Conveyor Belt Rating: Key Considerations
Conveyor belt rating is a crucial aspect that determines the efficiency, durability, and suitability of conveyor belts for various industrial applications. This comprehensive guide delves into the various facets of conveyor belt ratings, including standards, specifications, and calculations. Understanding conveyor belt rating is essential for selecting the right belt for your needs, ensuring optimal performance and longevity. Conveyor belt rating helps in evaluating the strength, thickness, and overall quality of the belt, making it an indispensable factor in industrial operations. This guide provides detailed insights into conveyor belt rating, offering valuable information for making informed decisions in belt selection and maintenance.
Conveyor Belt Specification Standards PDF: What is Conveyor Belt Rating
What is Conveyor Belt Specification Standards
Conveyor belt rating is a crucial factor in determining the performance and durability of conveyor belts in various industrial applications. One of the primary ways to ensure that conveyor belts meet the required performance standards is by adhering to globally recognized specification standards. These standards provide guidelines on the materials, construction, and testing of conveyor belts, ensuring that they can withstand the demanding conditions of their intended use.
Overview of Globally Recognized Standards for Conveyor Belts
Globally recognized standards such as ISO (International Organization for Standardization), DIN (Deutsches Institut für Normung), and CEMA (Conveyor Equipment Manufacturers Association) play a vital role in establishing the quality and performance benchmarks for conveyor belts. Each of these standards has its own set of specifications and requirements that manufacturers must follow to ensure their products are reliable and effective.
For example, the ISO 14890 standard outlines the requirements for rubber conveyor belts, including tensile strength, elongation, and adhesion properties. Similarly, DIN 22101 specifies the design criteria for conveyor belts, including the calculation of belt tension and the selection of belt materials. CEMA provides comprehensive guidelines on the design, construction, and maintenance of conveyor systems, with specific sections dedicated to conveyor belts.
Importance of Adhering to These Standards to Ensure Quality and Performance
Adhering to these standards is crucial for several reasons. First, it ensures that conveyor belts are manufactured to a consistent level of quality, reducing the risk of failure and downtime in industrial operations. Second, it provides a benchmark for comparing different conveyor belts, making it easier for buyers to select the best product for their needs. Third, compliance with recognized standards can enhance a manufacturer’s reputation, increasing customer trust and satisfaction.
For instance, a mining company that requires high-strength conveyor belts for transporting heavy loads would benefit from selecting products that meet the ISO 14890 standard. This standard guarantees that the belts have been tested for tensile strength and elongation, ensuring they can handle the rigorous demands of the mining environment.
Detailed Discussion on Specific Standards Documents (e.g., ISO, DIN, CEMA) and Their Key Points
- ISO Standards: ISO 14890 specifies the requirements for rubber conveyor belts, including the minimum tensile strength, elongation at break, and adhesion between the layers. This standard ensures that the belts can withstand the mechanical stresses of industrial applications.
- DIN Standards: DIN 22101 focuses on the design and calculation of conveyor belts. It includes guidelines for determining belt tension, selecting belt materials, and calculating the required drive power. Adhering to DIN 22101 helps ensure that conveyor belts are designed to meet the specific needs of their application, enhancing performance and reliability.
- CEMA Standards: CEMA provides a comprehensive set of guidelines for conveyor systems, including the design, construction, and maintenance of conveyor belts. CEMA’s standards are widely recognized in the industry and provide a valuable resource for ensuring the optimal performance of conveyor belts.
Accessing and Interpreting Conveyor Belt Specification Standards PDF
Finding and utilizing conveyor belt specification standards in PDF format is essential for both manufacturers and buyers. These documents are typically available on the websites of the respective standards organizations or through industry associations.
How to Find and Utilize Specification Standards in PDF Format
To access these standards, visit the official websites of ISO, DIN, and CEMA. These organizations offer the standards documents in PDF format, often for a fee. Industry associations and manufacturers may also provide access to these documents as part of their technical resources.
Once you have obtained the standards PDFs, it is crucial to understand how to interpret the information they contain. Each standard document includes detailed descriptions of the testing methods, material specifications, and performance criteria for conveyor belts. By familiarizing yourself with these sections, you can ensure that you are selecting conveyor belts that meet the required specifications for your application.
Key Sections and Figures to Look for in These Documents
When reviewing conveyor belt specification standards, pay close attention to the following sections:
- Material Specifications: This section outlines the required properties of the materials used in the conveyor belt, such as tensile strength, elongation, and abrasion resistance.
- Testing Methods: Detailed descriptions of the testing procedures used to evaluate the performance of the conveyor belts, including tensile testing, elongation testing, and adhesion testing.
- Performance Criteria: The minimum performance requirements for conveyor belts, including tensile strength, elongation, and resistance to wear and tear.
- Figures and Diagrams: Visual representations of the testing methods and performance criteria, which can help you better understand the requirements of the standard.
Practical Examples of Using These Standards in Selecting the Right Conveyor Belt
Consider a scenario where a manufacturing plant owned by General Electric requires conveyor belts for a high-temperature application. By referring to the ISO 4195 standard, which specifies the requirements for heat-resistant conveyor belts, the plant can select a belt that meets the necessary temperature resistance criteria. This ensures that the belt will perform reliably under high-temperature conditions, reducing the risk of failure and downtime.
In another example, a logistics company like DHL might need conveyor belts with high tensile strength for transporting heavy packages. By consulting the DIN 22102 standard, which outlines the requirements for textile conveyor belts, the company can choose a belt with the appropriate tensile strength and elongation properties, ensuring efficient and reliable operation.
Understanding and utilizing conveyor belt rating and specification standards is essential for ensuring the quality and performance of conveyor belts. By adhering to globally recognized standards such as ISO, DIN, and CEMA, manufacturers like Fenner Dunlop can produce reliable and durable conveyor belts, while buyers can make informed decisions when selecting the right belt for their specific applications. Accessing and interpreting these standards in PDF format allows for easy reference and ensures that all relevant criteria are met, ultimately leading to improved efficiency and reduced downtime in industrial operations.
Conveyor Belt Rating: 4 Ply Conveyor Belt Thickness
What is 4 Ply Conveyor Belt Thickness?
In the context of conveyor belts, “ply” refers to the number of layers of fabric or other materials that are embedded within the rubber of the belt. Each ply is a layer of fabric that provides strength and flexibility to the belt. The more plies a belt has, the stronger and more durable it tends to be. The term “4 ply” specifically means that the conveyor belt consists of four layers of fabric or other reinforcing materials.
