Enhancing Efficiency with Gravity Shipping Rollers
Shipping rollers are essential components in the logistics and warehouse industries, designed to facilitate the smooth and efficient movement of goods. These rollers are part of conveyor systems, which consist of cylindrical tubes mounted on bearings and framed in supporting structures. Typically, shipping rollers are used to transport large volumes of items from one point to another within a facility, reducing the need for manual labor and increasing workplace safety. The simplicity of their design allows for easy integration into various conveyor systems, including gravity roller conveyors, motorized roller conveyors, and more. This introduction aims to explain the basic functionality and significance of shipping rollers in modern shipping and handling operations.
Types of Shipping Rollers
Shipping rollers are integral to the functionality of many industries, enabling the easy and efficient transfer of goods within various environments. These rollers come in several types, each designed to meet specific operational needs and environmental conditions. This section provides a detailed overview of three primary types of shipping rollers: gravity roller conveyors, roller conveyor tables, and heavy-duty conveyor rollers.
Gravity Roller Conveyor
Gravity roller conveyors are one of the simplest and most cost-effective types of shipping rollers available. They operate without the need for motor power, using the natural force of gravity to move products along the conveyor line. This makes them ideal for situations where minimal product elevation change occurs, ensuring a smooth flow of items.
Benefits:
- Cost efficiency due to the lack of electrical components.
- Low maintenance needs.
- Easy to install and reconfigure as needed.
- Quiet operation compared to motor-driven conveyors.
- Suitable for a variety of product weights and sizes.
Applications:
- Warehousing and distribution centers.
- Manufacturing assembly lines.
- Packaging industries.
- Loading docks.
- Retail backroom spaces.
Roller Conveyor Tables
Roller conveyor tables are versatile shipping rollers that support the efficient handling and sorting of goods. They are especially useful in packaging and assembly lines where manual intervention is required.
Description and Uses:
- Facilitate manual sorting and assembly operations.
- Support intricate product routing and handling.
- Ideal for stations where products need to be accessed from different angles.
- Useful in linking different stages of a production or packaging line.
- Can be customized with various widths and roller sizes to accommodate specific products.
Comparison:
Roller conveyor tables often feature adjustments for height and angle, unlike standard gravity conveyors, which are more fixed in design. The flexibility of roller tables allows for a more dynamic setup, accommodating a wider range of activities and product types compared to traditional shipping rollers.
Heavy Duty Conveyor Rollers
Heavy-duty conveyor rollers are designed to handle high-capacity loads and endure harsh operational conditions. These shipping rollers are built with robust materials to ensure durability and sustained performance.
What Makes Them Heavy Duty:
- Thick steel tubing for the rollers.
- Reinforced bearings and mounting brackets.
- Higher load-bearing capacity.
- Resistance to wear and tear in extreme industrial environments.
Benefits and Applications:
- Ideal for moving heavy or bulky materials.
- Common in mining and construction material industries.
- Used in heavy manufacturing sectors like automotive and aerospace.
- Essential in shipping hubs and freight terminals.
- Crucial for heavy pallet and container handling.
Each type of shipping roller plays a vital role in modern industrial operations, tailored to specific tasks and environments. Whether for light-duty packaging or heavy-duty construction, shipping rollers ensure the efficient, safe, and continuous movement of goods across numerous sectors.
Popular Brands and Products of Shipping Rollers
In the market for shipping rollers, certain brands stand out for their quality, reliability, and innovation. Among these, Uline and Ultimation Inc are prominent providers, each offering unique solutions tailored to different industrial needs. This section explores these brands and their specific products, showcasing why they are preferred choices in the realm of shipping rollers.
Uline Roller Conveyor
Uline is a well-known name in the packaging and shipping industry, renowned for its wide range of products that cater to organizational and shipping needs. Among their extensive catalog, the Uline roller conveyors are particularly notable for their durability and efficiency in handling materials.
Product Features:
- The Uline roller conveyors are available in various sizes and load capacities, making them suitable for a broad range of applications.
- They feature adjustable conveyor legs and sections that can be connected for extended lengths, providing great flexibility in setup.
- Manufactured with galvanized steel, these conveyors resist corrosion and ensure longevity even under rigorous use.
Specific Products:
- Heavy-Duty Gravity Roller Conveyor – Designed for handling heavy loads such as pallets and large containers, this model is robust and built to last.
- Expandable Roller Conveyor – Perfect for temporary or dynamic setup needs, it expands and contracts and is easy to store when not in use.
Ultimation Inc’s Conveyors
Ultimation Inc specializes in conveyor technology and offers a wide range of shipping rollers designed to meet various industrial requirements. Known for their innovative approach and custom solutions, Ultimation Inc’s products are crafted to enhance operational efficiency and adaptability.
