Maintaining a Carrying Roller Conveyor Belt
Carrying roller conveyor belts play a pivotal role in numerous industrial sectors by facilitating the efficient transport of materials. These systems are integral to the smooth operation of facilities such as manufacturing plants, distribution centers, and packaging industries. A carrying roller conveyor belt consists primarily of a series of rollers mounted on a frame, which supports the belt as it moves items from one location to another. This setup not only enhances productivity but also minimizes labor costs and improves workplace safety. In this introduction, we’ll delve deeper into the mechanics of carrying roller conveyor belts and their essential components, highlighting their significance in modern industry.
What are Carrying Roller Conveyor Belts?
Carrying roller conveyor belts are critical components in automated systems across various industries, designed to transport materials efficiently from one point to another. These systems consist of a series of rollers that support and propel a conveyor belt loaded with materials.
Role of Carrying Idler Rollers
Carrying idler rollers are fundamental to the operation of carrying roller conveyor belts. Positioned along the conveyor path, these rollers support the belt and the material load, distributing the weight evenly and ensuring smooth movement. The rollers minimize friction and wear on the belt, thereby enhancing the system’s overall efficiency and longevity.
Impact Rollers
Impact rollers are specially designed to absorb the shock and stress of loading materials onto the conveyor belt. Located typically at the loading points, these rollers have a robust design with thicker, rubber-coated surfaces that cushion the belt against the force of falling materials. This protection is crucial for reducing wear and tear on the conveyor belt, extending its lifespan and maintaining the integrity of the belt’s surface.
Through understanding these components, one can appreciate how carrying roller conveyor belts operate within industrial settings, contributing to process optimization and increased productivity.
Types of Carrying Roller Conveyor Belts
Carrying roller conveyor belts are versatile components essential in various industrial settings, each type tailored to meet specific operational needs. This section explores the different types of carrying roller conveyor belts and their unique functions within production and handling environments.
Heavy Duty Conveyor Rollers
Heavy duty conveyor rollers are designed for environments where robustness and durability are paramount. These rollers are typically made from reinforced materials such as hardened steel or heavy-gauge metal to withstand high loads and abrasive conditions. Ideal for mining, quarrying, and other heavy industries, these carrying roller conveyor belts are built to ensure longevity and reliability under tough working conditions.
Guide Rollers
Guide rollers are critical in maintaining the alignment and tracking of a carrying roller conveyor belt. Positioned along the sides of the conveyor framework, these rollers help prevent the belt from slipping off its track, which is crucial for the smooth operation of the conveyor system. They are particularly useful in applications where the conveyor path involves curves or when the belt is subject to lateral forces.
Return Rollers
Return rollers play a vital role in the lifecycle of carrying roller conveyor belts. After the belt has transported materials to their destination, it must return to the start point to begin the process again. Return rollers support the underside of the belt on this journey back, reducing wear and tear and ensuring the belt travels smoothly without sagging or dragging. These rollers are simpler in design but are essential for the efficient functioning of the conveyor system.
By understanding the various types of carrying roller conveyor belts and their specific uses, industries can optimize their operations for better efficiency and reduced maintenance costs. Whether handling heavy loads, ensuring precise alignment, or facilitating smooth return paths, each type of roller plays a crucial role in the conveyor’s overall performance and longevity.
Key Components of Carrying Roller Conveyor Belts
Understanding the key components of carrying roller conveyor belts is essential for maximizing efficiency and extending the lifespan of the system. This section delves into the crucial elements that make up a robust carrying roller conveyor belt system, focusing on how these parts work together to facilitate smooth operation.
Conveyor Belt Drive Systems
The drive system is the heart of a carrying roller conveyor belt, responsible for the movement and control of the belt itself. Typically, the system includes a motor, gearbox, and drive pulley. The motor provides the necessary power, which is transferred through the gearbox to adjust the torque and speed. The drive pulley then transmits this power to the belt, propelling it forward. This setup is crucial in applications where precise speed control and torque are required for the efficient transport of goods.
Conveyor Drum Pulley
The conveyor drum pulley plays a pivotal role in the effective functioning of carrying roller conveyor belts. Located at the ends of the conveyor belt loop, drum pulleys support and drive the belt. These pulleys can be either drive pulleys, which power the belt, or idler pulleys, which simply guide and maintain tension in the belt. The correct sizing and selection of drum pulleys are vital to prevent slippage and increase the belt’s efficiency and durability.