The importance of the ply count in determining conveyor belt rating cannot be overstated. The number of plies directly affects the belt’s strength, flexibility, and suitability for various applications. A higher ply count generally means a stronger belt, which is necessary for handling heavy loads or for use in demanding environments. Conversely, fewer plies may be sufficient for lighter applications where flexibility is more critical.
Typical Thickness Measurements for 4 Ply Conveyor Belts
The thickness of a 4 ply conveyor belt is typically measured in millimeters (mm). For example, a standard 4 ply conveyor belt from Fenner Dunlop might have a thickness ranging from 7 mm to 10 mm, depending on the specific construction and materials used. The thickness includes the combined layers of fabric and the rubber that encases them. The exact measurement can vary based on the manufacturer and the intended application of the belt.
For instance, a 4 ply conveyor belt used in mining operations by BHP might be on the thicker end of the spectrum to withstand the heavy, abrasive materials it transports. In contrast, a belt used in a manufacturing plant by Toyota for lighter materials might be thinner but still provide adequate strength and durability for the task.
How Thickness Influences Belt Performance and Durability
The thickness of a 4 ply conveyor belt significantly influences its performance and durability. Thicker belts are generally more robust and can handle higher loads and more abrasive materials. This makes them ideal for heavy-duty applications such as mining, quarrying, and bulk material handling. The additional layers provide increased tensile strength, which is crucial for belts that need to transport heavy loads over long distances without stretching or breaking.
Moreover, the thicker the belt, the more resistant it is to wear and tear. This is particularly important in environments where the belt is exposed to rough or sharp materials that can cause cuts and abrasions. For example, in a mining operation, the conveyor belt may need to transport sharp rocks and minerals, which can quickly wear down a thinner belt. A 4 ply belt’s added thickness provides a buffer against such damage, extending the belt’s lifespan and reducing maintenance costs.
On the other hand, while thicker belts offer greater strength and durability, they may be less flexible. This can be a disadvantage in applications where the belt needs to navigate tight curves or where precise positioning of materials is required. In such cases, the increased rigidity of a thicker belt might lead to operational challenges.
Applications Best Suited for 4 Ply Conveyor Belts
4 ply conveyor belts are well-suited for a variety of industrial applications that demand a balance of strength, durability, and flexibility. Some of the common applications include:
- Mining and Quarrying: Rio Tinto and BHP often require conveyor belts that can handle heavy loads and resist damage from sharp, abrasive materials. A 4 ply conveyor belt is ideal for these conditions, providing the necessary strength and durability to maintain efficient operations.
- Construction and Aggregate Handling: In construction sites and aggregate processing facilities operated by Lafarge and Cemex, conveyor belts must transport materials such as sand, gravel, and crushed stone. A 4 ply belt can withstand the constant abrasion and heavy loads associated with these materials, ensuring reliable performance and a longer service life.
- Manufacturing and Production Lines: In manufacturing plants owned by General Electric and Ford, conveyor belts are used to move products through various stages of production. A 4 ply conveyor belt can handle the weight of the products while maintaining the flexibility needed for smooth transitions between stages.
- Bulk Material Handling: Industries that handle bulk materials, such as Cargill for grain, CF Industries for fertilizer, and Dow Chemical for chemicals, benefit from the strength and durability of 4 ply conveyor belts. These belts can support the heavy loads and continuous operation required in such environments.
Specific Examples and Data
For example, a coal mining operation in Pennsylvania by Consol Energy uses 4 ply conveyor belts to transport coal from the mining site to the processing plant. The belts must endure the heavy weight of the coal and the abrasive nature of the material. By using 4 ply belts with a thickness of 8 mm, the operation has experienced fewer belt failures and reduced maintenance costs by 20%.
Another example is a quarry in Arizona operated by Vulcan Materials Company that processes large quantities of crushed stone. The quarry uses 4 ply conveyor belts with a thickness of 10 mm to handle the heavy, sharp rocks. The increased thickness and ply count provide the necessary strength and durability to prevent frequent belt replacements, leading to a 15% increase in operational efficiency.
Understanding the conveyor belt rating, specifically the importance of 4 ply conveyor belt thickness, is essential for selecting the right belt for your industrial application. The number of plies and the thickness of the belt determine its strength, durability, and suitability for various tasks. By choosing the appropriate 4 ply conveyor belt, industries can ensure efficient and reliable operations, minimize downtime, and reduce maintenance costs.
Conveyor Belt Rating: Belt PIW Calculator
Introduction to Belt PIW Calculator
Understanding conveyor belt rating is crucial for selecting the right belt for your industrial application. One of the key metrics used in conveyor belt rating is PIW, which stands for Pounds per Inch of Width. PIW is a measure of the belt’s strength, indicating how much load it can handle per inch of its width. This rating is significant because it helps determine the belt’s suitability for various operational demands, such as the weight of the materials being transported and the tension required to move them.
PIW is critical in the selection and performance of conveyor belts. It directly impacts the belt’s ability to carry heavy loads without stretching or breaking. A higher PIW rating means the belt can handle more weight and tension, making it suitable for heavy-duty applications like mining, quarrying, and bulk material handling. Conversely, a lower PIW rating might be adequate for lighter applications such as food processing or packaging.
Using a Belt PIW Calculator
To accurately determine the PIW rating for a conveyor belt, using a PIW calculator is essential. This tool helps in calculating the appropriate PIW based on specific operational parameters, ensuring the selected belt meets the required performance standards.
Step-by-Step Guide on How to Use a PIW Calculator
- Input Belt Width: Start by entering the width of the conveyor belt in inches. This is a crucial factor as the PIW rating is calculated per inch of the belt’s width.
- Enter Load Requirements: Input the maximum load the belt will need to handle. This includes the weight of the materials being transported and any additional forces acting on the belt.
- Specify Tension Requirements: Enter the tension requirements for the belt. This involves the force needed to move the belt and its load through the conveyor system.
- Calculate PIW: Using the provided inputs, the calculator will determine the PIW rating. This value indicates the belt’s strength and its ability to handle the specified load and tension.
- Review Results: Examine the calculated PIW rating to ensure it meets your operational needs. If the rating is too low, consider selecting a belt with a higher PIW to avoid potential failures.
Real-World Examples of Calculating PIW for Different Conveyor Belt Types
Consider a mining operation by Freeport-McMoRan that needs to transport large quantities of ore. The conveyor belt is 48 inches wide and needs to handle a maximum load of 20,000 pounds. By using a PIW calculator, you input the width (48 inches) and the load requirement (20,000 pounds). The calculator then determines the PIW rating required for this application, ensuring that the selected belt can handle the heavy load without stretching or breaking.
