Maximize Efficiency with Magnetic Conveyor Roller Solutions
In the realm of modern industrial operations, the advent of magnetic conveyance has marked a significant evolution, especially with the integration of magnetic conveyor rollers. These rollers, embodying the perfect blend of magnetic technology and mechanical engineering, offer a seamless and efficient solution for material handling and movement across various sectors. Magnetic conveyor rollers stand out for their ability to provide contactless movement of ferrous materials, ensuring minimal wear and tear on both the materials being moved and the conveyor system itself. This innovative approach not only enhances the lifespan of the conveyor system but also ensures a reduction in maintenance costs and downtime. In industries ranging from mining and recycling to food processing and manufacturing, the importance of magnetic conveyor rollers cannot be overstated. Their role in improving operational efficiency, safety, and productivity has made them an indispensable component of contemporary industrial machinery. By harnessing the power of magnetism, these rollers offer a revolutionary method of conveying that transcends traditional mechanical constraints, paving the way for more sophisticated and efficient industrial processes.
What are Magnetic Conveyor Rollers?
Magnetic conveyor rollers are at the heart of magnetic conveyance systems, designed to leverage magnetic forces for the seamless and efficient transport of ferrous materials. These rollers are engineered with a core of magnetic material, usually encased in a durable, non-magnetic tube that can withstand the rigors of various industrial environments. The design intricacies of a magnetic conveyor roller allow it to create a magnetic field strong enough to move ferrous objects, aligning with the conveyor’s path without direct contact. This innovative design minimizes physical wear and significantly reduces the need for maintenance.
The structure of a magnetic conveyor roller is a masterpiece of engineering, incorporating magnets that are strategically placed to generate a uniform magnetic field. The outer shell, typically made from stainless steel or another non-magnetic material, is not only robust but also protective of the internal magnetic array. This design ensures that the magnetic field is directed precisely where it is needed, along the surface of the roller, to exert the necessary force on the materials being conveyed.
There are primarily two types of magnetic conveyor rollers available in the market: standard magnetic rollers and high-intensity Rare Earth magnetic rollers. Standard magnetic rollers are suitable for general applications, where they provide adequate magnetic strength for the transport of ferrous materials over short to medium distances. These rollers are widely used in industries such as recycling, where the need for magnetic separation and conveyance is essential but not exceptionally demanding in terms of magnetic strength.
On the other hand, high-intensity Rare Earth magnetic rollers are designed for applications that require an extra level of magnetic force. These rollers employ rare earth magnets, known for their ability to produce a powerful magnetic field in a compact design. This makes them ideal for handling materials that are either very heavy or that present a higher challenge in magnetic separation processes. Industries dealing with mining, mineral processing, and advanced manufacturing find high-intensity Rare Earth magnetic rollers indispensable for their operations.
Magnetic conveyor rollers are a key component in the field of magnetic conveyance, offering a versatile and efficient method for moving ferrous materials. Whether it’s a standard model for everyday tasks or a high-intensity version for more demanding applications, these rollers represent a crucial advancement in industrial technology, streamlining processes, and enhancing productivity.
The Magnetic Head Roller
At the forefront of the magnetic conveyance system is the magnetic head roller, a pivotal element designed to enhance the functionality and efficiency of the magnetic conveyor roller setup. This specialized roller is positioned at the discharge end of the conveyor system, serving a multifaceted role that significantly impacts the material handling process. The magnetic head roller is engineered to provide a powerful magnetic force necessary for the separation and release of ferrous materials from the conveyed goods. Its strategic placement and magnetic prowess ensure a clean and precise separation of materials, which is crucial for the following applications:
- Recycling Industries: In recycling operations, the magnetic head roller is indispensable for separating ferrous metals from a mixed stream of recyclable materials, thereby improving the purity and value of the recycled goods.
- Mining and Mineral Processing: It plays a critical role in extracting ferrous contaminants from crushed ore, enhancing the quality of the ore and protecting downstream processing equipment from potential damage.
- Food Processing: The magnetic head roller ensures food safety by removing metallic contaminants from food products, thus preventing potential health hazards and maintaining consumer trust.
- Manufacturing and Assembly Lines: It is vital for maintaining the integrity of the product by removing any ferrous particles or tools that may have accidentally mixed with the components during the manufacturing process.
