Key Features of Resistance Polyurethane Conveyor Rollers
Conveyor rollers play an indispensable role in the seamless operation of numerous industrial systems, where they facilitate the efficient movement of materials across assembly lines and production facilities. Central to these components’ efficacy and longevity is the material from which they are made. Polyurethane, renowned for its exceptional properties, emerges as a superior choice for crafting these rollers. The resistance polyurethane conveyor roller offers against abrasion, coupled with its durability, makes it ideal for handling the rigorous demands of continuous operational cycles in industrial environments. By opting for polyurethane, industries benefit from a reduction in maintenance needs and downtime, enhancing overall productivity and operational cost-efficiency.
The Role of Resistance Polyurethane Conveyor Roller in Industrial Applications
In the realm of industrial operations, the durability and functionality of conveyor systems are pivotal. A key component of these systems is the resistance polyurethane conveyor roller, designed to withstand harsh conditions while maintaining performance. This section delves into the significance of abrasion and wear resistance in these rollers and the challenges they face across various environments.
Importance of Abrasion and Wear Resistance
The resistance polyurethane conveyor roller offers substantial benefits due to its high abrasion and wear resistance. Here are five examples illustrating why this resistance is crucial:
- Mining Operations: In the abrasive environment of mining, rollers are subjected to constant friction and debris. The high resistance of polyurethane extends the life of conveyor rollers, reducing the frequency of replacements.
- Packaging Facilities: High-speed conveyor systems in packaging facilities require rollers that can endure continuous contact with various materials. Resistance polyurethane conveyor rollers maintain their integrity, avoiding deformation over time.
- Food Processing Plants: The cleanliness and non-porous nature of polyurethane prevent food particles from adhering to the rollers, making it ideal for applications requiring strict hygiene standards.
- Recycling Centers: Conveyors in recycling centers deal with a diverse range of materials, from metals to plastics, all of which can wear down lesser materials. Polyurethane’s resistance ensures long-term performance.
- Automotive Manufacturing: The heavy loads and high throughput of automotive parts require rollers that can resist wear while handling significant weight, a task well-suited to polyurethane rollers.
Challenges in Different Industrial Environments
The resistance polyurethane conveyor roller also faces a variety of environmental challenges, each demanding a unique response to maintain efficiency.
- Extreme Temperatures: In foundries or cold storage warehouses, extreme temperatures can affect roller materials. Polyurethane is capable of performing within a wide temperature range without losing its mechanical properties.
- Chemical Exposures: In chemical processing plants, rollers may be exposed to corrosive substances. Polyurethane is chemically resistant, preventing degradation that could compromise roller functionality.
- Wet and Humid Conditions: Industries like paper production or marine loading docks often involve exposure to moisture. Polyurethane’s hydrolytic stability ensures that it does not swell or degrade in wet environments.
- Dusty Environments: In environments such as flour mills or cement factories, dust can accumulate on roller surfaces, leading to wear and failure. The smooth surface of polyurethane rollers makes them easier to clean and less likely to accumulate deposits.
- High Load Stress: In heavy industry sectors like steel production, the intense loads can wear down rollers quickly. Polyurethane’s high load-bearing capacity makes it ideal for these applications, providing both resilience and reliability.
Through understanding the multifaceted role of resistance polyurethane conveyor rollers, industries can better tailor their conveyor systems to meet specific operational demands, ensuring both efficiency and longevity in their mechanical investments.
Advantages of Resistance Polyurethane Conveyor Roller Material: Cast Polyurethane
Polyurethane, particularly in its cast form, is a versatile polymer that provides superior performance over traditional materials used in conveyor rollers. This section will detail the inherent advantages of cast polyurethane and highlight its applications in the manufacture of resistance polyurethane conveyor rollers.
What is Cast Polyurethane?
Cast polyurethane is a type of thermosetting polymer that can be molded into complex shapes and sizes, which is essential for creating specialized industrial components like conveyor rollers. Unlike thermoplastics, cast polyurethane is set through a chemical reaction process, resulting in a material that is incredibly resilient and adaptable to harsh operational demands.
