Maximizing Efficiency with Trough Roller Conveyors
The concept of a trough roller conveyor might seem intricate at first glance, but it plays a pivotal role in the seamless operation of various industries. Essentially, a trough roller conveyor is a specialized material handling mechanism designed to transport bulk materials across short or long distances. Characterized by its distinctive trough-shaped carrying surface, which is supported by rollers, it ensures the safe and efficient movement of materials, especially those that are loose or granular in nature. This introduction aims to shed light on the fundamental aspects of conveyor troughing rollers, including their design, functionality, and the indispensable role they play in the logistics, mining, and agricultural sectors, among others. Understanding trough roller conveyors is essential for optimizing operations and achieving higher productivity in environments where material handling is a critical component.
What are Trough Roller Conveyors
Delving deeper into the essence and utility of trough roller conveyors, these systems are ingeniously crafted to enhance the efficiency of material transport. At its core, a trough roller conveyor is a mechanized system designed to handle a significant volume of materials, particularly those in bulk form such as grains, sand, coal, and more. It comprises a series of rollers set in a frame that forms a trough shape, cradling the material and preventing spillage while it moves from one point to another. This distinctive design is crucial for maintaining the integrity of the materials transported, especially when dealing with substances that are prone to scattering or spilling.
The functionality of conveyor trough rollers extends across various industries, from mining and agriculture to manufacturing and packaging. For instance, in the mining sector, they are pivotal in moving mined materials from excavation sites to processing facilities. In agriculture, they facilitate the transport of grains and feed. Manufacturing plants utilize these conveyors for the movement of raw materials and finished goods, while packaging industries rely on them for the efficient handling of packaged products.
Manufacturers
When it comes to manufacturers who specialize in the creation of trough roller conveyors, the market is diverse, with several leading names that stand out due to their innovation, quality, and service. Some notable manufacturers include:
- ConveyorTek – Renowned for their bespoke conveyor solutions, including state-of-the-art trough roller conveyors.
- Flexco – Offers a wide range of conveyor systems and components with a focus on durability and efficiency.
- Martin Engineering – Specializes in the development of advanced conveyor technology and bulk material handling solutions.
- Precision Pulley & Idler (PPI) – Known for their high-quality conveyor components, including idlers and rollers that are essential for trough roller conveyors.
- Superior Industries – Provides a comprehensive lineup of conveyor equipment and parts, focusing on innovation and reliability.
Parts
A trough roller conveyor is made up of several key components that work together to ensure its efficient operation. These parts include:
- Troughing Rollers – The primary component that shapes the conveyor’s trough, guiding and supporting the belt and materials.
- Conveyor Belt – Acts as the carrying medium, moving materials along the conveyor’s length.
- Frame – Provides structural support to the rollers and the conveyor belt.
- Drive Unit – Powers the conveyor, enabling the belt to move.
- Tail Pulleys – Located at the conveyor’s end, these pulleys adjust the belt’s tension and allow it to return after unloading the materials.
Price
The cost of a trough roller conveyor can vary widely, influenced by several factors such as size, material quality, and the specific needs of the operation. However, some common factors that affect the price include:
- Material Quality – Higher quality materials for components such as belts and rollers can significantly increase the price.
- Length and Width – Larger conveyors require more materials and more robust construction, leading to higher costs.
- Custom Features – Customization for specific operational needs, like temperature resistance or special coatings, can add to the price.
- Manufacturer – Prices can vary between manufacturers based on brand reputation, quality, and service offerings.
- Installation and Maintenance – The complexity of installation and the expected maintenance needs can also influence the overall cost.
Understanding these components and cost factors is crucial for anyone considering the integration of a trough roller conveyor into their operation, ensuring they make an informed decision that aligns with their material handling needs and budget constraints.
Used Trough Roller Conveyors
The market for used trough roller conveyors offers a valuable alternative for businesses looking to enhance their material handling capabilities without the significant expense of new equipment. Opting for a used trough roller conveyor can provide several benefits, including cost savings, quicker deployment, and the potential for finding equipment that has been discontinued but fits perfectly with existing systems. These conveyors, having already been in operation, can still offer reliable service for transporting bulk materials efficiently with the proper maintenance and refurbishment.
Benefits of Buying Used Trough Roller Conveyors
- Cost Efficiency: The most apparent benefit of purchasing used equipment is the substantial savings compared to buying new. This cost-effectiveness allows businesses to allocate their resources to other areas, such as maintenance or expansion.
- Immediate Availability: Used conveyor troughing rollers are often available for immediate purchase and can be installed and operational in a shorter timeframe than ordering new custom-built systems.