Product Features:
- Ultimation Inc’s shipping rollers are characterized by their robust construction and versatility in applications ranging from automotive assembly lines to small-scale workshops.
- They offer both powered and non-powered versions, catering to different environmental needs and energy efficiency goals.
- Their conveyors often come with options for customization, including roller material, size, and motor type, allowing for a tailored conveyor solution.
Specific Products:
- Motorized Roller Conveyor – Ideal for environments where precise control of the movement and speed of goods is necessary.
- Gravity Conveyor with Steel Rollers – This cost-effective solution is perfect for areas where electrical power is limited or non-preferential.
Both Uline and Ultimation Inc provide top-tier shipping rollers that are essential in modern shipping and manufacturing processes. Their products demonstrate a commitment to quality and efficiency, making them leaders in the shipping rollers market. Whether for heavy-duty applications or more refined, controlled movements, these brands offer solutions that can dramatically improve logistical operations.
Buying Guide for Shipping Rollers
When it comes to enhancing operational efficiency in logistics and warehousing, selecting the right shipping rollers is crucial. This buying guide aims to equip you with essential information on the advantages and considerations involved in choosing between new and used shipping rollers, understanding price factors, and deciding on specialized equipment like expandable roller conveyors.
New vs. Used Shipping Rollers
New Shipping Rollers:
Buying new shipping rollers comes with several benefits and drawbacks that are important to consider:
Pros:
- Reliability and Warranty: New shipping rollers come with manufacturer warranties and less risk of breakdown.
- Latest Technology: They often incorporate the latest advancements in materials and engineering for better efficiency.
- Customization: New rollers can be customized to specific requirements of size, material, and load capacity.
- Longer Lifespan: With no prior wear and tear, new rollers typically offer a longer service life.
- Energy Efficiency: Newer models may be more energy-efficient, which can reduce operational costs over time.
Cons:
- Higher Initial Cost: The upfront investment is significantly higher than used options.
- Depreciation: Like most new equipment, shipping rollers depreciate quickly in the initial years.
- Longer Lead Times: Custom orders and newer models might have longer delivery times.
- Potential Over-specification: There’s a risk of over-specifying features that aren’t necessary for the task.
Used Shipping Rollers:
Opting for used shipping rollers can be a cost-effective alternative with its own set of benefits and potential pitfalls:
Benefits:
- Lower Cost: Used rollers are considerably cheaper, offering significant upfront savings.
- Immediate Availability: They are often available immediately, without the wait times associated with new orders.
- Proven Functionality: Used equipment has been tested in real-world conditions, potentially highlighting any operational issues.
- Depreciation: Less depreciation cost as the initial reduction in value has already occurred.
- Eco-Friendly: Purchasing used equipment is a form of recycling, reducing environmental impact.
Risks:
- Wear and Tear: Existing wear might reduce the lifespan and efficiency of the rollers.
- No Warranty: Most used shipping rollers come without a warranty, increasing risk.
- Maintenance Costs: Potential higher maintenance and repair costs.
- Outdated Technology: Older models may not have the latest features or efficiencies.
- Hidden Defects: There may be undetected issues that can affect performance.
Factors Affecting Shipping Rollers Price
Several factors can influence the price of shipping rollers:
- Material Quality: High-quality materials like reinforced steel cost more but offer greater durability.
- Size and Load Capacity: Larger rollers and those capable of handling heavier loads are priced higher.
- Custom Features: Custom modifications for specific operational requirements can increase costs.
- Brand Reputation: Well-known brands might charge a premium for their proven track records.
- Supply Chain Factors: Fluctuations in material costs or logistical challenges can impact pricing.
Expandable Roller Conveyor
Expandable roller conveyors are flexible solutions that can be extended, curved, and contracted to fit various spaces and needs.
Benefits:
- Flexibility to adjust to different lengths and layouts.
- Easy to store and move, ideal for temporary or dynamic setups.
- Scalable for varying operational demands.
Considerations for Purchasing:
- Maximum Load Capacity: Ensure the conveyor can handle the weight and size of your goods.
- Adjustability Features: Look for easy adjustability in length and height.
- Build Quality: Opt for robust construction to withstand frequent changes and movements.
- Ease of Movement: Consider models with high-quality casters or wheels for mobility.
- Cost: Balance the initial investment against the expected utility and efficiency gains.
This guide aims to assist you in making informed decisions when investing in shipping rollers, ensuring that you select equipment that aligns with your operational needs and budget constraints.
Guide to Shipping Rollers Parts and Accessories
Proper maintenance and timely replacement of parts and accessories are crucial to ensuring the optimal performance and longevity of shipping rollers. This guide provides a comprehensive overview of the essential components of shipping rollers and offers practical advice on how to maintain and replace them effectively.
