Conveyor Roller Material Suit You
In the vast world of industrial applications, conveyor systems stand out as the backbone of material handling, streamlining the movement of goods across facilities. At the heart of these systems lies a crucial component—the conveyor roller, whose material can significantly influence efficiency, durability, and cost-effectiveness. This guide aims to shed light on the various types of conveyor roller material, underscoring their importance in selecting the optimal solution for different industrial needs. From the rugged demands of mining and heavy manufacturing to the precise requirements of pharmaceuticals and food processing, the choice of conveyor roller material directly impacts the conveyor’s performance and longevity. As we delve into the essentials of roller materials, we’ll explore how each option serves distinct applications, guiding you through the selection process to enhance your operations.
Conveyor Roller Types and Their Impact on Material Selection
Choosing the right type of conveyor roller is paramount to achieving optimal performance in material handling systems. The material of the conveyor roller plays a vital role in its suitability for specific tasks and environments.Conveyor roller materials include steel, stainless steel, plastic, and rubber-coated options for specific applications. Here, we explore the different types of conveyor rollers and how the choice of roller conveyor material affects their application.
Gravity Rollers
Gravity rollers are the simplest and most cost-effective type. They rely on gravity to move items across flat or slightly inclined surfaces. Ideal for light to medium-weight products, these rollers are commonly made from plastic or steel. The choice of conveyor roller material here depends on the load; steel for durability and heavier loads, and plastic for lighter applications.
Applications: Warehousing, packaging, and assembly lines where manual loading and unloading are feasible.
Motor-driven Rollers
Motor-driven rollers, powered by an external source, are perfect for moving heavy loads or for applications where precise control of the roller speed is necessary. The conveyor roller material, often steel or aluminum, is selected based on strength requirements and the need for corrosion resistance.
Applications: Automotive manufacturing, airport baggage handling, and food processing where consistent and reliable movement is crucial.
Grooved Rollers
Grooved rollers are designed with grooves that engage with belts or chains, providing drive force to the conveyor. The material of these rollers can be metal or plastic, depending on the application’s demands for load capacity and environmental conditions.
Applications: Postal sorting offices, document handling, and packaging lines where alignment and accurate positioning are key.
Heavy Duty Rollers
Built to handle the highest loads and toughest conditions, heavy-duty rollers are usually constructed from steel or specialized alloys. The choice of conveyor roller material is critical for industries that demand durability and resistance to wear and tear.
Applications: Mining, construction, and heavy manufacturing, where rollers must withstand harsh conditions and heavy materials.
Determining the Right Type for Your Industry
Selecting the appropriate roller type and material involves considering several factors:
- Load Weight: Heavier loads require more durable materials like steel.
- Environment: Corrosive or sanitary environments may necessitate stainless steel or plastic.
- Speed Requirements: High-speed applications might benefit from motor-driven rollers.
- Budget Constraints: Gravity rollers offer a cost-effective solution for simpler applications.
- Maintenance Considerations: The ease of maintenance and replacement can influence material choice, with some materials offering longer life spans with less upkeep.
These aspects will guide you in selecting the conveyor roller material that best fits your operational needs, ensuring efficiency, durability, and cost-effectiveness in your conveyor system.
Assessing Conveyor Roller Material and Capacity
In environments where the demands on conveyor systems are extreme, selecting heavy-duty conveyor rollers is essential. These rollers are designed to withstand high loads, abrasive conditions, and continuous operation without compromise. Understanding what qualifies as heavy-duty rollers and the specific capacities and conveyor roller material requirements for these applications is crucial for ensuring the longevity and efficiency of your conveyor system.
What Qualifies as Heavy-Duty Rollers
Heavy-duty conveyor rollers are characterized by their ability to handle significantly higher loads and more rigorous operating conditions than standard rollers. These qualities are achieved through:
- Robust Materials: Heavy-duty rollers are often made from materials such as hardened steel, stainless steel, or even reinforced plastics, which offer superior strength and durability.
- Enhanced Design: They may feature thicker walls, larger diameters, and reinforced bearings or housings to improve load-bearing capacity and reduce wear.
- Special Coatings: To resist corrosion, abrasion, and wear, heavy-duty rollers can be coated with materials like polyurethane, rubber, or specialized paints.
The Capacities and Material Requirements for Heavy-Duty Applications
The choice of conveyor roller material and design for heavy-duty applications hinges on several factors, each critical to the roller’s performance under challenging conditions:
- Load Capacity: Heavy-duty rollers are engineered to support loads that can significantly exceed standard operational weights, often necessary in industries such as mining, construction, and heavy manufacturing. The material and diameter of the roller must be selected based on the maximum load it will consistently bear.