The technology behind the magnetic head roller is both sophisticated and elegant. It incorporates a series of permanent magnets, often of the high-intensity Rare Earth type, due to their superior magnetic strength and durability. These magnets are configured in a specific pattern to generate a focused magnetic field across the roller’s surface. As the conveyor belt passes over the roller, the magnetic field attracts and holds ferrous materials, pulling them away from the non-ferrous items and securely holding them until they are carried beyond the influence of the magnetic field. At this point, without the magnetic attraction, the ferrous materials fall away, effectively separated from the rest of the conveyed items.
The design and engineering of the magnetic head roller take into account the need for a strong, consistent magnetic field that can be tailored to specific operational requirements. Factors such as the roller’s diameter, the magnetic field’s intensity, and the speed of the conveyor belt are all critical considerations in maximizing the efficiency and effectiveness of the magnetic separation process. The result is a seamless, automated process that enhances operational efficiency, reduces labor costs, and minimizes the risk of contamination or damage to the machinery or the products being processed. Through the integration of the magnetic head roller, magnetic conveyor rollers not only transport materials but also refine and purify the product stream, showcasing their indispensable role in modern industrial operations.
How Magnetic Conveyor Roller Enhance Industrial Operations
The incorporation of magnetic conveyor rollers into industrial operations has revolutionized the way businesses handle materials, providing a plethora of benefits across a wide range of applications. These rollers are not just components of a conveying system but pivotal instruments that enhance efficiency, safety, and productivity in various sectors. Below are four key industries where magnetic rollers have made a significant impact, followed by four major benefits that these innovative components offer.
Applications Across Industries
- Recycling Sector: Magnetic rollers are crucial for separating metallic waste from non-metallic materials, facilitating recycling processes, and improving the purity of recycled materials. This separation is vital for the efficient recycling of metals and the protection of shredders and grinders from damage.
- Pharmaceutical Industry: In pharmaceutical manufacturing, magnetic rollers help in removing metal contaminants from raw materials, ensuring the safety and purity of medications. This application is critical for maintaining the highest standards of product quality and compliance with health regulations.
- Food Processing: Magnetic conveyor rollers play a pivotal role in food safety by extracting metal debris from food products. This not only helps in complying with food safety standards but also protects consumers from potential health hazards.
- Manufacturing and Assembly: These rollers are used to remove metallic particles and ensure the cleanliness of components in manufacturing lines, especially in the automotive and electronics industries, where precision and cleanliness are paramount.
Benefits of Using Magnetic Rollers
- Enhanced Operational Efficiency: Magnetic rollers automate the process of separating ferrous materials from non-ferrous ones, speeding up production lines and reducing the need for manual sorting.
- 24/7 Operation: Designed for continuous operation, magnetic conveyor rollers can run around the clock without the need for rest periods. This capability is crucial for industries that operate on tight schedules and need to maximize their output.
- No Running Costs: Unlike many other mechanical or electrically powered systems, magnetic rollers do not require energy to operate once they are installed. This absence of running costs significantly reduces the operational expenses of a conveying system.
- Extended Equipment Lifespan: By removing potentially damaging metallic debris from the production line, magnetic rollers prevent wear and tear on machinery. This not only extends the lifespan of the equipment but also reduces maintenance costs and downtime.
The adoption of magnetic conveyor rollers offers an effective solution to several industrial challenges, streamlining operations and bolstering efficiency. Through their diverse applications and substantial benefits, these rollers have become indispensable in modern industrial settings, demonstrating the transformative potential of integrating magnetic technology into traditional conveying systems.
Magnetic Conveyor Roller Specifications
To fully harness the potential of a magnetic conveyor roller in industrial applications, it’s crucial to understand its specifications and how they impact performance. Two key performance metrics stand out: Gauss performance and magnetic field depth. Additionally, the construction materials, notably NdFeB magnets and stainless steel covers, play a significant role in the roller’s functionality and durability.
Performance Metrics
- Gauss Performance: This metric refers to the strength of the magnetic field generated by the roller. Measured in Gauss (G), it indicates the intensity of the magnetic field at the surface of the roller. Higher Gauss values signify a stronger magnetic field, capable of attracting and holding ferrous materials more effectively. This is particularly important in applications requiring the separation of small or weakly magnetic particles.