- Proven Reliability: Equipment that has been in use and maintained properly has proven its reliability and functionality in real-world conditions.
- Sustainability: Opting for used conveyors is an eco-friendly choice, extending the life of the machinery and reducing waste and the demand for new manufacturing materials.
- Flexibility: The secondary market may offer a variety of configurations and sizes not available in current models, providing more options to fit specific needs.
Tips for Purchasing Used Trough Roller Conveyors
When venturing into the market for a used trough roller conveyor, consider the following tips to ensure a wise investment:
- Inspect for Wear and Tear: Carefully examine the conveyor for any signs of excessive wear, especially on the rollers, belt, and frame. It’s crucial to assess the remaining lifespan of these components.
- Verify Operational History: Inquire about the conveyor’s previous application, including the materials it transported and the environment it operated in. This information can give insights into potential future issues or the need for specific repairs.
- Check for Compatibility: Ensure the conveyor’s specifications, such as belt width, speed, and load capacity, align with your operational requirements. Compatibility with existing systems should also be considered.
- Ask for Maintenance Records: Maintenance logs can reveal how well the conveyor was taken care of and highlight any recurring issues or parts that have been replaced.
- Consult a Professional: If possible, have a conveyor specialist or engineer assess the equipment’s condition and suitability for your needs. Their expertise can help identify any concerns or modifications that may be necessary.
Purchasing a used trough roller conveyor can be a strategic decision that yields significant advantages. However, due diligence during the buying process is essential to ensure that the equipment will serve its intended purpose effectively and reliably.
Sizing Trough Roller Conveyors
Correctly sizing a trough roller conveyor is a critical step in ensuring efficient operation, optimal performance, and longevity of the conveyor system. Inappropriate sizing can lead to a multitude of issues, including inadequate throughput, excessive wear and tear on the conveyor components, and even premature failure of the system. Here are examples illustrating the importance of appropriate sizing:
- Efficient Material Handling: Properly sized conveyors can handle the expected volume of material efficiently, without overloading or underutilization.
- Cost-Effectiveness: A conveyor that is correctly sized for its intended use can operate more cost-effectively by minimizing energy consumption and reducing wear on parts.
- Space Optimization: Appropriate sizing ensures the conveyor fits well within the available space, avoiding unnecessary alterations to the facility.
- Safety: Oversized or undersized conveyors can pose safety risks, including the potential for spillage or the creation of hazardous working conditions.
- Productivity: A conveyor that is sized to match the production requirements can significantly improve the overall productivity of an operation.
Key Factors in Determining Conveyor Size
Several key factors must be considered when determining the size of a trough roller conveyor for a specific application:
- Material Type and Characteristics: The nature of the materials being conveyed, such as their bulk density, abrasiveness, and moisture content, can influence the required size and type of conveyor.
- Conveying Capacity: The volume of material that needs to be transported per unit of time directly impacts the conveyor’s width and speed.
- Conveyor Length and Incline: The distance the materials need to be transported and whether the path includes inclines or declines affect the size and power requirements of the conveyor.
- Loading and Unloading Points: The locations where materials are loaded onto and discharged from the conveyor can influence the design and size of the conveyor system.
- Operational Environment: Factors such as the surrounding environment’s temperature, humidity, and the presence of corrosive or abrasive elements can dictate specific sizing adjustments to ensure durability and reliability.
Typical Trough Roller Conveyor Sizes
Trough roller conveyors come in a variety of standard sizes, which are often customizable to fit specific needs. Typically, these conveyors are categorized by the width of the belt, which can range from as narrow as 18 inches (approximately 45 cm) to as wide as 72 inches (approximately 183 cm) or more for heavy-duty applications. The length of these conveyors can vary greatly, from a few meters for small processing lines to several hundred meters for large-scale operations. The roller diameter and the spacing between rollers are also customizable based on the material load and the conveyor’s intended use, ensuring that each trough roller conveyor is optimally sized for its specific application.
Purchasing a Trough Roller Conveyor
When it comes to integrating a trough roller conveyor into your operation, making a well-informed purchase is crucial. This type of conveyor system plays a pivotal role in the efficiency and productivity of various material handling tasks. Here’s a guide on where to find conveyor trough rollers for sale and the essential factors to consider before making a purchase.
Where to Find Trough Roller Conveyors for Sale
- Manufacturer Websites: Directly visiting the websites of manufacturers who specialize in conveyor systems is a great way to find detailed information about available models and custom options.
- Industrial Equipment Distributors: Distributors often offer a wide range of conveyor systems from various manufacturers, providing the opportunity to compare different brands and models.