- Environmental Conditions: The operating environment plays a crucial role in selecting the appropriate conveyor roller material. For example, stainless steel may be preferred for its corrosion resistance in wet or chemical environments, while reinforced plastics may be chosen for their weight advantages and corrosion resistance in less abrasive conditions.
- Operational Speed: High-speed applications require rollers designed to minimize friction and heat buildup, ensuring longevity. Materials and bearings are chosen for their ability to maintain integrity and performance at high rotational speeds.
- Maintenance and Lifespan: The expected lifespan of the roller and the maintenance regime also influence material choice. Materials that can withstand wear and tear with minimal maintenance are preferred for heavy-duty applications to ensure continuity in operations and reduce downtime.
When choosing heavy-duty conveyor rollers, it’s essential to consult with manufacturers and engineers who can provide insight into the most suitable materials and designs for your specific needs. The right choice of conveyor roller material and capacity specifications not only enhances the efficiency and reliability of your conveyor system but also significantly impacts its overall cost-effectiveness and operational lifespan.

Essentials of Conveyor Roller Materials
Selecting the appropriate conveyor roller material is a pivotal decision that affects the performance, durability, and cost-efficiency of a conveyor system. This section dives into the critical nature of this choice, backed by a comparative analysis of commonly used materials.
Why Material Choice Is Critical for Conveyor Rollers
- Load Capacity: Different materials can support varying load weights, with steel being ideal for heavy loads and plastic for lighter goods.
- Environment Compatibility: Some environments may be corrosive or require a high level of sanitation, necessitating materials like stainless steel or plastic.
- Speed and Efficiency: The material’s weight influences the roller’s inertia, affecting the speed and energy efficiency of the conveyor system.
- Durability and Wear Resistance: Materials like steel and aluminum offer high durability, whereas plastic may wear faster but offers quiet operation.
- Cost Implications: Initial investment and long-term maintenance costs can vary significantly based on the material, impacting overall cost-effectiveness.
Comparative Analysis of Commonly Used Materials
The following table presents a comparative analysis of the five most common conveyor roller materials: plastic, steel, stainless steel, galvanized steel, and aluminum.
Material | Durability | Weight | Cost | Corrosion Resistance | Application |
---|---|---|---|---|---|
Plastic | Low | Light | Low | Moderate | Light-duty applications, environments requiring low noise |
Steel | High | Heavy | Moderate | Low | Heavy-duty applications, high load capacity |
Stainless Steel | High | Heavy | High | High | Food processing, pharmaceuticals, corrosive environments |
Galvanized Steel | Moderate | Heavy | Moderate | Moderate | Outdoor applications, moderate corrosion resistance |
Aluminum | Moderate | Light | Moderate | Low to Moderate | Lightweight applications, where moderate durability is needed |
The Influence of Material on Durability, Weight, and Cost
Durability: Steel and stainless steel rank highest in durability, making them suitable for environments where rollers face constant use or heavy loads. Aluminum and plastic, while less durable, offer advantages in specific applications requiring lighter weights or corrosion resistance.
Weight: The weight of the material affects the system’s energy efficiency and operational cost. Lighter materials like plastic and aluminum require less energy to move, which can lead to savings in power consumption.
Cost: Initial costs can vary, with plastic being the most economical option and stainless steel being the most expensive due to its enhanced properties. However, the total cost of ownership, including maintenance and replacement costs, must also be considered. Durability and maintenance requirements can offset the initial investment over time.
These essentials of conveyor roller material helps in making an informed decision that aligns with operational needs, budget constraints, and environmental conditions, ensuring the long-term success and efficiency of the conveyor system.