Advantages Over Conventional Materials
The following table outlines the key advantages of cast polyurethane compared to conventional materials like rubber, metal, and plastic:
Property | Cast Polyurethane | Rubber | Metal | Plastic |
---|---|---|---|---|
Abrasion Resistance | Excellent | Good | Poor | Moderate |
Load-Bearing Capacity | High | Moderate | High | Low |
Chemical Resistance | High | Poor | Variable | Moderate |
Temperature Range | Wide | Narrow | Wide | Narrow |
Longevity | Long | Moderate | Long | Short |
These properties make cast polyurethane a prime choice for the core material in resistance polyurethane conveyor rollers, particularly where durability and performance are critical.
Relevance of Cast Urethane Products in Conveyor Roller Manufacturing
Cast urethane products are pivotal in the design and manufacturing of resistance polyurethane conveyor rollers due to their tailored properties.
- Customization Flexibility: The versatility of polyurethane allows it to be cast into virtually any shape and size, meeting specific requirements of conveyor systems in different industries.
- Enhanced Performance: The elasticity of polyurethane provides excellent shock absorption and noise reduction, which are essential for maintaining a smooth and efficient conveyor operation.
- Reduced Maintenance Needs: Due to its wear resistance and mechanical strength, polyurethane rollers require less frequent replacements, thus reducing downtime and maintenance costs.
- Improved Cost-Efficiency: Although the initial cost of polyurethane may be higher than some materials, its longevity and reduced maintenance intervals translate to lower lifecycle costs.
- Environmental Resistance: Resistance polyurethane conveyor rollers can withstand exposure to various chemicals, oils, and water, which often degrade other materials.
Cast polyurethane significantly enhances the functional capabilities of conveyor rollers, making resistance polyurethane conveyor rollers a superior choice for industries seeking reliability and efficiency. This advanced material not only meets the rigorous demands of modern industrial operations but also adapts to the specific environmental challenges faced in different sectors.
Detailed Features of Resistance Polyurethane Conveyor Roller Components
In this section, we delve into the specific resistance features of polyurethane rollers, emphasizing the durability and functionality of resistance polyurethane conveyor roller parts. These components are essential for optimizing the performance and longevity of conveyor systems in harsh industrial conditions.
Examination of Resistance Polyurethane Conveyor Roller Parts
- Core Material: The core is typically made from steel or aluminum, providing structural strength. Covered in polyurethane, it gains enhanced corrosion resistance and load-bearing capacity.
- Coating Layer: The outer layer of polyurethane offers superb abrasion resistance, crucial for rollers operating in environments with particulate matter, sharp objects, or abrasive chemicals.
- Sealing System: High-quality seals prevent contaminants such as dust, water, and other particulates from entering the roller bearings, prolonging the lifespan of the roller.
- Bearings: Encased in polyurethane, the bearings benefit from reduced vibration and noise, as well as increased protection against environmental factors that can cause mechanical wear.
- Shaft Adapter: This component allows the roller to be easily fitted onto different sizes of shafts, with polyurethane providing a snug fit that reduces slippage and wear.
Comparison with Other Materials
The following table compares polyurethane to other common materials used in conveyor rollers—rubber, steel, and PVC—across various performance indicators:
Property | Polyurethane | Rubber | Steel | PVC |
---|---|---|---|---|
Abrasion Resistance | Excellent | Good | Poor | Fair |
Impact Resistance | High | Moderate | Low | Low |
Chemical Resistance | Excellent | Fair | Variable | Poor |
Temperature Tolerance | Excellent | Good | Excellent | Poor |
Maintenance Requirement | Low | Moderate | High | Moderate |
Lifespan | Long | Moderate | Long | Short |
Polyurethane’s superior abrasion resistance and impact absorption make it an ideal choice for applications where durability and reduced maintenance are priorities. Its excellent chemical resistance and temperature tolerance further enhance its suitability for diverse industrial environments, where it outperforms other materials significantly.