Highlight on Non-Standard Components
In addition to standard components, certain applications may require non-standard features tailored to specific operational needs. For instance, heavy-duty rollers are used in environments that deal with extreme loads or abrasive materials. These rollers are often made from specialized materials such as hardened steel to resist wear and tear. Customized dimensions are also common in industries where the standard sizes do not fit the specific needs of the operation. These custom components are designed to fit unique conveyor layouts or to handle specialized materials.
By closely examining these key components, one can gain a deeper understanding of how each part contributes to the overall effectiveness of a carrying roller conveyor belt system. Whether it’s the power transmission capability of the drive system, the support provided by drum pulleys, or the specialized functions of non-standard components, each plays a critical role in the conveyor’s operation.
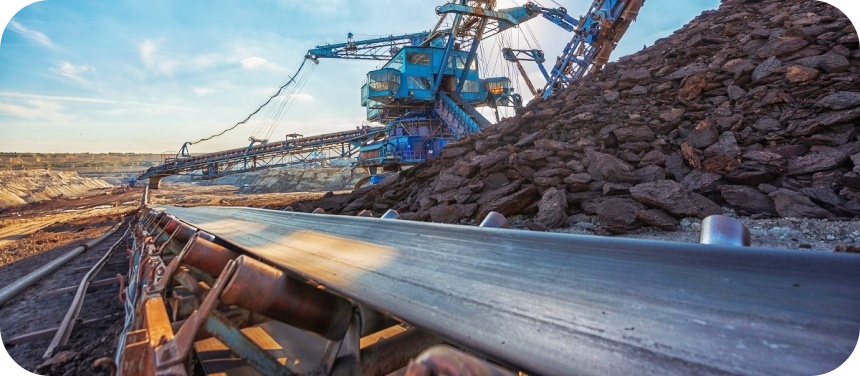
Dimensions and Specifications
In the context of industrial machinery, the dimensions of components are critical, particularly when selecting the right conveyor belt for specific operations. This section delves into the significance of these measurements and outlines the standard dimensions for carrying roller conveyor belts, demonstrating how they influence performance and are tailored to suit various industrial tasks.
Importance of Dimensions in Selecting the Right Conveyor Belt
- Load Capacity: Dimensions determine the load capacity of a conveyor belt. A belt that is too narrow or too short may not handle the required volume of material, leading to inefficiencies or potential damage to the belt.
- Speed of Operations: The width and length of a conveyor belt can affect the speed at which materials are transported. Properly sized belts optimize the flow and timing of operations.
- Compatibility with Machinery: Dimensions must be compatible with existing machinery. Incorrectly sized belts can cause operational disruptions and may not fit the machinery designed for specific tasks.
- Efficiency in Space Usage: In facilities where space is a premium, the dimensions of the conveyor belt must be maximized for efficiency while fitting within the physical constraints of the site.
- Cost-Effectiveness: Choosing the right dimensions can be more cost-effective. Oversized or undersized belts can lead to increased wear and tear, higher maintenance costs, and premature replacement.
- Safety: Proper dimensions reduce the risk of accidents and material spillage. A belt that is too wide or too long might lead to unsafe working conditions.
- Energy Consumption: The size of a conveyor belt impacts its energy consumption. Larger belts require more power to operate, which can increase operational costs.
- Material Handling Requirements: Different materials require different conveyor belt sizes. For instance, bulky materials might need wider belts for stable transport.
- Installation Requirements: Certain dimensions facilitate easier installation and maintenance. Choosing the right size can reduce downtime and labor costs associated with these activities.
- Adaptability and Flexibility: The right dimensions offer more flexibility in operations, allowing for adjustments in material volume and type without requiring complete system overhauls.
Standard Dimensions for Carrying Roller Conveyor Belts
The standard dimensions for carrying roller conveyor belts are crucial as they directly impact the belt’s performance and its suitability for various tasks. Typical dimensions include:
- Width: Standard widths range from 400 mm to 2200 mm. The width is selected based on the type and volume of material to be transported.
- Length: Conveyor lengths can vary significantly depending on the layout of the installation site and the distance materials need to be moved.
- Thickness: Belt thickness is typically between 10 mm and 30 mm, influenced by the material’s weight and the type of rollers used.
- Roller Diameter: The diameter of the rollers often ranges from 50 mm to 140 mm. Larger rollers are used for heavier loads and longer belts to reduce the belt’s operational stress.
