforcing cords. The core of the V-belt is built by wrapping the rubber sheets and cords into the desired V-shape.
Vulcanization:The assembled V-belt is placed in a mold and vulcanized under heat and pressure to form the final V-shape. Vulcanization ensures that the rubber adheres firmly to the reinforcing cords and provides the necessary strength and flexibility.
Cutting and Finishing:The vulcanized V-belt is cut to the required dimensions and inspected for quality. Protective coatings may be applied to improve resistance to heat, oil, or abrasion.
Packaging and Dispatch:Finished V-belts are packaged and labeled for dispatch, ensuring proper identification and handling instructions.
The result is a durable, reliable V-belt capable of transmitting power efficiently across a wide range of industrial applications.
The process of manufacturing conveyor belts involves several key steps:
Material Preparation: The rubber compound is plasticized in an extruder to make it pliable.
Shaping and Preforming: The plasticized rubber is fed into a preform head and then enters the calender to achieve the desired thickness and width.
Fabric and Carcass Construction: Fabric layers, usually polyester or nylon, are coated with rubber during calendering, and additional rubber sheets are applied as cover sheets.
Lamination: The calendered fabric carcasses are passed through a laminating table to bond multiple layers together, forming the belt’s core.
Vulcanization: The belt undergoes a curing process with heat and sulfur to create cross-links in the rubber, enhancing its strength and durability.
Inspection and Quality Control: The final belts are inspected for defects and tested for tensile strength and other mechanical properties.
Customization and Finishing: The belts are cut, trimmed, and customized to specific requirements before being prepared for shipping.
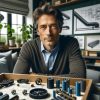
Jordan Smith, a seasoned professional with over 20 years of experience in the conveyor system industry. Jordan’s expertise lies in providing comprehensive solutions for conveyor rollers, belts, and accessories, catering to a wide range of industrial needs. From initial design and configuration to installation and meticulous troubleshooting, Jordan is adept at handling all aspects of conveyor system management. Whether you’re looking to upgrade your production line with efficient conveyor belts, require custom conveyor rollers for specific operations, or need expert advice on selecting the right conveyor accessories for your facility, Jordan is your reliable consultant. For any inquiries or assistance with conveyor system optimization, Jordan is available to share his wealth of knowledge and experience. Feel free to reach out at any time for professional guidance on all matters related to conveyor rollers, belts, and accessories.