These features collectively explain why resistance polyurethane conveyor rollers are favored in industries that demand high performance with minimal downtime. By investing in polyurethane, companies can reduce the frequency of roller replacements and maintenance interventions, thus achieving more consistent production outcomes and lower operational costs. This detailed examination underscores the significance of choosing the right materials for critical components in industrial machinery.
Enhancing Durability with PSI Urethanes in Resistance Polyurethane Conveyor Rollers
PSI Urethanes is a leader in the development and production of high-quality polyurethane for industrial applications, including conveyor rollers. This section explores how PSI Urethanes contributes to the durability and functionality of resistance polyurethane conveyor rollers, focusing on the quality and resilience of these components.
Impact of PSI Urethanes on Conveyor Roller Quality and Resilience
PSI Urethanes enhances the durability of resistance polyurethane conveyor rollers through several key innovations and practices:
- Custom Formulations: PSI Urethanes develops specific polyurethane formulas tailored to meet the unique demands of different industrial environments, improving the wear resistance and load-bearing capabilities of the rollers.
- High-Quality Raw Materials: By using premium-grade raw materials, PSI Urethanes ensures that the polyurethane not only lasts longer but also withstands harsh chemicals, temperatures, and mechanical stress better than standard materials.
- Precision Casting Techniques: Advanced casting techniques are employed to produce rollers with very tight tolerances, ensuring uniform thickness of the polyurethane layer, which enhances the overall strength and performance of the rollers.
- State-of-the-Art Curing Processes: The curing process used by PSI Urethanes optimizes the mechanical properties of polyurethane, such as its elasticity and hardness, making the rollers more resistant to abrasion and deformation.
- Quality Control and Testing: Each batch of resistance polyurethane conveyor rollers undergoes rigorous testing for durability, performance, and resistance to environmental factors, guaranteeing that only the best products are delivered to clients.
Manufacturing Process Enhancements
The manufacturing process of resistance polyurethane conveyor rollers at PSI Urethanes is meticulously designed to enhance their resistance and durability:
- Material Preparation: The polyurethane prepolymer and curative are precisely measured and mixed to achieve the desired mechanical properties.
- Molding and Casting: Rollers are cast using custom molds that shape the polyurethane to exact specifications. This process ensures that the polyurethane adheres flawlessly to the roller cores, eliminating weaknesses that could lead to premature wear or failure.
- Post-Curing Enhancement: After demolding, the rollers undergo a post-curing process that further enhances their mechanical strength and chemical resistance.
- Finishing and Inspection: Each roller is finely ground to the perfect diameter and inspected for any imperfections. This step ensures that all rollers maintain a high standard of quality and uniformity.
- Performance Testing: Finally, the rollers are tested under simulated conditions that mimic their intended industrial environment. This includes testing for abrasion resistance, load-bearing capacity, and resilience to various chemicals and temperatures.
Through these detailed processes and the commitment to quality, PSI Urethanes significantly contributes to the durability and efficiency of resistance polyurethane conveyor rollers. Industries leveraging these high-performance rollers can expect reduced downtime, lower maintenance costs, and improved overall efficiency, highlighting the critical role of advanced materials and manufacturing techniques in modern industrial operations.
Maximizing Durability through Rubber Compression Calculation in Resistance Polyurethane Conveyor Rollers
Understanding the technical aspects of material science, particularly rubber compression calculation, is pivotal in designing durable and efficient resistance polyurethane conveyor rollers. This section delves into how these calculations influence roller performance and contribute to the superior resistance and durability of polyurethane rollers.
Importance of Rubber Compression Calculation
Rubber compression calculation is a critical aspect of designing conveyor rollers, as it determines how much a roller will deform under load. This deformation, or compression set, directly affects the roller’s ability to absorb impacts, maintain shape, and return to its original form. For resistance polyurethane conveyor rollers, mastering this calculation ensures that the rollers can withstand heavy loads without permanent deformation, which is essential for maintaining the integrity and efficiency of the conveyor system.