- Magnetic Field Depth: This specification pertains to how deep the magnetic field penetrates beyond the surface of the roller. A deeper magnetic field can attract and hold ferrous materials from a greater distance, which is crucial for processing bulk materials or for applications where the material is not in direct contact with the roller’s surface. The field depth is influenced by the design of the magnetic array within the roller and the size and type of magnets used.
Construction Materials
- NdFeB Magnets: Neodymium Iron Boron (NdFeB) magnets are among the most powerful permanent magnets available, making them a preferred choice for high-performance magnetic conveyor rollers. These magnets offer a superior Gauss performance, enabling the rollers to generate a strong magnetic field from a compact design. Their high magnetic strength is essential for efficiently separating and conveying ferrous materials, especially in demanding industrial environments.
- Stainless Steel Covers: The external covers of magnetic conveyor rollers are typically made from stainless steel. This material is chosen for its durability, corrosion resistance, and non-magnetic properties. Stainless steel covers protect the internal magnets from physical damage and environmental factors, ensuring the roller maintains its performance over time. Additionally, these covers are easy to clean, which is an essential feature for applications in food processing and pharmaceutical industries where hygiene is a priority.
Understanding these specifications is critical when selecting a magnetic conveyor roller for a specific application. The Gauss performance and magnetic field depth determine the roller’s effectiveness in various operational contexts, while the choice of NdFeB magnets and stainless steel covers affects its longevity and suitability for different industrial environments. By considering these factors, businesses can optimize their material handling processes, achieving higher efficiency and productivity.
Pricing Insights: Magnetic Conveyor Roller Price
Understanding the pricing of magnetic conveyor rollers is essential for budgeting and financial planning in any project involving their use. The price of a magnetic conveyor roller can vary widely based on several factors, each contributing to the final cost. Here, we explore four primary elements that influence the pricing of these essential industrial components, followed by a general price range to aid in budgeting.
Factors Influencing Price
- Material Quality and Type: The type of magnets used (e.g., NdFeB or Ferrite) significantly affects the price. NdFeB magnets, being more powerful, also come with a higher price tag. Additionally, the quality of the stainless steel cover, designed to protect the magnetic core, can influence costs. Higher grades of stainless steel offering better corrosion resistance and durability typically command a higher price.
- Magnetic Strength and Performance Specifications: Rollers designed to generate a higher Gauss performance or deeper magnetic field depth are more complex to manufacture and, consequently, more expensive. These rollers are capable of handling more demanding applications, such as separating fine ferrous particles or working with thick material layers.
- Size and Customization: The dimensions of the magnetic conveyor roller play a crucial role in pricing. Larger rollers, which require more material for both the magnetic core and the outer covering, cost more. Customization to fit specific conveyor systems or to meet unique operational requirements can also add to the cost.
- Market Demand and Availability: The cost of raw materials and the demand for magnetic conveyor rollers can fluctuate, impacting prices. Limited availability of certain magnet grades or stainless steel types due to market conditions can lead to price increases.
Ballpark Pricing
Given the variability in specifications and market conditions, the price of magnetic conveyor rollers can range significantly. For standard magnetic conveyor rollers, prices might start from around $1,000 to $2,500 each for smaller sizes with standard NdFeB magnets. High-intensity or large custom rollers, especially those designed for specific industrial applications or equipped with Rare Earth magnets, can see prices ranging from $2,500 to over $5,000 each. It’s important to note that these prices are indicative and can vary based on the supplier, quantity ordered, and current market conditions.
When budgeting for magnetic conveyor rollers, it’s crucial to consider not only the initial purchase price but also the long-term operational savings they can offer, such as reduced maintenance costs and increased efficiency. Consulting with manufacturers or suppliers can provide more precise pricing based on your specific requirements and the latest market trends.
Availability: Magnetic Conveyor Rollers for Sale
Finding the right magnetic conveyor roller for your industrial application involves knowing where to look. These vital components are available through a variety of channels, ensuring that businesses can find the exact specifications they need to optimize their operations. Moreover, for those looking to economize, considering used magnetic conveyor rollers presents a cost-effective alternative. Below we explore where to find magnetic conveyor rollers for sale and highlight how used rollers can serve as a budget-friendly option.
Where to Find Magnetic Conveyor Rollers
- Manufacturers and Suppliers: The most direct route to purchasing magnetic conveyor rollers is through manufacturers specialized in conveyor technology. Many suppliers offer a range of standard and customizable roller options to fit specific industrial needs.