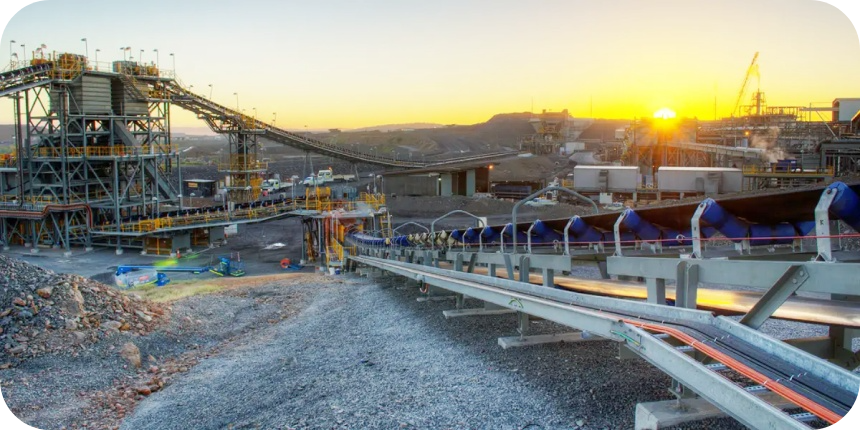
Conveyor Roller Replacement
The longevity and efficiency of a conveyor system significantly depend on the condition of its rollers. Over time, wear and tear on the conveyor roller material can lead to the necessity for replacement. Understanding when and why to replace conveyor rollers, as well as the steps involved in their replacement, is crucial for maintaining the optimal performance of your conveyor system.
Indications That Rollers Need Replacement
Several signs indicate the need for conveyor roller replacement:
- Visible Damage: Cracks, dents, or significant wear on the roller surface can impair functionality.
- Unusual Noises: Squeaking, grinding, or other abnormal sounds may suggest that the rollers are not rotating smoothly.
- Inconsistent Movement: Products that wobble or stray off their path can signal uneven wear or damage to rollers.
- Increased Resistance: If the conveyor requires more power to move the same loads, the rollers might be failing.
The Impact of Worn-Out Rollers on Conveyor Efficiency
Worn-out rollers can drastically affect the efficiency and safety of a conveyor system. Damaged rollers can cause product mishandling, leading to potential damage to goods or creating hazards in the workplace. Furthermore, the additional stress on the conveyor motor to overcome increased resistance can lead to higher energy consumption and premature equipment failure. Regularly assessing and replacing compromised rollers, considering the specific conveyor roller material, is essential to avoid these issues.
Step-by-Step Guide to Replacing Rollers
Replacing conveyor rollers is a straightforward process that can significantly extend the life of your conveyor system. Here’s how to do it:
- Safety First: Ensure the conveyor is turned off and locked out to prevent accidental startup.
- Identify the Damaged Rollers: Inspect the conveyor and mark rollers that show visible signs of wear or damage.
- Remove the Damaged Rollers: Depending on the system, this may involve loosening bolts or clips that hold the roller in place. Carefully slide the roller out from the frame.
- Select the Right Replacement: Choose a replacement roller that matches the original specifications, including the type and material. It’s crucial that the new roller is compatible with the existing conveyor roller material and design for seamless operation.
- Install the New Roller: Slide the new roller into position and secure it with the original fasteners or clips. Ensure it is properly aligned with adjacent rollers for smooth operation.
- Test the Conveyor: Once all replacements are installed, unlock the system and run the conveyor empty to ensure smooth operation and correct alignment.
Regular maintenance and timely replacement of conveyor rollers, with attention to the specific conveyor roller material, are vital practices that prevent downtime and maintain the efficiency of your conveyor system. By following these guidelines, you can ensure your conveyor continues to operate smoothly, supporting your operational needs efficiently.

Selecting the Right Conveyor Roller Manufacturer: Prioritizing Conveyor Roller Material
When it comes to maintaining the efficiency and longevity of your conveyor system, choosing the right conveyor roller manufacturer is as critical as the material roller conveyor itself. The right manufacturer not only provides quality products but also supports your operations with a variety of materials, customization options, and exceptional service. Here are the essential factors to consider:
Material Variety
Different applications require different conveyor roller materials, each with unique properties that affect performance, durability, and cost. A top-tier manufacturer offers a wide variety of materials, including plastic, steel, stainless steel, galvanized steel, and aluminum. This variety ensures you can select the most appropriate material for your specific environment and load requirements.
Customization Options
No two conveyor systems are exactly alike. The ability to customize roller dimensions, material, and features is crucial for optimizing your system’s performance. Whether you need a specific roller diameter, bearing type, or coating, the right manufacturer should accommodate these needs. Customization also extends to solutions for unique challenges, such as extreme temperatures, corrosive environments, or unusual loads.
Support and Service
Post-purchase support and service are indicative of a manufacturer’s reliability and commitment to customer satisfaction. This includes timely delivery, responsive customer service, and accessible technical support. Additionally, consider manufacturers who offer maintenance advice and assistance with selecting the right conveyor roller material and specifications for new or replacement rollers.
Tips for Sourcing Reliable Material Suppliers
- Research and Referrals: Start with thorough research and seek referrals from industry peers. Positive testimonials from trusted sources can lead you to reputable suppliers.