Technical Specs and Performance Implications
Rubber compression calculation involves assessing the material’s stress-strain behavior, which describes how the material reacts to being compressed and how it recovers. The ideal material for conveyor rollers should exhibit a low compression set, meaning it experiences minimal permanent deformation after being subjected to compressive forces.
- Stress-Strain Curves: These curves are generated from testing the material under controlled conditions to see how it behaves under compression. For polyurethane, the curve helps determine at what point the material yields to permanent deformation.
- Modulus of Elasticity: This is the measure of the stiffness of the rubber material, which is crucial for understanding how much it can flex under load without being damaged.
- Compression Set Under Load: This measurement assesses how much the roller material permanently deforms after a specified time under a defined load at a certain temperature.
Relevance to Polyurethane Roller Design
When designing resistance polyurethane conveyor rollers, utilizing rubber compression calculations helps engineers optimize the material formulation and roller structure for maximum performance. Here’s how these calculations are integrated into the design process:
- Material Selection: By understanding the compression characteristics, engineers can select or formulate a polyurethane mix that balances flexibility and stiffness, ensuring the roller can absorb impacts without sustaining damage.
- Dimensional Accuracy: Accurate rubber compression calculations allow designers to predict how the roller will behave under real-world conditions, enabling them to specify the correct roller dimensions that will perform optimally within the intended load parameters.
- Performance Optimization: These calculations help in fine-tuning the polyurethane properties to enhance the wear resistance, reduce downtime due to deformation, and extend the overall lifespan of the rollers.
- Customization for Specific Applications: Different industrial applications may require rollers to withstand varying loads and environmental conditions. Rubber compression calculations guide the customization of polyurethane rollers to meet these specific requirements effectively.
Through the precise application of rubber compression calculations, resistance polyurethane conveyor rollers are designed to meet the highest standards of durability and efficiency. This scientific approach ensures that each roller is capable of performing under intense industrial conditions, thereby safeguarding the operational continuity and productivity of the conveyor systems they are a part of.
Innovation in Resistance Polyurethane Conveyor Roller Design: The Role of Cast Urethane Products
The application of cast urethane in the design of resistance polyurethane conveyor rollers represents a significant advancement in the engineering of industrial conveyor systems. This section explores the meticulous process of creating cast urethane products and highlights the benefits of choosing cast polyurethane rollers, especially for heavy-duty applications.
Process of Creating Cast Urethane Products
The creation of cast urethane products for resistance polyurethane conveyor rollers involves several critical steps:
- Formulation of Urethane Pre-Polymer: The process begins with the formulation of a urethane pre-polymer tailored to meet specific performance requirements such as hardness, resilience, and temperature resistance.
- Mold Design and Preparation: Custom molds are designed and prepared, often from aluminum or steel, to shape the urethane into the desired form of the conveyor roller.
- Mixing and Casting: The pre-polymer is mixed with a curing agent and other additives, then poured into the prepared molds. This mixture is carefully degassed to eliminate any air bubbles before curing.
- Curing and Post-Curing: The urethane is allowed to cure at controlled temperatures. Post-curing may follow to enhance the mechanical properties and dimensional stability of the final product.
- Demolding and Finishing: Once cured, the rollers are removed from the molds. They undergo various finishing processes, such as grinding and polishing, to meet precise dimensional and surface finish specifications.
Benefits of Cast Polyurethane Rollers for Heavy-Duty Use
Choosing cast polyurethane for conveyor rollers offers numerous advantages, particularly in heavy-duty industrial settings:
- Superior Wear Resistance: Cast polyurethane is highly resistant to abrasion and wear, which is critical in environments with high particulate matter or abrasive materials.
- Enhanced Impact Resistance: The shock-absorbing properties of cast polyurethane protect the roller and conveyor system from impacts and vibrations, prolonging the lifespan of both.
- Chemical and Oil Resistance: Cast polyurethane is impervious to many chemicals and oils, making it ideal for use in chemical processing plants or facilities where oil spillage is common.
- Customizable Hardness Levels: The hardness of cast polyurethane can be adjusted to suit specific applications, from soft rollers that grip fragile items to hard rollers capable of moving heavy loads.