- Industrial Equipment Distributors: Distributors dealing in industrial conveyor systems and components often stock magnetic conveyor rollers from various manufacturers. This can be a convenient option for comparing different brands and specifications in one place.
- Online Marketplaces: Platforms like Alibaba, Amazon Business, and eBay serve as a marketplace for new and used industrial components, including magnetic conveyor rollers. These platforms can offer competitive pricing and a wide selection of products from global sellers.
- Trade Shows and Expos: Industrial and manufacturing trade shows often feature the latest advancements in conveyor technology, providing an opportunity to see magnetic conveyor rollers firsthand and discuss specifications with suppliers.
Used Magnetic Conveyor Rollers: A Cost-effective Alternative
Opting for used magnetic conveyor rollers can be a prudent financial decision for businesses looking to reduce costs without compromising on functionality.
- Refurbished Rollers: Some suppliers offer refurbished magnetic conveyor rollers, which have been restored to a like-new condition. This option guarantees functionality at a fraction of the cost of new equipment.
- Direct Purchases from Industries: Businesses upgrading their conveyor systems often sell their old equipment directly. Purchasing used rollers from these companies can offer significant savings.
- Online Industrial Auctions: Auction websites specializing in industrial equipment can be a source for finding used magnetic conveyor rollers at lower prices, especially when companies liquidate assets.
- Specialized Used Equipment Dealers: Some dealers focus exclusively on used and refurbished industrial machinery and components. These dealers can be a reliable source for high-quality used magnetic conveyor rollers, often with a warranty or guarantee of performance.
When considering used magnetic conveyor rollers, it’s essential to inspect the equipment thoroughly or purchase from a reputable source to ensure that the rollers will meet your operational requirements. Whether new or used, magnetic conveyor rollers remain a vital component in various industries, enhancing efficiency and productivity through innovative magnetic technology.
Installation and Maintenance for Magnetic Conveyor Roller
Proper installation and maintenance are crucial for maximizing the efficiency and lifespan of magnetic conveyor rollers. These practices ensure that the rollers perform optimally within the conveyor system, providing reliable service over an extended period. Below, we delve into advice for the installation process and maintenance tips for keeping your magnetic conveyor rollers in top condition.
Installation Advice for Magnetic Conveyor Rollers
- Alignment:Ensure that the magnetic conveyor roller is perfectly aligned with the conveyor’s framework. Misalignment can lead to uneven wear and tear, reducing the efficiency of magnetic separation and the overall lifespan of the roller.
- Clearance:Maintain adequate clearance between the magnetic conveyor roller and the conveyor belt or material being conveyed. Too little clearance can cause mechanical wear, while too much can reduce the effectiveness of the magnetic field.
- Electrical Considerations:For rollers designed with an electric motor, verify that all electrical connections are secure and comply with local electrical codes. Proper grounding is essential to prevent any potential electrical hazards.
- Testing:After installation, conduct a thorough test with various materials to ensure that the magnetic conveyor roller is functioning as expected. This testing phase can help identify any adjustments needed to optimize performance.
Maintenance Tips for Prolonged Service Life and Optimal Performance
- Regular Inspections:Conduct periodic inspections to check for signs of wear, misalignment, or damage. Pay particular attention to the roller’s surface and the integrity of the magnetic field. Early detection of issues can prevent costly downtime and repairs.
- Cleaning:Keep the surface of the magnetic conveyor roller clean to maintain its effectiveness. Ferrous materials stuck to the roller can shield the magnetic field, reducing its ability to attract new materials. A scheduled cleaning regimen can prevent this buildup.
- Lubrication:If the roller includes bearings or any moving parts, ensure they are adequately lubricated according to the manufacturer’s recommendations. Proper lubrication reduces friction, wear, and overheating, extending the life of these components.
- Replacement of Worn Parts:Replace any worn or damaged parts promptly. This includes the roller itself, bearings, and any other components that show signs of excessive wear. Using only manufacturer-approved parts for replacements maintains the integrity and performance of the magnetic conveyor roller.
- Following these installation and maintenance guidelines will help ensure that your magnetic conveyor rollers operate efficiently and continue to serve your operational needs for as long as possible. Regular attention and care not only prolong the life of these rollers but also maintain the safety and productivity of the conveyor system as a whole.