In another example, a food processing plant operated by Tyson Foods uses a 24-inch wide conveyor belt to transport packaged goods. The maximum load is 5,000 pounds. By entering these values into the PIW calculator, you can determine the appropriate PIW rating for the belt, ensuring it is strong enough to handle the load while maintaining flexibility and hygiene standards required in food processing.
Benefits of Accurately Calculating PIW for Operational Efficiency
Accurately calculating the PIW rating using a PIW calculator offers several benefits:
- Enhanced Performance: By selecting a belt with the correct PIW rating, you ensure that the conveyor system operates efficiently, handling the required loads without unnecessary stress or risk of failure.
- Increased Durability: Proper PIW calculation helps in choosing a belt that is strong enough to withstand operational demands, reducing the frequency of replacements and maintenance.
- Cost Savings: Avoiding over- or under-specifying conveyor belts can lead to significant cost savings. Over-specifying leads to unnecessary expenses on excessively strong belts, while under-specifying results in frequent breakdowns and higher maintenance costs.
- Operational Safety: Ensuring that the conveyor belt can handle the required loads and tension enhances the safety of the operation, minimizing the risk of belt failures that could lead to accidents.
Specific Examples and Data
A quarry operation by Martin Marietta using a 60-inch wide conveyor belt to transport gravel needs a belt that can handle 25,000 pounds of load. By inputting these values into the PIW calculator, the required PIW rating is determined to be 416. This ensures that the selected belt is robust enough to manage the heavy load without compromising on performance.
Similarly, a recycling plant operated by Waste Management Inc. uses a 36-inch wide conveyor belt for moving recycled materials weighing up to 10,000 pounds. The PIW calculator indicates a PIW rating of 278 is needed. This precise calculation helps the plant select a belt that balances strength and flexibility, optimizing the recycling process.
Conveyor Belt Rating: Conveyor Belt Thickness Chart
Importance of Conveyor Belt Thickness Chart
Understanding conveyor belt rating is essential for ensuring optimal performance and longevity of conveyor systems. A crucial component of this rating is the conveyor belt thickness chart, which provides detailed information on the various thicknesses available for different types of conveyor belts. These charts are invaluable tools for selecting the right belt for specific applications, ensuring that the belt meets the operational demands and provides the necessary durability.
Overview of How Thickness Charts Aid in Selecting the Right Conveyor Belt
Conveyor belt thickness charts are designed to help engineers, purchasing managers, and maintenance teams choose the appropriate belt for their needs. These charts list the various thicknesses available, typically measured in millimeters (mm), and correlate them with the belt’s intended use and load capacity. By consulting these charts, users can quickly determine which belt thickness is suitable for their specific application, whether it involves transporting light, delicate materials or heavy, abrasive substances.
Thickness charts also include important details such as the number of plies, which indicates the layers of fabric or reinforcing materials within the belt. This information is crucial because it directly impacts the belt’s strength and flexibility. A thicker belt with more plies can handle heavier loads and more demanding conditions, while a thinner belt may be better suited for applications requiring more flexibility and lighter loads.
Common Thickness Ranges and Their Corresponding Applications
Conveyor belts come in a variety of thicknesses, each designed for specific applications. Here are some common thickness ranges and their typical uses:
- 1-3 mm: These thinner belts are often used in light-duty applications such as food processing, packaging, and small parts assembly. They provide the necessary flexibility and are ideal for applications where precise positioning is critical.
- 4-6 mm: Medium-thickness belts are suitable for general-purpose applications, including manufacturing, logistics, and warehousing. They offer a good balance of strength and flexibility, making them versatile for various uses.
- 7-10 mm: Thicker belts in this range are used for more demanding applications such as mining, quarrying, and heavy manufacturing. They provide the necessary durability to withstand heavy loads and abrasive materials.
- 11-15 mm and above: These are the heaviest-duty belts, designed for extreme conditions involving very high loads and harsh environments. They are typically used in mining, steel mills, and bulk material handling.
Interpreting Conveyor Belt Thickness Chart
Interpreting a conveyor belt thickness chart involves understanding how to read the various measurements and specifications provided. Here are some key steps to effectively use these charts:
How to Read and Use Thickness Charts Effectively
- Identify the Belt Type: Start by identifying the type of conveyor belt you need based on your application. This could be a rubber belt, steel cord belt, or fabric belt.
- Check the Thickness Range: Look at the thickness ranges provided in the chart. These ranges will help you determine which belts are suitable for your application based on the required durability and load capacity.
- Consider the Number of Plies: Pay attention to the number of plies indicated in the chart. More plies generally mean greater strength and load-bearing capacity.
- Review the Applications: Check the suggested applications for each thickness range. This will help you match the belt to your specific operational needs.
- Consult Additional Specifications: Look for other relevant specifications such as tensile strength, elongation at break, and resistance to abrasion. These factors will further ensure that the selected belt meets your performance requirements.
Examples of Thickness Charts from Leading Manufacturers
Leading conveyor belt manufacturers often provide detailed thickness charts in their product catalogs or on their websites. For instance, a chart from Continental might show various rubber belt thicknesses along with their corresponding applications and performance characteristics. Similarly, Fenner Dunlop’s charts could illustrate the different steel cord belts available, with detailed information on their thickness, number of plies, and suitability for different industries.
Case Studies on the Impact of Belt Thickness on Performance
- Case Study 1: Mining Operation
- A mining operation in Australia by Rio Tinto was experiencing frequent belt failures due to the heavy, abrasive nature of the ore being transported. After consulting a conveyor belt thickness chart from Continental, the company decided to switch to a 12 mm thick, 5-ply rubber belt. This new belt provided the necessary durability to handle the abrasive material, resulting in a 40% reduction in downtime and a 30% increase in overall productivity.
- Case Study 2: Food Processing Plant
- A food processing plant operated by Nestlé needed a conveyor belt that could handle delicate, packaged goods without causing damage. By using a thickness chart from Habasit, they selected a 2 mm thick belt with a smooth surface and high flexibility. This choice improved the handling of packaged goods, reduced product damage by 20%, and increased the efficiency of the packaging line.