- Reduced Maintenance and Downtime: The durability and resilience of cast polyurethane minimize the need for frequent roller replacements and maintenance checks, thereby reducing operational downtime and maintenance costs.
These characteristics make resistance polyurethane conveyor rollers an essential component in the design of efficient, reliable, and cost-effective conveyor systems. By incorporating cast urethane products, industries can achieve higher operational standards, ensuring that their conveyor systems operate smoothly under the toughest conditions. The innovative use of cast urethane not only enhances the performance of conveyor rollers but also contributes significantly to the overall productivity and sustainability of industrial operations.
Tailored Efficiency: Customizing Resistance Polyurethane Conveyor Rollers with PSI Urethanes
PSI Urethanes stands out in the industrial sector for its ability to provide custom-made solutions that precisely meet the varied demands of different industries. This section highlights the distinct advantages of choosing custom-made resistance polyurethane conveyor rollers from PSI Urethanes and explores the customization options available to enhance their resistance and load-bearing capacities.
Advantages of Custom-Made Polyurethane Rollers by PSI Urethanes
Custom-made resistance polyurethane conveyor rollers from PSI Urethanes offer several key advantages:
- Precision Fit and Performance: Custom rollers are designed to fit perfectly within the specific machinery, reducing mechanical stress and enhancing the efficiency of the conveyor system.
- Optimized Material Properties: PSI Urethanes can tailor the polyurethane’s chemical composition to improve performance attributes like abrasion resistance, impact strength, and load-bearing capacity, ensuring the roller suits the specific environmental conditions it will face.
- Enhanced Longevity: Custom-designed rollers can be optimized for durability, significantly extending the operational lifespan of the rollers in harsh industrial environments, thus reducing the need for frequent replacements.
- Improved Operational Efficiency: With rollers specifically designed to meet the precise needs of an application, the overall efficiency of the conveyor system is improved. This customization helps minimize downtime and maintenance costs.
- Versatility in Application: PSI Urethanes’ ability to provide custom solutions makes it possible to use their rollers in a variety of industrial settings, from food processing and pharmaceuticals to heavy manufacturing and mining.
Customization Options and Industrial Catering
PSI Urethanes offers extensive customization options that cater to specific industrial needs regarding resistance and load-bearing:
- Custom Formulations: Depending on the application’s needs, PSI Urethanes can adjust the hardness, elasticity, and resistance properties of the polyurethane. This customization is crucial for applications that require unique solutions for abrasion, chemical exposure, or extreme temperatures.
- Dimensional Customization: Rollers can be manufactured in any size or shape, which is particularly beneficial for unique or non-standard conveyor systems where standard rollers are not suitable.
- Color Coding: Rollers can be produced in different colors, aiding in quick visual identification for maintenance or operational purposes, which is particularly useful in complex multi-line facilities.
- Surface Treatments: Various surface textures and coatings can be applied to meet additional specifications, such as increased grip for slippery materials or smoothed surfaces for delicate goods.
- Integrated Technologies: Rollers can incorporate advanced features like anti-static properties, UV resistance, or enhanced thermal properties to handle special operational requirements.
By offering these customization options, PSI Urethanes ensures that each resistance polyurethane conveyor roller is not only a part of the conveyor system but an enhancement to it, providing tailored solutions that directly address the specific challenges and needs of any industrial application. These custom solutions underscore the company’s commitment to innovation and customer satisfaction, solidifying its reputation as a leader in the polyurethane manufacturing industry.
FAQs About Resistance Polyurethane Conveyor Roller
Polyurethane rollers offer several advantages over rollers made from other materials such as rubber, steel, or PVC. Firstly, polyurethane is renowned for its exceptional abrasion resistance, which significantly extends the roller’s lifespan in environments where wear and tear are common. This material also possesses excellent load-bearing capabilities, which prevents deformation under heavy weights, ensuring stable and reliable conveyor operations.