Common Parts and Accessories for Shipping Rollers
Shipping rollers comprise several key components that work together to ensure smooth operation. These include:
- Roller Tubes: The cylindrical parts that directly contact and move the materials. They can be made from various materials such as steel, aluminum, or plastic, depending on the application.
- Bearings: These help the rollers move smoothly and are critical for reducing friction and wear.
- Axles: Connect the rollers to the conveyor frame and are crucial for the structural integrity of the system.
- Frame: Supports the rollers and can be constructed from materials like steel or aluminum to provide stability.
- Motor Drives (for powered conveyors): These are used to power the rollers and can vary in type from electric motors to pneumatic systems.
Tips for Maintaining and Replacing Roller Conveyor Parts
Regular maintenance and timely replacement of parts are essential to prevent downtime and extend the life of shipping rollers.
- Regular Inspection: Conduct regular inspections to check for wear and tear, especially on roller tubes and bearings. Look for signs of damage or deformation that could impair functionality.
- Lubrication: Bearings should be lubricated regularly to ensure smooth operation and to prevent overheating and wear. Use the correct type of lubricant as recommended by the manufacturer.
- Cleaning: Keep the rollers and conveyor frame clean from debris and dust that can accumulate and cause damage or inefficiency. This is especially important in environments with high levels of particulates.
- Replacement of Worn Parts: Replace parts such as bearings and roller tubes when they show signs of significant wear or damage. Waiting too long can lead to failures that might cause extensive damage to other components.
- Alignment Checks: Ensure that the rollers are properly aligned and the conveyor is level. Misalignment can lead to uneven wear and tear and reduce the efficiency of the conveyor system.
By adhering to these maintenance tips, you can significantly enhance the performance and lifespan of your shipping rollers, ensuring that they continue to function effectively and efficiently. Proper care and attention to the parts and accessories of your shipping rollers not only save costs in the long run but also improve the safety and productivity of your operations.
FAQs About Shipping Rollers
The rollers on a conveyor are cylindrical components that facilitate the movement of materials along the conveyor system. These rollers are mounted on bearings and rotate around a fixed axis, helping to transport goods smoothly across the surface of the conveyor. They can be made from various materials such as metal, plastic, or rubber, depending on the specific needs of the application. The choice of material affects the durability, traction, and noise level of the conveyor. Rollers are crucial in minimizing the friction and resistance involved when moving objects, making them essential for efficient conveyor operations in industries like manufacturing, packaging, and distribution.
A roller conveyor is a type of conveyor system that uses a series of rollers mounted within a frame to transport materials across a designated space. Roller conveyors are versatile and can be powered by motors or gravity, depending on their design and the requirements of the operation. Motorized roller conveyors are driven by belts or chains, whereas gravity roller conveyors use a slight decline in elevation to move items from one point to another, relying on gravity to provide the momentum. This type of conveyor is particularly useful for handling items with a flat bottom like boxes, pallets, or trays. Roller conveyors are popular in material handling and packaging facilities due to their efficiency and the ease with which they can be integrated into complex logistical workflows.
Conveyor rollers come in a wide range of sizes tailored to various industrial needs. The diameter of conveyor rollers can vary significantly, typically ranging from as small as 0.75 inches to over 8 inches. The width of the rollers also varies, designed to accommodate the breadth of the materials being transported. The size of the roller required depends on several factors including the load capacity, the type of materials being moved, the speed of the conveyor, and environmental conditions such as exposure to chemicals or temperature extremes. Manufacturers can provide custom-sized rollers to meet specific operational demands, ensuring that the conveyor system operates efficiently with minimal downtime.
Conveyors are used in a variety of industries to transport materials from one point to another efficiently and safely. They are fundamental in production lines, warehouses, distribution centers, and many other settings. Conveyors can handle a wide range of materials, including but not limited to boxes, pallets, bags, bulk materials, and individual parts. They are particularly crucial in sectors such as manufacturing, mining, agriculture, automotive, electronics, and food processing. Beyond just moving items, conveyors can be equipped with additional features like sorters, dividers, and sensors to perform more complex tasks such as sorting products based on size, weight, or destination, thereby enhancing automation and improving operational efficiency.
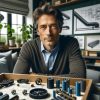
Jordan Smith, a seasoned professional with over 20 years of experience in the conveyor system industry. Jordan’s expertise lies in providing comprehensive solutions for conveyor rollers, belts, and accessories, catering to a wide range of industrial needs. From initial design and configuration to installation and meticulous troubleshooting, Jordan is adept at handling all aspects of conveyor system management. Whether you’re looking to upgrade your production line with efficient conveyor belts, require custom conveyor rollers for specific operations, or need expert advice on selecting the right conveyor accessories for your facility, Jordan is your reliable consultant. For any inquiries or assistance with conveyor system optimization, Jordan is available to share his wealth of knowledge and experience. Feel free to reach out at any time for professional guidance on all matters related to conveyor rollers, belts, and accessories.