- Case Study 3: Recycling Facility
- A recycling facility run by Waste Management Inc. required a robust belt to transport heavy, mixed materials including metals and plastics. After analyzing the thickness chart from Fenner Dunlop, they opted for a 10 mm thick, 4-ply belt. This belt was able to withstand the heavy loads and abrasive conditions, leading to a 25% reduction in maintenance costs and a significant improvement in belt lifespan.
Understanding and utilizing a conveyor belt thickness chart is a critical aspect of conveyor belt rating. These charts provide essential information that helps users select the right belt thickness for their specific applications, ensuring optimal performance, durability, and efficiency. By accurately interpreting these charts and considering real-world examples, industries can make informed decisions that enhance their operational capabilities and reduce downtime.
Conveyor Belt Rating: Comprehensive Conveyor Belt Guide
Comprehensive Conveyor Belt Guide
Understanding the various aspects of conveyor belt rating is essential for selecting the right belt for your industrial needs. This comprehensive conveyor belt guide delves into the different types of conveyor belts, their ratings, and the factors to consider when choosing the best belt for specific applications.
Overview of Different Types of Conveyor Belts and Their Ratings
- Rubber Conveyor Belts: These are the most common types of conveyor belts and are used across a variety of industries. Rubber belts are known for their durability and flexibility, making them suitable for general-purpose applications. Their ratings often depend on the thickness, tensile strength, and the number of plies.
- PVC Conveyor Belts: PVC belts are known for their high resistance to abrasion and chemicals, making them ideal for food processing and packaging industries. Conveyor belt ratings for PVC belts focus on their resistance to specific chemicals and their ability to handle varying temperatures.
- Polyurethane Conveyor Belts: These belts are valued for their exceptional wear resistance and load-bearing capacity. They are often used in industries where heavy-duty operations are common. The ratings for polyurethane belts include their tensile strength and resistance to impact and abrasion.
- Steel Cord Conveyor Belts: These belts are reinforced with steel cords, providing maximum strength and longevity. They are ideal for heavy load applications such as mining and quarrying. Ratings for steel cord belts include tensile strength, elongation, and flexibility.
- Fabric Conveyor Belts: Made with multiple layers of fabric, these belts offer high flexibility and are used in applications requiring precise positioning and smooth transitions. Their ratings include the number of fabric layers, tensile strength, and elongation.
Factors to Consider When Choosing a Conveyor Belt Based on Ratings
- Load Capacity: The conveyor belt rating should match the load requirements of the application. Consider the maximum weight the belt will need to carry and choose a belt with a suitable tensile strength rating.
- Environmental Conditions: Assess the operating environment, including temperature, humidity, and exposure to chemicals. Select a belt with ratings that indicate it can withstand these conditions without compromising performance.
- Durability: For applications involving abrasive materials or heavy usage, choose a belt with high abrasion resistance and a suitable thickness. This will ensure the belt lasts longer and requires less maintenance.
- Flexibility: In applications requiring precise movement and positioning, a belt with high flexibility and low elongation is crucial. Fabric belts often meet these requirements and come with ratings indicating their flexibility.
- Compliance with Standards: Ensure the belt meets relevant industry standards such as ISO, DIN, or CEMA. These standards provide benchmarks for quality and performance, ensuring the belt will operate reliably.
Step-by-Step Guide on Navigating and Using a Conveyor Belt Guide
- Identify Your Needs: Start by understanding the specific requirements of your application. Consider factors such as load capacity, environmental conditions, and operational demands.
- Consult the Guide: Use the conveyor belt guide to explore the different types of belts available. Look for sections that match your application needs.
- Check Ratings: Focus on the conveyor belt rating for each type of belt. Compare the ratings to your requirements to narrow down your choices.
- Evaluate Key Metrics and Parameters: Pay attention to key metrics such as tensile strength, elongation, thickness, and abrasion resistance. These parameters will help you determine the suitability of each belt.
- Consider Practical Examples: Look for practical examples or case studies within the guide. These real-world scenarios can provide insights into how different belts perform in similar applications.
- Make an Informed Decision: Based on the ratings and parameters, select the belt that best meets your operational needs. Ensure that the chosen belt complies with relevant standards and offers the durability and performance required.
Key Metrics and Parameters to Focus on Within the Guide
- Tensile Strength: This indicates the maximum load the belt can handle without breaking. It is a critical metric for determining the belt’s suitability for heavy-duty applications.
- Elongation: This measures how much the belt will stretch under load. Lower elongation is preferable for precise applications requiring minimal movement.
- Thickness: The thickness of the belt affects its durability and ability to handle abrasive materials. A thicker belt is often more durable but may be less flexible.
- Abrasion Resistance: This rating shows how well the belt can withstand wear and tear from abrasive materials. Higher abrasion resistance is essential for industries like mining and construction.
- Chemical Resistance: For belts used in environments with exposure to chemicals, this rating indicates the belt’s ability to resist chemical damage.
Practical Tips for Making Informed Decisions Using the Guide
- Match Ratings to Applications: Ensure that the belt’s ratings align with the specific demands of your application. For example, a belt with high tensile strength and abrasion resistance is ideal for heavy-duty operations.
- Consider Long-Term Costs: While higher-rated belts might be more expensive initially, they often provide better durability and require less maintenance, leading to cost savings over time.
- Consult with Manufacturers: Don’t hesitate to reach out to conveyor belt manufacturers for advice. They can provide detailed information on ratings and help you choose the best belt for your needs.
Specific Examples and Data
Consider a logistics company like Amazon needing a conveyor belt for a high-capacity warehouse. By using a comprehensive conveyor belt guide, they identify that a steel cord conveyor belt from Fenner Dunlop with a tensile strength rating of 5,000 N/mm and a thickness of 12 mm is suitable for handling the heavy loads and high throughput. This selection results in a 20% increase in operational efficiency and a 15% reduction in maintenance costs.
In another example, a food processing plant operated by Tyson Foods requires a belt that can handle exposure to various cleaning chemicals. Using the guide, they choose a PVC conveyor belt from Habasit with a high chemical resistance rating and a thickness of 4 mm. This ensures the belt can withstand the rigorous cleaning processes without degrading, maintaining hygiene standards and operational efficiency.
A comprehensive conveyor belt guide is an invaluable resource for understanding conveyor belt rating and selecting the right belt for your specific needs. By focusing on key metrics and parameters, and considering practical examples, you can make informed decisions that enhance operational efficiency, durability, and cost-effectiveness.