- Industry Reputation: Consider suppliers with a strong reputation in the industry. Look for awards, recognitions, or certifications that indicate a commitment to quality and innovation.
- Supply Chain Transparency: Choose suppliers who provide clear information about their supply chain, sourcing practices, and production processes. Transparency is key to assessing the sustainability and ethics of their operations.
- Technical Support: Opt for suppliers that offer comprehensive technical support, including assistance in selecting the right conveyor roller material for your specific needs.
- Sample Testing: Request samples of the conveyor roller material for testing under your specific operational conditions. This can help you evaluate the quality and suitability of the material firsthand.
The Importance of Material Quality and Consistency
nufacturer should adhere to stringent quality control standards across all stages of production. This ensures that the conveyor roller material not only meets industry specifications but also your specific operational needs. Look for certifications or accreditations that attest to the manufacturer’s commitment to quality.
- Durability and Longevity: High-quality materials result in rollers that are more durable and have a longer lifespan, reducing the need for frequent replacements.
- Operational Efficiency: Consistent material quality ensures that each roller performs reliably, maintaining the overall efficiency of the conveyor system.
- Safety: Superior material quality reduces the risk of roller failure, which can lead to accidents and injuries, ensuring a safer workplace.
- Cost Savings: Investing in quality materials can lead to cost savings over time, as it minimizes downtime, maintenance, and replacement costs.
- Compliance: High-quality materials are more likely to meet industry standards and regulations, ensuring compliance and avoiding potential legal issues.
How to Assess Supplier Credibility and Track Record
- Years in Business: Long-standing suppliers are likely to have accumulated extensive experience and a proven track record of reliability.
- Client Portfolio: A diverse and reputable client base can be a strong indicator of the supplier’s credibility and the quality of their conveyor roller material.
- Reviews and Feedback: Look for online reviews, case studies, and client testimonials. Negative reviews, especially those mentioning quality issues, are red flags.
- Financial Stability: Financially stable suppliers are more likely to maintain consistent quality and fulfill orders promptly.
- Compliance and Certifications: Ensure the supplier complies with industry standards and holds relevant certifications. This can include ISO certifications or specific product quality standards relevant to conveyor roller materials.
By carefully selecting your conveyor roller material suppliers based on these guidelines, you can ensure a high level of quality and reliability in your conveyor system components. This proactive approach will help you maintain operational efficiency, minimize downtime, and achieve a better return on investment.
Selecting the right conveyor roller manufacturer requires a careful assessment of these factors. The quality of the conveyor roller material, the variety of materials offered, the ability to customize products, and the level of post-purchase support and service all contribute to the success of your conveyor system. Prioritize manufacturers who not only meet these criteria but also demonstrate a clear understanding of your industry’s specific needs and challenges.

Ensuring Longevity of Conveyor Roller Material
Maintaining the integrity and functionality of conveyor rollers is essential for the smooth operation of any conveyor system. Understanding the components that make up a conveyor roller and how to maintain them is critical. This section focuses on the breakdown of conveyor roller parts, maintenance tips for extending the lifespan of conveyor roller material, and troubleshooting common issues associated with these materials.
Breakdown of the Parts of a Conveyor Roller
Conveyor rollers consist of several key components, each playing a vital role in its operation:
- Bearings: Facilitate smooth rotation of the roller with minimal friction.
- Axles: Connect the roller to the conveyor frame, allowing rotation.
- Tube: The outer shell of the roller, made from the chosen conveyor roller material, supports the conveyed items.
- Sprockets (for driven rollers): Engage with the conveyor belt or chain to provide motion to the roller.
- End caps: Seal the ends of the roller, protecting the bearings from dust and debris.
Maintenance Tips for Prolonging Roller Lifespan
Proper maintenance can significantly extend the life of conveyor rollers and their components.
- Regular Cleaning: Keep rollers clean of dust, debris, and any material buildup to prevent wear and tear on the conveyor roller material.
- Lubrication: Periodically lubricate bearings to ensure smooth operation and prevent overheating and wear.
- Inspection: Routinely inspect rollers for signs of wear, damage, or misalignment. Pay special attention to the condition of the conveyor roller material, looking for cracks, warping, or excessive wear.
- Alignment Checks: Ensure rollers are properly aligned within the conveyor frame to prevent uneven wear and potential damage to the roller material.
- Replacement of Worn Parts: Replace bearings, axles, or the entire roller if wear is significant, to prevent failure and maintain efficiency.