These dimensions are not only a reflection of the carrying roller conveyor belt’s capability to handle different industrial tasks but also a determinant of its operational lifespan and reliability. By understanding and choosing the correct dimensions, businesses can ensure efficient and safe conveyor belt operations tailored to their specific needs.
Buying and Selling Carrying Roller Conveyor Belts
When it comes to purchasing or selling carrying roller conveyor belts, making informed decisions is crucial for ensuring long-term efficiency and cost-effectiveness. This section offers a comprehensive guide on what to consider when engaging in transactions involving carrying roller conveyor belts, as well as tips for maintaining them to maximize lifespan and performance.
Considerations for Buying Carrying Roller Conveyor Belts
New vs. Used Conveyor Belts
Choosing between new and used carrying roller conveyor belts involves weighing several factors:
- Pros of New Belts: Guaranteed performance, latest technology, warranty coverage, and no wear and tear.
- Cons of New Belts: Higher initial cost.
- Pros of Used Belts: Lower cost, suitable for low-budget or short-term applications.
- Cons of Used Belts: Potential hidden defects, limited lifespan, and generally no warranty.
Evaluating Prices
When evaluating carrying roller conveyor belt prices, consider the following:
- Quality and Material: Higher-quality materials like reinforced steel or specialized rubbers might cost more but offer better durability and efficiency.
- Custom Features: Custom dimensions or features such as integrated sensors for automation can increase the price.
- Supplier Reputation: Established suppliers might offer higher prices but provide better after-sales service and reliability.
Finding Carrying Roller Conveyor Belts for Sale
- Industry Suppliers: Regularly check with specialized industrial suppliers who can offer a range of options tailored to specific industry needs.
- Online Marketplaces: Platforms like Alibaba, IndiaMART, or eBay can provide a variety of options, from new to used belts.
- Trade Shows: Industry trade shows are excellent places to meet manufacturers and dealers, see products firsthand, and negotiate deals.
Tips for Maintaining Carrying Roller Conveyor Belts
- Regular Inspections: Schedule regular inspections to check for wear and tear, alignment issues, and other potential problems.
- Proper Cleaning: Keep the conveyor belt and rollers clean to prevent material buildup that can cause damage or inefficiency.
- Lubrication: Ensure that all moving parts, especially bearings and rollers, are properly lubricated according to manufacturer recommendations.
- Tension Adjustment: Incorrect belt tension can lead to premature wear and operational issues. Adjust tension regularly to maintain optimal performance.
- Replace Worn Parts: Replace rollers, bearings, and sections of the belt as needed to avoid larger system failures.
- Monitor Load Capacities: Do not exceed the recommended load capacity, as this can stress the belt and reduce its lifespan.
- Use Skirtboards: Implement skirtboards where necessary to keep materials on the conveyor and reduce spillage.
- Implement Preventative Maintenance Software: Use software to track maintenance schedules, predict failures, and automate maintenance tasks.
- Train Staff: Ensure that all operators are trained on the proper use and maintenance of the conveyor system.
- Check for Misalignment: Regularly check and correct any misalignment of the conveyor belt to prevent uneven wear.
- Monitor Environmental Conditions: Protect the conveyor system from environmental conditions like extreme temperatures and moisture that can degrade materials.
- Seek Professional Help: When in doubt, consult with a professional for maintenance and repair to ensure that the system is handled correctly.
By carefully considering these factors when buying and committing to regular maintenance, businesses can significantly enhance the longevity and efficiency of their carrying roller conveyor belts, thereby optimizing their operations and reducing overall costs.
Practical Applications of Carrying Roller Conveyor Belts
Carrying roller conveyor belts are indispensable in a wide range of industries, proving their versatility and efficiency. This section examines the practical applications of these systems in various sectors and highlights how businesses can benefit from optimized conveyor belt systems through real-world case studies.
Manufacturing
In the manufacturing sector, carrying roller conveyor belts are crucial for assembly lines where components must be moved swiftly and reliably between different stages of production. For instance, in the automotive industry, these conveyor belts transport parts across the assembly floor, allowing for the sequential assembly of vehicles. This not only speeds up production but also reduces labor costs and enhances safety by minimizing manual handling of heavy components.
Packaging
The packaging industry relies heavily on carrying roller conveyor belts to streamline the packaging process. These belts facilitate the movement of products through various stages, from filling and sealing to labeling and final packaging. A notable case study involves a food processing company that implemented an advanced conveyor system, resulting in a 50% increase in packaging efficiency. The system’s ability to handle different package sizes and weights with precision greatly reduced downtime and product damage.