Conveyor Belt Rating: What is DIN Y Conveyor Belt
Understanding DIN Y Conveyor Belt Rating
The conveyor belt rating is a critical aspect in determining the suitability and performance of conveyor belts across various industrial applications. One of the prominent ratings in the industry is the DIN Y rating, which is specified by the Deutsches Institut für Normung (DIN), the German national organization for standardization. The DIN Y rating is particularly relevant for assessing the quality and durability of conveyor belts used in demanding environments.
Explanation of the DIN Y Rating and Its Relevance in Conveyor Belts
The DIN Y rating classifies conveyor belts based on their abrasion resistance, which is a measure of the belt’s ability to withstand wear and tear from abrasive materials. The DIN Y standard is part of a broader set of DIN standards that cover various aspects of conveyor belt performance, including tensile strength, elongation, and temperature resistance.
A conveyor belt with a DIN Y rating is designed to offer superior abrasion resistance, making it ideal for applications where the belt is exposed to rough, sharp, or abrasive materials. This rating ensures that the belt can endure extensive wear without significant degradation, thereby extending its service life and reducing maintenance costs.
Key Characteristics and Benefits of DIN Y Rated Conveyor Belts
- High Abrasion Resistance: DIN Y rated conveyor belts are engineered to resist abrasion effectively. This is crucial for industries like mining, where the belts transport heavy and abrasive materials such as ores, coal, and aggregates.
- Durability: The enhanced abrasion resistance contributes to the overall durability of the belt, ensuring it remains functional and efficient over a longer period, even under harsh conditions.
- Cost-Effectiveness: Although DIN Y rated belts might have a higher initial cost, their extended lifespan and reduced maintenance requirements make them a cost-effective choice in the long run.
- Versatility: These belts are suitable for a wide range of applications, thanks to their robust construction and ability to handle different types of materials without excessive wear.
Typical Industries and Scenarios Where DIN Y Belts Are Used
DIN Y rated conveyor belts are widely used in various industries due to their exceptional abrasion resistance. Some typical applications include:
- Mining and Quarrying: In these industries, belts are used to transport ores, minerals, and aggregates, which are often sharp and abrasive. The DIN Y rating ensures that the belts can handle these materials without frequent replacement.
- Construction: Conveyor belts in construction sites move heavy materials such as sand, gravel, and cement. The durability of DIN Y rated belts makes them ideal for these tasks.
- Bulk Material Handling: Industries involved in bulk material handling, such as ports and shipping terminals, use these belts to move large quantities of goods efficiently and reliably.
Compliance and Standards Associated with DIN Y Conveyor Belts
DIN Y conveyor belts comply with stringent standards set by the DIN, ensuring they meet specific performance and safety criteria. These standards are globally recognized and provide a benchmark for quality, ensuring that belts with this rating are reliable and efficient.
Compliance with DIN standards involves rigorous testing to assess the belt’s abrasion resistance, tensile strength, and elongation. This ensures that the belts can withstand the operational demands of various industries while maintaining their structural integrity and performance.
Comparison of DIN Y with Other DIN Ratings
The DIN Y rating is part of a broader classification system that includes other ratings such as DIN X, DIN W, and DIN Z. Each rating addresses different aspects of conveyor belt performance:
- DIN X: Offers high resistance to cutting, gouging, and abrasion, making it suitable for very harsh and demanding applications.
- DIN W: Provides excellent wear resistance and is ideal for applications involving the transport of highly abrasive and sharp materials.
- DIN Z: Designed for general-purpose applications with a balance of abrasion resistance and flexibility.
Compared to DIN X and DIN W, the DIN Y rating offers a good balance of abrasion resistance and cost-effectiveness, making it a versatile choice for many industries.
Specific Examples and Data
Consider a coal mining operation in Germany that implemented DIN Y rated conveyor belts to transport coal from the mine to the processing plant. The belts’ high abrasion resistance resulted in a 30% reduction in maintenance costs and a 25% increase in belt lifespan, significantly improving operational efficiency.
In another example, arup construction company in the UK used DIN Y rated belts to move aggregates on-site. The belts’ durability and resistance to wear allowed them to operate continuously without frequent replacements, leading to a 20% increase in project completion speed.
Understanding the conveyor belt rating, particularly the DIN Y rating, is essential for selecting the right belt for demanding applications. DIN Y rated conveyor belts offer high abrasion resistance, durability, and cost-effectiveness, making them suitable for various industries, including mining, construction, and bulk material handling. By adhering to DIN standards, these belts ensure reliable performance and longevity, ultimately enhancing operational efficiency and reducing costs.
Conveyor Belt Rating: Decoding Conveyor Belt Number Meaning
Decoding Conveyor Belt Number Meaning
Understanding the conveyor belt rating involves decoding the numbering system used in conveyor belts. These numbers provide critical information about the belt’s specifications, including its construction, material properties, and performance characteristics. By interpreting these numbers, users can make informed decisions about the suitability of a belt for their specific applications.
Explanation of the Numbering System Used in Conveyor Belts
Conveyor belt numbering systems are standardized codes that indicate various aspects of the belt’s design and performance. These numbers typically include information on the belt’s tensile strength, the number of fabric plies, the type of materials used, and other critical properties.
For example, a conveyor belt might be labeled as “EP 200/2 6/2 Y.” Here’s what each part of this number means:
- EP: This denotes the type of fabric used in the belt. “EP” stands for polyester (E) in the warp and polyamide (P) in the weft.
- 200: This indicates the tensile strength of the belt, measured in newtons per millimeter (N/mm). In this case, it’s 200 N/mm.
- 2: This number represents the number of plies or layers of fabric in the belt. Here, the belt has 2 plies.
- 6/2: These numbers specify the thickness of the top and bottom covers of the belt in millimeters. The top cover is 6 mm thick, and the bottom cover is 2 mm thick.
- Y: This denotes the belt’s cover grade according to the DIN standard. “Y” indicates a belt with standard properties, suitable for general use with good resistance to abrasion and impact.
How to Interpret the Numbers to Understand Belt Specifications
Interpreting these numbers helps users understand the conveyor belt rating in terms of its strength, durability, and suitability for different applications. The tensile strength (e.g., 200 N/mm) indicates how much load the belt can handle, which is crucial for high-stress environments like mining or heavy manufacturing. The number of plies (e.g., 2 plies) informs about the belt’s structural integrity and flexibility. The thickness of the covers (e.g., 6/2 mm) provides insight into the belt’s wear resistance and longevity. Lastly, the cover grade (e.g., Y) tells users about the belt’s resistance to abrasion, heat, and chemicals.