Troubleshooting Common Roller Material Issues
The choice of conveyor roller material can influence the type of issues you may encounter. Here are common problems associated with different materials and how to address them:
- Plastic Rollers: May become warped or cracked under excessive load or in high-temperature environments. Regularly check for deformities and replace as needed.
- Steel and Stainless Steel Rollers: Susceptible to corrosion if exposed to harsh chemicals or if used in wet environments. Inspect for rust or pitting and consider galvanized or coated options for better resistance.
- Aluminum Rollers: While lightweight and corrosion-resistant, they can dent under heavy loads. Monitor for dents or bending that could affect roller performance.
- Galvanized Steel Rollers: The zinc coating offers corrosion resistance, but the layer can wear off over time, exposing the steel underneath to rust. Check the integrity of the coating periodically.
By understanding the components that constitute a conveyor roller, implementing regular maintenance routines, and troubleshooting common material-specific issues, you can ensure the longevity and reliability of your conveyor system. The right care and attention to the conveyor roller material not only prolong the life of the rollers but also maintain the efficiency and productivity of the entire system.
High-quality conveyor rollers available. Contact us for more information!
Success Stories with Different Conveyor Roller Material
The selection of material roller conveyor plays a pivotal role in the optimization of conveyor systems across various industries. Through real-world examples, this section highlights how businesses have achieved significant benefits, such as cost savings and reduced downtime, by choosing the appropriate roller materials for their specific needs.
Food Processing Industry – Stainless Steel Rollers
A leading food processing plant faced frequent downtime due to corrosion and contamination of their conveyor rollers. By switching to stainless steel rollers, known for their corrosion resistance and easy cleaning, the plant significantly reduced contamination risks and maintenance time. The switch led to a 30% reduction in downtime and a noticeable improvement in compliance with food safety standards.
Warehouse Distribution Center – Plastic Rollers
A large distribution center struggled with noise levels and energy costs due to their extensive conveyor system. The adoption of plastic rollers, which are lighter and operate more quietly than metal alternatives, resulted in a quieter working environment and a 20% decrease in energy consumption due to the lower power required to move the lighter rollers.
Heavy Manufacturing Facility – Steel Rollers
A heavy manufacturing facility frequently replaced worn-out rollers, incurring high costs and operational delays. Transitioning to heavy-duty steel rollers, which offer superior durability and load-bearing capacity, extended the lifespan of their conveyor system components by 50%. This switch resulted in significant cost savings in maintenance and replacement parts.
Chemical Processing Plant – Galvanized Steel Rollers
Exposed to harsh chemicals and fluctuating temperatures, a chemical processing plant experienced rapid deterioration of their conveyor rollers. Implementing galvanized steel rollers, which provide excellent corrosion resistance and durability in harsh environments, led to a 40% improvement in roller lifespan and reduced the frequency of replacements.
E-commerce Fulfillment Center – Aluminum Rollers
An e-commerce fulfillment center needed to increase the speed and efficiency of their sorting and packaging line. By installing lightweight aluminum rollers, the center benefited from faster conveyor speeds and improved efficiency. The change contributed to a 25% increase in parcel throughput and a reduction in energy costs due to the lower inertia of aluminum rollers.
Analysis of Benefits Achieved
These case studies demonstrate the critical impact that the right roller conveyor material can have on operational efficiency, cost savings, and system longevity. Key benefits observed include:
- Cost Savings: Reduced maintenance and replacement costs by selecting materials that better withstand the operational environment.
- Reduced Downtime: Enhanced durability and material suitability led to less frequent breakdowns and operational interruptions.
- Improved Efficiency: Lighter materials like plastic and aluminum can reduce energy consumption and increase throughput.
- Enhanced Safety and Compliance: Materials like stainless steel in food processing ensure compliance with industry standards and improve safety.
- Operational Optimization: Tailoring roller materials to specific operational needs leads to overall system optimization and performance improvements.
These success stories underscore the importance of carefully selecting conveyor roller materials to meet the unique demands of different industrial applications, ultimately leading to significant operational benefits.