- Online Marketplaces: Websites like eBay and Alibaba feature listings for both new and used trough roller conveyors, catering to a wide range of budget and specification needs.
- Trade Shows and Expos: Attending industry-specific trade shows provides a unique opportunity to see the equipment in person, get demonstrations, and talk directly with manufacturers or distributors.
- Referrals: Sometimes, the best way to find quality equipment is through referrals from industry peers who have experience purchasing and using trough roller conveyors.
Things to Consider When Purchasing
- Material Handling Requirements: Understand the specific types of materials the conveyor will transport, including their weight, size, and properties (e.g., abrasive, corrosive). This knowledge is crucial for selecting the right conveyor design and materials.
- Conveyor Size and Configuration: Based on the layout of your facility and the material flow, determine the required size and configuration of the conveyor, including length, width, and curvature.
- Capacity and Speed: Assess the capacity (how much material needs to be moved) and the desired speed of the conveyor to ensure it meets your operational throughput requirements.
- Durability and Maintenance: Look for conveyors made with high-quality materials and components that offer durability and ease of maintenance. Understanding the maintenance requirements will help ensure the conveyor remains in optimal condition.
- Cost: While initial cost is a significant factor, also consider the total cost of ownership, which includes maintenance, repairs, and potential downtime. Sometimes, a higher upfront investment in a more durable and efficient system can save money in the long run.
- Warranty and Support: Check the warranty coverage and the manufacturer’s or distributor’s support services. Reliable after-sales support can be invaluable for troubleshooting and maintenance.
Purchasing a trough roller conveyor is a significant investment that can greatly impact the efficiency of your operations. Taking the time to research and consider the points outlined above will help ensure you select the right conveyor for your needs, providing long-term benefits to your material handling processes.
What are Trough Roller Conveyor Components
A thorough comprehension of the components that make up a trough roller conveyor system is essential for anyone involved in the design, maintenance, or operation of these conveyors. Each component plays a critical role in the system’s overall functionality and efficiency. This section delves into the key components that are fundamental to the operation of trough roller conveyors.
Conveyor Idler Rollers
Conveyor idler rollers are cylindrical rods that function to support the conveyor belt and the materials being transported. Their primary purpose is to maintain the structural integrity of the belt and facilitate smooth motion.
- Load Zones: Where materials are loaded onto the belt, idler rollers provide the necessary support to withstand the weight.
- Transition Zones: At the start and end of the conveyor belt, idler rollers help in transitioning the belt from a flat to a trough shape.
- Carry Side: Along the length of the conveyor where the belt carries the material, idler rollers support the belt and material weight.
- Return Side: On the underside of the conveyor, idler rollers support the belt as it returns after depositing the materials.
- Impact Zones: Special impact idler rollers absorb the shock and impact of heavy materials being dropped onto the conveyor belt.
Differences between conveyor idler rollers and other types of rollers are best highlighted through comparison:
Feature | Conveyor Idler Rollers | Other Types of Rollers |
---|---|---|
Purpose | Primarily to support the conveyor belt and material being transported. | May serve to drive the belt or provide tension. |
Position | Positioned along the conveyor path both on the carrying and return sides. | Often located at the ends of the conveyor. |
Load Handling | Designed to support loads over long distances. | May not be designed for heavy or continuous loads. |
Shape | Typically cylindrical, some may be slightly tapered for belt alignment. | Can vary widely depending on specific use. |
Movement | Do not drive the belt but allow it to move smoothly over them. | May directly drive the belt or control its tension. |
Return Roller Conveyor
A return roller conveyor is specifically designed for the return path of the conveyor belt after it has deposited the materials. These rollers support the empty belt on its way back to the starting point. They are crucial for maintaining belt tension and preventing sagging or dragging, which can lead to wear and energy inefficiency.
Conveyor Idlers
Conveyor idlers refer to the entire set of rollers that support the conveyor belt. They come in various types to suit different functions and conveyor designs:
- Troughing Idlers: Support the belt in a trough shape for carrying materials.
- Impact Idlers: Located at loading points to absorb the impact of falling materials.
- Return Idlers: Support the return path of the belt.
- Guide Idlers: Ensure the belt stays in alignment and does not wander off its path.
- Training Idlers: Automatically adjust the belt alignment if it starts to drift.
Conveyor Rollers
Conveyor rollers, a broad term, encompasses all types of rollers used in conveyor systems, including idler rollers, drive rollers, and return rollers. Their general purpose is to facilitate the movement of the conveyor belt or the materials being transported, depending on their specific role within the system.