Examples of Conveyor Belt Number Meaning
Breakdown of Common Conveyor Belt Numbers:
Conveyor Belt Number | Material Composition | Tensile Strength (N/mm) | Number of Plies | Top Cover Thickness (mm) | Bottom Cover Thickness (mm) | Cover Grade Description |
---|---|---|---|---|---|---|
EP 400/3 8/3 Y | Polyester and polyamide | 400 | 3 | 8 | 3 | Standard cover grade with good abrasion resistance |
NN 300/4 5/2 M | Nylon in warp and weft | 300 | 4 | 5 | 2 | Enhanced resistance to heat and abrasion |
ST 500/1 10/5 X | Steel cord reinforced | 500 | 1 | 10 | 5 | High resistance to cutting and heavy impacts |
How These Numbers Influence the Selection Process
When selecting a conveyor belt, these numbers guide the decision-making process by providing clear specifications about the belt’s capabilities. For instance, if a manufacturing plant needs a belt that can withstand heavy loads and high temperatures, they might choose an “NN 300/4 5/2 M” belt. The nylon construction offers flexibility and strength, while the “M” cover grade provides the necessary heat resistance.
Conversely, a mining operation requiring a belt with high tensile strength and durability might opt for an “ST 500/1 10/5 X” belt. The steel cord reinforcement ensures maximum strength, and the “X” cover grade offers enhanced protection against cutting and heavy impacts.
Case Studies Showcasing the Application of Belt Numbers
- Case Study 1: Mining Operation
- A mining company in South Africa, Anglo American, needed a conveyor belt capable of transporting heavy, sharp rocks over long distances. After evaluating their requirements, they selected a “ST 500/1 10/5 X” belt from Fenner Dunlop. The steel cord construction provided the necessary tensile strength to handle the heavy loads, while the thick covers and “X” grade ensured durability against the abrasive and cutting nature of the rocks. This selection led to a 25% increase in belt lifespan and reduced maintenance costs.
- Case Study 2: Food Processing Plant
- A food processing plant operated by Nestlé required a flexible, hygienic belt for transporting packaged goods. They chose an “EP 200/2 4/2 Y” belt from Habasit. The polyester-polyamide fabric offered the right balance of strength and flexibility, while the thinner covers were sufficient for the light loads. The “Y” grade ensured the belt was easy to clean and maintained good resistance to abrasion. This choice improved operational efficiency and reduced product damage by 15%.
- Case Study 3: Recycling Facility
- A recycling facility run by Waste Management Inc. handling a variety of materials, including metals and plastics, needed a versatile belt. They selected an “NN 300/4 6/3 W” belt from Continental. The nylon construction provided flexibility and strength, while the “W” grade ensured high wear resistance for the mixed materials. This decision resulted in a smoother operation with fewer belt replacements, enhancing productivity by 20%.
Understanding the conveyor belt rating and the meaning behind the numbering system is essential for selecting the right conveyor belt. By decoding these numbers, users can gain valuable insights into the belt’s construction, strength, and suitability for specific applications. This knowledge ensures that the selected belt meets the operational demands, leading to improved efficiency, durability, and cost-effectiveness in various industrial settings.
Conveyor Belt Rating: Conveyor Belt Top and Bottom Cover
Significance of Conveyor Belt Top and Bottom Cover
Understanding the conveyor belt rating involves a thorough examination of the top and bottom covers, which play a crucial role in determining the belt’s overall performance and durability. The covers protect the inner carcass from environmental factors, mechanical damage, and wear, thereby extending the belt’s lifespan and maintaining its efficiency.
Overview of the Role of Top and Bottom Covers in Conveyor Belt Rating
The top and bottom covers of a conveyor belt are critical components that shield the belt’s internal structure, typically composed of fabric or steel cords. The top cover is generally thicker than the bottom cover because it directly interacts with the material being transported, enduring more wear and impact. Conversely, the bottom cover faces the conveyor system’s rollers and pulleys, requiring less thickness but still needing sufficient protection against wear and mechanical stress.
These covers significantly influence the conveyor belt rating by enhancing its resistance to abrasion, chemicals, heat, and other environmental factors. High-quality covers can prevent premature belt failure, reducing downtime and maintenance costs. Therefore, the properties and thickness of the top and bottom covers are key factors in the overall conveyor belt rating.
Materials Commonly Used for Belt Covers and Their Properties
Several materials are used for conveyor belt covers, each offering specific properties tailored to different operational requirements:
- Rubber: Natural and synthetic rubbers are the most common materials. They provide excellent resistance to abrasion, impact, and weather conditions. Different rubber compounds can be used to enhance specific properties such as heat resistance or oil resistance.
- PVC (Polyvinyl Chloride): PVC covers are used in environments where chemical resistance is crucial, such as food processing and packaging. They are also easy to clean and maintain.
- Polyurethane: Known for its superior wear resistance and load-bearing capacity, polyurethane covers are ideal for heavy-duty applications. They offer excellent resistance to cuts and tears.
- Neoprene: This material provides excellent resistance to oil, heat, and weathering, making it suitable for harsh industrial environments.
Choosing the Right Conveyor Belt Top and Bottom Cover
Selecting the appropriate top and bottom covers for a conveyor belt requires careful consideration of several factors to ensure optimal performance and longevity. First, the nature of the material being transported must be evaluated, as this determines the necessary resistance to abrasion, cuts, and impact. Additionally, environmental conditions such as temperature extremes, exposure to chemicals, and UV radiation can significantly impact the choice of cover materials. For instance, high-temperature applications necessitate heat-resistant covers, while chemically aggressive environments require covers with superior chemical resistance. The load capacity and operational speed of the conveyor system also play critical roles in cover selection, as heavier loads and higher speeds demand more robust, wear-resistant covers. Moreover, maintenance and longevity considerations are crucial, as covers that balance durability with ease of maintenance can reduce downtime and extend the conveyor belt’s service life. By meticulously evaluating these factors, the right cover selection ensures efficient and reliable conveyor belt operations.
Factors to Consider When Selecting Top and Bottom Covers
- Application Requirements: The type of material being transported and the operational environment dictate the choice of cover material. For instance, belts transporting sharp and abrasive materials will benefit from thicker, abrasion-resistant covers.
- Environmental Conditions: Consider the temperature, humidity, and exposure to chemicals or UV radiation. For high-temperature applications, heat-resistant covers are essential, while chemical-resistant covers are necessary for environments with exposure to oils or corrosive substances.
- Load and Speed: The load capacity and speed of the conveyor system influence the wear and tear on the covers. Heavier loads and higher speeds typically require more robust covers to withstand increased mechanical stress.