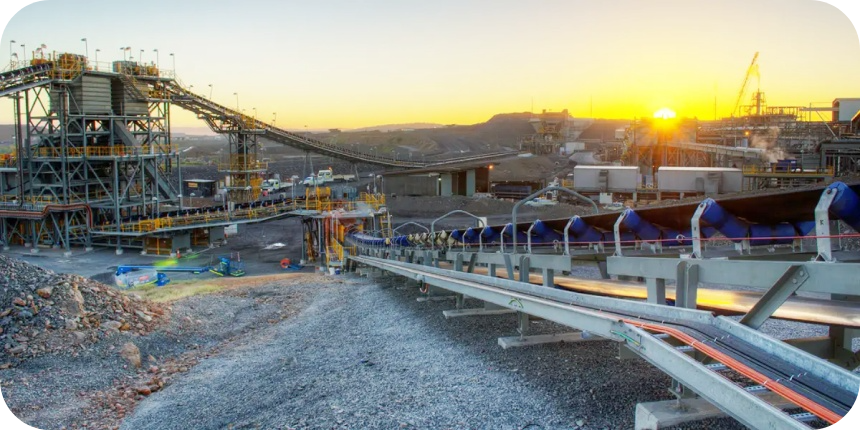
Considering Used Conveyor Roller Material: A Cost-Effective Option?
Opting for used conveyor roller material can be a budget-friendly alternative for businesses looking to optimize or expand their conveyor systems without a hefty investment. However, this approach comes with its set of advantages and challenges. Here, we discuss the pros and cons of using second-hand roller materials and offer guidance on assessing their condition to make an informed decision.
Pros of Using Second-hand Roller Materials
- Cost Savings: The most apparent benefit is the potential for significant cost reductions compared to purchasing new materials, allowing for budget allocation to other operational needs.
- Environmental Sustainability: Choosing used materials contributes to recycling efforts, reducing waste and the environmental footprint of your operations.
- Immediate Availability: Used conveyor roller materials often come with shorter lead times, as they are readily available from the supplier’s stock, providing a quick solution for urgent needs.
- Proven Durability: Second-hand materials that are still in good condition have demonstrated durability in real-world applications, potentially offering a reliable option.
- Flexibility in Application: For temporary setups or testing new processes, used materials offer a flexible and low-cost solution without the commitment required for new materials.
Cons of Using Second-hand Roller Materials
- Wear and Tear: Used materials may come with wear, reducing their lifespan and potentially leading to more frequent replacements or maintenance.
- Limited Selection: Finding the exact specifications, such as size or material type, may be challenging, leading to compromises on system efficiency or compatibility.
- Hidden Damage: Not all wear is visible, and internal damage or wear (like bearing issues) can lead to unforeseen breakdowns.
- Lack of Warranty: Second-hand materials often come without the warranties or guarantees that accompany new purchases, increasing the risk.
- Inconsistent Quality: Variability in the condition of used materials can lead to inconsistent performance across the conveyor system.
Assessing the Condition of Used Roller Materials
To mitigate the risks associated with used conveyor roller materials, thorough assessment and inspection are crucial:
- Visual Inspection: Look for visible signs of wear, such as cracks, rust, or deformation. Pay close attention to the surface of the rollers and the condition of the bearings.
- Rotation Test: Manually rotate the rollers to assess smoothness and resistance. Any grinding noises or uneven movement could indicate internal damage.
- Material Suitability: Ensure the material type is appropriate for your application, especially if the environment involves exposure to chemicals, extreme temperatures, or moisture.
- Compatibility Check: Verify that the dimensions, load capacity, and design of the used rollers are compatible with your existing system to avoid integration issues.
- Supplier Reputation: Source from reputable suppliers who are known for quality used materials. They should offer some level of inspection or certification of the materials’ condition.
Choosing used conveyor roller material can be a viable option under the right circumstances. By carefully weighing the pros and cons and conducting a thorough assessment, businesses can capitalize on the benefits while minimizing the drawbacks, ensuring their conveyor systems run efficiently and cost-effectively.

Tailoring Conveyor Roller Material for Unique Applications
In the diverse world of conveyor systems, one size does not fit all. Custom conveyor roller solutions are essential for addressing the unique challenges and requirements of specific applications. By customizing the conveyor roller material and design, manufacturers can significantly enhance the efficiency, durability, and functionality of conveyor systems. This section highlights how custom designs cater to specialized needs and the process manufacturers use to tailor materials for unique applications.
Spotlight on Custom Roller Designs for Specialized Needs
Custom conveyor idler roller designs play a pivotal role in industries where standard solutions fall short. For instance:
- High-Temperature Environments: Operations like foundries or steel mills require rollers that can withstand extreme heat. Manufacturers may use high-temperature resistant materials like specialized alloys or coatings to ensure longevity and performance.
- Corrosive Conditions: In chemical processing or outdoor environments, corrosion can rapidly degrade standard rollers. Custom solutions might include stainless steel, galvanized steel, or plastic materials known for their resistance to corrosive substances.