Conveyor Belt Idler Roller
Conveyor belt idler rollers are the backbone of the conveyor system, providing a smooth surface for the belt to rotate on. They are strategically placed to support the weight of the belt and any materials it carries, minimizing friction and wear. Their role is critical in extending the lifespan of the conveyor belt and ensuring efficient operation of the trough roller conveyor system.
PPI Idlers Catalog and Superior Trough Roller Conveyor
The PPI (Precision Pulley & Idler) Idlers Catalog is a comprehensive resource for anyone in need of idler rollers, offering a wide range of solutions tailored for various applications within a trough roller conveyor system. This catalog presents an extensive selection of idler designs, each engineered to meet the specific demands of material handling processes. Whether the requirement is for heavy-duty mining operations, agricultural applications, or manufacturing facilities, the PPI Idlers Catalog provides detailed specifications, including roller diameters, belt widths, and load capacities, to assist in selecting the optimal idler for every application.
Overview of the PPI Idlers Catalog
The PPI Idlers Catalog distinguishes itself with its emphasis on durability, efficiency, and customization. It features:
- Troughing Idlers: Designed to support the belt in a trough shape, enhancing the conveyor’s capacity to carry bulk materials.
- Impact Idlers: Built with materials that absorb the impact of heavy or sharp objects, minimizing damage to the conveyor belt at loading points.
- Return Idlers: Engineered to support the return path of the belt, ensuring smooth operation and extending belt life.
- Specialty Idlers: Including spiral, rubber disc, and self-aligning idlers designed for specific challenges such as sticky materials, belt misalignment, and excessive wear.
Each product in the catalog is accompanied by technical data that specifies its use-case scenarios, making it easier for engineers and procurement specialists to make informed decisions.
Recommendations about Superior Conveyor Rollers
When it comes to selecting superior conveyor rollers for a trough roller conveyor, several factors should be considered to ensure the longevity and efficiency of the conveyor system. Recommendations include:
- Material Compatibility: Choose rollers made from materials compatible with the environment in which the conveyor will operate. For example, stainless steel or coated rollers for corrosive environments.
- Load Capacity: Ensure the rollers can handle the maximum expected load without deformation or failure. PPI’s catalog can help identify rollers that meet or exceed these requirements.
- Sealing and Lubrication: Opt for rollers with high-quality seals and lubrication to protect against dust, water, and other contaminants, which can prolong the life of the rollers and reduce maintenance needs.
- Energy Efficiency: Consider rollers designed to minimize friction and energy consumption, contributing to lower operational costs.
- Manufacturer Reputation: Choose products from manufacturers with a proven track record for quality and reliability. The PPI Idlers Catalog is a trusted source for many industry professionals due to its comprehensive selection and detailed product specifications.
Integrating superior conveyor rollers from the PPI Idlers Catalog into your trough roller conveyor system can significantly enhance performance and reliability. These recommendations are designed to help select the best components for your system, ensuring it meets the operational demands and provides long-term service in moving materials efficiently and effectively.
Idler Roller Design About Trough Roller Conveyor
The design of conveyor idler rollers is a fundamental aspect that determines the efficiency, durability, and overall performance of a trough roller conveyor system. Precision in the design of these components is crucial because they directly interact with the conveyor belt and the materials being transported, affecting everything from material handling capacity to operational safety.
Importance of Design
The design of conveyor idler rollers is important for several reasons:
- Load Distribution: Properly designed idler rollers ensure even distribution of load across the conveyor belt, reducing stress and wear on both the belt and the rollers.
- Belt Alignment: Idler rollers play a critical role in maintaining the alignment of the conveyor belt. A well-designed idler roller can prevent the belt from drifting off its intended path, minimizing the risk of damage or spillage.
- Operational Efficiency: The efficiency of a conveyor system depends significantly on the friction between the conveyor belt and the idler rollers. Optimal design reduces friction, enhancing operational efficiency and reducing energy consumption.
- Durability and Lifespan: The right design features can greatly extend the life of idler rollers and the conveyor belt by minimizing wear and tear.
- Maintenance Requirements: Efficiently designed conveyor idler rollers can lower the need for maintenance, thereby reducing downtime and operational costs.
Common Design Features
Several design features are common among high-quality conveyor idler rollers, ensuring they meet the operational demands of a trough roller conveyor:
- Material Selection: High-grade materials such as steel, stainless steel, or composite materials are used for durability and to withstand the environmental conditions of the conveyor system.
- Sealing Mechanisms: Superior sealing mechanisms protect the roller bearings from contaminants such as dust, water, and chemicals, extending the life of the idler rollers.