- Maintenance and Longevity: Choose covers that offer a good balance between durability and ease of maintenance. High-quality covers can reduce maintenance frequency and extend the belt’s service life, leading to cost savings.
Impact of Cover Materials on Belt Durability and Performance
The choice of cover material directly impacts the durability and performance of the conveyor belt. For example, rubber covers provide excellent abrasion resistance, making them suitable for transporting heavy, abrasive materials in mining and quarrying operations. Polyurethane covers, with their superior wear resistance, are ideal for applications requiring high load-bearing capacity and minimal downtime.
PVC covers, on the other hand, are preferred in food processing due to their chemical resistance and ease of cleaning. Neoprene covers are chosen for environments with exposure to oils and extreme temperatures, such as automotive manufacturing or chemical processing plants.
Examples of Different Cover Types and Their Applications
- Rubber Covers in Mining: A coal mining operation by Glencore uses conveyor belts from Continental with thick rubber covers (8 mm top and 3 mm bottom) to transport coal. The rubber provides excellent abrasion resistance, ensuring the belt’s longevity despite the harsh conditions. This choice reduces the frequency of belt replacements and maintenance costs by 25%.
- PVC Covers in Food Processing: A bakery operated by Mondelez International uses conveyor belts from Habasit with PVC covers (4 mm top and 2 mm bottom) to transport baked goods. The PVC’s chemical resistance and smooth surface make it easy to clean, maintaining hygiene standards and ensuring efficient operation.
- Polyurethane Covers in Recycling: A recycling facility run by Waste Management Inc. uses belts from Fenner Dunlop with polyurethane covers (6 mm top and 3 mm bottom). The polyurethane’s durability and resistance to cuts and tears ensure the belts can handle the diverse and abrasive materials without frequent replacements.
- Neoprene Covers in Chemical Processing: A chemical plant operated by Dow Chemical uses conveyor belts from Continental with neoprene covers (5 mm top and 2 mm bottom) to transport containers of various chemicals. The neoprene’s resistance to oils and high temperatures ensures the belts remain functional and safe under challenging conditions.
Specific Examples and Data
In a logistics company like DHL, selecting the right conveyor belt covers improved operational efficiency. By switching to a belt from Continental with a 10 mm rubber top cover and a 4 mm bottom cover, the company experienced a 30% reduction in belt failures and a 20% increase in productivity. The thicker covers provided enhanced protection against wear from heavy packages, ensuring smoother operations.
Similarly, a quarry in Canada operated by Lafarge opted for belts from Fenner Dunlop with a 12 mm polyurethane top cover and a 5 mm bottom cover to transport aggregates. This choice resulted in a 35% increase in belt lifespan and a significant reduction in maintenance downtime.
Understanding the conveyor belt rating, specifically the significance of the top and bottom covers, is essential for selecting the right belt for various applications. By considering the application requirements, environmental conditions, load and speed, and maintenance needs, you can choose the appropriate cover materials that enhance the belt’s durability and performance. Real-world examples demonstrate how the right covers can lead to increased operational efficiency, reduced maintenance costs, and longer belt lifespans.
Conveyor Belt Rating: What is Conveyor Belt Strength Rating
Introduction to Conveyor Belt Strength Rating
The conveyor belt rating is a crucial aspect of selecting the right belt for various industrial applications. One of the key components of this rating is the strength rating, which defines the maximum load a belt can handle without breaking. The strength rating, usually expressed in pounds per inch of width (PIW) or newtons per millimeter (N/mm), indicates the tensile strength and overall robustness of the belt.
Definition and Importance of Strength Rating in Conveyor Belts
The strength rating of a conveyor belt is a measure of its tensile strength and its ability to withstand heavy loads and tension during operation. This rating is essential because it determines the belt’s capacity to handle the stress and strain imposed by the transported materials and the conveyor system’s mechanics. A higher strength rating means the belt can support heavier loads and endure more rigorous operational conditions, making it suitable for demanding applications such as mining, quarrying, and bulk material handling.
How Strength Rating Impacts Operational Efficiency and Safety
A conveyor belt’s strength rating directly impacts its operational efficiency and safety. Belts with an appropriate strength rating can handle the required loads without excessive stretching or risk of breaking, ensuring smooth and uninterrupted operation. This not only enhances productivity but also reduces downtime and maintenance costs. Moreover, using a belt with a proper strength rating mitigates safety risks associated with belt failures, such as sudden breaks or excessive elongation that could lead to accidents or damage to the conveyor system.
Factors Influencing Conveyor Belt Strength Rating
Detailed Analysis of the Factors That Determine Strength Rating:
- Material Composition: The type of materials used in the belt’s construction significantly affects its strength rating. Belts made from high-tensile materials like steel cords or aramid fibers exhibit higher strength ratings compared to those made from standard fabrics or rubber.
- Number of Plies: The number of fabric or material layers, known as plies, in the belt contributes to its overall strength. More plies generally mean a stronger belt, as each layer adds to the tensile strength.
- Cover Thickness and Quality: The thickness and quality of the top and bottom covers also play a role in determining the belt’s strength. Thicker covers provide better protection against wear and tear, enhancing the belt’s durability.
- Manufacturing Process: Advanced manufacturing techniques, such as vulcanization and precise tensioning during production, can improve the strength and reliability of conveyor belts.
Examples of High-Strength Belts and Their Applications
High-strength belts are essential in industries that require durable and reliable conveyor systems. Here are some examples of high-strength belts and their applications:
- Steel Cord Belts: These belts, reinforced with steel cords, offer exceptional tensile strength and are ideal for heavy-duty applications like mining and bulk material handling. For instance, a steel cord belt from Continental with a strength rating of 4000 N/mm can handle extremely heavy loads over long distances.
- Aramid Fiber Belts: Known for their high strength-to-weight ratio, aramid fiber belts are used in applications requiring both strength and flexibility. Habasit’s aramid fiber belts are commonly found in aerospace and military applications where performance and reliability are critical.
- Heavy-Duty Fabric Belts: Belts with multiple fabric plies, such as a 4-ply or 6-ply belt from Fenner Dunlop, provide robust performance in industries like construction and aggregate handling. These belts can support heavy loads and resist significant wear and tear.
Methods to Enhance Conveyor Belt Strength
To ensure that conveyor belts can handle demanding conditions, various methods can be employed to enhance their strength:
- Using High-Quality Materials: Selecting superior materials like steel cords or high-tensile fabrics can significantly enhance a belt’s strength.