- Sanitary Applications: Food processing and pharmaceutical industries often require easy-to-clean surfaces that meet strict hygiene standards. Custom rollers made from food-grade stainless steel or certain plastics can meet these requirements, featuring designs that minimize crevices where bacteria could hide.
- Heavy Loads: Heavy manufacturing and mining applications need rollers designed to carry exceptionally heavy loads without failure. Custom heavy-duty rollers often utilize reinforced steel or specific alloys tailored for strength and durability.
- Sensitive Materials: Operations handling delicate or easily damaged goods may benefit from rollers with custom surfaces, such as softer materials or non-marking coatings, to prevent damage during transport.
How Manufacturers Tailor Materials for Unique Applications
The process of customizing conveyor roller material involves several key steps:
- Assessment of Needs: Manufacturers start by thoroughly assessing the client’s specific needs, including environmental conditions, load requirements, speed, and any regulatory compliance issues.
- Material Selection: Based on the assessment, manufacturers select the most suitable materials. This decision is crucial, as the right conveyor roller material directly impacts the system’s efficiency, safety, and cost-effectiveness.
- Design Customization: Engineers design the rollers to meet the unique specifications, considering factors like diameter, length, bearing type, and any special features required, such as anti-static properties or special coatings.
- Prototyping and Testing: Before full production, prototypes may be created and tested under conditions simulating the actual application. This ensures that the custom rollers meet all performance and durability requirements.
- Production and Quality Control: Once the design is finalized and tested, production begins. Throughout this process, strict quality control measures are in place to ensure that each custom roller meets the high standards set during the design phase.
Custom conveyor roller solutions offer a targeted approach to solving the complex challenges presented by various industrial applications. By meticulously tailoring the conveyor roller material and design to specific needs, manufacturers can provide solutions that significantly improve the performance, reliability, and overall efficiency of conveyor systems, ensuring they meet the precise demands of their unique operational environments.
Standard Sizes and Special Orders: Navigating Conveyor Roller Material Options
In the realm of conveyor systems, the diversity in applications necessitates a wide range of conveyor roller sizes and materials. Understanding the standard sizes available and the process for placing special orders for non-standard sizes or materials is crucial for optimizing your system’s performance. This section provides insights into commonly used roller sizes and offers guidance on custom orders to meet specific operational needs.
Commonly Used Roller Sizes
Conveyor rollers come in a variety of diameters and lengths to suit different conveyor widths and load requirements. Two of the most commonly used diameters are:
- 1-inch Diameter Rollers: Ideal for lightweight applications and small products. These rollers are commonly used in retail, packaging, and light manufacturing environments where precision and maneuverability are key.
- 4-inch Diameter Rollers: Designed for heavier loads and more robust applications. Such rollers are typically employed in heavy manufacturing, distribution centers, and applications requiring the movement of larger and heavier items.
Besides these sizes, rollers can range in diameter from less than an inch for specialized applications, up to several inches for industrial uses requiring the movement of very heavy loads. The length of the rollers is also variable, tailored to match the width of the conveyor and the size of the items being transported.
Guidance on Placing Custom Orders for Non-Standard Sizes or Materials
When standard roller sizes or materials do not meet your specific requirements, custom orders become necessary. Here’s how to navigate the process:
- Specification Development: Start by clearly defining your requirements. Consider the load weight, conveyor speed, environmental conditions (e.g., temperature, chemicals), and any regulatory compliance needs. This will help in determining the appropriate conveyor roller material and size.
- Manufacturer Consultation: Reach out to manufacturers with experience in custom conveyor solutions. Provide them with your specifications and discuss potential materials and designs that meet your needs. Experienced manufacturers can also offer recommendations based on similar applications.
- Request Quotes: Once you’ve identified potential manufacturers, request detailed quotes that include pricing, production timelines, and any minimum order quantities.
- Review Samples: If possible, ask for samples of the custom rollers to evaluate their quality and suitability for your application. This step is particularly important when experimenting with new materials or designs.
- Place Your Order: After reviewing samples and finalizing specifications, place your order. Ensure that the manufacturer provides a clear agreement on delivery schedules, quality assurance practices, and after-sales support.
- Follow-Up: Maintain communication with the manufacturer during the production process to address any issues promptly and ensure that the final product meets your expectations.
By understanding the standard sizes of conveyor rollers and knowing how to effectively place custom orders for unique sizes or materials, businesses can significantly enhance the efficiency and functionality of their conveyor systems. Tailoring the conveyor roller material and size to the specific demands of your operation is a critical step in optimizing performance and achieving long-term reliability.