Logistics and Warehousing
Logistics centers and warehouses benefit significantly from the use of carrying roller conveyor belts, which optimize the handling and sorting of goods. These belts enable the rapid movement of items from storage areas to loading docks, improving the speed and accuracy of order fulfillment. A case study from a large e-commerce warehouse illustrates how upgrading to a more sophisticated conveyor belt system led to a 30% improvement in order sorting and dispatch times, directly impacting customer satisfaction and operational scalability.
Case Studies
- Automotive Assembly Plant: A leading automotive manufacturer redesigned its assembly line to include heavy-duty carrying roller conveyor belts, which resulted in a 25% increase in production rates.
- Pharmaceutical Packaging Facility: By integrating sensor-driven guide rollers in their conveyor belts, a pharmaceutical company was able to reduce product misalignment issues, significantly decreasing waste and increasing throughput.
- E-commerce Fulfillment Center: An e-commerce giant implemented zoned carrying roller conveyor belts in its fulfillment centers. This allowed sections of the conveyor to operate independently, enhancing the system’s flexibility and reducing bottlenecks during peak demand periods.
These practical applications showcase the effectiveness of carrying roller conveyor belts in enhancing operational efficiency across diverse industries. By tailoring the conveyor system to the specific needs of the sector, businesses can achieve remarkable improvements in productivity, cost reduction, and overall efficiency.
Optimize your production with our expert conveyor belt solutions.
FAQs about Carrying Roller Conveyor Belt
A roller conveyor belt is a type of conveyor system that uses cylindrical rollers, either in gravity applications or powered, to move goods across a horizontal or slightly inclined path. Unlike traditional belt conveyors where a single continuous loop of material (the belt) is used to convey products, roller conveyors are composed of many rollers that are attached to the conveyor frame. This design allows for handling a wide variety of products differing in size, weight, and material, making them versatile for industries ranging from packaging and materials handling to manufacturing and distribution. Roller conveyors are highly efficient, reducing the effort and energy required to move products over long distances within facilities.
In a conveyor belt system, the rollers serve as the critical components that facilitate the movement of the conveyor belt and support the items being transported. These rollers are typically cylindrical and are made from materials such as metal (steel or aluminum), plastic, or a combination of both. The type of roller used can vary based on the conveyor’s application, load capacity, and environmental conditions. There are different types of rollers including drive rollers that propel the belt, idler rollers that rotate freely and help to shape and support the belt, and return rollers that help in recycling the belt back to the start after unloading the goods. Each type of roller is vital for the conveyor’s operation and efficiency.
Loading a conveyor belt properly is essential for the efficiency and longevity of the conveyance system. The process typically begins by ensuring that the conveyor is switched off before loading. Goods should be placed centrally on the conveyor belt to ensure balance and to prevent overloading one side, which could cause the belt to run off its track or wear unevenly. It’s important to distribute the weight evenly and ensure that items are stable and secure. To avoid damage or spills, items should be loaded gently onto the conveyor. Once loading is complete, the conveyor can then be turned on. It’s also crucial to regularly inspect and adjust the conveyor setup to handle different types of loads effectively.
Rollers on a conveyor are generally referred to based on their function within the system. The most common types include:
Drive Rollers: These are powered rollers that propel the conveyor belt forward. They are connected to motors and can control the speed and direction of the belt.
Idler Rollers: These rollers are not powered and are used primarily to support the belt and the materials it carries over the distance of the conveyor.
Return Rollers: Located on the underside of the conveyor, these rollers guide the belt as it loops back to the beginning after unloading.
Each type of roller plays a specific role in the function and effectiveness of a conveyor belt system, ensuring smooth operation and the transport of goods across various distances.
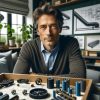
Jordan Smith, a seasoned professional with over 20 years of experience in the conveyor system industry. Jordan’s expertise lies in providing comprehensive solutions for conveyor rollers, belts, and accessories, catering to a wide range of industrial needs. From initial design and configuration to installation and meticulous troubleshooting, Jordan is adept at handling all aspects of conveyor system management. Whether you’re looking to upgrade your production line with efficient conveyor belts, require custom conveyor rollers for specific operations, or need expert advice on selecting the right conveyor accessories for your facility, Jordan is your reliable consultant. For any inquiries or assistance with conveyor system optimization, Jordan is available to share his wealth of knowledge and experience. Feel free to reach out at any time for professional guidance on all matters related to conveyor rollers, belts, and accessories.