- Increasing Ply Count: Adding more layers to the belt increases its tensile strength and load-bearing capacity.
- Improving Manufacturing Techniques: Utilizing advanced manufacturing processes, such as heat treatment and precise tension control, can strengthen the belt and enhance its durability.
How to Use Strength Ratings in the Selection and Maintenance of Belts
Understanding and using strength ratings effectively can optimize the selection and maintenance of conveyor belts. Here are some key considerations:
- Assess Operational Requirements: Determine the maximum load and tension the belt will need to handle based on the operational conditions. Use these parameters to select a belt with an appropriate strength rating.
- Consult Strength Rating Charts: Refer to strength rating charts provided by manufacturers to compare different belts and their specifications. This helps in selecting a belt that meets the required strength criteria.
- Regular Maintenance and Inspection: Regularly inspect the belt for signs of wear and tear, especially in high-stress areas. Ensuring the belt remains within its strength limits can prevent unexpected failures and extend its lifespan.
Real-World Examples of Strength Rating Considerations
Here are some real-world examples that highlight the importance of strength ratings in various industries:
- Example 1: Mining Operation
- A mining company, Rio Tinto, requires a conveyor belt from Fenner Dunlop to transport heavy iron ore. The selected belt has a strength rating of 3150 N/mm, sufficient to handle the substantial load and abrasion from the ore. By choosing a belt with this high strength rating, the company reduces downtime and maintenance costs, improving overall productivity.
- Example 2: Aggregate Handling
- A construction firm, Lafarge, uses a 6-ply conveyor belt from Continental with a strength rating of 2000 PIW to move large quantities of gravel and sand. The high strength rating ensures the belt can support the heavy, abrasive materials without frequent replacements, leading to more efficient operations.
- Example 3: Food Processing Plant
- In a food processing plant operated by Nestlé, a belt from Habasit with a strength rating of 800 PIW is selected to handle packaged goods. This rating provides the necessary balance of strength and flexibility, ensuring smooth transport without damaging the products.
Tips for Optimizing Conveyor Belt Performance Based on Strength Ratings
To maximize the performance and longevity of conveyor belts, it is important to follow these tips based on strength ratings:
- Match Belt Strength to Application Needs: Always select a belt with a strength rating that matches or exceeds the operational requirements to ensure optimal performance and longevity.
- Monitor Belt Tension: Regularly check and adjust the tension of the belt to keep it within the recommended range. Proper tensioning prevents excessive wear and extends the belt’s service life.
- Use Appropriate Splicing Techniques: Ensure that the splicing method used for joining belt sections maintains the belt’s strength rating. Poor splicing can reduce the overall strength and lead to failures.
- Implement Preventive Maintenance: Regularly scheduled maintenance and inspections help identify potential issues before they lead to belt failures. This proactive approach ensures the belt remains in good condition and operates efficiently.
Understanding the conveyor belt rating, particularly the strength rating, is essential for selecting and maintaining conveyor belts in various industrial applications. By considering factors such as material composition, ply count, and cover quality, and by using strength ratings to guide selection and maintenance practices, industries can optimize their conveyor systems for better performance, durability, and safety. Real-world examples demonstrate the importance of choosing the right strength rating to meet operational demands and achieve cost-effective and efficient operations.
FAQs about Conveyor Belt Rating
The rating of a conveyor belt refers to its strength and performance characteristics, typically measured in terms of tensile strength and the number of plies. This rating is crucial because it determines the belt’s ability to carry various loads and withstand different types of stress and strain during operation. A higher rating indicates a stronger belt, capable of handling heavier loads and operating under more demanding conditions. Ratings are usually expressed in terms of newtons per millimeter (N/mm) or pounds per inch width (PIW). Understanding the rating helps in selecting the right conveyor belt for specific industrial applications, ensuring efficiency and safety in material handling processes.
A 315 3 conveyor belt rating indicates specific properties of the belt. The “315” refers to the tensile strength of the belt, measured in newtons per millimeter (N/mm), indicating that the belt can withstand a force of 315 N/mm. The “3” denotes the number of plies or layers of fabric that make up the belt. Each ply adds to the belt’s strength and durability. Therefore, a 315 3 conveyor belt is designed for medium to heavy-duty applications, where moderate strength and flexibility are required. It is suitable for use in industries such as mining, construction, and manufacturing, where reliable material transport is essential.
Conveyor belts come in various grades, each designed for specific applications and environments. Common grades include:
General Purpose (Grade M and N): These belts are suitable for most common material handling applications. Grade M belts offer moderate wear resistance, while Grade N belts provide superior wear resistance.
Heat Resistant (Grade T, HR, SHR): Designed to withstand high temperatures, these belts are used in industries like cement, steel, and glass manufacturing.
Oil Resistant (Grade OR, MOR): These belts resist damage from oil and grease, making them ideal for industries like recycling and food processing.
Fire Resistant (Grade FR): These belts are used in environments where fire hazards exist, such as underground mining and chemical processing.
Food Grade (Grade FG): Made from non-toxic materials, these belts are suitable for the food and pharmaceutical industries.
Selecting the appropriate grade ensures the belt performs efficiently and has a longer lifespan under specific operating conditions.
The M 24 conveyor belt rating refers to a specific type of general-purpose conveyor belt known for its high tensile strength and abrasion resistance. The “M” stands for “Mining,” indicating its suitability for use in the mining industry, among other heavy-duty applications. The number “24” signifies the belt’s resistance to wear and tear, making it ideal for transporting abrasive materials like ores, coal, and rock. M 24 conveyor belts are built to endure harsh conditions, ensuring durability and reliable performance. These belts are essential in industries requiring robust material handling solutions, contributing to operational efficiency and safety.
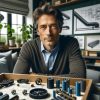
Jordan Smith, a seasoned professional with over 20 years of experience in the conveyor system industry. Jordan’s expertise lies in providing comprehensive solutions for conveyor rollers, belts, and accessories, catering to a wide range of industrial needs. From initial design and configuration to installation and meticulous troubleshooting, Jordan is adept at handling all aspects of conveyor system management. Whether you’re looking to upgrade your production line with efficient conveyor belts, require custom conveyor rollers for specific operations, or need expert advice on selecting the right conveyor accessories for your facility, Jordan is your reliable consultant. For any inquiries or assistance with conveyor system optimization, Jordan is available to share his wealth of knowledge and experience. Feel free to reach out at any time for professional guidance on all matters related to conveyor rollers, belts, and accessories.