FAQs About Conveyor Roller Material
Conveyor rollers are integral components of conveyor systems, designed to support and move items along the conveyor belt efficiently. The materials used for conveyor rollers vary, catering to different industrial needs based on load capacity, environment, and application specificity. Common materials include steel, stainless steel, aluminum, and plastic.
Steel Rollers: Widely used for their strength and durability, steel rollers are suitable for heavy-duty applications where high load-bearing capacity is essential. They are particularly favored in manufacturing, mining, and other sectors that deal with heavy goods.
Stainless Steel Rollers: Chosen for environments where corrosion resistance is necessary, such as in food processing, pharmaceutical, and chemical industries. Stainless steel offers longevity and cleanliness, meeting strict hygiene standards.
Aluminum Rollers: Lightweight yet sturdy, aluminum rollers are used where weight reduction is crucial without compromising the system’s integrity. They’re often found in packaging and assembly lines.
Plastic Rollers: Ideal for light-duty applications and environments requiring low noise levels. Plastic rollers are corrosion-resistant and offer a cost-effective solution for various industries, including retail and distribution.
Each material brings unique properties to conveyor rollers, like durability, weight, cost-effectiveness, and environmental resistance, making the selection process critical to the conveyor system’s overall performance and longevity.
Rollers can be made from a variety of materials, each selected for its specific properties to suit different operational requirements. The most commonly used materials include:
Steel: Offers high strength and durability, perfect for supporting heavy loads.
Stainless Steel: Provides excellent corrosion resistance, making it ideal for use in harsh environments or where strict cleanliness is required.
Aluminum: Known for its lightweight and corrosion-resistant properties, aluminum is suitable for applications where reducing the conveyor system’s overall weight is beneficial.
Plastic: Often used in light-duty or specific applications requiring corrosion resistance or quieter operation than metal rollers.
The choice of material impacts the roller’s durability, maintenance needs, operational noise, and suitability for various environments. For example, stainless steel rollers are preferred in the food and pharmaceutical industries for their ease of cleaning and resistance to corrosion, while heavy manufacturing might favor the strength and load capacity of steel rollers.
Gravity rollers, which rely on gravity to move items along the conveyor, are commonly made from materials like steel, aluminum, and plastic. The choice of material for a gravity roller depends on the application’s specific requirements, including the weight of the items being moved, the environment in which the conveyor operates, and cost considerations.
Steel: Used for its strength and durability, steel gravity rollers can handle heavier loads, making them suitable for industrial applications.
Aluminum: Chosen for its lightweight nature, aluminum rollers are easier to maneuver and are well-suited for applications where the conveyor needs to be moved or reconfigured frequently.
Plastic: Offers a corrosion-resistant and cost-effective option for lighter loads. Plastic rollers also operate more quietly, reducing noise in the work environment.
The material chosen for gravity rollers plays a significant role in the conveyor’s performance, affecting everything from load capacity and system weight to maintenance requirements and longevity.
Belt roller supports, which underpin the conveyor belt and provide a smooth surface for it to roll over, are typically made from materials that offer durability and low friction. Common materials for belt roller supports include:
Steel: Known for its strength and durability, steel is a popular choice for heavy-duty applications where the conveyor system must support heavy loads.
Polymer or High-Density Polyethylene (HDPE): These materials are used for their low friction, wear resistance, and noise-reducing properties. They are suitable for applications where a quieter operation is preferred or where minimal wear on the conveyor belt is crucial.
Stainless Steel: Selected for environments requiring corrosion resistance or high levels of hygiene, such as in the food processing or pharmaceutical industries. Stainless steel supports ensure the conveyor system remains clean and free from rust.
Choosing the right material for belt roller supports is crucial for ensuring the efficient operation of the conveyor system, minimizing wear and tear on the belt, and reducing maintenance requirements.
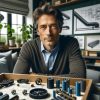
Jordan Smith, a seasoned professional with over 20 years of experience in the conveyor system industry. Jordan’s expertise lies in providing comprehensive solutions for conveyor rollers, belts, and accessories, catering to a wide range of industrial needs. From initial design and configuration to installation and meticulous troubleshooting, Jordan is adept at handling all aspects of conveyor system management. Whether you’re looking to upgrade your production line with efficient conveyor belts, require custom conveyor rollers for specific operations, or need expert advice on selecting the right conveyor accessories for your facility, Jordan is your reliable consultant. For any inquiries or assistance with conveyor system optimization, Jordan is available to share his wealth of knowledge and experience. Feel free to reach out at any time for professional guidance on all matters related to conveyor rollers, belts, and accessories.