Additionally, polyurethane is highly resistant to chemicals, oils, and various solvents, making it suitable for use in a wide range of industrial settings, including chemical processing and food production. The material’s versatility allows it to perform well under extreme temperature variations, maintaining its integrity and functionality whether in hot or cold environments. Furthermore, polyurethane rollers can be custom formulated to achieve specific properties such as hardness, resilience, and resistance to UV light, providing tailored solutions that meet precise operational needs. Overall, the use of polyurethane enhances the efficiency and durability of conveyor systems, reducing maintenance needs and operational costs.
A PU coated roller refers to a conveyor roller that has been coated with a layer of polyurethane (PU). This coating is applied to enhance the roller’s performance characteristics in several key areas. PU coating improves the roller’s abrasion resistance, making it more durable against wear and tear from continuous contact with materials being conveyed. This is particularly beneficial in industries where the conveyor system handles abrasive materials.
The polyurethane coating also offers excellent grip and traction, which helps prevent slippage of materials and ensures smoother operation of the conveyor system. This feature is crucial in applications such as packaging lines where precise movement and positioning of items are required. Additionally, PU coated rollers are resistant to corrosion and chemical damage, which makes them ideal for use in harsh environments where they might be exposed to aggressive cleaning agents, chemicals, or moist conditions. The coating also helps dampen noise, creating a quieter working environment. PU coated rollers are versatile, durable, and can be customized to fit specific industrial requirements, enhancing the functionality and longevity of conveyor systems.
Conveyor rollers can be made from a variety of materials, each selected based on the specific needs of the application and the environment in which they will operate. Common materials include:
Steel: Highly durable and suitable for heavy-duty applications. Steel rollers can handle high loads and are often used in mining and quarrying operations.
Stainless Steel: Used in environments that require cleanliness and resistance to corrosion, such as food processing, pharmaceuticals, and chemical industries.
Aluminum: Lighter than steel and resistant to corrosion, aluminum rollers are used in applications where weight is a concern, such as in packaging and light manufacturing processes.
Plastic: Often used in lighter applications and where moisture resistance is necessary. Plastic rollers are less expensive and provide adequate performance in less demanding environments.
Rubber-Coated: Provide extra grip and noise reduction. Suitable for handling fragile or delicate materials that require gentle handling to prevent damage.
Polyurethane (PU): Known for their abrasion resistance and ability to reduce noise. Polyurethane rollers are versatile and can be used in both light and heavy-duty applications across various industries.
The choice of material depends on factors such as load capacity, environmental conditions, potential exposure to chemicals, and the need for noise reduction, among others.
The term “standard conveyor roller” typically refers to a roller designed to fit the most common specifications for size, load capacity, and material handling capabilities in various industries. These rollers are manufactured in a range of standard diameters and lengths to suit different conveyor widths and load requirements. The most common diameters range from about 1.9 inches to 3.5 inches, with lengths varying according to the width of the conveyor belt they are supporting.
Standard rollers are designed to handle a variety of materials and conditions with moderate load capacities and speed requirements. They are constructed using materials such as steel, stainless steel, or aluminum, and may also feature coatings or coverings such as rubber or polyurethane for enhanced performance. Standard conveyor rollers are widely used in industries like manufacturing, distribution, logistics, and packaging, where they contribute to the smooth and efficient operation of conveyor systems. The choice of a standard roller is often dictated by the balance between cost and performance, providing a reliable solution for general-purpose conveyor applications.
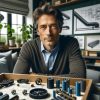
Jordan Smith, a seasoned professional with over 20 years of experience in the conveyor system industry. Jordan’s expertise lies in providing comprehensive solutions for conveyor rollers, belts, and accessories, catering to a wide range of industrial needs. From initial design and configuration to installation and meticulous troubleshooting, Jordan is adept at handling all aspects of conveyor system management. Whether you’re looking to upgrade your production line with efficient conveyor belts, require custom conveyor rollers for specific operations, or need expert advice on selecting the right conveyor accessories for your facility, Jordan is your reliable consultant. For any inquiries or assistance with conveyor system optimization, Jordan is available to share his wealth of knowledge and experience. Feel free to reach out at any time for professional guidance on all matters related to conveyor rollers, belts, and accessories.