Buying Tips for Used Magnetic Conveyor Rollers
Purchasing used magnetic conveyor rollers can be an economical choice for many businesses, but it requires due diligence to ensure that you’re getting a component that will serve your needs without unexpected issues. Understanding how to assess the condition of used magnetic conveyor rollers and knowing the right questions to ask sellers are crucial steps in making an informed decision. Here’s a comprehensive guide to navigating this process successfully.
Assessing the Condition of Used Magnetic Conveyor Rollers
- Visual Inspection: Begin with a thorough visual inspection of the roller. Look for any signs of physical damage, such as dents or cracks on the surface. Also, check for excessive wear on the roller ends where it meets the bearings or frame, as this can indicate heavy use or misalignment.
- Magnetic Strength: If possible, test the magnetic strength of the roller. This can be done using a simple ferrous material to gauge if the roller still has sufficient magnetic pull. A significant decrease in magnetic strength could indicate demagnetization issues.
- Rotation Check: Manually rotate the roller to ensure it moves smoothly without any obstruction or noise. Any irregularities in rotation could signal bearing issues or internal damage to the roller structure.
- Compatibility and Specifications: Verify that the roller’s specifications, such as its magnetic field depth, size, and material, are compatible with your conveyor system and operational requirements. This ensures that the roller will perform effectively in your specific application.
Questions to Ask Sellers
When engaging with sellers of used magnetic conveyor rollers, asking the right questions can provide valuable insights into the roller’s condition and history. Consider the following:
- “How long was the roller in use?” This gives you an idea of the roller’s age and potential wear level. Rollers used for shorter periods may have less wear and a longer remaining lifespan.
- “What application was the roller used for?” Knowing the previous application can help assess whether the roller was subjected to high stress or corrosive materials, which could affect its condition and longevity.
- “Have there been any repairs or replacements done on the roller?” Information on past repairs can indicate recurring issues or modifications that might not meet your needs.
- “Is there a warranty or return policy available?” Even when buying used equipment, some level of guarantee can provide peace of mind and protection against unforeseen defects.
By meticulously assessing the condition of used magnetic conveyor rollers and asking detailed questions about their history and usage, buyers can make confident purchases. This approach not only ensures the acquisition of a functional and reliable component but also maximizes the investment’s value, contributing to efficient and cost-effective operations.
Case Studies and Real-World Applications About Magnetic Conveyor Roller
The transformative impact of magnetic conveyor rollers on various industries is best illustrated through real-world applications and success stories. These case studies showcase how businesses have leveraged magnetic conveyor rollers to address unique challenges, streamline operations, and achieve significant efficiencies. Below, we explore four examples from different sectors, highlighting the innovative use of magnetic rollers and the tangible benefits realized.
Automotive Manufacturing
Challenge: An automotive parts manufacturer faced issues with metal shavings and small ferrous particles contaminating their assembly line, leading to product defects and machinery damage.
Solution: By integrating magnetic conveyor rollers into their production line, the manufacturer was able to capture and remove ferrous debris continuously.
Outcome: This not only improved product quality by reducing contamination but also extended the lifespan of their machinery, resulting in a noticeable decrease in downtime and maintenance costs.
Food Processing
Challenge: A large food processing company struggled with maintaining product purity and adhering to strict safety regulations due to the occasional presence of metallic contaminants in their products.
Solution: Implementing magnetic conveyor rollers in critical points of the processing line enabled the company to effectively remove metallic contaminants from raw materials before packaging.
Outcome: This ensured compliance with food safety standards, significantly reduced the risk of product recalls, and protected consumer health, thereby enhancing the brand’s reputation.
Recycling Industry
Challenge: A recycling facility experienced inefficiencies and low throughput in separating ferrous materials from bulk waste streams, impacting their operational efficiency and profitability.
Solution: The facility upgraded its sorting line with high-intensity magnetic conveyor rollers designed to handle the volume and diversity of materials processed.
Outcome: This upgrade resulted in a dramatic increase in the separation efficiency of ferrous materials, boosting throughput, and allowing the facility to process larger volumes of recyclables more effectively.
Pharmaceutical Production
Challenge: In the pharmaceutical industry, ensuring the absolute purity of products is critical. A manufacturer was challenged by the occasional presence of tiny ferrous contaminants that traditional methods failed to capture.
Solution: By incorporating magnetic conveyor rollers into their material handling systems, the manufacturer was able to capture even the smallest ferrous particles, ensuring an exceptionally high level of product purity.