- Bearing Quality: High-quality bearings are essential for smooth operation and longevity. They must be selected based on load requirements and environmental conditions.
- Tubular Design: Many idler rollers feature a tubular design that offers an optimal balance between strength and weight, facilitating easier handling and installation while still providing sufficient support to the conveyor belt and materials.
- Adjustable Angle: For troughing idler rollers, the ability to adjust the angle of the side rollers allows for customization of the trough shape, accommodating different types of materials and operational needs.
The design of conveyor idler rollers is a critical factor in the success of a trough roller conveyor system. By focusing on important design aspects and incorporating common design features, manufacturers can ensure their conveyors operate efficiently, reliably, and with minimal maintenance requirements. This attention to design detail supports the conveyor’s ability to handle materials effectively, providing a seamless and productive material handling solution.
FAQs About Trough Roller Conveyor
A trough roller is a specialized component of a conveyor system designed to support the conveyor belt and guide it into a trough-shaped configuration. This shape is essential for efficiently transporting bulk materials, as it prevents spillage and ensures the materials are centrally located on the belt for even distribution. Trough rollers typically consist of a series of three or more rollers – a flat central roller flanked by two angled side rollers. The precise angle and arrangement of these rollers are crucial for forming the conveyor belt into the optimal trough shape, which can vary based on the material being transported and the specific requirements of the conveyor system. The design and materials of trough rollers are selected for durability, efficiency, and the ability to withstand the environmental and operational conditions of the conveyor system.
A trough conveyor is a type of conveyor system that utilizes a troughed belt design to transport bulk materials efficiently. This design incorporates a belt that, with the help of trough rollers, forms into a trough shape, cradling the material and preventing spillage along the conveyor’s path. Trough conveyors are particularly useful in industries such as mining, agriculture, and construction, where the movement of large volumes of loose or granular materials is required. They offer several advantages, including reduced material loss, improved safety by minimizing spillage, and the ability to transport materials over long distances, uphill, or downhill. The customization options for trough conveyors are vast, with adjustments available for belt width, roller type, and conveyor length to suit specific operational needs.
The purpose of a roller conveyor is to facilitate the efficient transport of goods and materials across a fixed path within manufacturing, distribution, and packaging facilities. Roller conveyors use a series of rollers mounted in a frame to move items either manually, by gravity, or by motor power. They are versatile systems that can handle a wide range of product sizes and weights, making them suitable for various applications, from simple material handling tasks to integrated manufacturing processes. The design of a roller conveyor allows for the accumulation of goods without the need for additional power, making it an energy-efficient choice for many operations. Furthermore, roller conveyors can be customized with different types of rollers, widths, and lengths to meet specific requirements, such as the handling of delicate items or the integration into automated systems.
Conveyor rollers come in several types, each designed to fulfill specific functions within a conveyor system:
Gravity Rollers: These rollers move goods along the conveyor through the force of gravity or manual effort, ideal for lightweight items and short distances.
Motorized Rollers: Powered by motors, these rollers are used in automated conveyor systems to transport items across longer distances or at variable speeds.
Grooved Rollers: Equipped with grooves, they are designed to drive belts or accommodate round belts for moving goods, often used in lightweight applications.
Tapered Rollers: Ideal for curves or corners in a conveyor system, tapered rollers ensure items maintain their orientation and direction of movement.
Impact Rollers: Installed at loading points, impact rollers absorb the shock and vibration of heavy items being dropped onto the conveyor, protecting the belt and system from damage.
Troughing Rollers: As discussed earlier, these rollers support a belt in a trough formation for the efficient transport of bulk materials.
Each type of roller is tailored to specific needs, from handling delicate products to moving heavy or bulk materials, ensuring that conveyor systems can be adapted to a wide range of industrial applications.
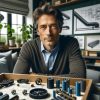
Jordan Smith, a seasoned professional with over 20 years of experience in the conveyor system industry. Jordan’s expertise lies in providing comprehensive solutions for conveyor rollers, belts, and accessories, catering to a wide range of industrial needs. From initial design and configuration to installation and meticulous troubleshooting, Jordan is adept at handling all aspects of conveyor system management. Whether you’re looking to upgrade your production line with efficient conveyor belts, require custom conveyor rollers for specific operations, or need expert advice on selecting the right conveyor accessories for your facility, Jordan is your reliable consultant. For any inquiries or assistance with conveyor system optimization, Jordan is available to share his wealth of knowledge and experience. Feel free to reach out at any time for professional guidance on all matters related to conveyor rollers, belts, and accessories.