Outcome: This intervention safeguarded against contamination risks, ensuring that the final products met the stringent standards for pharmaceuticals and enhancing patient safety.
These case studies underscore the versatility and effectiveness of magnetic conveyor rollers across a spectrum of industries. By solving unique industrial challenges, such as improving product purity, protecting machinery, and increasing operational efficiencies, magnetic rollers demonstrate their critical role in modern manufacturing and processing environments. The success stories of businesses deploying this technology further highlight its potential to transform operations and drive significant improvements in productivity and quality.
FAQs About Magnetic Conveyor Roller
A magnetic roller is a critical component in various industrial and manufacturing processes, primarily used for material handling and separation tasks. It leverages magnetic forces to attract and hold ferrous (iron-containing) materials, effectively separating them from non-ferrous materials as part of a conveyor system. This capability makes magnetic rollers invaluable in industries such as recycling, where they facilitate the sorting of metal scraps from other waste, or in manufacturing settings for removing metallic contaminants from product lines. Beyond separation, magnetic rollers are also utilized to transport ferrous materials securely along the production line, preventing slippage and ensuring smooth operation. Their ability to operate continuously without direct contact with the materials minimizes wear and tear, reducing maintenance needs and enhancing system longevity.
A magnetic conveyor utilizes magnetic forces to transport ferrous materials along its path. It consists of a series of magnetic rollers or plates beneath a conveyor belt or within the conveyor frame. When powered, these magnetic components generate a strong magnetic field that attracts and holds ferrous items, pulling them along the conveyor’s path. This method allows for the efficient movement of metal products or scraps, even in vertical or inverted orientations, without the need for physical containment. Magnetic conveyors are particularly beneficial in situations where traditional conveying methods might be hindered by slippage or spillage. They’re also used extensively for material separation, where the conveyor’s magnetic field can isolate ferrous materials from non-ferrous ones, facilitating recycling and quality control processes.
Conveyor rollers come in various types to suit different industrial needs and conveyor designs. The primary types include:
Gravity Rollers: These rollers rely on gravity to move items along the conveyor, making them suitable for lightweight applications and requiring no external power source.
Driven Rollers: Powered by motors or chains, driven rollers are used in automated systems for transporting heavier loads and controlling the conveyor speed.
Grooved Rollers: Designed with grooves to accommodate belts or o-rings, these rollers are used in belt-driven conveyors.
Tapered Rollers: These are used in curves and corners of conveyor systems to maintain the alignment and spacing of items.
Impact Rollers: Positioned at loading points, impact rollers are designed to absorb the shock and stress of heavy items being dropped onto the conveyor, protecting the belt and structure.
Magnetic Rollers: Specialized for handling ferrous materials, magnetic rollers use magnetic fields to transport or separate metal items or scraps.
Each type of roller is tailored for specific operational requirements, considering factors like load capacity, material characteristics, environmental conditions, and the desired movement mechanism.
A gravity roller conveyor is a simple yet effective material handling solution that uses the force of gravity to move items along its path without the need for an external power source. This type of conveyor is typically used for applications where items are manually pushed along the conveyor or moved by gravity, often on a slight decline. Gravity roller conveyors are widely used in various industries, including packaging, warehousing, manufacturing, and distribution centers, due to their simplicity, reliability, and cost-effectiveness. They are particularly suited for moving boxes, packages, pallets, and other items with a firm bottom surface. The key advantages of gravity roller conveyors include their low maintenance, ease of installation, and the ability to easily adjust and expand the system as needed.
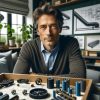
Jordan Smith, a seasoned professional with over 20 years of experience in the conveyor system industry. Jordan’s expertise lies in providing comprehensive solutions for conveyor rollers, belts, and accessories, catering to a wide range of industrial needs. From initial design and configuration to installation and meticulous troubleshooting, Jordan is adept at handling all aspects of conveyor system management. Whether you’re looking to upgrade your production line with efficient conveyor belts, require custom conveyor rollers for specific operations, or need expert advice on selecting the right conveyor accessories for your facility, Jordan is your reliable consultant. For any inquiries or assistance with conveyor system optimization, Jordan is available to share his wealth of knowledge and experience. Feel free to reach out at any time for professional guidance on all matters related to conveyor rollers, belts, and accessories.